
32 minute read
Prime Mover News
> NTC to tackle driver distraction
The National Transport Commission (NTC) has released a consultation regulation impact statement (RIS) seeking feedback on technology-neutral options to regulate driver distraction. Distraction is seen as a significant road safety risk that is not as well understood as other risk factors such as drinkdriving and speeding, according to the NTC. Studies have found that a task which takes a driver’s ‘eyes off the road’ for as little as two seconds can be particularly hazardous. NTC CEO, Gillian Miles, said that new technology-related distractions, outdated rules and a general lack of understanding from road users present significant challenges. “Drivers engage in non-driving activities every 96 seconds while behind the wheel. Distractions take our concentration off the road which means we may not have time to react to hazards. “We are proposing four options for consideration. The views of a broad range of stakeholders are crucial to guide any policy reform to deal with driver distraction.” The Australian Road Research Board (ARRB) reviewed the best international research available to date on driver distraction. This work supports the NTC’s efforts in stimulating discussions about driver distraction research, policy and legislative reform options. Consultation on this paper closed on 21 August 2019. The NTC aims to deliver a decision RIS for transport ministers’ consideration in May 2020.
> Compassionate driver honoured with Bridgestone Bandag Highway Guardian title
A Linfox truck driver has been named a Bridgestone Bandag Highway Guardian by the Australian Trucking Association (ATA) following his remarkable actions and compassion at a multi-vehicle crash site in February. Andrew Hastings was travelling west on Victoria’s Western Freeway when he came across the collision between two passenger vehicles. As the first on the scene, he immediately used his fire extinguisher to suppress flames and aid an injured woman out of her car, before rushing to the aid of the severely injured driver of the other vehicle. After administering first aid to the man’s wounds until paramedics arrived, Hastings then pried open the passenger door in order to sit with and comfort the driver while he received treatment. “Andrew Hastings’ actions are the definition of going above and beyond the call of duty, and he is undoubtedly a deserving recipient of the Bridgestone Bandag Highway Guardian title,” said ATA Chairman, Geoff Crouch. “It’s in the face of adversity that we see the true gems of our industry. The Bridgestone Bandag Highway Guardian accolade is a fitting way to recognise these incredible individuals.” Linfox has a commitment to safety under its internal ‘vision ZERO’ initiative,
Linfox driver Andrew Hastings presented with his award.
working towards no workplace injuries or motor vehicle incidents. According to Victoria Road Manager at Linfox Intermodal, Paul Gregory. He added that Hastings leads by example in this area. “As a driver, Andrew is safe and law abiding,” said Gregory. “Andrew takes pride in his job: is always presented well in uniform and gives informative feedback during tool box meetings. “Andrew’s aspirations are to become a driver trainer. His eagerness has already been demonstrated and clearly there is a care factor for his peers,” he said. According to Bridgestone Australia & New Zealand Managing Director, Stephen Roche, Hastings’ actions are worthy of significant praise. “Andrew Hastings’ story is heart-warming and confronting at the same time,” he said. “His actions go well beyond his job description, and the level of compassion that he showed is nothing short of incredible. We are honoured to recognise him with the Bridgestone Bandag Highway Guardian title.” Together with the ATA, Bridgestone aims to shine a light on outstanding members of the trucking industry through the Bridgestone Bandag Highway Guardian honour.


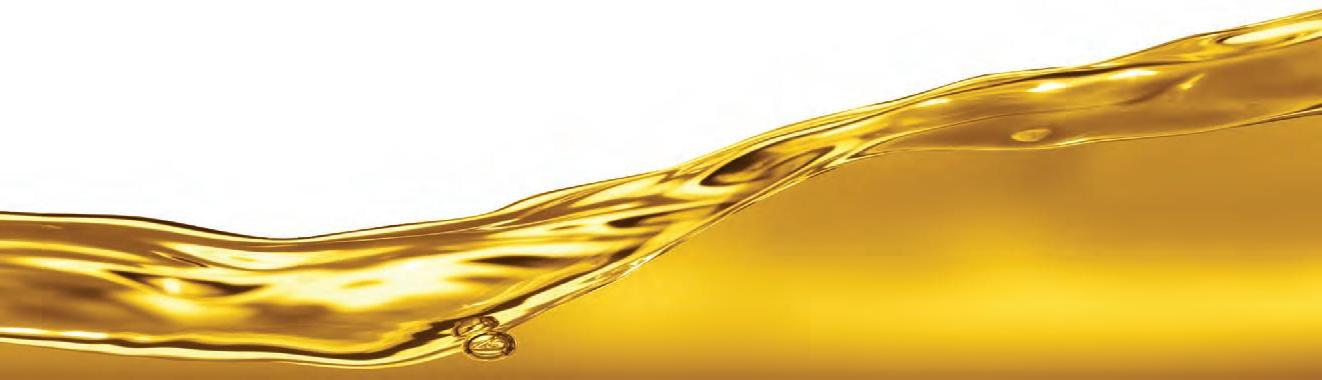
> NHVR releases safety bulletin about heavy vehicle fires
The National Heavy Vehicle Regulator (NHVR) aims to reduce the risk of vehicle fires in the heavy vehicle industry with its latest safety bulletin, following ongoing investigation into causes and preventative actions. NHVR Safety Standards Director, Tony Martin, said the intent of the safety bulletin is to raise awareness of common fire risks and outline actions to help mitigate risks. “We recently sat down with a cross section of industry to tackle the issue of truck fires and it is clear that prevention is better than cure,” said Martin. “We’ve outlined some measures available to different parts of the heavy vehicle industry that can assist in fire prevention,” he said. The Bulletin outlines a number of common fire risks in heavy motor vehicles, including: shorting of electrical cables and connections; inappropriately rated electrical components; fuel line failures; the heat generated by a turbocharger; and maintaining a clean engine bay. The NHVR said there are also preventative actions operators should take, including: reviewing the common causes of fires and identify those that may be present in their fleet; reviewing maintenance management systems to remove or reduce any risk factors and improve the safety of their transport activities; and ensuring those who carry out servicing or modification on higherrisk components or systems on their vehicles, such as electrical systems, have measures in place to verify that fire risks are not introduced. Martin said that when an operator experiences a heavy vehicle fire incident, or a near-miss event, they should report the incident. “This allows the NHVR to improve our understanding of this safety-critical issue,” he said. “Reports can be made to the Heavy Vehicle Confidential Reporting Line or to the NHVR’s Vehicle Standards team. For operators accredited in the National Heavy Vehicle Accreditation Scheme, reports can also be made to the NHVR’s Accreditation team.”
