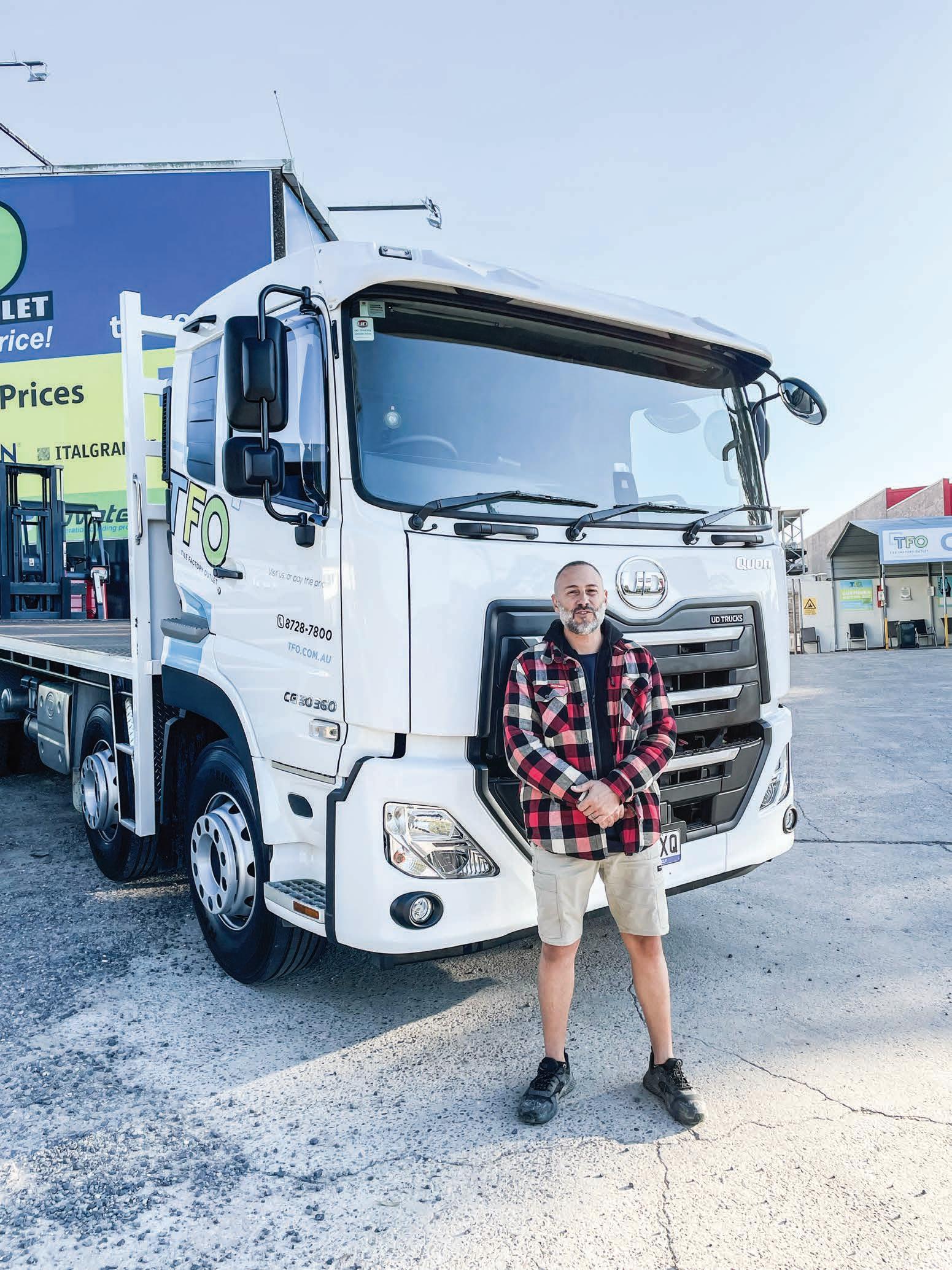
23 minute read
Believe the Hype
from Prime Mover May 2022
by Prime Group
John Perri.
BELIEVE
THE HYPE
Drivers for Tile Factory Outlet in Sydney are noticing serious improvements in productivity, safety and fatigue management with a pair of recently delivered UD Quon 8x4s.

Scarcity of supply during the recent era of lockdown economics has for importers foreshadowed dramatic rises in container prices — too dramatic for some. Many wholesalers, subsequently, have chosen to scale back on orders for their product lines leaving them, at least in the short-term, at the mercy of the market and low on stock. Tile Factory Outlet (TFO) was not one of these. Through shrewd planning the business, despite ocean freight fees soaring over the last 18 months, is sitting pretty having backed its direct-to-customer model. As an importer/wholesaler, TFO eschews the showroom model allowing it to focus on stock levels even in an environment not particularly conducive to it. Instead of buttoning down the hatches like many of its rival competitors have done, TFO was importing additional stock in spite of the prohibitive outlays. There was, after all, a national housing boom underway. Owners Len and Maria Franco, who source the latest quality tiles and natural stone coming direct from suppliers in Spain, Turkey, India, Italy and China, base their business in Smithfield near the Cumberland Highway, making it easily accessible by road for commercial vehicles of which they rely on several subcontractors to distribute their products around the greater metropolitan area of Sydney and beyond. Since moving to the location in 2009 the business has evolved from what was essentially a clearance house to the largest single tile store in Australia. For dispatching customer orders of ceramic and porcelain bathroom tiles as well as pavers for outdoor areas, a pair of new UD Quon 8x4s have been enlisted. John Perri, Secureload Sydney, is a veteran of the transport industry. He purchased the UD Quon last November and the move has proven something of a revelation. A random encounter last year in the yard with a driver who suggested he consider UD persuaded him to take a closer look. Up until that point John had mainly driven Hinos including many years as a driver trainer. As parts were always readily available, he had no reason to look beyond it. “I only knew that brand,” he recalls. Following some deliberation John organised a test drive in a UD Quon. “After driving it and meeting the UD sales representative Craig Aller, I fell in love with the vehicle,” he recalls. A self-described family man, John enjoys driving and knows his way around a truck. For 15 years he worked as a driver trainer and assessor at his father’s driving school. That predated a stint at the Roads & Traffic Authority where he spent a majority of time as a heavy vehicle testing officer and clocked hundreds of hours training new drivers, at an affiliated training organisation, to become company drivers at the likes of Busways, Forest Coach Lines and Veolia. When an opportunity presented itself through his father-in-law, Len Franco, to drive for TFO as a contractor, he jumped at it, purchasing an old Hino GH with a front mounted Palfinger crane. It wasn’t long before business started to take off. Things changed again for John in 2021 when he was introduced to the UD Quon. He works as part of a team of drivers who
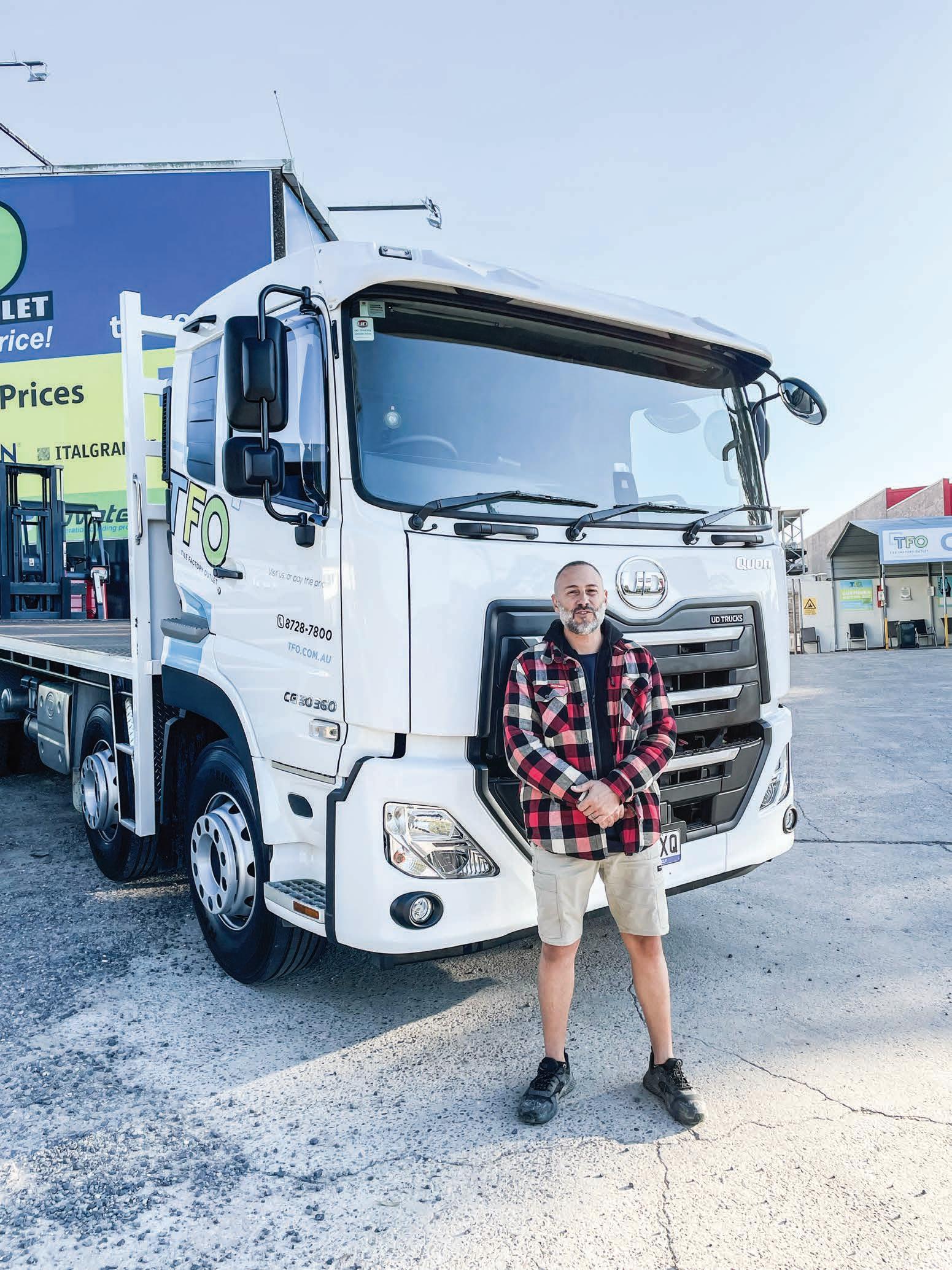
The 8x4 UD Quons with the Moffett mounted forklifts.
are dispatched on customer deliveries by a central computer that generates the sale to each driver. “When you decide you need your two pallets of tiles which is too heavy to move by car as it’s 300kg plus, one of us gets the allocation,” he says. “If we can’t do the job we’ve been allocated it goes to the next driver. We don’t have to advertise. We just have to be ambassadors and drive our trucks safely and deliver on time.” Elevate Transport driver, David Pustaj, also provides contract services for TFO. In March he seized an opportune moment and purchased a new UD Quon 8x4 upon John’s recommendation. The UD CG420, like John’s, comes with a tray and Moffett mounted forklift. His delivery regime is similar, mainly around the urban precinct with the occasional foray into the Blue Mountains, Illawarra area or Central Coast. Previous to this vehicle David operated a crane truck. The differences are pronounced. The 8x4 facilitates a major gain in payload. Opting for a longer wheelbase of 5200mm makes it ideal for use in this application, whereby the truck, during deliveries, can be parked out on the street and the forklift is used for site access. No crane required. No idling. No worries. The twin-steer with rear air suspension and parabolic leaf springs on the front axle ensure it glides over Sydney’s many new major motorways and is comfortable to drive on unsealed roads, an issue for
