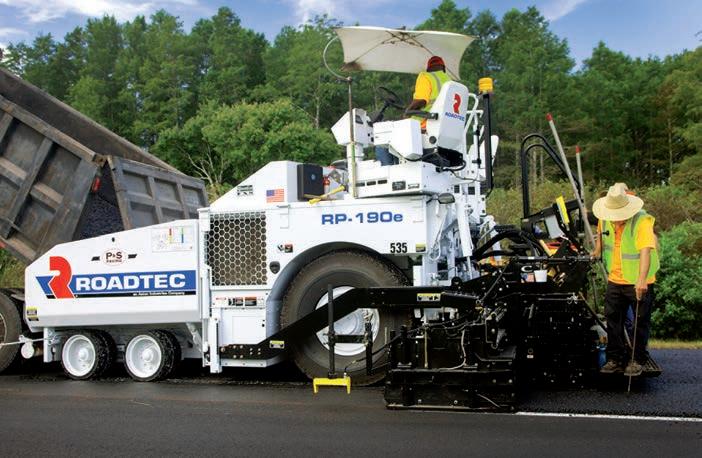
3 minute read
Paver maintenance
SMOOTH RUNNING ASPHALT
PAVERS ARE A KEY COMPONENT IN THE CHAIN OF WORKS ON ASPHALT PROJECTS. ASTEC’S JORGE BOIL EXPLAINS THE IMPORTANCE OF DAILY PAVER MAINTENANCE AND THE PROCESSES THAT CAN LIMIT COSTLY DOWNTIME.
Astec’s Jorge Boil says it’s best to keep the machine moving continuously in asphalt paving.
Downtime can be unavoidable, but on projects where it could have been prevented, it becomes a costly mistake. Working with asphalt presents some risks to the machinery if it is not cleaned properly after use, especially when the asphalt begins to cool down and set onto machine parts. According to Jorge Boil, Astec Australia’s Business Line Manager, there are ways to effectively minimise those risks and maintenance is the place to start.
“The simplest form of maintenance is cleaning. As one of the most important components of the asphalt production line, a paver should be thoroughly cleaned after each use,” Mr. Boil says.
Daily machine maintenance doesn’t generate direct profits, so it can be easy to lose sight of its importance. But preventing downtime can be priceless for paving jobs.
“If a paver breaks down, the entire asphalt supply chain comes to a halt. Downtime means everyone on site has to stop work, the trucks supplying asphalt are stopped, the asphalt plant production is affected.”
“Some companies doing major highway paving projects or road maintenance jobs will have a back-up paver sitting there in case of a breakdown. That’s because the machine is such an important part of the works.”
He says at the beginning of each shift, it is important for the operator to inspect the machine with everything turned off. This is the time to check for any visual damage, missing parts or oil leaks.
“Once you’ve walked around the paver, start the machine to warm it up. Make sure it can perform basic paving functions, such as the heating of the screed,” he says.
“Check the engine oil levels, hydraulic oil levels, fluid levels and tyre inflation. If the paver has Autolube capability, the operator should check to make sure it’s working. Autolube pumps grease onto the bearings and you want it operating well.”
At the end of the day’s work, the essential job of cleaning the paver begins.
“If a paver is not properly cleaned at the end of a shift and asphalt is left on the screed or anywhere else, it will cool off and harden like rock. Then when the machine is turned on again, parts such as the auger, chain or pump are at risk of breaking stopping the entire production,” Mr. Boil says.
The complete clean of a paver should take only about 10 to 15 minutes, and most machines now have a built-in tank containing a solvent spray that helps remove the asphalt.
“It’s critical that cleaning is done straight after the paver has finished production. Everything must be kept running because it’s much easier to remove the asphalt when it’s hot rather than when it has cooled and dried,” Mr. Boil says.
“The screed is the most important component to get clean, but other areas such as augers and conveyors need to be thoroughly cleaned, too.”
Preventative maintenance efforts such as daily checks and cleaning not only help prevent the significant costs associated with downtime, but can also enhance the quality of the paving job.
‘Safety, quality and productivity as a means to ensure success,’ is one of Astec’s core values and helping customers limit downtime is a key part of that. Educating operators and technicians about best practice care for their machinery is a high priority for the company.
“For every paver that goes out the door, we perform a total machine handover over five working days. In that time, we ensure the operators and service personnel are well trained in maintaining and servicing their machine,” Mr. Boil says.
As with most of the company’s machines, Astec pavers are equipped with the Guardian system, a telematics program that alerts owners, through their computer or mobile device, if components on the paver are not performing as expected.
The Guardian system will send an alert if a pump on a machine is showing high pressures, something that could indicate imminent failure. “Prevention is the key. If you wait until something goes wrong, you’ve lost control of your schedule. But when you’re in control you can keep maintenance up-to-date, and that means higher productivity and increased profits. And that’s something we all want to see.”