
20 minute read
HINO AIMS HIGHER
HINOAIMSHIGHER
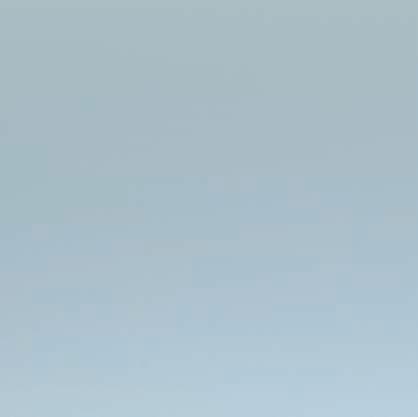
Following extensive updates to its light and medium-duty line-ups, Hino has previewed a vastly upgraded range of 700-series heavyduty models set to hit the market in the next few months. Advanced safety systems, improved and expanded powertrains, and new configurations are all part of a significantly stronger assault by a brand with ambitious plans for a bigger bite of the heavy-duty business. Steve Brooks reports
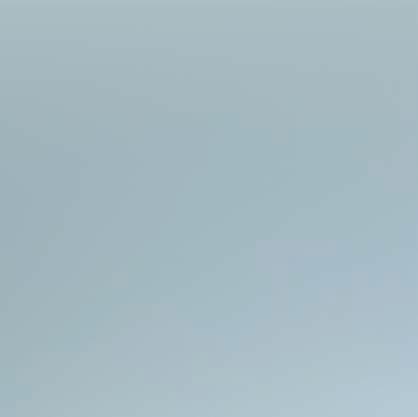
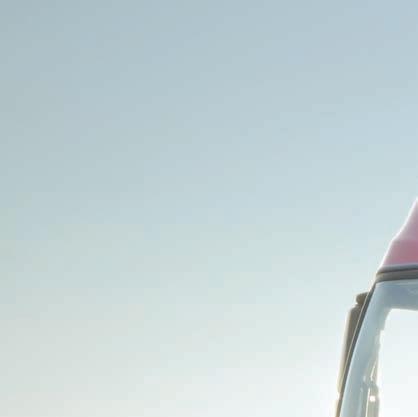
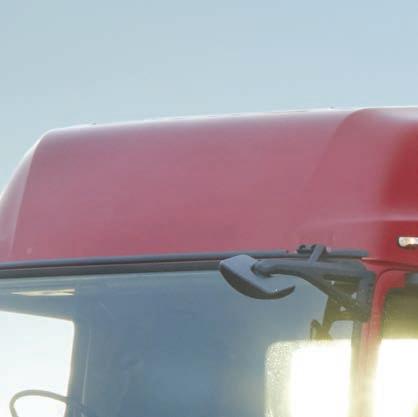
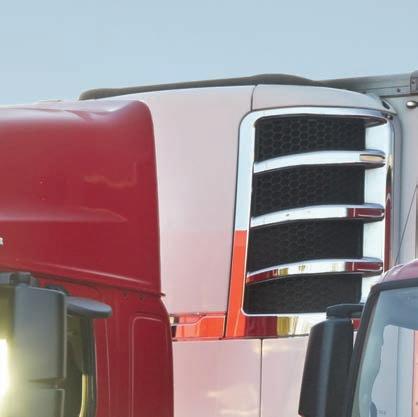



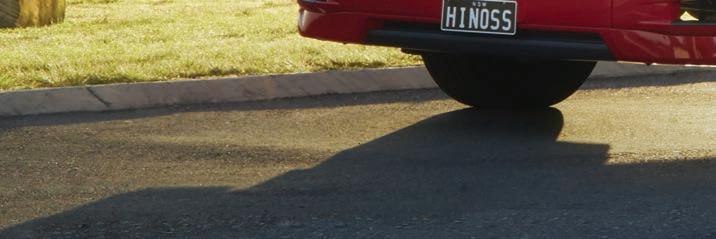

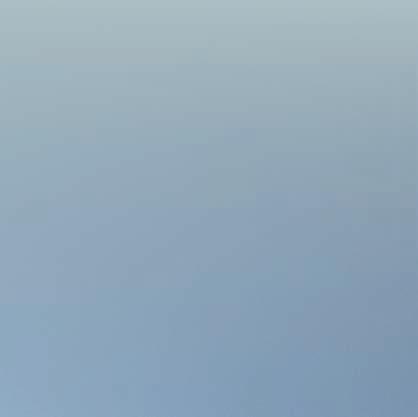

IT WAS no surprise that a major upgrade of the Hino 700-series heavy-duty range would follow much earlier updates to its 300-series light-duty and 500-series mediumduty models.
What did surprise, however, during a recent preview of the latest heavy-duty hopefuls was just how far Hino has gone in its bid to make the 700-series a far more competitive and appealing line-up and, in the process, provide a platform entirely capable of challenging European competitors as well as its Japanese rivals.
Have no doubt, on first impression this is a heavy-duty line-up far beyond anything Hino has ever offered before in any weight class. Moreover, while company insiders say it’ll be three or four months until we get the chance to climb behind the wheel, there was enough to see and hear at a static display in Sydney to predict a bold new appreciation for the Toyota-owned brand’s heavyduty credentials.
Similarly surprising, though, was Hino’s somewhat strange decision to retain peak power of the 700’s reliable 13-litre engine at the current peak of 480hp (358kW). Strange indeed!
