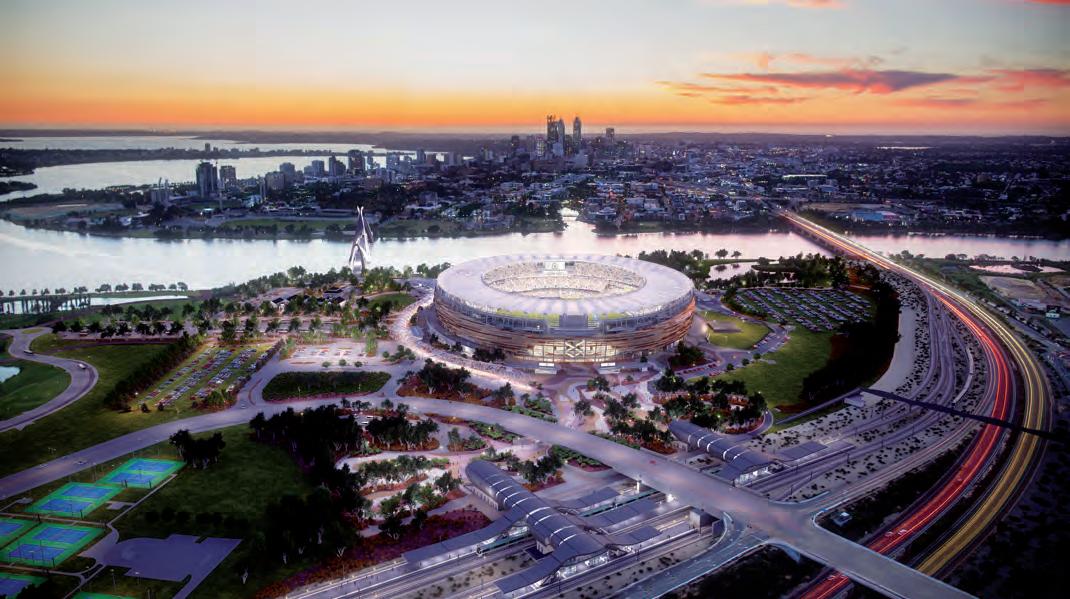
7 minute read
The latest news from National Precast Concrete Association Australia
PRECAST’S ROLE IN AWARD-WINNING INFRASTRUCTURE
NATIONAL PRECAST PROVIDES AN OVERVIEW OF HOW PRECAST IS CONTRIBUTING TO AUSTRALIA’S INFRASTRUCTURE SUCCESS AND THE AWARD-WINNING PROJECTS LEADING THE WAY.
With Australian cities making a substantial commitment to statement infrastructure, interest in the nation’s civic structures is dramatically increasing. Infrastructure becomes iconic by striking a permanent pose and Australian precast concrete is doing just that with award-winning projects on national and worldwide scales. 2018 was an impressive year for National Precast’s members, with a range of member projects making headlines for their feats. From the Australian Institute of Architect’s Architecture Awards to internationally renowned The Stadium Business Awards in London, Australian precast concrete is stepping into the spotlight and stealing the show.
OPTUS STADIUM
In one of many accolades for this remarkable project, Optus Stadium was recognised as a world-class venue at The Stadium Business Awards in London, winning the Project of the Year award for 2018. The project also earned the highest honour at the Australian Institute of Architects’ 2018 WA Architecture Awards, winning the prestigious George Temple Poole Award. The stadium also received three named awards at the event: the Jeffrey Howlett Award for Public Architecture, the Wallace Greenham Award for Sustainable Architecture and the Mondoluce Lighting Award and the Colorbond Award for Steel Architecture.
Designed by Hassell, Cox and HKS, the stadium’s architectural wall façade features 4000 square metres of precast panels manufactured by Western Australia-based precaster Delta Corporation. Some panels have a smooth surface, some have exposed aggregate and some have images etched into selected segments and sandblasted at varied depths. Integral colouring using pigments produced earthy tones and a saw tooth profile was achieved using custom moulds.
