
8 minute read
Cleaning up Canberra
from Prime Mover May 2020
by Prime Group
CANB CLEANING UP
Most of us don’t usually think about sewers and drainage unless confronted with a problem due to a blockage, so we call a plumber. Canberra based Flexible Australia utilises an ultra high tech approach to the maintenance of what can be lying beneath the nation capital’s streets.
ERRA
Flexible Australia was established in the ACT in 1999 by Kurt Kaks who has been in this niche service industry since 1982. Flexible specialises in infrastructure maintenance and particularly the maintenance and cleaning of sewers and stormwater drains. This service includes the regular and emergency cleaning of Gross Pollutant Traps (GPTs) which function to collect trash such as plastic bottles, cigarette butts and other debris and sediment to prevent the litter and pollutants from urban runoff entering the ACT’s lakes and rivers. To perform its operations the company employs some quite unique equipment fitted to a fleet of Scania cab/chassis which are rather specialised themselves. The Kaiser AquaStar water jet, vacuum and recycling equipment comes from Lichtenstein and the most recent additions are fitted to Scania P480 day cab trucks which have been equipped with a third steerable axle. The innovative axle configuration addresses several fundamental issues for the type of work carried out by Flexible including increasing the payload from seven tonnes to ten tonnes when compared with the more conventional Scania 8x4s in the Flexible fleet. This significantly contributes to the overall efficiency because on most days each unit can operate for a full day without having to offload the trash it has collected. According to General Manager Tim Rolfe, the increased capacity has changed the work schedule in a very positive manner and helps justify the investment of around $1million in each vehicle. “We no longer need to take a trip in the middle of the day to offload debris at the recycling stations,” says Tim. “Instead we work right through and it means we can get bigger jobs done considerably more quickly, saving our customers time and money. Plus, we get more jobs done during the course of a week, which means we are gaining improved asset utilisation.” Safety is enhanced as well. This is due to the location of the extra axle in front of the drive wheels instead of the more conventional tag at the rear which provides much more vehicle stability when tipping thanks to the larger footprint of the bogie dual wheel arrangement. “Instead of a more typical 10x4 which has a steerable tag axle with single tyres, we worked with Kaiser, the Scania factory and the relevant Federal and State authorities to come up with an imaginative solution,” says Shane Griffin, Scania Australia National Manager, Specialist Vehicles. “We knew Flexible wanted to tip the waste out of the vehicle so tipping over the back axle on single, not dual, wheels would have been a less suitable solution, plus the rear overhang length would have been too long. So, in consultation with the factory engineers we came up with the idea of a supersingle centre axle that steered in a pusher arrangement.” The trucks are 11 metres long and 3.9 metres tall and although Canberra is
The Kaiser Aqua Star water jet is supplied by Lichtenstein.
renowned for its wide streets and large diameter roundabouts the vehicles still need to be manoeuvrable. The steerable third axle permits a turning circle which has a diameter only one metre larger than a more conventional and shorter 8x4 Scania. The Kaiser/Scania combinations allow Flexible to provide many more services than the usual storm water and sewer cleaning as scheduled maintenance. On call 24/7, its emergency work can involve clearing blockages causing flooded roads and clean-ups involving oil, diesel, sewage or paint and chemical spills as well as dry bulk products (and half a million eggs from a rolled B-double on one occasion). Demands on the Scania engines include driving pumps that are capable of delivering 400 litres per minute at up to 3,000 psi and powering the vacuum equipment which has a capacity of 3,100 cubic metres per hour. The high pressures available can be utilised to clean hard surfaces including road and footpath surfaces as well as using the high pressure water function to perform non-destructive ‘hydro excavation’ for service locating and of inaccessible or high-risk sites to prevent damage to in-ground services such as electricity, gas, or fibre optic cabling. A sector of Canberra’s Cotter Dam wall was cleaned using these high pressure capabilities for inspection by geologists. Flexible also can carry out

