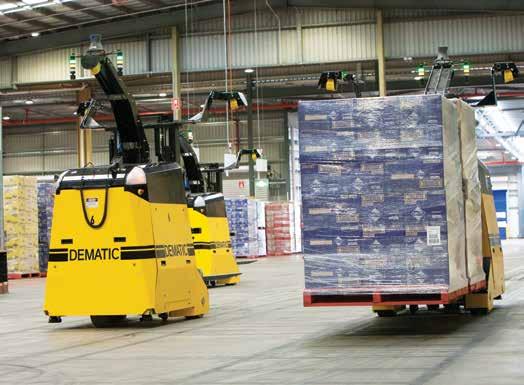
6 minute read
Reduce operational costs with AGVs
Philip Makowski at Dematic offers his tips for optimising and reducing costs in food and beverage logistics.
The importance of optimising productivity and reducing costs in supply chains has never been greater for manufacturers across Australia and New Zealand.
Dematic AGV accessing the top level of pallet racking at Oxford Cold Storage. While labour costs continue to rise and drive the need to increase productivity, these cost pressures are being compounded like never before by the increasing concentration of the grocery retail market, and increasingly price conscious consumers.
As a result, more and more local companies are turning to automated guided vehicles (AGVs), especially in the food and beverage (F&B) sector, to help improve productivity and reduce operational costs in their manufacturing and warehousing facilities.
THE CHALLENGES FACING MANUFACTURERS IN FOOD AND BEVERAGE Grocery retailers are currently in a unique position of strength and this has major implications for F&B manufacturers. In Australia, the market share of the two top grocers stood at 68 per cent in 2017-18 according to IBISWorld, which means it is one of the most concentrated grocery retail markets in the world.
Major grocers are also consolidating market share in liquor retail. Australia’s two major grocers – with their big box liquor outlets and aggressive pricing – now control 67 per cent of the alcohol retail market. The grocers have leveraged their position to drive strong agreements with suppliers, enabling them to offer low store prices that smaller outlets find difficult to compete with. They are also using their position to drive their own private label ranges, further cutting manufacturer’s margins.
In a highly competitive, consumerdriven market it is imperative for F&B manufacturers to get the right
product in the right quantity at the right time to customers, more so than in any other industry. Grocers are less tolerant of missed delivery windows or incorrect products that lead to out of stock store shelves, imposing penalties for late or incomplete deliveries.
Manufacturers need to ensure there are no bottlenecks in their operations – such as an operator leaving a pallet at the end of a palletising line – which can lead to production lines being stopped. In turn they need to ensure they have the correct product in the required stock quantity, and that orders are complete and accurately despatched in a timely manner. The challenge many F&B companies are facing to reduce costs is compounded by increasing labour costs and the growing difficulty in finding and retaining workers who want to work in warehouses and distribution centres (DCs), especially in cold storage facilities.
THE IMPLEMENTATION OF AGVS IN THE WAREHOUSE F&B manufacturers are investing in AGVs to drive productivity gains in their warehouses and distribution systems. They’re also switching from manual forklifts to automated operations with AGVs to reduce operational costs and reduce reliance on scarce labour.
These companies are implementing AGVs in their warehouses to cover numerous applications. Dematic’s range of AGVs provide pallet transport within and between production and warehousing, storage and retrieval from rack – including heights up to 10.7m, double-deep, narrow aisle, drive-in and mobile rack – and block stack operations, pick face replenishment and truck loading, within a variety of environments including outdoors
and freezer facilities. AGVs can, and typically do, work alongside human operators, and as such have safety features in place, with sensors to identify and stop when in proximity to humans or machinery that cross their paths. When sensors detect an object in the guide path, the AGV first slows and then stops, depending on the distance to the object. These same sensors also assist in navigation. For example, they help determine the exact positioning for picking/putting objects within a rack or other location. Further, costs savings and reduced warehouse operation disruptions are gained because unlike a forklift operator, AGVs can operate around the clock without needing breaks, and can run at night with the lights out in a freezer warehouse, which has a temperature of minus 25 degrees Celsius. The addition of AGVs in the warehouse also eliminates human error. Replacing manual forklifts with AGVs increases reliability, improves OH&S and eliminates product damage, increases operational visibility and traceability, and maximises despatch and shipping accuracy.
IMPROVED OCCUPATIONAL HEALTH AND SAFETY Occupational health and safety (OH&S) is a significant priority for F&B manufacturers due to the movement and storage of heavy pallet loads, potential breakages and spills, which all pose dangers to warehouse operators.
Apart from the human factor, lost time due to injuries are becoming increasingly costly to operations. And with an ageing workforce the need to address OH&S challenges is increasing.
Thanks to their safety and accuracy features, AGVs create a safer working environment with no accidental collisions and zero damage to loads. They strictly comply with and exceed the demands of international safety standards. AGVs are also suitable for materials handling applications in harsh environments such as cold storage.
INCREASED VISIBILITY AND TRACEABILITY Food Standards Australia New Zealand (FSANZ) requires food to be tracked through all stages of production, processing and distribution. The aim is to enable quick and effective corrective action in the event of something going wrong, such as product recall, and to prevent contaminated product from reaching consumers.
Supply chain management systems need to capture sources of raw materials, additives and other ingredients and all other inputs, and provide product batch or lot identification, production and expiry dates. In addition to meeting Food Standards Code requirements, F&B companies recognise that product traceability systems help protect their brands by enabling a rapid and effective response to any incident. Apart from batch and lot tracking, warehouse management systems need to effectively manage inventory and FIFO (First In, First Out) rules; in many cases, major grocers will only accept consecutively numbered batches and expiry dates.
By fully automating transport and storage tasks, and fully tracking all movements, AGVs provide full visibility of operations and complete traceability of product from production through to warehousing and despatch.
FLEXIBILITY AND SCALABILITY F&B companies’ operations can change and they need systems that provide them the flexibility to be able to adjust warehouse operations accordingly. AGVs are a flexible automation solution and can scale or flex as required. Adding new machines or reallocating AGVs from one area of a facility to another is quick and easy. The AGV management software is shared so that changes can easily be made to one machine and replicated to all, and new machines can be operational in minutes after arriving at a facility.
Because today’s AGVs use laser and vision-based navigation, modifying or changing a guide path is an easy operation. Simple software changes to the fleet management software can allow guide paths to easily be changed or modified. Changing the guide path only needs to be done once, and all the machines in the system get the change. Redeploying AGVs to different locations is equally easy. This allows AGVs to be shared among multiple facilities or areas within a facility to alleviate seasonal demands.
AGVs can significantly transform the efficiency and productivity of F&B manufacturers logistics operations, they provide long term benefits that will enable F&B companies to remain competitive, now, and in the future. ■
EXHIBITION SPACE NOW ON SALE

1ST - 3RD APRIL 2020 MELBOURNE CONVENTION & EXHIBITION CENTRE



SUSTAINABILITY | AUTOMATION INDUSTRY 4.0 | E-COMMERCE
SUPPORTING SPONSORS

ASSOCIATION PARTNERS