
18 minute read
News@MM
from MM Aug 2019
by Prime Group
IMCRC, UTS, 3D printing research partnership hits one-year milestone
A research partnership between the Innovative Manufacturing CRC (IMCRC), the University of Technology Sydney (UTS) and Downer’s Mineral Technologies has reached its one-year anniversary. The project aims to develop custom 3D printed technologies for precision-engineered mineral separation and mining equipment. The idea of the project is to create mineral separation spirals, which can be produced with a 3D printer after individual models are created by Mineral Technologies.
Once up and running, the project hopes to print on site and as required, to save costs and reduce lead-time.
According to Alex de Andrade, UTS associate professor and global manager, sales, equipment and technology for Mineral Technologies, the past 12 months have set the project up for further development. “In the first year, we designed a small printer and machinery code as well as printed a scaled version of our selected spiral model. We are now into the cost and wear testing comparisons and in parallel we are building the fullscale bespoke prototype printer,” said de Andrade.
Working out of UTS’s Rapido, an advanced technology development unit, the project has all the
The collaboration will create 3D printed technologies for the mining sector.
core components of innovative manufacturing, according to UTS Rapido director Hervé Harvard. “The project is a worldclass innovation in the area of Industry 4.0, particularly additive manufacturing and internet of things (IoT) sensing, specific to what the project has achieved. Working with such an innovative team at Mineral Technologies is refreshing and shows that Australia can be a leader in adopting Industry 4.0 principles for global impact,” said Harvard.
One outcome that the team have already achieved is applying for a patent for IoT connectivity, which goes towards the project’s Industry 4.0 goals.
With IMCRC facilitating the project, the leadership of the program has been a collaboration between industry and the university, something that David Chuter, CEO and managing director of IMCRC, welcomed.
“This exceptional project takes industry-led research collaboration to the next level. Within a year we have seen Mineral Technologies and UTS form a team that ‘collaborates to innovate’ and deliver on milestones. Seeing a 3D printed version of their selected spiral model puts it into perspective,” said Chuter.
UNSW students push the potential for vacuum travel
Students from the University of New South Wales (UNSW) have been selected to compete in the 2019 Hyperloop Pod Competition. A subsidiary of SpaceX, Hyperloop attempts to create a new method of long-distance travel where people travel through vacuum tubes in pressurised pods, at speeds similar to aircraft.
The competition, held on July 21, judges participants by one criteria, maximum speed, including a successful deceleration to finish within 30m of the end of the milelong vacuum tube.
The team from UNSW had to condense their engineering process from the normal 18 months down to six, while competing against top universities around the world. In February the team were invited to go to the SpaceX headquarters in Hawthorne, California.
Last year’s winner, the Technical University of Munich, achieved a top speed of 467km/h.
In developing the project, the components used are largely off-the-shelf products, according to technical manager Francis McDonald.
“It’s such a simple idea, pretty much the best team is the one that goes fastest, but it’s also very complex, we’re dealing with vacuums, so we have to seal all our systems and that’s very interesting to play around with,” said McDonald. The team’s design connects the internal machinery to a chassis which is enclosed within an aerodynamic shell.
“While we want this to be aerodynamic, it has to be also aesthetic and can conform to the regular engineering requirements that you would need for a Hyperloop pod,” said UNSW Hyperloop structures lead Yasmin Zaman.
In addition to the ability to test their engineering skills, the competition provides an opportunity for the students to connect with engineers from other countries and students who have similarly attempted to create a pod that can innovate
The winners will be decided on one criteria, speed.
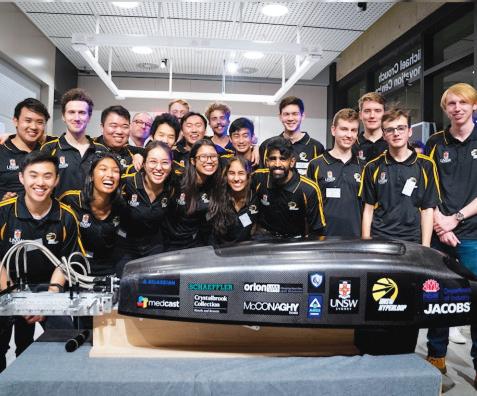
travel around the world.
“The people who do compete and make it through the multiple rounds of elimination are quite revered in engineering around the world,” said Zaman.
News@MM
Swinburne researchers train robots to relieve chronic pain
Researchers at Swinburne University, in conjunction with Infrared Robotics (IR), have developed a collaborative robot system that automatically treats soft tissue injuries in the neck, back, and head.
Based on an analysis of the patient through a thermal camera, the system uses a collaborative robot to apply targeted laser therapy to identified pain, known as “hot spots”.
“Unlike conventional industrial robots that operate in a cage, collaborative robots are designed to work alongside people,” said Dr Matt Isaksson, senior lecturer and project leader at Swinburne.
“They are power and speed limited so they can collide with people without causing harm.”
Dr Isaksson’s aimed to develop an automatic solution for safe robotic examination and treatment of patients experiencing chronic pain.
“Using the same technology used in cricket to show whether the ball has made contact with the bat, a thermal camera scans the patient and locates injuries and inflammation through identifying hot spots in a thermal image,” Dr Isaksson said.
“The locations of the hot spot are then sent to the collaborative robot that moves a low-level infrared laser into contact with the patient to perform treatment.”
The project has delivered a fully working prototype for automated photobiomodulation (PBM) therapy for chronic pain. This is a form of therapy that applies low-level lasers or LED lights emitting diodes to the surface of the body to stimulate and heal soft tissue. “Studies have shown PBM therapy to have positive effects on chronic pain symptoms,” said Dr Mark Rogers, a co-founder of IR Robotics and one of the Australian pioneers of PBM therapy.
“Introducing collaborative robots
Using cobots and thermal cameras to treat pain.
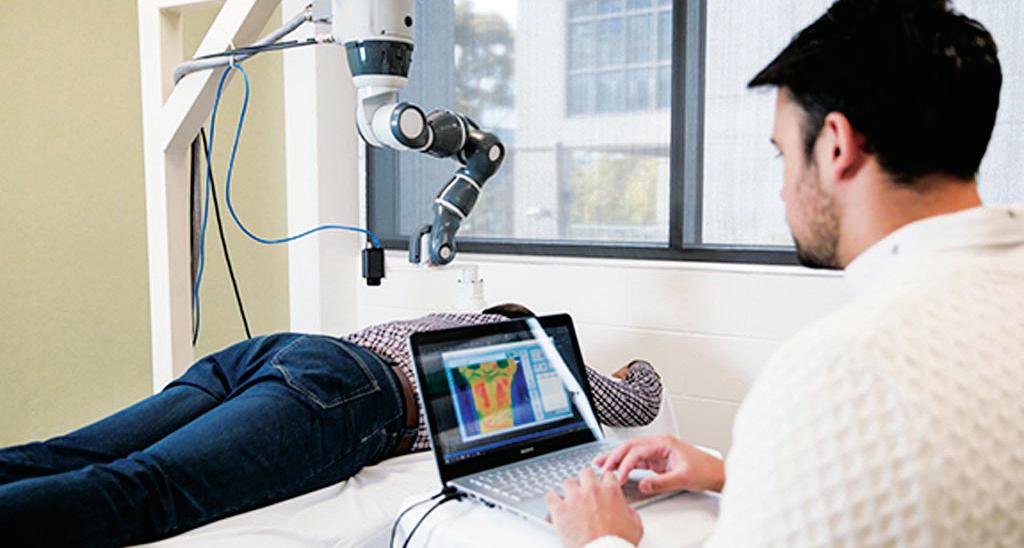
to deliver treatment has the potential to improve the precision of the therapy in addition to reducing costs involved. Building on Industry 4.0 technologies and big data analysis, the derived platform can self-adapt to provide individually optimal treatment.”
