
13 minute read
Solving industry challenges with AGVs
from MHD May 2020
by Prime Group
In a competitive environment like food and beverage logistics, AGVs can present a number of efficiency and productivity benefits. MHD speaks with Tony Raggio, General Manager Sales – AGV at Dematic to find out more.
Dematic has helped Lactalis Australia to achieve increased productivity at its Lidcombe Milk Site in NSW.
Food and beverage (F&B) companies across Australia and New Zealand are facing increasing challenges in a hyper-competitive environment, including cost pressures and the squeeze on margins, reduced availability of labour, and the need to maximise customer service levels, improve occupational health and safety, and increase visibility and traceability across operations.
According to Tony Raggio, General Manager Sales – AGV at Dematic more and more local companies are replacing manual forklifts with Automated Guided Vehicles (AGVs) to address these specific challenges and improve productivity, reliability, efficiency, and flexibility in their manufacturing and warehousing facilities.
COST PRESSURES
The imperative to optimise productivity and reduce costs in supply chains has never been greater for F&B manufacturers, Tony says.
“While labour costs continue to rise and drive the need to increase productivity, these cost pressures are being compounded like never before by the increasing concentration of the grocery retail market, and increasingly price conscious consumers,” he says.
Grocery retailers putting pressure on manufacturer margins
Grocery retailers are in a unique position of strength and this has major implications for F&B manufacturers. In Australia, the market share of the two top grocers stood at 68 per cent in 2017 -18 according to IBISWorld, one of the most concentrated grocery retail markets in the world. The New Zealand the concentration is even higher, with the top two grocery holding 79 per cent market share.
Major grocers are also consolidating market share in liquor retail. Australia’s two major grocers – with their big box liquor outlets and aggressive pricing – now control 67 per cent of the alcohol retail market.
“The grocers have leveraged their position to drive strong agreements with suppliers, eroding suppliers’ margins and enabling them to offer low store prices that smaller outlets find difficult to compete with. They are also using their position to drive their own
private label ranges at the expense of branded products, further cutting manufacturer’s margins,” Tony says.
LABOUR: RISING COSTS, DECREASING AVAILABILITY
According to Tony, the challenge to reduce costs is compounded by increasing labour costs. “Furthermore, operators who want to work in warehouses and distribution centres are becoming hard to find and retain. Nowhere is this more acute than in cold storage facilities,” he says.
Customer service pressures
In a highly competitive, consumer-driven market it is imperative for F&B manufacturers to get the right product in the right quantity at the right time to customers, more so than in any other industry.
“Grocers are less tolerant of missed delivery windows or incorrect products that lead to out of stock store shelves, imposing penalties for late or incomplete deliveries,” Tony says.
Manufacturers need to ensure there are no bottlenecks to operations – such as an operator leaving a pallet at the end of a palletising line – which can lead to production lines being stopped. In turn they need to ensure they have the correct product in the required stock quantity, and that orders are complete and accurately despatched in a timely manner.
THE KEY BENEFITS OF AGVS
Increasing productivity to reduce operational costs, reliance on labour
F&B companies are investing in AGVs to drive productivity gains in their warehouses and distribution systems, switching from manual forklifts to automated operations with AGVs to reduce operational costs and reduce reliance on scarce labour.
“In a two-shift operation, a typical company can expect a return on investment in around two years. These savings increase with the number of AGVs on site due to scale,” Tony says.
Tony states that if an operation runs three shifts a day, five days per week, the annual cost per forklift is approximately $240,000. This cost includes the wages of three drivers, capital expenditure or leasing for the vehicle, and running costs. Over ten years the cost of a forklift equates to approximately $2.4 million per forklift.
“Over a ten-year period, businesses can potentially save nearly $2.1 million per forklift by investing in an AGV system,” Tony reveals.
Businesses that run their warehouse for over eight hours per day can achieve substantial cost savings by switching to AGVs. And the more
AGVs create a safer working environment.