Consequently, Hino will remain the only brand in the market today that doesn’t offer 500hp (373kW) or more from a 13-litre engine, yet fully aware that Japanese rival Fuso will later this year add a 13-litre 510hp (380kW) model to its top-end Shogun range. Again, a strange decision indeed, particularly given the brand’s stated resolve to be a bigger player in the heavy-duty business and one day realise its long-held ambition to overtake Isuzu as Australia’s top selling truck brand.
That said, though, Hino Australia’s somewhat circumspect manager of product strategy, Daniel Petrovski, was quick to hint that bigger things are brewing and what we were shown in Sydney is effectively the first of several phases in the brand’s pursuit of a substantially bigger footprint in the heavy-duty field. Whether a 500-plus version is part of any future phase, he wouldn’t say.
What he did say, however, is: “The reliability of the Hino E13C engine is already well proven, and the improved version in the all-new 700-series range is available in two power ratings of 450hp (336kW) and 480hp.”
More to the point, perhaps, the 13-litre in-line six is just one part of many significant features in a thoroughly modern makeover of Hino’s flagship range. One of the most appealing is the smart addition to the heavy-duty mix of the brand’s A09C nine-litre engine, with both nine- and 13- litre displacements meeting Euro 6 emissions

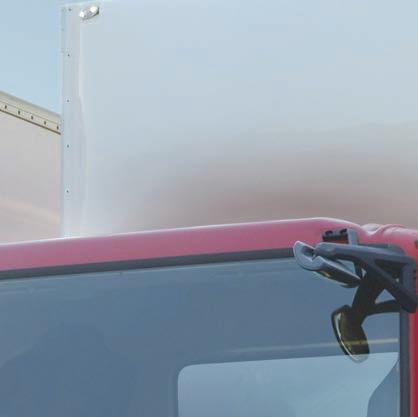
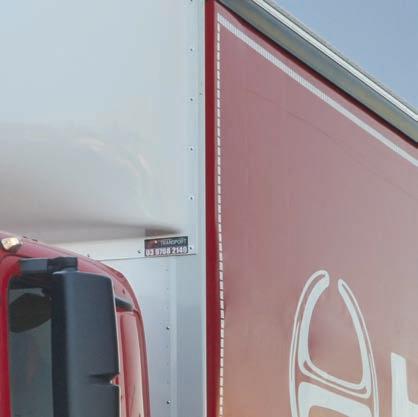
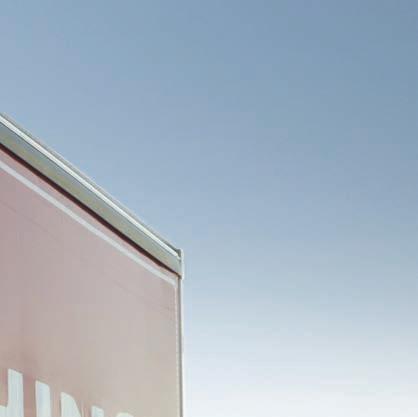
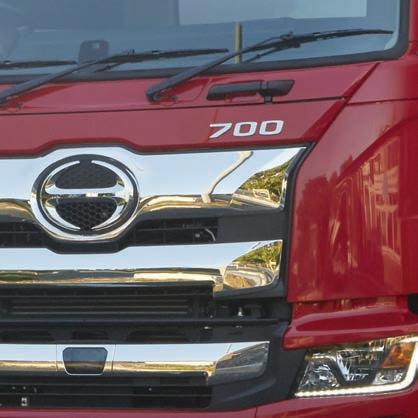
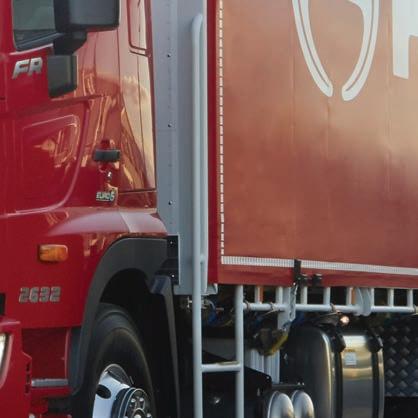

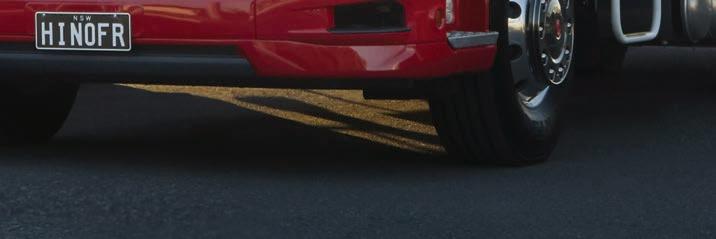
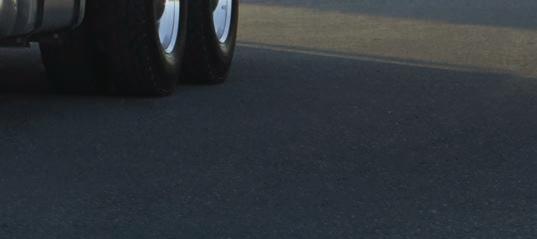

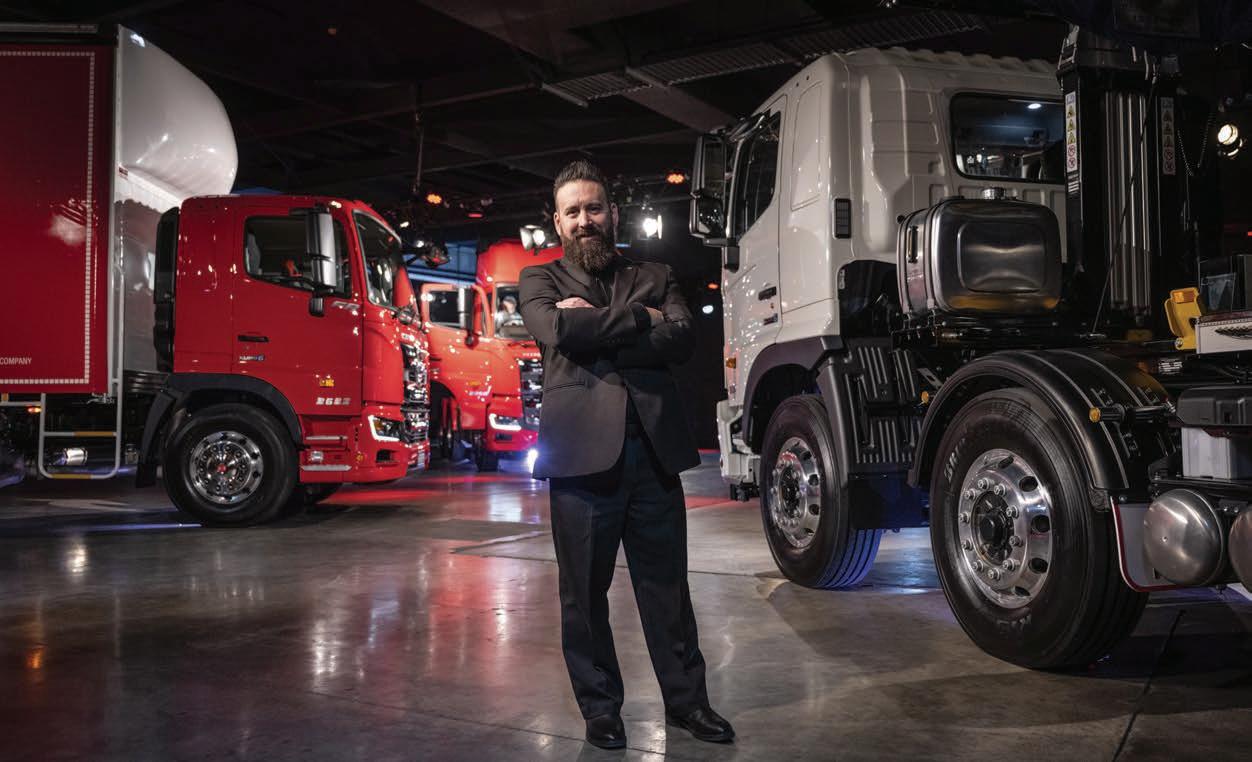
standards through the combined effects of a selective catalytic reduction (SCR) system, cooled exhaust gas recirculation (EGR) and a diesel particulate filter (DPF).