Indigenous artwork was etched into the surface of the precast panels with graphic concrete. Delta worked in collaboration with National Precast Industry Partner and graphic concrete specialist, ramsetreid, to manufacture a surface relief that showcases the Nyoongar Aboriginal language and stories.
At the centre of the sporting action are
Optus Stadium’s wall facade features 4000 square metres of precast panels.
Stage 2 of the Bendigo Hospital project included construction of a multi-level car park and conference centre, both using precast elements.
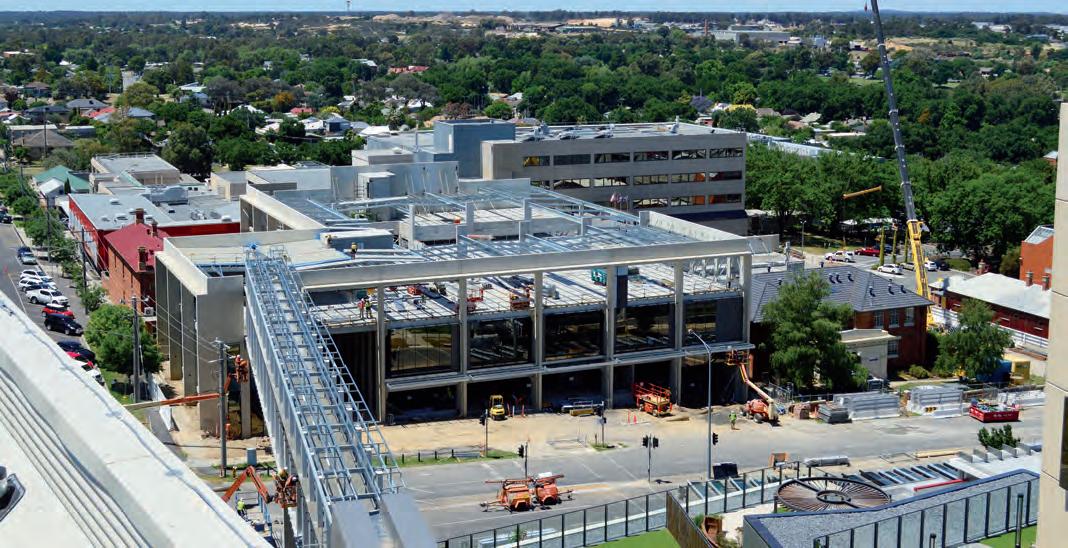
more than 3500 units of prestressed precast seating plats manufactured by Delta and fellow Western Australia-based member, PERMAcast. All structural elements were manufactured to an immaculate Class 2 off-form finish.
BENDIGO HOSPITAL
At $630 million, Bendigo Hospital is Victoria’s largest regional hospital. Designed by Bates Smart and Silver Thomas Hanley, the hospital fuses Bendigo’s natural environment and vernacular architecture with a holistic approach to healthcare. It is morphologically divided into sections, including healthcare facilities, retail facilities, a childcare centre and a hotel.
Bendigo Hospital won the Sir Zelman Cowen Award for Public Architecture at the Australian Institute of Architects’ 2018 National Architecture Awards. Stage 2 of the project included the construction of a multi-level car park and a conference centre, which comprise precast floor planks, beams, columns, stairs and wall panels manufactured by Melbourne-based National Precast member Hollow Core Concrete.
Speed of construction, high quality architectural finishes, a long span design and a Class-2-to-3 fire rating were among the design requirements. Hollowcore floor planks achieved the long spans, while solid floor planks were suitable for the complex geometry. Coloured concrete with a specially designed concrete mix was used for the wall panels and two types of surface finishes were applied to the face of the wall panels. Some have an acid washed surface finish, while others have been sandblasted.
