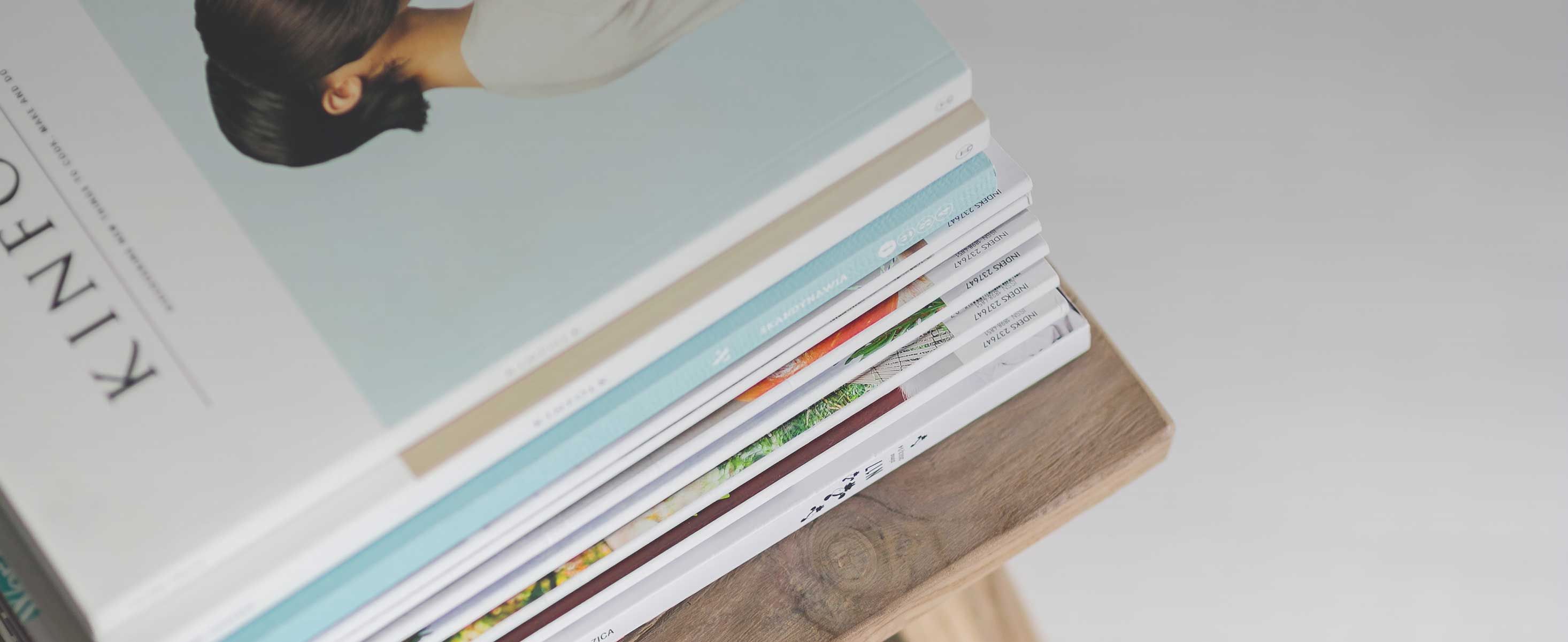
4 minute read
Manco delivers a new thread for rail automation
from REX Sep 2019
by Prime Group
A new thread in rail automation
New Zealand-based Manco Rail is delivering a better bet for rail threading and sleeper laying with a new design that combines the best of both worlds.
AUTOMATION TECHNOLOGIES have been used for rail sleeper and track laying projects in the past, but the systems are often disparate. Project coordinators may have to source tugs, excavators, and machines for laying sleepers and track from several different equipment manufacturers.
New Zealand-based OEM Manco Rail spent more than a year designing an inclusive, automated system that incorporated all these elements into a single piece of equipment supported by electricpowered tugs with the potential to expedite rail and sleeper-laying operations considerably.
Manco managing director Bryan Black said that during the company’s research it found that manufacturers in Europe were using individual items to accomplish these tasks in an automated fashion, but none were combining them to the degree that the entire process could be accomplished in one go. It would prove a hugely ambitious undertaking for the company.
“Nobody has done this before – we’re combining sleeper laying and rail threading and it’s all automated,” Black told Rail Express.
“We had six engineers working on it for the best part of 14 months. It took thousands of hours of work. It lays the rail, spreads it out, places the sleepers, then pull the rail back over the top.”
The automated rail threading and sleeper laying device works through the complex integration of several systems into a single format.
The first stage of the process is rail transport and distribution. The design is led by a 23-tonne rail-wheeled excavator at the nose of the device that drags, several 110-metre rail sections using a motorised rail thimble and clamp with a hydraulic rotator.
An excavator with a rail grab function is also placed at the rear of the consist to help hold it in place during stoppage.
The front excavator tows the consist forward until its end lines up with the last section of off-loaded rail, at which point the rear excavator grabs the innermost sets of rail from the dolly while the front excavator pulls the consist forward.
The front excavator stops pulling before the rail completely slides off the dolly so that the rear excavator can move forward to prise the other end of the rail into a straightened position. Once all the rail has been laid, the rear excavator can connect to the rearmost dolly and be towed back to the dive for reloading.
This is followed by sleeper transport, distribution and placement. Sleepers are pre-stacked on a specially designed intermodal sleeper transport container comprised of up to four
40-tonne, 14.7-metre bogies carrying up to 420 sleepers (210 sleepers on each of the
two rear trailers).
“The towing and delivery methodology are based on the two rear trailers being
unloaded first so that they can return to the dive for further loading,” Black says.
“Once loaded these two trailers, being assisted by a powered tug will return and re
join the sleeper laying consist.”
The sleepers are grabbed from overhead by a specially designed straddle crane and
sleeper transfer gantry, which can grab seven sleepers at one time and slide down to the
front of the consist to gently place them into position. The front of the sleeper trailer
consist includes a sleeper truss lead trailer to accommodate the placement of seven
sleepers concurrently on the tunnel invert.
Black explained that this was an important consideration of the design as Manco
wanted to avoid the pitfalls of conveyor-based sleeper layers, which are prone to
dropping the sleepers with greater force.
“The problem with conveyor laying systems is that it tends to drop the sleeper on
the ballast and the ballast acts as a cushion. If you drop a sleeper under that principle,
it sort of drops it then pulls it into line,” he explains. “If you drop it like that you can
damage the sleeper.”
Positioned beneath the lead truss trailer and secondary rail threading trailer are a
set of hydraulically operated rail threaders with thimbles underneath that can allow
threading to take place simultaneously to sleeper laying as the dollies move forward.
These rail threaders help to compress the rail gauge distance to 1435 millimetres,
but they have hydraulically adjustable gauge widths that help to hold the rail at the
correct height off the sleepers.
Propulsion of the system is handled by a rail-wheeled excavator on the tunnel invert
in combination with the electric power of the tugs, and, like the rail placement consist,
the sleeper distribution system can also be towed back to the dive for sleeper reloading.
“We were looking to make an automation system where we could ‘pick and place’ –
pick the rail up and spread it out using a spreader beam,” Black says. “We worked in
conjunction with an English company who had done those before using an excavator
but not on a straddle.” Overall, Manco Rail has big plans for its new system, offering a
truly holistic system that combines multiple ‘threads’ into a single, cohesive unit. 654321 7 8 9 10
A
B
C
D
E 11
F
G
ABOVE: The device works through the complex