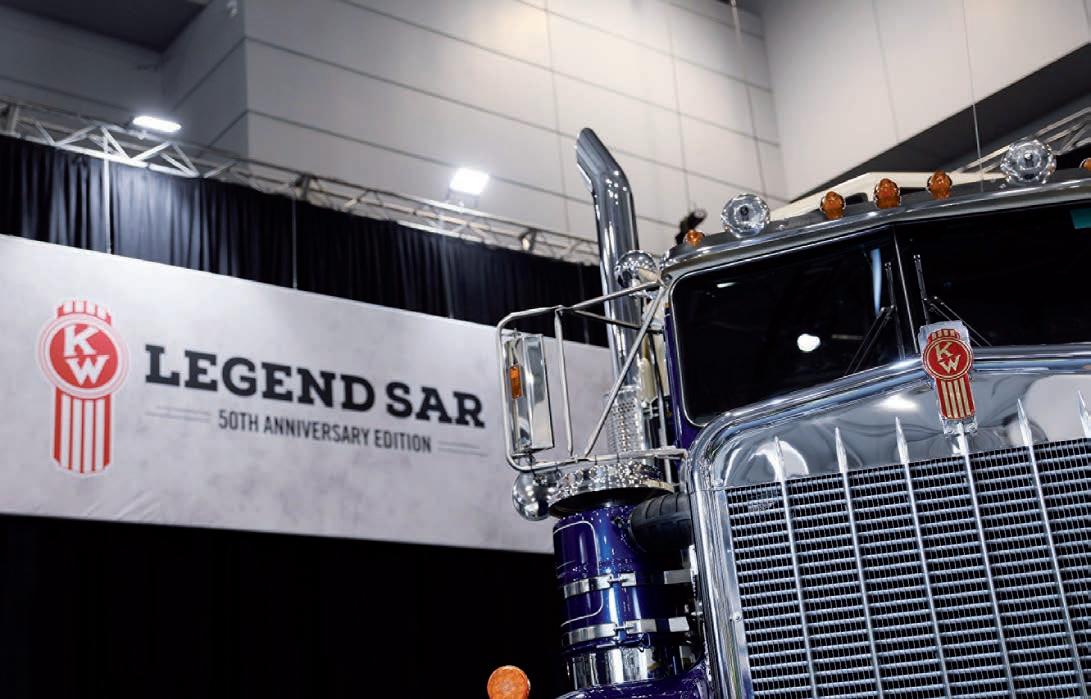
84 minute read
Prime Mover News
by Prime Group
> Kenworth debuts 50th Anniversary edition Legend SAR truck
New Kenworth Legend SAR launched in Brisbane.
Based on legendary Kenworth models from the past, the third in the series of special edition Kenworths, the Legend SAR, has been unveiled. Following the outstanding response to the Legend 950 in 2015 and the Legend 900 in 2017, the timing of the much-anticipated debut of the Legend SAR is aligned with Kenworth celebrating 50 years of manufacturing trucks in Australia. The 50th Anniversary Edition Legend SAR combines the latest technology for safer, cleaner and more productive operation, with features that embrace Kenworth’s unique heritage. Modelled on the iconic W900SAR, built and sold in Australia from 1975 until 1985 and the first Kenworth model designed, the Legend SAR is engineered and made in Australia specifically for Australian operating requirements. With its sloping bonnet and raised cab position allowing for the first use of under cab battery and toolboxes, the W900SAR (SAR standing for ‘Shortbonnet Australian Right-hand drive’) is considered an iconic fusion of the W900AR and S2 models. Importantly, it could take the high horsepower engines favoured by Australian transport operators and still carry the maximum legal payload within existing length limits and was lighter than the AR and Kenworth’s cab-over model of the day, the K100. Built to honour the character of the first all-Australian Kenworth truck, the Legend SAR represents the iconic appeal of the much-loved W900SAR. While more than 45 years have passed since it first went into production and other SAR models have ensued, the allure of the original ‘SAR’ still remains and is reignited with the release of the third in the series of Legends, the Legend SAR. “The truck not only commemorates 50 years of proudly manufacturing Kenworth trucks in Australia, it symbolises what was a turning point for local design and engineering and the custom-build philosophy that Kenworth is still renowned for today,” said Brad May, PACCAR Australia Director Sales and Marketing. “In addition to recognising our long heritage in this country, the Legend SAR pays homage to all those that have stood, and stand today, behind the badge of a Kenworth truck. The ones that have helped make Australian-made Kenworths an integral part of the unique Australian landscape.” Appropriately named ‘Son of Nugget’ as tribute to the iconic W-Series limited edition ‘Gold Nugget’ released in 1984, the Legend SAR was officially unveiled at the Brisbane Truck Show in May. The Legend SAR includes a full suite of heritage style limited edition features that celebrate the journey of Kenworth in Australia’s Road Transport Industry.
> Daimler names Dealer of the Year
Family-owned Mavin Truck Centre has won the coveted 2020 Daimler Dealer of the Year. Daimler Truck and Bus Australia Pacific President and CEO, Daniel Whitehead, presented the award to Mavin Truck Centre Dealer Principal, Dean Mavin, at a special event in Brisbane. The Daimler Dealer of the Year award recognises the best dealership representing the Daimler Truck and Bus portfolio of Mercedes-Benz, Freightliner, Fuso and Alliance Truck Parts brands. Mavin Truck Centre was, according to Whitehead, a deserved Daimler Dealer of the Year award winner. “Dean Mavin and the team and Mavin Truck Centre look after their customers like they are family,” he said. “This sharp customer-first focus is one of the reasons they are a key regional dealership for the Daimler Truck and Bus network in Australia and makes them a worthy winner of the Daimler Dealer of the Year Award.” The Kempsey-based Mavin Truck Centre has won several Regional Dealer of the Year awards for both Mercedes-Benz and Freightliner brands during the last five years, including the 2020 Freightliner Regional Dealer of the Year award. It recently added Fuso to its stable and opened a new dealership in Coffs Harbour, further boosting its customer support. Last year, the dealership also achieved Elite Support certification after implementing a raft of improvements. Daimler Truck and Bus Australia Aftersales and Network Operations Director, Greg Lovrich, said the Mavin Truck Centre team is always looking to improve customer experience. “Mavin Truck Centre is part of the positive transformation we have seen across the Daimler Truck and Bus network in Australia during the last few years,” he said. “They are prepared to invest and commit to improvements that make a big difference to our customers and help keep them on the road getting the job done,” said Lovrich. In order to achieve Elite Support certification dealerships must meet 129 criteria as part of the initiative introduced by Daimler Truck and Bus in partnership with its dealership network. Elite Support certified dealers across the country have, according to Daimler, seen improved customer satisfaction levels since they entered into the initiative.
Mavin Truck Centre Dealer Principal, Dean Mavin.
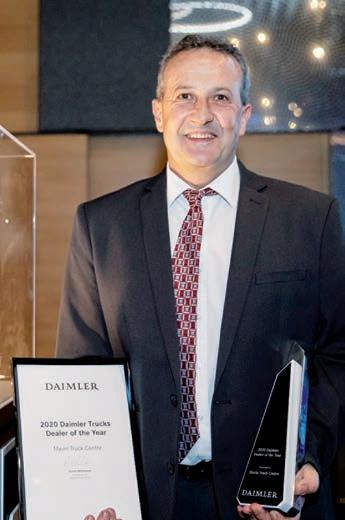
> Report reveals PBS vehicles involved in fewer major crashes
Findings from a new report reveals Performance-Based Standards (PBS) vehicles are involved in 60 per cent fewer major crashes than conventional vehicles. It represents a significant improvement over the results in a 2018 report which found 46 per cent fewer major crashes compared to the conventional fleet. The Review of Major Crash Rates for Australian Higher Productivity Vehicles: 2015 – 2019 report, a joint undertaking from the National Heavy Vehicle Regulator (NHVR), Chartered Institute of Logistics and Transport Australia (CILTA) and the National Truck Accident Research Centre (NTARC) looked at the reduced crash rates, fewer kilometres driven, and lives saved by using PBS vehicles. PBS vehicles are also forecast to save 143 lives over 20 years. NHVR Chief Engineer Les Bruzsa said PBS vehicles were achieving safety gains beyond what was originally anticipated. “In the last five years, PBS vehicles were involved in 60 per cent fewer major crashes than conventional trucks” he said in a statement. “PBS articulated combinations had the lowest rate of crashes per distance travelled with 5.4 crashes per 100 million kilometres travelled, compared to 17.6 crashes for their conventional counterparts — almost 70 per cent lower,” said Bruzsa. “Not only are these vehicles equipped with the latest in braking and safety technologies to help prevent crashes, but they are also productive – delivering more goods with fewer vehicles in a safe manner. Over the last five years Bruzsa said PBS vehicles travelled 1.6 billion fewer kilometres on Australian roads compared to conventional vehicles to transport the same freight task. “This huge reduction in distance travelled means improved safety benefits to our drivers, the community and reducing damage to our roads,” he said. Significant acceleration in the uptake of the PBS scheme has delivered a compound annual growth rate close to 43 per cent. “There are now more than 12,000 PBSapproved combinations operating across Australia,” Bruzsa added. “Further growth will deliver greater safety and productivity benefits, supporting a strong and prosperous Australia, and the saving of more lives on our roads.”
> Rum City Foods lands milestone Scully RSV Hino 500
Refrigerated truck specialist, Scully RSV, has taken delivery of its 100th Hino 500 Series Wide Cab. Widely considered an Australian industry leader, Scully RSV builds approximately 300 trucks a year, approximately half of which are sold to customers with the remainder forming Scully RSV’s rental fleet. According to Cameron Hogg, Scully RSV General Manager producing quality vehicles is at the core of what Scully RSV is about. “The Hino range of trucks has always been one of the market leaders in quality – we have never been disappointed with any Hino trucks, and they continue to get better,” he said in a statement. “The Hino 500 Series Wide Cab is one of the workhorses of the Scully RSV fleet given its high quality build, safety features, comfortable ride and superior drivability,” said Hogg. Over the last ten years, Scully RSV has purchased over 480 Hino trucks, with the Hino 500 Series Standard Cab a chassis favoured by its customers. Like the 99 before it, the milestone 500 Series Wide Cab is a FL 2628 with a six-speed automatic transmission, and was built for Rum City Foods, a familyowned and operated food and beverage distribution company based in Central Queensland. “Scully RSV have been supplying vehicles to us for more than 25 years, and as a trusted partner to our business, we are proud to be part of this milestone celebration for Hino and Scully RSV,” said Scott McIntyre, Rum City Foods Sales Manager, whose father founded the business in 1978. “It’s always great to bring another reliable and quality vehicle to our fleet,” he said. Brian Wright, General Manager of Sales and Supply Chain for Hino Australia congratulated Scully RSV on the milestone. “We are proud to partner with Scully RSV – both of our organisations are focused on delivering quality products to our customers,” he said. “Since its launch in 2017, we have sold over 3,800 500 Series Wide Cabs – Scully RSV is one of many customers that appreciates the safety, quality and transmission options of the 500 Series Wide Cab. “The 500 Series Wide Cab was a gamechanger for Hino – it boasted the most comprehensive active safety package of any Japanese truck in the mediumduty truck segment at that time,” said Wright. “It was the first truck in its class to feature Vehicle Stability Control (VSC) and a microphone-equipped, night vision enabled reverse camera as standard fitment.” The 500 Series Wide Cab’s safety package also includes ABS, Anti Slip Regulator (ASR), ECE R29-rated cab strength, driver SRS airbag, ADR84/00 Front Underrun Protection (FUP), Easy Start, Cruise Control and Fog Lamps. “Transmission options include six speed Allison automatic available across the range, or synchromesh manual in either six speed or nine speed dependent upon the model selected,” Wright said.
Jeff Nicotra, Cameron Hogg, General Manager of Scully RSV, Scott McIntyre, Sales Manager for Rum City Foods, Damien Scully, Craig Andersson, Dealer Principal, Sci-Fleet Hino and Will Gaulton.

> New Scania G 540 XT primed for construction boom
Scania Euro 6 G 540 XT.
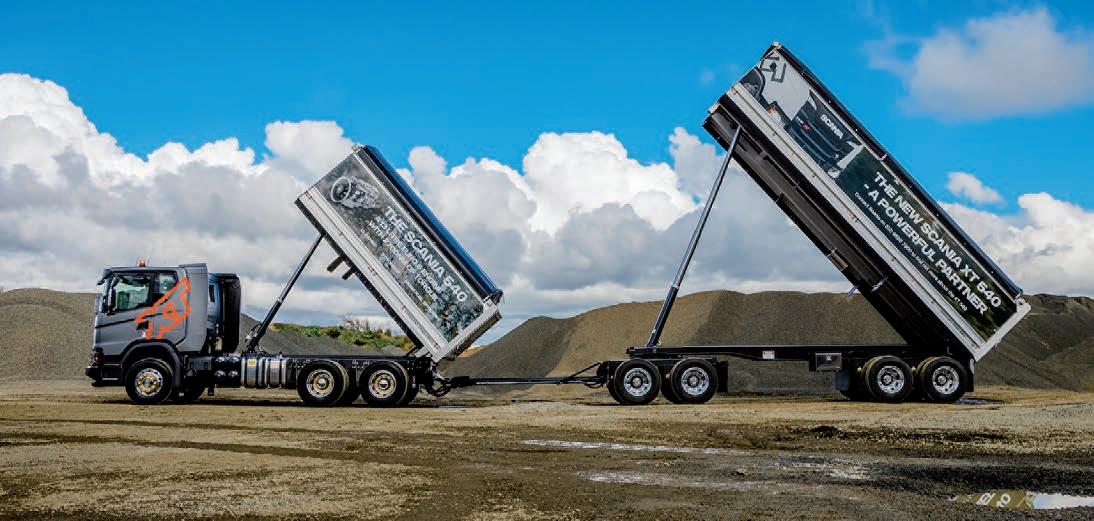
Tipper and dog operators have been given a glimpse of Scania’s new G 540 XT. The commercial vehicle manufacturer expects the market for high demand power applications to take to the new 540 hp six-cylinder SCR-only Euro 6-compliant engine that it claims delivers 2700 Nm of torque — 100 Nm more than its nearest rival. Businesses seeking superior total operating economy from tipper and dog operations are likely to appreciate its elevated chassis for superior ground clearance and its quarry and construction site friendly features that protect the lights and front of the vehicle. These are supported by a 150 mm protruding steel bumper with integrated tow-hook, as well as a front under bumper bash-plate. Introduced in late 2018 as a solution for builders and contractors working in the booming construction, civil engineering and infrastructure sector, the XT range is equipped with the most powerful sixcylinder in the company’s bracket of modular engines. Rated to 75 tonnes GCM and with peak torque available between 1000 and 1300 rpm, Scania can offer even smoother acceleration more than likely to be appreciated by drivers at traffic lights in built up areas. Where front axle weight is critical, the engine, according to Scania, excels on low-down driveability, with adequate torque to make shifting loads uphill seamless. The inline six-cylinder engine saves around 300 kg over the front axle compared with the Scania V8s which have proven popular with the likes of tipper operators to date. Updates include new friction-reducing coatings on pistons, rings and bores, increased compression rates and higher cylinder pressures, the adoption of smart auxiliary pumps, and modified inlet and exhaust manifolds, all of which work to reduce fuel consumption by up to 2.5 per cent. Paired with a Scania GRSO905R overdrive 14-speed gearbox, the 540 hp derives an extra 40 hp over the previous iteration courtesy of Scania XPI fuel injection, and a new ball-bearing fixed geometry turbocharger which delivers more useable grunt. The G 540 XT tipper is fitted with side curtain roll-over protection airbags and a steering wheel-mounted airbag as standard. Further advanced safety features include advanced emergency braking (AEB), electronic stability program (ESP), lane departure warning (LDW), adaptive cruise control (ACC), driver and passenger seat belt pretensioners, auto hill hold, and LED head and taillights. “Scania is very pleased to add the 540 hp engine to the very successful XT family for construction and civil engineering tipper work. We expect this combination to be very popular as it offers an excellent mix of performance and economy,” said Dean Dal Santo, Scania Australia Truck Sales Director. “Scania continues to provide greater torque than its rivals at identical horsepower outputs and the new 540 XT is no different, giving our customers an advantage in terms of driveability and fuel efficiency,” he said. “The Scania 540 engine has proven itself to be frugal and powerful on Australian roads in the eight months that it has been available for haulage operations. We know that construction and infrastructure work has equally tough operating environments: high payloads, gruelling city driving in congested streets as well as for the drivers, long hours behind the wheel. That’s why the combination of Scania’s traditional strengths of comfortable and quiet operation will be enhanced further with the addition of this more potent, higher output engine.”
> Velocity opens Daimler account with huge Goldstar Transport order
Perth-based Goldstar Transport has taken delivery of the first batch of commercial vehicles in an order of 50 new Mercedes-Benz units it recently placed. The order marks the first major delivery for Velocity Vehicle Group, the US headquartered dealer group that acquired the Eager’s Daimler Truck business earlier in the month. Part of a metropolitan distribution contract newly awarded to Goldstar Transport in Perth, the Mercedes-Benz Actros vehicles are a combination of Euro 6-rated 2643 and 2646 6x4s for single trailer ambient and refrigerated freight ferrying into non-regional retail sites. Every unit is equipped with brand new JSK42AW fifth wheels supplied and manufactured by JOST. In Australia it represents the first in the books for the Velocity Vehicle Group. Goldstar Transport Managing Director Sean Carren said the MP5 package and the Velocity team’s ability to deliver several dozen units in such a short space of time made it a compelling offer. “Aside from being a solid piece of equipment, it’s a best-in-class vehicle and the driver training package included made it an easy decision to make,” he said. “All of our requirements were met pertaining to timing, schedules, technology and fuel efficiency,” he said. “The people at Velocity and MercedesBenz involved in this deal were the ones that made it happen. We like the efficiencies and safety benefits these vehicles bring to our fleet, but ultimately we buy trucks from people. They make these partnerships possible.”
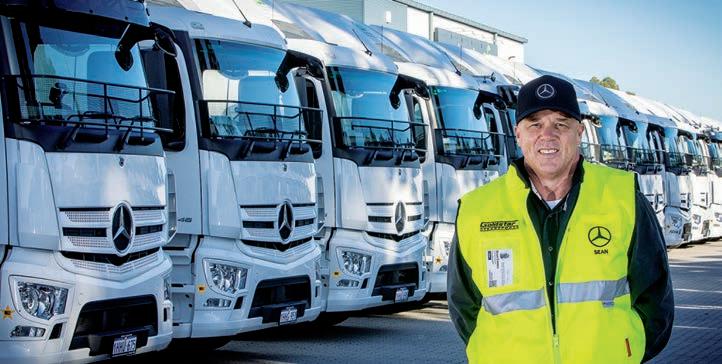
Sean Carren.
> Long-promised Strzelecki Track sealing underway
The sealing of the first 50 kilometres of the Strzelecki Track has commenced in South Australia. A vital supply link historically used by outback roadtrains supplying major oil and gas facilities located near Moomba, the Strzelecki Track is also an essential transport corridor for outback communities, tourism and pastoralists. Stage 1 of the project, immediately north of Lyndhurst, has been allocated $10 million by the Marshall Liberal Government with another $125 million already confirmed by the Federal Government for Stage 2. An additional $64 million for sealing of the Strzelecki Track was announced by the Australian Government in the 2020-21 Federal Budget towards completely sealing the full length of the track. All 472 kilometres of the track will eventually be sealed following joint funding announced by the Federal Government and State Government of South Australia. As the Strzelecki Track remains an essential transport corridor for outback communities, tourism and pastoralists, the project is expected to help increase outback prosperity, productivity and road safety. Minister for Infrastructure and Transport, Corey Wingard, said unsealed roads contribute to higher direct freight costs, increased supply chain costs and the likelihood of accidents. “It is great that local small and medium companies have been able to partner with us to fix this crucial route,” he said. Pavement rehabilitation works on the first 50 kilometre section have been completed by South Australian company T&J Constructions, with sealing works completed by Downer EDI. Additional pavement widening and shoulder sealing of the previously-sealed 24 kilometre section now means a total of 74 kilometres of sealed road is open to traffic to improve travel reliability and efficiency. Santos Chief Executive Officer and Managing Director Kevin Gallagher said the funding commitments from the Australian and South Australian governments will grow jobs and encourage more development in regional South Australia. “Each year hundreds of trucks with equipment and supplies for the Santos operated Moomba Gas Plant and surrounding gas fields are sent via the Strzelecki Track,” he said. “The conditions of the track can vary widely causing delays and costly maintenance for the operators of the vehicles and damage to the equipment they carry,” said Gallagher. “The sealing of the track will ensure one of Australia’s great inland roadways is safer to travel for freight and logistics, tourists and pastoralists. This will increase productivity and trade and bring benefits to all users and communities in the region.” Pre-construction activities for the next two packages of works, a 10 kilometre section south of Innamincka and a 93 kilometre section south of Moomba to the Strzelecki Creek crossing are now underway.