What’s more, in an innovative move that recognises an increasingly obvious trend throughout the road freight sector, every model in the expanded range is fitted with either an automated manual transmission (AMT) or an Allison automatic. There are no manual options.
As Petrovski put it: “Australian customers clearly prefer the convenience of two-pedal transmissions [and] Hino is the only Japanese manufacturer to offer a true automatic transmission option across the light-, medium- and heavyduty model ranges.”
According to Hino, key new models include 4x2 and 6x2 rigids for distribution work and 6x4 and 8x4 models for heavier roles. Critically, after years on Hino Australia’s wish list, the new eight-wheeler is at last equipped with the greater weight carrying allowance of a load-sharing twinsteer suspension designed specifically for our market.
Meanwhile, the addition of the nine-litre engine to Hino’s heavy-duty repertoire finally provides the brand with what it says is, “a Hino solution in the 300 to 400 horsepower area”.
As the company explains, the nine-litre line-up starts with the FH 1832 4x2 model, the FR 2632 6x2 and the FS 2632 6x4, all punched by the A09C engine rated at 235kW (320hp) and 1,275Nm of torque, mated to an Allison 3200 six-speed automatic transmission.
For the higher weights of the FY 3036 8x4 model, the nine-litre delivers 265kW (360hp) and 1,569Nm of torque feeding into the heavier-duty Allison 4440 series six-speed automatic.
In the 13-litre class, the revamped range starts with the SH 1845 4x2 model powered by Hino’s E13C dispensing 331kW (450hp) and 2,157Nm of torque.
Above: Hino Australia product strategy manager, Daniel Petrovski. Among an extended 700-series model range is a new eight-wheeler offering a nine- or 13-litre Euro 6 engines. But the big gain for Hino’s 8x4 is a loadsharing twin-steer. Finally!
