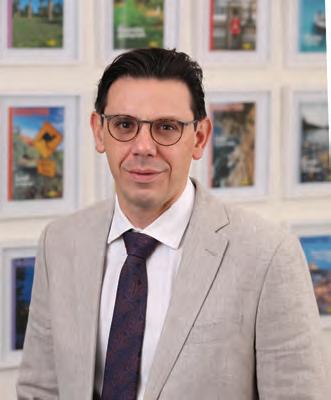
6 minute read
Building the roads of future
BUILDING THE ROADS OF THE FUTURE
WITH A FOCUS ON DEVELOPING SUSTAINABLE PAVING SOLUTIONS, SAMI BITUMEN TECHNOLOGIES HAS BEEN PIONEERING RESEARCH AND TRIALLING OF SOME UNIQUE PAVEMENT PRODUCTS. SAMI’S GENERAL MANAGER SEBASTIEN CHATARD TALKS ABOUT THE COMPANY’S VISION FOR GREENER ROADS.
With Australia going through an unprecedented period of infrastructure investments, a growing number of agencies, companies and government bodies are embracing the principles of sustainability in infrastructure.
A sustainable pavement, as defined by the US Department of Transportation’s Federal Highway Administration (FHWA), is one that achieves its specific engineering goals, while, on a broader scale, (1) meets basic human needs, (2) uses resources effectively, and (3) preserves/restores surrounding ecosystems.
Sebastien Chatard likes to add one more condition to the FHWA definition – and that is durability. He notes that if asphalt binders are designed to improve the serviceability of pavements, they inevitably contribute to effective use of resources and help minimise the need for repair and maintenance, therefore leading to greater sustainability outcomes.
It is in line with these principles, he says, that SAMI Bitumen Technologies has been building its growing portfolio of speciality bituminous products.
“At SAMI, we have been concentrating on expanding our innovative products list with a sustainability focus for many years. In doing that, our focus has been on developing products that can be applied with lower energy cost and lower carbon emissions into the environment, while improving the long-term performance of asphalt and sprayed seals,” he tells Roads & Infrastructure.
SAMIFALT I-BRID One such product that SAMI launched in 2020 and successfully trialled was the SAMIfalt I-Brid, a hybrid asphalt binder with proven rut resistance at elevated road temperatures and high flexibility at cold temperatures under heavy traffic.
The first application of SAMIfalt I-Brid was at the Bundaberg Airport in Queensland for Bundaberg Council, which was laid by Colas Queensland in June 2020. The binder was required to adhere to the strict requirements for aircraft movement.
In March 2021, SAMI in conjunction with Centre State Asphalting paved 540 tonnes of SAMIfalt I-Brid asphalt at Kangaroo Flat, near Bendigo, for Victoria’s Department of Transport. In June SAMI supplied I-Brid binder to Colas’ Newcastle asphalt plant where it was paved as a wearing course on Weakleys Drive. This is one of the busiest roads in the Maitland Council network and the project was carried out on what was considered one of the coldest nights in the last decade. Both trials successfully demonstrated a high-quality binder that’s suitable for all weather conditions and in high traffic areas.
Chatard says SAMI developed the SAMIfalt I-Brid as part of a collaborative research project with RMIT University, with an eye on developing a universal binder suitable for use in different locations and for different types of applications.
“As a national player in the bitumen industry, we listen to the local market to learn what’s required for the Australian environment. That’s why we developed SAMIfalt I-Brid as we saw a gap for a ‘universal’ binder,” he says.
SAMIBOND 007
Year 2021 was also when SAMI’s SAMIbond 007 trackless tack coat cationic bitumen emulsion found widespread use in the industry, Chatard says.
SAMI first developed its trackless tackcoat emulsion in 2019 as a solution to improve bonding between the base course and the asphalt overlay in airports, where heavy construction machines are required to traffic the freshly sprayed tack coated surfaces. Improved bonding leads to longer lasting pavements and this has prompted pavement engineers to make the product’s use mandatory on asphalt projects.
After being successfully used on a number of airports across Australia, including for runway/taxiway upgrades for the Solomon Airport in Western Australia and the Sydney International Airport, Chatard says the broader construction industry has also adapted the product.
“With SAMIbond 007, we have developed a new emulsion-based trackless tack coat to prevent the loss of bond coat due to construction traffic movement. This product has already gained acceptance by the Australian market and is used to improve pavement performance, particularly in high-traffic areas,” he says.
Sebastien Chatard, General Manager, SAMI Bitumen Technologies.
REDUCING USE OF CUTTERS Minimising the use of kerosene-based
cutters in hot bituminous binders is another way by which SAMI is contributing to sustainable pavements.
One of these solutions that SAMI introduced in 2020 and further demonstrated in 2021 with the VSA Group was SAMIseal S45R-LV, a crumbed rubber binder that can be sprayed cutterfree, to minimise on the use of kerosene cutters significantly. Using the Germanbuilt OB Vario synchronised bituminous surfacing technology, the VSA Group uses the low-viscosity crumbed rubber binder to eliminate the use of hazardous cutback bitumen for sprayed sealing in the cold climate.
