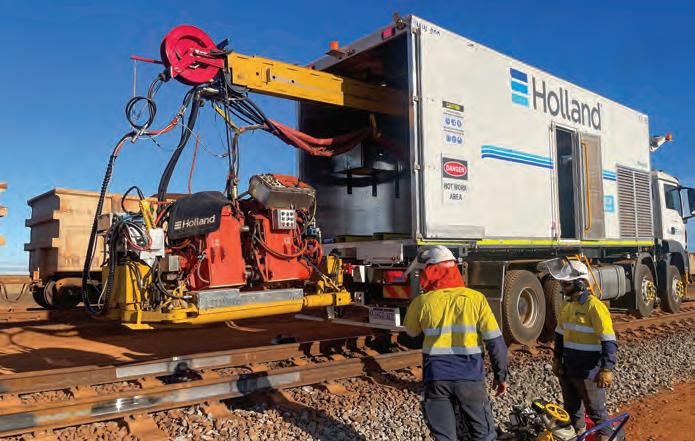
6 minute read
Holland’s innovative welding solutions
Plant, Machinery and Equipment
Innovative welding solutions
Holland has a rich history in innovative welding equipment. This is best demonstrated in its industry-leading Intelliweld control system recently introduced in Australia.
When Holland entered the Australian market in early 2020, its goal was to bring the newest and highest quality welding equipment together with expert operators to serve Australia’s heavy haul and transit rail sectors. Its service offering is unique precisely because of that pairing.
As the engineer and manufacturer of the equipment it operates, Holland’s history is one of innovating based on real experience in the field. From the first self-propelled railcar with a portable electric flashbutt welding machine in 1972, the company has been improving its equipment based on the needs of its operators and customer partners on-track.
“Holland has a long history of identifying problem areas and making our own custom solutions,” Shane Mayhill, Holland’s general manager of welding technology, said. “From the beginning when Holland entered the flashbutt welding industry using acquired technology and equipment we have taken on problems and found solutions.”
Although Holland is best known for its MobileWelders in the field, the company has also managed, operated and maintained several large, fixed welding plants over the last 50 years.
“Going back to the late 1980s and early 1990s, one of our key welding subject matter experts, Kenny Lankford, took over the fixed plant welder automation. It wasn’t just the welding itself, but he set his sights on improving the automation of the process,”
Specialised flashbutt welding crew making in-track welds in the Pilbara. Mayhill said. This identification of an opportunity and subsequent improvements made by those using the existing equipment allowed Holland to improve weld production by approximately 20 to 25 per cent in its fixed plants.
“Holland has used at least five different welding control systems on our mobile welding equipment over the years, with varying degrees of success,” noted Mayhill. “Around 2014 we were using a control system supplied by a third party. We were fine with some aspects of the system, but there were some areas that were lacking the data input and output that we wanted to improve our weld quality and production. When the supplier discontinued the system and tried to move us into using a new system that still had some of those same weak areas, Holland decided it was time to take the welding control 100 per cent in-house.”
A UNIQUE PROPOSITION
This began the development of what is now known as Holland’s industry-leading Intelliweld control system. Mayhill added: “A team with over 150 years’ cumulative welding experience was formed and the organisation dedicated capital to spec out hardware and software that would work for what we wanted out of a bespoke one-of-a-kind weld control system.”
Holland took what was learned in more than 40 years of welding and brought that into a specifically designed control system for flashbutt welding rail.
“This system took into account all the problems that we had with our past control systems as well as those things that we believed would improve the system. The times our operators were in the field and thought, ‘If only we had this or could do that’, were built into the system,” Mayhill said.
“After almost a year of development and testing Holland introduced its current Intelliweld system into new mobile welding units being built. And with a small amount of development we were also able to modify the Intelliweld system to develop a retrofit kit that could be installed on existing welderheads in the field by a field technician in one day.”
By the end of 2017, Holland had updated its entire fleet to a single, proprietary control system. Having a single control system in a fleet of more than 200 units improved efficiencies in training, unit repair times, and access to needed spare parts.
Recently arrived in Australia, the Intelliweld system provides real-time weld monitoring and automated data connection, along with low consumption weld capability. Being used in the contracting fleet means Intelliweld continues to be improved based on feedback from Holland’s operators as well.
These improvements include things as simple as debugging issues, all the way to underlying welding principles that can affect or improve weld quality. Bringing it all together in Australia and like North America, flashbutt welding is a contracted service. Holland says its key differentiator is on the technical side with its machine and control system intelligence. It involves science, engineering and data collection.
