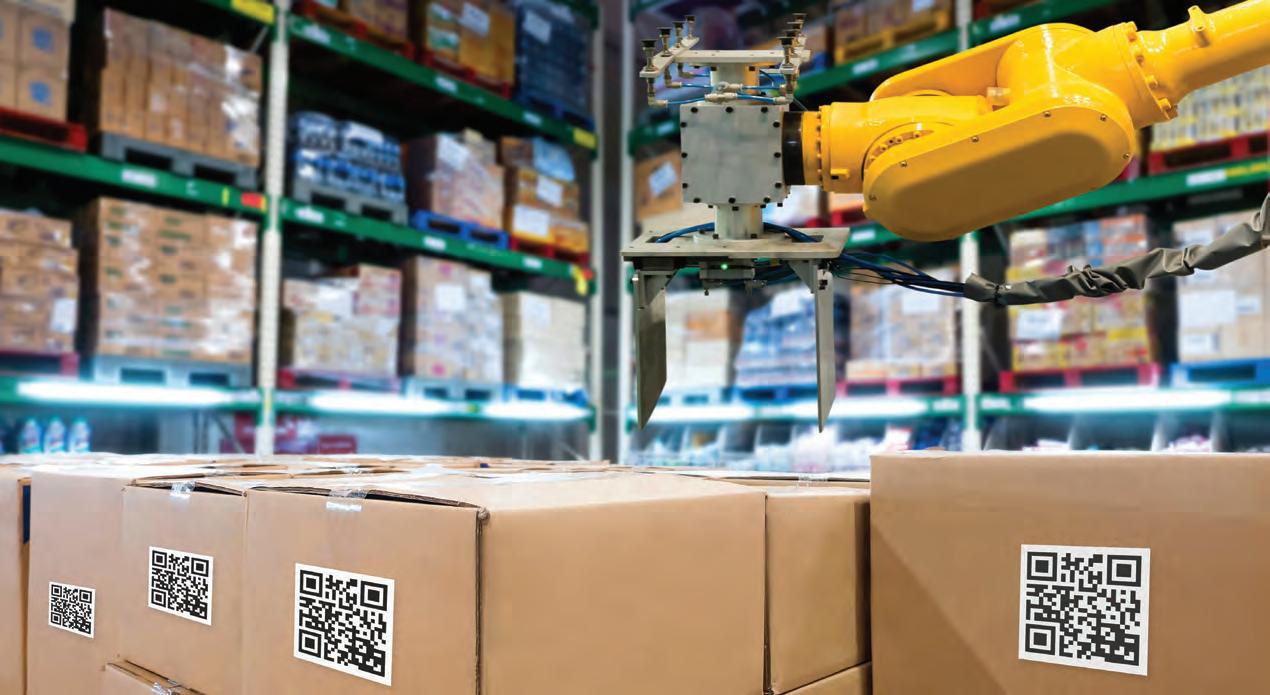
2 minute read
Editor’s Note
Comment
SYED SHAH – Managing Editor, Manufacturers’ Monthly
Further strides to manufacturing in 2022
PUTTING a pause on the issues COVID has currently caused, like supply chain issues for high demand products and services for domestic consumption, and the racket-fuelled drama that has gripped the nation over a certain international sporting personality’s vaccination status, let’s look instead at issues to do with bigger ongoing concerns on industrial developments that business can focus on and control, internally.
It has been quite some time since the concept of the Internet of Things (IoT) has been introduced into the traditional manufacturing mainframe and having the skills to manage IoT technologies has been an issue for a while until very recently.
Most local manufacturing conferences in the past decade addresses this “gap”, time and again. Initially, the thought of having data to measure the deterioration of your existing equipment was just something fancy that you saw at a convention centre and not practical.
Then rising costs of production set with cheaper overseas competition for similar products in huge quantities, and before we knew it, local manufacturing was behind the eight ball. We took quite a while in terms of skills to bridge the gaps for upskilling, and it’s still not enough, but we’re on the way.
Today, the IoT for the industrial sector – the Industrial Internet of Things (IIoT) or Industry 4.0, depending on the organisation you’re from – is highly developed, and the global market for it is large. Accenture’s report Winning with the Industrial Internet of Things already stated that the IIoT market will be more than US$14.3 trillion ($19.63 trillion) by 2030.
Recently, there has been an increase in the bridging of the “missing link” between universities who offered science, technology, engineering, and mathematics (STEM) courses and manufacturing companies who offer real-life work experience. One such collaboration that happened last year would be the advanced research centre for next generation vehicles that will be established at Deakin Univerity thorough a $13 million Next Generation Simulator project at Waurn Ponds. In this project, there will be partnerships with Ford Australia and Ansible Motion that will ensure locally made vehicle products are commercially viable and internationally competitive. The project will create 15 jobs by 2025, as well as four PhD positions and two internships each year.
In Australia, there is an active drive towards involvement by governments to have training implemented before students get into the workforce. Also, there are programs to reskill workers in the existing workforce for the new, advanced skills needed in a rapidly changing manufacturing sector.
Whether the person is a fresh graduate or someone that is retrained, as long as he or she is equipped with the adequate skillset where smart manufacturing is concerned (analytics, automation, artificial intelligence, etc.), then a difference can be made on the manufacturing floor.
The collaborations from a few years back between TAFE and industry partners constantly needs updating in terms of training manuals, styles, technology, equipment, etc. The structure for collaborations has drastically improved, and unlike in the past, both sides are now willing to understand the urgency and react to integrate training related to IIoT technologies. But will this bear fruit and steer our manufacturing sector to greater heights in the years to come? That remains to be seen.