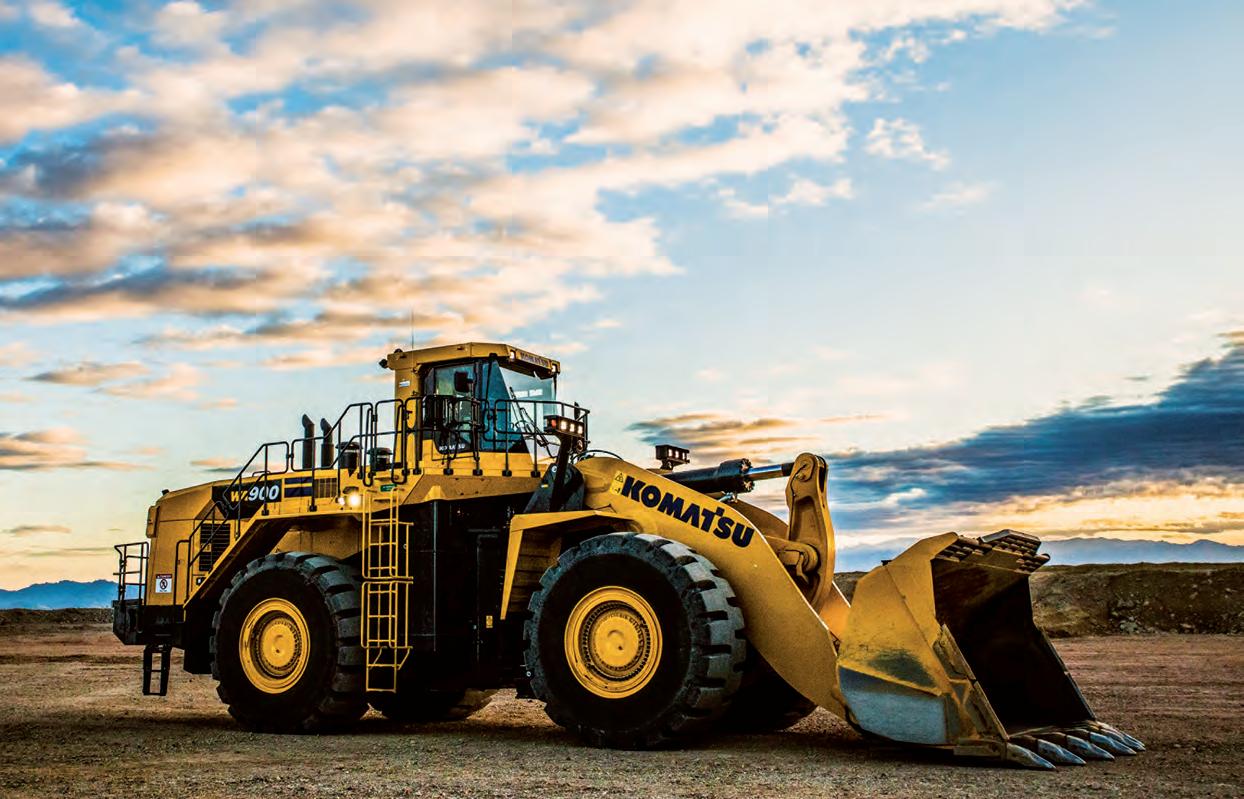
14 minute read
LARGE LOADER PROMISES MORE PRODUCTIVITY
from Quarry October 2021
by Prime Group
LARGE LOADER OFFERS
HIGHER PRODUCTIVITY, LOWER COSTS
Komatsu Mining, the mining division of Komatsu Australia, has released an upgraded version of its 11m3 to 13m3 class mining loader: the WA900-8R. It incorporates innovative technology features that deliver increased productivity and ease of operation, while reducing operating costs.
The WA900-8R loader, the largest that can be operated in a quarry, incorporates Komatsu’s SmartLoader Logic technology to provide the engine with the precise torque for each part of the duty cycle.
Komatsu’s national product manager Mark Summerville said SmartLoader Logic can improve the WA900-8R’s fuel economy by up to 10 per cent compared with the previous WA9003E0, while also increasing productivity. Other productivity improvements include a modulation clutch for controlling speed and torque, along with faster boom raise speeds for faster cycle times.
“These features combined with automatic dig and a semi-automatic approach and dump system means the WA900-8R can improve an average operator’s efficiency,” Summerville said.