BAC Modular Workplace & Drawer Storage Systems Made and designed in Australia to Perfection
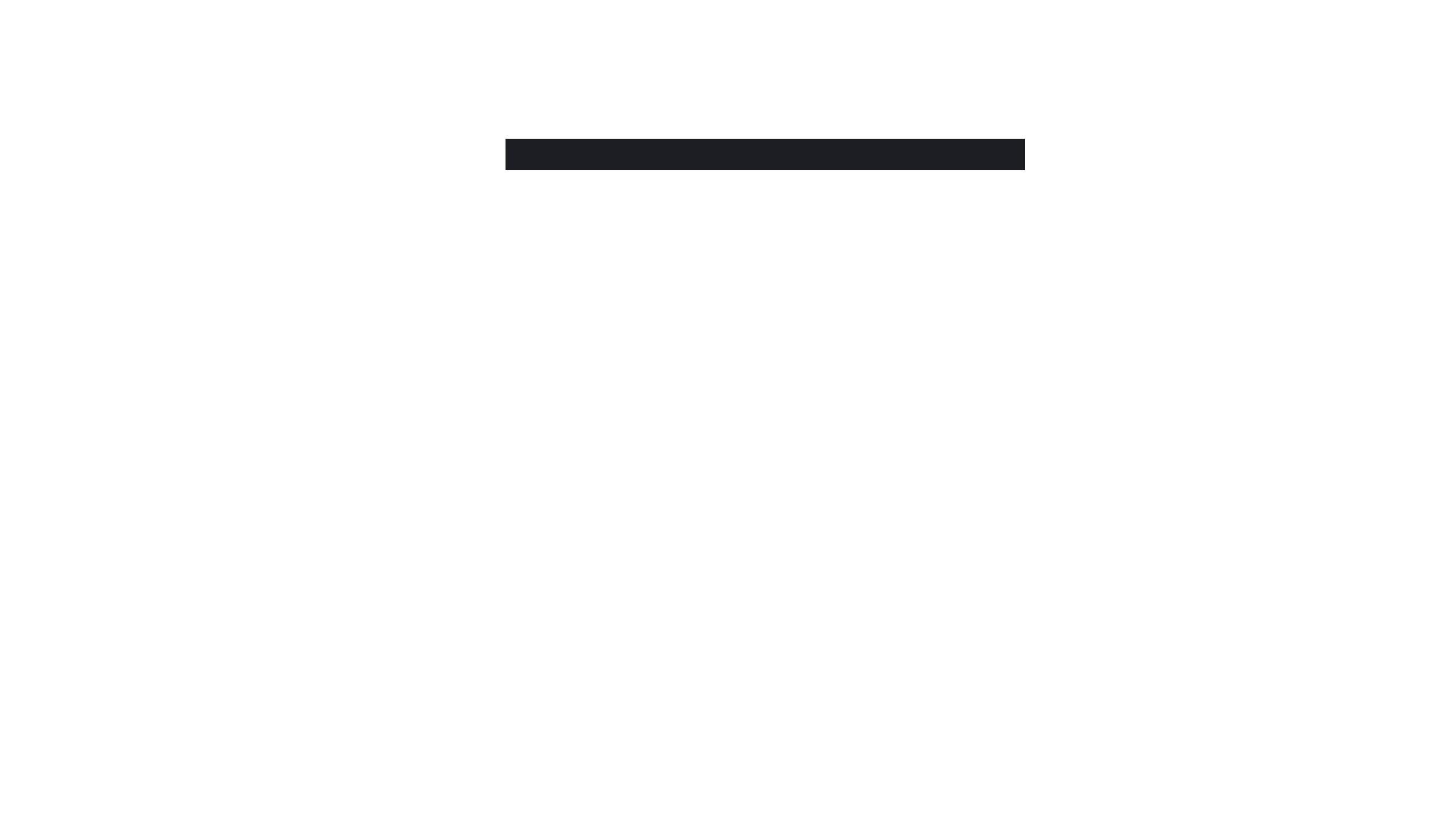
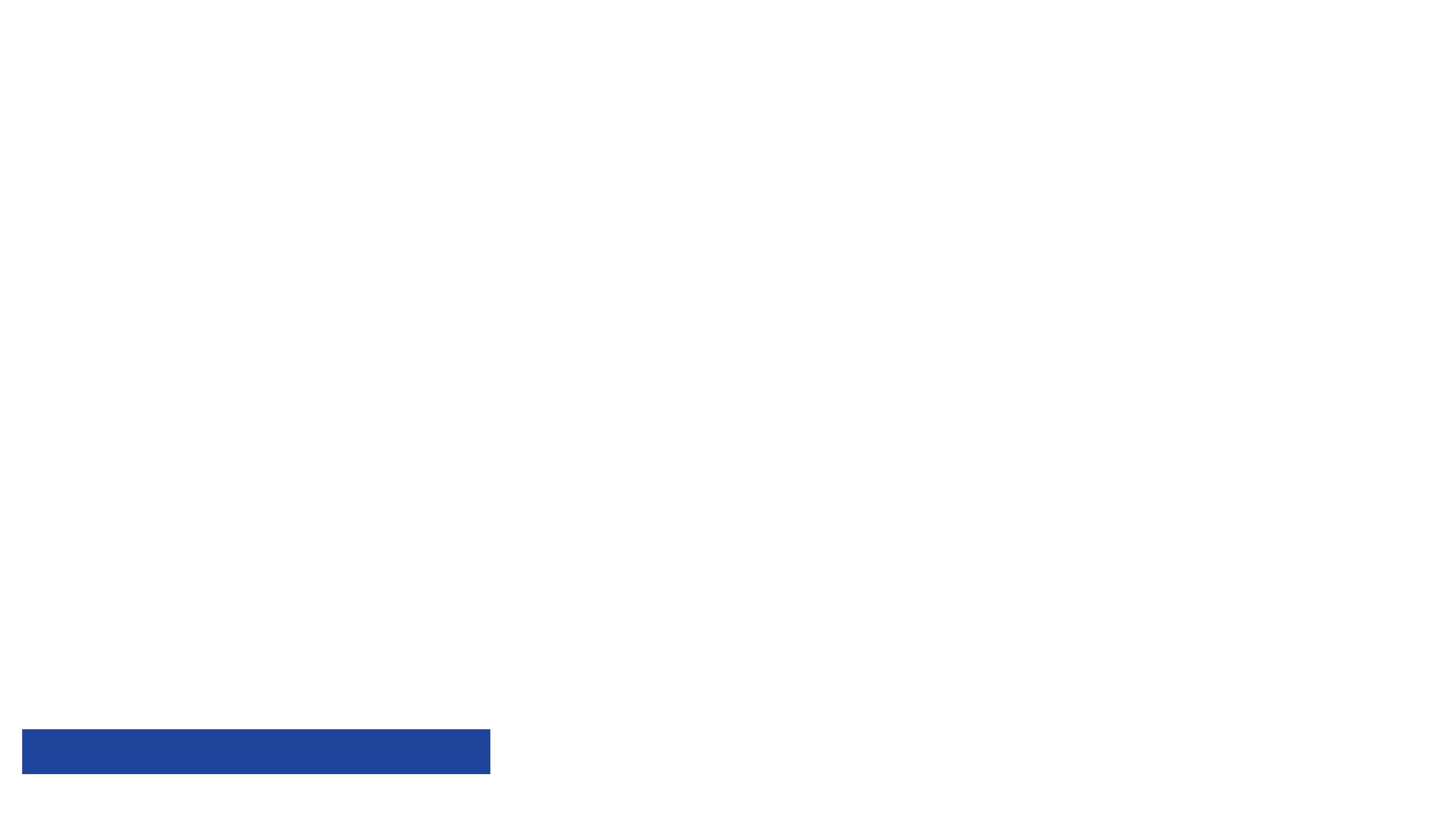