> QLD move on OSOM vehicle permits will boost freight productivity: ALC
The Australian Logistics Council (ALC) has applauded the Queensland Government’s decision last month to extend permit durations for Class 1 Oversize Overmass (OSOM) vehicles to 12 months. “This is a sensible reform from the Queensland Government that will improve the efficiency of freight movement, reduce red-tape for freight operators and help keep costs under control,” said ALC CEO, Kirk Coningham. “ALC advocated for a national review of the rules governing OSOM vehicle movements a year ago, because it was clear that delays in approvals and the constant need to obtain new permits for every vehicle movement was hampering supply chain efficiency, and having a negative impact on our economy. “The decision announced today by the Hon. Mark Bailey MP, Minister for Transport and Main Roads, is a win for Queensland’s freight logistics industry, which will now be able to plan its operations more effectively and see its administrative burden reduced. “As the Queensland Freight Strategy released earlier this year outlined, the state’s freight task is expected to increase by over 20 per cent in the next decade. “With such strong growth anticipated, it is imperative that the Queensland Government works closely with industry participants to enhance the efficiency of the freight network. “This reform of OSOM provisions is the sort of positive outcome that can be achieved when industry and governments work together to deliver regulatory reform. “ALC looks forward to continued discussions with the Queensland Government on further opportunities to reform OSOM arrangements and deliver greater national consistency in this area. “We also encourage the Queensland Government to continue working closely with industry and with the Commonwealth on the National Freight and Supply Chain Strategy, which is due to be finalised this year. “This continued cooperation will be vital in securing the outcome the logistics industry and Australian consumers truly deserve - regulatory frameworks which recognise that freight does not stop at state borders.”

G500 punches above its weight
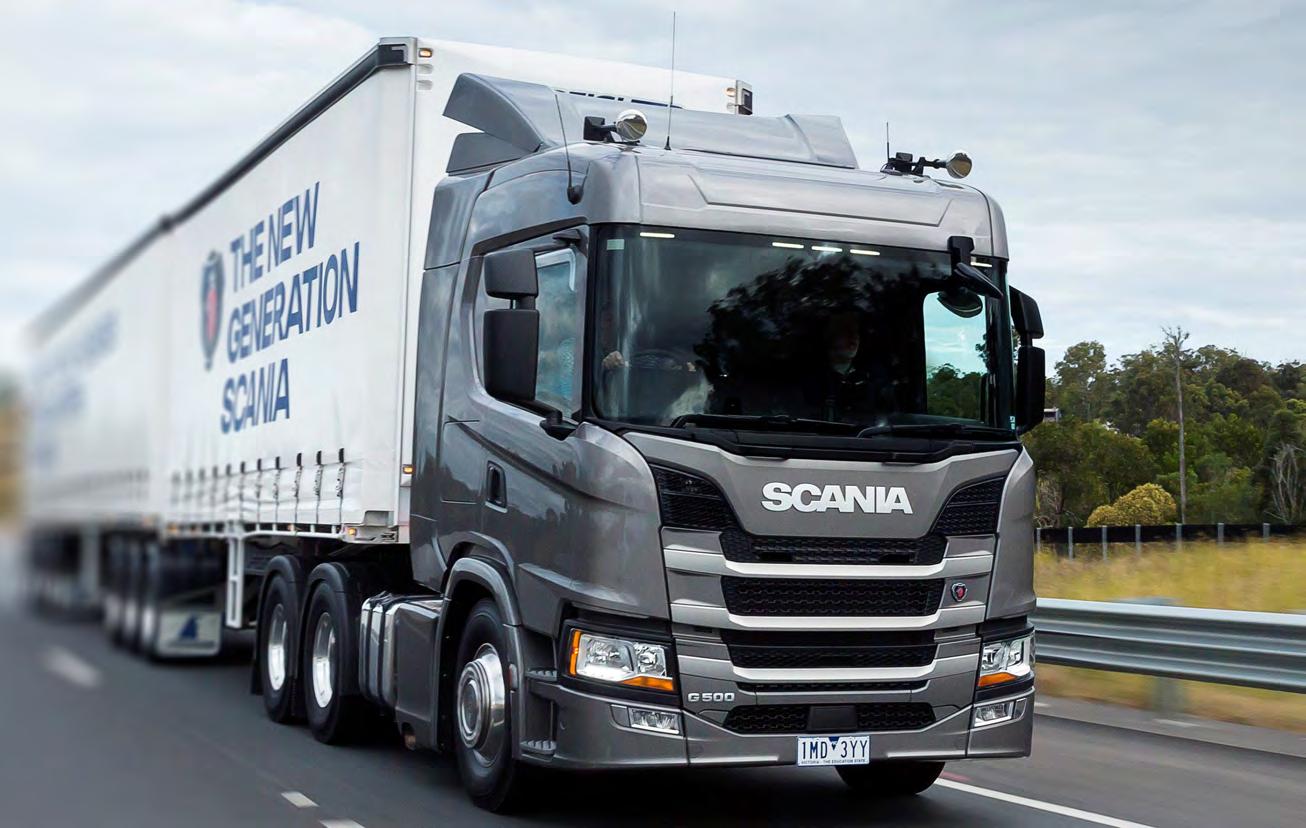
Scania’s New Truck Generation G500 6x4 prime mover is a real surprise packet.
• Brute pulling power. 500 hp and 2550 Nm of torque.
• Fuel efficiency. The new range has outstanding fuel consumption.
• Safety. Unique, world first side curtain roll over airbags as standard plus a host of other features make Scania’s New Truck Generation range the safest trucks in Australia
• Luxury Interior – excellent visibility, great cabin acoustics and customised digital dash.
And, with our included maintenance offer across the New Truck Generation range, you’ll have complete peace-of-mind for 5-years /500,000 km*.
Visit www.scania.com.au
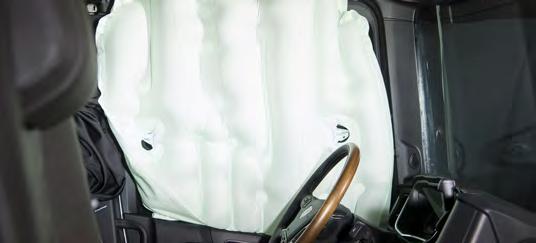

5 YEARS or
kilometRE
maintenance INCLUDED
> K&S Freighters tips Scania for smelter delivery contract

Scania G 500s will operate between the Tomago Aluminium smelter for K&S Freighters in Newcastle.