> NHVR approves fifth EWD for heavy vehicles
The National Heavy Vehicle Regulator (NHVR) has approved another provider of electronic work diaries (EWD) for use in Australia. The decision to approve Quallogi by Kynection, making it now the fifth EWD option to receive regulatory approval, was announced at the Brisbane Truck Show. “Drivers have been switching over to using an electronic work diary since we approved the first system in December last year and it’s great to see Quallogi is also available as an alternative to the National Written Work Diary,” said NHVR CEO Sal Petroccitto. “The introduction of EWDs means drivers can record their work and rest hours by pressing a button, rather than spending time ruling lines and counting multiple time periods on multiple pieces of paper,” he said. The Quallogi system includes features, such as alerts, to assist drivers to manage their compliance with work and rest rules. It will be available on selected devices, which are outlined on the NHVR website. Heavy vehicle drivers can confirm via the NHVR website if the EWD they are using has been officially approved by the NHVR. Drivers must continue to carry their written work diary for a transition period, to ensure that they comply with the requirement of carrying 28 days of records.
> Shell launches carbon neutral lubricants range
Global lubricant leader Shell has launched a range of carbon neutral products it recently announced. The initiative is the largest and most significant carbon neutral program in the lubricants industry today, aiming to offset the CO² or equivalent (C0²e) emissions of more than 200 million litres of high-quality lubricants. Shell provides approximately five billion litres of finished lubricants annually to customers across the world. The company’s expansive industry reach spans aviation to power generation, marine to mining and both consumer and commercial automotive. As well as helping to avoid or reduce emissions through material choices and operational efficiencies, these products are now carbon neutral in accordance with Shell’s global portfolio of naturebased carbon credits. “These lubricants help to keep the world moving by ensuring machinery can operate consistently and efficiently at the peak of its performance,” Shell said in a statement. To help it meet a target of becoming a net-zero carbon emissions energy business by 2050 or sooner, Shell
Workers at the Viva Energy facility in Geelong. acknowledges its lubricants business has a large part to play in achieving the goal. According to the company, there is an ongoing need to balance increased operational output with reduced environmental impact. Shell recognises as demands evolve, expectations also change. “Customers and consumers alike now expect brands to offer sustainable solutions that make it easier for them to make sustainable choices,” it said. “We know our customers are increasingly in need of sustainable solutions. So, to meet this growing industry demand, Shell is exploring a range of initiatives that seek to avoid, reduce and offset emissions while helping consumers and customers to find solutions that benefit both their operational and sustainability goals.” The extended range of carbon neutral lubricants is suitable for heavy duty diesel engine oil, premium passenger car motor oil and industrial portfolios. “Our carbon neutral lubricants provide customers with more sustainable choices without compromising the high performance and engine protection that they expect from Shell,” the company said. “By helping customers manage their sustainability needs, and by avoiding, reducing and offsetting our own emissions, we can help drive change for the better.”
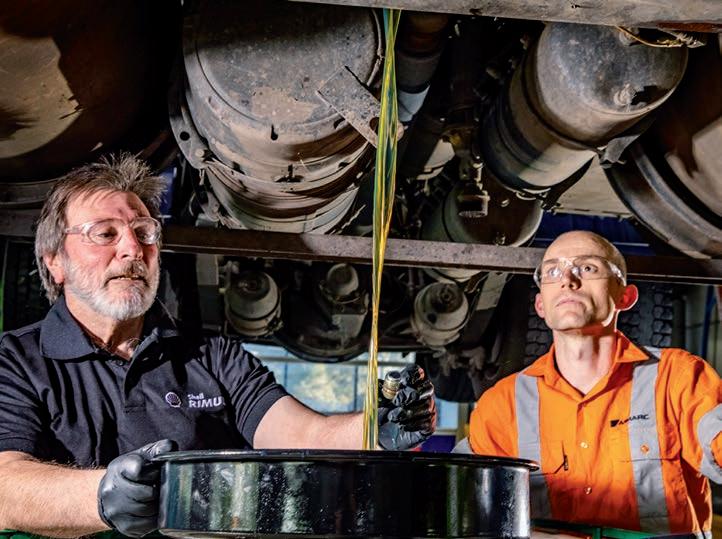
> Daimler commences testing fuel cell truck
Mercedes-Benz GenH2 Truck.
Commercial vehicle manufacturer, Daimler Trucks, has gotten closer to testing fuel cell vehicles on public roads. Recently, the prototype Mercedes-Benz GenH2 Truck began a rigourous evaluation program. During an extensive series of tests, the vehicle and its components were assessed on continuous operation against different weather and road conditions and according to various driving manoeuvres. Daimler Trucks is focusing on hydrogen-powered fuelcells for the electrification of its vehicles for flexible and demanding long haul transport. The company confirmed it was aiming to achieve ranges of up to 1,000 kilometres and more without any stops for refuelling. Development engineers at Daimler Trucks are at present designing the GenH2 Truck so that the vehicle and its components meet the same durability requirements as a comparable conventional MercedesBenz Actros. In metrics this will look like 1.2 million kilometres on the road over a period of ten years and a total of 25,000 hours of operation. According to Daimler Trucks, the vehicle has, during the first few weeks of testing, already covered hundreds of kilometres under continuous load on a road-torig test stand and gone through many extreme situations that are based on reallife operating conditions. Further examples of this include emergency braking and kerbstone drives along the test track. According to its development plan, the vehicle will also be tested on public roads before the end of the year with customer trials scheduled to begin as early as 2023. The first series-produced GenH2 Trucks are expected to be handed over to customers starting in 2027. Martin Daum, Chairman of the Board of Management of Daimler Truck AG said program was currently moving ahead to schedule. “We are consistently pursuing our technology strategy for the electrification of our trucks. We want to offer our customers the best locally CO2-neutral trucks — powered by either batteries or hydrogen-based fuel-cells, depending on the use case. We’re right on schedule and I’m delighted that the rigorous tests of the GenH2 Truck have started successfully,” he said in a statement. “The hydrogen-powered fuel-cell drive will become indispensable for CO2neutral long haul road transport in the future. This is also confirmed by our many partners with whom we are working together at full steam to put this technology on the road in seriesproduction vehicles. “Moreover, considerable momentum is being generated by the clear commitment of national and European regulators to the use of hydrogen for road freight transport. Political support plays an important role in promoting the creation of an infrastructure for green hydrogen and making an economically viable use of fuel-cell trucks possible for our customers.”

> MAN TGX takes honours at design awards
The functionality of the new MAN Truck Generation has impressed an international jury at the iF DESIGN AWARD following its recent Gold award in the German Design Awards. Earning praise for its choice of materials and colours, the MAN TGX particularly impressed for its practical design of the driver’s workplace. The workplace is defined by three systems that can be operated independently of each other. On one hand the instrument cluster can be found, while on the other the media and navigation system which features a display of up to 12.3 inches where the MAN SmartSelect operating element is conveniently located. In long haul cabs, the interior remote control for controlling comfort and entertainment functions from the rest area. Each system has its own truck-specific control logic and is at the same time integrated into what MAN Truck & Bus considers an holistic interaction concept. Göran Nyberg, Executive Board Member for Sales and Customer Solutions at MAN Truck & Bus said he was delighted by the recognition afforded the MAN TGX amid competition from nearly 10,000 entries from 52 different countries. “We are very proud of this new award. It’s a great recognition of the creativity and passion of our entire design team,” he said. “The new trucks are real MAN and lionstrong companions for every driver,” said Nyberg. The jury of 98 independent judges acknowledged the high-quality and practical materials of the truck with the ergonomically perfected seating and sleeping comfort it offered. In addition to the numerous assistance and safety systems, the future-oriented connectivity of the new truck generation is designed to create a lasting contribution to simplifying the increasingly demanding everyday working lives of truck drivers. The interplay of expressiveness and practicality, according to Rudolf Kupitza, Head of Truck Design MAN, to facilitate the unmistakable overall appearance of the new MAN Truck Generation. “On the outside, the dynamic design combines progress, tradition and sustainability and creates a powerful and emotional truck personality with the lion logo. Inside, it is consistently geared to the driver’s need for an intuitive, safe and comfortable workplace and living space, even for long tours,” he said.
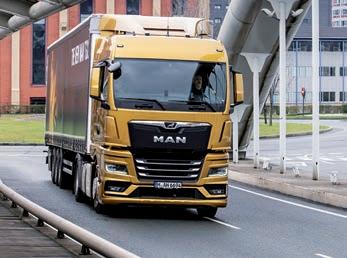
New truck generation MAN TGX.
Darren Wales, CEO
Let us take a load off your mind.
Heavy Vehicle Accident Repairs. Australia Wide.
At AMA Heavy Vehicle Accident Repairs we do one thing - and we do it well.
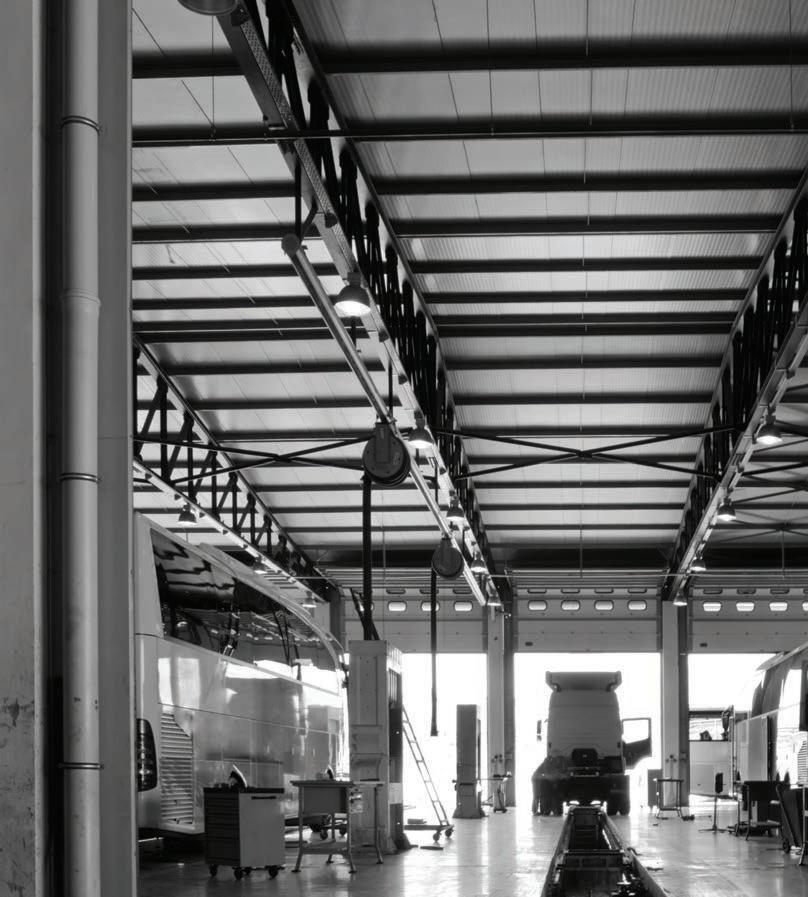
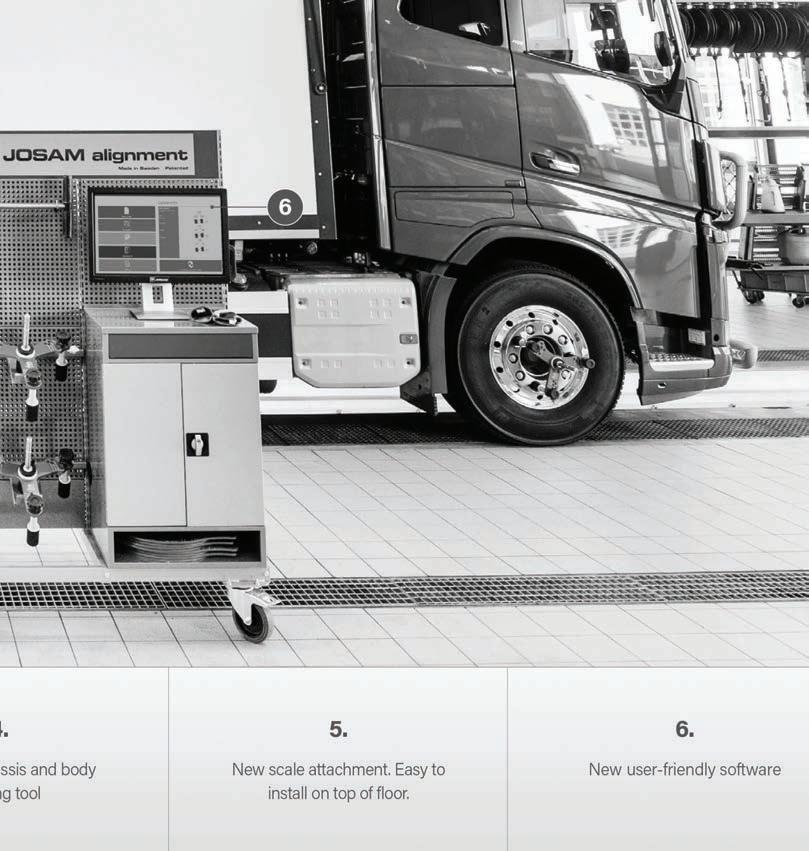
The superior craftsmanship from our experienced teamof repair professionals across Australia ensures your truck or bus is in the best hands. Our combined knowledge and ongoing investment in equipment, technology and people means we defeat the challenges of today, and into the future, for all types of heavy vehicles and trailers. And because we have strong and binding relationships with all major insurers we are able to quickly assess, quote and complete your repairs to ensure you are back on the road as soon as possible. Be safe on our roads, but if you need a repair contact us:
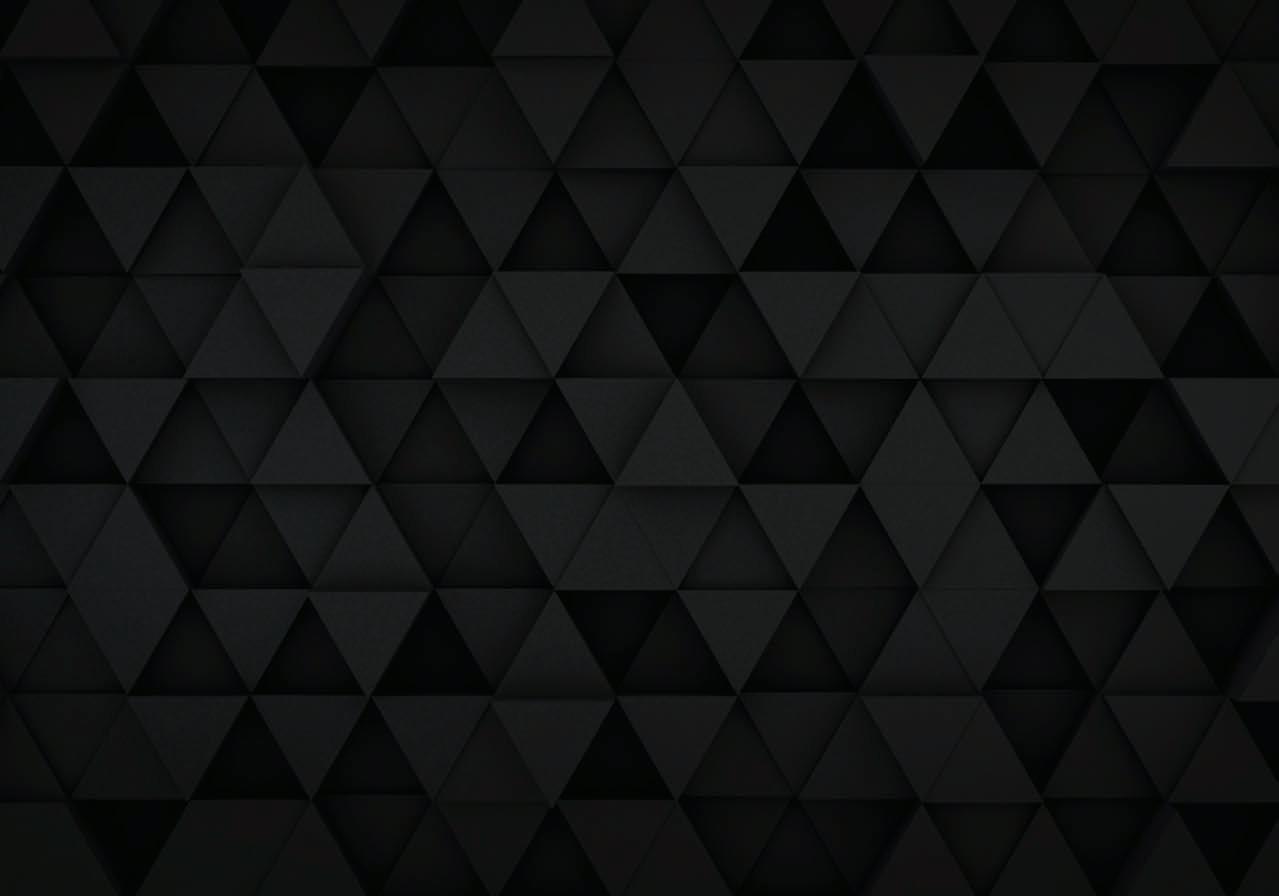
Phone: 1300-223-072 Email: info@amagroupsolutions.com.au Web: www.amaheavyvehicle.com.au
PERTH
ADELAIDE BRISBANE
NEWCASTLE SYDNEY
Iain Sharples
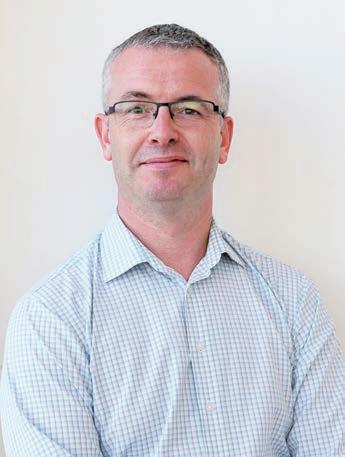
Iain Sharples is National Manager, Marine and Transport Liability at Zurich Financial Services Australia and has been in the insurance industry for the past two decades. He works with freight forwarders, logistics operators, port, terminals, charterers, marina operators and ship repairers to manage their marine liability.
NEW LEGAL POTHOLES IN THE INSURANCE LANDSCAPE
In this fast changing landscape some transport operators may learn that being considered a small business is as much of an advantage as a hindrance.
Imagine this: after colliding with a bridge, a transport operator is clearly at fault and probably negligent – but they can deny liability for loss or damage of goods under the terms of the contract. And, as a result, it will be up to the cargo owners or their insurers to try and find a way around that contract term. As it stands, the above scenario is lawful – but that could soon change following amendments to Australian Consumer Law (ACL). In particular, the Unfair Contract Terms (UCT) provisions have now been extended to cover general insurance contracts, potentially increasing liability exposure and insurance claims for transport operators. In the past, domestic transport companies have provided services based on an ‘all care but no responsibility’ approach when it comes to the carriage of a customer’s goods. This means they did their best to carry goods safely but, when failing to do so, they did not accept liability for the loss or damage of goods. Rather, there has been the expectation that the owner of the goods insured the cargo separately. I believe that this has tended to create difficulties for the transport operator, the cargo owner and the insurers involved. This is something we’ve been giving a lot of thought at Zurich in light of the amended UCT provisions, which remove the transport operator’s power to deny all liability – regardless of whether they are at fault or not. In fact, I anticipate that the strict contractual requirements on the timing of claims may now be deemed unfair, along with any clauses limiting the size of liability payments to small monetary amounts. Furthermore, clauses specifying very short collection periods before goods can be placed under lien and sold, with little or no notice to the customer, may also be deemed unfair. However, this is just the beginning. With more changes to the ACL announced last November, I think all parties in the industry need to consider the consequences of further extensions to the UCT laws. The exact timing of these changes remains unclear, but it’s expected that under the new amendments the small business definition will be widened to include any company with up to 100 employees. The current threshold for a small business is 20 employees. The coverage of small business contracts is also anticipated to be broadened by removing the dollar value threshold on the upfront price payable, currently $300,000 for less than one year’s duration or $1 million
where a contract is over 12 months. This means many more transport operators will have to comply with the ACL and the extended UCT provisions. As a result, I imagine that these companies may find that the courts will not allow them to deny or limit liability, pushing up claims costs and potentially impacting premium levels or policy terms, such as excesses. That said, we’re still in the early stages of seeing any impact from the changes as the widening of the small business definition is not yet in place. Interestingly, while more companies are using the existing UCT provisions to attempt to recover damages from transport operators, to date the frequency or value of successful court settlements has not increased. Nonetheless, the recent changes have had a long lead time, allowing many in the industry to be well prepared. The better operators got organised early, but in my mind some companies are still playing catch-up. To successfully negotiate any potential potholes, transport operators should get specialist legal assistance to review their contract clauses, softening or adapting these where possible so they are less likely to be deemed unfair by a court. I think it’s important for transport operators to demonstrate flexibility by allowing customers to select their preferred level of risk transfer. A customer should understand that they will be unable to make a recovery for damaged goods by agreeing to a defined liability level with the transport operator. Providing that insurers on both sides are aware of the position and understand the approach, this can be a viable insurance solution for all. To help transport operators deal with the changing landscape, Zurich will work closely with insurance brokers to ensure they comply with their policy’s terms and conditions. We can also recommend specialist law firms to assist transport operators in adapting their contractual terms, thereby ensuring they are properly protected. Cargo owners have relatively low-cost insurance cover available to insure their goods in transit and, considering the low profit margin that transport operators achieve, I expect that the contract terms between the cargo owner and the transport owner should reflect this. On reflection, it is possible that cargo owners may benefit from the changes since transport operators will be forced to accept a greater level of risk transfer. However, I anticipate that the new laws may also favour some transport companies as they will not have to accept the terms and conditions of large customers or those of their subcontractors. This is because the approach of ‘you sign it, or you don’t get the work’ will not be possible under the new UCT provisions. Consequently, I suspect that some transport operators may learn that being considered a small business is as much of an advantage as a hindrance.
