
16 minute read
Final Mile
ZOOM MORE
The Mazda BT-50 has undergone a ground-up renewal for 2021.
The initial line-up of dual cab models of the 2021 BrandNew Mazda BT-50 range became available in Australia in October. The capitals on the words ‘Brand-New’ are Mazda’s reference to the significant number of changes to the BT50 range which had its world premiere in June and is now available here just a few months later. This has been a universally challenging year for business globally, yet Mazda has stayed true to its plans for the BT-50, probably in response to the number of new models coming from other manufacturers including the Isuzu D-Max with which the BT-50 has shared some development. Mazda has designed a relatively muscular looking exterior which is tempered with comfortable interiors and a plethora of built-in safety technology. Mazda’s commitment to offering bestin-class safety features carries over from its passenger cars and SUVs to the BT-50 with standard equipment including Adaptive Cruise Control, Autonomous Emergency Braking, Lane Departure Warning, Blind Spot Monitor and Rear Cross Traffic Alert as well as the expected functions such as Anti-lock Braking System and Dynamic Stability Control. SRS airbags are fitted for the driver, front passenger, side curtain, driver’s knee and driver’s far side to afford a significant level of occupant protection in the unfortunate event that the other systems are unable to prevent a serious impact. The new BT-50 line-up includes 4x2 and 4x4 drivetrains, six-speed manual or six-speed automatic transmissions and Dual cab-chassis and dual cab pickups with single and extended ‘freestyle’ cabs expected to join the range by early 2021. Three trim levels are available across the XT, the sportier XTR, and the high-spec GT which is available exclusively as a 4x4. All three models are available in cab-chassis or pickup configuration, and interestingly, 4x2 models are only available with the six-speed auto. Power is provided by a turbocharged 3.0 litre, four cylinder diesel engine which delivers 140kW peak power with 450Nm of torque available between 1,600 and 2,600 rpm which should provide sufficient pulling power for most circumstances and is much the same engine as currently available in the D-Max and offers more power and torque than the previous BT-50. Depending upon the specific model, a focus on saving weight has reduced tare weight by around 50kg from the previous BT-50 which makes a modest yet worthwhile contribution to fuel efficiency. Again, depending upon the
model, combined cycle figures of down to 7.7lt/100km are claimed, which is an improvement on the previous model’s 3.2 litre five-cylinder engine’s results. The 3,500kg braked towing capacity is complemented by a payload at least in excess of 1,000kg for all models. The base XT models have a seven inch colour touchscreen infotainment system, and the XTR and GT models are equipped with a nine inch version, all including Android Auto, wireless and USB connected Apple CarPlay, plus Bluetooth hands-free telephone and audio capabilities as well as DAB+ digital radio. The touchscreen also serves as the monitor for the reversing camera which is standard on all models. Satellite navigation and keyless entry are also standard in the XTR and GT packages. Adaptive Cruise Control with a ‘Stop & Go’ function is standard on all BT-50s fitted with automatic transmissions and included in the features of automatic GT versions is a remote engine starting function. The BT-50’s Hill Descent Control is particularly useful when towing or when venturing off the pavement by bringing engine and wheel
GT packages come a with remote engine starting function.
braking into play without any pedal input from the driver. The 4x4 models are equipped with a rear diff lock which can be activated by a switch on the dash. Mazda Australia provided some significant input into the overall BrandNew BT50 project and as part of that the local in-house engineering team has designed an optional premium bullbar which integrates with the BT-50’s vital
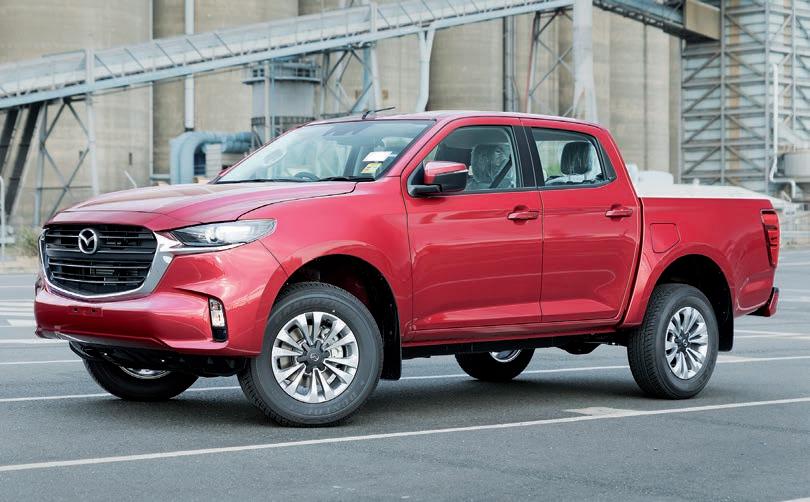
A braked towing capacity of 3,500kg is complemented by a payload in excess of 1,000kg.