site restoration and landscaping at the completion of projects. Utilised in many of the tasks involved in that process is a Scania T 124 equipped with a tipping body and often pulling a float loaded with 15 tonnes of plant and equipment. The iconic bonneted Scania T model has travelled more than 500,000 kilometers and is a testament to the rigorous service and maintenance regime applied to all of Flexible’s vehicles. Due to the nature of their work the Kaiser Scania’s travel relatively low kilometres so their servicing is carried out every 300 hours of operation. Providing precision control of all of the functions is the Kaiser Tronic CANBUS system which is seamlessly integrated with the Scania electronics. This means

the operator is able to adjust the engine speed and torque output to suit the requirements of the equipment for any particular job and also maximise the fuel efficiency of the Scania engine when driving through the power take-offs (PTOs). This has resulted in a significant fuel saving during operations as most operations can be carried out with the Scania constantly running at around 1500 rpm which keeps the engine within the green efficiency band on its tachometer. “We have done a lot of homework with Scania and Kaiser to tweak the system to be able to deliver the required power with the economy we need,” says Tim. “With the integrated CANBUS talking to the Scania system, and the efficiency of the R480 engine, we’re using around 40 to 41 litres of fuel per hour when running the engine with all of its gearbox PTOs under load. In the past we were using between 50 and 59 litres per hour without any CANBUS integration, so the savings are considerable.” The Scania six cylinder 480hp engine specification was chosen to deliver adequate power to run the latest high efficiency suction and jetting systems which Kaiser specifically developed for the AquaStar units. “The Scania R480’s ample horsepower allows us to run the engine slower, cooler and with less wear and tear, still coupled with greater fuel efficiency,” says Tim who adds that the quiet running Scania engines are important when working in the sedate Canberra suburbs. “Municipal authorities like that because they get no complaints.” The cleaning operations are organised via a remote radio control panel worn around the operator’s waist which facilitates excellent visual access for the operator to the job being performed and at the same time contributes to their safety. A Scania on-board weighing system is also connected wirelessly to the remote panel’s screen and displays axle weights in real time. The compartmentalised tank holds 13,000 litres of wastewater and debris plus 3,000 litres of fresh water. About 99 per cent of all wastewater collected
Most of the Scanias have been eqipped with a third steerable axle.
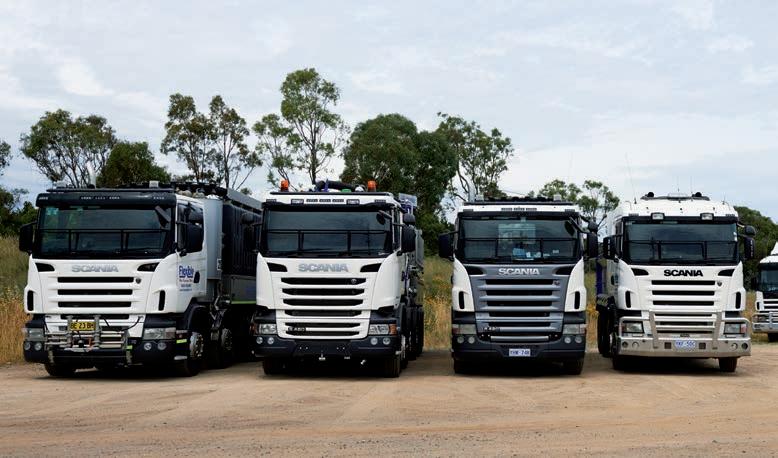
Tim Rolfe General Manager, Flexible Australia
is recycled. The on-board recycling of wastewater allows for 800 litres per minute to be filtered and reused in the cleaning processes contributing to environmental and cost benefits. Through the unit’s inbuilt high-pressure filtering system, the captured water is able to be reused for washing down and cleaning the insides of the GPT and unblocking any blocked inflows. As such, the operating protocols are environmentally friendly. One of the primary benefits of a combination water recycler is that it eliminates the need for time costly water refilling stops and turns them into productivity gains. Another benefit of a combination water recycler is the use of increased water flows. Because a recycler reuses the water and does not require refills, a much higher water flow can be used in the cleaning process, thereby reducing cleaning times. This results in benefits including increased productivity, improved efficiency, and reduced fuel consumption. Building the Kaiser AquaStar unit for Australia presented its own challenge due to the European design being intended for left hand drive vehicles operating with the kerb on the right hand side. This required all of the components other than the water tank to be mirrored so the drums holding the water hoses can be used in conjunction with our left hand kerbs and the top mounted suction hose for the vacuum unit emerges on the right hand side of the truck at the rear, not on the left. A 4K modem connected to the body enables technical monitoring by Kaiser in Europe which helps with any fault finding and diagnosis to maximise uptime. Flexible’s staff mechanic also has access to the Scania software in order to diagnose any fault codes from the trucks’ systems. “At Flexible we are committed to running the best gear available so we can offer our clients a high quality service that is reliable and efficient,” Tim says. “Scania helps us achieve this.”