Right: Modern makeover. Vastly upgraded 700-series takes its interior design cues from its 500-series medium-duty stablemate which has enjoyed positive driver feedback. Function and form rate high in Hino’s new flagship range
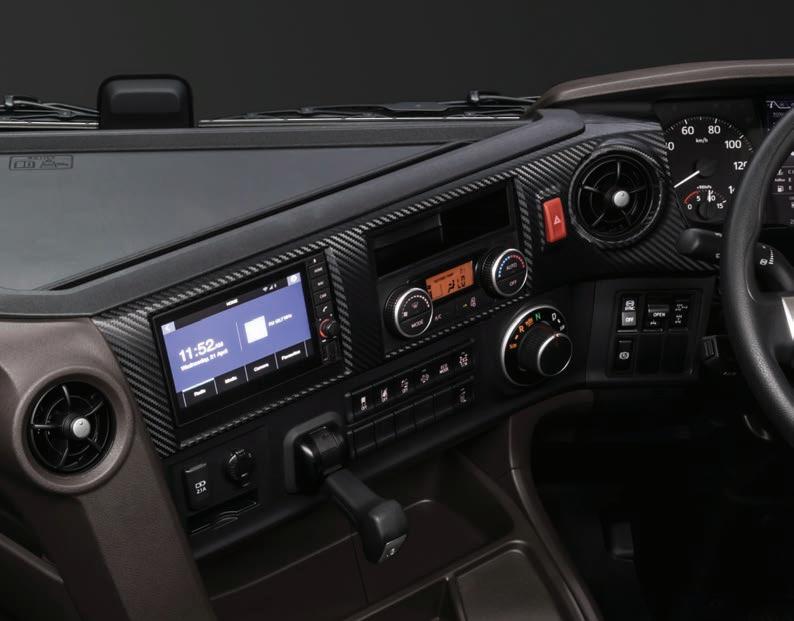
All other 13-litre models – the high-roof SS 2848 6x4 prime mover, the FS 2848 6x4 rigid and the FY 3248 eightwheeler – have the engine rated to existing performance peaks of 353kW (480hp) and 2,157Nm of torque, though Hino points out that peak torque is now dispensed across a wider 1,000 to 1,500rpm rev range.
Coupled to all 13-litre variants is the ZF Traxon 16-speed AMT, with forward, neutral and reverse controlled through a rotary dash-mounted shift knob; uncannily similar to Traxon installations in MAN models. The knob also controls a ‘slow mode’ for crawling in either forward or reverse.
Furthermore, says Hino: “The dash-mounted selector is complemented by a sequential-type shift lever on the steering column that allows the driver to switch between automatic and manual modes, and manually select gears.” Also part of the AMT package is Hino’s Easy Start (hill hold) system for smooth lift-offs on grades.
The list of standard features in the new range is undeniably impressive and includes alloy wheels in an obvious move to improve both tare weight and aesthetics.
Much like its light- and medium-duty brothers, though, some of the most notable advances in Hino’s vastly upgraded 700-series have been in the deployment of advanced safety systems.
Safety first
Hino is adamant its new 700-series range comprises the safest trucks it has ever produced and it all starts with an electronic brake system (EBS) on every model.
Yet, it’s not just the quicker braking performance of EBS that sets Hino’s new heavy-duty models apart from the current crop. As the company states, the 700-series has moved from the traditional S-cam design to Hino’s ‘Taper Roller’ brake system, which it says: “… reduces tare weight, decreases compressed air requirements, provides a smoother and more consistent brake feel, and uses less moving parts, resulting in reduced maintenance requirements and lower operating costs.”
Importantly, auxiliary braking is a strong suit in the new line-up with the inclusion in all 700-series models of the ever effective Jacobs engine brake, coupled in 13- litre versions with the additional braking strength of the ZF Intarder, integrated into the rear of the Traxon transmission.
Even on paper, service and auxiliary braking in the new Hino heavies appears a cut above.
However, it are the overall safety features in what Hino calls its ‘SmartSafe’ package that truly put the new models on a higher plane.
“The 700-series answers a lot of the major safety issues that confront the transport industry and other road
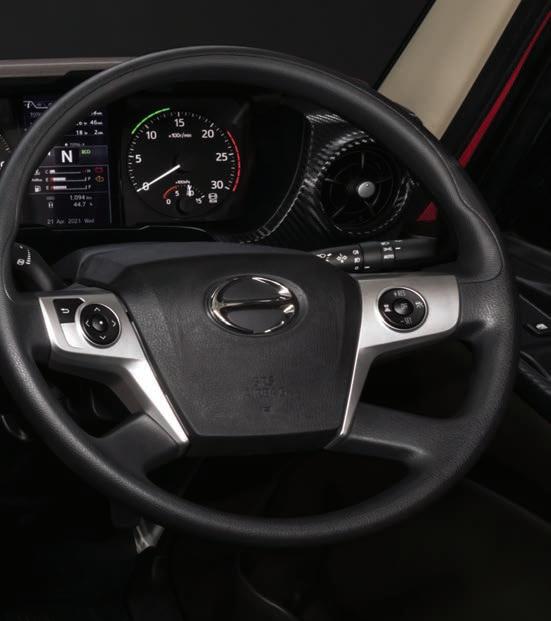
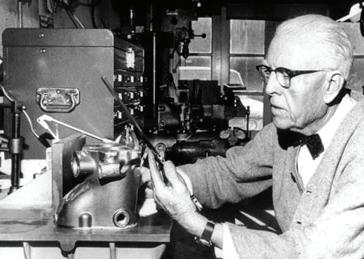
HAPPY BIRTHDAY JAKE
Hiding in the shadows of Hino’s preview of its new 700-series trucks and the use of a Jacobs engine brake in all models is the fact that 2021 marks the 60th anniversary of Jacobs Vehicle Systems.
Jacobs introduced the first engine brake for commercial vehicles in 1961 and, since then, more than nine million Jake brakes have been produced for trucks around the world.
In fact, Jacob engine brake use has grown markedly over the past few years. The company sold its eight millionth engine brake in 2019 but it was only two years later, in March 2021, that the nine millionth unit rolled off the Jacobs assembly line.
It may, however, surprise more than a few people to learn that the world’s best known engine retarder was actually invented by Clessie Cummins, the man who, in 1919, founded the Cummins Engine Company. And it may also be a surprise to learn that safety and a near-death experience were the reasons why Cummins made an effective engine brake one of his most enduring engineering legacies.