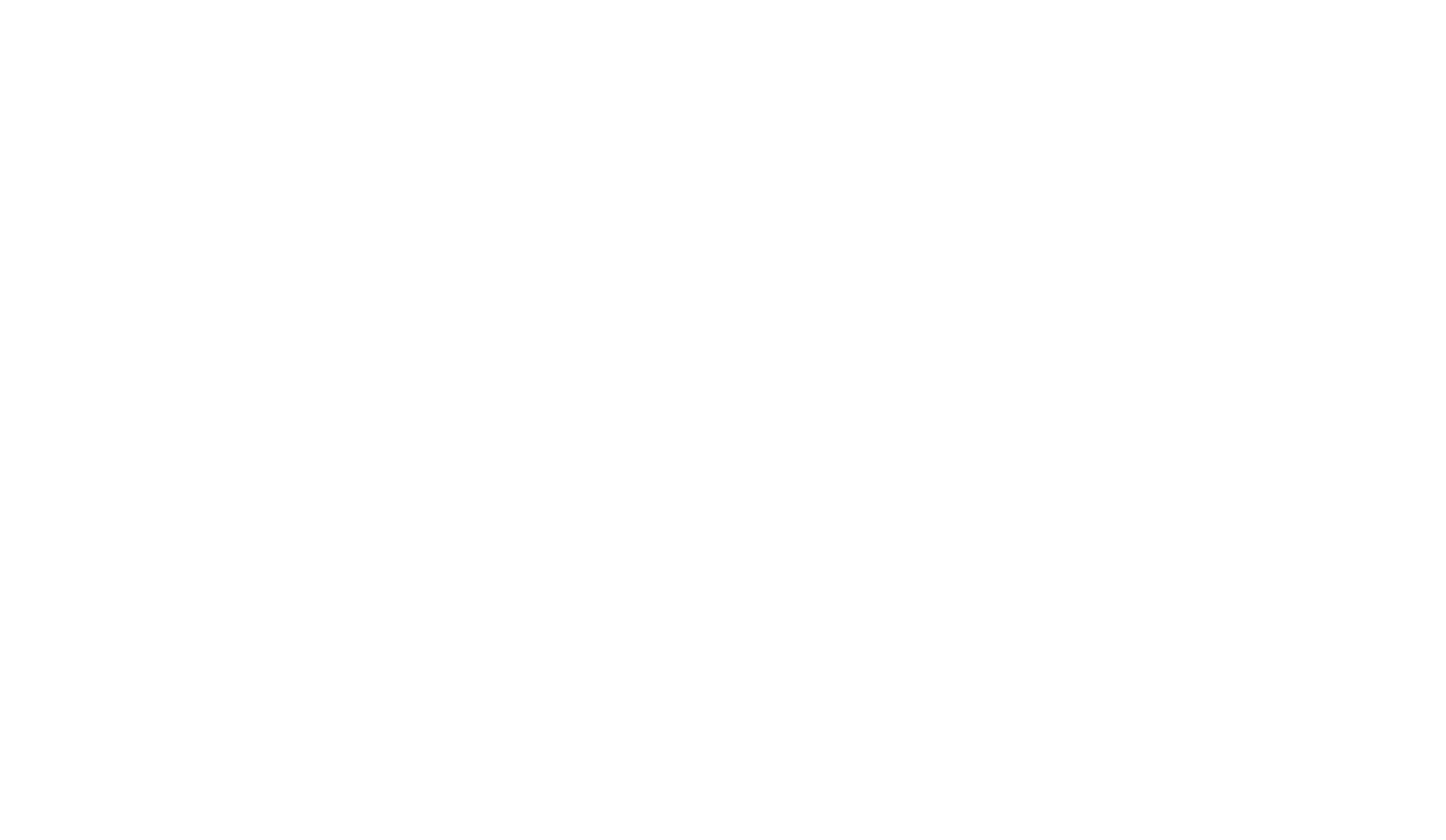
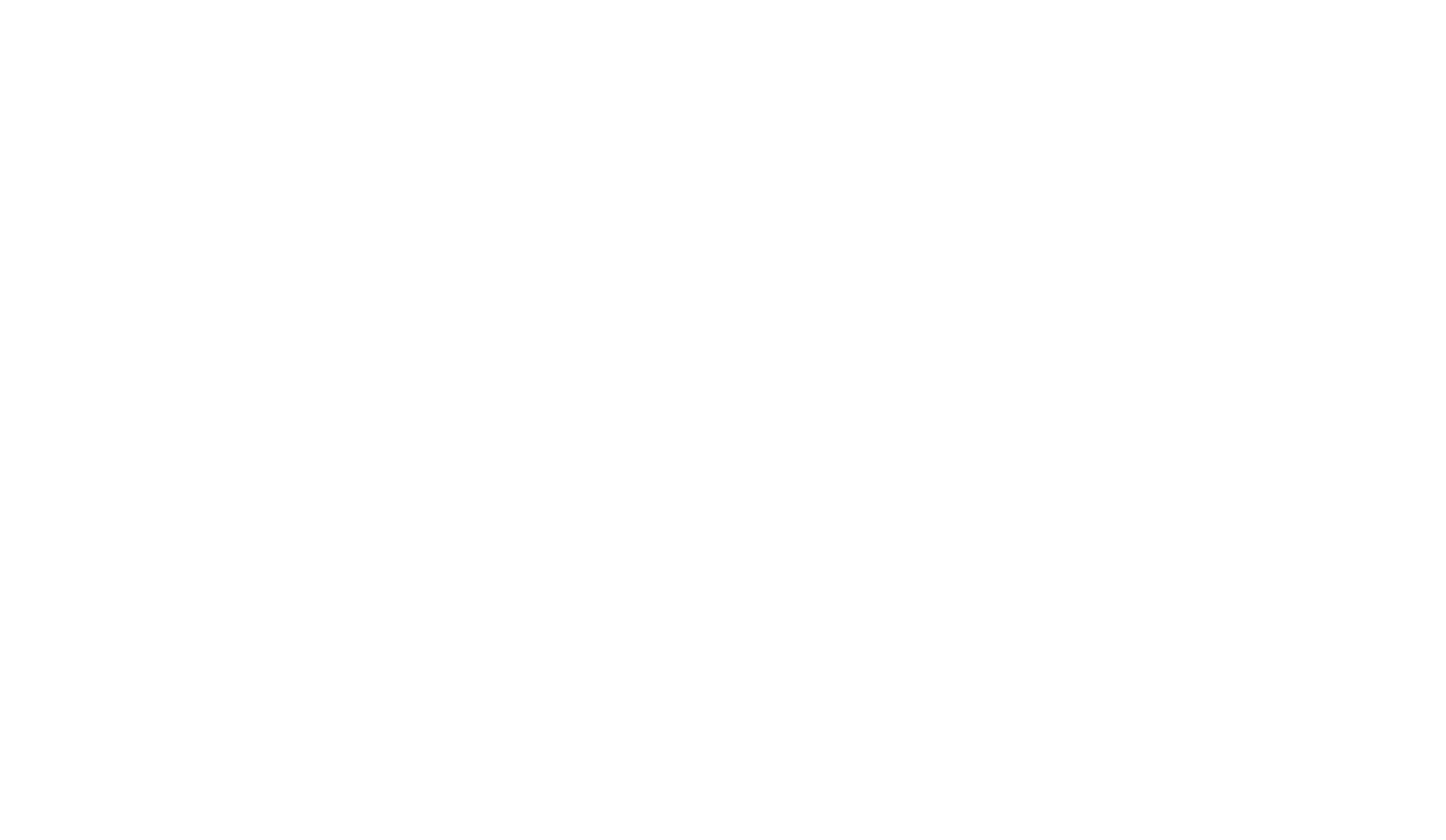
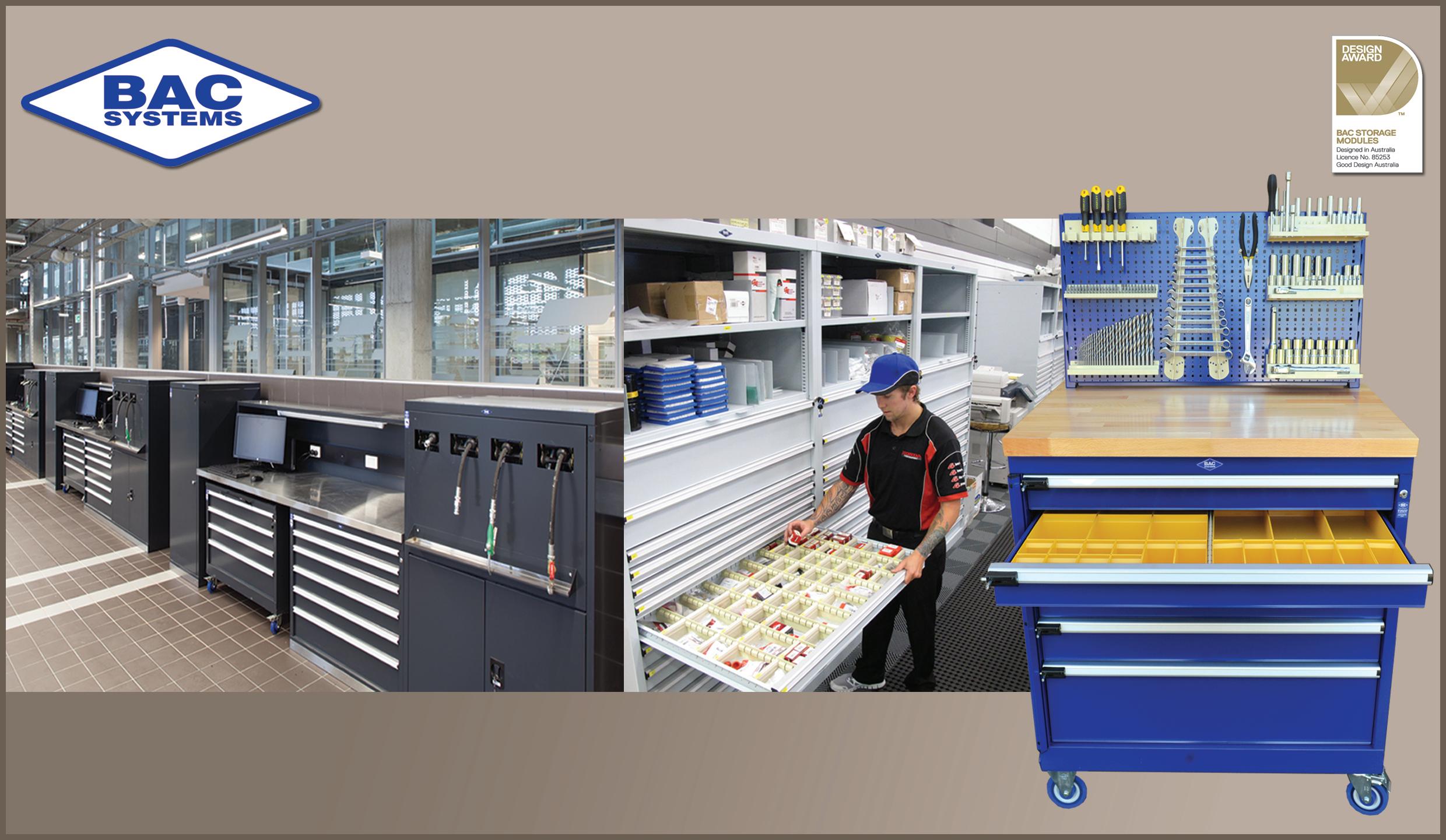
Order now the latest BACCatalogue online!