commercial vehicle drivers following recent weather events. “Most of the gravel roads in regional areas are now rutted after all the rain we’ve had,” says David. “The eight airbags on the Quon rear suspension make these trips much more comfortable than they probably should be. It feels like I’m sitting in my own Ford Ranger.” High-tensile single skin steel has been applied in the chassis construction to help achieve the vehicle’s improved low tare weight. The 14-pallet tray holds a gross weight of 13.5 tonnes. “With the extra payload I’m getting to more jobs,” he says. “That alone has made the UD a winner.” In the previous truck David was limited to a six-speed manual transmission. Nor did he have any of the active safety features the UD is equipped with. Traction control, Lane departure warning and precollision warning are three he appreciates navigating the city traffic. “The UD, when it’s loaded, knows exactly what gear it needs to be in,” he says. “It’s as smooth as butter. On the freeway the pre-collision warning calculates the distance between me and cars in real-time as the radar adapts. There’s a lot to like about it.” Approaching 5,000km David is nearing his first service. John, however, is already up to 35,000km having had more time
The new Quons at Tile Factory Outlet in Sydney. to subject the vehicle to further scrutiny. Another advantage of the 8x4 twin-steer bogie drive are the standard diff locks. A low centre of gravity is also a significant contributor to stabilising load sharing on the suspension system for the steer axles. As the engine is off when John is using the forklift, he is not burning fuel. On the last truck John was accustomed to sitting at 1000rpm while the crane was in operation. The tank on the UD is rarely topped up during the week and is proving, with the Moffett now employed on site, much more economical. The average pallet of tiles weighs around 1.2 tonnes. That, for John’s UD Quon, equates to 12 pallets which he carries with peace of mind knowing he’s compliant within his axle weights. Depending on the size of the storage at hand John can put between six to nine pallets in a customer’s garage. He can charge a premium, too, as customers prefer the convenience and added security of knowing their tiles are inside their home. “I can’t do that with a crane,” says John. “Now I’ve got more energy when it comes to the afternoon whereas with the old truck and set-up I would have been up and down on the swings, depending on times, in the heat and it leaves you exhausted. He adds, “I would never go back to a crane.” The forklift has also eliminated the need to enter driveways in the truck so having more wheels on the UD Quon 8x4 is, by no means, an inconvenience. The nature of the work means the transition between jobs tend to be shorter. This does increase idle and traffic time, but John is on and off the M4 and M5 frequently which reduces allotted time spent in transition. In the main part this is suburb-to-suburb commuting via one of the main arteries. “I’m using around 36 litres per 100 hundred kilometres,” says John. “The AdBlue lasts a bit longer than a month depending on the scheduling of jobs and travel involved.” Despite the higher bowser costs at the minute, the UD Quon is consuming around 1.7 litres of AdBlue per 100 kms. John considers it more than reasonable. “It probably could do with a splitter in it or an extra six gears to make it even more economical,” he says. “But it’s a joy to drive. The technology in it and cab space are fantastic.” The 8-litre UD Quon, according to John, functions as his own fatigue mitigation tool. He advances the 12-speed AMT transmission as a case in point. “The ESCOT that I’m using leaves you still busy. You can’t treat it like an automatic. You can’t get lazy in it,” he says. “So you’re still active and challenged as a driver but at the right times. I think it probably helps with fatigue rather than just driving as an afterthought, foot on the accelerator, foot on the brake. “You’re actually challenged at times to wake up and think about how are we going to approach this hill. Do I drop it back two gears? And so I like the ESCOT. That was what was sold to me. I could have gone Allison, but Craig suggested, for what I’m doing in the truck, the ESCOT was really going to suit the job.” Because it is such a comfortable ride, John is not only more alert, but by the end of a hard day on the road, much more agreeable. Proper fatigue management therefore means, at the very least, he has more time for customers. “In the old truck by late afternoon I would be tired,” he says. “Hardly bubbly with time to talk to journalists.”