More recently, SAMI introduced SAMIfloat, a cationic high-float thixotropic sprayed sealing emulsion in late 2021. With field trials being planned, the emulsion acts as an environmentally friendly alternative for cutback hot unmodified or hot polymer modified binders in sprayed sealing applications.
Year 2021 was also when SAMI’s BioPrime prime coat emulsion hit the market. As an emulsion with no petroleum solvents, SAMI’s BioPrime allows safe sealing operations without exposing workers to fumes or harmful volatiles during the priming process.
Gerard Gnanaseelan, SAMI’s Bitumen Technical Manager, says these products and more coming out of SAMI’s research laboratories all serve the same purpose: to improve the quality of asphalt pavements, while reducing carbon emissions and energy consumption during the application process.
“Our new product range is made by substituting the light petroleum raw materials with bio-based raw material to reduce hydrocarbon emissions. Our BioPrime and BioPrecoat – currently under development at SAMI’s research laboratory – are fine examples of products that reduce significant quantities of hydrocarbon emissions from being released to the environment,” he says.
A BROAD SUSTAINABILITY STRATEGY More broadly, Chatard says SAMI is guided in its sustainability initiatives by the 2030 target set out by the Colas Group as SAMI’s parent company.
“Globally, the Colas Group has set a target of 30 per cent reduction in direct greenhouse gas emissions across its entire upstream value chain by 2030 from the company’s 2019 level. Every product we develop at SAMI is in line with achieving that overarching target, while our customers benefit from the flow-on effect as they use our products,” he says.
To assist its clients even further, Chatard says SAMI is making sure it remains close to its customers and removes any logistical constraints that could delay product delivery.
“With both production and technical support available in every state, we like to stay close to our clients. Our laboratories are available for any client looking to test or even develop a new product with us. SAMI has also reinforced its fleet capability to remove any logistical constraints to moving products to project sites.”
The journey has not been without challenges.
“The past two years have definitely posed some new challenges in terms of availability of raw materials and restrictions on the movements of people. With disruptions in global freight, we have had to wait sometimes three to four times longer for raw material supplies. But we have found that by listening to the market and being proactive in predicting our customers’ demands, we can still deliver to our clients what we promise,” Chatard says.
“SAMI has business, technical and logistical experts available in every state, who work closely with clients to meet their requirements. In 2022, we look forward to continuing provision of quality sustainable products to the market, which will be supported by our increased terminal and fleet capacity.”
The SAMIfalt I-Brid asphalt was used on a road section near Bendigo, in a project done for Victoria’s Department of Transport.
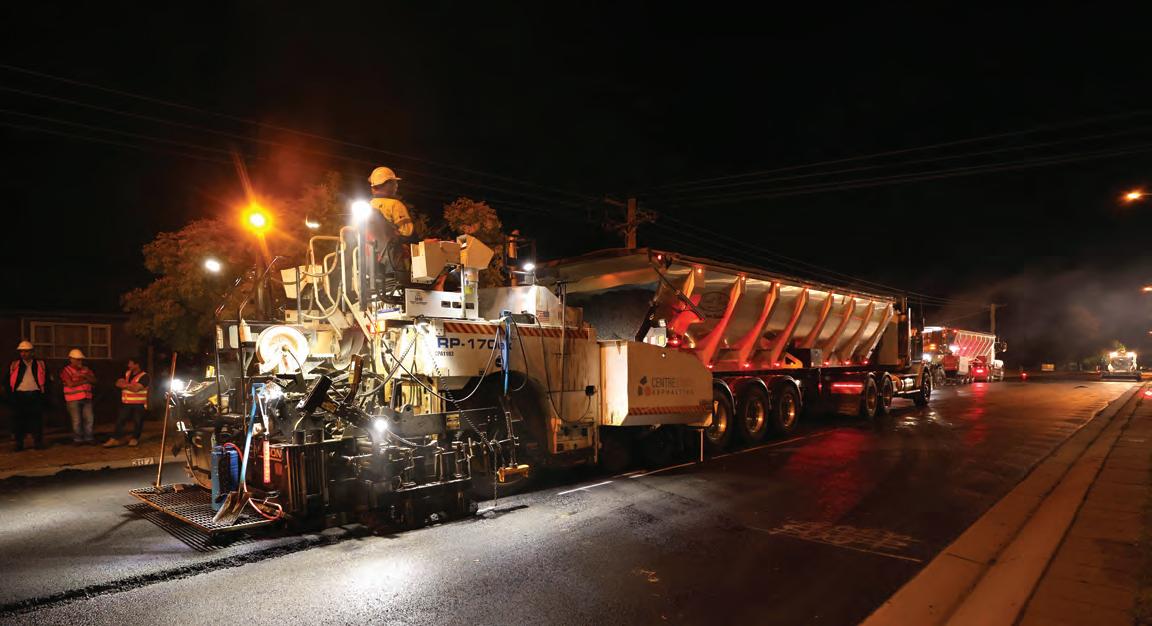