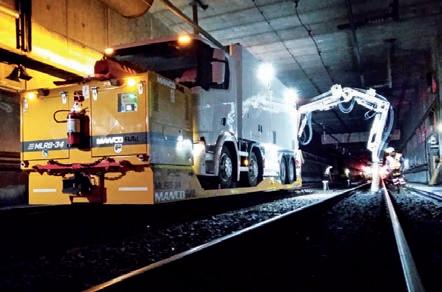
2 minute read
Mechatronics in the Manco mindset
by Prime Group
Operations and Maintenance
The mechatronics revolution transforming rail equipment sector
Mechatronics, the interface of mechanical and electrical engineering with advanced computer technology, now plays a vital part in today’s rail construction, electrification, and maintenance programs.
Even as short as 10 years ago, the industry never envisaged a rail construction consisting of around 300 tonnes being fully controlled via a multi-channel remote handpiece that incorporates not only finite movements of multiple functions, but also a host of failsafe safety features.
Perhaps the mechatronic evolution was really advanced and was acknowledged when the control of today’s truck-mounted cranes moved completely into the radio remote control era.
Time endowed “hard to please” railmen, brought up with the likes of manual lever controls, safety chains, and wind-up and downrail modules are now conceding that without robust mechatronic systems, today’s rail efficiencies would be significantly hampered.
Manco Rail, a major rail equipment supplier over the past 40 years, has taken a leading role in embracing this revolution, starting from a team of talented young design engineers from a wide array of backgrounds, who frequently engage in demanding brainstorming sessions.
As Manco Rail managing director Bryan Black says, apart from the high level of productivity gains, the safety features are insurmountable, and have enabled the industry to provide a higher degree of worker safety, with the clear downstream benefits.
In Manco Rail’s particular case, examples of this evolution include: • Multiple self-drive and towed 50 tonne GVM trailers, locked in a consist of around 300 tonnes, with power units “talking to each other” as grades and track speed demands constantly change. Such a concept has been used in the Sydney Metro Line Wide, twin 15k rail tunnels. • Automated fold-down handrails and folddown and -up access steps on Sydney Trains’ new Elevated Work Platforms, which enable the slewing function to be achieved at the lowest possible height when working under live wire conditions. • Special low height 30 tonne capacity rail transporters, enabling large truck-mounted
vacuum excavators to gain access to tunnel environments, with the rail transporter direction and speed being controlled from either the operator or in the carried vehicle or any location within 100 metres of the operating unit. • Complex wire tensioning units, interfacing advanced PLC designs, that ensure the desired tension, track speed and drum feed speeds are fully interfaced while simultaneously feeding both cantenary and contact wire. • The constant and ongoing developments in providing automatic warning and shut down exclusion zones. • Rail trailer-mounted radio-controlled multipurpose straddles that can transit trailer to trailer with significant loads up to six tonnes.
“These are just a few examples of the incredible advancements the hydraulic, electrical, robotic, and mechanical component suppliers now interface to provide such manufacturers as Manco Rail with suitable and highly reliable integrated systems,” Black said.
“Where to next? Well, we are all familiar with automated driverless passenger transit units, so perhaps there will be an age where robots execute complex maintenance work, in high-risk environments controlled from a central control room.”
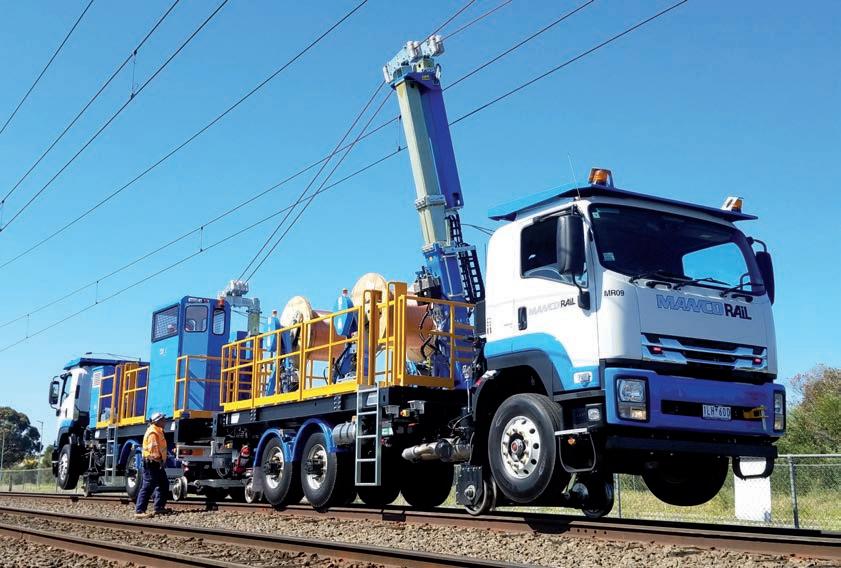
Manco Rail’s complex wire tensioning units and advanced PLC designs ensure the desired tension, track speed and drum feed speeds are fully interfaced while simultaneously feeding cantenary and contact wire.
A Manco truck-mounted vacuum excavator.