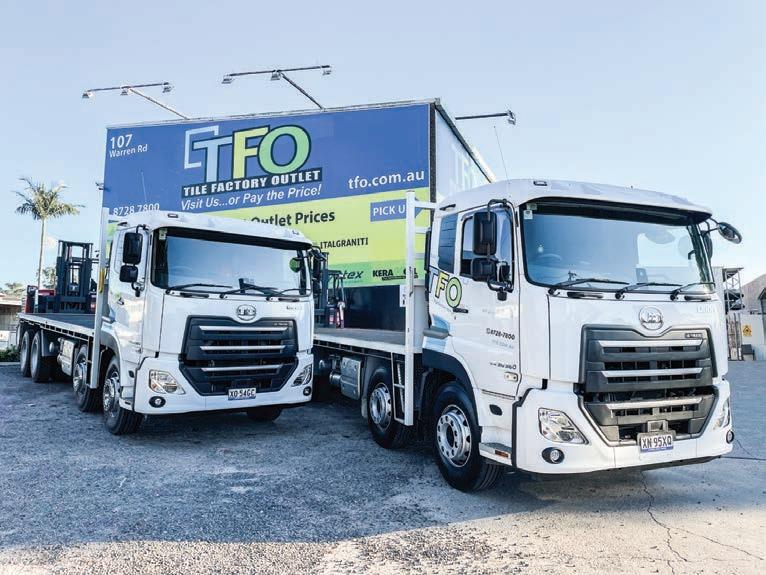
WHY SAF?
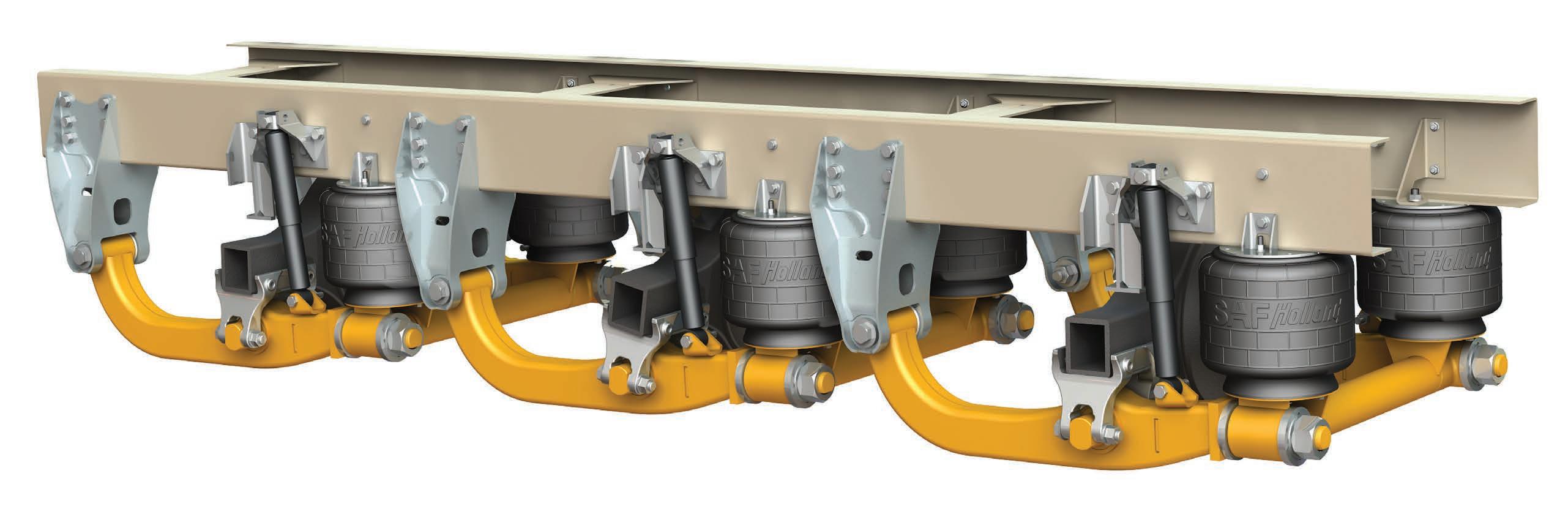
A company pumped to reach its goal of becoming the go-to choice for industry professionals. That’s SAF-Holland Australia today. With a strong leadership team, the equipment specialist is driven to further improve its already market-leading product range. The aim: To offer a more dependable and wider range of products for the Australian market.
The SAF-Holland Group is one of the world’s leading international manufacturers of chassis-related assemblies and components for trailers, trucks and buses. The company produces global market-leading products such as axle and suspension systems, fifth wheels, coupling systems, kingpins and landing legs, under the brands SAF, Holland, V.Orlandi, Neway, KLL and York. SAFHolland is continually working on producing innovative components and systems that function to engineer the customer’s road to success. “At SAF-Holland, we are proud to be a part of this industry,” says SAF-Holland Australia Managing Director, Mario Colosimo. “We have excellent suppliers, manufacturers, transport company operators – all of whom make this a fun industry to work in. We are a new management team in Australia, so this company will feel different from what it has been in the past, while holding on to our values, continuing to be peoplefocussed and staying on top of our
SAF Intradrum suspension.
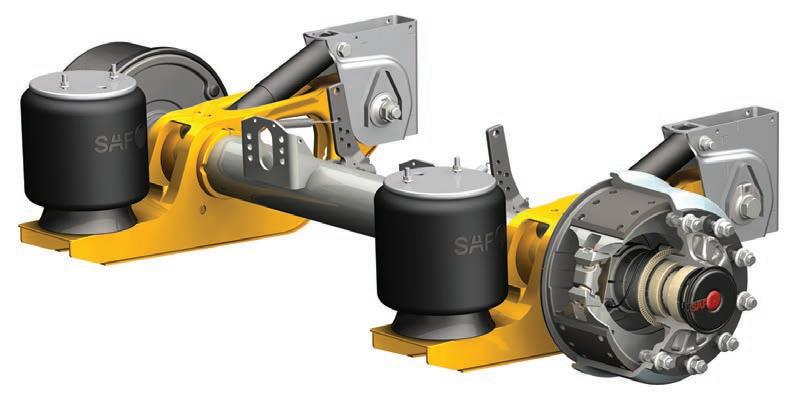
Neway AD369 Tridem suspension.