Commercial vehicle manufacturer, Scania, has delivered eight new G 500 prime movers to K&S Freighters in Newcastle for use on a contract to move alumina or coke from the port to the Tomago Aluminium smelter 20km away. The trucks will run around-the-clock for six days per week, across two 12-hour shifts, so reliable uptime was reportedly a key decision-making factor in the K&S Freighters’ specification process. Scania’s New Truck Generation G 500s have been specified exactly for the task and will pull new Tefco B-double tippers running on Higher Mass Limits (HML) mass management certification. According to Scania, the day cabs are fitted with a fridge and LED headlights, with a rear axle ratio specifically calibrated for the loads they will be pulling over the mostly flat haul route. The latest Scania 4100 Retarder is also fitted to provide the drivers with additional safety margins when hauling 64.5-tonnes gross, while simultaneously extending service brake wear intervals. The Tefco trailers also feature Electronic Braking Systems (EBS) which integrates with the Scania system. Scania said reducing the tare weight of the vehicle was another specification requirement, which led to the selection of the shorter day cab and the selection of a single 400-litre fuel tank, sufficient for a full day’s work. As with all NTG Scanias, the G 500s are equipped with the highest standard of factory-fitted safety equipment, as well as having additional equipment, such as dash and reversing cameras fitted by K&S. The trucks also feature MT Data connectivity for geo fencing and navigation. “We have undertaken a very detailed specification and build program for K&S Freighters for this contract,” said Scania Australia Fleet Sales Manager, Steven Alberse. “First, we discussed with K&S Freighters exactly what the task was that the trucks were required to undertake, acknowledging the need for uptime and excellent endurance over a typical working week,” he said. “With the client undertaking their own servicing we were able to structure a bespoke parts supply and pricing solution to fit the duty-cycle profile of the vehicles, again to maximise their uptime.” Alberse said the trucks will spend considerable time idling and powering the hydraulic systems that raise and lower the tippers. He added that Scania G 500 fleet for the Tomago Smelter contract are not the first Scanias to be based in the K&S Freighters’ yard at Newcastle. “The drivers already have a good understanding about how these trucks drive, and how comfortable, quiet and smooth they are, even with two fullyladen B-double tippers behind the cab,” he said. “The driver response so far has been excellent with a high degree of acceptance for the G 500, and a good level of understanding of how to extract the best performance combination of low fuel consumption and safe on-road driving, in sometimes very heavy commuter traffic.”
BETTER FASTER STRONGER LONGER
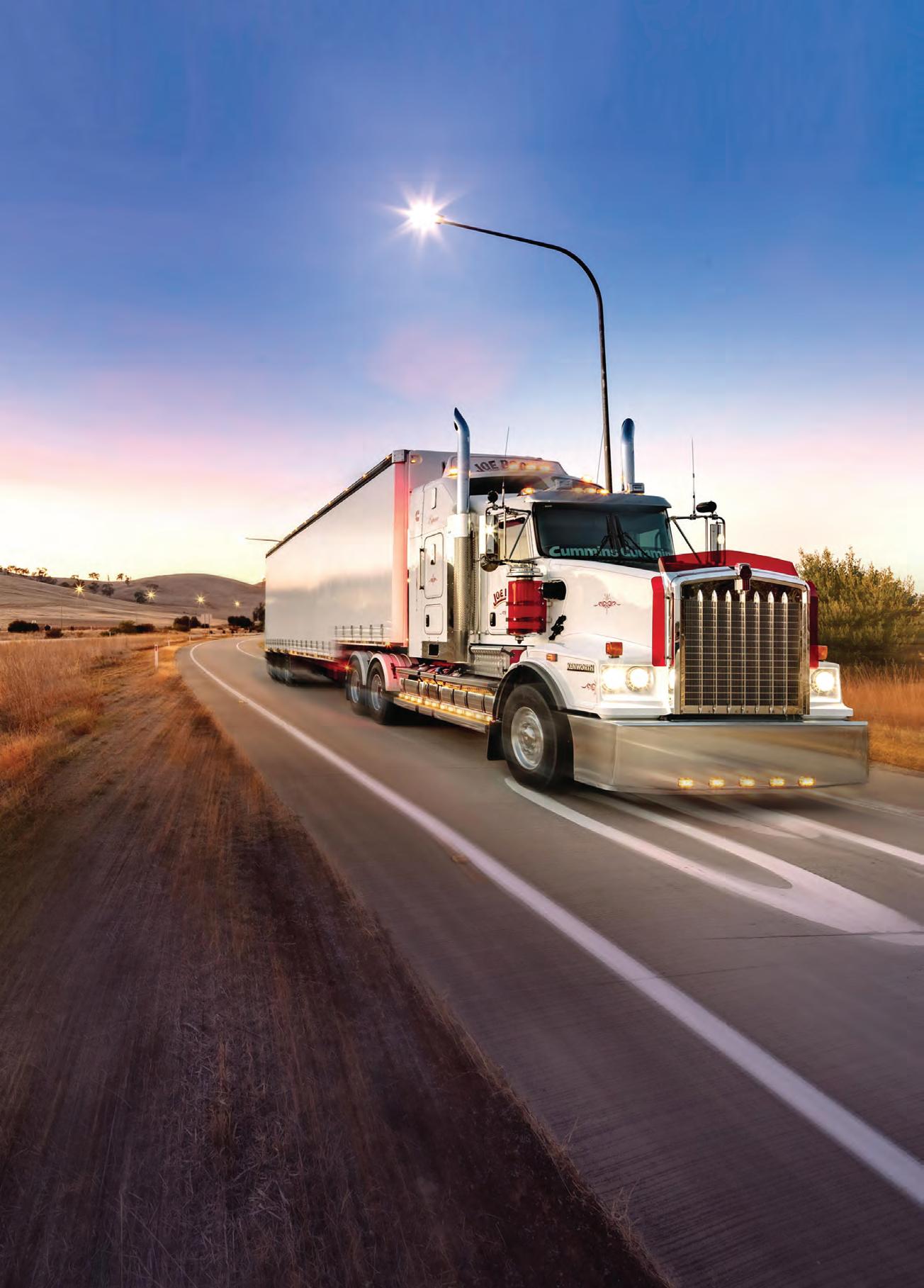
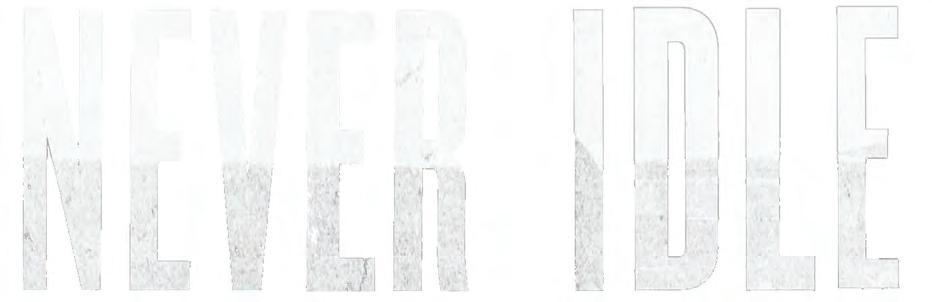
As long as there are engines on the road, machinery on site or equipment in the field, there are ways to help them run better, faster, stronger and longer. 150 years of innovation doesn’t just happen in the lab. It happens because of our people. People who are passionate about doing better. People who prove that experience and expertise alongside quality products will generate innovative solutions. It is our commitment to innovation and continuous improvement that ensures our customers equipment keep running at optimum efficiency throughout our harsh Australian environment and all over the world.


