
3 minute read
U-Trough beams
LEVEL CROSSING INNOVATION
ROADS & INFRASTRUCTURE SPEAKS TO NVC PRECAST ABOUT THE BENEFITS OF USING PREFABRICATED CONCRETE U-TROUGH BEAMS IN AN AUSTRALIAN FIRST ON A LEVEL CROSSING REMOVAL PROJECT.
The Level Crossing Removal Project will see 75 level crossings throughout Melbourne removed by 2025 in order to increase safety, reduce travel times and better connect communities across the city.
So far 29 level crossings have been removed and completed across Melbourne, including one at Skye Road in Frankston.
For the first time in Australia, the Level Crossing Removal Authority, principle contractor, designers, engineers and NVC Precast worked together to deliver the elevated rail using prefabricated concrete U-Trough beams.
The design of the Skye Level Crossing Removal used 24 prefabricated concrete U-Trough beams, that were over 6 metre wide, 30 metres in length and weighing an impressive 280 tonnes to construct the rail bridge using Rapid On-Line Construction techniques. This reduced the rail occupation period and sped up the overall construction of the project for the benefit of the community.
NVC Precast were chosen to manufacture the U-Trough beams based on their experience in precast and the L-Beams used for elevated rail for level crossing removal.
NVC Precast were able to manufacture and store the beams at their precasting facility in Kilmore Victoria, coordinating delivery to arrive just in time to be erected on site.
The U-Trough beams were produced by stitching two precast concrete L-beams together which were between 25 and 31 metres long with masses up to 120 tonnes each, creating a single unit that weighted up to 280 tonnes.
The project involved extensive planning to create the forms and casting beds for the manufacture of the beams, the plant to transport them to site, and to create the infrastructure for the stitching and loading at the precast yard.
NVC Precast Construction Manager oversaw the casting of the L-Beams and the process for the stitching of the U Troughs which took four weeks to complete in April 2018.
NVC Precast manufacture up to four L-beams at a time casting 140 to 160 m3 to produce 12 L-Beams per week. To create a single segment U-Trough Beam, 50% of
The L-Beams were positioned to be stiched out in the yard.
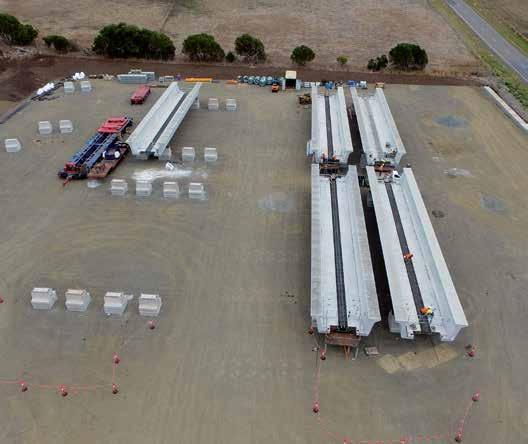
The U-Trough beams were positioned by stiching two precast concrete L-beams together.
the L-Beams were rotated 180˚, matched positioned on pedestals for the joining stitch to be cast. The rotation and match positioning was achieved using GPS guided SPMT and 80 tonnes Portal Gantry Cranes for the final touches.
The U-Trough beams were stored at NVC Precast’s Kilmore site before transporting to site and final installation into the elevated rail viaduct.
NVC Precast had to ensure that the load out facility it constructed allowed for 2 No. 12 axle Platform trailers to be accurately positioned under the 280-tonne segments for loading and chaining down.
Mr. Bell says the recent redevelopment of the NVC Precast site has created plenty of storage area for both storage and ancillary works such as painting, attaching hand rails, barrier rails and temporary walkways.
“This allows us to work closely with our clients to provide both precast concrete elements and solutions to some of the common construction problems, such as working at heights,” Mr. