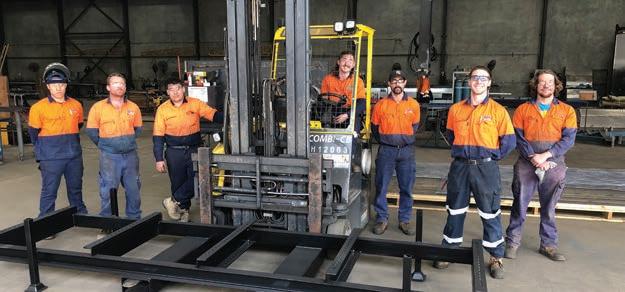
4 minute read
Lifting Solutions
from MM Aug 2020
by Prime Group
Saving time and improving efficiency
Combilift forklifts have increased productivity and improved processes for many Australian steel manufacturers. Watkins Steel operations manager Matt Hunter speaks with Manufacturers’ Monthly.
Watkins Steel has been a traditional manufacturing business since 1968.
MAKING the change from using traditional gantry forklift to Combilift has made life a lot easier for Watkins Steel operations manager Matt Hunter.
The company is a Brisbane-based steel sub-contractor, specialising in structural steel and metalwork fabrication.
Operating since 1968, it has serviced clients in the building, mining, and construction industries throughout Brisbane and south-east Queensland. Watkins Steel provides services to complete a variety of projects across multiple industry sectors. These include residential, education, health, retail, industrial, commercial, mining, landscaping, and fit-out refurbishments.
The business was founded in 1968 by Des Watkins Senior, and in 2004, his son Des Watkins took over the business.
“We have been a traditional steel fabrication business the whole time, but what sets us aside now is the innovation and the equipment that we utilise to make our business successful and a little bit different to a traditional steel fabrication business,” Hunter said.
Up until June 2019, it was operating out of one facility in Banyo, Brisbane, and the difficulty at the time was the bottleneck caused by the unloading and loading of trailers.
“We would have four trailers waiting outside our premises and a truck would take up to three hours to unload, using the traditional method of unloading steel items using overhead gantry cranes,” Hunter said.
The company now has 18 people working on a separate site since acquiring another premises in December 2019.
“We have invested in two Combilifts and leased a Combilift C6000 forklift, another six-tonne Combilift forklift, which we utilise to load and unload vehicles on a hard-stand concrete floor outside the warehouse but not outside the facility,” Hunter said. “We also have a Combilift CB, a smaller threetonne forklift, which is very much based on the design of a traditional counterbalance forklift, but with the option to drive sideways.”
Hunter said with steel manufacturing, products are often very long, and with tight workspaces around the fabricators, and there is no space to move sideways with traditional cranes.
The Watkins Steel Four Step Process
The Four Step Process, an awardwinning concept developed by Watkins Steel director Watkins Snr, has been implemented to set the business apart from other traditional steel fabricators.
It is a unique digital workflow that links an entire steel fabrication and installation process for a project from start to finish, and factors in data such as steel detailing, processing, and installation.
The company created the digital workflow by investing in a series of technological equipment that could integrate with Tekla Structures Software for steel detailing.
“It involves 3D laser scanning the construction site, and the work area that we’ve been asked to supply steel for. The scanner captures the images of all the hard fixtures on the job site,” said Hunter.
“The second step in the process is the Tekla Structures Software, which is designed to deliver a 3D image of the steelwork that needs to be manufactured, which visualises for the builder or the customer.
“The Combilift comes in at the third step, and that is the raw processing of materials. The NC1 files, which are developed from Tekla software, are also passed through the third step, and that’s where a lot of the automation comes in through our investment in Voortman equipment.”
The Voortman V808 coping machine processing equipment cuts the material to length, then drills and etches the location for fitting members. A coping robot completes the complex mitering of all hard-todo projects that would normally be done by a fabricator with a traditional oxyacetylene torch. The Combilift is used to prepare the material to go into the processing equipment.
Improving safety and saving time
Optimising floor space and looking after the safety of workers have been a priority for Hunter in using Combilift machines.
“I’ve developed large storage racks in the new facility, so now I store material vertically, whereas I couldn’t do it before with a traditional overhead gantry crane,” he said.
Before, the company would have to store all the material on the floor, and other floor space was utilised by the fabricators. Using the Combilift forklift now, the workers rack material, so the company stores material vertically, whereas it couldn’t do that with the overhead gantry cranes. All manufactured materials are now stored outside.
“We’re lucky in Queensland that we have such good weather and in turn we utilise the space just for processing and fabrication, not storage of either complete projects or ready-to-be-manufactured projects,” Hunter said. “We’ve created a safety corridor and that has improved our safety. With the bulk of our loading being done outside, we don’t have staff outside. It’s just the forklift and the truck, and the driver stands in a safety zone away from the area of unloading.”
For more information please visit https://combilift.com/en and www.watkinssteel.com.au
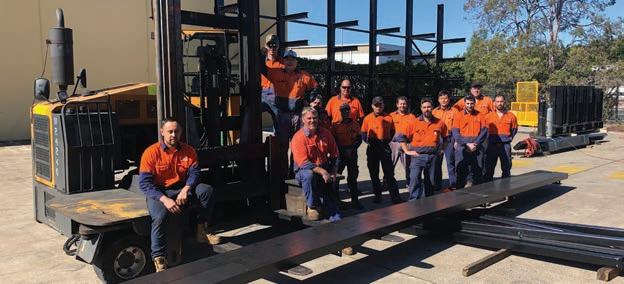