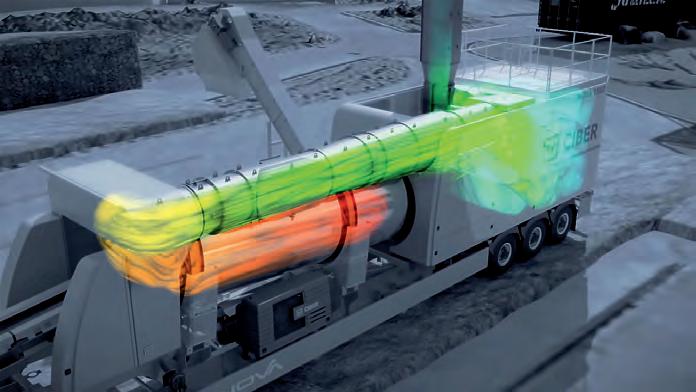
5 minute read
A green focus
ASPHALT PRODUCTION GOES GREEN
AS THE ROAD CONSTRUCTION INDUSTRY MOVES TOWARDS MORE GREEN AND ENVIRONMENTAL INITIATIVES, CIBER EQUIPMENT DETAILS THE TECHNOLOGY IN ITS iNOVA ASPHALT PLANTS THAT OFFERS FUEL SAVINGS AND EMISSION REDUCTIONS.
As the States and Territories across Australia set zero emissions targets for the future, construction companies are looking at the role they can play in the reduction of pollution across the supply chain.
In early 2020, the Infrastructure Sustainability Council of Australia (ISCA) released a report which found in Australia, construction and the operation of physical infrastructure assets for transport, energy, water, waste and communications, contributes to around 70 per cent of greenhouse gas emissions.
Direct contributions to emissions were calculated at 15 per cent and the report also found a 55 per cent contribution to the influencing of annual emissions through activities enabled by the infrastructure.
In recent years the road construction industry has been investigating new processes to reduce some of these emissions.
These kinds of environmental considerations have been a large focus for original equipment manufacturer, CIBER Equipment when creating asphalt plants.
CIBER’s Product and Application Specialist, Marcelo Zubaran says the gasses released during production of an asphalt plant will depend on the type of fuel used and the quality of combustion.
“In a complete combustion with hot mix asphalt plants, when fuel reacts completely with the oxygen, normally CO2 and H2O are released. If the combustion is incomplete and part of the fuel does not react with the oxygen it has the chance of releasing CO2, but also CO, SO2 and NOx,” Mr. Zubaran says.
Working towards an economy that has close to zero emissions will require a significant reduction of greenhouse gasses such as CO2, and CIBER recognised asphalt plants could have an impact on this endeavour.
Mr. Zubaran says the asphalt burner is crucial to ensuring quality of combustion and therefore reduction of emissions, as some harmful gasses may only be generated
When the burner is blowing fuel and air through the plant a flame is produced. in incomplete combustion.
The iNOVA Total Air burner features CIBER’s Total Air technology which automatically controls the optimum air to fuel ratio necessary for combustion.
Mr. Zubaran says the technology mechanically supplies the air to the plant through two fans, without suctioning air through the plant from the outdoor environment.
“The use of Total Air burners allows a closed-loop combustion system. This way a pressure gauge, placed in the combustion chamber, can monitor negative pressure inside the dryer drum and can vary the rotation speed of the exhaust fan in real time,” he says.
When the burner is blowing fuel and air through the plant, a flame is produced to avoid the injection of unburned fuel into the aggregates. This flame creates the gas in an asphalt plant and Mr. Zubaran says this in turn creates the need for a bag filter.
“In CIBER plants the exhaust fan is responsible for sucking the gasses from the burner, this forces the gasses to travel in the exhaust pipe and reach the bag filter. From there it goes through the fabric, into the exhaust fan and finally the gasses are released into the environment,” he says.
During this process powder or dust can get blown, with the gasses, through the exhaust pipe. At this point the filter bag catches and retains the dust while the gas passes through, reducing dust contamination outside of the plant.
Mr. Zubaran says the filtering system has a significant impact on the amount of dust particles that are released into the environment.
“CIBER plant bag filters are made of a special fabric that can resist temperatures of
the equipment in operation with a cylindrical shape or pleated surfaces,” he says.
The pleated bags were developed by CIBER with the purpose of obtaining a large filtering area in a reduced amount of space.
“When the filtering area is higher it means the filter will stay cleaner for longer during production. This enables the filter to better contain dust or powder,” Mr. Zubaran says.
“A dirtier filter creates a barrier for the air to pass through, which increases the loss of pressure in the plant. This causes a reduction in the amount of air necessary for combustion, reducing the amount of fuel that can be injected into the burner,” Mr. Zubaran says.