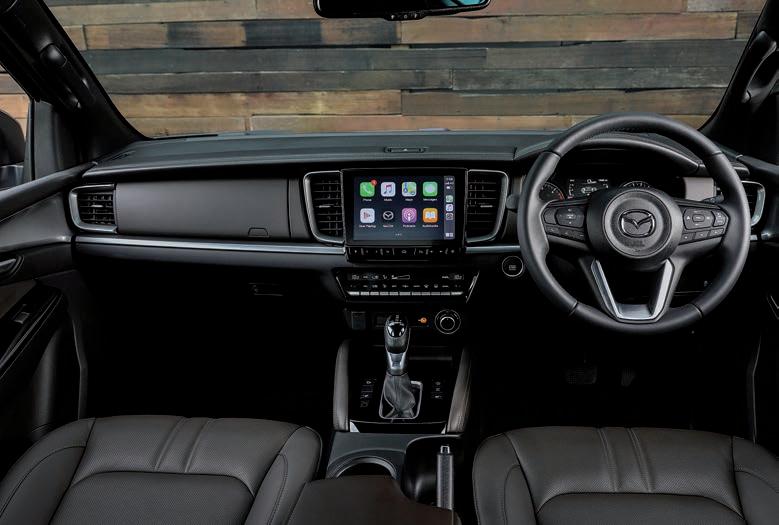
safety technologies such as crumple zones, airbags and the numerous systems included in the Advanced Driver Assistance safety packages. Known as the “Queensland bar” the unit was developed for heavy-duty applications such as found in the Far North of Australia but should appeal to buyers regardless of their location. The black finished steel bar offers headlight hoops to afford additional protection to the BT-50’s front end. Where equipped, the front parking sensors remain fully operational and the bullbar has been thoroughly tested to ensure there are no compromises with the engine and transmission cooling functions. A matching locally designed Sports Bar is available for the pickup bed. The pickup’s tonneau cover continues along the previous BT-50’s path of removing the ‘bungy cords’ of traditional ute tonneaus which enhances style and increases durability at the same time as improving access via the tailgate. This latest BT-50 offers sophisticated technology, especially in the area of safety, plus the performance and style levels demanded by the Australian market.
PLAYING
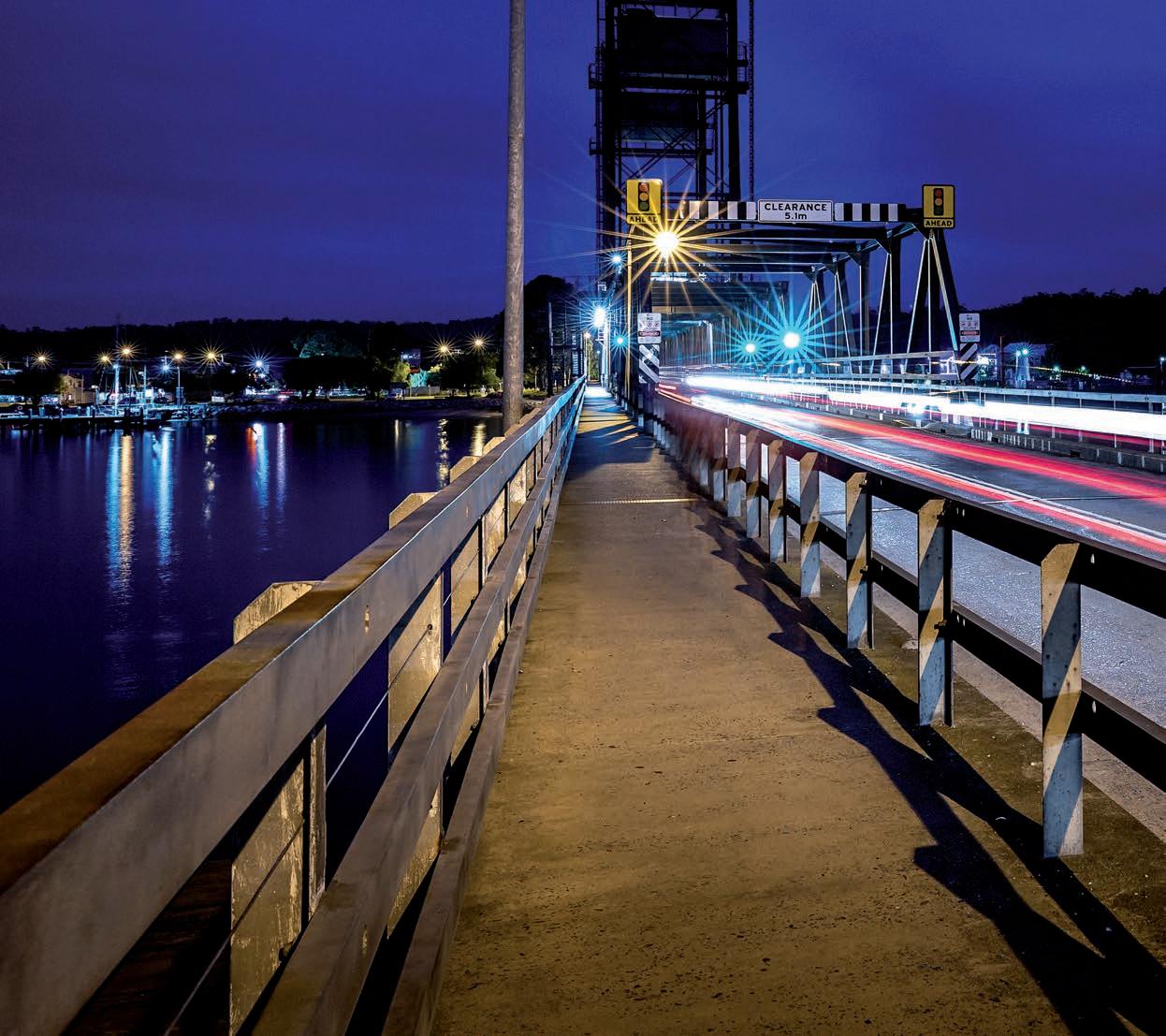
SafeWork NSW is the state’s workplace health and safety regulator.
The main functions of SafeWork NSW include the provision of advice aimed at improving health and safety at work, the administration of licences and registrations for potentially dangerous work, the investigation of workplace incidents, and the enforcement of work health and safety regulations within New South Wales. SafeWork’s WHS Regional Director Lisa Foley displays a real passion
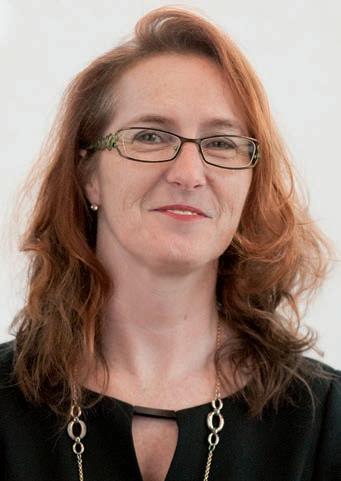