> Road safety campaign has new face

NHVR CEO Sal Petroccitto (right).
Australian Supercars star and current commentator, Garth Tander, will head a new heavy vehicle safety campaign which encourages all road users to give trucks space. National Heavy Vehicle Regulator (NHVR) CEO, Sal Petroccitto, said the We Need Space campaign would provide advice on how light vehicle drivers should act when they are around trucks. “Recent research shows that light vehicles cause up to four-out-of-five crashes involving heavy vehicles,” said Petroccitto. “Being aware of simple safety tips such as a truck’s blind spot, allowing extra distance for a heavy vehicle to brake and the space needed to turn can reduce the risk for all road users. “Having a driver of the quality of Garth Tander keen to learn more about driving safely around trucks shows that everyone can still learn about driver safety on our roads,” he said. “Across Australia we’ve seen a gradual decline in heavy vehicle fatalities from 220 in 2014 to 177 in 2018, but that figure is still too high.” Tander was Australian Supercars Champion in 2007, won three Bathurst 1000s at Mount Panorama, and finished first and second in the Bathurst 24hr Race. He’s joined in the campaign by truck driver Kerri Connors, who was named Tasmania’s best professional truck driver at the Tasmanian Transport Industry awards in October 2018. Petroccitto said the campaign would include three videos and a range of information and fact sheets for light vehicle drivers. “It’s important that all road users are aware that a truck is difficult to manoeuvre, it has large blindspots and can have unpredictable traffic coming from behind, alongside and in front,” he said. “When you add it all together, it really does take a lot of skill for a truck driver to get from point A to point B safely and all road users need to play a role in the safety of that journey.” The We Need Space Campaign was funded by $250,000 from the NHVR’s Heavy Vehicle Safety Initiative program, supported by the Commonwealth Government.
Keep track of your fleet with our compliments.
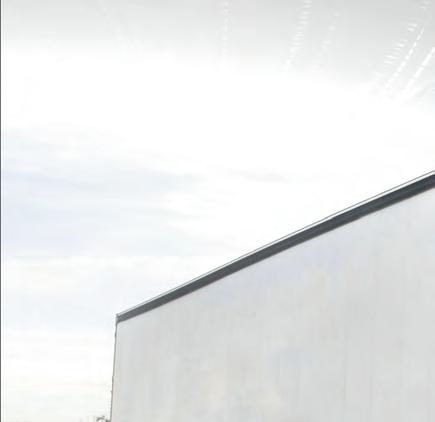





Lower total costs Greater safety Maximised use
As part of our committment to keeping your business moving, when you purchase a new Mercedes-Benz truck, you will also receive complimentary access to the telematics program * , allowing you to monitor driver performance data, track vehicle location and trips, plan for maintenance and receive update information on your vehicle.
To find out more about Telematics, visit mercedes-benz-trucks.com.au/telematics or contact your local authorised Mercedes-Benz Trucks Dealer.
*Offer available until 31st December 2019 and on Actros, Arocs and Atego models only. Telematics services are provided by Directed Electronics OE Pty Ltd ('DE'). Offer is subject to the vehicle owner signing up to DE's Telematics Services terms and conditions during the offer period.
> Road fatalities down for May year-on-year
The Bureau of Infrastructure, Transport and Regional Economics (BITRE) has released its bulletin for May on road fatalities in Australia. There was a total of 111 road deaths during May 2019, according to the report. The current figure is 9.9 per cent higher than the average for May over the previous five years. During the 12 months ended May 2019 there were 1,204 road deaths, which is a decrease of 3.3 per cent from the 12-month period ending May 2018. The rate of annual deaths, at present, per 100,000 population stands at 4.8. This is a 4.8 per cent decrease compared to the rate for the 12-month period ending May 2018. The statistical report is produced monthly and published online. Data is sourced from road traffic or police authorities in each jurisdiction.
> Hino shifts the standard in medium-duty trucks
After its first six months on sale, Hino claims its all-new 500 Series Standard Cab has shifted the standard in the medium-duty segment, primarily due to its class-leading safety levels. “So far, strong sales volumes are reinforcing what we believed when we launched the all-new 500 Series Standard Cab in November 2018,” said Hino Australia General Manager of Brand and Franchise Development, Bill Gillespie. “Customers are no longer willing to accept safety as an option in the Australian medium-duty segment, which is why our trucks feature a classleading safety package as standard. “There have been almost 800 orders of the all-new 500 Series Standard Cab, which positions us well to meet our sales targets for the year,” said Gillespie. According to Hino, the 500 Series Standard Cab boasts a standard level of safety that has never been seen before in a Japanese mediumduty truck in Australia, including Vehicle Stability Control (VSC), Lane Departure Warning System (LDWS), and a Pre-Collision System (PCS) with Autonomous Emergency Braking (AEB), Pedestrian Detection (PD) and Safety Eye (SE). “These safety features have been particularly appealing to our customers in the agitator/mixer industries, while the Hino build attributes of Quality, Durability and Reliability continue to impress our customers in the traditional tilt tray
Hino 500 orders have been strong.
applications,” said Gillespie. “While safety is the primary motivator for many customers, they are also attracted to the superior torque, increased power and improved fuel efficiency of the heavy-duty Hino A05 turbo-charged five-litre four-cylinder diesel engine,” said Gillespie, adding that the six-speed Allison 2500 Series fully automatic transmission is available across the range and accounts for 65 per cent of sales to date. “Customer orders of the 500 Series Standard Cab have been strong across the country with New South Wales leading the way, followed closely by


Victoria and Queensland.” He went on to say that in the overall medium-duty segment – which covers 500 Series Standard Cab and its award-winning stablemate, 500 Series Wide Cab – Hino has sold 908 trucks year-to-date, which translates to a 30 per cent market share – a promising increase when compared to 860 units and a 26.9 per cent share in the same period last year. “With very strong customer orders, we are striving for an overall yearly sales result of over 6000 units, which would be our best result since 2007.” said Gillespie.
