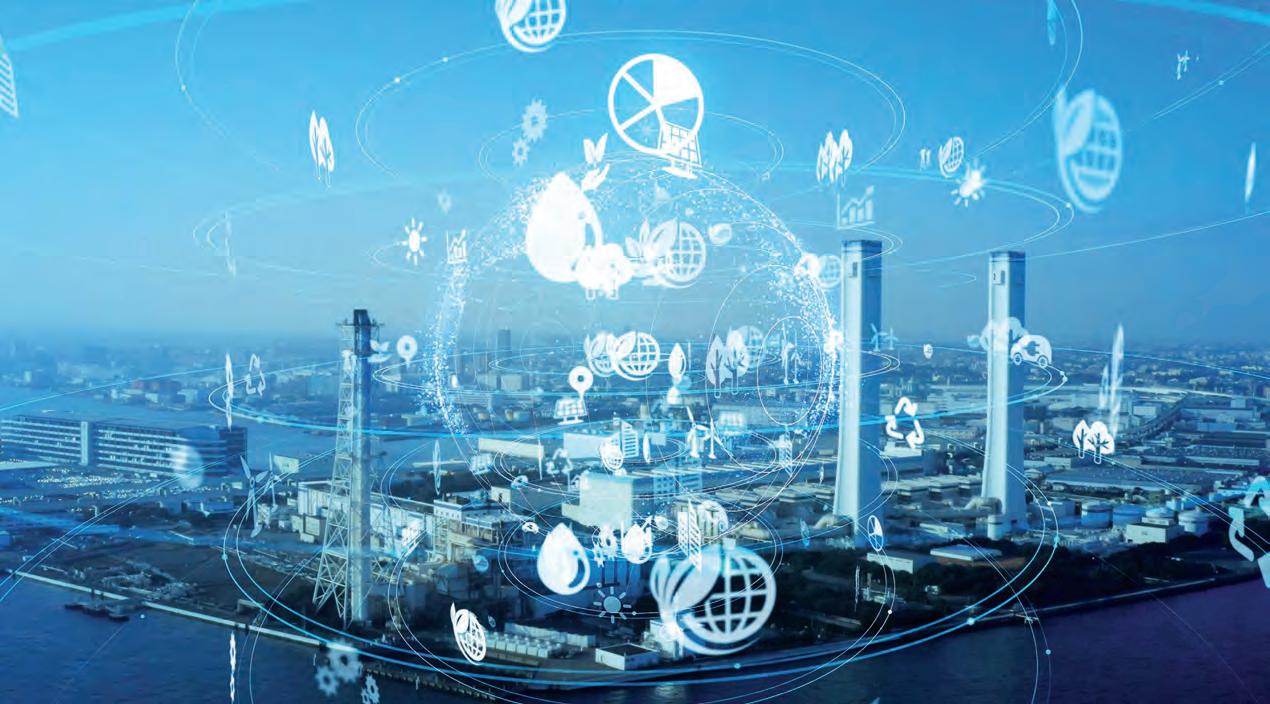
2 minute read
Editor’s Note
Comment
SYED SHAH – Managing Editor, Manufacturers’ Monthly
Sustainable manufacturing for the future
LOOKING back a couple of decades ago, the general manufacturing industries in Australia were more concerned with throughput and upskilling. Let’s not get it wrong – these are still right up there on the wish list, but trends related to sustainability were not popular until 10 years ago when rising fuel and energy costs became a concern. Back in those days, safety, continuous improvement, and globalisation of locally manufactured products were the greatest concerns. Today, these still are, with a caveat – the impact on the environment, which is something of great concern and unavoidable.
Attention to responsible energy and water usage became dominant in the past few years, and the term sustainability has been widely featured in Manufacturers’ Monthly over the past couple of years featuring interviews with top scientists in varsities like Dr Julia Ciarlini Junger Soares and her work with electricity to clean up heavily polluted wastewater streams as well as electrical and electronic manufacturer Tritium who are pushing forward with promoting electric vehicles on to roads. In short, there’s been no stopping the sustainability force ever since.
Australia’s climate policy, under the Paris Agreement, is to reduce emissions to below 26-28 per cent of 2005 levels by 2030 and from a manufacturing perspective, it covers a diverse range of activities: from metal production to the food and beverage industry, and everything else.
At climate summits like COP26 or the Paris Climate Accords, targets about decarbonisation are usually made and while there are sectors of the economy that might be relatively easy to carry out decarbonisation, there are those at the other end of the scale whose many industrial activities are firmly towards the difficult end. For example, in the heavy industry, there might be certain processes in the manufacturing chain that might prove more difficult or simply impossible to electrify with existing technologies, and it might take years of research and innovation before there is a breakthrough for a reasonable sustainable solution for carbon capture and storage of those processes.
Currently, there are low energy manufacturing techniques, increased recycling in manufacturing, or what is known as remanufacturing. With remanufacturing, costs can be reduced, raw materials saved, and energy and water can be kept to a minimum.