The new loader includes a Komvision obstacle detection system that uses radar and 360-degree cameras to alert the operator if a person, vehicle or obstacle is detected. This greatly improves personnel safety in and around the machine.
The WA900-8R, powered by a 671kW Komatsu engine, has an operating weight of 116.4 tonnes. It is matched for loading 90-tonne dump trucks (Komatsu HD785 size) in standard configuration, and up to 140-tonne trucks (Komatsu HD1500) in high-lift spec. PRODUCTIVITY AND ECONOMY FEATURES Komatsu Mining has listed numerous features that can increase the loader’s productivity while reducing operating costs, including: •SmartLoader Logic system for improved fuel economy. •A large capacity torque converter. •A tyre slip control system. •Increased boom speed and breakout force.
SmartLoader Logic optimises the engine torque across all applications to minimise fuel consumption while giving the loader the torque and digging power it needs.
“This system functions automatically and doesn’t interfere with operation, saving fuel without decreasing production,” Summerville said.
The system is matched to the loader’s automatic transmission, with an electronically controlled modulation (ECM) valve that automatically selects the correct gear speed based on travel speed, engine speed, and other travel conditions.
“This ECM system also engages the clutch smoothly to prevent lags and shocks when shifting,” Summerville said.
The WA900-8R’s powertrain has a large capacity torque converter designed to ensure optimum efficiency. “This ensures greater productivity in ‘V-shape’ loading applications because the torque converter’s increased tractive effort means it doesn’t require full throttle,” Summerville said. “It also allows the loader to achieve higher gear ranges and maintain higher travel speeds when working in load and carry applications.”
The loader’s hydraulics are designed around Komatsu’s closed-centre load sensing system (CLSS) technology. “This uses a variable displacement piston pump combined with CLSS to deliver hydraulic flow exactly when the task requires it, preventing wasted hydraulic flow, which contributes to better fuel economy,” Summerville explained.
Another feature is a tyre slip control system. When it senses tyre slip, the control system applies the modulated clutch to control the torque converter and minimise tyre slip. “All these features combine to reduce fuel consumption by up to 10 per cent – while also increasing productivity – compared with the WA900-3E0,” Summerville said.
The WA900-8R features Komatsu’s latest generation cab to improve operator comfort and safety. It includes the addition of a trainer seat, shockless stop cylinders, climate control air conditioning and modulated clutch. These features, combined with ergonomic improvements, all contribute to higher operator productivity, easier and safer operation, and
reduced fatigue. The cab also includes: •A new automatic digging system. •A semi-automatic approach and dump system. •A redesigned large operator cabin seat, incorporating low effort control levers and an advanced joystick steering system. •An electronically controlled suspension system (ECSS).
“Our new automatic digging system actuates the bucket tilt and lifting operations by detecting the sensing pressure applied to the equipment,” said Summerville. “It’s designed to significantly reduce operator fatigue and improve efficiency, ensuring optimum bucket fill every time the machine enters the pile, whether in rock or in loose materials.”
The digging system works in conjunction with the semi-auto approach and dump system.
“This automates boom lift and bucket dumping when approaching a dump truck, particularly in ‘V-shape’ loading operations,” Summerville said. “Combining this with our automatic digging system, loading operations from stockpile to dump truck are made easier, and operator effort and fatigue greatly reduced.”
The operator’s compartment – a large, pillarless ROPS/FOPS cab – features a new air suspension seat that provides enhanced support on rough roads and dampens machine vibrations. “Integrated within the seat is an electronic pilot control lever console and a joystick steering lever,” Summerville said.
With WA900-8R loaders used in load and carry applications, Komatsu has standardised the ECSS to reduce pitching and bouncing on uneven surfaces. “This ensures better travel performance, reduced operator fatigue and less material spillage, while delivering a smooth ride, even at high travel speeds,” Summerville said.
SERVICEABILITY Maintenance and serviceability have been optimised through a high resolution in-cab monitoring system, which works in conjunction with Komatsu’s Komtrax Plus remote system.
Maintenance is also simplified through sideopening engine doors, an accessible engine compartment with dual-side engine bay access ladders, along with a swing-out reverse cooling fan and wide-core radiator (with modular core).
An adjustment-free braking system, along with service brakes mounted in-board from the final drives and brake on the sun gear, ensure increased brake life.
Improved loader linkage and upgraded structures for the front and rear frame provide a longer structure life. The machine is also fitted with nine lanyard anchorage points, providing safer maintenance access in difficult areas.
