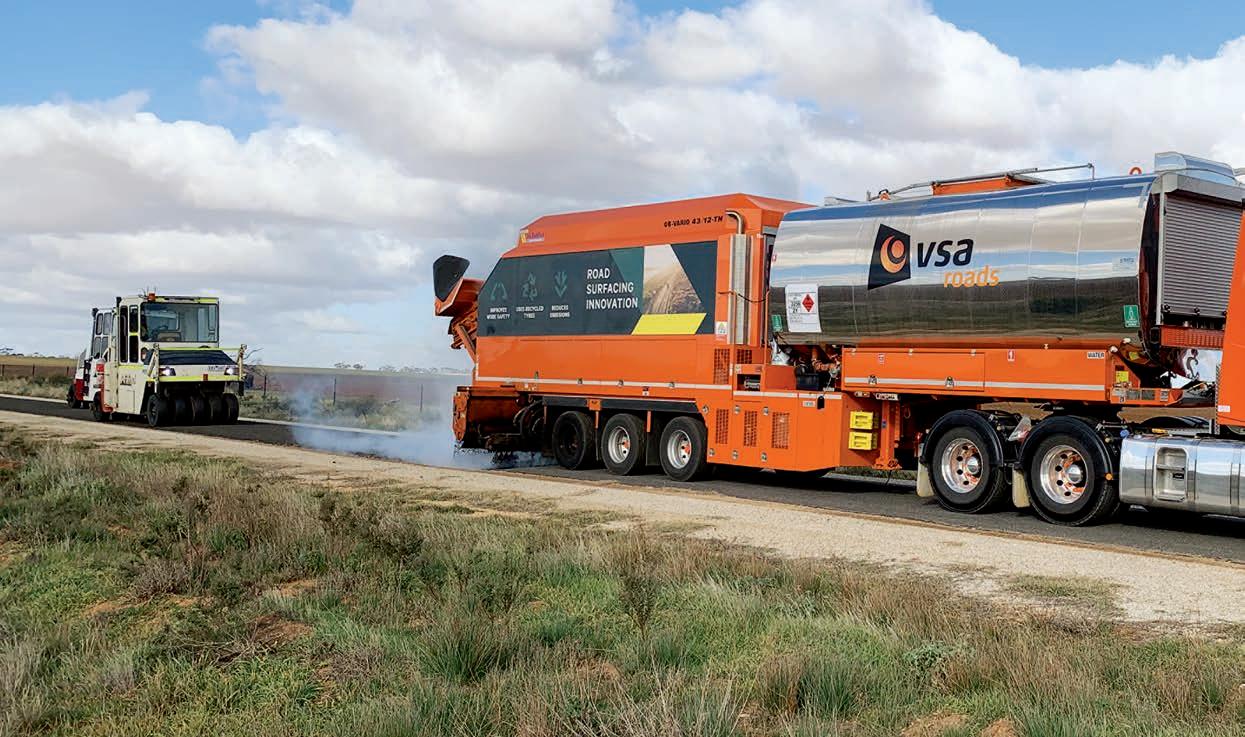
4 minute read
Low viscosity crumb rubber binder
MOVING BINDER
INNOVATION FORWARD
SAMI BITUMEN HAS DEVELOPED A LOW VISCOSITY CRUMB RUBBER BINDER THAT CAN BE SPRAYED DURING THE COOL PERIODS OF THE YEAR FEATURING A SIGNIFICANT REDUCTION IN THE USE OF KEROSENE. WE SPEAK TO PRIMAL SURFACING, A COMPANY USING THE PRODUCT DUE TO ITS SAFETY AND ENVIRONMENTAL BENEFITS.
Commonly used in crumb rubber binders as a cutter, kerosene can generate fumes which contribute to pollution, acid rain and greenhouse gas emissions.
For spray sealing applications kerosene can improve the binder wetting of the aggregates to create a better-quality road. It also reduces the bitumen’s viscosity to ensure it is fluid enough to be sprayed evenly onto the surface without streaking.
However, SAMI Bitumen has created a low viscosity crumb rubber binder capable of achieving these outcomes without using a kerosene cutter for the most part of the year and with a significant reduction in the use of kerosene during winter time.
Iulian Man, SAMI Bitumen Technical Services Manager, says the company recognised that if it could create a crumb rubber binder without kerosene that has low viscosity, it could help to improve the environment without compromising the spray seal performance.
In order to create the low viscosity binder, the SAMI Bitumen team performed chemical modifications to produce the right formulation.
“We basically reengineered the formula of our standard crumb rubber binder in order to lower the viscosity and create the new, a more fluid crumb rubber binder. No fluxant additives were used in the process” Mr. Man says.
“We got to a stage where we have created a crumb rubber binder that doesn’t need any cutter or very little during winter applications.”
Elimination or significant reduction of kerosene in the binder can also reduce
Primal Surfacing’s OVB production unit.
the risk of fires and the need to handle dangerous goods onsite as kerosene is a combustible hydrocarbon liquid.
In the spraying process the increased fluidity of the binder enables a uniform coverage of the road surface and therefore there is little risk of leaving portions of the road uncovered. “For a spray seal, the ability for a binder to retain the aggregate is the most important aspect for the performance of the road. Prevention of aggregate stripping improves a pavement’s life cycle outcomes,” Mr. Man says.