about supporting the road transport industry and, along with her team, engages regularly with the sector including attending industry events and conferences where she frequently focuses on incidents relating to nondriving activities. “To get into the heads and hearts and minds I find myself having to use real life incidents where people know what I’m talking about and therefore I am able to catch their attention,” Ms Foley says. “Truck drivers know about fatigue, drugs, tailgating and trip planning but how many times is a truck driver going to jump out of the cab and not engage the handbrake? It only takes one time for him to do it and be fatally crushed.” SafeWork NSW doesn’t use the word ‘accident’ according to Ms Foley, as the truck driver has successfully driven from A to B and potentially encountered a mix of opportunities for accidents which they have successfully avoided. “Among the key harms we have identified includes ‘failure to immobilise’ where they get out of the truck without applying the parking brake and within moments the truck is crushing them, often as they have tried to get back in to apply the brakes,” she says. “We had a run of three such fatalities over a three-month period at the end of 2019.” Other incidents can be due to distraction during the process of coupling or uncoupling a trailer, so the driver leaves the yard and the trailer drops off a few kilometres down the road. “That typically happens while the truck is in motion on a road, but the root cause is back in the yard,” Ms Foley says. “A driver or offsider can become blind to the hazard of a reversing forklift during loading and unloading because they are so used to the reversing beeper of the forklift they get distracted and find themselves impacted by the forklift.” SafeWork statistics and injury data are generally recorded according to where the incident happened. For example, an injury caused by material falling off a truck at a construction site will be marked down as a construction incident because it happened on a construction site. “But the root cause is actually to do with the transportation of products,” Ms Foley says. Not all incidents, however, involve truck drivers and loaders. “We’ve had a run of fatal incidents where the driver or mechanic is doing work on