CADOGAN SONG SCHOOL
Designed by Palassis Architects, the Cadogan Song School at St George’s Cathedral in Perth was celebrated for its outstanding contribution to the quality of concrete in Australia at the Concrete Institute of Australia’s 2017 Awards for Excellence. The project won the prestigious Kevin Kavanagh Trophy – the highest honour awarded to a concrete project. It was also awarded the 2017 WA
Precast floors, plans, beams, columns, stairs and wall panels were manufactured for the Bendigo project.
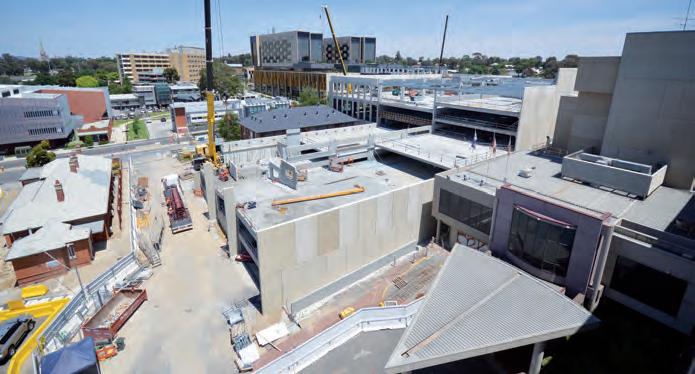
State Award of Excellence in the category of Commercial Buildings.
The Cadogan Song School continued to soar in 2018. The project was awarded the National Award for Heritage at the Institute of Architects’ National Architecture Awards 2018. At the Australian Institute of Architects’ 2018 WA Architecture Awards, the project received the Margaret Pitt Morison Award for Heritage and the Julius Elischer Award for Interior Architecture. It also earned an award in the Public Architecture category and a commendation in the Mondoluce Lighting award category.
South Australia-based National Precast member SA Precast (Specialty Architectural Precast) manufactured all precast concrete
Precast features of the Cadogan Song School include curved beams, spires and lattice feature wall panels.
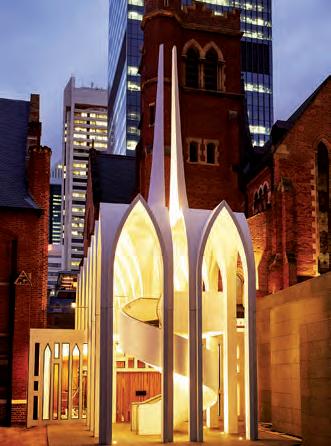
elements for the project. These included curved beams, spires, lattice feature wall panels, the first storey supporting columns for the second storey shells and the shells for the second storey that form the colonnade. The elements were manufactured with a white cement and featured a lightly textured off-form finish.
WYNYARD WALK
A major pedestrian walkway now connects Sydney’s Wynyard Station to the bustling Barangaroo waterfront precinct and the CBD. Having won the State Award for Infrastructure Projects at the Concrete Institute of Australia’s 2017 Awards for Excellence and the Public Design Award at the 2018 Australian Interior Design Awards, the Wynyard Walk is a stunning example of precast concrete in Australian infrastructure.
National Precast member Asurco Contracting manufactured precast glass reinforced concrete panels for the walls and ceiling of the tunnel at its South Australian factory. This process involved the framing, mould-making, manufacture, installation and coating of the elements.
Barangaroo’s waterfront development attracts up to 33,000 visitors and host approximately 23,000 office workers daily. The new 180-metre walkway allows pedestrians to travel from the station to the waterfront in just six minutes, making it a vital part of the state government’s commitment to meet Sydney’s transport needs.
SYDNEY SKYTRAIN
With an aesthetic appeal that sets a new infrastructure benchmark, the Sydney Skytrain is the most visible legacy of the Sydney Metro Northwest project – Australia’s first fully automated metro rail system.
Delivered by Salini Impregilo, the Sydney Metro Northwest project won the top prize for the railway sector at
Wynyard Walk won the
Public Design Award at the 2018 Australian Interior Design Awards.

the 2018 Global Best Project Awards by US construction magazine Engineering News-Record. The project was selected by a jury for its excellence in construction, attention to safety and diversity and community benefits.