“With our new WA900-8R loader, Komatsu has developed a best in class loader, while delivering significantly higher productivity and operating efficiency, combined with lower fuel consumption and reduced operating costs,” Summerville said.•
For more information about the WA900-8R and other products, visit komatsu.com.au
Our vision is to connect people, processes and products, advancing innovative solutions from rock to road as OneAstec.
FIXED • TRACK • RECYCLING • WASHING • MODULAR • MATERIALS HANDLING
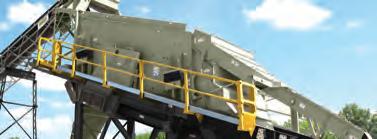
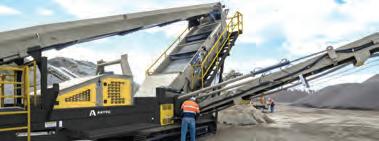

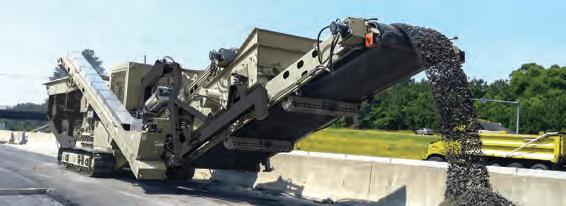
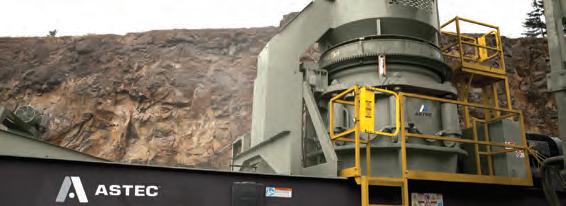
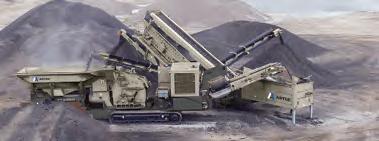
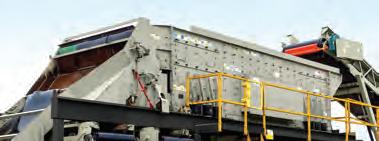
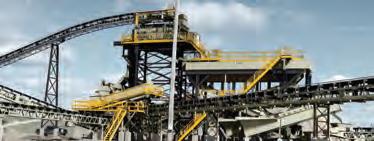
FULL TURNKEY PLANT
LATEST JEWEL IN FAMILY CROWN
A South Australian family business with Victorian quarrying interests has taken delivery of a full turnkey plant – while overcoming a few pandemic curveballs during installation.
GEM Group Holdings is a family-owned business that was commenced by owner/director Ian Sutherland in 1959 and has specialised in earthmoving, civil construction and quarrying projects for 62 years.
The group’s headquarters is in Mount Gambier, South Australia. It has 127 staff, each with a range of specialised skills and abilities. The group covers all aspects of civil construction from the supply of quarry materials such as Telfords Quarry rubble for road making and agricultural lime through to roading sealing and a state of the art asphalt plant. Gambier Stone, another member of the group, provides dimension stone to the building industry, while Martes Quarry supplies agricultural dolomite to the farmers. Gambier Earth Movers also operate the Mount Graham Quarry bluestone site at Mount Burr, SA.
The company also operates Moree Quarries, in Harrow, in central western Victoria, about 150km northeast of Mount Gambier. GEM Group covers a radius of 200km in terms of clients and projects.
In addition to these sites, GEM Group’s managing director and civil project works supervisor Glen Sutherland (son of founder Ian) told Quarry that the combined companies’ overall output is 500,000 tonnes per annum. “We have mobile units that crush in other quarries,” he said. “We have 14 leases in South Australia to our name. Our mobile crushers also do work for local councils as well.”
Sutherland divides his time between working daily at GEM’s HQ in Mount Gambier and working at least one day per week at Moree Quarries, which the GEM Group has operated for 35 years. The site is anticipated to have more than 20 years of reserves of a bluestone/ basalt deposit. Sutherland said the quarry is producing Class A sealing aggregates, asphalt aggregates, concrete aggregates, ballast and Class 1 to 4 crushed rock and scalps. “We also have pre-coated sealing aggregates on-site, which are being used for roadwork and asphalt works,” he added.
The end use of these products can be found in roads, concrete paths, farms, and asphalt and sealing operations throughout regional Victoria and SA.