IT SAFE
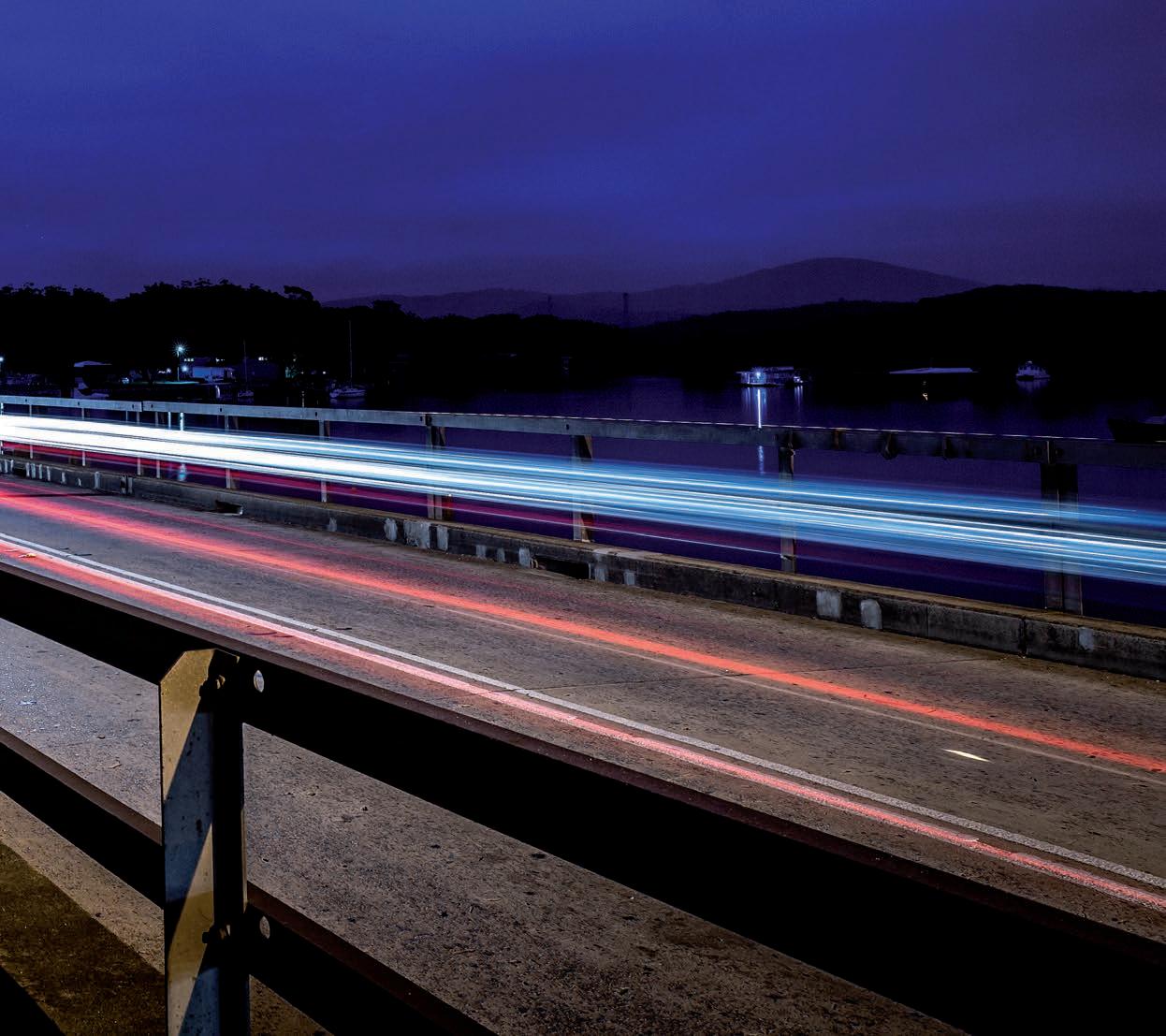
a suspended component of a hydraulic system and are doing so without using any bracing or chocks. If the hydraulic system for whatever reason fails, there’s nothing stopping it from coming down in a hurry,” explains Ms Foley. SafeWork’s Manager of the Central West Scott Murray is based in Dubbo. With his team he is developing a compliance strategy that is educational as well as about enforcement. “Industry consultation has certainly been a major factor of this plan,” Mr Murray says. “It is important for us to differentiate ourselves from the other regulators in the Heavy Vehicle industry such as the National Heavy Vehicle Regulator, Roads Maritime Services and other entities in various jurisdictions including police. We didn’t want to come along as yet another regulator tacking on another list of rules. There are a lot of injuries and deaths that don’t receive the media attention that road accidents and road safety related incidents get according to Mr Murray. People can be surprised at the number of and types of serious injuries and the deaths that occur from the transport sector in non-driving activities. “As a workplace safety regulator, we have focused our latest plan at those non-driving activities because they do account for a lot of misery within the industry. Our whole approach has been one of collaboration and industry consultation and is not all about a ‘big stick,’” he says. “It’s about how can we make genuine improvements and lift the profile of workplace health and safety because in the transport sector, when people talk of safety, the industry straight away thinks of road safety.” As most drivers know about