193-195 Power Street GLENDENNING NSW 2761 Tel: (02) 9832 2777 Fax: (02) 9832 3899 www.bacsystems.com.au
News@MM
Graphene extracted from eucalyptus trees
An international collaboration between researchers from RMIT University and the National Institute of Technology, Warangal (India) has led to the development of a new way to extract graphene.
The method derives graphene from eucalyptus bark and is cheaper and more sustainable than current synthesis methods, according to a statement from RMIT.
While the current cost of production stands at US$100 ($142.95) per gram of graphene, this new method could potentially reduce the cost to US$0.5 per gram. With such a lowered cost, new applications and industry uses could be developed for the material, without significant investment in research and development.
“Eucalyptus bark extract has never been used to synthesise graphene sheets before and we are thrilled to find that it not only works, it’s in fact a superior method, both in terms of safety and overall cost,” said lead researcher Suresh Bhargava.
Currently, graphene is renowned for its conductive abilities, with the material able to conduct heat and electricity 10 times better than copper. While being flexible and transparent, graphene is the thinnest and strongest material known to humans.
The new extractive method opens up the use of graphene for applications as diverse as flexible electronics, water filters, and bio-sensors.
An additional benefit of the eucalyptus extraction method is the lack of its reliance on toxic reagents, making it an example of “green” chemistry, according to professor Vishnu Shanker from the National Institute of Technology, Warangal. The graphene extracted from eucalyptus was tested in the
Eucalyptus bark provides a cheap source of graphene.
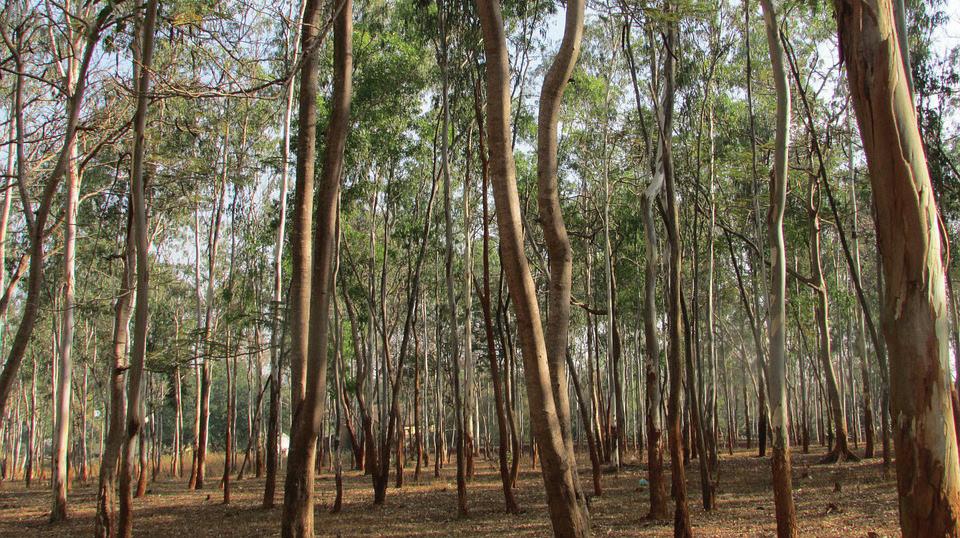
application of a super-capacitor and matched the quality and performance characteristics of graphene extracted in other methods, which rely on harmful reducing agents.
With eucalyptus trees abundant in Australia, as well as around the world, while also being one of the ten quickest trees to grow, graphene could be created with ease.
“Graphene is a remarkable material with great potential in many applications due to its chemical and physical properties and there’s a growing demand for economical and environmentally friendly large-scale production,” said Bhargava.
Researchers look for ways forward in advanced materials
A two-day workshop at the Australian Institute for Innovative Materials (AIIM) focussed on the future of opportunities in materials science.
The use of quantum mechanics has the potential to enable the fabrication of new materials and devices, according to a statement released at the end of the workshop. Held by the Institute for Superconducting and Electronic Materials (ISEM) at the University of Wollongong’s Innovation Campus, the meeting was entitled “Workshop on Surface Science and Technology” and brought together researchers from fields that contribute to current advances in material sciences, including physics, chemistry, photonics, and biology. Currently, ISEM researches how to create batteries used for electric vehicles and energy storage, superconductivity for electrical and medical devices, and nanostructured materials.
The event highlighted the opportunities that research in this area could create, noted associate professor Yi Du.
“These workshops are an invaluable opportunity to exchange ideas and seek broad collaborations as we look for ways to solve fundamental challenges that will enable a new generation of electronic devices that are more efficient, smarter, and more compatible with our lives,” said Du. One of the areas canvassed were new quantum materials for lowenergy quantum electronics. While existing electronic technologies in this field are unable to be adopted broadly because of their high cost, new materials that bypass current limitations could allow for the integration of large-scale super performance electronics in emerging quantum computers and devices.
“All of these new devices will require not only revolutionary materials to laws of physics and chemistry, but new ways to make those materials that is also cost effective and scalable,” said Du. A statement on the workshop
Researchers gathered at the Australian Institute for Innovative Materials.
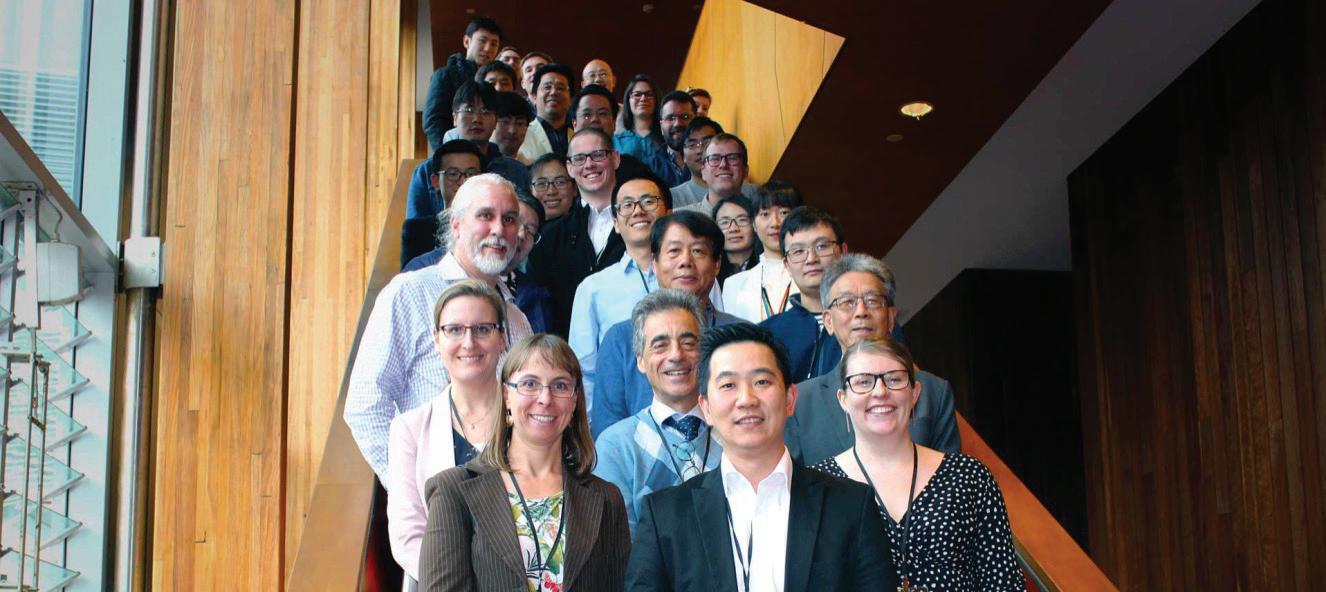
described how a critical part of the discussion was how theoretical or experimental research in this area could be applied in a commercial setting.