Furthermore, a business can potentially also save money by reducing the amount of waste to be disposed of.
There are also other alternative technologies that are no doubt crucial for the decarbonisation process like wind turbines and electric vehicle batteries – but with the existing level of technology at hand, expend high levels of resources and energy in their production. In other words, the costs are still a lot higher than what we would like it to be. Can they be designed in such a way that they can easily and cheaply be repurposed in the future? This would reduce emissions, resource extraction, and cost.
In this edition, we speak to Century Yuasa who supplies the Australian automotive market with more than 1.5 million batteries every year – and they have found techniques that could point the battery manufacturing market in the right direction in terms of manufactuing and sustainability.
WHAT WOULD A POWER OUTAGE COST YOUR BUSINESS?
WIDE RANGE OF GENERATORS FROM 9 TO 4,600 KVA QUALITY EUROPEAN MADE RELIABLE, EASY TO MAINTAIN AUTOMATIC TRANSFER SWITCH IN STOCK $ READY TO DISPATCH
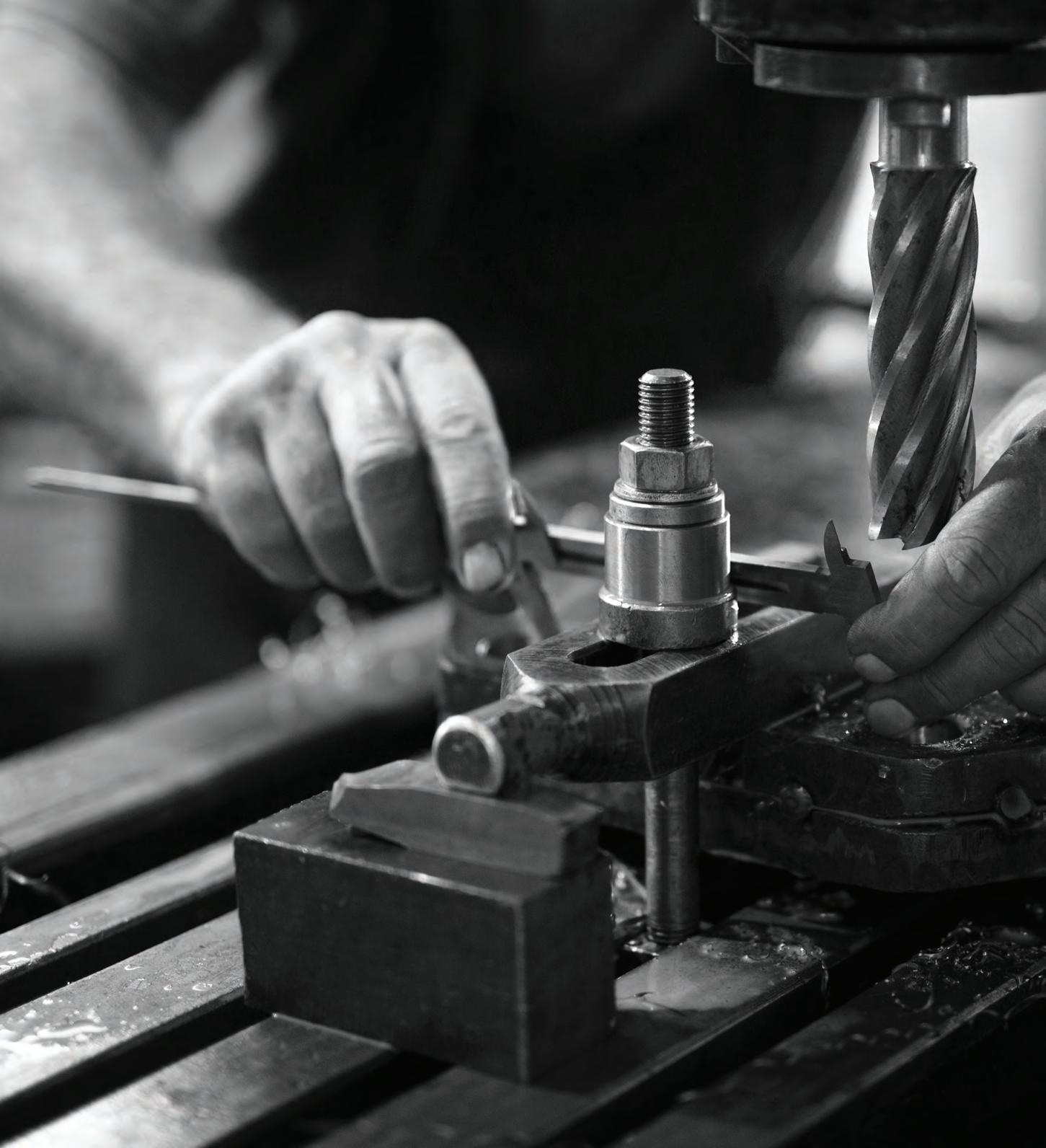