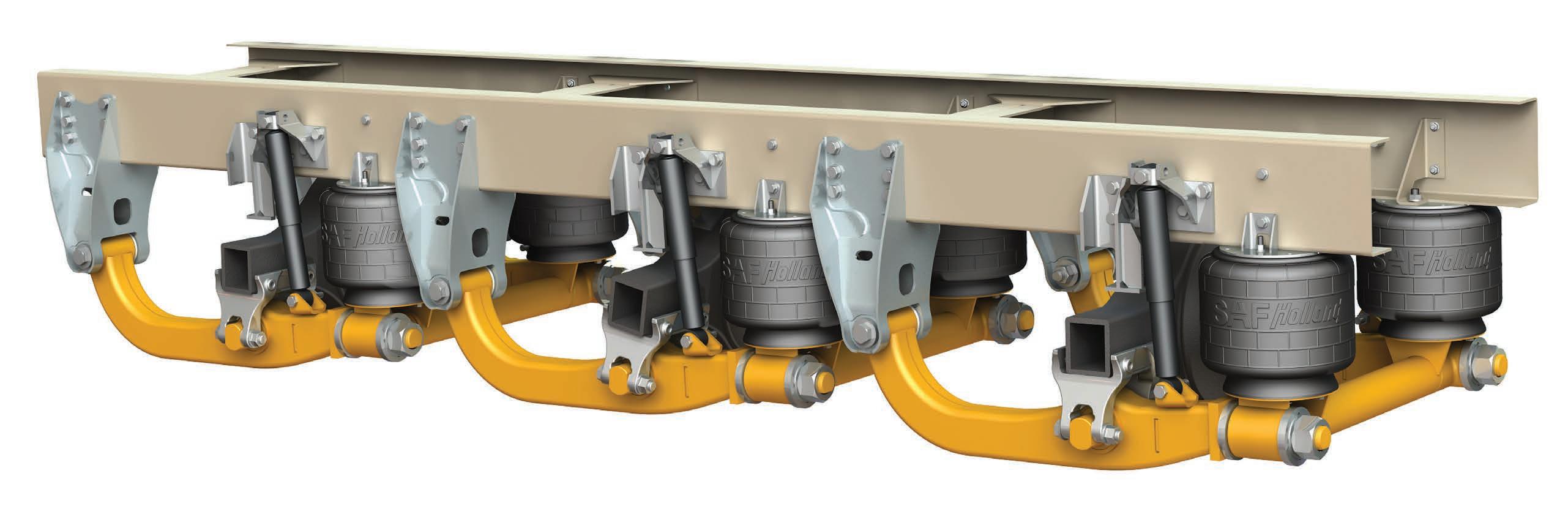
constant drive to improve. “We’ve got a very good product range. Some of our products are at peak optimisation, while others are in various stages of continuous development. We offer class leading truck and trailer suspensions in the market currently. While we’re proud of our products, we’re constantly looking at our product range and making improvements where needed. In the past two years we’ve made some great strides in that area, and it will hold us in good stead in the future. We are poised to become the industry’s first choice when people are looking for a solutions partner.” SAF-Holland’s use of a range of innovative manufacturing processes, practical application techniques and intelligent material mixes have helped raise the industry standard in Australia. These cutting-edge technologies help customers in the truck and trailer industry achieve more operational efficiency, enhance safety and increase uptime. “I can’t think of a competitor that offers the range we do,” says SAF-Holland Australia Sales Director, Stephen Vranesic. “If you’re buying truck and trailer combinations, look no further than SAF-Holland. We have everything from truck suspensions, trailer axles and suspensions, fifth wheels, kinpins, couplings, landing legs and more.” The Neway product portfolio covers single, tandem and tridem configurations for heavy vehicle operators. It offers superior traction and braking performance according to Stephen. “The Neway product line is defined by trouble free operation,” says Stephen. “It is designed to take on the most rugged vocational vehicle applications.” SAF-Holland offers extensive aftersales support to customers through dedicated services and guidance across over 500 retailers and 30 authorised service centres in Australia and New Zealand. The company offers a vast range of spare parts, tools, service offerings that make the operation of its products as efficient as possible and reduce the potential
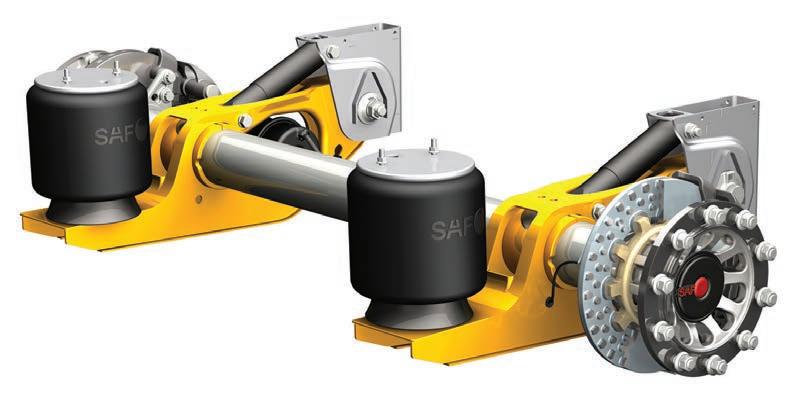
SAF Intradisc plus Integral air suspension system with disc brake.
Holland 3510-150 Fifth Wheel.
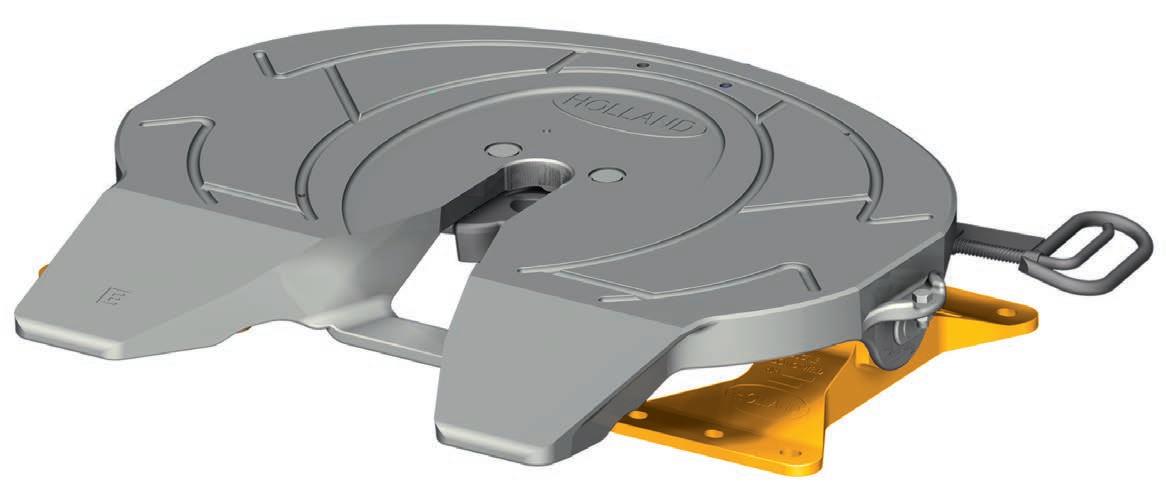
downtime to a minimum. SAF-Holland has products that fit all applications – semi-trailers, A-doubles, B-doubles, road train A-triples, super quads and truck and dog combinations. However, the company understands that many unique applications need very specific solutions, therefore its team is ready to answer calls and technical queries from customers trying to find the best fit for their business needs. “SAF-Holland Australia has a good foundation to build upon,” Mario says. “We have an experienced and knowledgeable team, with the right attitude to drive the business forward. We’re very customer focussed Our company’s aim, not just here in Australia but also in Europe, is to take direction from the customer and offer them what they need to make their operations more efficient with less downtime.” Stephen believes Mario’s vision for the business, his leadership skills and over 35 years’ experience in sales, supply and manufacturing of road transport equipment and componentry will pave the way for greater success for SAFHolland in the near future. “I’ve known Mario for a long time, as have many of our customers,” Stephen says. “Mario’s excellent leadership skills, his level of expertise, his strong industry experience will influence the way he steers our ship and helps SAF-Holland become the business partner of choice for the industry, and to give the industry those solutions they need to excel.”
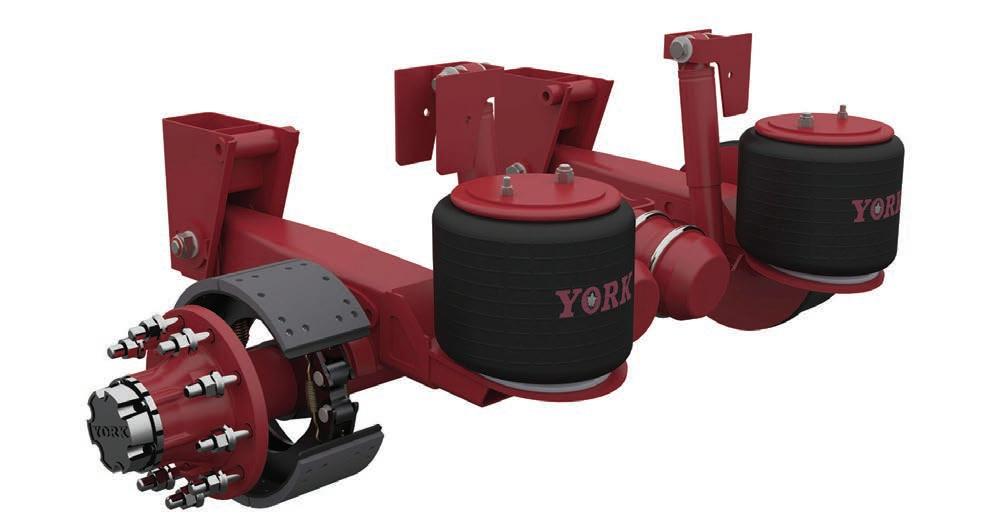
York Duratrac air suspension.