More companies are using the existing UCT provisions to attempt to recover damages from transport operators.

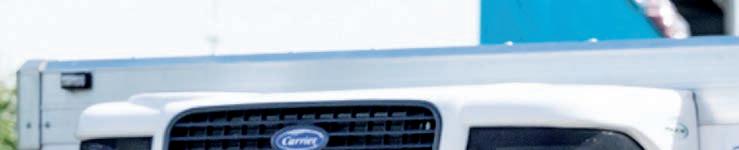
COMFCOLD


ORTS
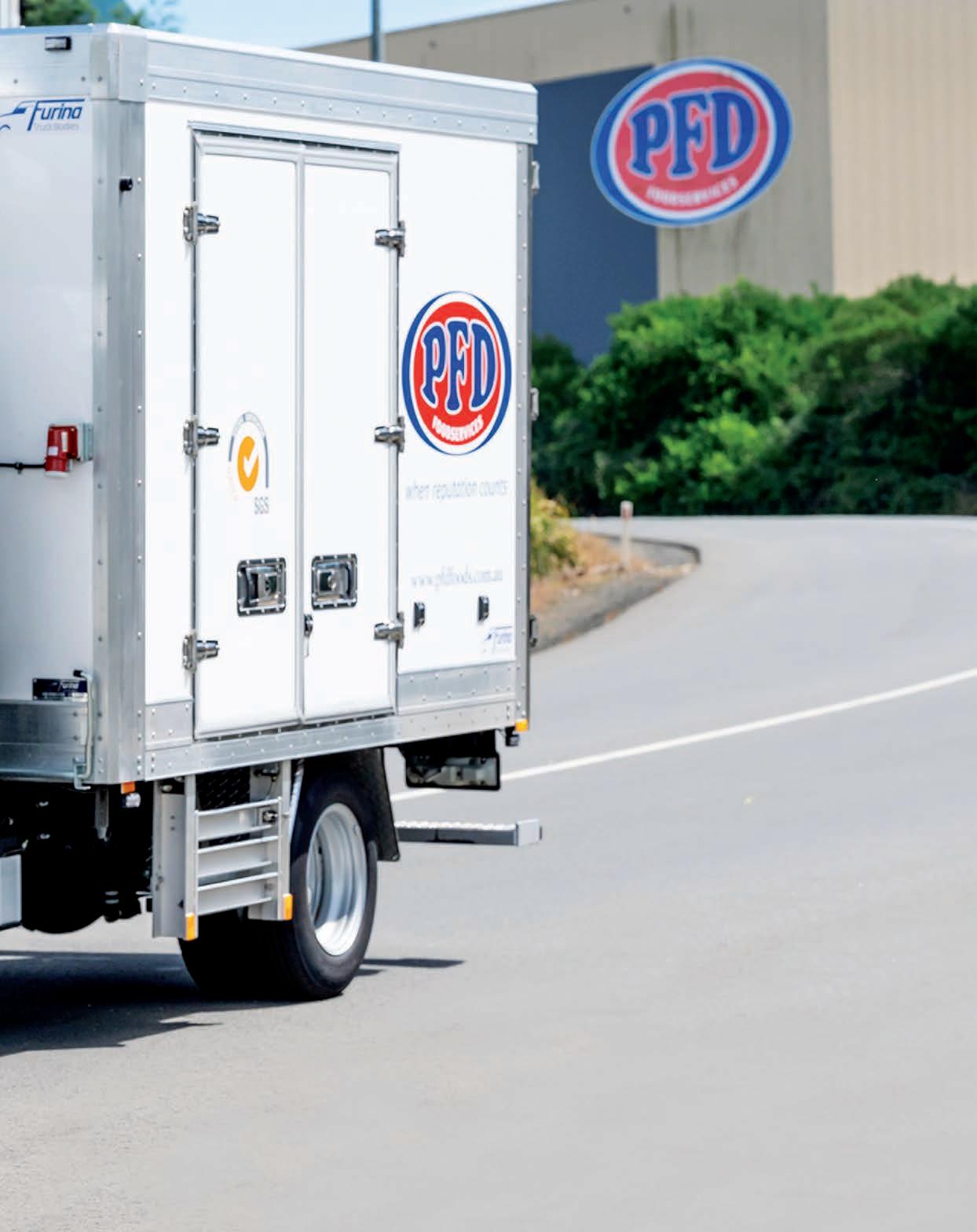
PFD Food Services ranks safety as a prime criteria in its decision to trial some of the latest Hino trucks.
The PFD Food Services story goes back to 1943 and today the company is a major provider with a broad range of dry goods, frozen and chilled products, fresh seafood and meat, confectionery, paper products and cleaning solutions mostly delivered direct to businesses associated with the food service industry. The clients of PFD are spread across a spectrum of venues where people need to eat, including clubs, pubs and hotels, cafes, airlines, restaurants, mines, aged care and retirement villages, resorts and theme parks, convenience outlets, venue and field caterers, fast food outlets, schools and kindergartens, and sporting, child care and even correctional facilities. One of the strengths of the PFD operation is its employment of its own transport division utilising company owned vehicles and company employed drivers. Steve Wright is PFD Food Services’ National Fleet Manager and has been with the company for around 25 years. When he started there PFD was still at the time a very much Victorian-based organisation. The company has since grown to be operating at 68 sites with a strong regional presence spread right across Australia. Steve has grown with it, progressing from manually unloading refrigerated containers into warehousing and store roles which also included maintenance work on equipment such as forklifts. Steve has been in charge of the company’s fleet comprising of around 750 light and medium duty trucks for the past decade. When he moved into fleet management Steve found that the fleet at the time was ageing and subject to numerous breakdowns and the resultant expensive repair bills. “I recall we had 18 truck engine failures in the six months prior to me taking on this position,” says Steve. “In the ten plus years I’ve been in the role we haven’t lost anywhere near that number in total.” Enthusiastic about the technical and mechanical aspects of his job involving trucks, bodies and refrigeration units, Steve follows through during his own time by tuning drag racing vehicles and
Steve Wright National Fleet Manager, PFD Food Services
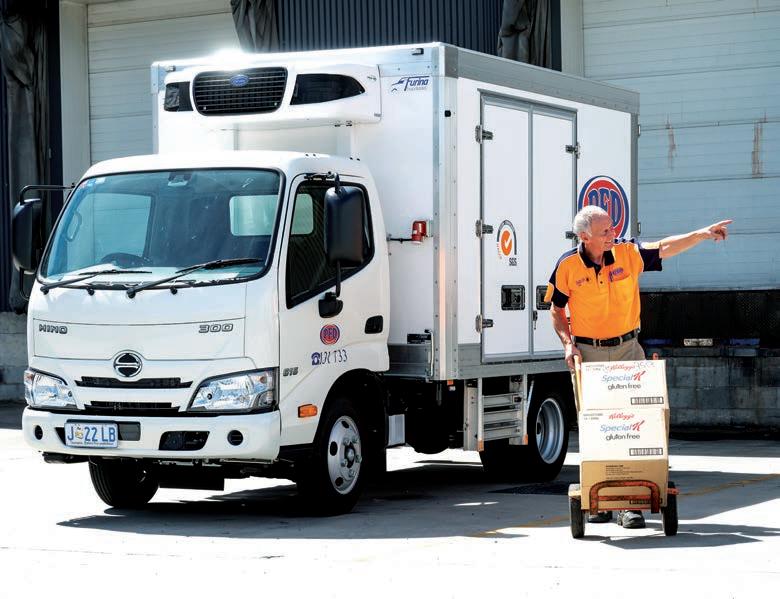
racing motorcycles with his sons. When the new Hino 300 Series was launched in mid-2020 PFD was one of the first fleets to take delivery of them with three currently operating in Tasmania. PFD also has had two Hino 500 Series Standard Cabs operating in Victoria during the past 12 months. Hino lays claim to offering Australia’s safest light-duty Japanese trucks, due mainly to the technology associated with Hino SmartSafe system. Hino SmartSafe is a comprehensive safety package with a suite of advanced driver assistance technologies which provide an active focus on protecting drivers and passengers as well as other road users. The standard fitting of the extensive suite of safety features were a major contributing factor in the decision to trial the Hino models in the PFD fleet. “Ten years ago I probably would have fought against buying Hinos but with today’s safety focus there is pressure to change that thinking,” he says. “Part of my own success has been due to people who didn’t want to take on change, or embrace the future, or embrace safety. They’ve made themselves redundant, so to speak. Safety is important not only to me as a fleet manager but it’s also of vital importance to the company. You have to be not just seen to be doing
Steve Wright PFD Food Services National Fleet Manager.
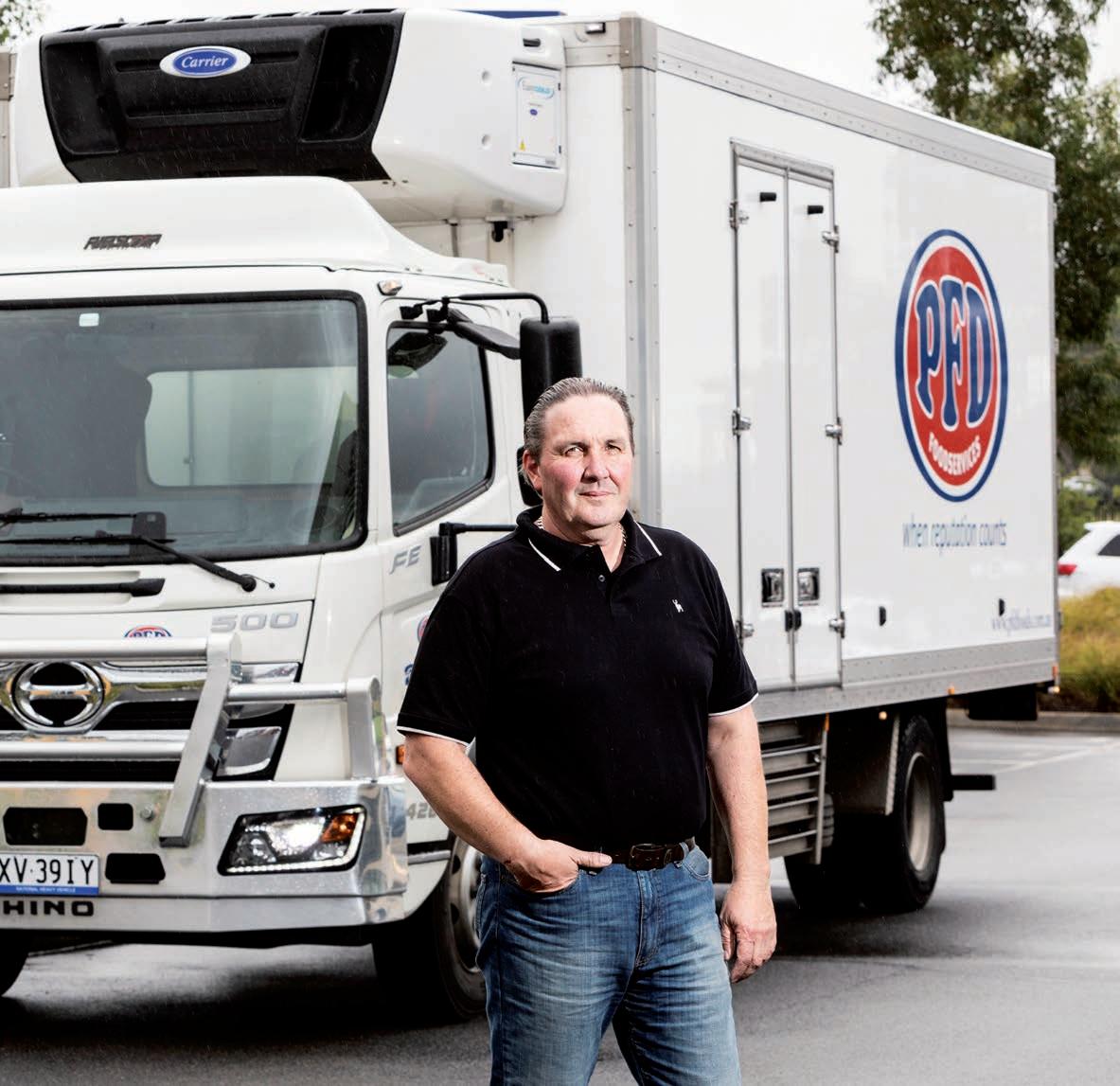
The purpose built refrigerated bodies have multiple temperature zones.
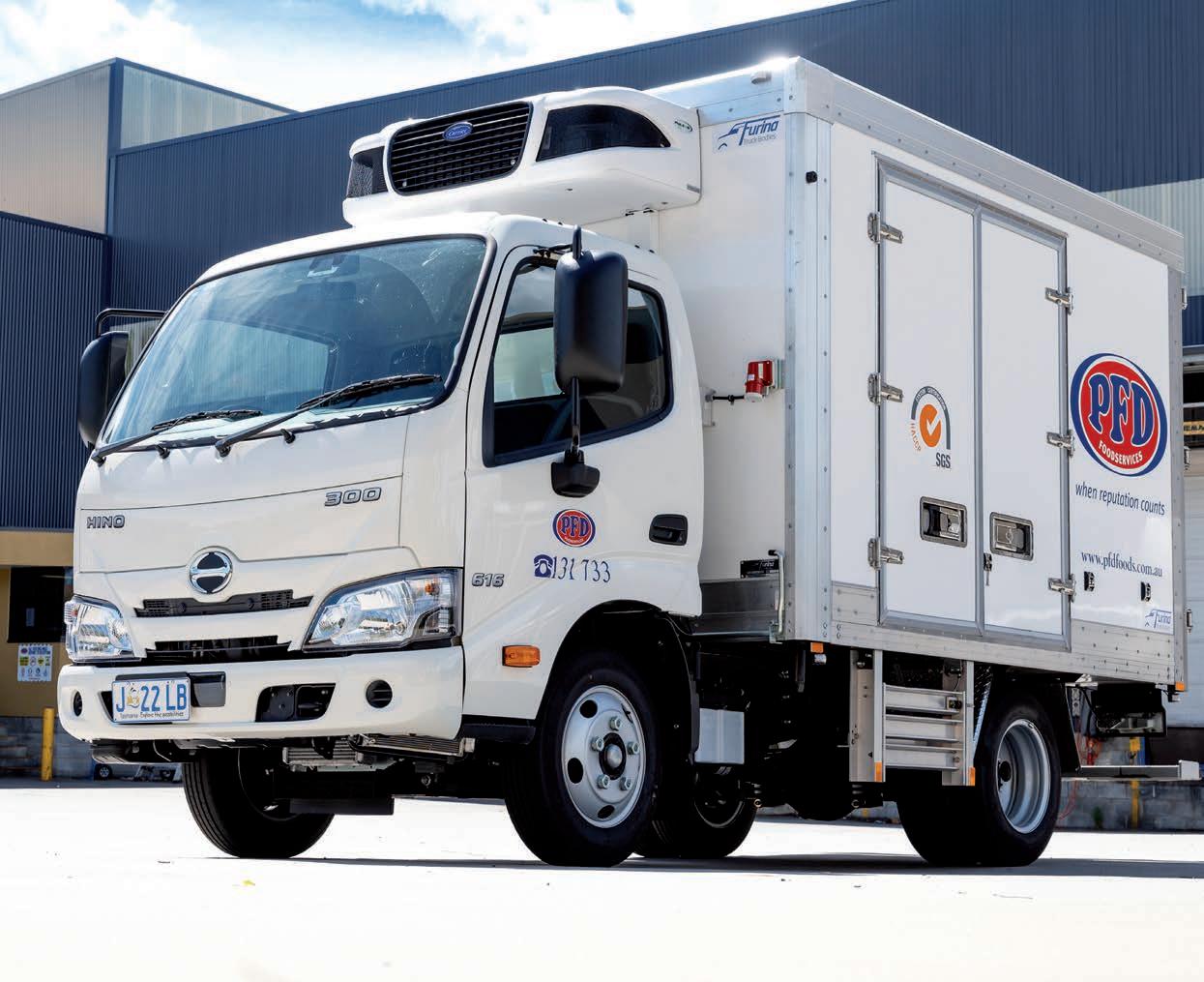
the right thing, you have to be actually doing it.” The Hino SmartSafe package integrates features such as the Pre-Collison System (PCS) which detects the possibility of a collision with a vehicle in front by using a combination of radar and image sensors and providing warnings to the driver. If the driver doesn’t react the truck’s brakes are applied autonomously. The system operates in a similar manner if a pedestrian is detected in front of the truck. Steve has become an agent of change and is quick to recognise that certain procedures are no longer appropriate even though they may have been acceptable even just five years ago. “I see the technology, things like the collision avoidance systems and electronic stability control they’ve got in their trucks now, and that can’t be ignored,” he says. Telematics also play an important role in the management of the PFD fleet which has resulted in significant improvements in the safety aspects coupled with a measurable rise in fuel savings. “We changed our whole driver culture based on our telematics system and essentially rewrote the company policy,” Steve says. “Due to constant monitoring, drivers can no longer speed undetected and speeding violations are minimal.” Compliance in terms of fatigue management and vehicle maintenance is managed by PFD’s in-house health and safety team who regularly audit all sites. Food safety is also a vital element in PFD’s business and all branches have an approved HACCP Plan (food safety program) to ensure all of the products supplied to its customers are safe and meet food safety requirements. An indication of the exceptional rigour of PFD’s food safety program has been demonstrated by the company being awarded the National HACCP Award for a Multi-site, Low Risk Company on two occasions. Steve runs the big fleet on principles similar to those applied by vehicle
Steve Wright National Fleet Manager, PFD Food Services
leasing companies, which sees the majority of servicing carried out by the manufacturer’s dealerships. All work has to be authorised via a formal work order issued by the fleet office which has access to comprehensive vehicle data such as whether the truck is still covered by warranty, and when was the last time a component, such as the clutch, was changed. Because of PFD’s national and regional footprint it is vital that any provider of major equipment such as trucks has a similar operational spread of dealers. Due to the large number of PFD branches and the nature of their operations, most PFD delivery vehicles work mostly in their own local area and do not register high annual kilometres. Consequently, trucks are able to remain active in the fleet for up to ten years due to their rigorous service regimes. “If you asked me what used to motivate me to buy a particular brand of truck I’d say it was the brand’s service network which was always the first thing because we’ve got so many branches and most are regionally based,” Steve says. “After that was the price and the product. Now it’s probably about safety, which may not have been mentioned ten years ago.” One metric which PFD uses to measure its fleet’s efficiency is the cost per kilometre to run a truck, and with a total of 32 million kilometres driven each year, it’s something which Steve and his team have been able to significantly reduce over the past decade. Steve has an interest in electric vehicles but maintains some reservations about the kind of impact the running of refrigeration units will have on compromising an electric truck’s operational range with current battery technology. There is also consideration of the additional weight of the batteries. Most of the PFD vehicles are fitted with purpose built refrigerated bodies with multiple temperature zones and incorporate specialised insulation to assist in maintaining stable internal temperatures in an application which involves multiple door openings during each shift. “Our fridge bodies are heavy. Equivalent size curtainsider bodies probably weigh nearly as much as a fridge unit on its own,” he explains. “We typically reach 60 per cent of our Gross Vehicle Mass with the truck still empty.” Other than those reservations concerning the practicality of electric vehicles using the currently available batteries, Steve is an enthusiastic supporter of evolving truck technology. “The more technology that becomes available in terms of things like trucks and telematics, the more I can see what the fleet is doing and how it’s behaving,” he says. “This should always influence how we operate.”