> Linfox Group Manager recognised for excellence in road transport
The 2019 Women in Industry Awards held at The Park in Melbourne, celebrated the women who lead, energise and inspire in their respective roles across various sectors including road transport. The Excellence in Road Transport award recognises an individual who has gone above and beyond to improve and positively impact the Australian road transport industry. Master of Ceremonies, Leah McLeod of Studio 10 fame, presented the Excellence in Road Transport Award to Sondra Kremerskothen, Linfox Australia Group Manager Training. Kremerskothen manages 30 trainers, administrators and managers across five sites throughout Australia. She has seen an opportunity to change culture and behaviours within the industry by upskilling Linfox operational trainers to influence positive employee behaviour and attitude. By modernising training, Kremerskothen was able to improve safety and productivity while meeting compliance requirements. Linfox has reportedly increased compliance by over 100 per cent in the past 18 months. Kremerskothen also leads a femaledriven program, which trains and licenses women to be heavy vehicle drivers. “I am a group trainer and I have been fortunate enough to be employed by Linfox, a fantastic employer. I have a great group of trainers who have developed a passion to change behaviour on Australian roads,” said Kremerskothen in her acceptance speech. She added that her team is especially passionate about improving road safety for heavy vehicle operators. Kremerskothen also actively encourages women to join the road transport industry. She praised the success of a female driver training program, which is a joint initiative made possibly by Linfox, Volvo Group Australia, Wodonga TAFE, Australia Post and Transport Women Australia Limited (TWAL). “We now have 14 women ‘through the doors’ and actually driving for Australia Post and Linfox – these women are amazing,” she said. “It’s incredible to see where they have come from. They’re all mums with adult children who just want to come to work, get the job done well and get home safely.” The finalists for the 2019 Excellence in Road Transport award were: Candice Lureman, Debbie Reich, Grace Lennox, Michelle Aspinall, Rose Ferguson and Vanessa Williams.
MAXIMIZE YOUR REVERSING SAFETY
Reversing with WABCO TailGUARD™
TailGUARD™ is a new WABCO Retrofit Solution for more safety when reversing. It recognizes small, large, fixed and moving objects in the blind spot behind the vehicle and brakes it automatically:

TailGUARD™ AUTOMATICALLY brakes the vehicle when it detects people or objects
Helps the driver in the dark and when restricted visibility is present.
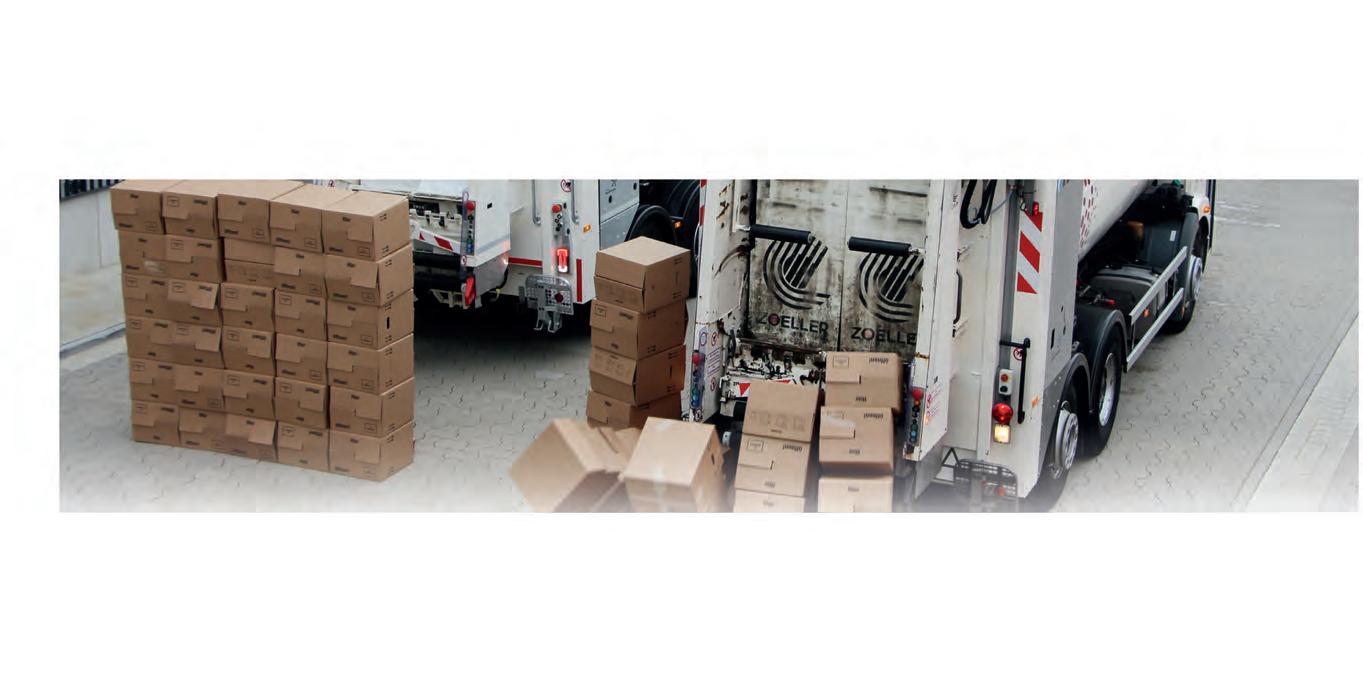
Helps reduce accidents and injuries of people who are behind the vehicle, when reversing.