Hanson Precast, one of National Precast’s New South Wales members, manufactured 2300 precast concrete parapets and 56 platform units for Stage 1 of the project – the Sydney Skytrain. The precaster also produced the Skytrain’s in-situ concrete. Part of the company’s factory was used to produce 1200 precast concrete viaduct segments.
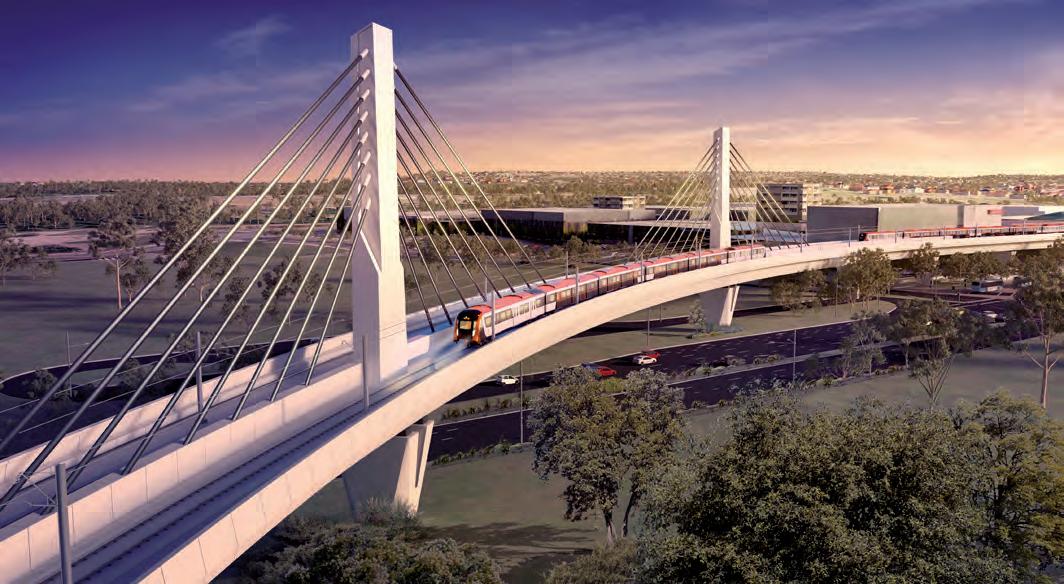
SMALL CULVERT ALIGNS WITH CURRENT PRACTICE
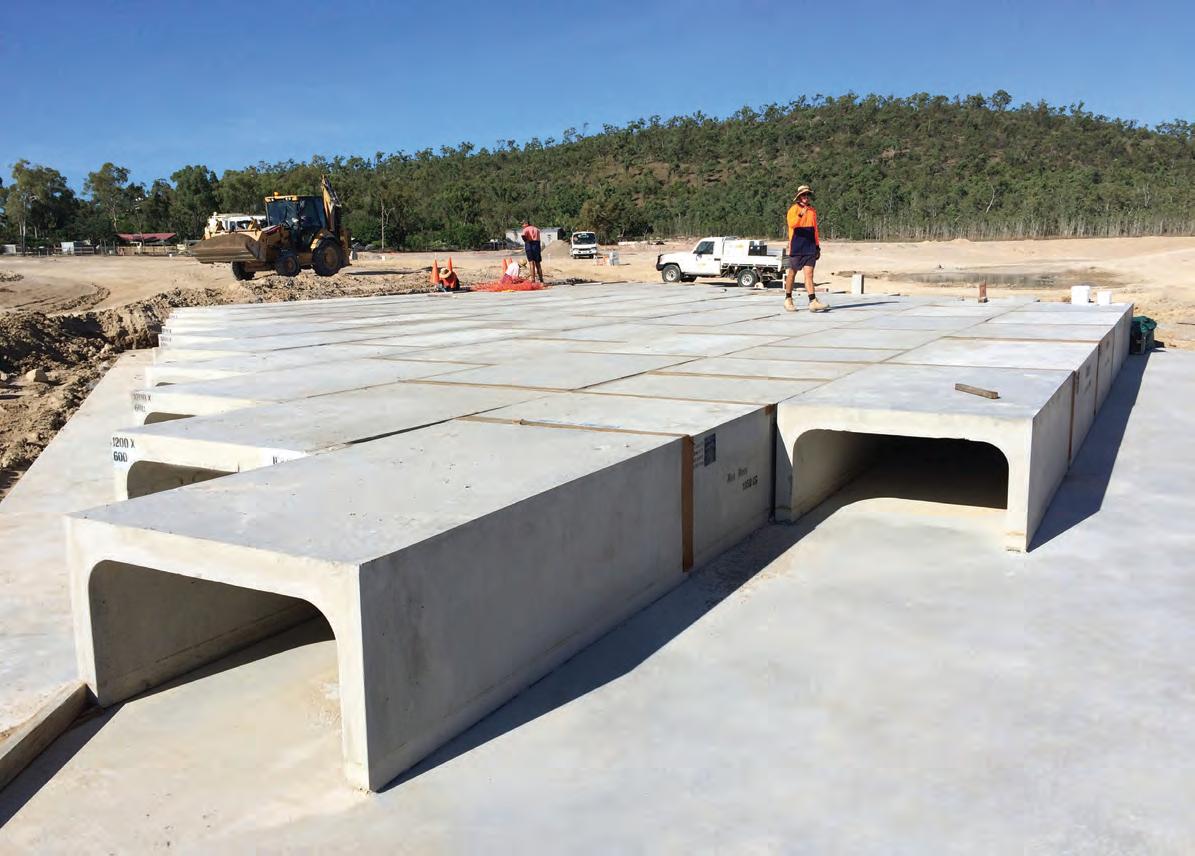
NATIONAL PRECAST CEO SARAH BACHMANN EXPLAINS WHAT NEW AMENDMENTS TO THE AUSTRALIAN STANDARD FOR PRECAST REINFORCED CONCRETE BOX CULVERTS MEAN AND THE BENEFITS THEY BRING.
AS 1597.1-2010 Precast reinforced concrete box culverts specifies minimum requirements for the design, testing, manufacture and installation of precast reinforced concrete rectangular box culverts that span up to 1200 millimetres.
According to National Precast Chief Executive Officer Sarah Bachmann, a recent amendment to the standard, which increases the number of nominal size classes, has several benefits.
“This amendment brings the standard in line with Australia’s current manufacturing and installation practices, as well as current governing design codes. It will also bring efficiencies to civil projects,” Ms. Bachmann explains.
Published by Standards Australia in August 2018, the amendment to the standard adds eight new nominal size classes in Table 2.5. The removal of note 2 beneath the table, “Other size culverts may be made to a specific order”, was a key part of the amendment.
Precast manufacturers that choose to align their product range to the new sizes can manufacture stock to provide customers with ready-made products. As designers and civil contractors become familiar with the expanded range of sizes, they can have more confidence that small box culverts will be readily available as “off the shelf” items.
“More nominal sizes should increase the likelihood of designers specifying one of the standard sizes, rather than custommade sizes,” Ms. Bachmann says.
“Being available at short notice will shorten lead times, allow projects to get started sooner and will reduce the overall timeframe of projects. This is a change that will benefit manufacturers, contractors and asset owners.”
About Australian Standards While on their own, compliance to Australian Standards is voluntary, government regulators and public health authorities often turn to standards in their regulation to provide a baseline level of safety requirements for houses, buildings, infrastructure and machinery. In the construction sector, compliance with Australian Standards helps to codify best practices, methods and technical requirements to create safe and sustainable infrastructure. It is vital that all asset owners, both in the private and public realms, have confidence that the products they are buying and installing meet the requirements of the relevant Australian Standard. Australian Standards set out specifications and procedures that aim to ensure all suppliers are manufacturing, supplying and testing their products in accordance to strict guidelines.