FTC MANAGER
Get the fuel tax rebate your business deserves
• First solution to receive an ATO
Product Ruling confirming the claim methodology is fair • Utilise second-by-second GPS data for accuracy • Paired with expert tax advice


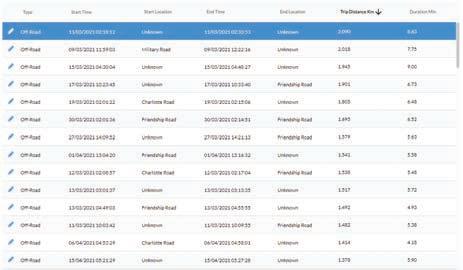

1300 111 477
PRIM
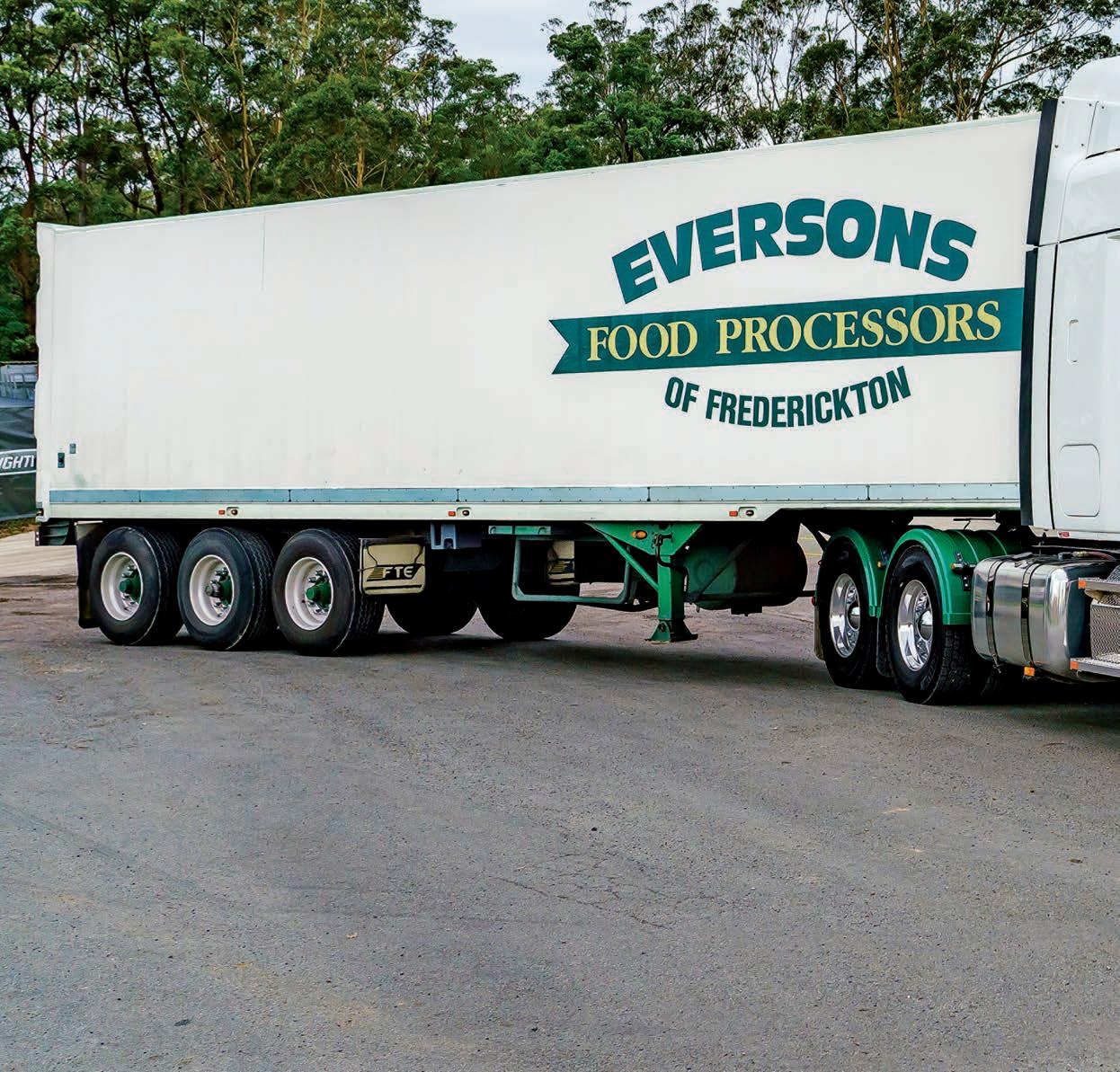
Everson’s Food Processors uses the latest in truck technology to deliver fresh cuts of meat across a wide expanse of terrain.
Everson’s Food Processors is a family-owned and managed multi-species abattoir and meat processing facility located in Frederickton, which is just north of Kempsey on the New South Wales mid-north coast. Everson’s supply meat products direct to Sydney, Newcastle, Gold Coast and Brisbane as well as to local butchers and supermarkets. Everson’s run a complete in-house operation from buying livestock, then processing and subsequently transporting the meat products to their customers. Previously the Everson’s operation was what the industry terms ‘service kill’ in that they would process customers’ cattle and lambs and freight the resulting meat back to them. Currently the business model leads more towards supplying wholesalers and butchers with packaged and dressed meats as well as full meat carcasses. Meat products are sold as far away as Perth and Far North Queensland, as well as into Victoria and South Australia. Everson’s own trucks deliver as far as the Sydney region and western New South Wales as well as to customers located just north of Brisbane. A growing market segment is the supply of mainly Halal broken lamb and carton meat direct to many Muslim butcher shops located in the Sydney region. Everson’s doesn’t export any of its meat products but has won an Excellence in Export award at the prestigious NSW Business Chamber State Business Awards. The award was in recognition of the sale of sheep skins direct to customers in China and Hong Kong which the Everson’s team negotiate themselves. Cattle hides are transported via an Everson’s tipper truck to Victor Topper at Gunnedah Leather Processors where, after further processing, they can be sold throughout the world. Jason ‘JA’ McKiernan is the transport manager at Everson’s and oversees a fleet dominated by the Freightliner brand with the Argosy and Columbia models recently being joined by a pair of Cascadia 116 prime movers fitted with 36-inch XT sleeper cabs. Both Cascadia’s are powered by Detroit DD13 engines
ECUT

with the DT12 automated transmission. The Cascadia’s are the twenty-first and twenty-second trucks that Everson’s have bought from Mavin Truck Centre in Kempsey and the tally includes 17 Freightliners and four Mercedes-Benz. The Cascadias are equipped with the fully-integrated Detroit Assurance 5.0 system which uses radar and high definition camera technology for Active Emergency Braking and to facilitate the Active Cruise Control. The system has the capability to detect a slower or stationary vehicle or even pedestrians, and in an emergency the Autonomous Emergency Braking can quickly bring the truck to a complete stop with no input from the driver. Lane departure warning, intelligent (self-dipping) high beam and automatic wipers and headlamps are all also standard equipment, as are anti-skid brakes, traction control and Electronic Stability Control. A good relationship with their local truck dealer, recently announced as the Daimler Dealer of the Year, makes good sense to Jason. “We’ve been dealing with Mavin’s for years and they have been really helpful with everything, and always have been,’ says Jason. The introduction to the Cascadias happened in a novel way. “Steve Pinkstone from Mavin’s just turned up in a Cascadia one day and gave me a call and asked me to come out the front and have a look. We went for a spin and by that afternoon we’d ordered two.” The Cascadias’ safety is further enhanced by the Sideguard Assist system which uses two short-range radars (one aiming forward and one aiming back) on the kerbside to warn the driver if the trailer can collide with objects such as utility poles or street signs when turning left (Trailer Sweep Assist) and also warns the driver if they are about to merge left into a lane already occupied (Turn Assist). This blind spot safety system uses audio warnings as well as a yellow light on the kerbside A pillar to alert the driver of a potential collision. “We started off with Freightliner and
Everson’s have deployed two new Cascadias with 36” sleeper cabs into their Freightliner dominated fleet.
we’ve always had Freightliner prime movers and smaller Freightliners for our rigids,” says Jason. The integration of some Japanese cab over rigids into the fleet has not been the success that was initially hoped for so the decision has been made to go back to bonneted Freightliner models for all rigid applications. The Argosys and the Columbia prime mover have manual transmissions, as do two of the Columbia rigids. The three latest Columbia rigids and both of the new Cascadias are automated manual transmissions. The autos are used mainly on the coast-based routes and Jason prefers to use experienced drivers in manual transmission trucks on runs up over the steep Walcha Mountain to access the New England area. FTE is the preferred brand of trailer combined with Thermo King refrigeration units. “They’re the best and you won’t get better,” says Jason. “We can use a refrigerated pantech on rigids over life of three or four trucks. We recently sold one that was here when I started 25 years ago.” The onboard truck and Navman telematics provide an insight into the Cascadia’s operational efficiencies and the trucks are usually fuelled out of the onsite bowser without the need to purchase fuel when out on the highway. “The fuel savings are unreal. Last time I checked we were using 20 per cent less fuel on a trip from here to Sydney than the others,” says Jason. He is also impressed with the reliability and integration of the Detroit engine and gearbox package. The semis carry full loads of meat every night of the week to Sydney where there are large wholesale meat centres in South Strathfield and Blacktown, as well as to Newcastle where Everson’s has its own depot. Jason aims to have the Cascadia drivers leave Frederickton by 3.00pm during the week, with their first drop usually at

the meat hall at South Strathfield. After unloading they can have their break and head home and generally arrive by 9.00am. If there is any meat brought back it is unloaded on the dock at the Frederickton facility and the trailers and rigid bodies head to the hot water wash out bay to be thoroughly cleansed. To ensure driver freshness the trucks are usually driven by different drivers on alternate nights of the week. In recent years the livestock industry has been affected, like most of the agricultural sector, by droughts, fires and the challenges of dealing with COVID. “The industry is hot and cold at the moment and getting livestock in to process and to sell is a big challenge,” explains Everson’s General Manager Shane Webber who has been with the company for 21 years. “Fires and floods lead to shortages so the price goes up. We’ve had a hard couple of years, but we haven’t shut for one day. Currently the supply of sheep and lamb is OK but cattle is a nightmare and the prices are the highest I’ve ever seen. Numbers are low and some abattoirs are only working two to three days per week. We’re multi species so we do lamb, beef and goat and can swap and change but beef-only abattoirs are doing it hard.” In common with many regional industries Everson’s has to deal with a shrinking workforce. “It’s not too bad for us,” says Shane. “We’ve got two floors going but we just can’t get enough staff so we’ve moved to running one crew on two floors. Upstairs will do the lamb until lunchtime and come down and do cattle until 3.00 or 4.00 in the afternoon. In a perfect world we’d have two crews going at once.” Despite having around 210 employees across the Everson’s group, Jason is constantly on the lookout for more good drivers. “I’ve got a good crew around me at the moment and I could do with another couple,” Jason says. Local drivers, who go in and out of butcher shops, need to be strong to be able to handle the 60-odd kilos of a carcass on their shoulders. “It doesn’t bother our blokes but for some newcomers it does,” says Jason. “I’ve been interviewing blokes for 19 years and the tactic now is to walk up to a truck, pull the ramp out sit it on the ground and ask how they’d go running up and down that 200 times a night with 60 kilograms on their shoulder. That’s when you know straight away if you’ve got another driver or not.”
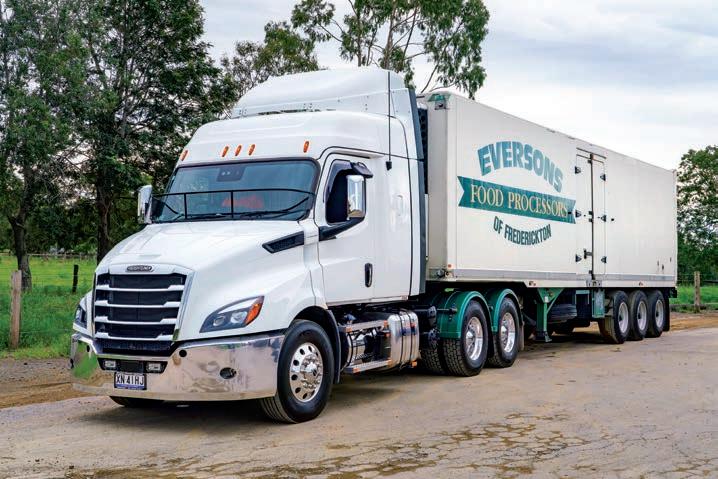
New Freightliner Cascadia 116.
Truck driver Mark Willard, Steve Pinkstone Mavin Truck Centre Sales Manager, Jason McKiernan Everson’s Transport Manager.
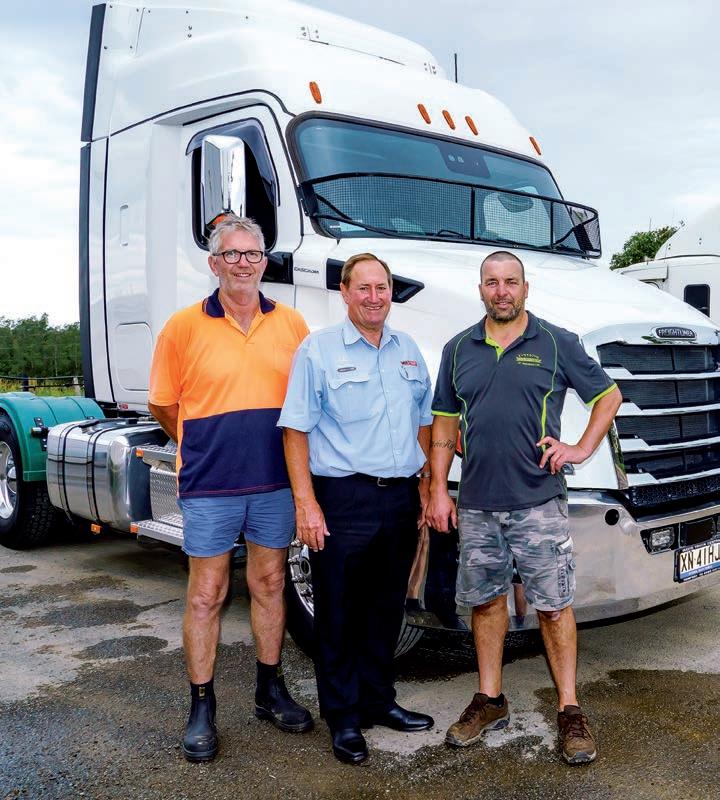
An STG Global water truck built on an Isuzu F Series vehicle.
BODY OF EVIDENCE
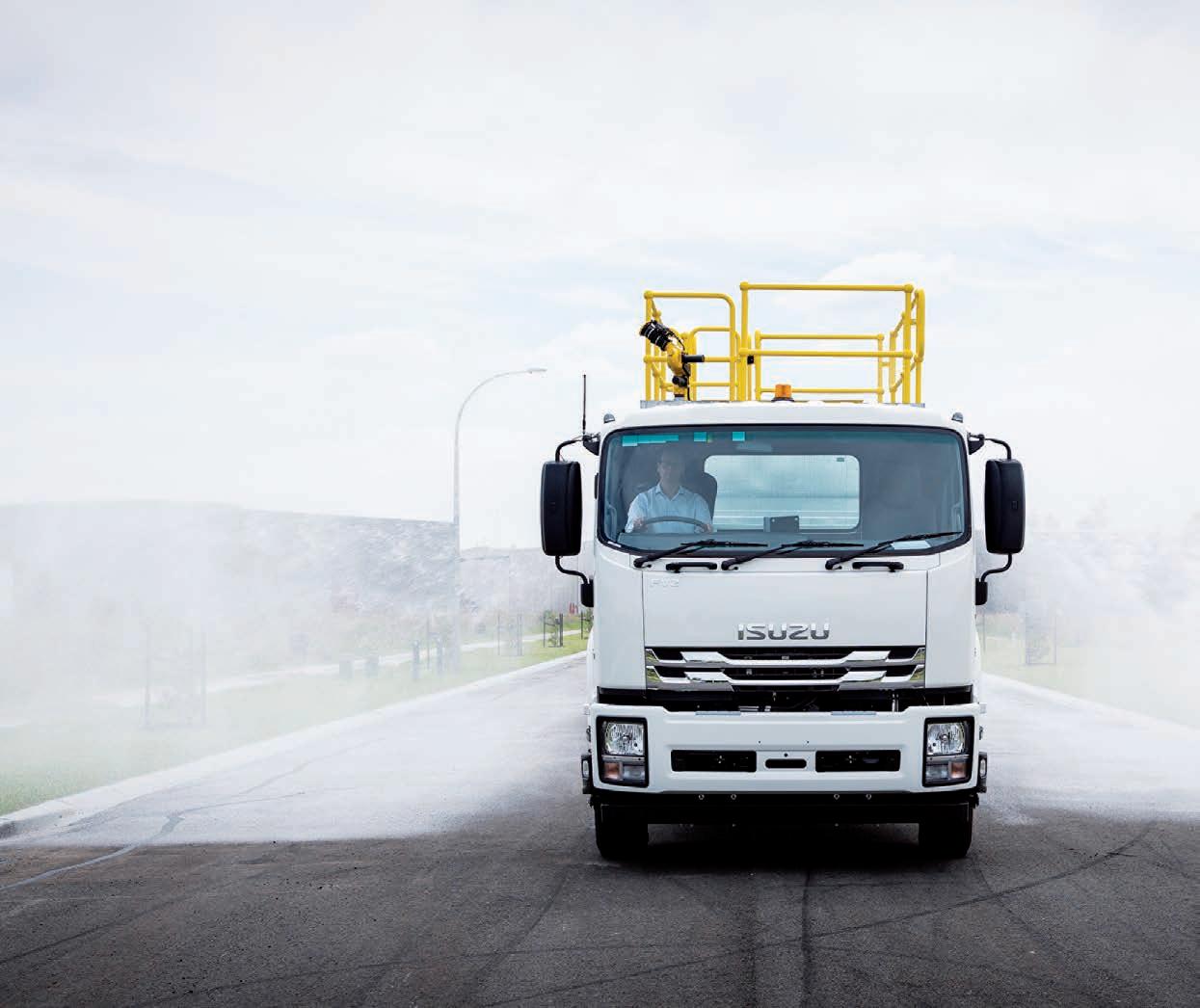
STG Global is a specialist body builder that predominantly uses Isuzu trucks as the basis of its builds. Having very short average build times of three weeks in addition to ready built stock on the floor means customers get their vehicles in record time.
The STG Global story starts in the small country Victorian town of Mansfield over 30 years ago when brothers Ross and Regan Yendle – a couple of young ground-breaking farm boys hit by drought and hard times – are looking for a way to keep the income rolling into the family farm. With the bank pressuring the family to sell, the entrepreneurial lads begin tinkering in the shed and brainstorming ways to save the farm. One hot summer’s afternoon, the boys spot a huge cloud of dust drifting off a construction site in town. Sensing an opportunity to make some money, they approach the site foreman and enquire about work. “Nothing here fellas, but if you know anyone with a water truck, let me know,” is the foreman’s somewhat dismissive reply. With equal measures of both desperation and quick wittedness, the boys respond in unison, “We have a water truck at the farm ready to work!” After negotiations on the rate, a deal is struck and the ‘water truck’ is due to start work the following day. There are only two minor problems: There is no water truck and, furthermore, the boys know next to nothing about water trucks. Within 24 hours, from spare parts rustled up around the farm, a water truck of sorts is created. However, it bears more resemblance to a walking disaster with items falling off and seemingly more water leaking out than held inside.
The modular nature of the bodies means they can be built in advance.