NEWAY
Neway product line has been around for many decades and it just works. • Trouble free operation • It is designed to take on the most rugged vocational vehicle applications • Single, tandem and tridem configurations • Superior traction and braking performance
A BULLISH
FUTURE
Meritor is ramping up efforts to capture a larger slice of the electrified global truck component market. The company is building on the success of its traditional MTT-14X drive axle and has recently moved into full production of the electric equivalent — the 14Xe ePowertrain solution for Original Equipment Manufacturers like PACCAR.
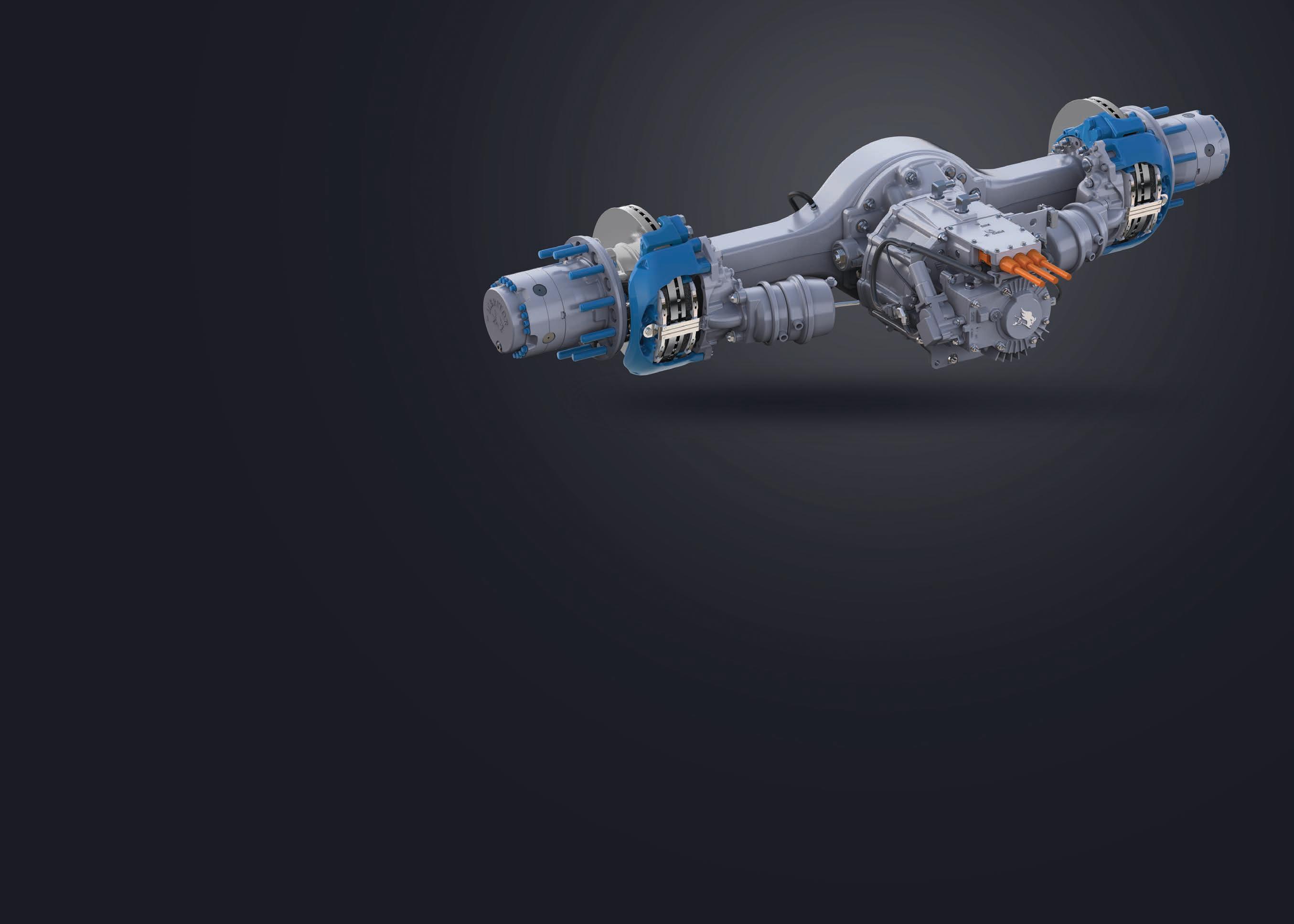
Meritor has long been renowned for its expertise in producing some of the toughest and most durable axles and drivelines on the planet. As part of its Blue Horizon strategy, to capture the rapidly developing electrification market, the company is evolving its core components – such as the MT-14X drive axle – into new products that also include electric drive units, control modules, inverters and power and battery management systems in order to meet the needs of the future. In fact, Meritor says it’s MT-14X epowertrain platform can cover around 60 per cent of current on-highway truck axle applications making it a prime candidate to develop further as the electric drive marches forward. The result of this is the MT-14Xe which capitalises on the modular capacity of the standard axle while elevating it to the level required for a new generation of electric trucks. The company has noted that electrification represents a risk, due in part to vertical integration by Original Equipment Manufacturers (OEMs), and that scale is required during the transition to electrification. Expectations are that an elongated global truck cycle will continue through 2025 and that the company plans to generate $USD1.5B of electrification revenue in 2030. This will be split between Heavy Duty, Transit (bus), and Medium Duty, with Meritor citing the latter as a category with potential for significant growth. In fact, the company commenced production of its 14Xe ePowertrain, which can be adapted to fit various powertrain needs based on vehicle application and duty cycle spanning Classes Five (medium duty) to Eight (heavy duty). The 14Xe ePowertrain is a fully integrated, all-electric drive system that is claimed to be the first and, at this stage, only integrated electric powertrain being produced for Class Eight trucks in North America. “Our 14Xe ePowertrain has been thoroughly tested doing real world miles hauling heavy loads in various conditions and multiple applications,” says Chris Villavarayan, Meritor Chief Executive Officer and President. “This new product enables us to offer the industry a proven, all-electric, zero emissions solution.” The 14Xe ePowertrain, which is produced at Meritor’s manufacturing facility in Asheville, North Carolina, is designed to provide efficiency, performance, weight savings and enhanced space utilisation. It is based on Meritor’s proven 14X axle housing, which maintains existing axle mounting locations and hardware for ease of OEM integration. The modular design enables the
Meritor 14Xe ePowertrain.