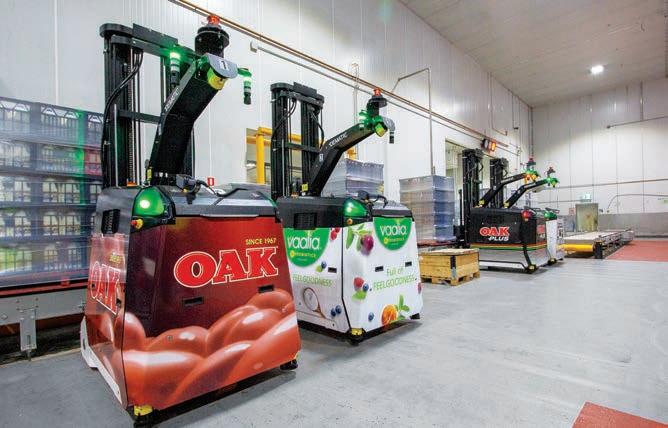
shifts there are, the more money businesses can save because AGVs can run 24-hours per day without any additional staffing costs or the need to pay any overtime or holiday rates.
IMPROVE OCCUPATIONAL HEALTH AND SAFETY
Occupational Health and Safety (OH&S) is regularly cited as the number one priority for many F&B manufacturers. The movement and storage of heavy pallet loads, potential breakages and spills, all pose dangers to operators. Apart from the human factor, Lost Time Injuries are becoming increasingly costly to operations. And an aging workforce only increases the imperative to address OH&S challenges.
According to SafeWork NSW, the main reasons why people are killed or seriously injured by a forklift include: • Hit by a forklift because of driver error, working too close to the forklift or inadequate traffic management • Hit by a load a forklift was moving because the driver did not use an attachment when one was needed, or assisting to adjust or steady the load • Not wearing a seat belt in a tip-over. The forklifts mostly tipped because operators were turning on uneven or sloping ground.
“Thanks to their safety and accuracy features, AGVs create a safer working environment. Dematics AGVs comply with all current safety standards,” Tony says.
AGV systems are suitable for materials handling applications in harsh applications including cold stores. AGVs can also operate around the clock and run at night with the lights out in the freezer warehouse, which has a temperature of minus 25 degrees Celsius. The addition of AGVs in the warehouse provides a reduction in occupational health and safety concerns as well as eliminating human error.
It is worth reiterating with regards to safety, with their multiple sensors AGVs are able to work safely alongside operators and other material handling equipment such as forklift trucks.
INCREASED VISIBILITY AND TRACEABILITY
Food Standards Australia New Zealand (FSANZ) requires food to be tracked through all stages of production, processing and distribution (also known as farm to fork). The aim is to enable quick and effective corrective action in the event of something going wrong, such as a product recall, and prevent contaminated product from reaching consumers.
Supply chain management systems need to capture sources of raw materials, additives and other ingredients and all other inputs, and provide product batch or lot identification, production and expiry dates.
In addition to meeting Food Standards Code requirements, F&B companies recognise that product traceability systems help protect their brands by enabling a rapid and effective response to any incident.
Apart from batch and lot tracking, Warehouse Management Systems (WMS) need to effectively manage inventory and First In First Out (FIFO) rules; in many cases, major grocers will only accept consecutively numbered batches and expiry dates.
By fully automating transport and storage tasks, and fully tracking all movements, AGVs provide full visibility of operations and complete traceability of product from production through to warehousing and despatch.
“AGVs are very reliable and significantly transform the efficiency of manufacturing logistics operations. When an AGV transports and puts a pallet somewhere, it constantly updates the WMS, so all materials handling is conducted in real time,” Tony says.
FLEXIBILITY AND SCALABILITY
F&B companies’ operations change, and they need the flexibility to be able adjust any systems accordingly. AGVs are a flexible automation solution and can scale or flex as required.
“Adding new machines or reallocating AGVs from one area of a facility to another is quick and easy. AGVs are able to communicate with each other and the control system for the AGVs is also very smart, so if one AGV is closer to a task than another, they’ll swap tasks.,” Tony says.