the dangers of fatigue, they will try to wrap their hours around technical logbook schemes according to Mr Murray. “Most know about the dangers of drink driving or drugs in their system. Most know about trip planning. There is a lot of money and resources being spent in that road safety space and most drivers have an inherent appreciation of those risks,” he says. “But when it comes to the same driver who is acutely aware of those on-road risks, he’ll pull up at the depot and he may just casually jump up on the back of the truck to help unload it. When it comes to non-driving that level of risk awareness is not carried through to other tasks which aren’t as glamorous as driving, but statistics show they can injure and kill more people than the driving incidents themselves.” Mr Foley says it’s not about when they are driving A to B, but rather about when they reach their destination. It’s about the safety in doing the loading and unloading and also ensuring they have an appropriate place to take the rest break, go to the toilet, make a coffee, and to be able to have a bit of a break to clear their heads he explains. “The rules and responsibilities for the loader of the truck are very much under the control of the NHVR, so with us, it’s about functions such as dropping the legs on the trailer or it’s the activity of getting on and off to hook up the lines,” says Mr Foley. “Anything where there is a risk that puts a force on the body.” It’s all the little things that accumulate such as jumping out of the cab and rolling an ankle. “A truck driver can have had a lifetime of knocks to their body and the accumulation of those physical injuries is going to lead on to them potentially being not as fit as they should be as they become older,” says Mr Murray. He adds, “Now how do you get that into the message to the new 20-year old whose just taken up his licence?”