The story goes that, in 1955, when Cummins retired from the engine company he’d created, his thoughts returned to a terrifying experience in the northern summer of 1931 when he and two colleagues drove a Cummins diesel-powered truck from New York to Los Angeles in an attempt to set a new truck speed record across mainland USA.
On the fifth day of the drive, at the top of a notorious pass on a stretch of historic Route 66 in Southern California, Cummins was at the wheel of the truck when it started a long, steep descent towards the San Bernardino Valley.
On a gravel road that plunged downwards for 35 miles (55km), criss-crossed by a busy railway line, the frequent slowing for twists and turns overheated the truck’s brakes. Cummins tried to restrain the runaway truck with engine compression but, with so much momentum and road speed, was unable to engage a lower gear than third. To his horror, the Cummins founder realised he “would just have to ride it out”.
With a freight train cutting across their path a short distance ahead, he was sure his days were done.
Cummins later recounted how the truck passed the back of the train with inches to spare and how he had vowed that someday, somehow, he would make his engine work just as well going downhill as it did uphill.
Almost 25 years passed before Cummins found the time in retirement to study what might be done to turn his engine into an effective brake. By 1957, he’d developed a design that would revolutionise engine braking. His idea was to take advantage of perfectly timed motion already built into Cummins and Detroit Diesel engines, which have a third cam on the main camshaft that activates the fuel injector of each cylinder. By transferring this motion to open the exhaust valve with a simple retrofit mechanism, the engine brake was born.
Although the principal of engine braking wasn’t new, the details of Cummins’ new technical approach made it novel enough to be granted patent protection.
As for getting his engine brake into the market, it wasn’t plain sailing. Cummins was contractually obliged to offer his invention first to Cummins Engine Co. but, strangely, his design was rejected on the grounds of commercial risk. Big mistake!
Fortunately, Cummins received a more positive response when he explained his idea to a vice-president of Jacobs Manufacturing Company. By April 1960, after the success of extensive tests of the design, Jacobs established a new Clessie L. Cummins Division (now named Jacobs Vehicle Systems) for the manufacturer of the engine brake.
The rest, of course, is history and, while the raucous bark of earlier Jakes has been criticised by many, the one salient fact that can’t be criticised is the engine brake’s inestimable contribution in keeping truck drivers and other road users safe on downhill grades.
Besides, the modern Jake is far quieter than its forebears thanks to the fact that Jacobs Vehicle Systems engineers continue to work closely with engine manufacturers throughout the world, not least Hino.
Above: Cummins Engine Company founder, Clessie Cummins. In retirement in 1955, he found the time to create the design that would become the remarkably effective Jake brake
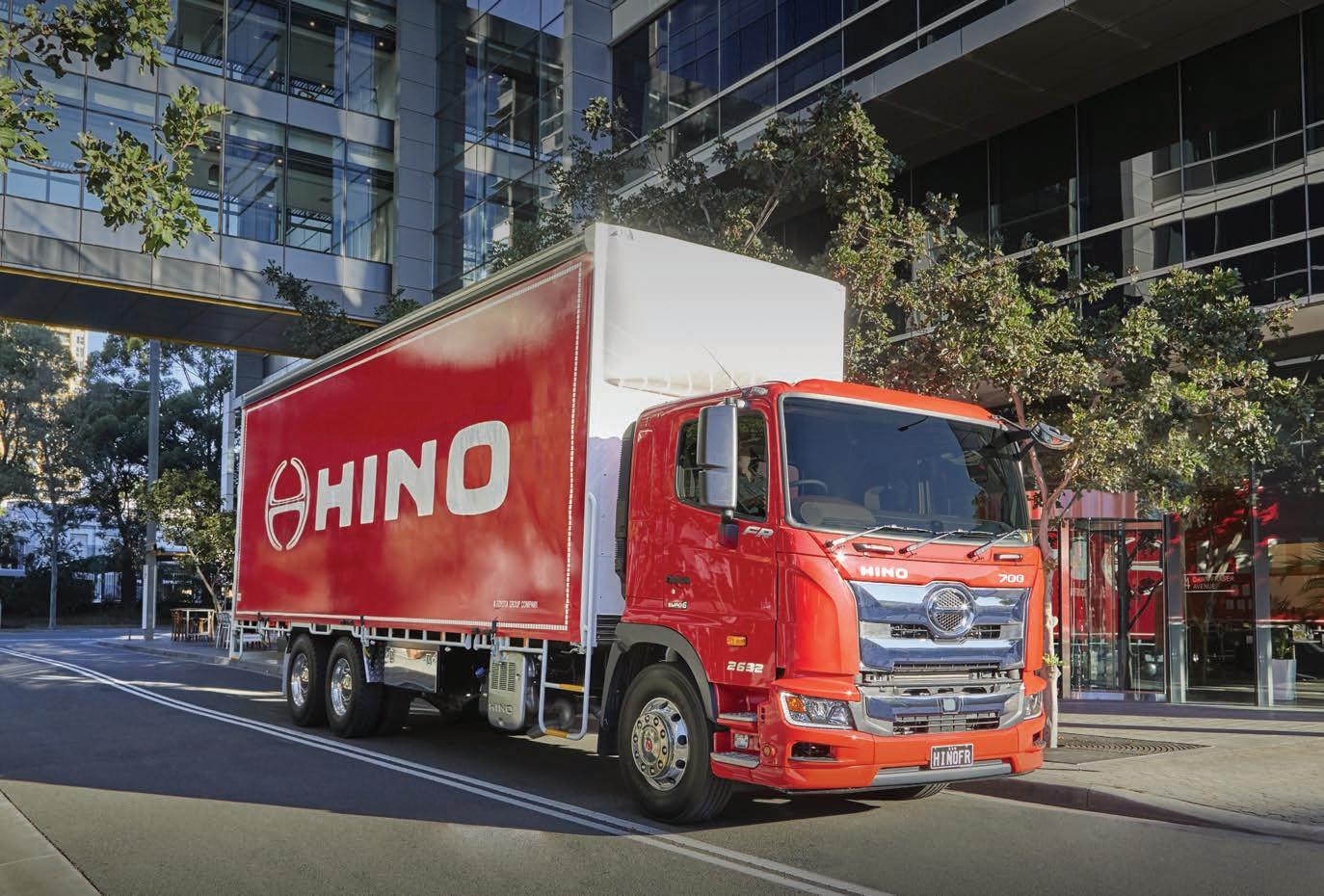
Top: Vital new model, the FR 2632 6x2 rigid, is punched by a nine- litre engine stirring through an Allison auto. All 700-series trucks will come with either an Allison automatic or automated manual transmission. There are no manuals users, with the implementation of advanced driver assist technologies, Hino SmartSafe and, more specifically, the introduction of Driver Monitor,” says Petrovski.