interchangeability of key components, including electric motors, transmissions, gearing, brakes, wheel ends and housings to suit individual customer specifications. Meritor’s electric drive solutions for an evolving market encompass three distinct architectures including Remote Mount Direct Drive, Remote Mount Multi-Speed and ePowertrain Fully Integrated. The company states that advantages of the first option are its speed to market and lowest initial cost. These advantages are also common to the second option, although it’s also said to be more efficient than the direct drive format. However, according to Meritor, its fully integrated ePowertrain is the superior solution of the three because it offers the highest efficiency, more battery space and lower weight. When it comes to specifications of the 14Xe ePowertrain, the core axle components – what Meritor terms its Legacy Content – includes either a fabricated or cast steel housing to suit conventional or independent suspension. A wide range of differential ratios is available ranging from 2.67 to 6.57:1. Wheel ends are available in either standard or hub reduction along with disc or drum brakes. Meritor has vast experience in producing these core driveline components stretching back 110 years. Today the company reportedly produces more than eight million gears annually including helical, spur, worm, straight bevel, spiral bevel, hypoid and amboid at facilities in North America, South America, Europe, India and China. Over the years Meritor has continuously refined its gear manufacturing and metallurgical processes – including precision and near-net forging, machining, grinding, heat treatment, case hardening and testing – in order to optimise efficiency, power density and noise control. It is this wealth of core gear manufacturing expertise that enables the company to leverage efficiencies in its differentiated ePowertrain solutions. To transform the core Legacy Content MT-14X axle with its high efficiency hypoid gearing into the 14Xe, Meritor incorporates an electric motor with application-specific continuous power/ peak torque outputs of either 150kW/ 1,000Nm, 180kW/ 1,000Nm or 200kW/ 1,100Nm. Transmission choices include fully integrated planetary one- or two-speed or dual countershaft two- or three-speed units. An inverter with base application software and controls works in harmony with a Power Control Module (PCM) which features transmission shift control logic along with pedal and efficiency mapping. At this stage Meritor has supplied the electric powertrain for more than 180 vehicles produced by a range of OEMs across various market segments. These include heavy-duty prime movers, refuse trucks, terminal tractors, school buses and reach stackers. PACCAR is a prominent player in the heavy-duty and refuse sectors in North America and Meritor is the primary supplier of battery electric systems including power control and accessory system (PCAS) and ePowertrain for Peterbilt 579EV and 520EV as well as Kenworth T680E models. Closer to home, Meritor has collaborated with PACCAR in Australia to develop the conventional MT-4014X tandem drive axle assembly used in the DAF CF340 8x4 that is custom
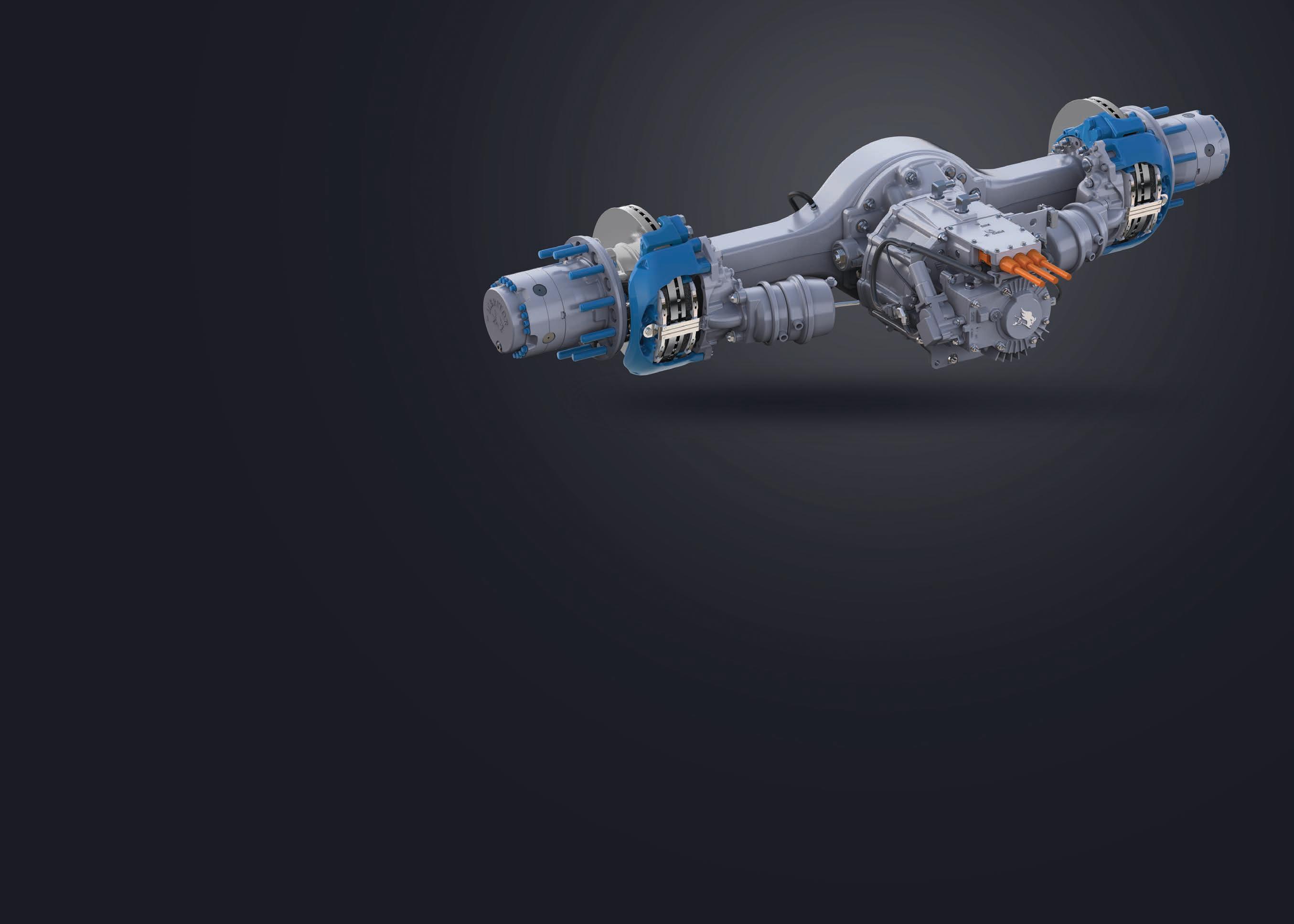
designed and built for front loading waste applications. The big news with this development is that around 500kg has been pared from the vehicle’s tare weight. According to Adam Carroll, Meritor Australia’s Marketing and Product Manager, the MT-14X axle has been the most widely used axle sold into the heavy duty truck market in the USA since it’s release and was subsequently introduced to Australian Kenworth variants several years ago. Now, fitting this drive axle assembly to the DAF CF 340 for waste applications has served to make the vehicle competitive with other brands in this segment.
DAF CF 340 8x4 fitted with the Meritor MT-14X. “The extra weight in the DAF tandem drive assembly is due to the European specification which works well in the European markets where tare weight is not so critical,” Adam explains. “However, the Australian market is similar to the US in that tare weights need to be kept to a minimum in order to optimise payload capacity. This is certainly the case in the 8x4 front loader waste segment in Australia.” The weight was reduced by using Kenworth Airglide suspension grafted onto the Meritor MT-14X tandem drive assembly which also underwent modifications to enable the use of DAF European-spec wheel ends with 335mm Pitch Circle Diameter (PCD) stud pattern and Meritor disc brake assemblies in place of the typical Kenworth drum-braked 285mm PCD wheel ends. The end result was a phenomenal weight saving of around 500kg, without any sacrifice in performance or durability. “This collaboration really showcases the prowess and flexibility of Meritor’s local engineering and manufacturing capabilities,” says Adam. “As we embrace the shift to electrification we expect to be able to add even more value, configuring and adapting our epowertrain solutions to suit our unique local applications.