Reversing without WABCO
TailGUARD™
> ATA restructure focuses on safety
The Australian Trucking Association (ATA) is combining its TruckSafe, Safety Truck, safety promotion and safety research activities into a single section of the organisation. The section will be headed by a new Safety, Health and Wellbeing Director, Melissa Weller. “Until now, the ATA has operated TruckSafe as a separate business unit to the rest of the ATA,” said ATA CEO, Ben Maguire. “This has resulted in duplication. We have also missed out on opportunities to cross-promote what we do. The restructure will enable us to leverage more benefits from the expertise of the TruckSafe board and will place safety accreditation and promotion at the centre of the ATA’s work. It will bring TruckSafe into the mainstream of how we work as a team. “The restructure emphasises our commitment to TruckSafe as an important part of the future of truck safety regulation. TruckSafe accredited operators do not receive the same regulatory concessions as NHVAS operators, even though they need to meet higher standards. This is not just unfair and anti competitive; it discourages operators from being in a higher quality scheme. “Our first submission to the Heavy Vehicle National Law review proposes that safety-based schemes like TruckSafe should be formally recognised under the law, with the NHVR regulating safety schemes and auditors rather than trying to run one.” The restructure follows Justin Fleming’s decision to leave the ATA after 10 years with the organisation. “Justin’s passion and commitment to TruckSafe and the industry is highly regarded by our team, sponsors, members, board and all the operators he deals with,” said Maguire. “Through Justin’s leadership, many a business has benefited from the business and safety improvements that TruckSafe offers. The industry is better for having people like Justin involved.” ATA Chair, Geoff Crouch, said the board greatly appreciated Justin’s dedication and leadership. “During Justin’s tenure at the ATA, he always demonstrated an unwavering commitment to promoting TruckSafe as the best safety management solution for Australian trucking operators, regardless of size,” said Crouch. “Justin’s dedication and passion have ensured that many companies have benefited from the TruckSafe product and improved their safety. Justin can be truly proud of this achievement. The restructure will deliver a compelling vision for the scheme’s future and a safer, healthier industry.” TruckSafe Chair, Ferdie Kroon, thanked Fleming for his commitment. “A large number of industry people, from all walks of life, have benefited and continue to benefit from Justin’s excellent work,” said Kroon. “In conjunction with Justin, the TruckSafe board has worked very hard on the future of our product. At our next board meeting, in July, we’ll hear a pitch for a new digital platform. We’ll also work on how we can further simplify our standards and guidance material.” Fleming said that TruckSafe was now in the best position it could possibly be to realise its full potential in the market. “We have so many exciting developments that will be released in the near future to assist all our operators with not only compliance, but also to make sure they are the safest trucking businesses in Australia,” he said. “I’ve had an incredible career in the trucking industry, and it’s been amazing because of the great people in the industry. I would like to thank everyone for their friendship during the last decade. “I also want to thank TruckSafe Adviser Kevin Walsh for his support over many years. I now plan to concentrate on my agricultural businesses and to do some management consulting in the
Melissa Weller.
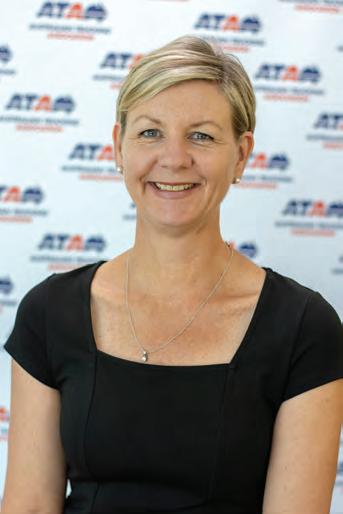
meat industry. I started my career as a trade-qualified butcher, so it will be fascinating to go back into the industry at a senior management level. “I am leaving TruckSafe in a wonderful pair of capable hands, in Melissa Weller. I know that Melissa will take the business forward into the future.” Weller said that her vision, as a safety practitioner, was for everyone to get home safely, every day. “Safety links to every aspect of business,” said Weller. “You simply can’t have a productive and viable business if it is not a safe business. I am very excited to have this opportunity to lead the ATA’s safety communication, TruckSafe safety management system and safety, health and wellbeing education. We have started vital actions in these areas, and I am looking forward to getting results with our very motivated and safety focused ATA community.” Weller has managed safety projects for eight years. In 2016, Melissa was recognised by the Institute of Public Works and Engineering Association awards for excellence and was a 3M Diamond Road Safety Awards finalist for a safety project she coordinated across nine local government areas.
> Mack celebrates centenary in Australia
Mack Super-Liner released as part of its centenary celebrations.
In honour of Mack trucks working in this country for 100 years, Mack Trucks Australia has released two limited edition models. Revealed at a recent customer event, the two gold bulldog models are part of Mack’s 100 Years Celebrations. The models, a Super-Liner and Trident, will be available for purchase by customers until the 100-truck allocation is exhausted. The recently revealed trucks were presented in green and gold, a nod to Mack’s authentically Aussie-made status. The company has been building trucks locally since 1963. According to Mack Trucks Australia Vice President, Dean Bestwick, Mack is the longest serving truck brand in Australia and has long been synonymous with durability and reliability. “Mack is one of the most iconic transport brands in the world, so it’s only right that such a special milestone be celebrated with such special trucks,” he said. “I think it is a

great opportunity for our passionate customers to own a piece of Mack history.” Mack trucks arrived in Australia in 1919, with the first bulldog, a tried and tested AC Model used in World War I, landing shortly after the end of the Great War. Not long after this first example arrived, Macks were put to work across the country to grow a young Australia into a thriving country. “Mack Trucks were counted on when Australia needed tough trucks to get the tough jobs done, and in this way we remember those first ever bulldogs,” said Bestwick. “We are proud of our history and want to showcase that for all to see, with an eye to the future using innovative technology in each of these models.” While the Limited Edition range is designed to commemorate Mack’s heritage and history in Australia, the trucks are bristling with up-to-theminute technology. The Super-Liner sports Mack’s legendary 685hp MP10 engine while the Trident totes the 535hp MP8 powerplant. Both feature the mDRIVE automated manual transmission along with Mack’s suite of active safety features. A number of special features have also been added to commemorate the uniqueness of each truck. These include unique 100 years identification insignia, inside and out, as well as luxurious cab fittings, an owner’s kit, a larger grille, and illuminated lights to highlight Mack’s branding, among other features. Furthermore, each truck will be identifiable by a number between 1 and 100 to signify its special edition status. The 100 Years Limited Edition trucks fit with Mack’s tradition of special edition anniversary models, following on from the Southern Cross Limited Edition range in 2013, the Centennial Limited Edition in 2000, and the 1988 Bicentennial Limited Edition Super-Liners.
> PPG launches paint system in the US and North America
PPG Delfleet One paint system includes undercoats, topcoats and clearcoats.