The AGV management software is shared so that changes can easily be made to one machine and replicated to all. New machines can be operational in minutes after arriving at a facility, minimising any disruption to operations.
Because today’s AGVs use laser and vision-based navigation, modifying or changing a guide path is an easy operation. Simple software changes to the fleet management software can allow guide paths to easily be changed or modified. Changing the guide path only needs to be done once, and all the machines in the system get the change.
Redeploying AGVs to different locations is equally easy. This allows AGVs to be shared among multiple facilities or areas within a facility to alleviate seasonal demands.
LOCAL PRODUCTION AND SUPPORT
Another important factor when considering the installation of AGVs here in Australia, is whether the provider can offer support at a local level.
Dematic manufacturers AGVs for its Asia Pacific market at its site in Belrose, New South Wales. “We’re capable of manufacturing around 120 AGVs a year at this site. In addition to local manufacturing, the biggest advantage for us is that we don’t have to rely on overseas resources to service our customers,” Tony says.
The software for the AGVs is also developed by Dematic locally. “Our warehouse control system, AGV Manage has been developed at Belrose and is tailored to each customer. Allowing us to offer hardware and software support in Australia,” Tony says.
Many providers in this field are based in Europe or the US, and therefore need to send an engineer to the site for the installation, adding significant cost to the solution. This may also present an issue for ongoing maintenance and support.
“While there are some fixes that can be done remotely, with a lot of AGV equipment there is a significant safety consideration, so some things you need to have the engineer on site. If that is the case it could cost upwards of $20,000 sending someone over from Europe or the US, while we have engineers based here in Australia,” Tony says.
During the current challenge of borders closing due to COVID-19 restrictions, this has become even more critical. “Now more than ever this is a huge advantage for our customers. We don’t need to rely on expertise from overseas, we are here in Australia and can support our customers during this crisis,” he says.
CONCLUSION
F&B companies have always faced challenges due to being part of a fast-paced and demanding grocery environment, and as technology advances and consumer expectations around product availability increase, the challenges facing F&B companies have also increased.
With growing cost pressures and customer service pressures, F&B companies need to improve productivity, increase visibility and ensure that their warehouse operations have the flexibility and scalability to keep up with future demands.
In order for F&B companies to accommodate and also capitalise on the changing demands of the market, they will need to think carefully about how supply chain processes can be optimised to better suit the needs of the F&B market.
Investing in technology allows F&B companies to improve warehouse operations and address a number of these key challenges, and many F&B companies are already choosing to implement AGVs in the supply chain.
AGVs increase productivity, reliability and improve OH&S through minimising the need for human workers in the warehouse, which also allows companies to bypass labour shortages and run operations 24/7 without incurring added wage costs.
“AGVs provide better visibility of warehouse operations by automating processes that were previously manual, as well as providing the flexibility needed to support any future growth of a company,” Tony says.
The significant benefits that AGVs provide to F&B companies enable businesses to remain competitive in an increasingly challenging environment, and ensure they are well positioned to address any future changes to the industry. ■
ARNOTT’S IMPLEMENTS DEMATIC AGVS FOR IMPROVED RELIABILITY EFFICIENCY AND SAFETY
Australia’s largest and most quintessential biscuit brand, Arnott’s, has introduced Automatic Guided Vehicles from Dematic to increase manufacturing productivity and reliability.
Arnott’s recently successfully completed the roll-out of six Dematic’s AGVs at its head manufacturing plant in Virginia, Brisbane, Queensland.
The advanced, self-charging Dematic AGVs are designed to increase efficiency, accuracy and safety in manufacturing and distribution centres, achieving this with high precision laser guidance and multiple collision avoidance sensors.
Tim Morgan, Arnott’s Group Plant Manager QLD & SA, says it partnered with Dematic in order to find a solution that enhanced the efficiency of its manufacturing operations.
“We elected to partner with Dematic as they are the market leader for AGVs in Australia,” Tim says.
