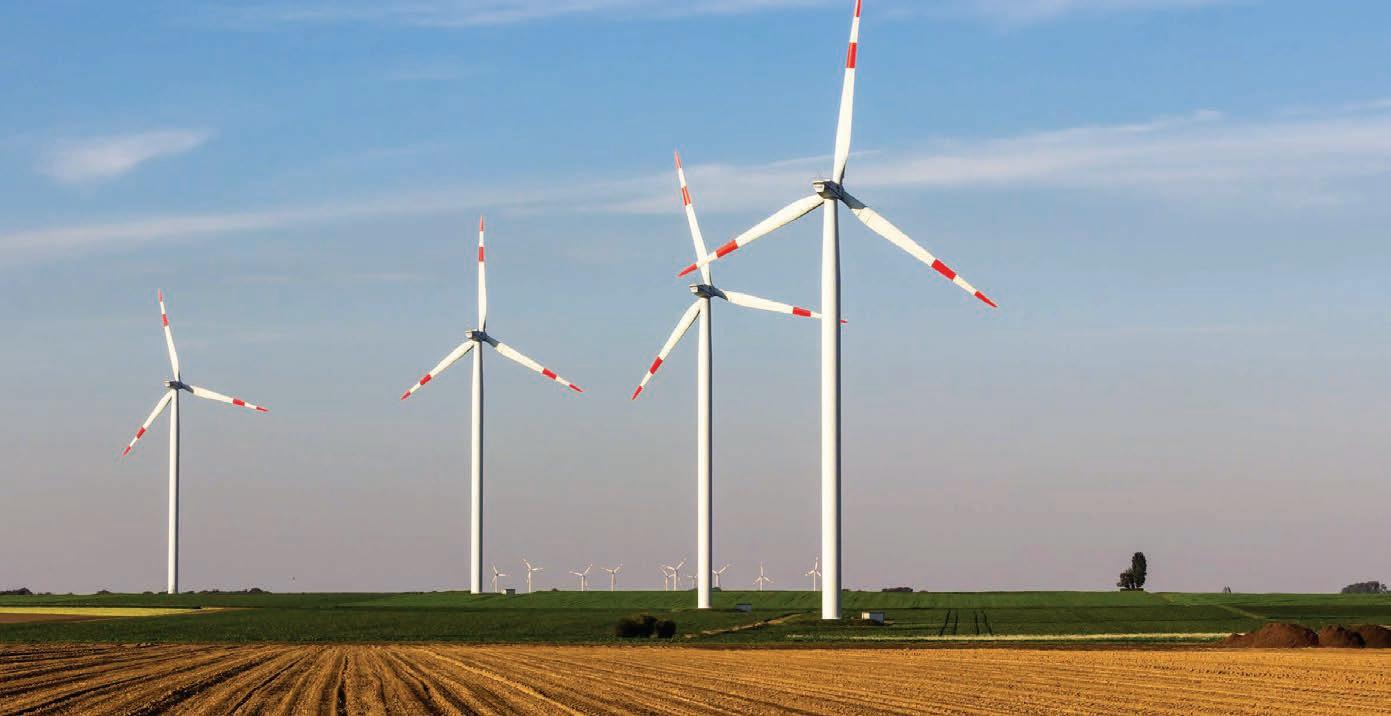
5 minute read
Sustainability
from MM July 2020
by Prime Group

A wind turbine usually comprises of roughly 8,000 parts or more and every part is critical.
The importance of maintaining wind turbines
Bestech Australia highlights the importance of monitoring maintenance for wind turbines using sensors.
WIND energy has grown into a sustainable power technology in recent times.
With various advancements going on in this sector and continued worldwide adoption and implementation, the application of condition monitoring techniques for the predictive maintenance of wind turbines becomes imperative.
A wind turbine typically comprises around 8,000 parts or more including the blades, rotor, main bearing, electrical generator and other major components.
Unlike the conventional power sources, wind turbines are consistently exposed to unpredictable and variable environmental conditions such as severe winds, tropical heat, hail and snow, stormy weather, and other weather conditions that affect the operations and health of a wind turbine.
These variations result in constantly changing loads that lead to intense mechanical stress on the components of a wind turbine.
Therefore, to estimate the remaining useful life of the equipment and to implement the best maintenance strategy before the failure occurs, condition monitoring systems are employed with the help of sensor technology to monitor various parameters such
Proactive monitoring of wind turbines based on precision sensor technology helps in providing a safe, productive, cost-efficient and reliable power output.
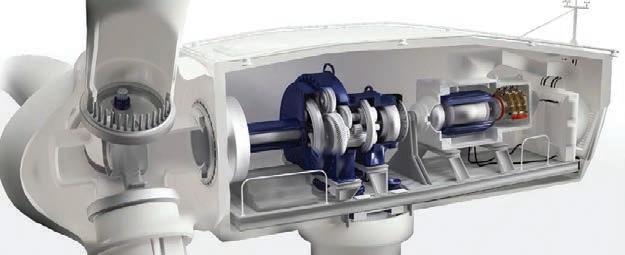
as temperature, voltage, current, noise or vibration.
Considering the huge number of components involved in the operation of a wind turbine, there are various maintenance tasks that are required to be performed on a regular basis. The maintenance is to ensure that it operates efficiently and to monitor the structural health of the wind turbine. Proactive monitoring of wind turbines based on precision sensor technology helps in providing a safe, productive, cost-effective and reliable power output.