As a Hino statement explains: ‘The new Driver Monitor system constantly monitors the driver’s attention towards the road using key metrics such as driving posture, face orientation, and eyelid status via a camera integrated into the A-pillar.
“The system provides a visual and audible alert if it detects drowsiness or a lack of attention from the driver.”
Emphasising the benefits of the Driver Monitor system, Petrovski commented: “National Transport Insurance recently released the 2020 National Truck Accident Research Centre report, which found that two of every three truck driver fatalities were as a result of either fatigue or distraction.
“The report also found the number of significant accidents caused by distraction more than doubled in the past two years, which makes Driver Monitor an important addition to the Hino SmartSafe package.”
Safety has been a major focus for Hino over the past decade and more, first demonstrated by the inclusion in 2011 of a vehicle stability control (VSC) system on the lightduty 300-series.
In fact, Hino now describes VSC as the cornerstone of its SmartSafe system that, in the upcoming 700-series, will include a radar-based pre-collision system (PCS) working in conjunction with autonomous emergency braking to dramatically minimise the incidence and impact of collisions caused by driver distraction or poor judgement.
Similarly, a pedestrian detection system is also part of the SmartSafe package, along with adaptive cruise control, lane departure warning, reversing camera and a driver’s airbag.
Meanwhile, LED headlights and daytime running lights are also standard in Hino’s new heavies, as well as larger electronically-adjustable, heated mirrors, a heated convex spotter mirror and spotters for the kerb and front of the truck.
Yet, while SmartSafe is a highly impressive package, all its features will not be initially available on 8x4 models. Apparently, the priority is to get the loadsharing twin-steer into the market.
Citing delays in validating the VSC and PCS systems on 8x4 models, Petrovski says: “The addition of SmartSafe to the 8x4 models will occur in mid-2022.
“We have made this decision in order to fulfil our customers’ requests for low tare weight and loadshare (twin) steer axle.”
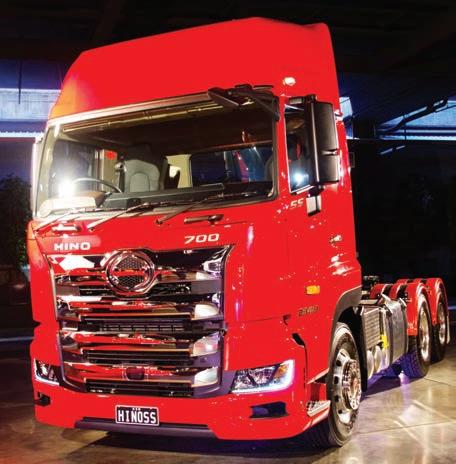
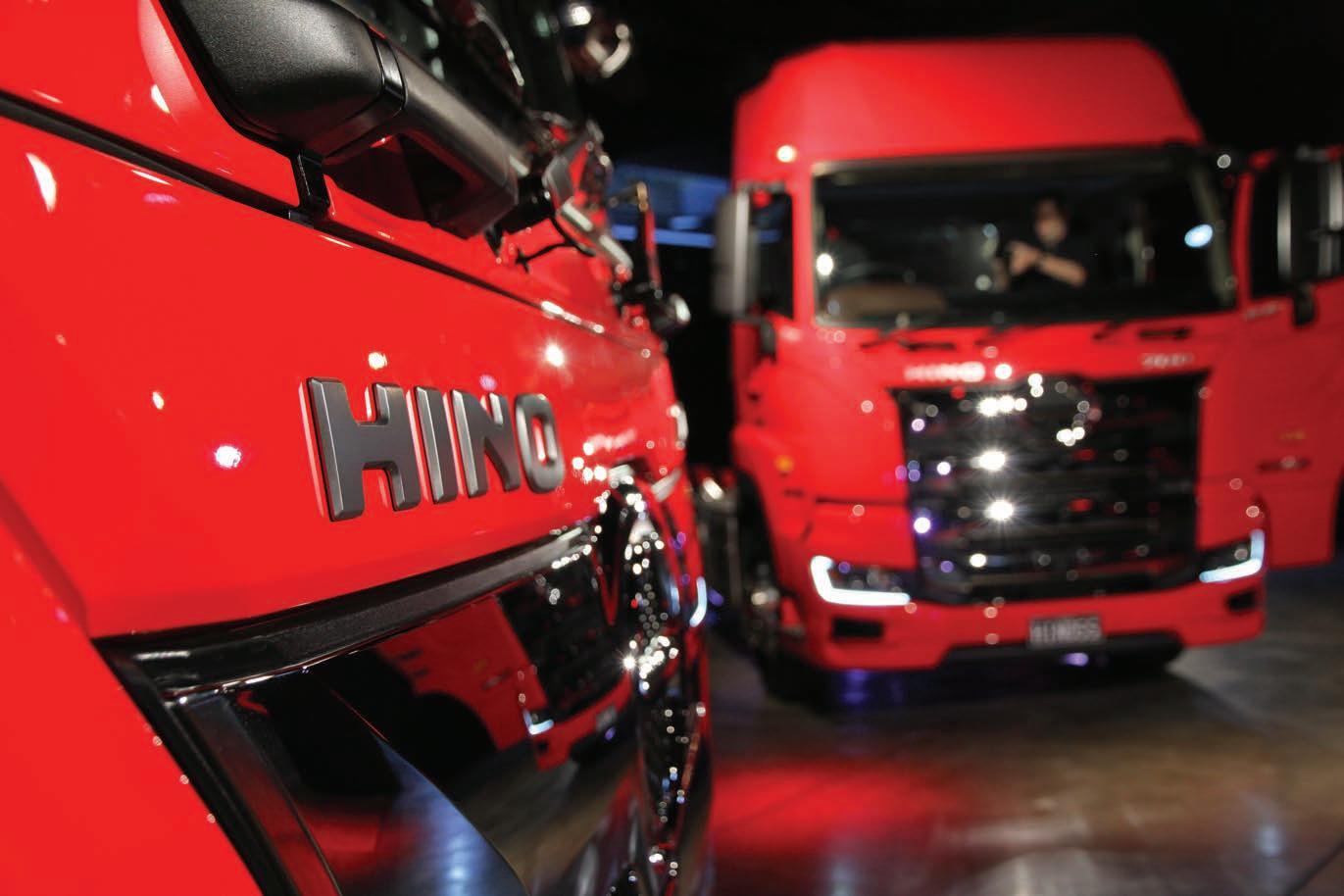
Below: All Hino 13-litre models run a ZF Traxon 16-speed automated transmission, engaged by a rotary knob on the dash. Manual or auto operation is via a wand on the steering column
Contemporary design