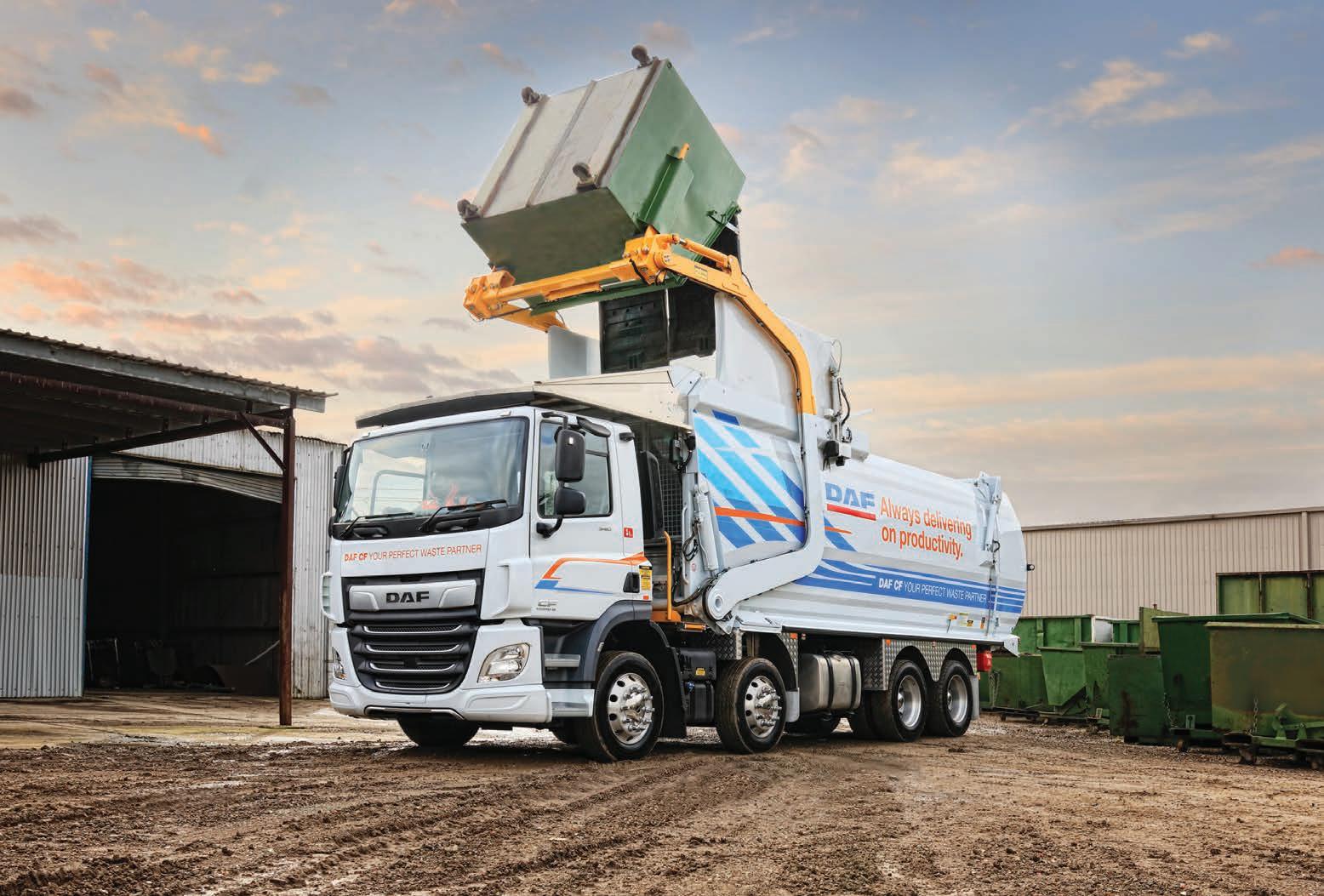
DAUNTING PROSP
Tiger Spider’s Marcus Coleman considers what a new era for Australian road transport will mean for future generations.
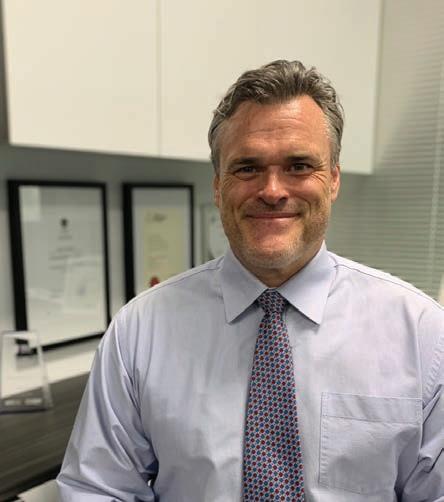
It’s been said that we’re living in the exponential age, so that the rate of change gets faster year upon year. For most of my professional life, whilst we’ve had economic ups and downs, the world has generally been stable. I have dim recollections of the cold war and a period of high inflation when a child growing up in the late seventies and eighties. But while alive, one could hardly say that I lived through those times. My grandfathers lived during the Second World War although they didn’t serve on the front line. One was on the farm working to feed the nation and the other an engineer making weapons at the Maribyrnong ordnance factory. The farmer maintained a stable of over 30 Clydesdales working the land in Maffra, the engineer worked on configuring the radar system for the Bofors gun, ensuring the anti-aircraft autocannons hit their target if Japanese fighters came over the horizon. I’ve always thought about how much the world changed during the lives of my now passed grandfathers. It’s hard to fathom the fact that I’ve probably witnessed more significant change than both and my children will probably witness double again. I was born in the late seventies but remember the milk man jogging behind an unmanned horse and cart, dashing door to door delivering milk in re-usable glass bottles. Until now it’s been a slow burn. Change has been constant, and while there have been significant geopolitical events like 9/11 and the global financial crisis, we’ve been able to muddle through with life rolling on essentially the same. Post-Pandemic, Russia’s invasion of Ukraine and with diesel prices over $2.30 at last fill, one does sense a tectonic shift in the global order. Many believe it’s the fourth turning as Generation Y ascends and the last of the silent generation pass away, an event that happens every 80-100 years. The internet is full of prophecy and much of it is compelling, predicting the decline of the American empire and the rise of China. We’re all impacted by these significant macroeconomic trends, but what does it really mean for the transport industry? Just over 100 years ago, in 1920, the 1941 km Princes Hwy was opened to connect Adelaide, Melbourne and Sydney. The Sturt Highway came in 1933, the Bruce in 1934, the Hume fully sealed by 1940, the Eyre opened in 1942 and the North-West Coastal Highway in 1944. The National Highway network along with the demands and constraints on rail and shipping associated with World War II kick-started the era of Australian trucking. Linfox was founded in 1956 and the first Kenworth was imported into Australia in 1960. The UNECE Vehicle Standards were formed with the 1958 Agreement and Australian Design Rules came into force with the 1989 Motor Vehicle Standards Act. State-based regulations and enforcement of truck size and axle weight limits began getting