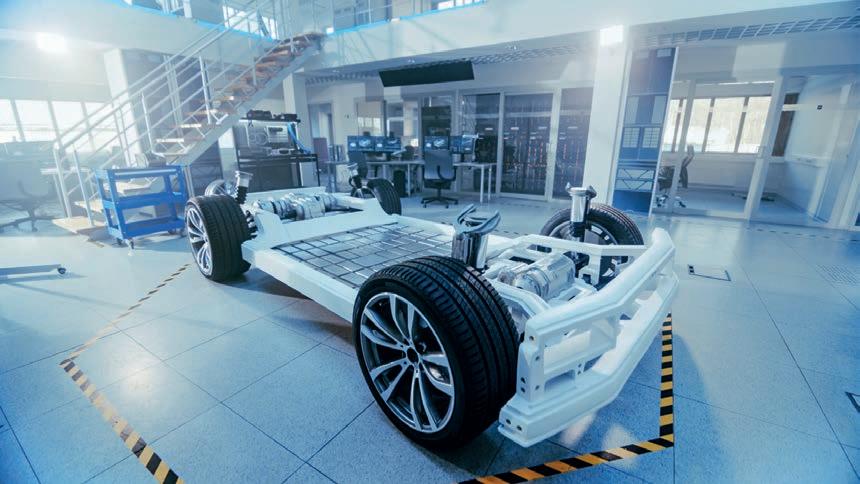
4 minute read
WASTE LAND
A research team at Stanford University have found a way to make lithium-ion battery packs last longer and suffer less deterioration from fast charging. Through the implementation of the required infrastructure and technology, this breakthrough could be a major factor in making Australia’s commercial vehicles more productive and efficient.
Actively managing the amount of electrical current flowing to each cell in a battery pack can minimise wear and tear according to recent findings by a team at Stanford University. According to Stanford Professor and Senior Study Author, Simona Onori, initial simulations suggested that batteries managed with the research’s new technology could handle at least 20 per cent more discharge cycles, even with frequent fast charging which puts extra strain on a battery. The findings of the report were first published in IEEE Transactions on Control Systems Technology on 5 November 2022, as
Extending Life of Lithium-Ion Battery Systems by Embracing Heterogeneities via an Optimal Control-Based Active Balancing Strategy. Motivation to embark on this project arose after Tesla announced it was working on a million-mile battery in 2020. According to Tesla, the battery would be capable of powering a car for over one million miles with regular charging before reaching the point where the battery would hold too little charge to be functional. A battery of this measure could exceed a typical warranty for electric vehicle (EV) batteries by eight years or 100,000 miles, easing the way for the electrification of long haul trucks and heavy vehicles.
However, Simona says it was later explained that the million-mile battery concept was not a new chemistry, but rather just a way to operate the battery without using the full charge range. Intrigued by Tesla’s efforts, Simona and her two researchers, postdoctoral scholar, Vahid Azimi, and PhD student, Anirudh Allam, decided to investigate how inventive management of existing battery types could improve performance and service life of a full battery pack.
To begin, they crafted a computer model of battery behaviour that represented physical and chemical changes which take place inside a battery during its operational life.
Running simulations with the model suggested that a modern battery back could be optimised and controlled by embracing differences among its constituent cells.
The team believes, pursuant of these findings, that the model can guide the development of battery management systems in the coming years, while also being deployed in existing vehicle designs.
While there have been many efforts made to extend battery lives, Simona explains that the majority of them have focused on improving the design, materials and manufacturing of single cells based on the understanding that a battery pack is only as good as its weakest cell. However, Stanford’s study differentiates in this aspect with a belief that while weak links are unavoidable due to manufacturing imperfections and the faster degrading of cells after being exposed to stresses such as heat, they don’t necessarily reduce the quality of the entire battery pack.
“Our approach equalises the energy in each cell in the pack, bringing all cells to the final targeted state of charge in a balanced manner and improving the longevity of the pack,” she says. Following the study, Simona says the key is to tailor charging rates to the unique capacity of each cell to stave off failure.