ISEM is one of a handful of multifunctional materials facilities that can create the processes and devices needed to scale-up labbased findings to allowed them to be applied commercially.
News@MM
Textile coating technology takes the next step
Representatives of Deakin University, textile technology company Xefco, and Proficiency Contracting have agreed upon a joint project for advanced coating technologies that will improve durability for textile coatings while reducing energy, water, and chemical consumption.
The $3.4 million project will be supported by the Innovative Manufacturing Cooperative Research Centre (IMCRC) and was developed, tested, and manufactured in Australia with the assistance of a local network of manufacturers.
The atmospheric plasma coating system developed by Deakin’s Institute for Frontier Materials (IFM) and Xefco reduces the costs and complexities of current coating equipment. The project announced this week will allow for the technology to emerge from the lab to a point at which it is commercially viable.
The coating will help make textiles resistant to water, absorbent, flame retardant, or odour free, according to IFM senior research fellow in plasma Dr Weiwei Lei.
“Thanks to support from our partners and IMCRC, we will now aim to improve and optimise the functional coating process to get this lab-scale technology ready for production testing at a textile mill and global commercial use by 2021,” said Lei.
While textile coating has been a less sustainable part of the production of textiles in the past, this technology reduces the environmental footprint of the process.
Created through a collaboration of research institutions and industry, the application of this
Coatings that improve durability are being developed.
technology has the potential to expand Australia’s capability in the manufacture of textiles, said CEO and managing director at IMCRC, David Chuter.
“The next decade will be about innovative textile manufacturing
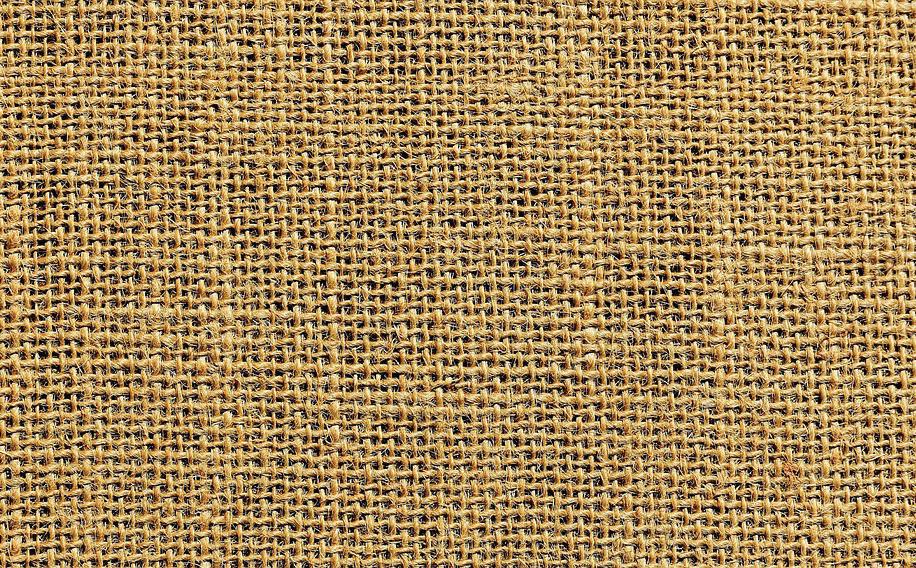
technologies and processes that are environmentally friendly and resource-efficient. The novel atmospheric plasma system that Xefco and IFM are developing will set the path for the future viability of the industry,” said Chuter.
OPEN UP YOUR WORLD
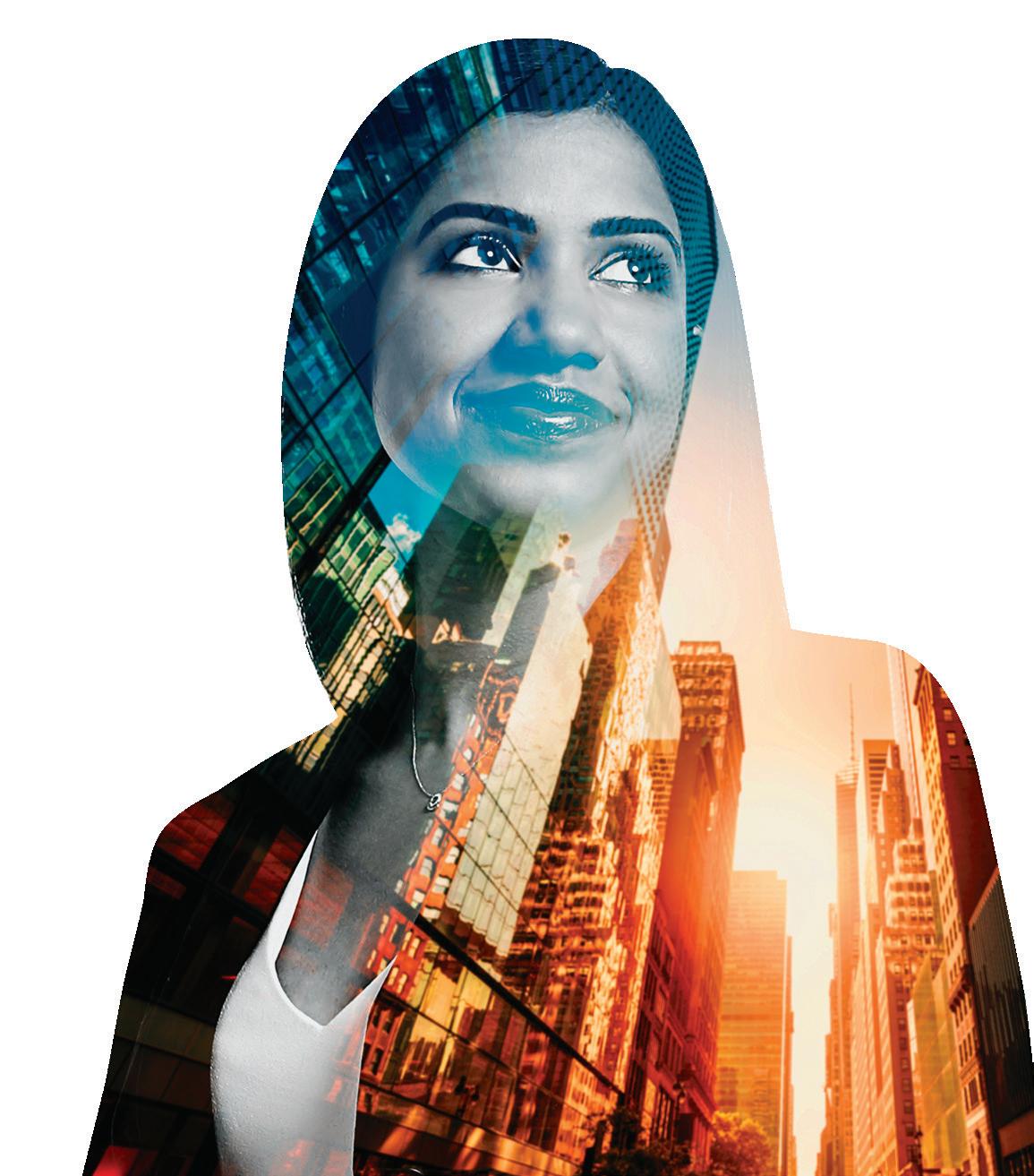
Uncover untapped PhD theory and discover knowledge that can see your business innovate further and expose new possibilities. See how a project with APR.Intern can expand the world you work in and influence the future.
News@MM
Federal government agency steps up support for medical manufacturing
The Australian Trade and Investment Commission (Austrade) is seeking to showcase the potential of medical manufacturing in Australia to encourage international investment. Launching a new digital health website, Austrade highlights Australia’s attractiveness as a location for developing, testing, and launching new medical technologies.