There will, however, be no delays in supplying a significantly improved cab layout that, like the 500-series standard cab, uses a modern mix of tones and designs to produce an extremely functional and pleasing driver environment.
With some sceptics wondering if Hino had gone too far in its bid for a modern contemporary cab interior at the 2019 launch of the 500-series standard cab, Hino’s Petrovski asserts: “Feedback from drivers has been overwhelmingly positive since we first introduced the new-look interior.”
Wisely, the new 700-series ignores the sceptics and delivers an attractive workplace with comfort and function obviously at the top of the design agenda.
As Hino states: “The ergonomically designed wraparound dash layout features all-new instrumentation with large, high contrast speedometer and tachometer, and a central seven-inch multi-information display, which contains important information such as SmartSafe settings, driving economy, gear selection and vehicle maintenance data.”
Driver comfort starts with a cab mounted on a fourpoint air suspension and the inclusion of an Isri 6860 NTS2 driver’s seat to provide more rearward seat travel, greater seat depth and lumbar air support.
Likewise, generous tilt and telescopic steering wheel adjustments make it easy to find a good driving position for ‘steerers’ of almost any shape and size, while control buttons on the steering wheel offer fingertip ease for phone calls, setting the adaptive cruise control system, and operating the information display screen.
On the outside, exterior design has been notably refreshed with style changes to the grille in particular. A shallower three-slat grille, for instance, denotes a nine- litre model and a taller four-slat grille, a 13-litre version.
All up, even a short stint behind the wheel of several static trucks suggests Hino’s new 700-series is something special for the brand in this country and perhaps, something special in the evolution of Japanese heavyduty trucks.
Time will tell, of course, but right now there’s a sense of expectation that on-road experience will only confirm what we’re already thinking. Stay tuned!
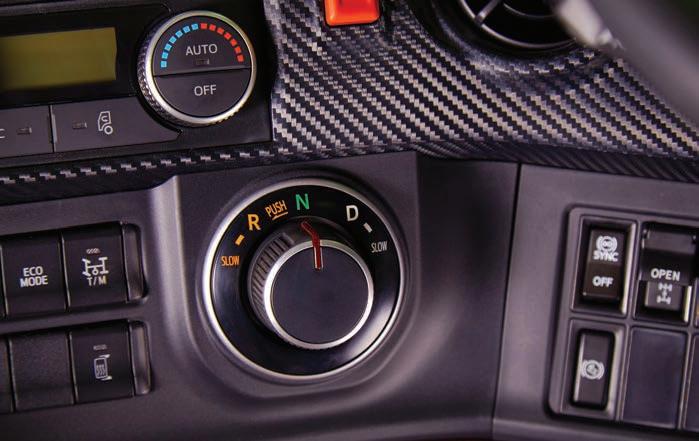
SAFETY ACCELERATOR Daniel Elkins

Shameful failure
The SA Inspection Scheme has proved to be inconsequential in its aim to reduce injuries and fatalities
ON JANUARY 1, 2017 the South Australian government’s Department of Planning, Transport and Infrastructure (DPTI) introduced stage one of the Heavy Vehicle Inspection Scheme (the scheme) after a 2015 coroner's report into a tragic accident. The scheme proposed to address serious injury and death related to mechanical failure (defects).
