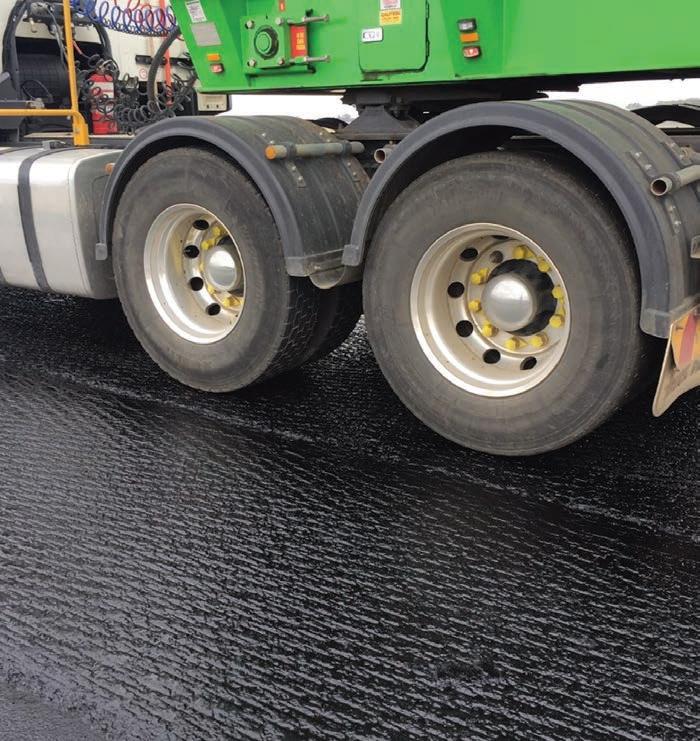
10 minute read
Special agent SAMIbond
WITH THE ABILITY TO PERFORM UNDER THE HIGH-STRESS OF AIRCRAFT TRAFFIC, SAMI BITUMEN TECHNOLOGIES SAMIBOND 007 TRACKLESS EMULSION IS PAVING THE WAY FOR NEXT GENERATION AIRPORT ASPHALT. A s one of the world’s most iconic characters, James Bond, created by author Ian Fleming in 1953, possesses a number of unique and highly recognisable traits.
The Secret Intelligence Service agent, code number 007, is intelligent, cunning and fiercely independent. Mr Bond is also known for his penchant for flying, with his cinematic equivalent chancing down opponents in a Britten-Norman BN-2 Islander aeroplane in the 2015 film Spectre.
SAMIbond 007, a special trackless polymer modified cationic bitumen emulsion developed by SAMI Bitumen Technologies in 2019, possesses many similar characteristics: namely strength, agility and an ability to handle aircraft.
The emulsion, according to lulian Man, SAMI Technical Services Manager, was designed specifically for airport applications, with high rutting and fatigue resistance engineered into the material. He adds that the central role of SAMIbond 007 is to improve bond strength between asphalt layers.
“Due to its good bonding characteristics, SAMIbond 007 is expressly designed to withstand the high shear stresses that develop under aircraft traffic loadings,” lulian says.
“The material provides a strong bonding element between base and wearing courses, allowing the pavement to act as a monolithic structure under the very high stresses of airport traffic.”
Working at the forefront of next generation airport binder development for more than 15 years, lulian says the importance of airport asphalt strength is well understood by SAMI.
“As a company, we are committed to improving airport asphalt technology, particularly in light of consistent growth in the global aviation sector,” he says.
Despite present-day disruptions, aircraft travel is projected to accelerate in coming years. Trends – Transport and Australia’s Development to 2040 and Beyond, a 2016 report published by the Department of Infrastructure and Regional Development, for instance, predicts international air travel will grow strongly to 2030, with domestic and international passenger movements through capital cities set to double.
The report suggests that growth at major airports is already testing the capacity of airport infrastructure during peak periods. While the Trends report examines airport infrastructure as a whole, lulian suggests the same predictions can be applied to asphalt.
“Standard airport pavements, be they, runways, taxiways or parking aprons, have to withstand loads previously unimaginable, SAMIbond 007 is designed to withstand high shear stresses that develop under aircraft traffic loadings.
in traffic levels and the growing weights of new aircrafts,” lulian says.
“This was at the forefront of our minds when developing the engineering properties of SAMIbond 007, which builds on SAMI’s previous work with airport asphalts such as our SAMIfalt B380 binder and SAMIfalt Multigrade Plus.” lulian says SAMIbond 007 is designed to not stick on construction vehicle tyres after the emulsion has broken and cured on the pavement. This tracklessness, he adds, is a critical feature for contractors managing often tight project deadlines.
During the breaking process, lulian says the colour of the applied product changes from brown to black to form a non-stick glossy appearance.