Denise Eaton, senior advisor at Austrade noted that Australia is inherently primed for success in medical innovation.
“Our background – in terms of vast distances, remote settlements, and a multicultural society – means we have a tradition of having to innovate,” said Eaton.
According to Austrade, its site has listings, case studies and data on subsectors such as telemedicine, precision medicine and genomics, big data and artificial intelligence, digital records, and virtual reality.
Support for the development of new pharmaceuticals will be channelled through the $20 billion Medical Research Future Fund (MRFF).
The MRFF augments Australia’s existing role in the production of new medicines, which includes 50 clinical research networks and bio labs which conduct 1,300 clinical trials a year.
The production of new medicines in Australia draws upon Australia’s creative IT sector and the nation’s history of producing Nobel laureates and devices like the cochlear implant. Eaton pointed out that there is an encouraging increase in outlay on medical manufacturing.
“Investment from venture capitalists more than doubled between 2016 and 2017. What’s more, we’re seeing a significant increase in interest from Asian investors – especially in medical science technology,” said Eaton.
Medical manufacturing in Australia in the past has led to the development of live-video equipment for real-time remote examination and diagnostics, integrated into electronic health records. Eaton noted the example of Visionflex, which has pioneered this technology.
The new website also highlights the medical manufacturer Anatomics, which uses 3D printing to help surgeons create customised implants and has in the past built a 3D printed titanium sternum and partial rib cage.
CSIRO designs algorithm vaccination technique
In a paper accepted to the 2019 International Conference on machine Learning (ICML), CSIRO researchers have presented a new method of preventing attacks on algorithms and machine learning systems.
Similar in principle to a vaccine, the innovation is designed to limit the effectiveness of hackers who target algorithms that could drive cars, identify spam emails, or diagnose diseases.
For manufacturers who are wary of adopting algorithms due to the risks associated with a system infiltration, whether it leads to the copying of proprietary information or a malicious shutdown, this technique from the CSIRO will help to ensure peace of mind.
CSIRO points out that with any new technology, securing it from outside interference is core to its effectiveness, and manufacturing software is no different. In 2017, Italian researchers in collaboration with cybersecurity firm, Trend Micro, found that factory robots can be easily hacked due to lax safety practices.
The work by CSIRO attempts
The algorithm will vaccinate systems against cyber attacks.
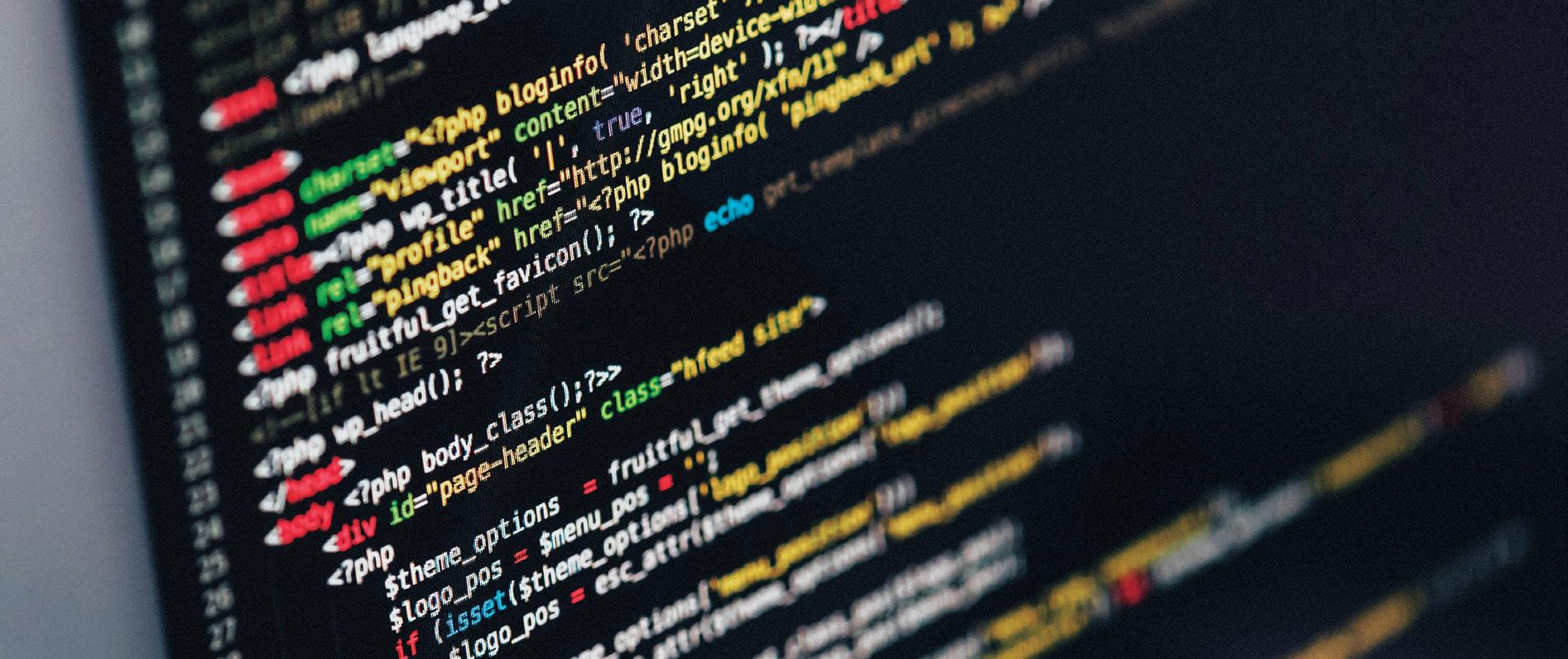
to counter hacking attempts that confuse an algorithm via adversarial attacks which trick machine learning models by inserting a layer of noise over an image. Hacking attempts in this style cause algorithms to misidentify the image, with potentially devastating effects. “Adversarial attacks have proven capable of tricking a machine learning model into incorrectly labelling a traffic stop sign as speed sign, which could have disastrous effects in the real world,” said Dr Richard Nock, machine learning group leader at CSIRO’s Data61, the data and digital specialist arm of the national science agency.
By preparing the machine learning algorithm by layering a weak version of a hacking attack over an image, the algorithm is able to learn from this minor layer of interference and respond to hacking attacks that introduce more complex disruptions.
According to CSIRO, while algorithms applied to the manufacturing sector promise great improvements in productivity and returns on investment, their benefits depend upon safety and security. With this innovation by CSIRO, there would be a safer future for AI.
“The new techniques against adversarial attacks developed at Data61 will spark a new line of machine learning research and ensure the positive use of transformative AI technologies,” said Adrian Turner, CEO of Data61.
News@MM
G20 puts forth agenda for energy transition and sustainable growth
Energy and environment ministers of G20 nations have adopted a statement outlining that the potential to transition to clean energy and sustainable environments depends upon improving business environments to encourage innovation and change.
The G20 is made up of 19 countries and the EU. Countries include Argentina, Australia, Brazil, Canada, China, Germany, France, India, Indonesia, Italy, Japan, Mexico, the Russian Federation, Saudi Arabia, South Africa, South Korea, Turkey, the UK and the US.
Held in the Japanese city of Karuizawa on the sidelines of the current G20 Summit in Osaka, the communiqué, published on June 15-16, identifies that in order to have a clean energy future, developed nations must collaborate to leverage competitive advantages.
The announcement demonstrates how in global policy-making arenas, innovation in clean energy technologies and energy efficient solutions are included as part of the solution to the challenges of climate change. Developing climate-resilient infrastructure will also be a priority, and the statement provides room for manufacturing enterprises to capitalise on this emerging need. The statement also outlines how governments globally will be looking to invest in and adopt new technologies that will enable them to meet their energy reduction targets. In particular, investment in technologies that will encourage the uptake of renewable energy, such as energy storage, smart grid technology,
Encouraging innovation is key to sustainability.
electric vehicles ,and demand side management are encouraged, presenting opportunities for manufacturing businesses involved in these areas.