serious in the 1970s. We’ve since seen PBS and other regulatory reforms shape the transport industry. However, the overarching paradigm of on highway diesel truck has not changed significantly since inception some 80 years ago. Change has been on the horizon for decades as have concerns about environment and climate change. During my time in the industry there’s been a long list of new technologies attempting to shake up the industry and supplant the diesel engine. As a young engineer I worked on Permodrive, a regenerative drive shaft which stored braking energy in a hydraulic accumulator to improve fuel efficiency. It generated a lot of interest and startup capital, but the dream ended when the Rudd government withdrew R&D funding. We’ve also seen CNG and LNG vehicles come and go with little success. While the transport industry has continually innovated, it demands
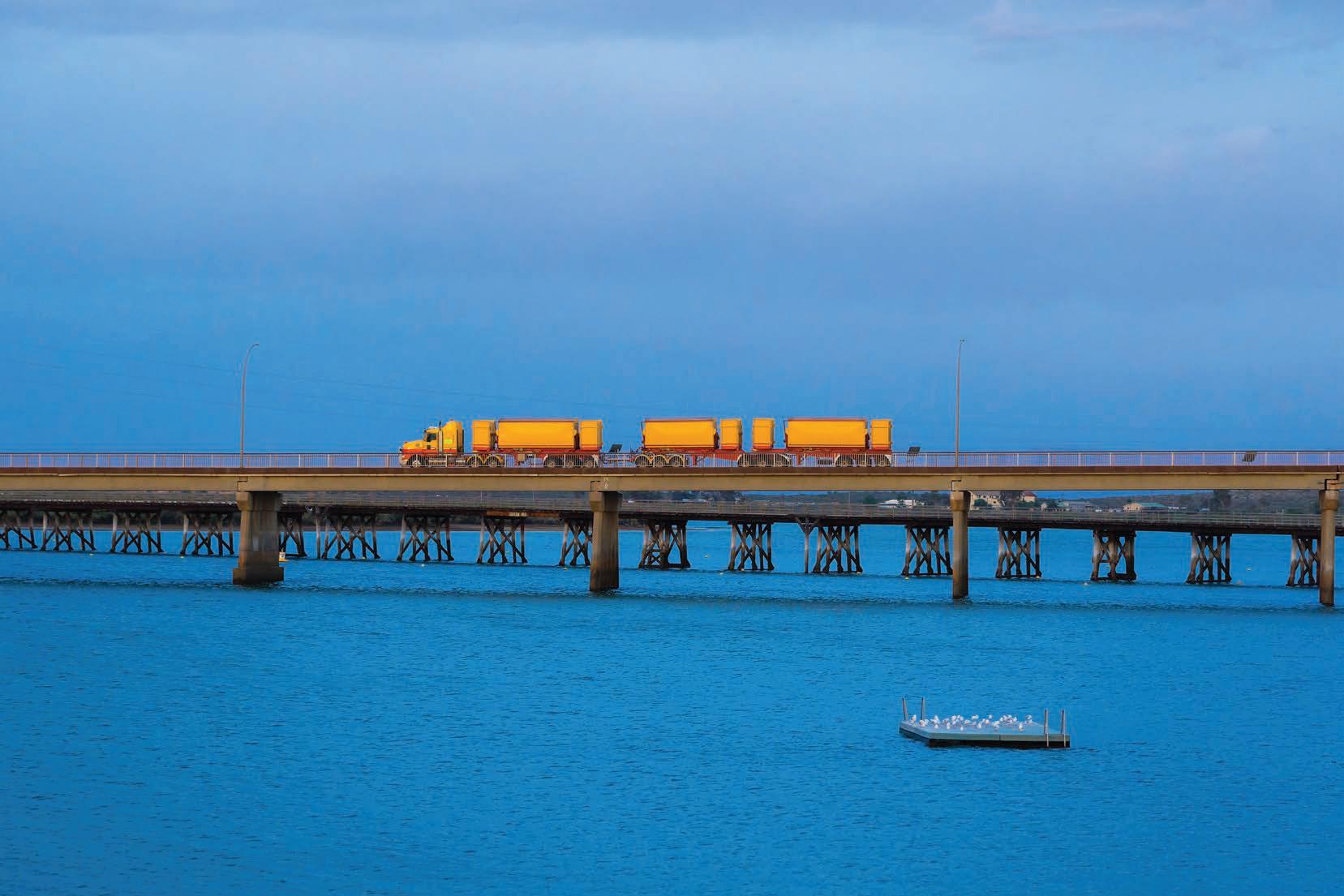
Marcus Coleman, Tiger Spider Managing Director.
ECTS
cost effective and reliable vehicles and those industry stalwarts that have lived throughout this incredible period of change have, perhaps correctly, concluded that zero emission and autonomous vehicles would not occur in their lifetime. There was a massive road infrastructure boom between 1920 and 1944. There are essentially no living Australians who remember a time prior to the national highway system. The Big Build underway will see billions in new highways and tunnels through our capital cities and, by 2040 hopefully the thousands of bridges built to support the vast Australian road network will have been upgraded to modern standards. Infrastructure and regulatory reforms to enable autonomous vehicles on our roads is a topic of debate globally. With Australian mining companies using these vehicles in controlled environments for some time we’ve had a chance to lead the way. However, rolling this out onto public roads is still a daunting prospect with the limitations of vehicle control without human interaction and the legal accountability of such systems on the road proving a high hurdle to leap. Recent incidents with passive vehicle automation being blamed for hit and run accidents provide an example of the difficulties to overcome. Stronger roads and bridges are needed to support the higher axle weights of electric trucks and buses. We need a network of electric fast-charging and hydrogen refuelling stations. Our roads need to be upgraded to be smoother, with fewer potholes, sealed shoulders, safety barriers, better lighting, consistent line marking to safely accommodate autonomous vehicles. The first Diesel truck was available in 1908 but the trucking industry didn’t take off until after national highway infrastructure was in place and two world wars were fought and won. Hopefully we can avoid World War III and just get on with the business of building the infrastructure for the next century and herald in a new era of Australian Road Transport.
A multi-combination roadtrain crosses a bridge in Western Australia.
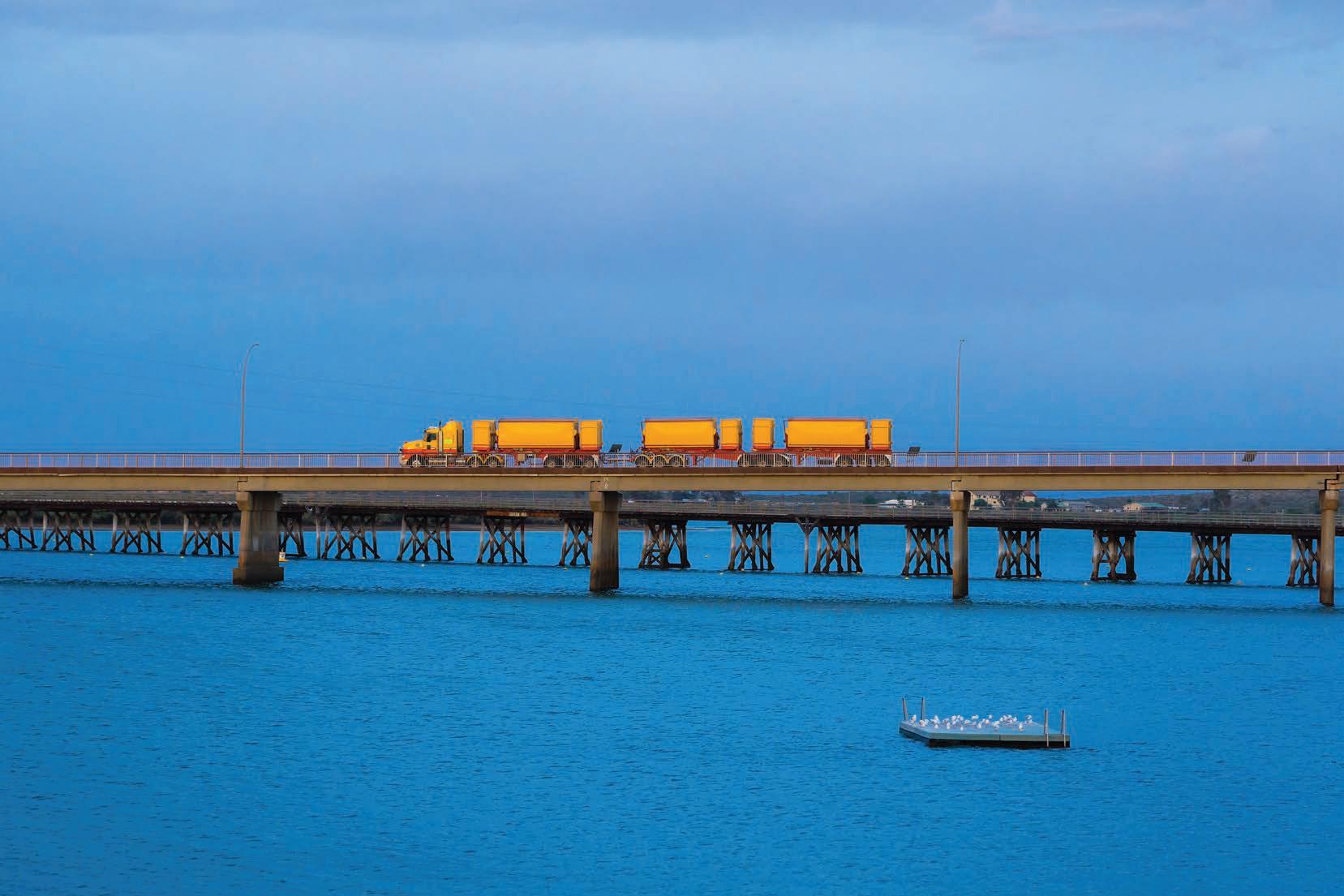