EVIDENCE
Needless to say, the next couple of days is a huge learning curve for the young Yendles, but they persevere, keep the contract and save the family farm. Such ad hoc beginnings are not normally vindicated in the eyes of history and yet they have flowed on all the same in the formation of what is now a leading Australian water truck and body builder company. From these agricultural beginnings they work their way through the earthmoving industry, and in due course recognise a gaping hole in the market calling for the manufacture and supply of world-class water trucks and other bespoke truck bodies. If you’ll forgive the pun, they see it as a hole that’s crying out to be plugged
Ashley Joseph Chief Executive Officer STG Global
and this, ultimately, becomes the basis for the brothers starting STG Global. From that point, 20 years ago, the Yendle brothers have continually refined their manufacturing processes, producing numerous bodies on an array of mostly Isuzu chassis. Then, around four years ago, the twosome became a triumvirate as Chief Executive Officer Ashley Joseph is welcomed to the fold as a partner in the family business. By this stage the company is significantly expanded with several branches located along the eastern seaboard including the Melbourne facility where Ashley is based. “We are a manufacturer of specialised truck bodies including water trucks, vacuum trucks, tilt trays and service vehicles,” Ashley says, “and we are also moving into the waste market with the construction of front loading, side loading and rear loading garbage compactors.” Ashley says while the company has been manufacturing truck bodies for the past 20 years, the last four years since he’s been onboard have seen the company grow significantly. “At present we are producing over 200 units per annum and our philosophy is to produce bodies that are ultra-reliable and that represent good value for our customers,” he says. “We have a national footprint and are very well represented on the east coast with large manufacturing and servicing facilities at both Dandenong South in Victoria and Ormeau in Queensland. There is also a dedicated service centre in Sydney and agents dotted around the rest of the country.” Up until 20 years ago most water trucks were ex fuel or milk tankers. It’s not an exaggeration to go so far as recognising STG Global as a pioneer of the dedicated water truck. Indeed, a major point of difference between STG and other manufacturers, according to Ashley, is that most of STG’s bodies are hot-dipped galvanised to ensure an extremely long service life. “We are the only manufacturer that hot-dip galvanises our bodies, which ties in with our philosophy of ultimate reliability and durability,” he says.
Isuzu F Series ensures there is a model for every style of body STG Global builds.
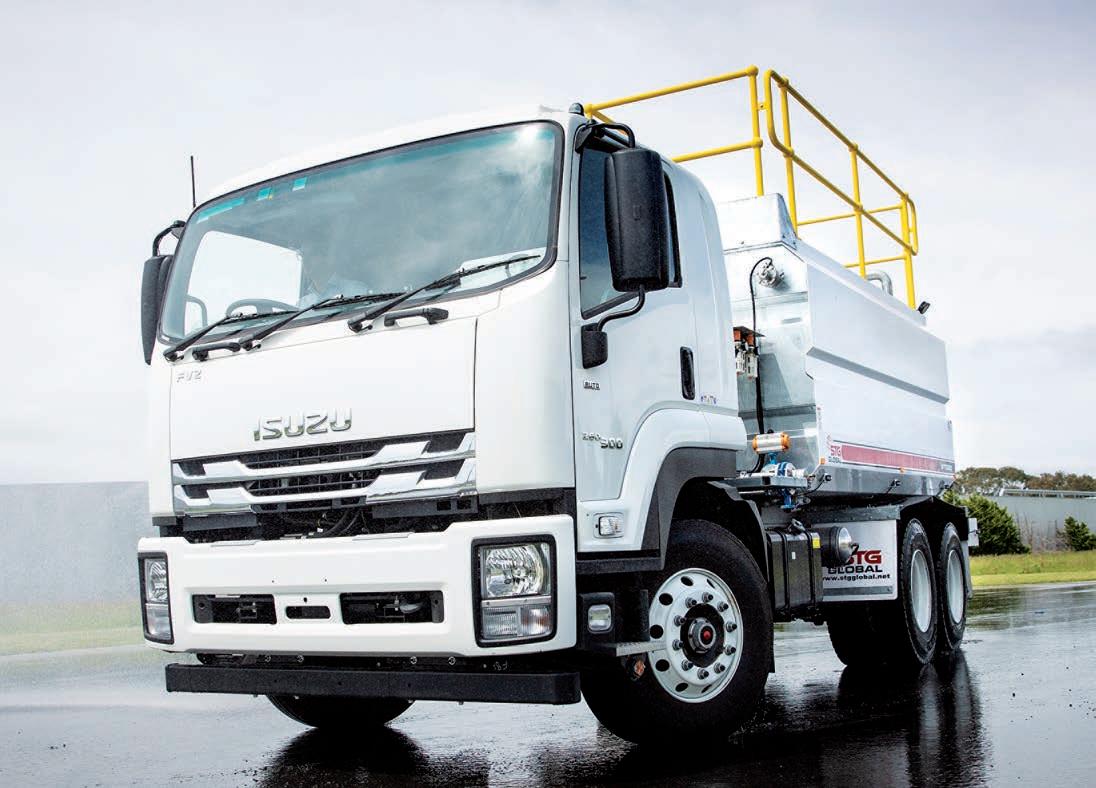
Ashley Joseph Chief Executive Officer STG Global Another big difference between STG and others is that the company has a stock of pre-built trucks that are basically ready for the customer to drive away the same day. Ashley says while this involves a degree of speculation, the vast experience the company has in the earthmoving sphere enables it to pre-empt which products the market will need and have it ready built and ready to go. “We take an educated punt and build our stock levels which means we have an average build turnaround time of three weeks, which we think is pretty amazing,” Ashley says. “We achieve this by building products for prospective customers in areas where we see the demand is highest. Understanding what the customers need or will need in the near future is the key. We find that many customers don’t want to wait six months to get their equipment, so having the quick turnaround is what gives us the edge over our competitors.” The modular nature of the bodies means they can be built in advance and held in stock ready to be fitted to a truck in accordance with customer needs. Speaking about the company’s connection with Isuzu trucks, Ashley says the majority of its builds are based on Isuzus because, as Australia’s overall
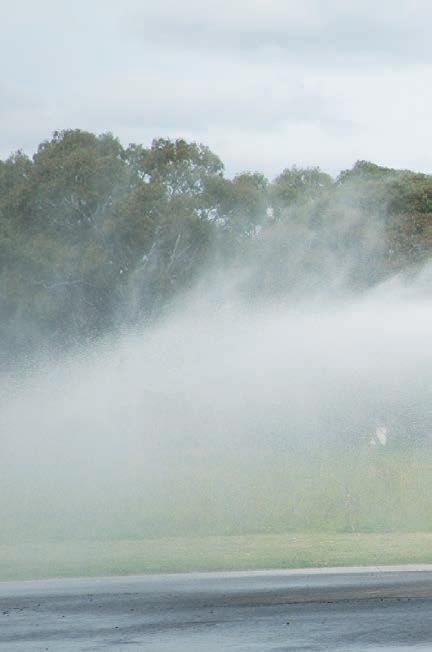
number one truck brand, this is what the vast majority of customers want. “We’ve had a very long association with Isuzu – they build a great product and they are well priced which explains why they are the market leader,” he says. The comprehensive range of Isuzu’s F Series also ensures there is a model to suit nearly every style of body the company produces. “We’ve picked the models that work for our ranges with chassis lengths that suit most of our products,” he says – adding that the company has the capability to modify chassis lengths if necessary. It produces the shortest wheelbase eightwheeler water truck on the market based on an Isuzu FYH or FYJ 8x4 chassis which it shortens to the same 4.3-metre wheelbase as the agitator spec Isuzu eight-wheeler. Reiterating the benefits of completely built products for customers, Ashley stresses that STG provides an end-to-end solution that encompasses everything from buying the Isuzu chassis to signwriting the finished product. “We’ll do the signwriting and install any custom features the customer wants so that as soon as they pick up the truck it’s ready to go to work,” he says. At the start of the year the company bought around 70 Isuzu trucks to make certain it had a continual supply of stock in the face of predicted shortages of trucks due to the flow-on effects of the COVID-19 pandemic. “We have taken the punt there, but we believe if you build the product right, the customers will come, and that’s exactly what has been happening,” he says. “A lot of it comes down to understanding your customers and what they need across the whole spectrum of products you manufacture. We find this philosophy combines ideally with the winning combination of reliability and value of Isuzu trucks, giving our customers the complete package to best suit their needs.”
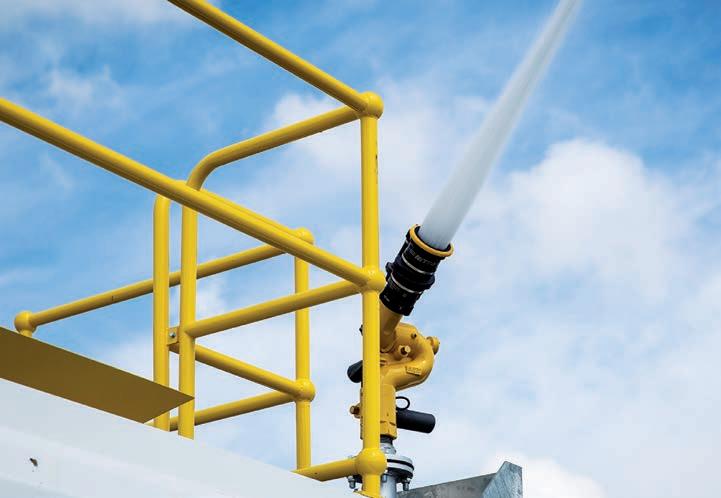
Water trucks have a hydraulic nozzle situated at the rear.
Most STG steel tankers are hot-dipped galvanised for a long service life.
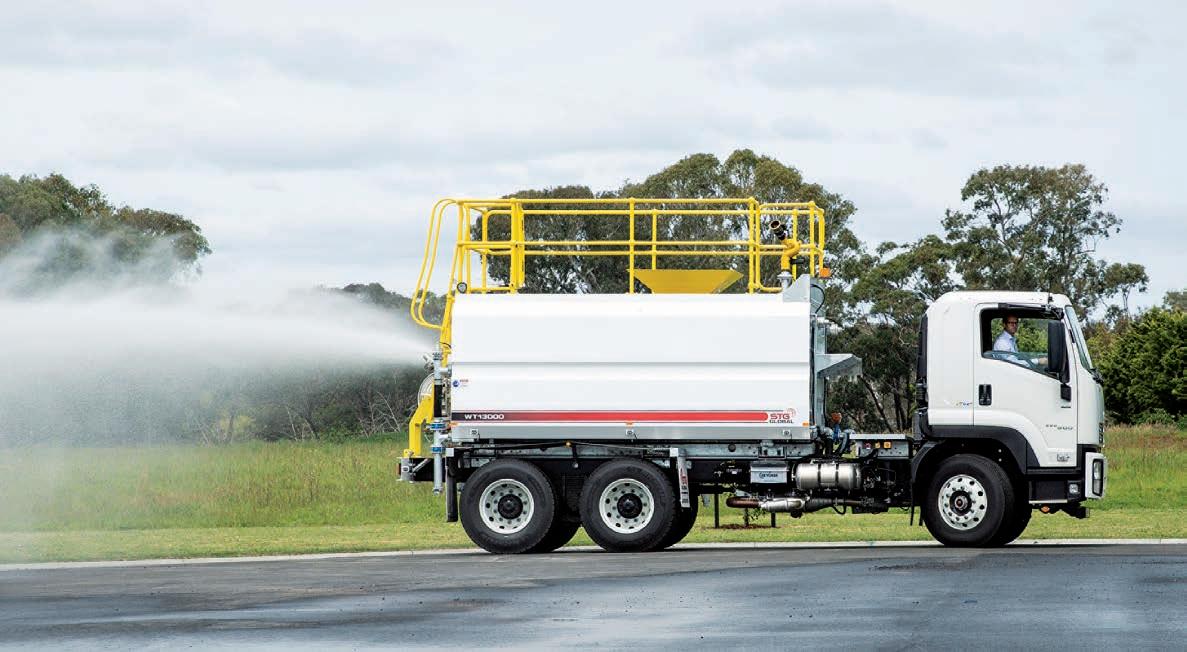
COOL SUPER
Interstate general freight specialist Palm Trans is trialling pumpless versions of Meritor’s popular MT21-165G tandem drive axle developed specifically for linehaul applications. The company has realised numerous benefits including lower operating temperatures and reduced parasitic losses.
Modern trucking operations demand equipment that is ideally matched to the application in order to derive the utmost in efficiency while minimising operating costs. Interestingly, advancements in technology and processes don’t always equate to the best outcome for all applications. This means that astute operators must be made aware of all options and choose the one that best matches their requirements. For heavy-duty drive axle manufacturing specialist Meritor, the quest to provide its customers with products precisely tailored to their individual requirements is ongoing. This is the reason why its latest line up of MT drive tandems, which supersede the previous RT series, are offered in three distinct versions including the MT21-165G Linehaul Series, MT21-165GP Vocational Series and MT23-168GP Severe-Duty Vocational Series. Designed in conjunction with PACCAR and it’s Kenworth K200 – which is the most popular linehaul B-double prime mover in Australia at present – Meritor’s pumpless MT21-165G is aimed squarely at long distance interstate operators looking to maximise fuel economy and minimise maintenance costs.
Palm Trans K200 B-double with Meritor pumpless tandem axles suited for linehaul.
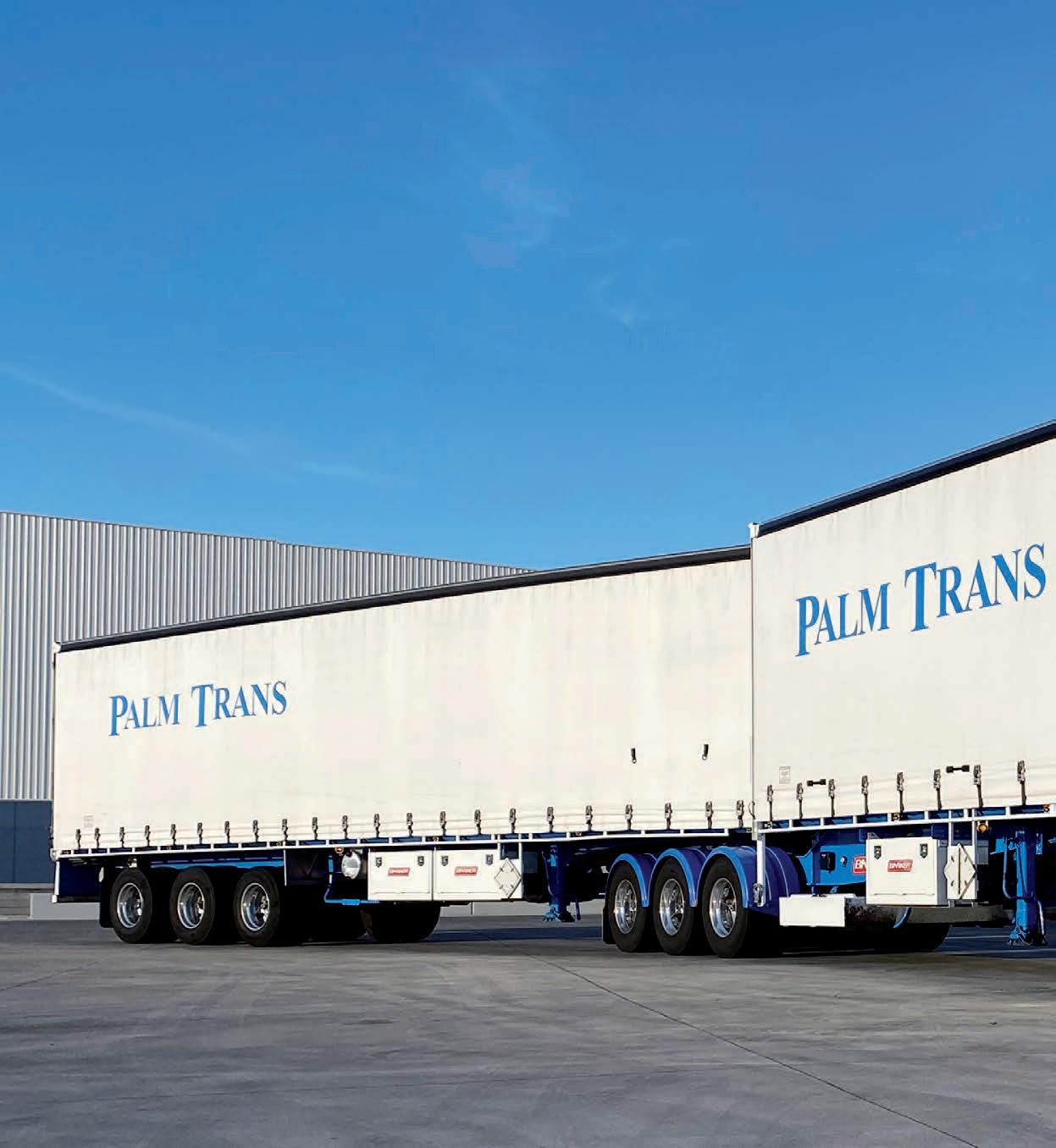
As the name suggests, one of the key differences in this design is the absence of an oil pump and filter in the front diff that are standard features in the other two versions. Before extolling the merits of the pumpless MT21-165G product for linehaul operations typified by Palm Trans, it’s worth taking a peek back through the annals of history at the differentials used in the early days of trucking. Truck differentials of old relied solely on splash lubrication which was effected by the crownwheel (also known as ring gear) teeth as they dipped into the oil like a paddlewheel and distributed it to the farthest reaches of the axle housing. However, for this to happen successfully, the crownwheel must be turning at a decent speed with the oil sufficiently warmed and fluid to be effectively ‘flung’. A good example of how splash lubrication can be inadequate in some circumstances was borne out in early single-drive trucks such as Austin tippers used to haul coal up the treacherously steep grade out of the Burragorang Valley southwest of Sydney in the 1940s and ‘50s. Having been loaded the previous afternoon and then started up stone cold the next morning, it was discovered that the trucks whose drivers gave them a thrashing up the mountain had no diff problems while those who nursed them thinking they were doing the right thing ended up blowing diffs. It was therefore deduced that the drivers who took it easy on the trucks were unwittingly starving the diff gears and bearings of sufficient splash lubrication under the high load conditions – largely due to the cold and therefore thicker oil – compared with those who gave them the gun right from the start, thus heating the oil quicker and enabling it to be splashed around sooner and more effectively to protect the moving parts. This scenario was potentially exacerbated further with the proliferation of tandem drive trucks in the ‘60s and ‘70s which feature a power divider located high up in the front differential housing. This transmits drive to the rear diff via a through or interaxle shaft, commonly called a jack shaft. The power divider functions like a ‘third differential’ dividing the torque from the transmission between front and
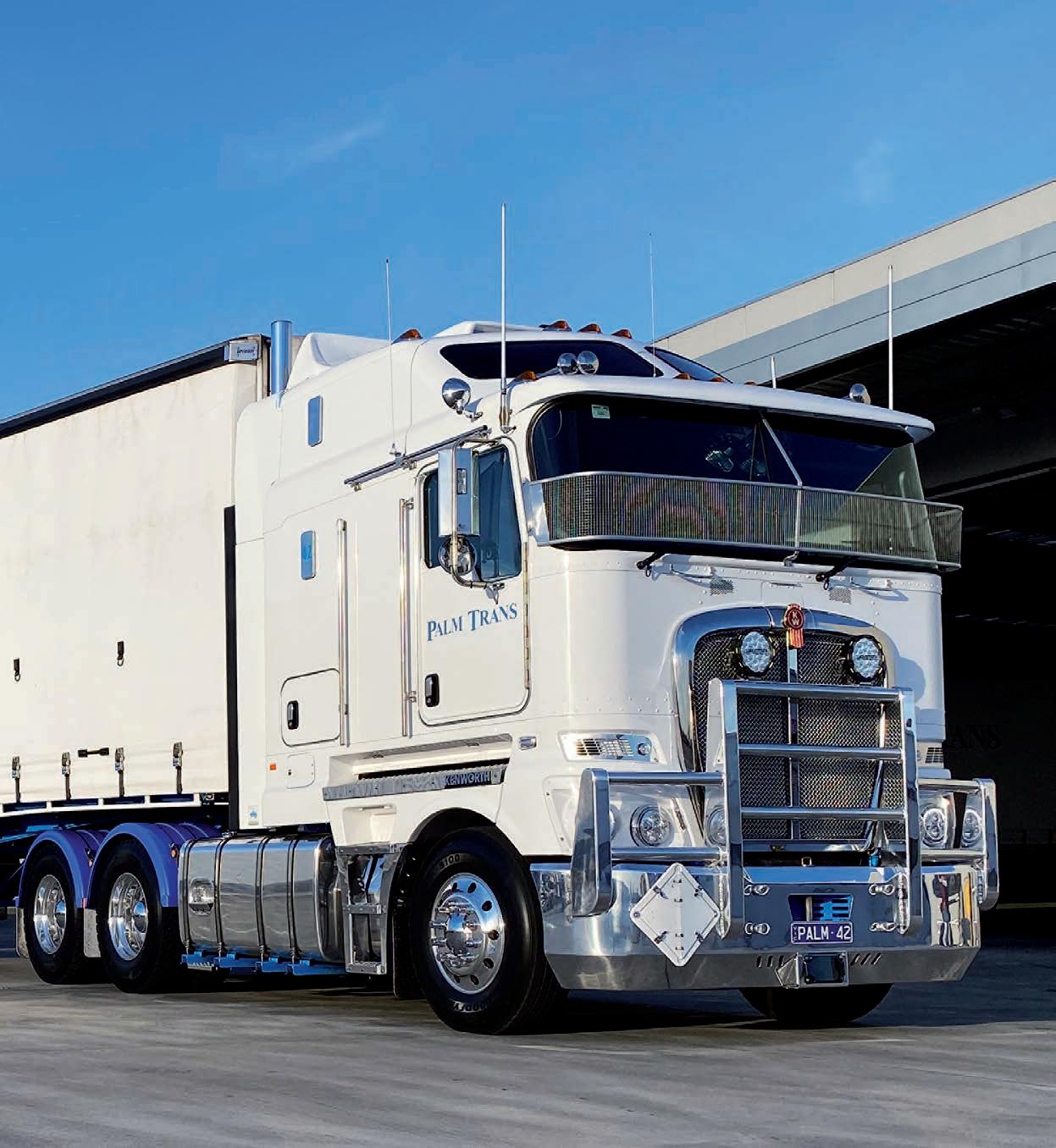
rear axles while also allowing for the slight variations in speed between front and rear axles. Again, in certain applications,, particularly where there was a possibility of one of the axles in the tandem set losing traction and spinning, it was found that splash lubrication was not entirely effective. Under these ‘spin out’ conditions the rapidly turning power divider components could quickly become starved of adequate lubrication and fail. This was a catalyst for the development of the diff oil pump which draws oil from the bowl of the diff, pushes it through a spin-on filter before supplying it under pressure to the bearings and cogs in the power divider gear set. For applications such as logging where low speeds and heavy loads off-road, often in cold conditions, are widely considered the norm, this is an ideal solution. But for operators at the other extreme – operating
MT21-165G Linehaul Series drive tandem viewed from below. trucks for long distances and maintaining 100km/h as much as possible – the aforementioned oil pump that was touted as a saviour in some applications actually became an impediment to efficiency and oil longevity. Enter Palm Trans, a privately owned family company managed by Darren and Julie Palmer. The company was established in 1989 with the goal of providing local haulage around Melbourne, Sydney, Brisbane and Adelaide, along with express interstate and container cartage. Today, Palm Trans has around 70 prime movers and 150 trailers operating throughout the eastern seaboard and South Australia. The all-Kenworth fleet is serviced and maintained by the company’s own workshop which is managed by Chris Mifsud who has been with Palm Trans since 2000. Speaking about the latest pumpless Meritor tandem the company has on trial, Chris says it is the best diff development he has seen in the two decades he has been working for Palm Trans. “We have always found the Meritor front diffs in the Kenworths to run hot due to the large volume of oil that the pump pushes around which generates quite a bit of heat,” he says. “It’s a bit of a doubleedged sword really, because there are also parasitic losses associated with driving the pump at such a high rate at highway speeds which impacts negatively on fuel efficiency.” Somewhat ironically, Chris explains that the issue of high front diff operating temperatures has become more pronounced on the Melbourne-Sydney and Sydney-Brisbane runs in recent times due to the massive upgrading of the freeways between the capital cities. “In earlier times the trucks would periodically slow down to 50 or 60km/h going through towns which allowed the diff oil temp to drop a bit whereas now with virtually all of the towns bypassed they are sitting on 100km/h consistently for much of the journey,” he says. Chris maintains that the sustained high speeds and long cycle times of the company’s linehaul trucks, particularly during the hot summer months, leads to the front diff oil temperature creeping above 100 degrees C, which can be detrimental to oil integrity and the O-rings and seals in the diff. It was for these reasons Palm Trans jumped at the opportunity to test the pumpless unit. “We were keen to jump onboard with this advancement and we’ve definitely seen benefits in increased longevity of the oil and reduced hardening of O-rings and seals caused by excessive operating temperatures,” he says. While acknowledging that the pump was originally incorporated to improve the lubrication of the power divider and upper areas of the differential, Chris says that as part of the pumpless design Meritor has redesigned the housing to create small dams and wells in the casting which help retain and feed oil into the components that need it. “It must be stressed that all of our trucks are on long distance work,” he adds. “For