“The trackless nature of the emulsion is of critical importance, as the residual binder does not pick up under the asphalt tipper or paver tyres during the paving process,” he says.
“This ensures that a strong bond is
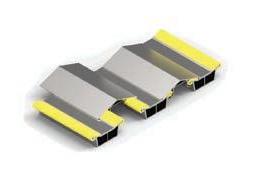
formed between the new asphalt and existing substrate, which allows the pavement to act as a monolithic structure to ensure a longer service life.”
Iulian adds that the trackless nature of the freshly sprayed tack coat works to ensure that no fresh bitumen is carried onto the surrounding areas.
During application, SAMIbond 007 is handled and applied in a tightly controlled manner, at a temperature of maximum 60°C via specialised sprayer trucks. Iulian adds that SAMIbond 007 can be stored for up to seven days without stirring, while noting that it must be gently stirred before use.
“The main challenges in application are related to the weather conditions, considering that the product is water based and wet weather would delay its curing once it has been sprayed,” lulian says.
“However, due its intrinsic engineered properties, the product is able to cure very fast, enabling paving to take place after one hour in normal daytime conditions.

The benefit of the fast curing process is reflected in increased productivity in asphalt laying, especially considering the tight deadlines for most projects.”
Minimum pavement temperature at the time of application should be 5°C, lulian says, with a minimum application rate of 0.25 litres/square metre for both milled and smooth surfaces.
“The application rate is to be agreed on-site with the contract administrator following site trials,” he adds.
It’s worth noting, lulian says, that SAMIbond 007’s usage is not limited to airport pavements and is also ideal on high traffic roadways like motorways and arterials, car racetracks, concrete pavement overlays and bridge decks.
“Given the emulsion’s high strength characteristics, SAMIbond 007 is well suited to any high trafficked pavement, making the material a versatile go-to option for contractors working on major projects throughout Australia,” he says.
ASPHALT FOR AVIATION
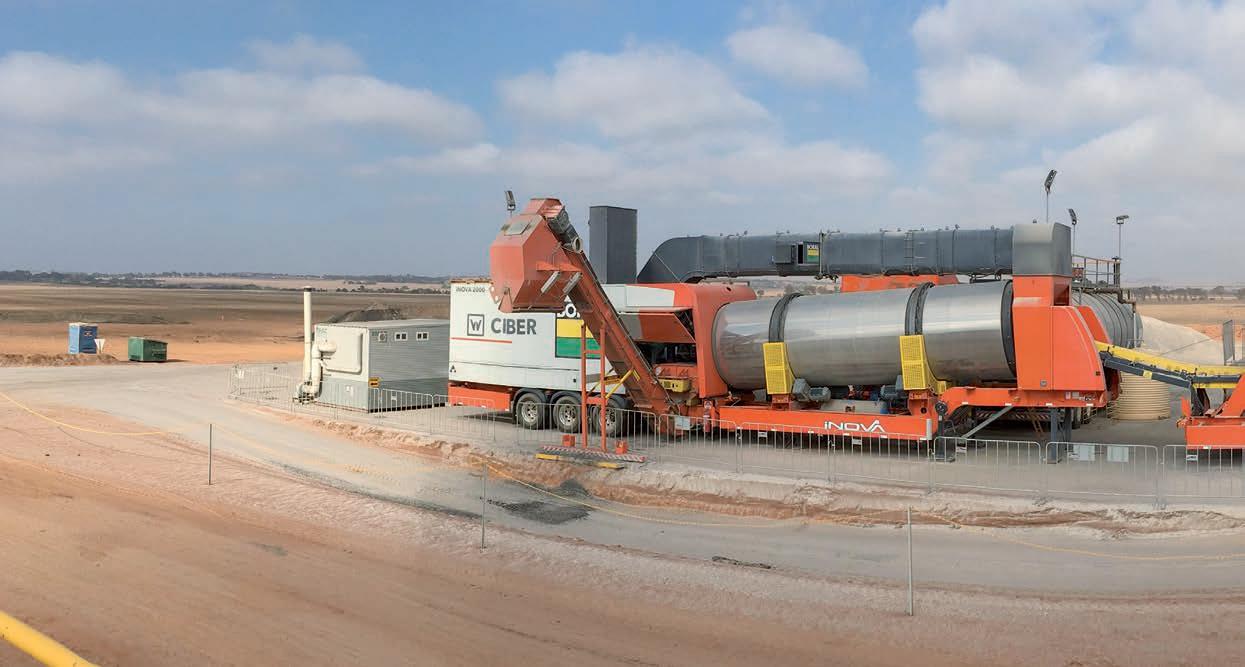
TASKED WITH RESURFACING AND EXTENDING THE GERALDTON AIRPORT RUNWAY IN WESTERN AUSTRALIA, BORAL TURNED TO WIRTGEN TO FIND A RELOCATABLE ASPHALT PRODUCTION PLANT WITH FLEXIBILITY AND A HIGH PRODUCTION RATE.