“When developing this binder we knew that we had to be well below the typical viscosity of a standard crumb rubber binder in order to achieve the adhesion properties we were looking for.”
During development of the low viscosity crumb rubber binder Mr. Man says that all testing was benchmarked against a standard crumb rubber binder. The new formulation complies with the specification for the S45R grade of crumb rubber binder.
“The product can be used in every situation from low to high traffic and is a very versatile option for all spray sealing jobs,” Mr. Man says.
So far SAMI Bitumen’s low viscosity crumb rubber binder has been used on a number of spray sealing projects in Victoria.
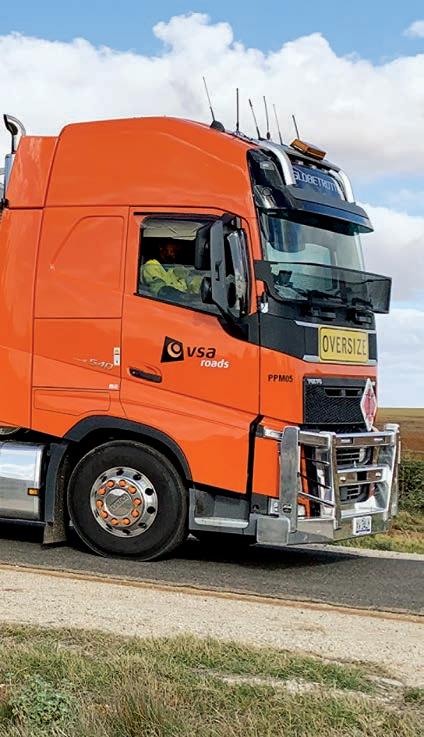
Increased fluidity of the binder enables a uniform coverage of the road surface during the spraying process.
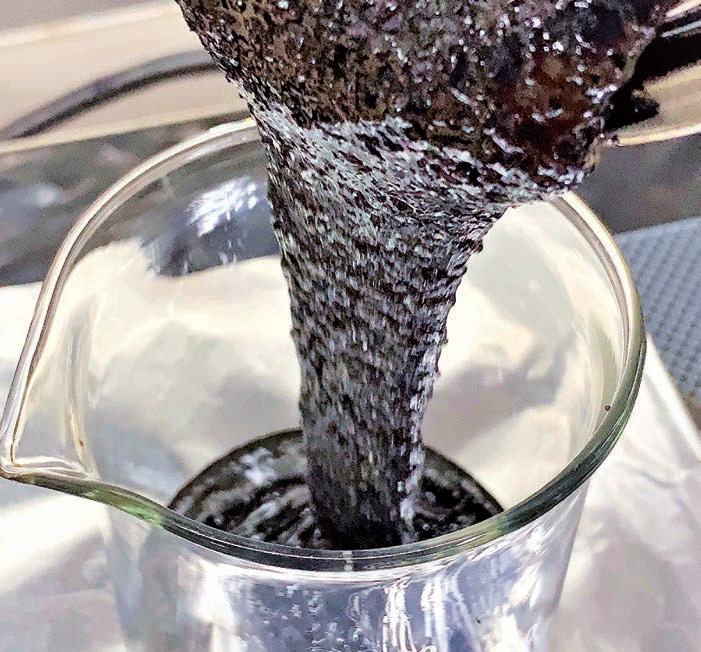
Primal Surfacing has been the first contractor to use the binder for works across the state. Managing Director Justin Bartlett says the company was looking to implement new forward moving synchronized bituminous surfacing technology designed and built in Germany.
Called the OBV production unit, the forward moving machine can spray bitumen and spread aggregate simultaneously in a forward direction.
“The OBV technology is used extensively throughout Europe but hadn’t previously sprayed a crumb rubber derivative. We specifically targeted the low viscosity product because we knew that the European technology could achieve lateral binder spraying uniformity with product viscosities less than 0.20 Pa.s.,” Mr. Bartlett says.
“If the OBV producton unit can spray an S45R binder, which is the highest level of modification, then we know it can spray all other modified binder used on the Australian road network. We also wanted to ensure the binder we were using met the specifications for torsional recovery and softening point and the SAMI binder did.”
Primal Surfacing has a mantra to support safer and more sustainable products and the removal of kerosene from this binder is in line with those goals.
In the past Primal Surfacing had experienced issues with some modified binders not retaining consistent viscosity levels when transported over long distances.
“If a product settles then some sections of it can have high viscosity and some will have lower levels which can result in inconsistent pavement performance,” he says.
“So far with this new binder we are really happy with the outcome. It is so important for blended binders to keep their consistency over long distances.”
As for its performance on spray seal sites, Mr. Bartlett says the OBV production unit coupled with the low viscosity binder achieved appropriate binder lateral distribution, immediate aggregate grabbing and overnight retention and a significant decrease in the use of kerosene.
“The binder doesn’t contain any kerosene, so we won’t see any flushing or bleeding. Because we got immediate aggregate retention when interacting with the binder all the signs are there to suggest it will perform well long term,” he says.
“This binder will end up being Primal Surfacing’s product of choice on future projects all because we can achieve the appropriate level of fanning out of the jet, lateral distribution and its environmentally friendly.”