Paint and coating specialist, PPG, has introduced its PPG Delfleet One paint system to the US and Canadian markets. This complete and compact line of advanced coatings is specially formulated to address the demanding refinish needs of the commercial transportation industry, according to PPG. PPG said in a statement that it engineered these next-generation coatings to deliver outstanding colour matching, ease of use, increased productivity and the commercial transportation industry’s lowest volatile organic compound (VOC) emissions for a premium paint system with full colour capability. The PPG Delfleet One paint system includes undercoats, topcoats and clearcoats. It features 57 per cent fewer VOC emissions compared to a traditional paint system, ensuring compliance with regulations in all regions of North America. “The PPG Delfleet One paint system is a major technological advance and the
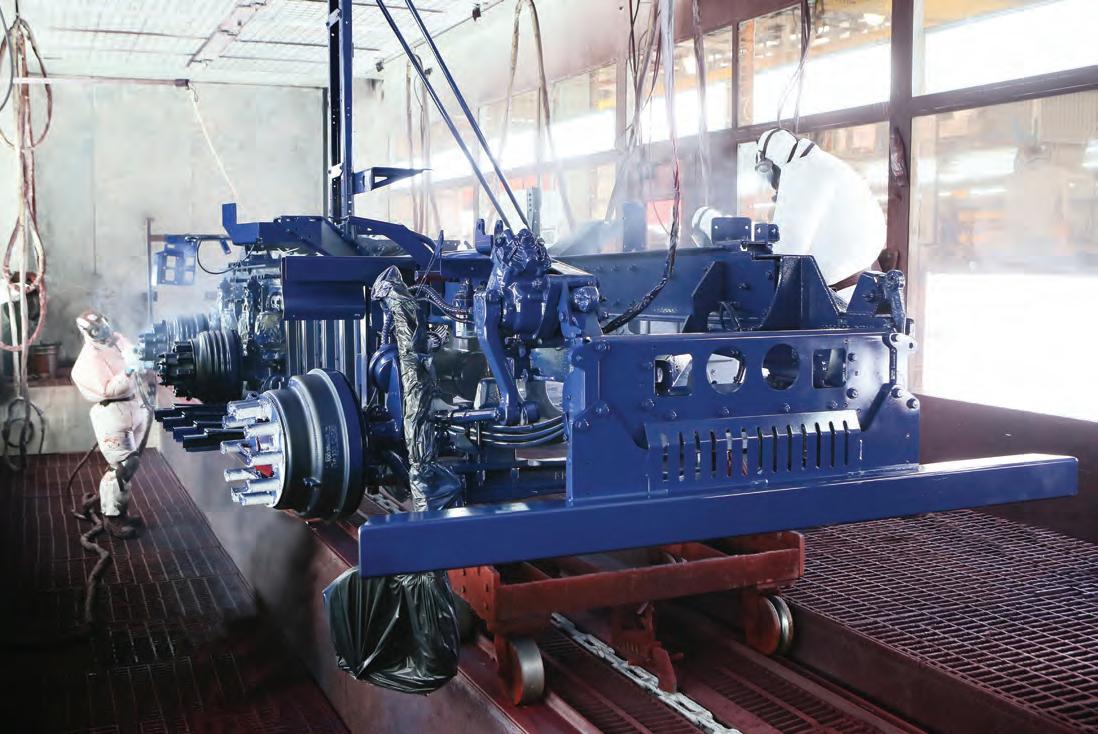
direct result of PPG asking the people who matter – fleet operators, truck body builders, repair facility painters and others who work with these types of products every day – what they wanted in a premium paint system,” said J.J. Wirth, PPG Segment Manager, Commercial Coatings, US and Canada. “We believe our customers will appreciate the product capabilities and productivity boost offered by the most environmentally progressive premium system in the commercial transportation original equipment manufacturer (OEM) and repair markets.” The PPG Delfleet One paint system includes the latest aluminium and pearl pigments to provide full colour capability for direct gloss, basecoat and matt colours. The compact paint system has 42 toners, four binders and four paint additives, reducing on-hand inventory requirements yet providing the resources needed to address all refinish or OEM work. The entire system is supported by PPG’s extensive colour database that expands as new colours, special mixes and variant formulas emerge. It uses the exclusive PPG Delfleet One Tint Guide and PPG Delfleet One Color Deck, which houses thousands of OEM colour chips and variants arranged chromatically. The system also ensures accurate color match through PPG’s cutting-edge color tools that include the Rapidmatch XI spectrophotometer, Touchmix XI computer and Paintmanager XI software. “The tools that support the PPG Delfleet One paint system make colour selection and matching accuracy much easier,” said Wirth. “Painters can rest assured that the system’s ‘what you see is what you’ll spray’ approach precisely matches commercial vehicle colours. All our colour tools are supported by the PPG Color Matching Laboratory, which is exclusively dedicated to accurately matching commercial vehicle colours.”
> Fifth consecutive month of growth for EU commercial vehicle registrations

Over 1.1 million new vehicles were registered in Europe for the period of January to May.

Commercial vehicle registrations in May 2019 continued to increase in the EU (+8.5 per cent), according to the European Automobile Manufacturers Association (ACEA). In May 2019, demand for total new commercial vehicle registrations was sustained across all segments, with trucks and buses recording the highest percentage increases. The region’s five largest markets contributed positively to this result. Germany (+24.7 per cent) and France (+12.6 per cent) saw the strongest gains last month. From January to May 2019, the EU market for commercial vehicles grew by 6.5 per cent, counting 1.1 million new vehicles in total. Germany led this growth with a 14.7 per cent increase, followed by the UK (+7.9 per cent), France (+7.7 per cent), Italy (+3.9 per cent) and Spain (+3.3 per cent). Last month, EU demand for vans remained positive, up 5.8 per cent compared to one year ago. With the exception of Spain, all major EU markets recorded solid growth in May. Germany (+23.5 per cent) showed the highest increase again, while France (+9.5 per cent), the UK (+5.4 per cent) and Italy (+5.1 per cent) followed with single-digit percentages. Five months into the year, registrations of new light commercial vehicles grew by 5.9 per cent to reach 908,291 vehicles sold. Each of the largest markets made a positive contribution to the region’s overall performance: Germany (+14.7 per cent), the UK (+7.5 per cent), France (+6.9 per cent), Italy (+6.0 per cent) and Spain (+3.8 per cent). In May 2019, demand for new heavy trucks (16 tonnes and over) grew significantly (+21.2 per cent) compared May 2018, counting 31,910 units registered. Growth was driven by double-digit gains in France (+35.3 per cent), Germany (+25.2 per cent) and Spain (+14.1 per cent). The UK (+6.2 per cent) and Italy (+5.0 per cent) followed with more modest increases. From January to May 2019, 143,694 heavy trucks were registered across in the European Union, or 8.6 per cent more than during the same period in 2018. The UK (+17.6 per cent), Germany (+14.8 per cent) and France (+14.5 per cent) posted strong increases, while the Italian (‐8.6 per cent) and Spanish (-1.9 per cent) markets saw falling demand for new heavy trucks.