SITE OUT OF
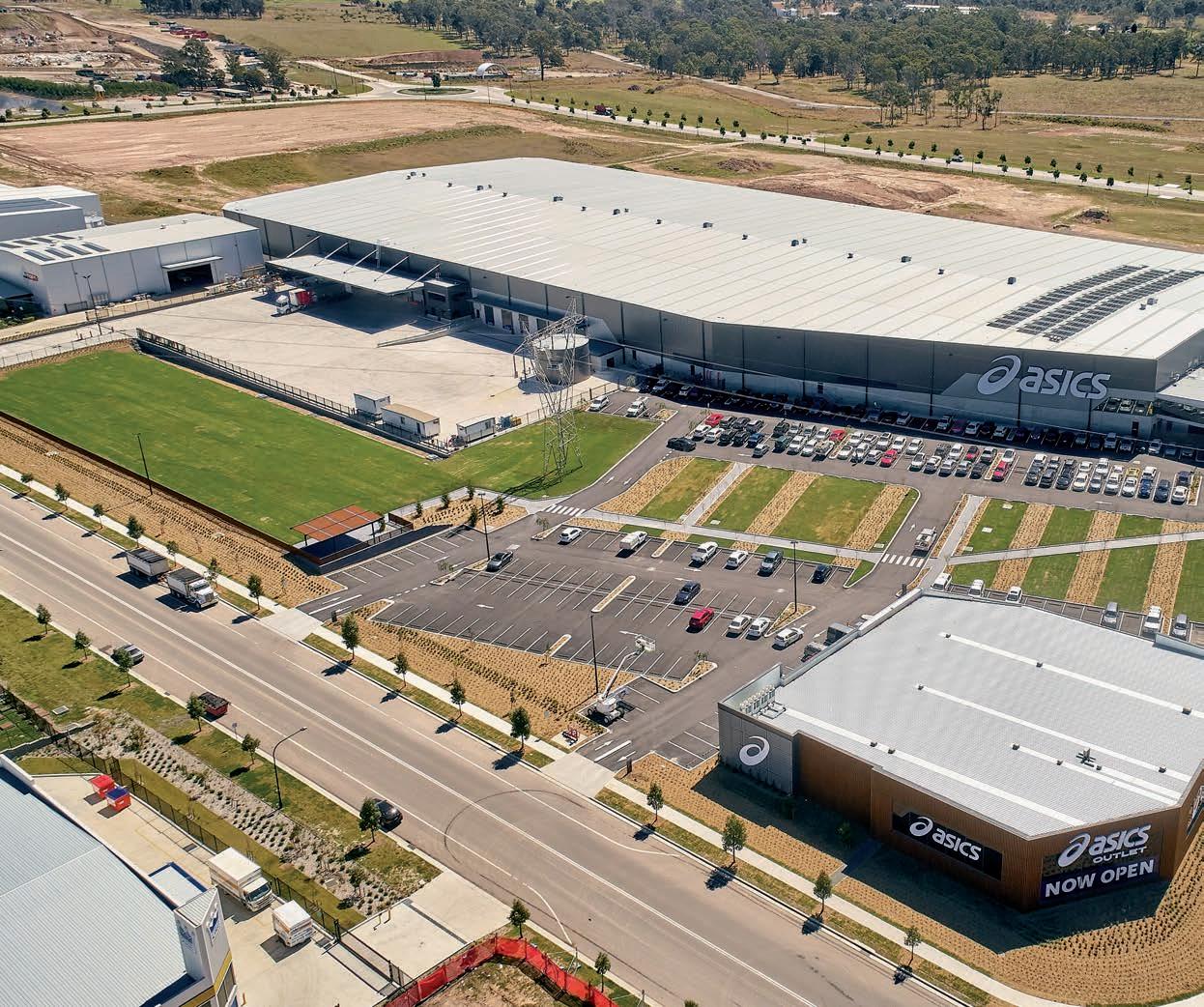
Commercial road transport and logistics operators in need of purpose-built commercial and industrial facilities are looking to CTFD Group to provide comprehensive solutions that balance the requirements of costs, design and development.
