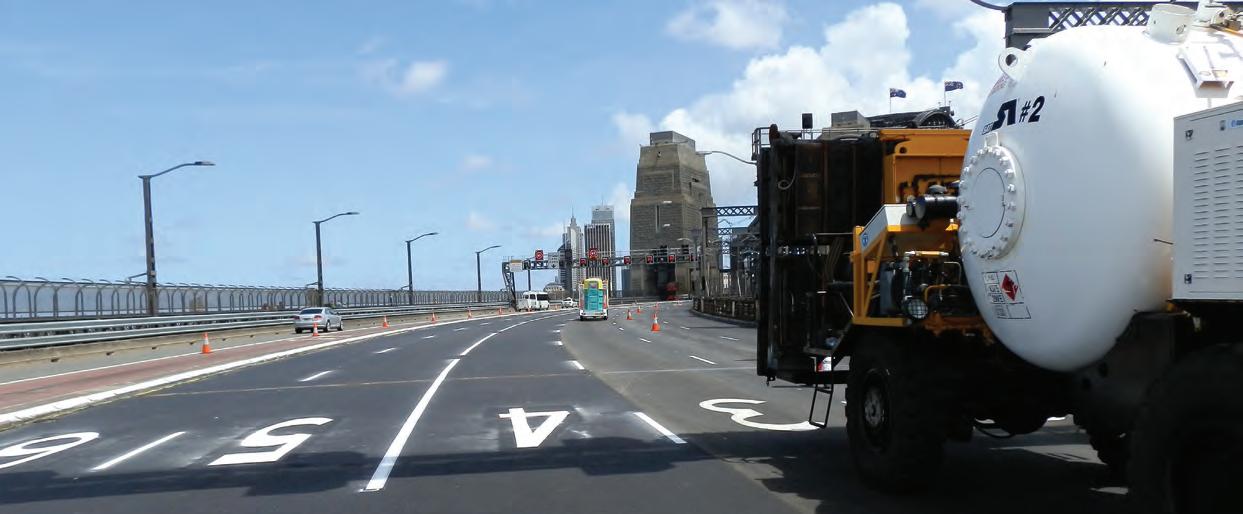
6 minute read
Introducing Hiway Group
FROM THE GROUND UP
SINCE ESTABLISHING ITSELF IN AUSTRALIA IN 2008, HIWAY GROUP HAS GROWN AND EXPANDED TO BE A MAJOR SOILS AND PAVEMENT STABILISATION CONTRACTOR, WITH INFRASTRUCTURE PROJECTS SUCH AS THE PACIFIC HIGHWAY UPGRADE PROJECT UNDER ITS BELT. A ccording to research published in international soil mechanics journal Géotechnique in 1983, soil movement is of great importance in Australia.
This is due to the fact that around 20 per cent of the total surface soils in Australia consist of expansive soils.
Expansive soils are those with excessive swelling such as clay minerals and can be affected by water, drying or surrounding vegetation.
Consequently, soil movement can affect the structures created on top of them unless the swelling and drying movements over seasonal and weather events can be treated. Stabilisation is one effective and sustainable method for achieving this.
Due to Australia’s vast size and diverse soils, one New Zealand family decided to bring its successful road stabilisation business to Australia in 2008.
The Boocock family, founders of Hiway Stabilizers, believed stabilisation would be an environmentally sustainable and effective way to repair and construct roads and provide strong and resilient foundations.
Over the past 12 years, the business has expanded across Australia with a group of companies providing stabilisation, profiling and micropatching solutions.
Paul Rhoden, Hiway Group General Manager of the Northern Region, says the company’s diverse locations and key products cover each stage of road stabilisation.
Hiway Group’s main stabilisation company, Hiway Stabilizers, reaches all of Australia. This spread, and its large fleet of specialised plant and people, means the company has the resources to scale up on major long term projects. Recently, Hiway Stabilizers provided up to eight subgrade stabilising crews on a major regional infrastructure project for an extended period.
Mr. Rhoden says each company under the Hiway Group aims to provide sustainable solutions for road and infrastructure projects across Australia’s diverse landscape.
“One of the key products for the company is subgrade modification, which adds a small quantity of stabilising additive to improve the engineering properties of the in-situ soils. This additive is lime, cement or triple blend stabilisation depending on the inherent or underlying ground conditions that we encounter,” he says.
To determine the right additive design, extensive testing prior to stabilising the soil is performed. This is to assess the material’s properties and determine which modification is best suited to the ground conditions to achieve the design outcome criteria.
“In collaboration with our clients, we are always looking for environmentally sustainable solutions that offer best wholeof-life value for infrastructure projects. Our in-house pavement and mix design group have a wealth of experience in
Hiway Group’s main stabilisation company – Hiway Stabilizers – reaches all of Australia.
stabilisation and materials, and this helps our clients to refine their project solutions,” Mr. Rhoden says.
“The soils underneath a road can affect the surface anywhere from two to five metres deep. In a drought, the materials contract, whereas in a flood, the materials expand.”