Moree Quarries has for 25 years operated a crushing plant that included a Jaques single toggle jaw crusher and a Canica model 90 VSI crusher. “That last plant simply couldn’t keep up with demand,” Sutherland said. “It was doing about 80 tonnes per hour (tph).”
Consequently, GEM Group put out a tender for a supplier to provide a new crushing and screening plant for the Moree site. “We wanted a plant that would be capable of producing up to 400 tph and could provide a quality shape and cleanliness in our aggregates,” Sutherland added. “We wanted the plant to be fully automated and QME answered the call.” PLANT INSTALLATION QME – Quarry & Mining Engineering – is involved in the fabrication and installation of full turnkey plant and equipment in mines and quarries throughout Australia. The company, which has been headquartered in Bendigo since its inception in 1980, is aided on all its projects by support services and contractors. It counts Terex Jaques, Sumitomo and Indeco among its network partners.
Ian Rowan, the managing director of QME, told Quarry that GEM Group first approached him in 2019 about establishing a new crushing and screening plant at Moree Quarries. After being briefed by Sutherland about the key requirements of the new plant, Rowan and the QME team recommended a new plant on a hectare-sized footprint that would incorporate Terex Jaques equipment.

The new Moree Quarries full turnkey crushing and screening plant has been operating since May 2021.
Sutherland was entirely comfortable with the recommendation. “Based on our history with Jaques and QME, we went with Jaques. We had some Terex Jaques machinery at Moree and our previous company Mount Schank Metals had Terex Jaques products as well.”
The new Moree Quarries circuit, which has been operating since May 2021, consists of a Terex Simplicity 5124 vibrating pan feeder, a Jaques ST48 jaw crusher, a Cedarapids TSV6203 medium scalper vibrating screen, two Cedarapids MVP450X cone crushers, a Canica 100 rock-on-rock (ROR) vertical shaft impact (VSI) crusher, and three triple-deck Cedarapids TSV8203 vibrating screens.
A Supervisory Control and Data Acquisition (SCADA) operating system manages the plant processes via a programmable logic controller (PLC); the PLC reports data to and communicates with the SCADA system. The plant operation and status is communicated to the plant operator via a 660mm touchscreen Human-Machine Interface (HMI) monitor (SCADA or Panelview system) in a deskmounted console.
FIXED CIRCUIT All the machines were statically mounted and designed to operate in a fixed system. Rowan and John Flynn, the Australian and New Zealand business manager for Terex Jaques, stated there was customisation to allow for the processing of different materials.
“All crushers have some configuration options,” Flynn told Quarry. “There has been no unique customisation but the machines are configured to best operate as a complete system per Moree Quarries’ requirements.”
Flynn said the 1295mm x 13m long Simplicity 5124 features a full length pan suitable for accepting a large primary feed. It is equipped with an oscillating twin-shaft drive arrangement that moves material efficiently and effectively.
As part of the new Moree Quarries circuit, the Simplicity 5124 feeds material to the Jaques ST48 single toggle jaw crusher which is renowned for its large gape feed opening (1067mm x 1219mm) and hydraulic closed side setting (CSS) adjustment. The primary feed from the ST48 is then transferred to the double-deck Cedarapids TSV6203 which, Flynn said, “is installed at a five-degree angle to best handle coarse jaw crusher product and resisting pegging in the large scalping apertures of the top deck”. The variable slope capability of these screens allows installation from a zero- to 10-degree angle to best suit the application. The TSV6203 is the latest generation El-Jay horizontal screen which can handle a broad range of applications.
The Cedarapids MVP450X cone crushers are the next links in Moree Quarries’ crushing and screening chain. They each feature a roller bearing design, a 10mm to 51mm CSS setting, a 300kW motor and a hydropneumatic tramp iron relief system. They can process sand and gravel, shot rock and recycled materials, with a throughput of up to 500 tph.
The secondary feed from the MVP450X is then passed to the 220kW Canica 100 VSI crusher, which has a maximum feed size of 125mm and a throughput of 400 tph. “The configuration of the Canica VSI can be set up with primary aim to crush, shape product or a combination of both,” Flynn said. “The Canica Model 100 ROR at GEM Moree has a rotor and rock box configuration. Its primary aim is to shape material already reduced by the cone crushers to a cubical final product.”
Feed from the Canica VSI is passed to the three Cedarapids TSV8203 triple-deck horizontal screens. Flynn said the TSV8203 is built for durability and its patented lubrication system, coupled with high tolerance machined components, enables efficiency and a long bearing life in the final screening duties at Moree Quarries. “A high G-force operation ensures that required specifications can be met through highly efficient screening.”