“We really take it to the next level in differentiation from other contractors. We are able to close the loop in-house because of our Intelliweld control system. We collect data from our machines as they’re welding, and we can perform predictive analytics with that data.
“Although we are a contractor and have expert operators that perform the welding service, we surround them with a lot of technical expertise making us a railroad service provider first, followed closely as a technology and data analytics business. We are very unique because there are not many businesses in our market that can do what we do.”
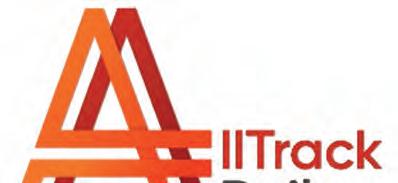
WE SELL AND SOURCE RAILWAY PLANT, EQUIPMENT AND PARTS. OUR GLOBAL NETWORK PROVIDES INVALUABLE INDUSTRY MARKET KNOWLEDGE AND UNDERSTANDING.
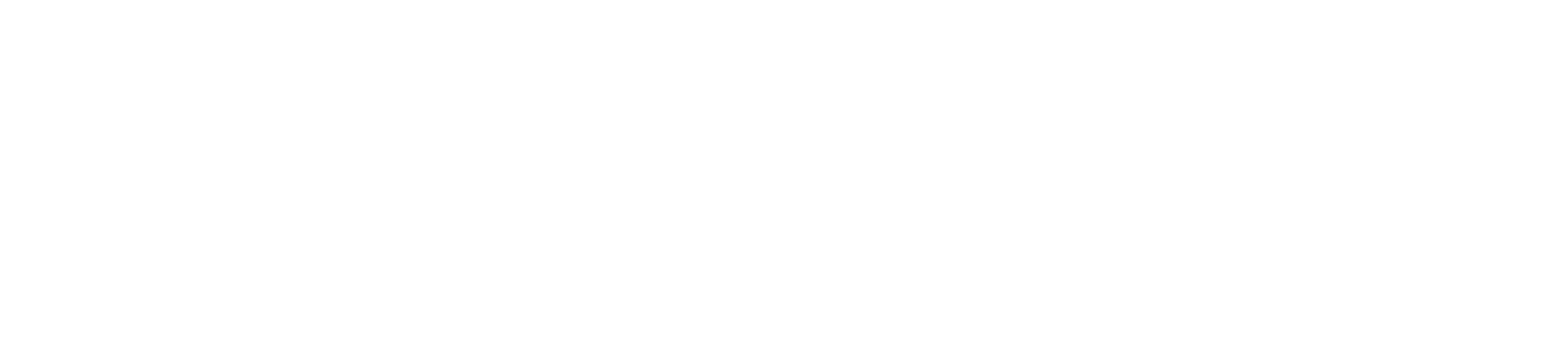
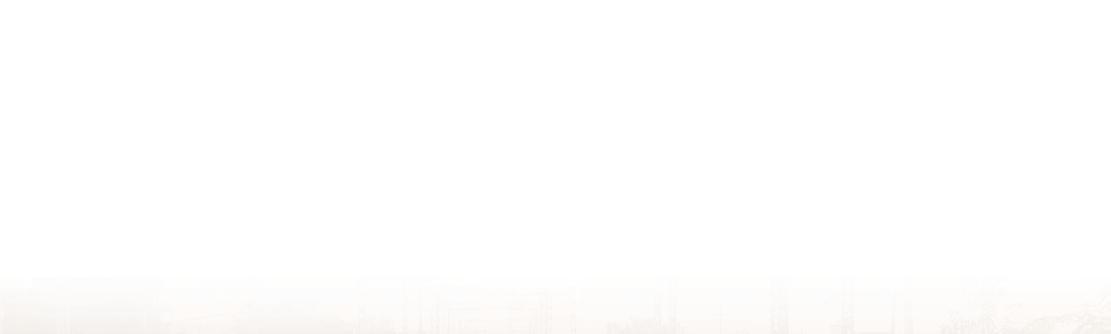
Alltrack Rail is a leading Australian purveyor (seller and dealer) of railway locomotives, rolling stock and associated rail maintenance parts and plant. We also source new and used railway perway materials such as rails, sleepers, turnout components and fastenings.
Our business is based in the Hunter Valley NSW, where it is owned and managed by rail industry veteran, Bob Taylor. With over 45 years’ experience in the rail sector, we boast an impressive list of clients and contacts in each of the continents across the globe which include major maintenance providers, rail track operators, major construction fi rms and contracting businesses.
With our network of contacts we can also fi nd a home for quality used equipment when the times comes to move your equipment along.