“If not properly tackled, cell-to-cell heterogeneities can compromise the longevity, health, and safety of a battery pack and induce an early battery pack malfunction.” While research in these instances may house the possibility to increase productivity in commercial EVs, it’s up to governments to better accommodate the uptake of batterypowered vehicles with better fuel efficiency standards and infrastructure. Within Australia’s borders, more than 100 corporate giants including Woolworths, Linfox, Uber, IKEA and Microsoft are calling on the legislation of fuel efficiency standards by the Labor Government, following a spike in EV sales as a result of Prime Minister Anthony Albanese’s election victory.
According to the Australian Bureau of Statistics, Motor Vehicle Census, Australia 31 Jan 2021, there were 20.1 million motor vehicles registered on Australian roads in 2021 and only 23,128 EVs.
Stanford’s breakthrough couldn’t be timelier as governments continue to push the sales of EVs while Australia prepares for an electric future.
As part of the Labor Government’s 2022-23 Federal Budget, the $500 million Driving the Nation Fund will see the development of EV charging stations at 117 highway sites and hydrogen highways for key freight routes around Australia in hopes of targeting a reduction in transport emissions.
To encourage the uptake of battery vehicles, a $345 million Electric Car Discount will exempt eligible electric cars from fringe benefits tax (FBT) and the five per cent import tariff – saving employers up to $9,000 a year on a $50,000 car or for an individual using a salary sacrifice arrangement up to $4,700 a year.
In addition, the Government also ensured that 75 per cent of new Commonwealth car purchases and leases will be electric by 2025, which in its eyes will encourage more EVs and help contribute to a “second-hand market”.
Although breakthroughs like those by the Stanford researchers suggest industry is on the right path towards making batteries more efficient, the more immediate challenges in Australia hinge on lack of technology and infrastructure when it comes to preventing the reduction of deterioration in fast charging.
There is a lot of stress involved in modern life. Some of it is felt by operators when the chassis rail, or a structural member attached to a chassis ladder fails. Mechanical stress arises from weight and road forces. Mechanical stress flows through the structure starting at the weight points and getting onto the road via the axles and tyres. The art of the design is to keep stress at relatively low levels to avoid members breaking. A Factor of Safety based upon static loads of at least 3 is advisable. This article is about how chassis designers and modifiers can minimise the chance of chassis failure, by keeping everyone’s stress within limits. Hopefully operators who purchase modified trucks can be informed about what to look for and what to insist upon from the vehicle modifier.
The starting point is the chassis ladder, which is the ‘spine’ of any truck or trailer. It takes the form of a ladder formed by two long structural rails that are usually C-section steel on trucks, and cross members that are bolted through the web of the chassis rails. The truck chassis rails are often reinforced by inserted C-section or L-section steel through the rear axle group installation. Some heavy-duty trucks have the rail inserts running from front to back. Figure 1 illustrates the chassis ladder concept.
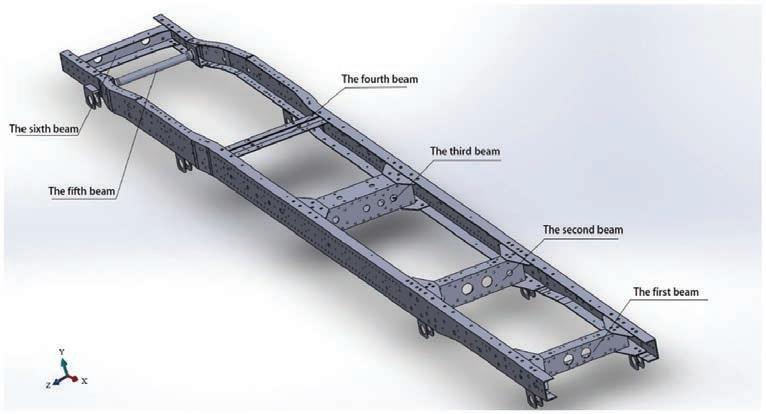
Nearly all trucks, except for prime-