The AGVs work systematically to carry large pallets of product from end-of-palletising stations to drive-in storage racking areas. From there the AGVs take the pallets to handover stations where forklifts transport them to manufacturing lines. The overall process of using the AGVs increases reliability, with the AGVs capable of working non-stop 24/7 every day of the year. This is in addition to improving efficiency and accuracy of operations, thereby minimising mistakes and workplace accidents which provides significant improvements in occupational health and safety standards.
“We are very pleased to be working alongside such a well-known and respected Australian brand as Arnott’s,” Tony Raggio, General Manager for AGVs at Dematic says. “Our AGV automated technology is a very exciting product for us here at Dematic, and it’s fantastic to see it making such successful improvements to Arnott’s warehouse processes.”
To find out more, watch the video here: https://youtu.be/VmbG51tOLXw
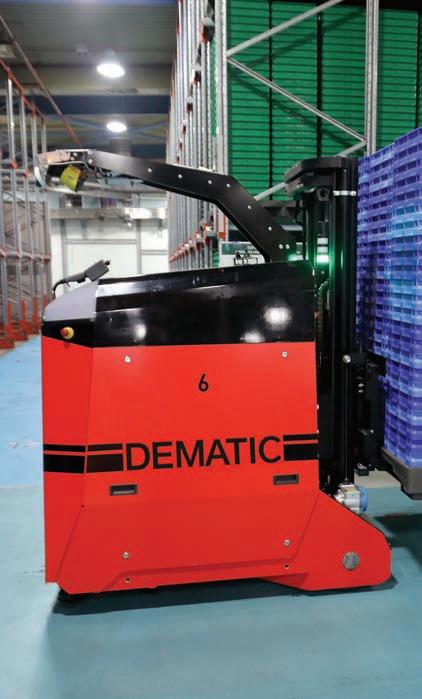
AGVs have helped Arnott’s to improve reliability, increase flexibility and provide better sanitation.
LACTALIS BOOSTS PRODUCTIVITY WITH AUTOMATED GUIDED VEHICLE 24/7 OPERATIONS AT LIDCOMBE MILK SITE
Dematic has helped Lactalis Australia to achieve increased productivity at its Lidcombe Milk Site in NSW, with the roll out of a new automated guided vehicle solution. Lactalis Australia (formerly Parmalat) is owned and operated by the Lactalis Group, a third generation, French family owned business. Its Australian operations date back to the original Pauls milk business which has been running since 1932. Locally, Lactalis has 2,500 employees who work closely with up to 500 Australian farmers. “One of Lactalis’ key goals is to invest in and grow the Australian dairy industry, as well as to promote Australia as a high-quality producer for the Asia Pacific region,” Kristian Brennan, National Logistics Optimisation Manager at Lactalis says. “To support this growth, Lactalis is always looking for new ways to improve our operations by boosting efficiencies and productivity. “The new AGV solution has successfully helped us to significantly increase productivity at our Lidcombe site, as it allows us to run a faster operation 24 hou rs a day, seven days a week.” The AGV solution chosen by Lactalis, Dematic’s Counterbalance Series AGV, manages the transportation of pallets of milk at the Lidcombe site and is capable of lifting loads of up to 1.2 tonnes to a height of six metres. The AGVs are well suited to working at the site, which is a chilled environm ent that has a temperature of 2 to 4 degrees Celsius. Four AGVs work to retrieve pallets from an inbound conveyer system from production, and then feed the pallets into an order buffer, releasing the pallets at a declined angle onto pallet live storage racking. They operate in a small space and manage tight traffic at high speeds of up to 1.7 metres per second. The AGV solution’s accuracy and safety around workers and any obstacles is ensured through sensors and laser scanners that help them navigate with precision. The AGVs are powered by Lithium Ion batteries and can drive themselves onto charging floor plates at times of inactivity and be fully charged in 2 hours. “The need to optimise productivity and reduce costs in food & beverage supply chains has never been greater,” Tony Raggio, General Manager AGVs at Dematic says. “We’re excited to see Lactalis Australia has increased its productivity, while also being able to receive a good ROI from its investment in Dematic AGVs.”