Mr. Rhoden says without stabilised foundations, there is nothing to counteract the expansive and dispersive soils under the road.
“Once we have stabilised the subgrade, the next is to treat the subbase and base course materials. The use of stabilisation on granular materials allows lower grade and cheaper materials to be improved to meet the required engineering properties. That could be a gravel cementitious stabilisation or a blended product using waste materials such as fly ash and slag,” Mr. Rhoden says.
Alternatively, Hiway Stabilizers uses foam bitumen by injecting water into bitumen, so it expands, and adding lime to promote adhesion and stiffness.
“The reason we foam the bitumen is to increase the surface area of the bitumen, so it disperses throughout all of the gravel mass. This ensures all aggregates are held together by small bonds of bitumen creating spot welds on the smaller aggregate particles.”
Foamed bitumen is especially suited to Australian conditions due to its resilience to weather events. In 2017, the Queensland Government published a blog post detailing foamed bitumen pavement’s performance during ex-tropical cyclone Debbie.
“The department’s foamed bitumen
Hiway Stabilizers has worked on a portfolio of projects over the past decade.
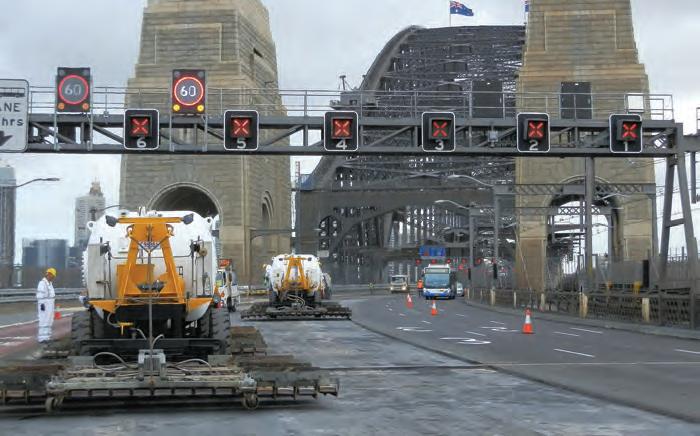
pavements, which when constructed in the right environment with appropriate stabilisation, are more resilient to flooding and have survived unscathed in some of the worst-hit parts of the state, displaying impressive strength in the face of catastrophic weather,” the post stated.
“When three-metre floodwaters inundated Camp Cable Road on the Mt Lindesay Highway, district staff understandably feared the worst. When waters receded, however, the foamed bitumen pavement was found completely intact.”
Mr. Rhoden says that one of the advantages of foamed bitumen is that due to its resistance to temperature and its strength, less asphalt is required when constructing the road.
“One further benefit to using foamed bitumen is that it can be kept in place and recycled again 10 to 15 years down the line by doing a couple of simple things to restabilise the material once the asphalt has been removed.”
The company has worked on a portfolio of projects over the past 12 years. One of the most notable is the Pacific Highway.
“We worked to some of the tightest tolerances on the Pacific Highway project in NSW. We paved two 220-millimetre layers to specification or higher, which I think is unheard of,” Mr. Rhoden says.
He says they will have produced and paved over 100,000 tonnes of plant mix foamed bitumen for the Pacific Highway.
The company has also worked on the Sydney Harbour Bridge conducting hot inplace asphalt recycling.
“We’ve got some large infrared heaters and we preheated the intermediate course on the Sydney Harbour Bridge because it was too cold to lay asphalt straight onto the foundation. If it’s cold in winter and you mill off the surface course, and it starts to rain, you can’t lay asphalt and open the road which is a big deal,” Mr. Rhoden says.
He says these heaters are part of the company’s Hot-in-place Asphalt Recycling operation that hot-recycles asphalt surfaces in situ.
Innovative ideas such as this are at the heart of the Hiway Group, which has also developed a process to create foamed bitumen stockpiles.
“When you make plant mix foamed bitumen, which we do, it can often only be used in an eight- to 12-hour window. Together with Transport and Main Roads in Queensland, we developed a plant mix foamed bitumen that can be stockpiled and still used for 14 to 28 days,” Mr. Rhoden says.
This enables companies to order much larger quantities of foamed bitumen for projects, lowering the price point and ensuring accessibility to superior road construction materials.
Mr. Rhoden says full-depth asphalt is most commonly used in Australia, and the company has been working towards changing the mindset of certain parts of the industry to use foamed bitumen.
“One thing foamed bitumen can solve is a reduction in the requirement of asphalt. Due to the pavement’s strength, fewer virgin materials are required for the asphalt portion of the pavement,” Mr. Rhoden says.
“Many in the industry haven’t been exposed to foamed bitumen and there is a resistance to change because in some places it is still an unknown product.”
That said, Mr. Rhoden believes this will change as more of the industry come around to the benefits of foamed bitumen and extensive use of stabilisation technologies.
“I do believe that we are the best at what we do. We may not always be the cheapest, but there is unique value in what we do and the engineered solutions we offer. I get excited about the opportunities we have to innovate and provide environmentally friendly and sustainable engineered solutions.”