PANDEMIC DELAYS Due to COVID-19 lockdowns and border closures in the past 20 months, Glen Sutherland has secured a border permit to cross from SA to Victoria and back regularly. The border closures had some impact on operations at Moree Quarries.
“From start to finish, installation was just over 12 months,” Sutherland said. “There was a delay because we couldn’t get across the [SA/ Victorian] border to do the earthworks. QME had the plant completed within the time that was promised. However, once the borders opened up and we completed the earthworks, the plant was delivered and installed. Throughout the process, there were phone calls between myself, Ian and Sue [QME’s project manager] but overall it ran smoothly.”
Sutherland’s impressions of the new plant over the past five months of operations are
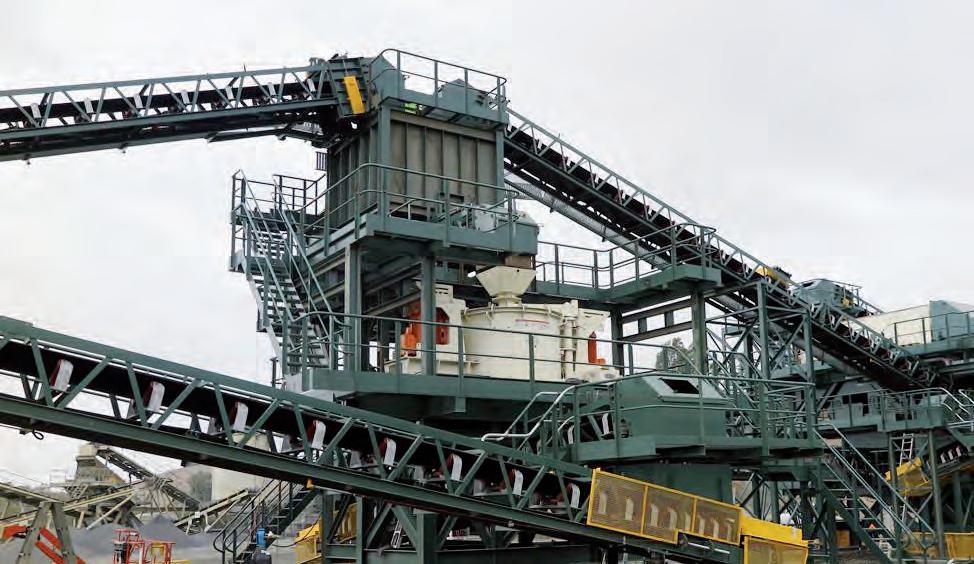
The Cedarapids MVP450X cone crusher (centre) features a roller bearing design, a 10mm to 51mm CSS setting, a 300kW motor and a hydropneumatic tramp iron relief system.
The Terex Cedarapids TSV6203 is the latest generation El-Jay horizontal screen which can handle a broad range of applications.
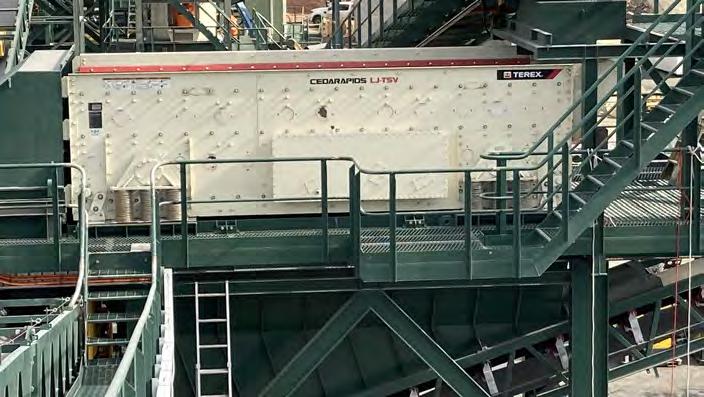

An aerial view of the new Moree Quarries circuit, which was a collaboration between GEM Group Holdings, QME and Terex Jaques.
positive. “From the time the first rock went through the plant, we’ve been impressed with the output and the cleanliness of the aggregates,” he said, “particularly as there has been a lot of rain in the past few months and conditions have been a bit dirtier than normal. The cleanliness of the rock coming out of the plant has been really impressive.”
Ian Rowan, of QME, agreed that the new plant has shown potential but has not had the opportunity to perform to its absolute best because it has “not had the consistent quality feed and the raw material has been very wet”. He was optimistic that as the spring season commenced and with drier rock conditions, the plant’s capabilities “would come to the fore”.