The statement identifies the role of the private sector in working alongside government bodies to lead
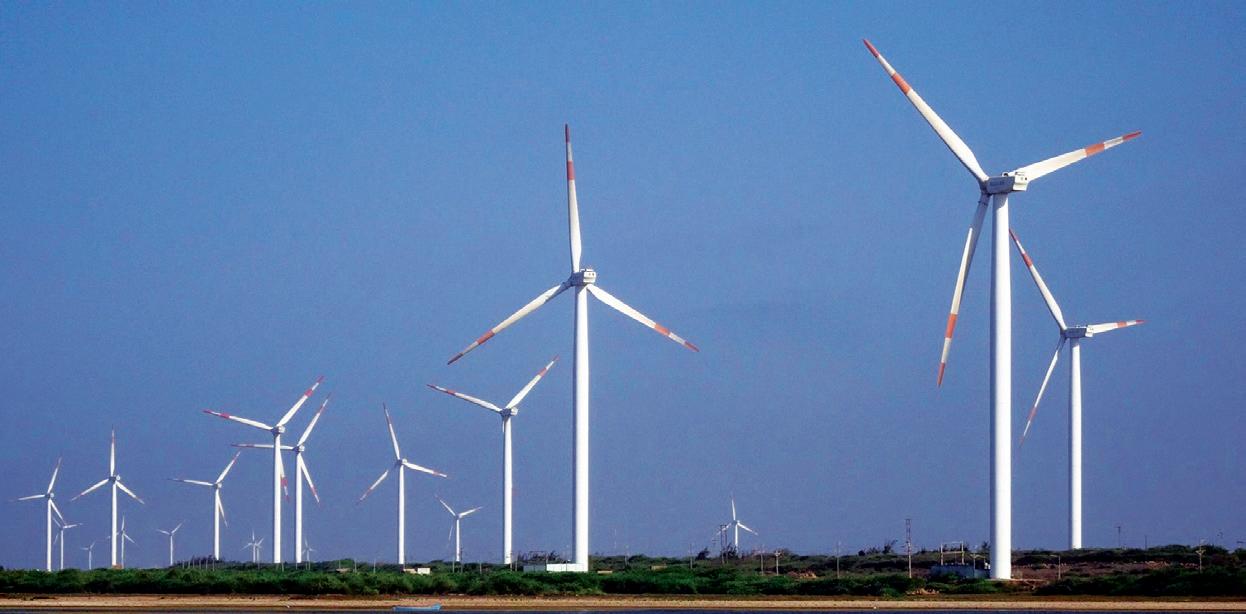
the transformation to a resilient, inclusive and sustainable future.
Governments, including Australia, are exhorted to improve resource efficiency, with the statement noting that “economic growth and environment protection can and should go hand-in-hand”.
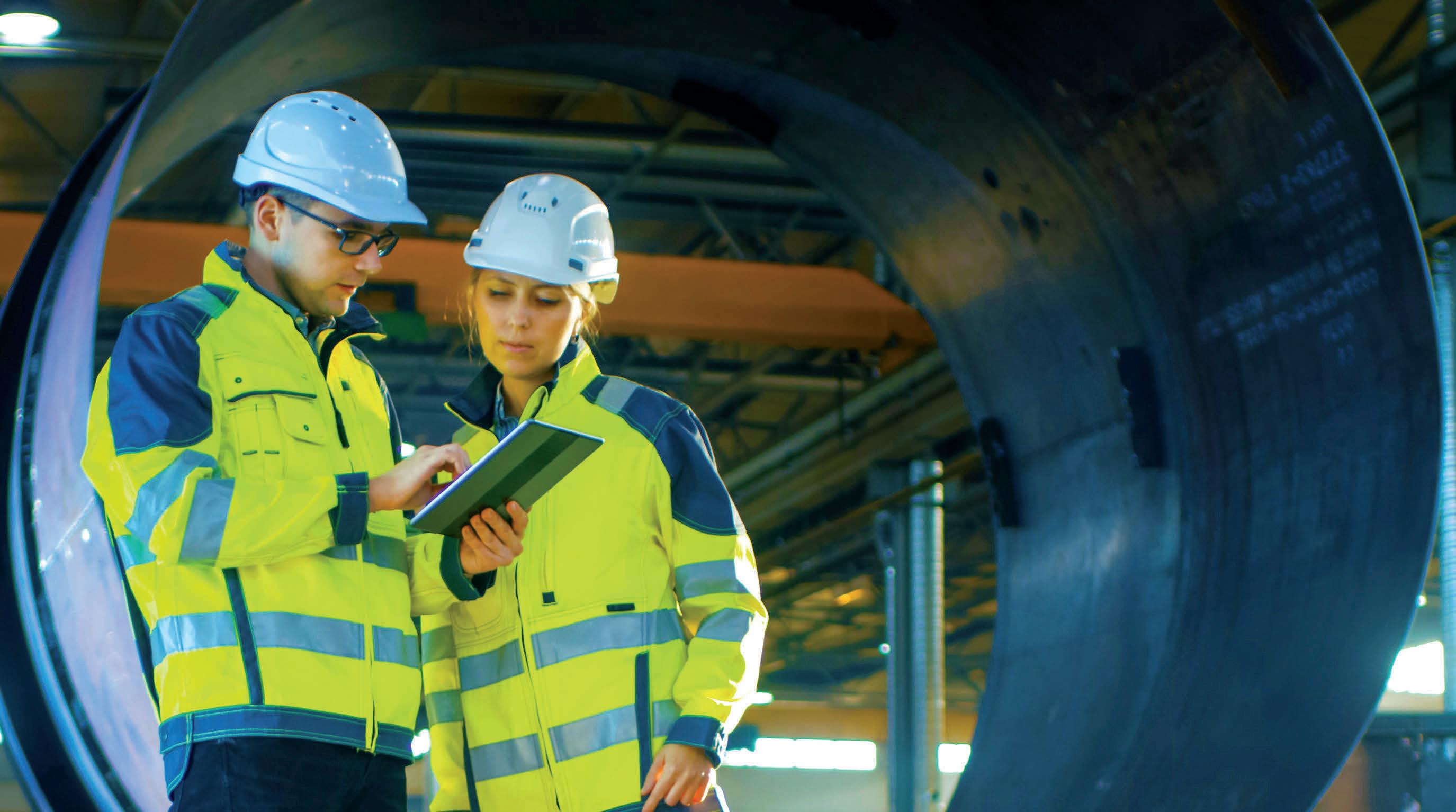
REGISTER NOW 22 AUGUST 2019 THE AUSTRALIAN SYNCHROTRON MELBOURNE Do you struggle to fill vacant positions? Concerned about the future of Australian manufacturing? Want to upskill your workforce with global-standard training? With the theme of Skills for the Future, the National Manufacturing Summit gathers leading representatives from all major Australian manufacturing stakeholders—to identify promising, pragmatic policy measures designed to support an industrial turnaround.
News @MM
Australian metal 3D printer expands worldwide
Australian 3D metal printing company Spee3D has developed the first metal 3D printer, called Lightspee3D, that can leverage supersonic 3D deposition technology.
Lightspee3D’s technology aims to manufacturing grade printing at production speeds. It also allows operators to print industrial quality metal parts in minutes.
“Typically, 3D printers of this size and complexity require up to two weeks to install and set up, however Speed3D printers can be installed in a matter of hours. We’ve had machines delivered at 9am and printing parts by lunch time,” said Byron Kennedy, co-founder of Spee3D.
In three weeks, Speed3D installed five industrial printers internationally, including at Australian National Manufacturing Week in Melbourne, Swinburne University, Fit Print Bureau in Germany, Rapid in Detroit, and the University of Delaware.
“The LightSpee3D printer we had installed is running great. It’s also easy to operate, Spee3D trained one of our staff who was then able
Spee3D machine at National Manufacturing Week.
to train other operators. The team are now using the machine every day,” said Larry Holmes, assistant director of Digital Design and Additive Manufacturing.