Our background is underpinned by our reputation for spotting opportunities and ensuring the best possible outcomes for our customers. Whether it concerns the sale or sourcing of new or used plant and equipment, Alltrack Rail can assist.
+61 487 811 007 | ADMIN@ALLTRACKRAIL.COM.AU | WWW.ALLTRACKRAIL.COM.AU
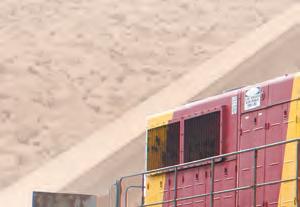
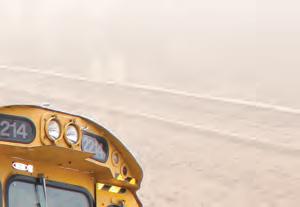
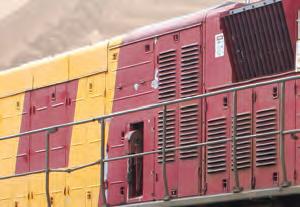

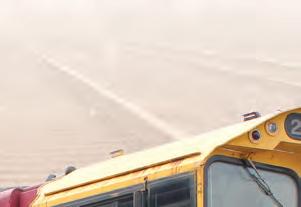
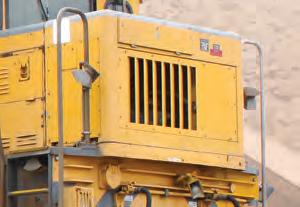
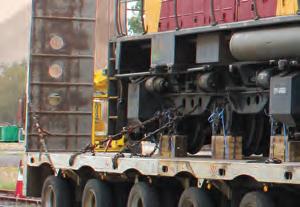
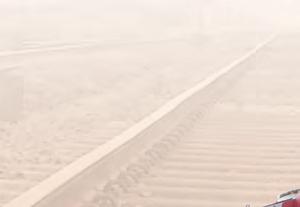