Although no specific targets were set as to how many incidents the scheme would eliminate, it was aligned with the Towards Zero Together: South Australia’s Road Safety Strategy 2020, which sought to reduce serious injury and death by 30 per cent by the year 2020.
In May 2017, DPTI released a Regulatory Impact Statement (RIS), it seems in an attempt to vindicate its new policy approach to heavy vehicle safety. It indicated that the scheme would be justified if one fatality per year was avoided.
The Towards Zero Together Strategy indicates that heavy vehicles are involved in 14 per cent of fatal crashes. SA provided no evidence of the contribution of heavy vehicle defects to serious injury and death in its RIS for SA. A National Transport Commission (NTC) RIS in 2015 identified that defects contributed to between one and six per cent of heavy vehicle incidents across Australia.
If the DPTI was to meet the Towards Zero Together Strategy target of a 30 per cent reduction, this would require that more than three lives be saved per year. What the RIS didn’t identify was how many deaths and serious injuries were caused by defects – or more precisely, mechanical failure – a deplorable failure.
DPTI was unable to accurately identify the problem caused by defects, nor provide an accurate baseline from which to measure the success or otherwise of the scheme's introduction. Is it not a fundamental obligation of our public institutions to clearly articulate what problem they are seeking to solve, its cost and the benefit it will deliver to industry and community? This should be particularly true where industry is paying for the privilege of being regulated or, in this case, obtusely regulated.
It demonstrates a depth of ineptitude that the heavy vehicle industry and the community should not accept from public institutions. Fundamental flaws in the RIS were identified and neither DPTI nor the National Heavy Vehicle Regulator (NHVR) acted on it. The failure in leadership to acknowledge these problems in the scheme and to undertake the necessary work to address them is shameful. What is worse is that associations who purportedly represent the heavy vehicle industry idly stood by and let it all unfold without a whimper.
DANIEL ELKINS has a wealth of experience in the safety and assurance (compliance and enforcement) space, is a safety accelerator and one of Australia’s foremost progressive safety thinkers.
FLAWED APPROACH
DPTI has proven itself incompetent in
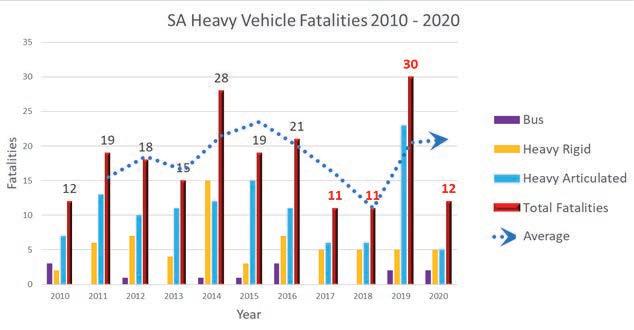
developing effective safety policy and incapable of implementing those policies – stage two of the scheme has been shelved – thankfully. The heavy vehicle industry and the NHVR in that entire time failed to hold them to account for the stage one outcomes of the scheme.
Serious injury and death have not reduced – at all – during the period of this scheme in South Australia – in fact on average they increased!
Despite being provided explicit advice by the NHVR that the approach was flawed they continued to pursue the scheme. The time, effort and funding expended on the scheme could have been directed to delivering other road safety initiatives. These could have produced higher returns for the investment whilst not placing additional regulatory burden on the South Australian heavy vehicle industry for no reported benefit.
THE FACTS
2015 NTC released RIS: Major Findings • The risk of a mechanical defect causing or contributing to a crash is more diffi cult to measure, with assessments of defects as the primary cause in fatal crashes involving a heavy vehicle ranging from one to six per cent. • Build a dataset that would enable a risk profi le to be built to identify most of the ‘at-risk [heavy] vehicles’ for inspection. • Implement a risk-based approach to [heavy] vehicle inspections and use of regulatory recognition [accreditation] rather than prescription.
2017 SA DPTI released RIS: Major Policy Direction • A breakeven analysis indicates that using a Willingness to Pay valuation for a fatal road accident, the option is justifi ed if one fatal accident per year is avoided. • The desired outcome is to develop a periodic inspection scheme for all higher risk heavy vehicles and trailers. • The scheme will be implemented and monitored by the Minister for
Transport and Infrastructure with
DPTI offi cers carrying out the core functions of the scheme.
2017 NHVR responds to SA RIS: Key Concerns • DPTI do not explain how they will directly improve the safety of the heavy vehicle fl eet and specifi cally address mechanical failure as a causal factor in heavy vehicle crashes. • The NHVR, and it is our understanding that Transport and
Infrastructure Council, does not support more onerous changes to inspection regimes currently operated by jurisdictions while there is insuffi cient evidence about whether inspections contribute to heavy vehicles roadworthiness and improve fl eet safety.
2020 Ministerial/ DPTI response to request for data on effectiveness of the HVIS • No discernible evidence from DPTI that the Heavy Vehicle Inspection
Scheme had any road safety impact after three years of operation. "…it is recognised that vehicles presenting for Change of Ownership inspections represent a small percentage of the total registered fl eet in South Australia and are therefore unlikely to impact heavy vehicle incident statistics." • DPTI failed to collect data to assess impact or effect on road safety of the HVIS.