Nonetheless, Sutherland said he and the GEM Group are pleased with the new plant’s early results and praised QME and Terex Jaques for their work. “From the first initial catch-up in January 2019 through to commissioning, QME has been fantastic,” he said.
“Day or night, Ian and Sue from QME have been available and had our best interests at the forefront. QME have handled the whole turnkey operation at a high level. The commissioning and handover between QME and Terex Jaques was smooth and I recommend both companies to anyone who is in the market for an upgrade to an existing plant or for a full turnkey plant.”
Sutherland anticipates that QME and Jaques will have a hand in the aftermarket support of the plant. “I’ll definitely talk to Ian quite closely about that, and we’ll talk to Terex Jaques as well. Communication is the key and we’ll work it out between all three parties.” •
To view the specs for Terex Jaques plant, visit terex.com/mps/en-au For more information about GEM Group Holdings, visit gem-group.com.au To learn more about Quarry & Mining Engineering, visit qmebendigo.com
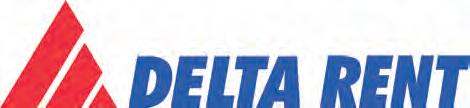
CONTACT US TODAY ON 1300 793 071
DELTA RENT IS THE HEAVY PLANT RENTAL DIVISION OF DELTA GROUP - ONE OF THE LARGEST DIVERSIFIED CONTRACTORS IN THE WORLD TODAY.
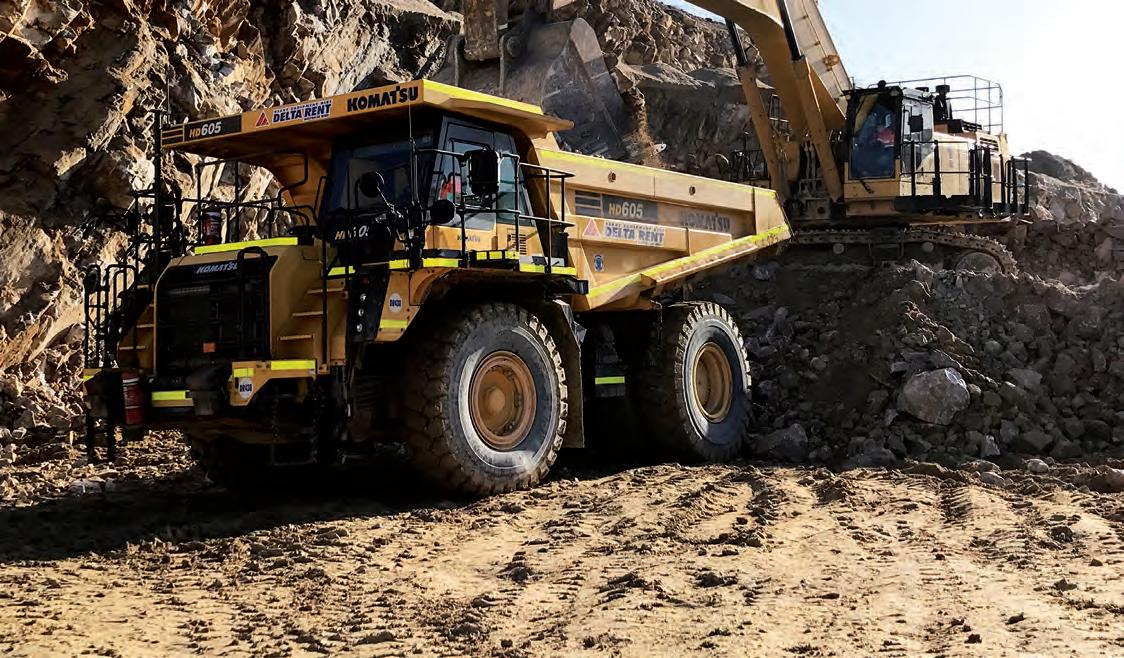
We have the financial, operational and organisational capacity to manage hundreds of projects at any one time - Australia wide. With one of the largest and youngest heavy rental fleets in Australia, our fleet is meticulously maintained and regularly upgraded to ensure we capitalise on late model machinery and the efficiencies they bring to a client’s project or site specific requirements. Delta Rent have equipment available for hire under flexible short, medium and long term rental plans, let Delta Rent provide your next solution to your quarry requirements.