He says when the fuel is reduced, it is important to maintain the ideal fuel to air ratio. To do this, the air is consequently reduced which can slow production down and at this point the filter bag would need changing.
In CIBER plants, the exhaust fan is responsible for sucking the gasses from the burner.
For CIBER’s iNOVA asphalt plants, four elements were implemented to increase its environmental responsibility.
“The main technologies we focused
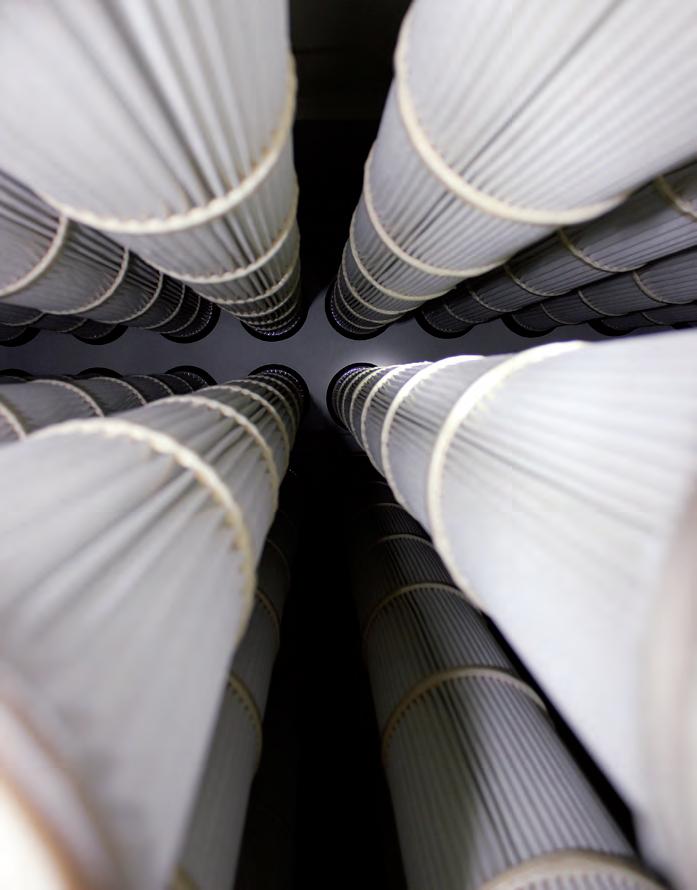
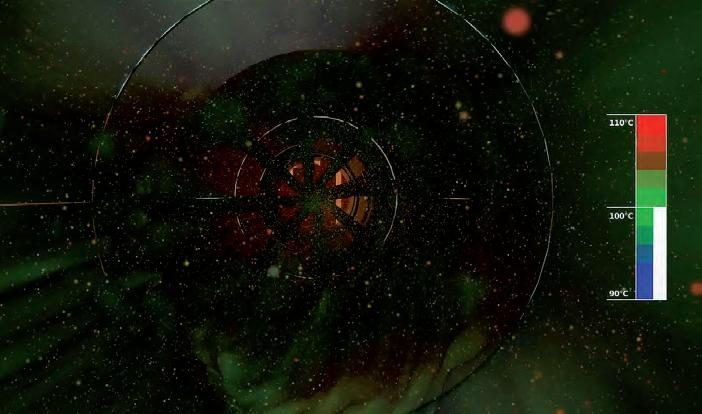
on to make the iNOVA plants more environmentally friendly were the bag filter and smart combustion system, but also the Total air burner and the exhaust fan on demand,” Mr. Zubaran says.
CIBER iNOVA plants feature a Smart Combustion System which allows the thermal energy in the plant to be kept at a consistent level.
“This is important because the more thermal energy the aggregates receive, the lower the temperature of the gasses traveling to the bag filter will be,” Mr. Zubaran says.
The temperature in the bag filter needs to be 100 degrees Celsius or higher to avoid condensation, which can be damaging in the combustion process. If the temperature is right, it will produce the most efficient level of heat exchange possible for the aggregates, while also achieving the right temperature in the filter.
“A perfect thermal exchange temperature can result in lower fuel consumption both when heating the aggregates and when powering the exhaust fan for the filter,” Mr. Zubaran says.
“These technologies applied in the plant’s drying system work to ensure the lowest fuel consumption possible and consequently, lower emissions.”
Mr. Zubaran says a CIBER asphalt plant is a long-term investment, as it will be in production for many years.
“As environmental technologies are also long term we need to be prepared for future demands. The road building industry are demanding more ‘green’ technologies and the ones applied on our plants help to reduce costs and emissions through fuel savings.”