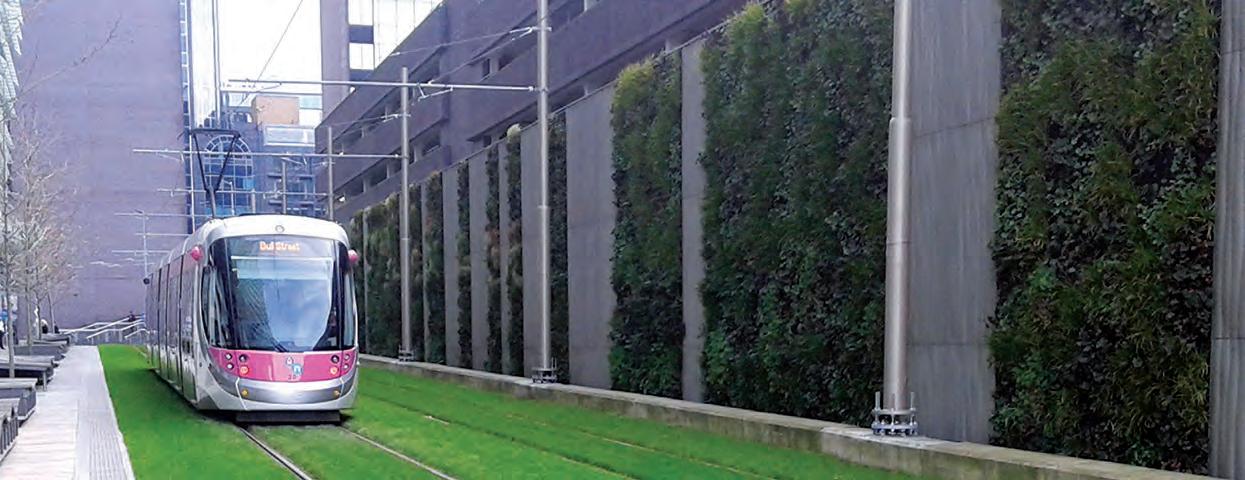
4 minute read
Strailastic tracks pass temperature test
Light Rail Solutions
The vulcanised rubber material used on this green track in Birmingham, UK, provides protection from temperature extremes.
Tough tracks pass temperature test
Track specialist STRAILastic is using vulcanised rubber to ensure light rail tracks are not severely affected by temperature conditions.
Temperature variations often place stresses on infrastructure, particularly if it’s in exposed environments. In many cases this includes tram and light rail tracks.
Whether set in asphalt, concrete, or earth as in the form of a “green track”, light rail tracks face stresses from rapid temperature change as the surrounding materials expand and contract.
Unlike heavy rail structures, where the ballast foundations allow for some contraction and expansion, the nature of light rail, being embedded in a surface, means thresholds are much lower.
The good news is that polymer sleeper specialist STRAILastic has developed a chamberfilling solution that helps mitigate the problem.
Australia operations director Andreas Göschl said the system is used in areas where there are big temperature variations.
Produced in a similar way to STRAILastic’s level crossing systems, the chamber filler avoids the use of bitumen joints by being level with the railhead. The fillers are designed to withstand the wear and tear of traffic crossing the rail line.
While chamber-filling elements are common to many light rail networks, not all are created equal. A common material not used by STRAILastic is polyurethane.
“The polyurethane products are more like plastic, so they expand when it’s warm and they shrink when it’s cold,” Göschl said.
“The systems that STRAILastic offers are instead made from vulcanised rubber.
“We don’t have this issue of expanding and contracting with our systems, as we have a temperature range between -40°C and plus 90°C.
“Because of our temperature stability, our system has a glass transition point – the point under deep temperature when a system breaks – of -55°C. Common systems have a glass transition point of -27 to -30°C. While this temperature is only reached in very cold countries, that shows how the system can move and how stable it is.”
While these temperature ranges are extreme, the stability of the STRAILastic system at such a wide range of temperatures means that for normal operating conditions, the product offers a more reliable solution.
The benefits of the vulcanised rubber solution extend beyond its rigidity. While made from 95 per cent recycled rubber, the outer cover of virgin rubber ensures that the systems can withstand the elements.
“Vulcanisation has several benefits as it is more UV and ozone- resistant. As we use a virgin rubber cover sheet, we have a higher density than polyurethane-bounded systems,” Göschl said.
The design of the system also means that the chamber-filling element fits to the rail like a hand into a glove.
“We do not need any glue or adhesive – the system is self-clamping – due to the seat profile of our systems,” Göschl said.
Not only does this promote the longevity of the track structure due to less wear and tear, but the intrusion of foreign particles is reduced.
“Due to our very small tolerances and very small movements in the track, we avoid gaps between the rail and the chamber filler. A gap is the worst thing that you can get in a light rail track, as it’s through these gaps that water, sand, sediment and dirt come in,” Göschl said.
“Over time the rail is then lifted up a little bit and when you have a lot of moisture inside there you also get electric problems, and these combine to corrode and destroy the rail web which is the weakest point of the rail.”
DESIGNED FOR CITY NEEDS
STRAILastic has introduced a unique naming system for each of its products in the track damping range.
“Our systems are called Type Berlin, Bremen, Bielefeld, Zurich, and so on. All light rail authorities in various countries have a special way of track building or track construction, so what we do is we create tailor-made solutions for them,” Göschl said.
Once complete, these solutions are then standardised so that future networks that are similar can use a standard product. Installed over 30 times in cities around Europe, the system has often been put to the test over the past 20 years in comparison with polyurethanebonded products.
After only a year, the difference can be seen clearly, with gaps visible to the naked eye in the alternative products. In contrast, in cities where the STRAILastic product has been installed, the solution is continuing to measure up after 10 years.
To ensure that authorities gain the maximum value for the products, in each new city where the STRAILastic system is installed, a member of the team will oversee the installation.
“For all first installations in all cities and areas we send at least one engineer to help and guide the installation,” Göschl said. “We’ve done that also in Australia, for our noise-attenuation products. From next year on we will have people in Australia who are trained for the track damping products.”
The design has also been optimised to reduce any variation during installation, while retaining the ability to be modified on site with regular tools. The lack of glue or adhesive means that removing or replacing the chamber filler is simple, reducing maintenance complexity.
Together, the product provides a reliable and sustainable solution to keeping trams running, no matter the weather.