CTFD Group, a specialist solutions provider when it comes to corporate headquarters and warehouse delivery, has been working with transport and logistics related customers since it was founded in 2004. The boutique development group offers a comprehensive service with early intervention on behalf of its clients through the process of property procurement, location development, construction, design and other necessary forward-thinking requirements. This includes taking into account the road network that surrounds the proposed site, zonings and all applicable industrial operational requirements according to statuary guidelines. As it compiles a detailed brief from the client, usually in close collaboration with the Chief Executive Officer or Chief Operating Officer, CTFD commences the first phase of the project by drafting up a wish list accounting for warehouse spatial considerations such as warehouse height, point load requirements, cubic capacity, truck and trailer combination allowance including vehicle swept paths, turning circles, loading docks and even future growth of the business. Consulting with real estate agencies is at once an involved and time-consuming task. As most commercial road transport companies don’t have a dedicated property manager, CTFD is in the unique position to handle the process of scouting sites and handling the ins and outs of securing property to specification without involvement of an unnecessary third party. CTFD then works closely through the process of meetings, draft drawings and presentations with the client’s executive team, to demonstrate how the facility, on the proposed block, will function. Headed up by Managing Director David Cameron for the last near 15 years, CTFD Group has completed projects on behalf of Vawdrey Trailers, Bridgestone Australia Truck Centre, PalmTrans Sydney Depot,
Asics Oceania built its new facility on a 56,000 sqm site in Marsden Park.
Visy, Fosters Warehouse and other blue chip businesses. “We effectively hold the steering wheel for companies when it comes to the development of new sites and navigate them through the process,” he says. “A real estate agent can’t offer the expertise we can of working in the industry. We understand the requirements of transport and logistics businesses and this informs the comprehensive solution we offer our clients.” Earlier this year CTFD helped deliver new state-of-the-art facilities for the Asics Oceania Corporate Headquarters and Warehouse facility located within the Sydney Business Park in western Sydney’s Marsden Park. The 56,000 sqm site footprint features a 25,000 sqm warehouse, with a 4,500 sqm corporate office and 1500 sqm retail floor. The twoyear project cost circa $70 million.
David Cameron CTFD Group Managing Director
Twice the size of its previous location in Eastern Creek, the Marsden Park site was chosen by Asics as its new head office and warehouse office to service the Australian market. Office space would need to accommodate a team of 140 staff. The site also had to be large enough to create a warehouse space to service the future growth of the business. Asics were also looking for a site located at a reasonable distance from Eastern Creek so that it could minimise disruption to its teams. Other major factors of note for selecting the property included accessing major roads for the team and distribution; having close proxity to other services like food and shopping; and zoning so they could offer retail without restriction. Future development in the precinct and local area was a crucial part of the criteria according to Mark Brunton Asics Oceania CEO. “The main service we were after was end to end project management,” he says. “We had some experience internally, but we wanted a dedicated resource who understood the requirements around a major project like this.” The solution sought by Asics Oceania, under these parameters according to Mark, meant that they would need someone not just to manage the process but also with an extensive experience they could draw upon to guide the decisionmaking for Asics. This is where David came in. “So many get it wrong with not having the right amount of space or poorly planning the design which fails to factor in operational considerations down the track,” says David. “It’s about getting it right with the client day one and then enacting the due diligence over progressive steps.”
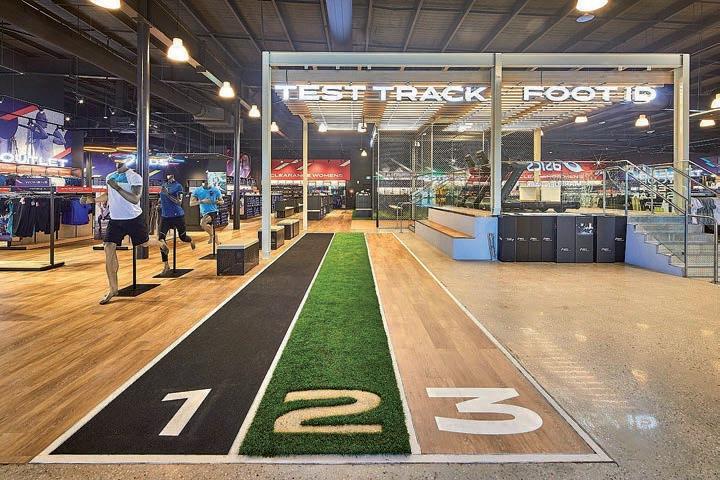
The new Asics facility includes 1500 sqm in retail floor.
The new facility features a 4,500 sqm allocation for corporate offices.