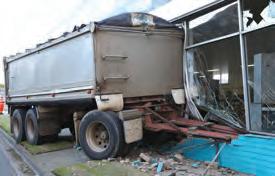
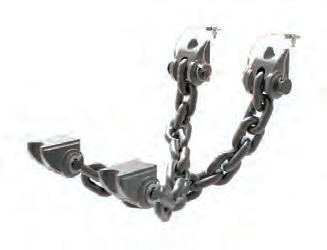

IAN BROUGHTON
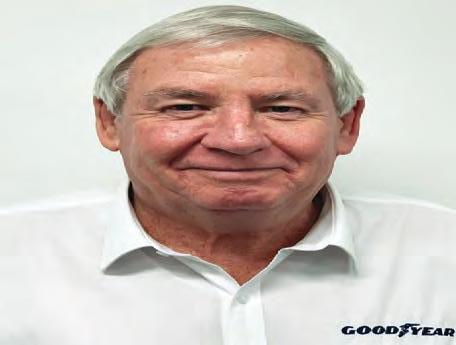
Ian Broughton has worked in the tyre industry since 1970 starting as a Technical Assistant with Dunlop Tyres in Rhodesia (now Zimbabwe). He has had various roles covering all aspects of tyre manufacturing and test laboratories. He studied Polymer Chemistry, Engineering and Design and is also a qualified trainer and an associate member of the Materials, Minerals and Mining Institute.
TREAD
RECKONING T he Customer Engineering team at Goodyear Dunlop Australia plays a crucial role as it ensures customers get the best performance from our tyres. It is a part of the global Goodyear technical community and provides an important link between the customers, tyre designers and manufacturing. This communication assists in developing new tyre sizes and products while ensuring key attributes such as running cost are minimised. Having local engineering allows products to be tailored specifically for the Australian market which is important given our unique roads, regulations and conditions. In the ‘80s working as a field engineer I began truck tyre testing at Nolan’s Interstate Transport based in Gatton, Queensland. They are a well maintained fleet specialising in transportation of produce from the Lockyer Valley to various destinations. The typical steer tyres were 11R22.5 and were at maximum capacity in terms of load and pressure. We were to help solve this by driving the conversion from 11R22.5 to 295/80 R22.5 resulting in further improvements in productivity. Now nearly 34 four years later we are seeing
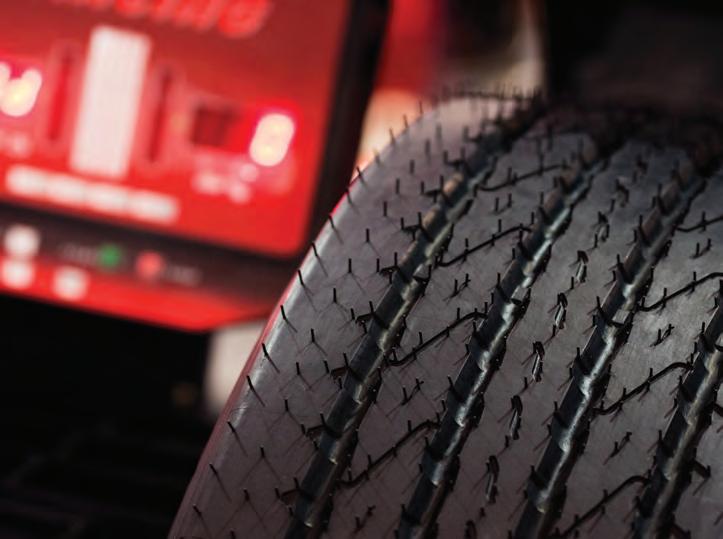
For a rubber compounder controlling heat build up in tyres remains critical.
“Casing design is also critical as the total number offlex-cycles the tyre will complete during first life and subsequent re-treads could be in the order of20 million.” Ian Broughton Goodyear Dunlop Senior Customer Engineer
steer axle loads are again approaching the tyre’s maximum load capability. This serves as a reminder that the industry requirements are always evolving. Controlling heat build-up in tyres, from a rubber compounder’s viewpoint, is critical. Tread compounds to satisfy the demands of current tyres rely on specialsed polymers both natural and synthetic. Technically enhanced reinforcing fillers along with other advanced additives are required to return high mileage, improve wet grip while keeping rolling resistance at low levels. Casing design is also critical as the total number of flex-cycles the tyre will complete during first life and subsequent re-treads could be in the order of 20 million. Once we identify a need for new products our product development process kicks in. This involves market review, competitor benchmarking and manufacturing feasibility. After passing these evaluated the design engineers and compounders create the detailed design including mould cavity shape, pattern, materials, compounds and reinforcements. New designs are simulated and tested prior to the manufacture of prototypes which are then tested in real-world conditions. To support the field trials, Customer Engineering use a number of tools. These include Data loggers to measure inertial forces and determine the severity of the operation; lateral & longitudinal acceleration, yaw, pitch and roll rates. Footprint pressure mapping sensors allows us to determine the shape and pressure profile of the tyre footprint; and portable weigh scales confirm actual axle weights Testing is normally conducted in at least two fleets using test and control tyres. The evaluation can take up to two years to complete and includes regular inspections and reporting. Treadwear can be difficult to predict and needs to consider many parameters which will influence the result such as route and topography; vehicle type; driver behavior; seasonal influence; maintenance (vehicle geometry, inflation pressure control, tyre rotations); and axle loadings. Feedback on vehicle handling, driver comfort, the tyres grip and response are also noted. On a regular basis, tyre test reports are submitted and reviewed with all stakeholders in the global development team. Modifications and design tuning are discussed and implemented with a key focus on the end customer’s needs. After extended field testing test tyres are examined in detail with a final field report issued. A sample of worn tyres will be retuned for laboratory analysis. Further testing is conducted by returning the tyres to the field after
Ian Broughton at work.

being retreading in a Goodyear retread facility. Special attention is paid to casing integrity and sidewall condition and is again monitored until removal. In some case the retreading process is repeated giving data over several retread cycles. Finally, tyres are recycled through responsible tyre recyclers, which is important to Goodyear being a foundation member of Tyre Stewardship Australia of (TSA). In the time I have been in the industry there has been an enormous shift in the tools and technology used to understand and design tyres. This trend will continue and enable tyres to evolve as vehicles become more advanced. Despite this the goal of understanding our customer needs and ensuring continuous improvement remains the same.