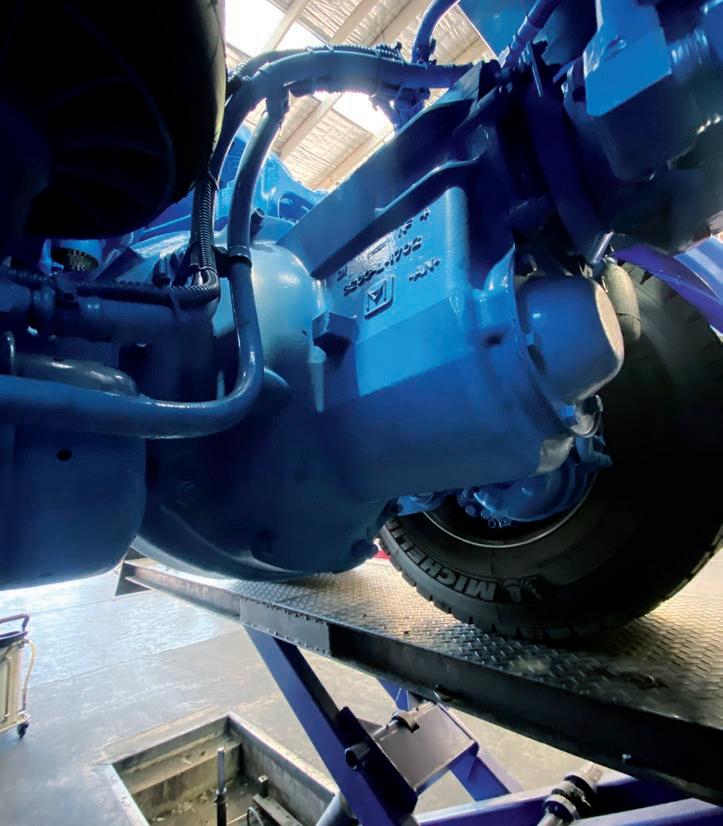
on-highway applications where there’s good splash lubrication provided by the crownwheel, its fine. We’ve had no issues in terms of longevity of power dividers and through shaft bearings – they seem to be standing up very well.” In fact, not having to drive an oil pump when it isn’t required makes mechanical sense to Chris as it reduces the parasitic loss. “If you’re driving less componentry, you’re wasting less horsepower and fuel and transmitting more power to the rear wheels which is where you want it,” he says. Chris’s comments are backed up by research carried out by Meritor that verifies the lower operating temperatures and reduced parasitic loss. According to Meritor, the parasitic loss attributed to the oil pump equates to 3.16kW (4.2hp) and bench testing has realised a potential improvement in fuel efficiency of up to 1.47 per cent for the pumpless unit compared with its pumped brethren. Potential fuel savings, Meritor claims, could be up to $3,300 per year, assuming a fuel price of $1.46/L and 250,000km annual distance travelled. These figures are based on a nine-axle B-double combination loaded to 68 tonnes gross combination mass pulled by a prime mover running a 4.3:1 final drive ratio with a cruising speed of 100km/h. Significantly, Meritor says its bench testing has shown that the pumpless carrier operates at up to 20oC lower than the carrier with the pump, while field tests revealed a drop of up to 15oC. In Palm Trans’s case, this suggests that under the most arduous linehaul operating conditions a desirable front diff oil temperature of between 85 and 90 degrees C should be maintained. Interestingly, Chris explains that there was no need to vary the oil change intervals with the pumpless compared with the pump equipped diffs. This is despite the fact that the pumpless units don’t have an oil filter. “We run the same 85W-140 gear oil and not having to change a spin-on filter is an added bonus in reducing maintenance costs and time,” he says. When Meritor and Kenworth approached Palm Trans to try the new pumpless diff there was no hesitation as the high front diff oil temperatures had been a concern the whole time Chris has worked for the company. “We are always keen to try new products that we can see will be beneficial to the business,” he says. “I would say this is the biggest advancement I have seen in the Meritor drive axle in the 20 years I’ve been working for Palm Trans.” Given the pumpless Meritor MT21165G drive tandem has been developed specifically to address the issue of excessive front diff oil temperature in on-highway applications, it’s refreshing to see a solution that actually makes the product eminently more fit for purpose while using fewer moving parts, and at the same time removing a parasitic loss and maintenance costs from the equation.
Much more than truck insurance.
Zurich helps to improve safety in the trucking industry through market-leading fleet risk management services. We work closely with customers to optimise business processes and driver behaviour. This helps to reduce claims, keeping your trucks on the road.
Ask your broker about Zurich today.
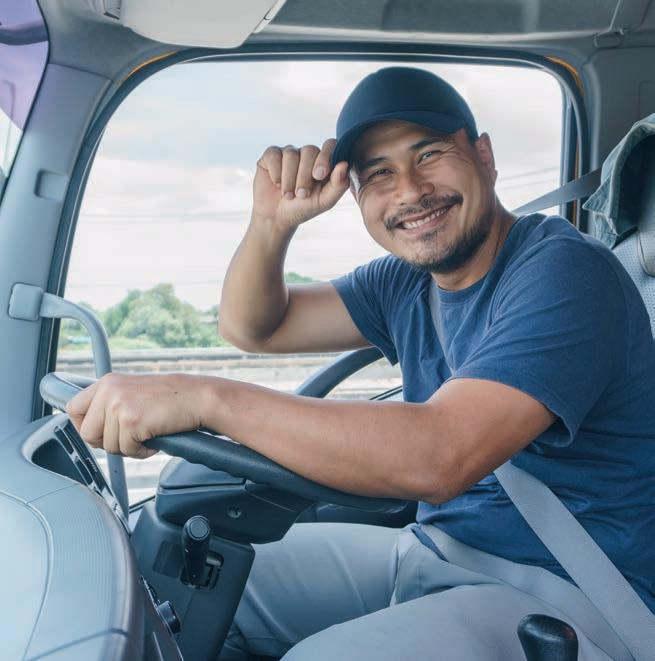
This information is general advice only and does not take into account your objectives, financial situations or needs. You should obtain and consider the relevant Product Disclosure Statement and Policy Wording (as applicable) from zurich.com.au before making a decision. The issuer of general insurance products is Zurich Australian Insurance Limited (ZAIL), ABN 13 000 296 640, AFS Licence Number 232507 of 118 Mount Street, North Sydney NSW 2060. ZU233775 V2 05/21 LEWG-016869-2021
TANKS FOR THE MEMORIES
Booth Transport went in search of an asset tracking and monitoring solution under the criteria it was both cost-effective and reliable. They found it through ORBCOMM.
Founded with a solo vehicle carrying wine and farm goods south of Adelaide in 1936, Booth Transport is now a leading carrier of bulk food, container transport and logistics. Today the business runs a fleet of nearly 200 commercial vehicles nationwide with depots in every state. The long-standing company is run by the third generation of the Booth family and has been active in dairy transport since the 1990s when it diversified the business with the purchase of a Deniliquin-based milk transport company with 15 tankers. Operations have since grown considerably and entails linehaul tankers of milk and dairy products moving up and down the east coast of Australia in addition to the handling of interstate containers from the port in Launceston to Melbourne and also from Melbourne via rail into Perth. As it continues to grow regardless of economic conditions the iconic company also transports dangerous goods with the mixed fleet heavily populated by the Kenworth brand although most major truck OEMs are represented in some capacity. It recently added six new Kenworth T659s to its road transport fleet. Active for many years in new developments and technology related to commercial vehicle transport, Booth Transport sought a better solution for
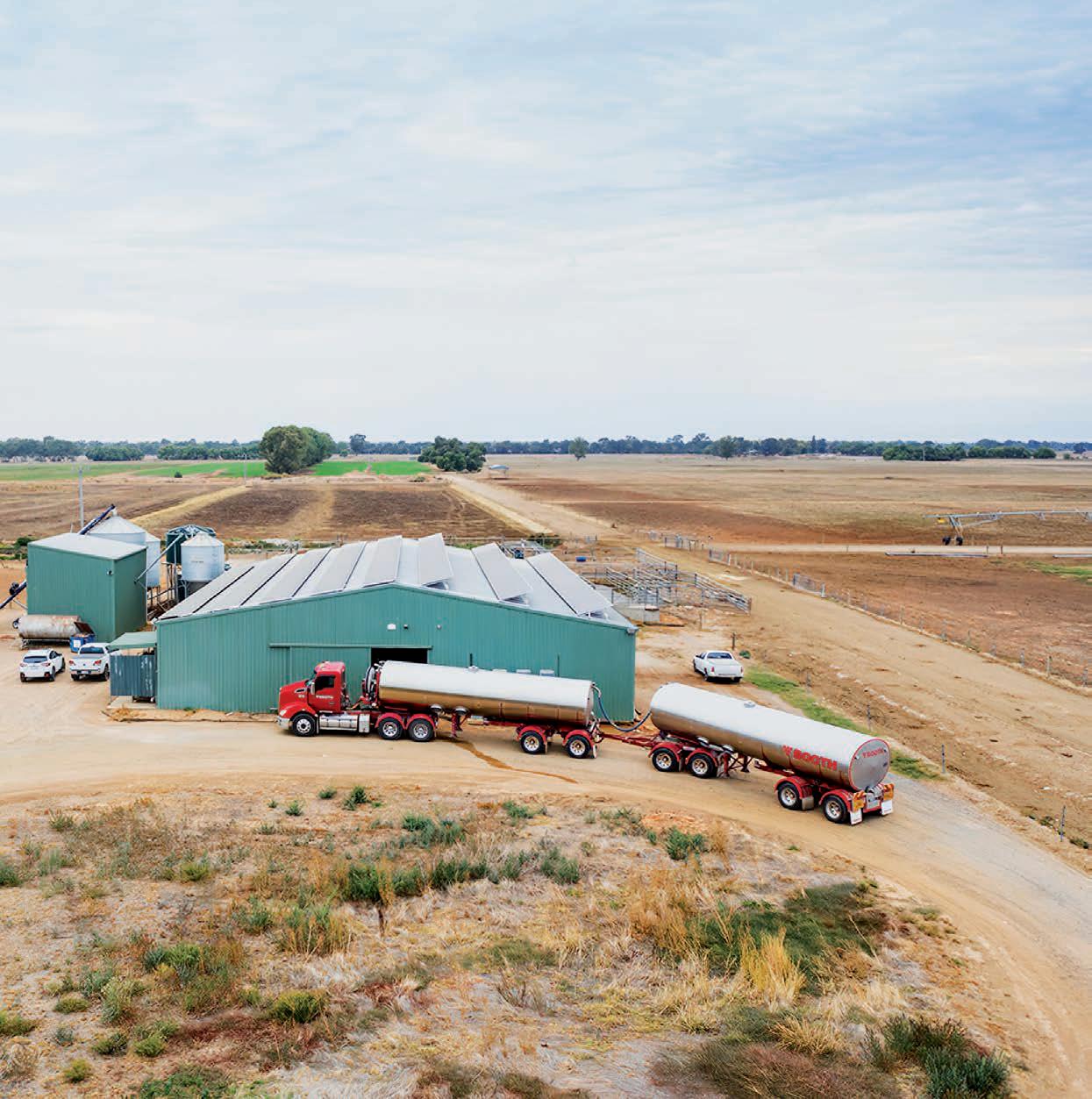
A Kenworth B-double pulls into a Booth Transport depot.
handling temperature-sensitive freight and after a fact-finding mission, conducted by General Manager Mitchell Booth in North America in 2016, found it. Mitchell was after a technology solution with extra functionality suitable for multiple asset classes that would be finely tuned to meet customer needs. In order to facilitate complete visibility across its dairy tankers to improve handling and transportation methods he turned to New Jersey industrial Internet of Things specialist ORBCOMM, a foremost provider in solutions that connect businesses to their assets. ORBCOMM hardware allows for wireless connectivity through a single, unified cloud-based analytics platform developed to optimise fleet management. This has enabled asset tracking across Booth Transport’s fleet of ISO tanks, road tankers and commercial chassis. IT Manager, Deanna Booth is part of the fourth generation of the family now leading the way at the company. A film production graduate, who had studied to be a director, she found her way back to the family business after she was engaged to make some instructional videos for customers. In the IT department, she works on application and software development which brings her into close contact with ORBCOMM. “We work alongside ORBCOMM especially with the integration of our tracking for our own application,” she says. “A big key for us was that they offered an extra or second serial port and we could plug in a temperature probe.” This detail was no less important for the reason the ISO operations include milk and cream in tankers making it critical that the temperature and whereabouts are tracked with real-time precision. No matter if the assets are in transit or at the depot, Deanna can access live and scheduled updates and know which of these are empty or loaded enabling improved turnaround times and better yard management while also saving the drivers, where it is applicable, time and fuel. The advanced asset monitoring solution being used by Booth Transport features a high-sensitivity solar panel and includes some units with a wired temperature sensor. “The device itself doesn’t require you to plug into the power. So there’s no leaching off the truck and trailer,” Deanna explains. “It basically allows you to switch it on, put in the temperature probe on the tanker and away we go.” Booth Transport had previously deployed tracking devices on its fleet. ORBCOMM’s solution, however, proved more stable than past products adding greater value for the scale of what was required across the fleet.

“We’re getting a consistency in terms of the devices not disappearing or turning off, for example, the power breaking down,” says Deanna. “We’ve used solutions in the past where you have to feed the power from the truck or the trailer. It just doesn’t work. ORBCOMM’s solution with the solar panel is great because it literally is a device that you stick on the trailer. I could go and stick it on my car right now and I’d be able to track its path. That’s the beauty of it.” Booth Transport at present has installed 226 of the ORBCOMM devices into its dairy transport division. The ORBCOMM devices can be installed externally on assets in about ten minutes, even when the asset is loaded, making Booth Transport’s deployments quick and efficient with minimal disruption to their operations. “The temperature probe goes into a metal cylinder device so it isn’t fit directly into the product,” says Deanna. “From there it is activated and a reading can be taken almost immediately.” While the asset tracking and temperature probes are the two key areas of focus, Deanna is looking at expanding it to kilometre-monitoring with Conor
Halloran, ORBCOMM Account Manager, to get a better handle on how the company can best leverage its use in operations. “We’re currently evaluating how it will work in with our fleet to best utilise its function and how we would use that information,” she says. “We expect it will offer significant gains for us especially given what we do here.” Booth Transport is in the midst of changing all of its tracking on its trailers to the solution because it is much easier to integrate given how their current fleet is set up. They are looking to put it
Booth Transport has installed over 220 ORBCOMM devices across its tanker fleet.
Booth Transport runs a linehaul dairy tanker fleet up the east coast of Australia.
against everything in the near future. “The plan is to put them on everything,” says Deanna. “It’s definitely helped us for the better. Especially because we’re very customer committed in terms of wanting to do what we can for our customers. Partnering with ORBCOMM has allowed us to do that with our temperature tracking and asset tracking more reliably and also pretty costeffectively. It’s not making it difficult for us to do which is great.” Because costs aren’t preventative ORBCOMM’s asset tracking solutions are set to be installed in every one of the ten depots Booth Transport has throughout Australia “That’s probably one of the key factors and why we’re so gung-ho about getting it all done across our fleet,” Deanna says. ORBCOMM’s telematics solution also provides Booth Transport with the unique ability to see precise data to schedule asset maintenance, inspections and time elapsed for increased utilisation and performance. In addition to simplifying the tracking and monitoring of multiple asset classes through one comprehensive view, the ORBCOMM platform creates an intelligent logistics environment that has also helped Booth Transport grow its customer portfolio and retain business in the highly competitive dairy and bulk liquids sector. “It gives us a leg up in the game because we can now provide this vital information with up-to-date reports on the product while it is in transit. The customer might not necessarily think they need to have the functionality of accessing this information but it’s something they end up wanting,” she says. “Technology is evolving and we’re trying to move with it and that means if we can be on top of it all we can provide the best service for our customers.” Should they see any deviations in the temperatures they are monitoring, Booth Transport can use the ORBCOMM software to investigate the factors that are the likely cause including prior events, changes in the environment and how it was loaded. “The great thing this solution does is provide us with the knowledge of an exact temperature measurement from the moment a tanker is loaded,” Deanna says. “You can also work out issues with equipment just from that failure which is great. It helps us as much as it helps the customers.” Customers are supplied with all of this information in reports so they, in turn, have full disclosure regarding the condition of their product the entire time it is in transit. “That way everyone has greater visibility,” Deanna adds. “It increases trust.” Deanna makes mention it wasn’t that long ago that customers had an estimated time of when they could expect a truck to deliver their product. “If you think back 20 odd years ago a truck would leave a depot with a trailer and they wouldn’t see it again until it completed the round trip or arrived at the next depot. Now I can watch it basically travel from the depot for the entire trip.” Deanna, whose two sisters and four cousins are also working at the company, has discovered she has a real passion for operations in the IT department. It’s also worth noting that advances in technology are increasingly prevalent in road transport and in her case have brought her back to an industry which is itself looking to attract more female professionals. “In IT and technology there’s so much new innovation going on it’s an exciting space to be in. Being able to build our own apps and provide that kind of information to customers through portals gives us a sense of pride. I never thought I’d be doing stuff like this in a million years but I have a real passion for it now which is great.” She jokes, “That IT applications class I did in year 12 really paid off.”