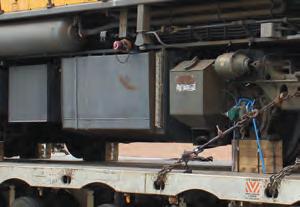
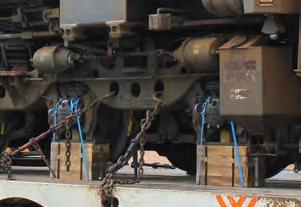
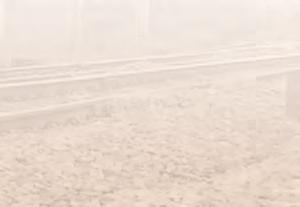
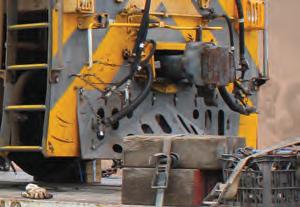
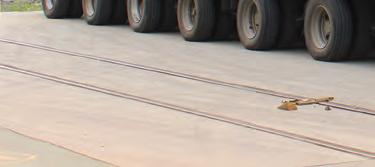
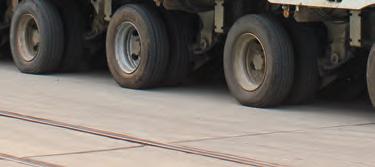
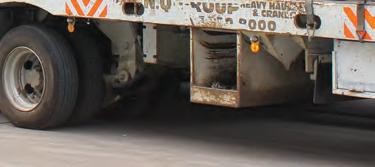
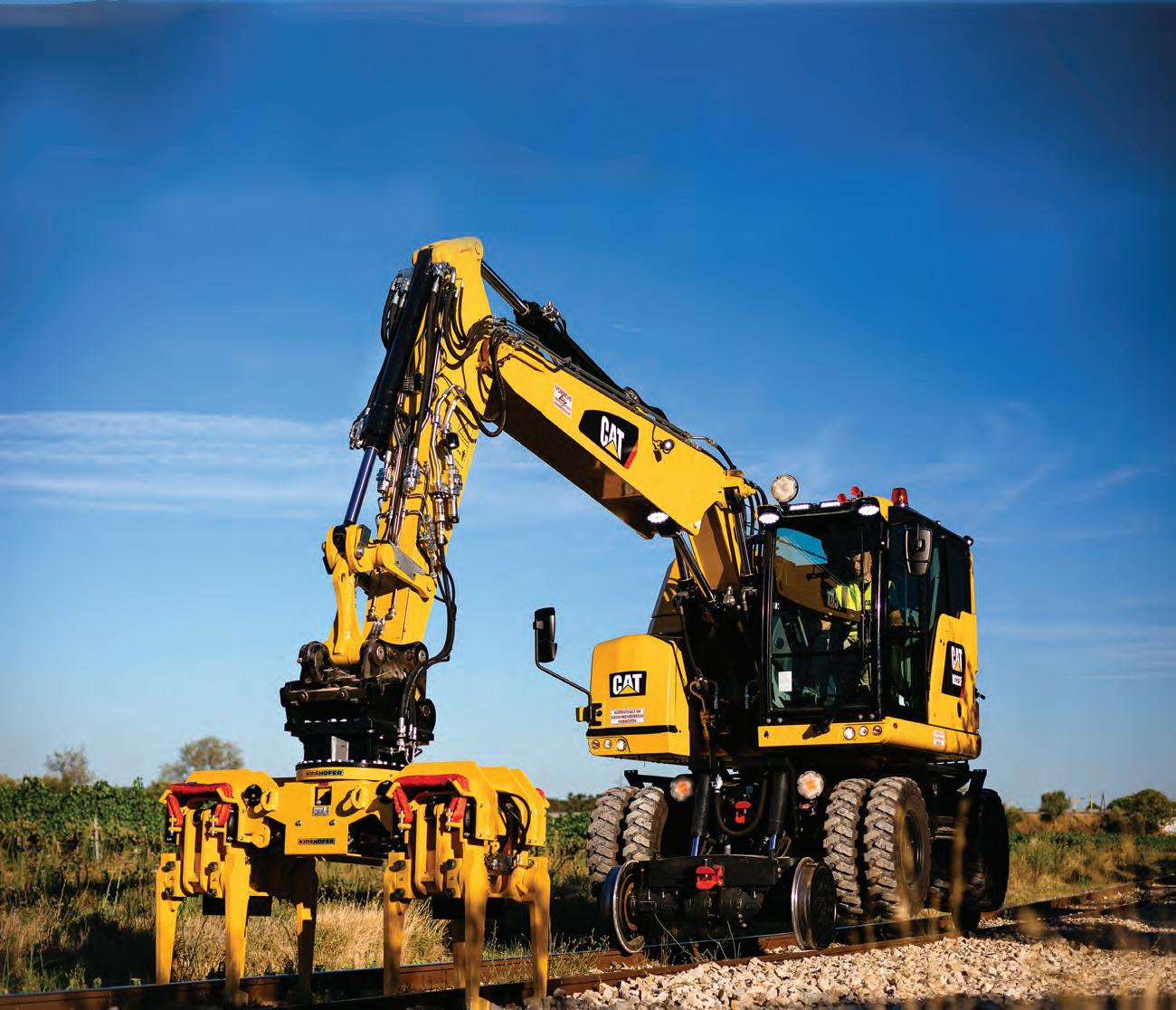
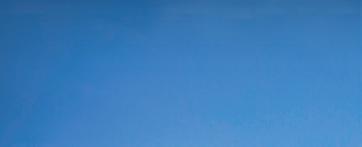
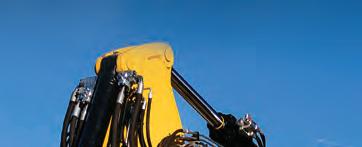
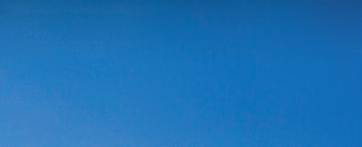
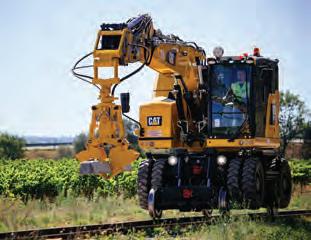
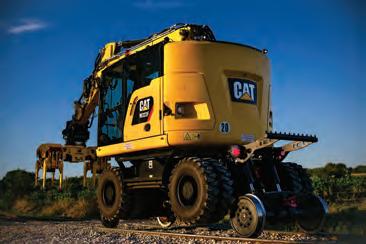
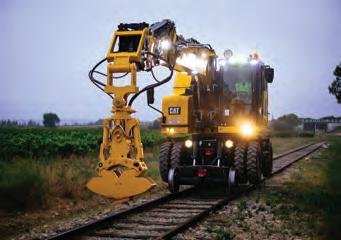
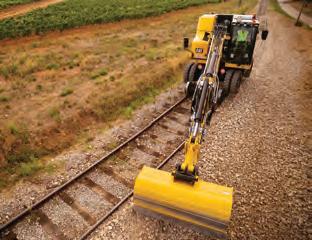