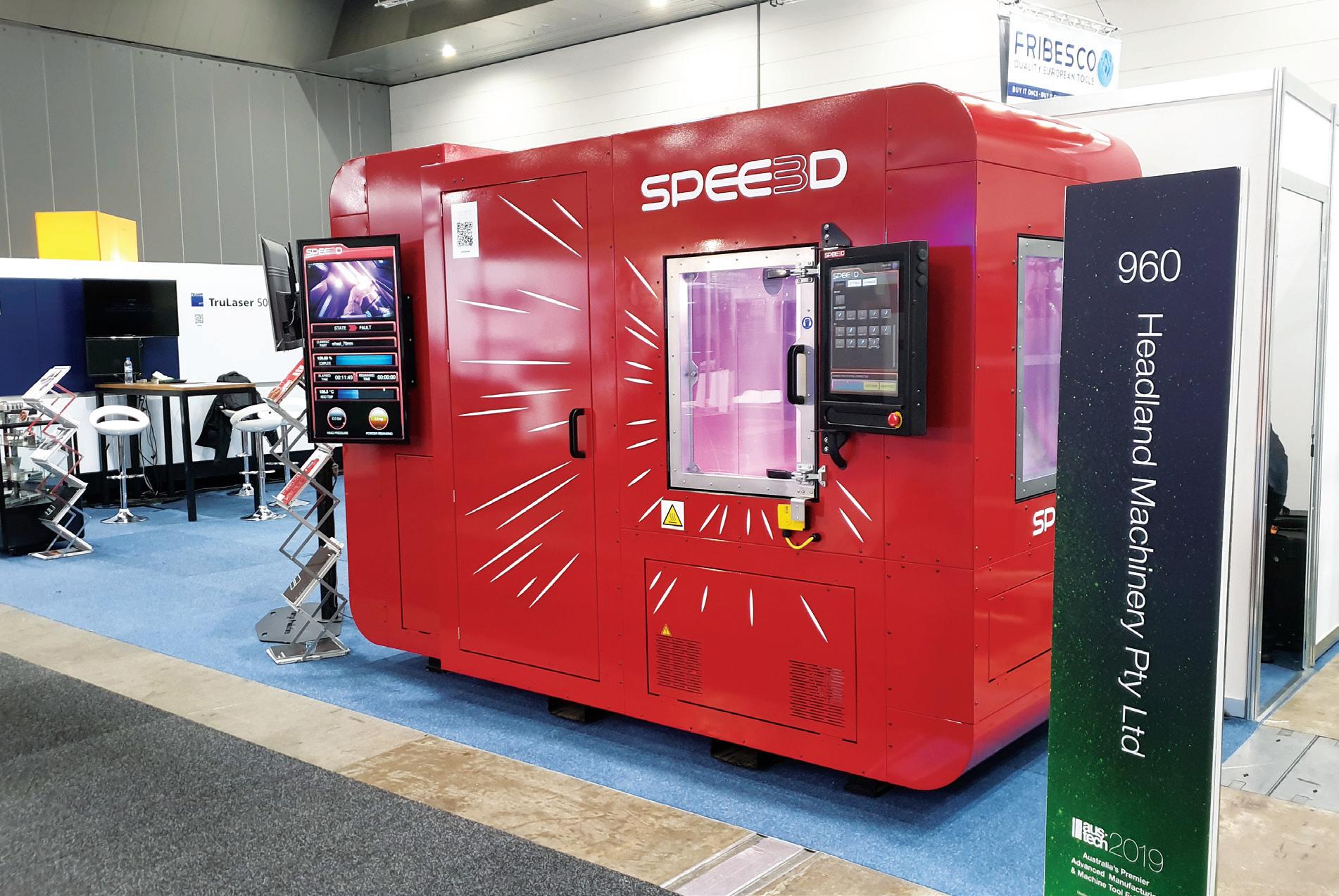
To encourage others to take on the challenge of quickly printing metal parts and components, Spee3D announced the “Supersonic 3D Printing Design Challenge”. The competition is open to 3D printing enthusiasts and communities worldwide and judges the best application designs that use Spee3D’s technology.
The federal government creates innovation lab for building industry
Australia’s manufacturing, building, and construction sectors will receive up to $2 million as part of the federal government’s Advanced Manufacturing Growth Centre (AMGC) to establish a collaborative innovation lab. The new lab will help manufacturers design new prefabricated buildings that are ecofriendly, affordable, and can reduce construction time.
Karen Andrews, Minister for Industry, Science, and Technology, said the new lab will support a wide range of buildings, including tiny houses and larger homes while strengthening Australia’s position in the global building market.
“This sector is starting to build significant momentum and currently represents three to five per cent of Australia’s $150 billion construction industry,” Andrews said.
“This share could grow to 15 per cent by 2025, creating 20,000 jobs and adding $30b to our economy.”
The prefabricated building industry includes modular houses and offices created in a factory setting and then transported directly to site.
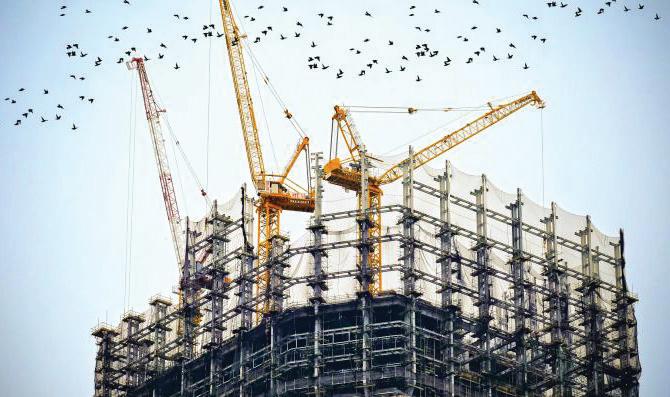
The innovation lab will support the prefabricated building industry.
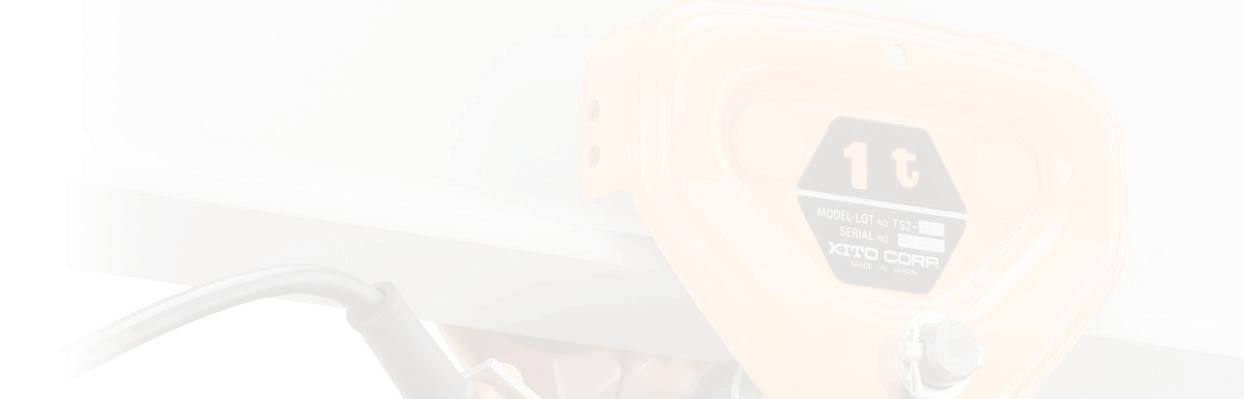
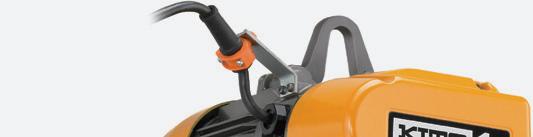

KITO EQ ELECTRIC CHAIN HOIST LEADERS IN CUSTOM LIFTING SOLUTIONS
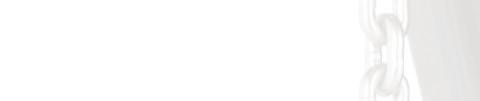
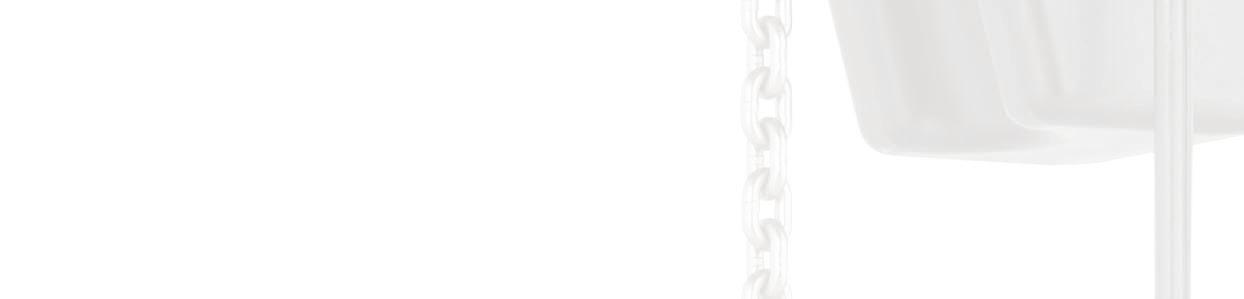


1300 792 262 | www.pwbanchor.com.au
HEAD OFFICE & MANUFACTURING PLANT Address: 441 Grimshaw Street, Bundoora, VIC 3083 Tel: 1300 792 262 Fax: 03 9467 7290
QLD OFFICE Address: 1/119 Bandarra Street, Richlands, QLD 4077 Tel: 07 3375 1288 Fax: 07 3375 8241