SAFETY IN NUMB
Going paperless can help a workforce stay compliant and also safe.
It’s not common knowledge that nearly one third of all workplace fatalities in New South Wales are the result of road crashes. For transport operators, ensuring the safety of a workforce can be challenging at best. Following Australia’s first industrial manslaughter convictions last year, vehicles are now legally considered a part of the workplace. This means being proactive in mitigating risks for staff, or risk serious fines and even jail time. Teletrac Navman’s Chief Product Officer, Andrew Rossington has some suggestions to assist decision-makers in keeping out of legal trouble while keeping the people under their care safe. Automated vehicle maintenance according to Andrew is a must. “Maintaining your fleet via paper pretrip checklists and manual maintenance scheduling creates potential hazards if paperwork is misplaced,” he says. “New issues that arise may not be captured or flagged with other staff, opening yourself up for serious trouble.” With integrated fleet management systems, drivers can electronically complete pre-start checklists and the back-office team can access up-todate engine and vehicle maintenance data at any point in time. That way a comprehensive history of each asset can be pieced together in addition to having a report generated on engine and driver performance, without always needing to physically be there or having to chase up previous paperwork.
“With digital pre-start checklists, drivers can notify maintenance staff of potential issues,” says Andrew. “The workshop team can order parts and schedule proactive repairs instantly, even if the driver is on the road, to be repaired upon return.” Another key area of focus should be road safety policies. Part of keeping drivers safe while they’re out on the road is creating a road safety policy that’s regularly updated and available to everyone. Ensuring that the technology used within the business is added into and updated constantly in the business’s policy is an important, yet often overlooked, step says Andrew. “Physical policy documents can be
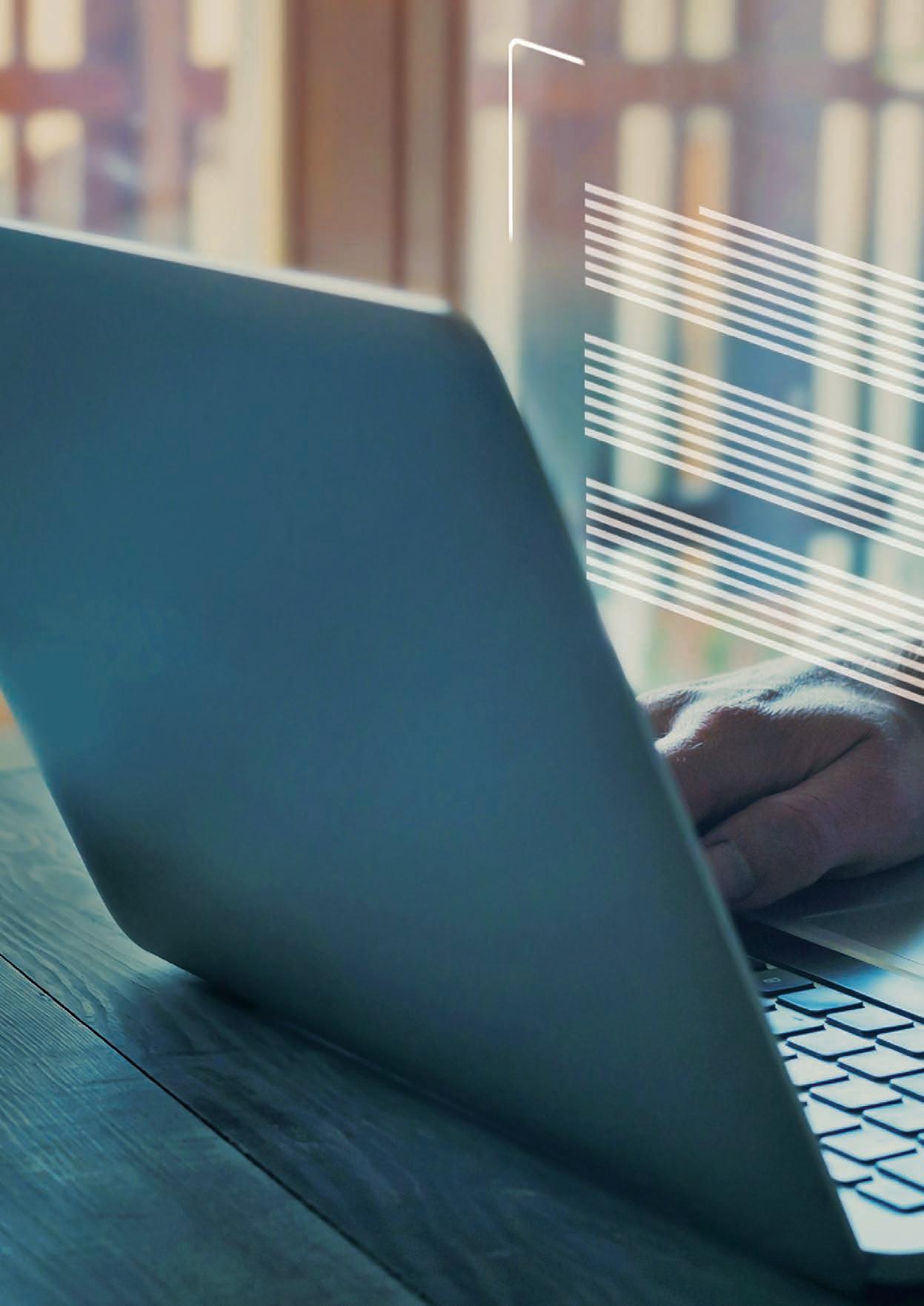
easily misplaced and need to be updated manually, making it tricky for everyone across the fleet to access the required and correct paperwork,” he explains. “Switching over to in-cabin devices means that drivers, contractors, and operators provides a simple yet powerful mechanism to view or access the road safety policy electronically
Andrew Rossington Chief Product Officer, Teletrac Navman
ERS
and be alerted to new or changed documents in real-time.” But policies are, as is often the case, only as good as how well they are practiced. “Encourage your team to keep up to date, voice any confusion and seek advice,” says Andrew. “Keeping these practices in conversation ensures they are always top of mind and it also helps to mitigate risk.” While advanced solutions greatly reduce the risk of incidents, Andrew believes the time taken to talk with each employee and understand any concerns they may have around driver safety is always beneficial. As some drivers may be more prone to dangerous habits, a fleet-wide policy should be paired with individual reviews of driver behaviours. By integrating telematics into the fleet, driver data can be used to create a safer workplace. Should several members have issues with safe driving practices such as speeding, custom driver training programs can be introduced that are tailored to their needs. “AI-enabled technology is revolutionising how we view fleet management, from the back office to the truck cabin, all while elevating driver safety and boosting efficiency,” says Andrew. “With vehicle cabins now legally considered part of the workplace, transport operators need to do everything in their power to keep staff safe, or risk serious legal consequences that now include jail time. By digitising your maintenance checklists, creating a road safety policy and using driver scorecards, you’ll be on the right path to mitigate potential risks and ensure the safety of your fleet.”
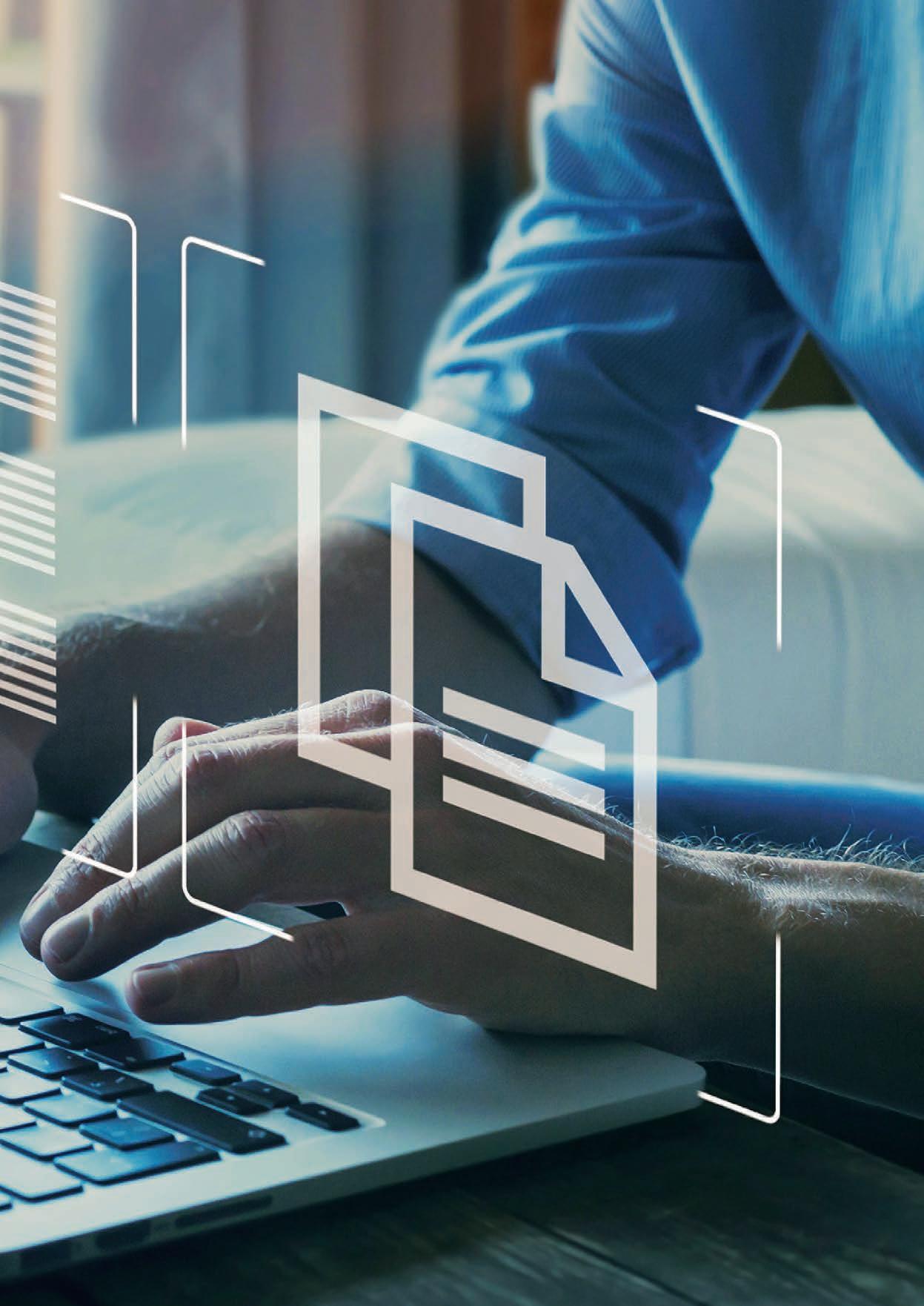
Workshop teams can order parts and schedule proactive repairs instantly following pre-start checklists.

GOOD
Understanding obligations across inspections, maintenance standards and defect management is a key means of bridging gaps in the task of compliance.
Periodic transitional phases are not uncommon in industry. In commercial road transport these shifts within the sector are often essential to keeping it viable and functional. A seismic shift occurred in 2018 when the primary safety duty on all parties under chain of responsibility legislation was applied at once to trucking businesses, the consignor or consignees. As it now imposes due diligence obligation on company directors and executives, the legislation has evolved past the point of penalising truck drivers for driving with undue care. As one of the most dangerous industries in Australia the necessity to weed out lax or negligent practices as it pertained to compliance have been viewed as a must to enforce regulations and improve safety. This has resulted in an industry wide onus on parties in the supply chain being responsible for proactively managing the risks associated with their transport activities. Fines of up to $3 million dollars for businesses who fail to do so, have made it imperative that all parties involved in the COR identify and manage risks rather than reacting when there is a possible breach of law. COR is now the legal foundation upon which supply chain safety is maintained and strengthened including vehicle maintenance, repair and fatigue management. While failures in the area of compliance might be minor, more often than not the penalties are not. In the worst case scenarios, where breaches are not only common but flagrant, it can deeply impact the wider community and is sadly, the stuff of national headlines. Indeed, no amount of image rehabilitation for companies and industry will suffice for compliance failures when collective professionalism is treated as the exception rather than the rule.
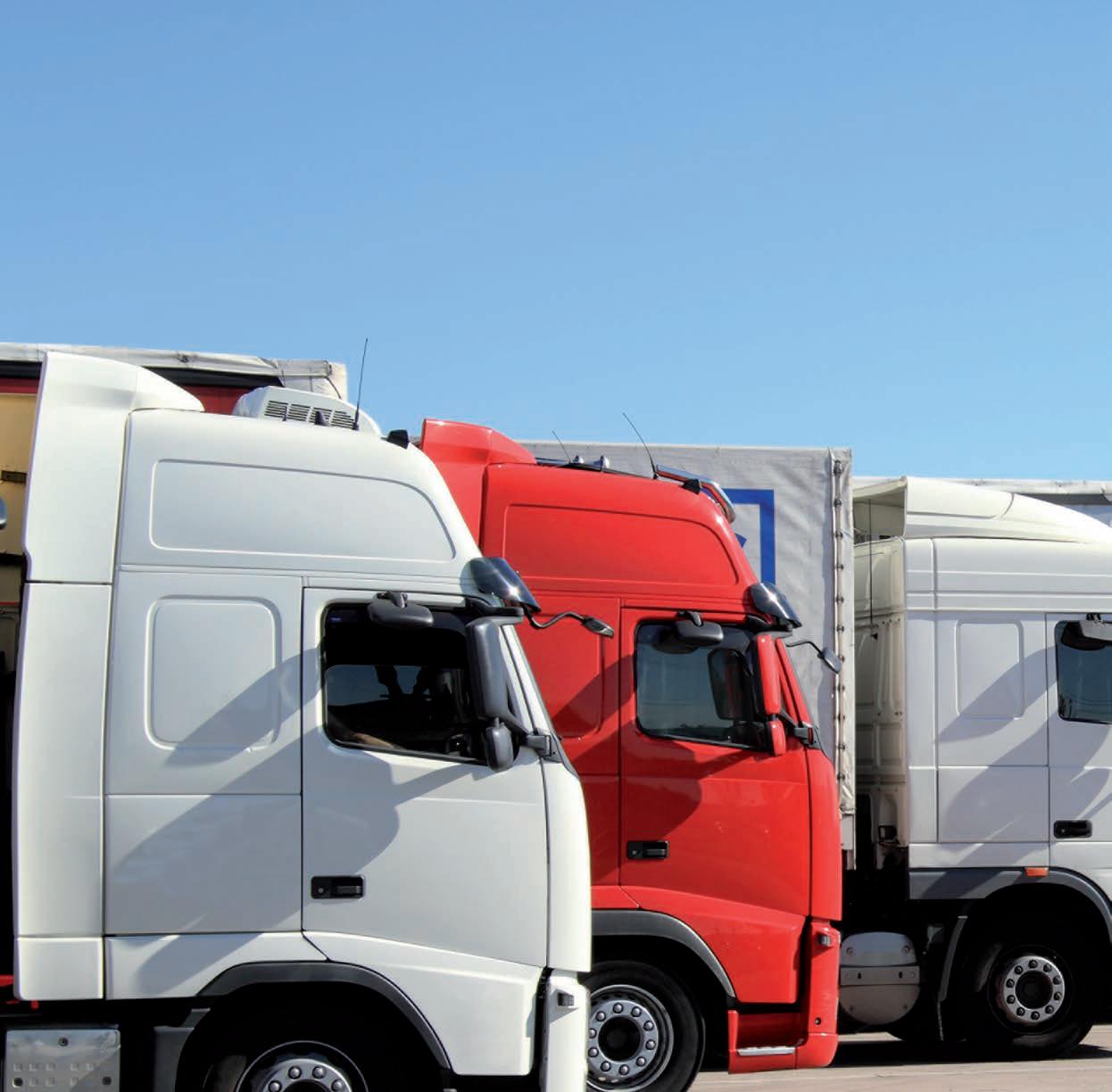
TO GO
Widespread industry consultation by the likes of the National Heavy Vehicle Regulator and SafeWork is helping to identify the highest priority risks and assisting with responses to the issues. Safety Around Your Vehicle Compliance Project is one recent undertaking in which SafeWork inspectors are speaking to operators on the requirement to have safe systems of work in place when carrying out activities around heavy vehicles. It goes without saying that operators who effectively maintain their vehicles are less likely to be involved in an incident. This is now supported unequivocally by critical road crash data shared earlier this year in a report by insurer NTI and the NHVR. The report studied the relationship between vehicle standards and safety performance. In finding clear links in two categories the report noted that the frequency for poorly maintained wheel and tyre defects increased by 32 per cent and was 26 per cent higher in cost claims for commercial road transport businesses. Poorly maintained couplings accounted for a 29 per cent increase in frequency. While the report was careful not to suggest causation between crashes and defects it did confirm a distinct correlation between operators involved in a greater number of claims with trucks in which couplings, wheels and tyres were not well maintained. Although the task to monitor and stay on top of all areas that can affect commercial road compliance can appear daunting it needn’t be. Companies that specialise in fleet management software have developed new product offerings that promise solutions to the challenge inherent in actioning everyone across the chain of responsibility in real-time. Having consulted with former members of the NHVR to better understand the expectations of inspectors, SG Fleet developed Inspect365 as a tool that mitigates risks for fleets via an entirely digital process so that a record is lodged and kept for access should it be required later on. Anyone using Inspect365 can log a defect the moment it is recognised. At that point, an electronic record identifies the issue and the workshop manager, for example, is then able to access the record from the time it was logged. This real-time visibility is particularly practical for drivers who, in the event they encounter an issue with the vehicle, can immediately pull over and make note of a fault by entering it into the system. NHVR Director Vehicle Safety and Performance, Peter Austin has acknowledged the importance of regular and effective maintenance regimes across the heavy vehicle fleet. “Well maintained vehicles operating on our road network are essential to the safety of all road users,” he says. “The NHVR has a long-standing commitment to evidence-based enforcement, which
Well maintained vehicles operating on the road network are essential to the safety of all road users.