Four-and-a-half hours north of Perth sits Geraldton, a coastal city in the Midwest with significant port infrastructure and a strong agricultural industry, affectionately known as the windsurfing capital of Australia.
Geraldton City has a population of over 40,000 and Geraldton’s airport punches above its weight, servicing around 120,000 passengers yearly, bringing many visitors.
When it came time for a runway upgrade at the airport, contractor Boral was awarded the $24 million Geraldton Airport Upgrade Project. This included resurfacing the newly extended runway to 2.4 kilometres.
As the chosen contractor for the job, Boral came to Wirtgen looking for a high capacity, modular asphalt plant, that could be easily mobilised and suited to efficient production targets of more than 2000 tonnes each shift.
While expanding and resurfacing the runway, the asphalt plant was also required to supply mix for the airport’s main aprons. This included a new parking bay which would provide necessary taxiway clearances for the operation of the larger aircraft.
For this job, Boral purchased the Ciber iNOVA 2000 asphalt plant. Greg Astill, General Manager of Mineral Technologies at Wirtgen Australia, says the main benefit of this plant is the combination of the ease of mobility and high material production.
“Ciber plants are compact and flexible and they are relatively fast to establish on site, which is ideal for an airport as there are tight restrictions around timings for airport projects,” Mr. Astill says.
When completing projects at airports, he says it is important the contractor can stick to tight timeframes and ensure the risks of production loss through breakdown and or lower productivity are minimised. There can be significant financial repercussions if airport projects run over time and it can be very difficult for the contractor when flights are disrupted by construction works.
“This is why the Ciber iNOVA 2000 plant was chosen by Boral. These plants are well suited to airport projects, with the main trailer featuring an integrated dryer and burner, baghouse and pugmill with a slat conveyor,” Mr. Astill says.
“The iNOVA is very fast to establish on site with only one mechanical connection required between the cold feeder and the mixing trailer. These features make the plant very reliable and excellent for high rates of sustainable and consistent production.”
He says all that is needed to set up the iNOVA 2000 is to drive to the site, set up the ramp, position the two main trailers and connect the power and the bitumen tanker. After calibrating the feeders, it is possible to move straight into production.
“When producing a new surface for a runway, it’s going to require an asphalt that is durable under heavy loads. With high levels of production quality, the plant needs to produce a consistent mix every day. If there are variations, this could affect the quality of the final product,” Mr. Astill says.
The Ciber iNOVA 2000 plant can produce up to 200 tonnes of asphalt per hour. It is also capable of producing mixes with 15 per cent reclaimed asphalt pavement to increase sustainability on projects.
The Geraldton Airport project was Boral’s first rural airport project using an iNOVA 2000 asphalt plant. The same model has been used in the past two years at other regional airports such as in Queenstown, New Zealand and Busselton, WA.
Mr. Astill says all contractors have achieved excellent outcomes and performance from the operators of the Ciber iNOVA plants. For the Geraldton project, Boral were meticulous with planning prior to departure. Mr. Astill says Boral’s risk management plan was actioned. Under the direction of Ronan Moore, General Manager of Asphalt, the Ciber iNOVA was delivered to Boral’s Welshpool facility to undergo a complete pre delivery and assembly. Technical and maintenance training for the Boral operations and service teams was also completed by the Ciber factory technicians. After completion of initial trial mixes, the plant was packed up
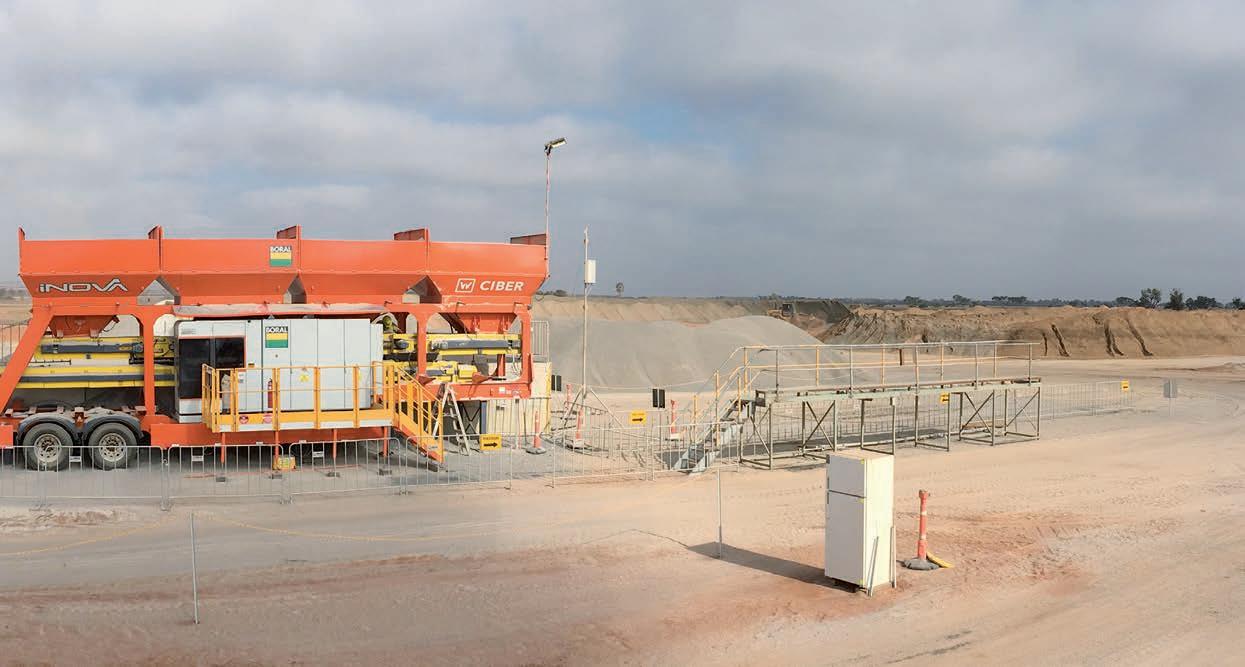
and mobilised at the Geraldton Airport site.