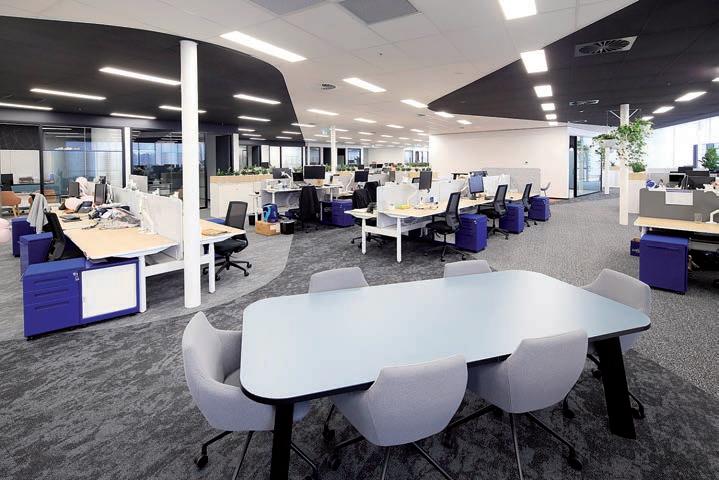
Mark Brunton Asics Oceania CEO
As key requirements can get lost early in the process, it’s crucial CTFD, the client and stakeholders are all on the same page. From the moment CTFD were engaged by Asics as its project manager, the executive team worked closely with Dave on managing the process of finding the right site, the involved design phase, in addition to understanding and adopting input alongside its architects, engineers and builders to ensure Asics received the right facility for its business and national headquarters. Draft designs were approved according to their best operational fit and incorporated a warehouse layout not excluding hardstand and dock requirements. “CTFD organised and managed our tender process and helped us objectively asses our requirements through to being physically on site to ensure we were getting what we paid for and problem solving on the fly with the various parties to ensure things stayed on track and we avoided any rework,” Mark says. That involved both applying knowhow when it was needed and the ability to anticipate challenges so that Asics was able to address these during the natural flow of the project rather than having
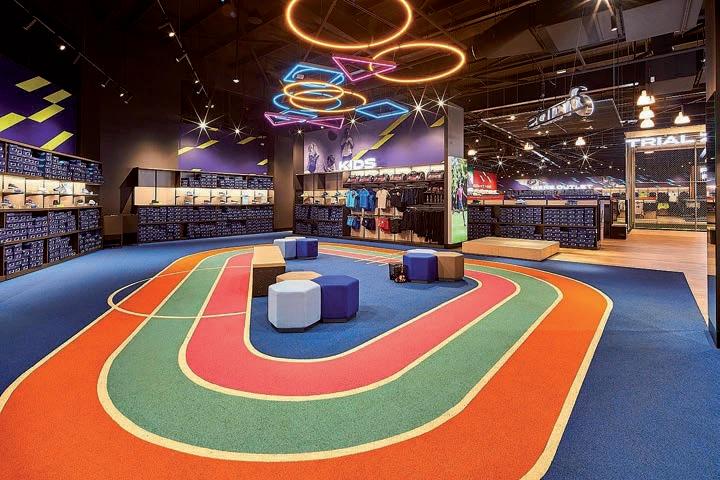
CTFD oversaw the two year project from location scouting to final design. to double back. Avoiding expensive rework is critical. Having David on site continually ensured that everyone’s commitments were being met. “Overseeing the variations with all parties is critical and if not managed carefully can definitely blow out,” Mark says. “Dave’s knowhow helped us avoid unnecessary costs.” Although the warehouse was completed close to the original design, the office space transitioned from the base build layout to a new design when the interior design company was appointed. Some significant changes ensued. To name one, it was now necessary for Asics to create a void at the entrance. With multiple stakeholders involved at this stage in the project, partner management was key says Mark. “To have someone who could manage the project but also have the experience and knowhow to bring practical insights to the table, look ahead in the delivery of the project and anticipate challenges and opportunities which can either avoid costs or create savings is invaluable,” he says. “Dave’s presence on site was also valuable building a rapport with the key people delivering the build through to ensuring we are getting what we were paying for. He took ownership for the delivery of the project like it was his own and integrated himself into the team getting to know stakeholders quickly and engaging throughout.”