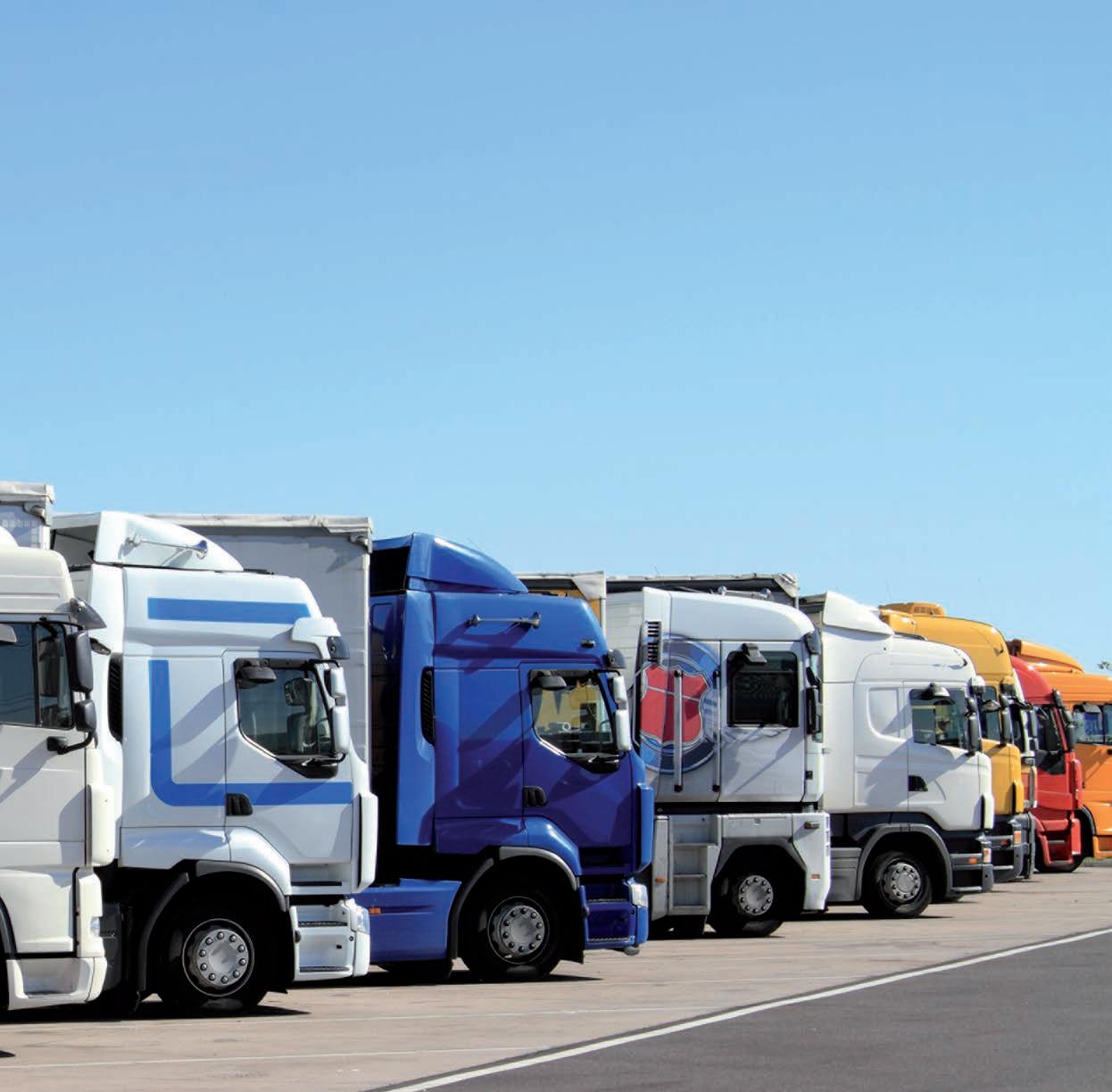
is why we take a national, risk-based approach to checking whether heavy vehicles in the fleet are maintained. “If we see a history of non-compliance, we intervene early and investigate further to prevent a potential accident from occurring.” By adopting agreed standards to ensure quality and consistency, operators not only remain fully compliant with safety and regulatory standards but ensure their partners can reduce costs and turnaround times. This means check lists and critical maintenance must be adhered to, tested and re-certified. The ability to start a job straight away reduces time off road by days and sometimes weeks. Before a heavy vehicle driver embarks on a journey, Inspect365 will take the driver through a sequence of checks and the faults are then logged and registered so they are prioritised. While compliance seems to be steadily increasing during national operations conducted by the NHVR, breaches of mechanical safety are going to be present given the average age of the national fleet is now closing in on 15 years. Having a documented outcome for work performed by a qualified repairer therefor remains crucial so that sign-off can be validated. This way drivers who are asked to take equipment out that might not be safe can be immediately identified. As a result everyone understands their part in the process in accordance to where and how accurately it has been reported. In short, by formalising such a process, reports become a trail of proof as to whether a driver knows if a vehicle is not safe to take out and alerts a workshop manager that a service is required. As a fleet management tool, Inspect365 automates the manual process of daily checking and fault reporting. This way, everyone in the decision-making chain from management, the workshop and inside the cabin of the truck, is kept in the loop. Under COR the freedom to prosecute all the way up the top of the decisionmaking tree might mean exposure for those who aren’t yet aware of where their organisation is vulnerable. Having line management correctly understand their roles and responsibilities is part of the challenge. Implementing the policies to ensure they are looking after mobile assets and the safety and welfare of their team is the other. The right fleet management technology can provide total visibility when it comes to the suitability of commercial vehicles based on each individual requirement. Standardising inspections across maintenance and repair, especially as it pertains to faults and scheduled servicing, also empowers the personnel in place to meet the obligations of the business. “In a post-COVID-19 world, fleet managers can add sanitisation to the checklist for commercial vehicles using our Inspect365 system,” says Andy Mulcaster, Managing Director of SG Fleet. “Everyone from the truck driver to the fleet manager will have confidence knowing that everything has been done to ensure the safety of the workforce and that the vehicle has been properly disinfected for each new driver.”
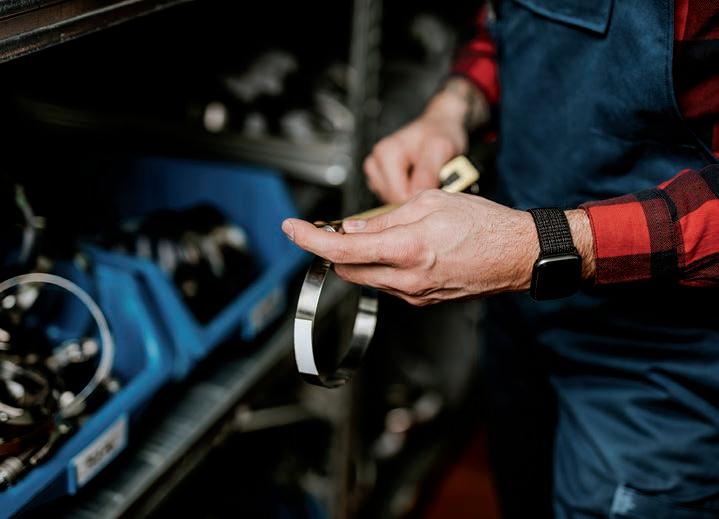
Check lists and critical maintenance must be adhered to, tested and re-certified. Inspect365 can help action everyone across the supply chain in real time.

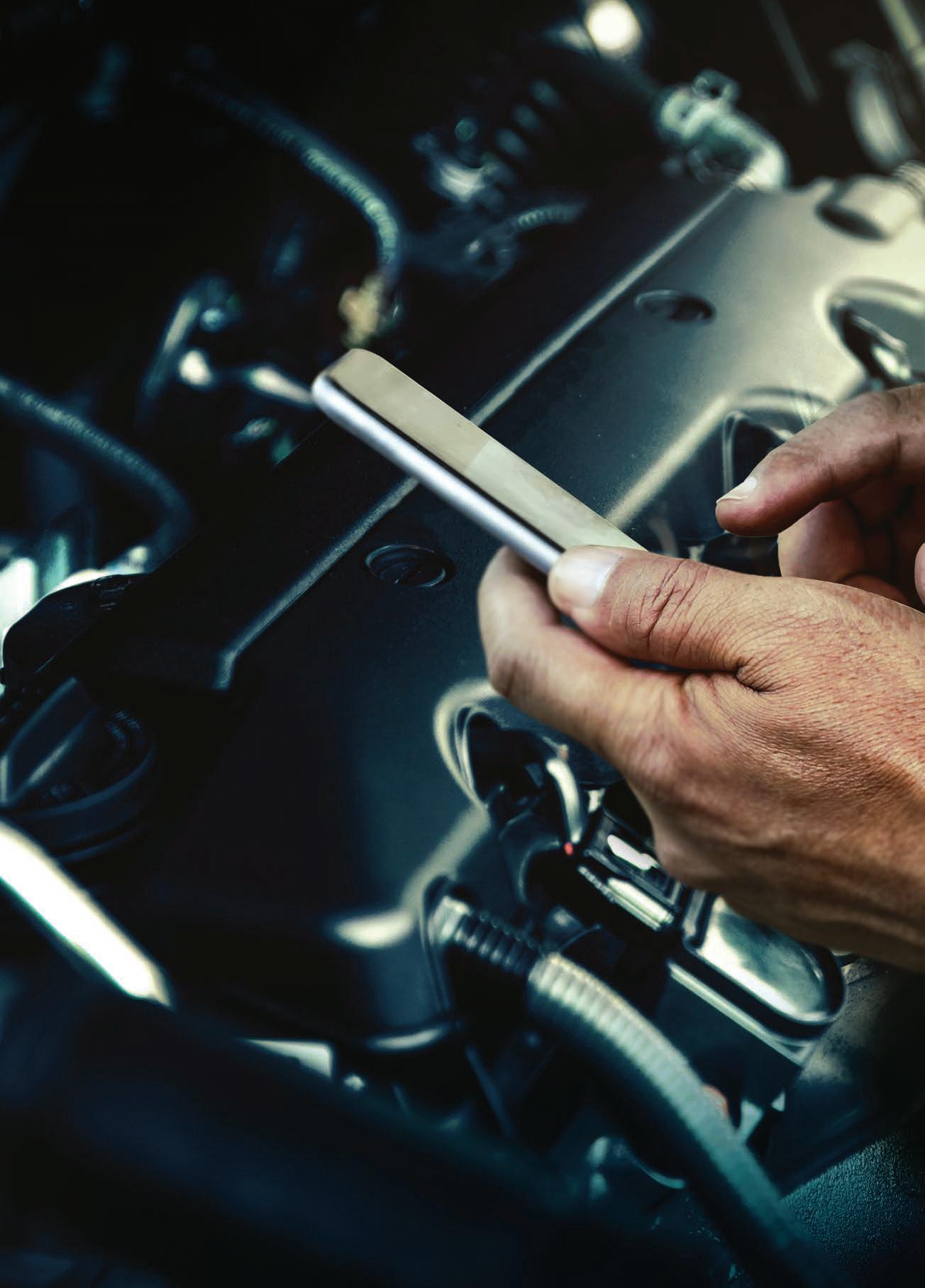
ROCKET POCKET
Scania’s latest engine targets the upper levels of the Medium Duty market.
Scania has a strong reputation for building ‘big’ engines including the 16-litre V8 which is currently available in Australia rated up to 730hp, with an even higher rating on the horizon for later in 2021. In addition to the V8, Scania’s six- and five-cylinder offerings provide a comprehensive range of engines suitable for heavy duty applications. With an obvious intention to provide trucks with the appropriate specifications for the upper levels of the Medium Duty sector traditionally dominated by Japanese brands in this country, Scania has set about developing a suitable engine for the maximum of 26 tonne GVW category. Logic would have operators using Scania Heavy Duty models with their big loads being suitable potential targets for trucks
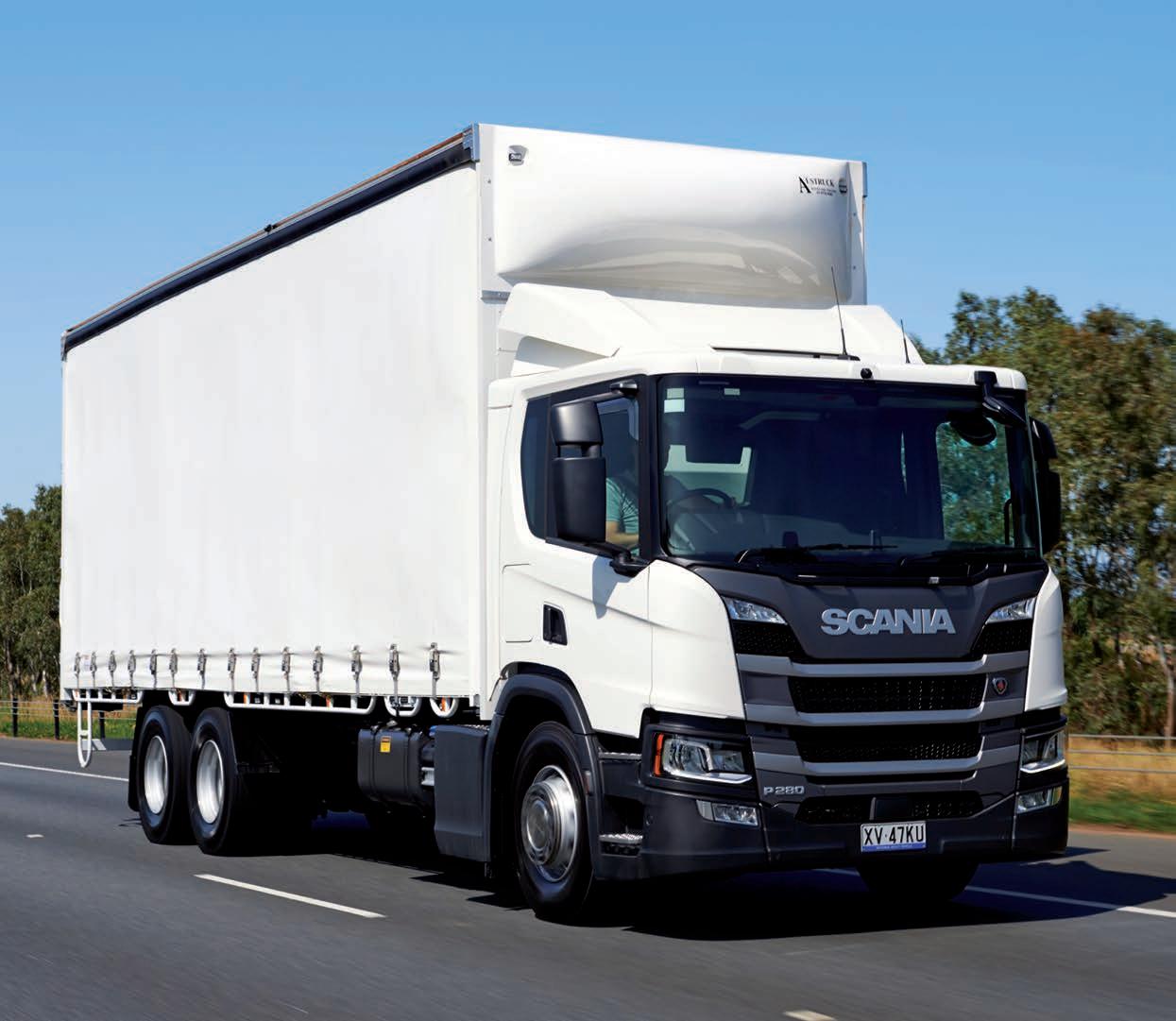
from the same brand to handle their requirements such as urban and even regional distribution activities. Scania’s solution involves the availability of a new 7.0-litre (actually 6.7-litres) six cylinder engine in a P cab configuration. Our test model has 280hp at 1,900rpm although the 7.0-litre is also available in ratings of 220hp and 250hp. The engine has been developed in conjunction with Cummins which has been a partner in engine development with Scania for some time. Cummins is mainly responsible for the ‘long’ engine while the monitoring and control systems have been developed by Scania as well as components such as manifolds and the turbocharger, which is an uncomplicated fixed geometry unit. The result is a quiet running, fuel efficient and well performing engine seamlessly integrated into the Scania trucks’ mechanical and electronic architecture which includes the Scania Opticruise automated transmission. Scania’s version of the engine has avoided the need for Exhaust Gas Recirculation (EGR) and the perceived problems which accompany that particular emissions technology. The 7.0-litre uses Supplementary Catalytic Reduction (SCR) and a Diesel Particulate Filter (DPF) as exhaust after-treatments to meet the Euro VI emission standards. The 7.0 litre has now been available in Australia for more than a year and only recently has the truck trade media had the opportunity to experience an extended drive. The route selected contains the infamous Mt Ousley section of highway between Sydney and Wollongong which provides excellent tests for engine power and the truck’s braking abilities. The truck provided for the road test is a Scania P280 6x2 fitted with a 14-pallet curtainside body from Austruck and loaded to a gross weight of 19.2 tonnes according to the on-board weighing system, with 5.6 tonnes on the steer axle. The 7.0-litre engine weighs 360kgs less than the larger 9.0-litre five cylinder Scania engine which adds to the payload capacity. The reduction in weight also makes its own contribution to fuel efficiency. The Opticruise transmission in this truck has 12 speeds plus two crawler settings which operate in forward and reverse and make manoeuvring easy and reduce the component wear on the automated clutch. The driver has the choice of Economy, Standard and Power modes for the transmission operation. The rear axle ratio of 3.07:1 translates to 100 km/h at around 1600 rpm in top gear. Holding down the column mounted

The on board weighing system verifies a gross vehicle weight of 19.2 tonnes.
transmission control stalk will select the Opticruise’s ‘automatic manoeuvring’ mode which isn’t a crawler gear as such, but feathers the clutch to produce a very smooth operation in circumstances such as backing up to a loading dock. The maximum torque of 1,200Nm from the 280hp rating is delivered between 1,050 and 1,600 rpm and the Opticruise makes good use of it in urban situations and also on the punishing climb back up Mt Ousley. The wide torque spread contributes to the truck’s excellent driveability and under load there is no temptation to interfere with the operation of the transmission, other than sampling the three modes. The interior of the Scania P Series low roof day cab has an impression of spaciousness due in part to the use of the floor from the G Series which provides a very low engine tunnel and also permits the inclusion of similar storage compartments to the larger G Series cabs. A refrigerator and lidded storage compartments are located behind the seats and other functional features include a fold out desk fitted above the glovebox. The full air suspension system provides the truck with a smooth and well-damped ride with none of the pitch and yaw that can sometimes be associated with airbagged front axles. The airbag control for
the rear suspension has three memory settings therefore enabling the operator to adjust the truck height to suit specific, frequently used, loading docks. The front airbags can lift the truck up to 100mm above normal ride height which can be a benefit when negotiating obstacles such as deep spoon drains. The suspension system is configured to return to the normal ride height automatically once the vehicle reaches 20 km/h. Both driver and passenger are treated with air suspended seats with integrated seat belts. The steering wheel and column have an extensive range of tilt and reach adjustments. This test drive takes place on a day when the East Coast is being lashed by very heavy rain, yet the wipers, demisters, heated mirrors and cab air conditioning combine to provide a
The 7-litre engine has been seamlessly integrated into the Scania trucks’ mechanical and electronic architecture.
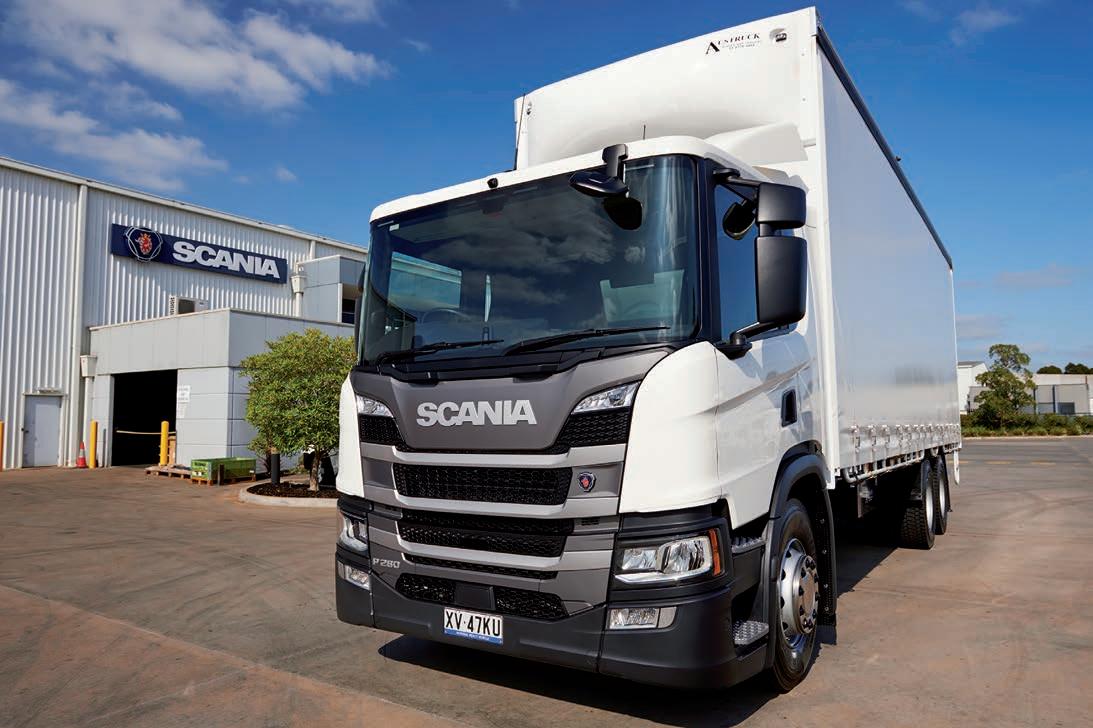
comfortable and, very importantly, a safe working environment. Scania’s level of active and passive safety features is second to none and this is the only truck in the Medium Duty sector which is equipped with standard side curtain airbags on both sides of the cab in addition to the driver’s airbag located in the centre of the steering wheel. It shares in common with other trucks in the current Scania range Lane Departure Warning and Autonomous Emergency Braking that provides visual and audible warnings of imminent crash situations in which the braking system is autonomously activated if the driver doesn’t respond to the warnings. This P Series is equipped with Scania’s 360-degree aerial view camera system which uses input from four cameras and some cunning software to deliver a drone-like overhead view of the truck and its surrounds displayed on the dashmounted tablet screen. When reverse gear is engaged the rear-mounted camera’s display is augmented by guidelines on the screen and another camera aimed down the kerbside is activated by the turn signal lever and minimises blind spots especially when merging or turning left. The rules of physics determine that smaller engines will have a reduced ability to provide engine braking compared with larger capacity engines. The two-stage exhaust brake is still reasonably effective and the Opticruise transmission automatically downshifts to maximise the level of available engine braking. A small slide switch on the transmission/exhaust brake lever selects the Scania’s brake blending function which in turn activates the exhaust brake when light pressure is applied to the brake pedal and progressively engages the four wheel disc brakes as additional pressure is applied. The ergonomics and driveability of the Scania range are well known and the 7.0-litre engine now expands Scania’s range into market segments overwhelmingly inhabited by Japanese trucks. In addition to its extensive suite of safety benefits and driver conveniences, the Scania P Series with the 7.0 litre engine retains Scania’s heavy-duty engineering and driveline features, which are optimised for lighter duty functions such as urban and regional distribution as well as infrastructure and maintenance applications.