The rotor tower of a wind turbine may weigh dozens of tons and standing high up in the sky. It is an essential component to be monitored as it may incur an astronomical cost for replacing it. Generally, the housing and tower of the wind turbine are exposed to huge wind loads. The effect of these wind loads become significant when they act on objects above 100m from the ground.
To minimise the impact of these loads, the gearbox and generator are equipment with an elastic bearing. However, the relative motion of the gearbox and the generator must be balanced by the couplings in wind turbines. The offset of these metallic coupling rings is measured using non-contact displacement sensors, which leads to the measurement of the load profile.
The oil gap between the bearing and the shaft is also a major concern in wind turbines for it prevents direct contact between the bearing surface and the shaft. In cases of extreme load, the oil pressure can rise, closing the gap. This may damage the bearing and eventually result in turbine failure. Hence, the gap between the bearing surface and the shaft needs to be consistently monitored.
In large generators and electric motors, the force imbalances caused by extreme wind and weather conditions during operations may close the gap between the rotor and the stator to come in contact. This may lead to component failure. For this reason, the gap between the rotor and the stator inside the motor is consistently monitored. The generator also tends to experience overheating and contact problems which may hamper the operations and compromise the efficiency. A monitoring system should be in place to detect potential overheating issues before it leads to failure.
Wind turbine monitoring sensors
The advancement in sensors’ techno logy have led to intensive use of sensors in industrial test and measurement. A wide range of sensors instruments are available for measuring the physical parameters. They also give the capability for the user to analyse and evaluate the trends as well as predict the changes
Sustainability
based on the measurement data.
Perhaps, eddy current sensors are one of the most commonly and frequently used sensors technology for maintenance applications in wind turbines.
These inductive displacement sensors are able to operate in harsh industrial environments as they have excellent resistance to dirt, high pressures and extreme temperatures.
Ideally, they are to be used for measuring the oil gap between the bearing surface and the shaft. Measurement can also be performed in different directions; axial, radial and tangential axes.
During gap measurement, they are mounted to the bearing shoe to measure through the oil film and the plain bearing directly onto the shaft.
The measured values are consistently monitored in order to avoid any unnecessary wear of couplings, bearings or shaft seals which may lead to some serious damages to the wind turbine.
Besides measuring oil gap, Eddy current sensors are also used to monitor the supporting moments of the nacelle.
They enable early recognition of ay oscillation by measuring the distance between the nacelle and the tower. This allows the operators to switch off the plant when the wind load is too high.
Laser triangulation sensors are also used in some critical applications that involve the detection of movement and vibration in the turbine.
These sensors measure based on the triangulation principle that includes sending a laser beam on the target object and the results are calculated based on the reflected beam from the object.
This non- contact measurement technique is also suitable for determining the distance between the mast and the foundation of a wind turbine.
These sensors can also be used to monitor the vibration of the tower as small changes can be detected with absolute precision. This provides data to perform trend analysis to study the vibration behaviour over time.
Another type of positioning sensor, capacitive sensors, are suitable for major monitoring task in a wind plant that requires gap measurement between the stator and the rotor. These sensors offer high precision reading with capability to provide the maximum resolution in picometer range.
Capacitive sensors can be incorporated while the motor is still running to provide real-time gap analysis. They are also resistant to the electromagnetic fields existing in motors. Therefore, these sensors are considered highly suitable for monitoring wind turbines.
Last but not least, draw wire sensors can also be considered when there are requirements for low-cost measurement. They can typically last in industrial environment and offer long service life if handled properly.
An infrared temperature sensor can also be considered as non-contact temperature monitoring solutions for preventive maintenance. It can be used with accelerometers as part of condition monitoring system for early detection of faulty components in the turbine.
As leading sensors and instrumentation company in Oceania, Bestech Australia supplies a wide range of instrument to support any challenging industrial test and measurement tasks. We have established the importance of using non-contact precision sensor technology for condition monitoring and preventive maintenance.
Using precision sensor technology, both off-shore and on-shore wind turbines can be monitored in real-time. This allows the maintenance engineers to detect any potential failure by providing reliable measurements and targeted evaluation of critical data.
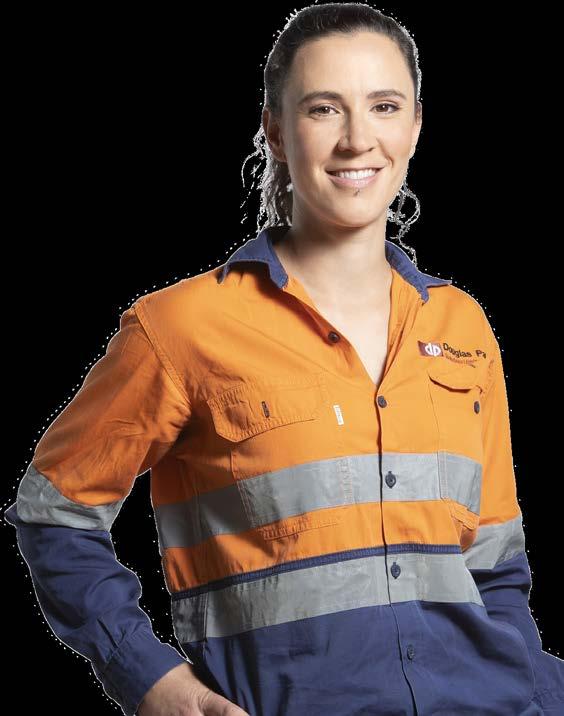