Boral then dissembled and shipped the iNOVA 2000 to the Port Hedland Airport Project in the Pilbara region of Western Australia.
Similarly, this project involved upgrades to the taxi line and a new layer of asphalt on the airport’s runway.
Ronan Moore says the team excelled at the Geraldton Project and were well prepared for the planned relocation of the Ciber iNOVA to Port Hedland.
“The pre work completed as part of project management plan ironed out any issues and we were quite quick to be up and running at Port Hedland,” Mr. Moore says.
“Its quite a relief to know that an OEM such as Wirtgen are right there supporting the Ciber product and once we were up and running, we were able to handle most issues with our own team.”
Mr. Astill says Wirtgen received great feedback from Boral about their support for the transfer of the asphalt plant and the quality training provided for the crew.
He says Wirtgen customers come to expect the right performance from any products sold in Australia and New Zealand. He says there is definitely some comfort among customers that dealing directly with an OEM, which can support both the customer and the product, is highly valued.
“It’s exactly the same with our Ciber iNOVA plants. We are there on the job site and in the office, working with the factory to make sure it works properly straight out of the box.”
He says even the control system for Ciber iNOVA plants is very intuitive and simple for an experienced operator.
“This new control system is excellent. It’s a very stable control system with a human interface that mimics the simplicity of working on an iPad or tablet. This control system is very strong,” Mr. Astill says.
Matt Schokker, Boral’s Production Manager of Mobile Asphalt Plants, says the touchscreen control system was simple.
“It displays a main plant overview screen, which shows the operator a detailed overview of all components synchronised from input aggregates to output of finished product asphalt,” Mr. Schokker says.
“Easy onscreen tabs help examine, in detail, individual process control operations to customise the plant for a variety of mixes such as dense grade, open grade, stone mastic asphalt, red laterite, and reclaimed asphalt product mixes. These all cater for local government, Main Roads WA and project specified mixes.”
He says Ciber’s PLC constantly monitors all inputs and outputs of the asphalt plant and makes adjustments autonomously to constantly keep parameters tight and keep the asphalt mix within specification.
“This consistency is evident through onsite laboratory production testing magnifying the exact process control achieved throughout the production process of the plant.”
Mr. Astill from Wirtgen says the plant is also well designed for other asphalt productions such as highways or freeway work in metropolitan or regional areas.
“All three airport project teams that have worked with the iNOVA 2000 had exceptional results with the plant. Operators identified consistent mix production and lower than expected production costs,”
“We see that the iNOVA 2000 operated by Downer has been relocated for the second time back to Queenstown for more work. Proving the point that the Ciber plant is very quick to relocate or mobilise, of course in these challenging times contractors need every advantage.”
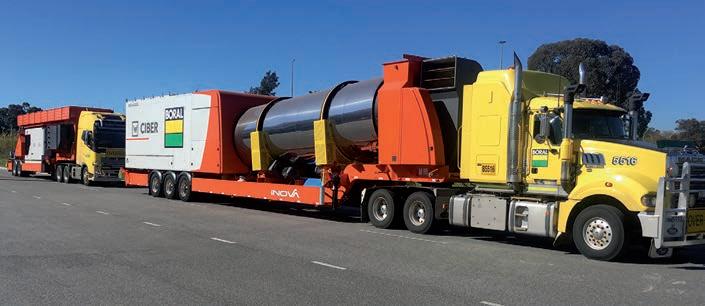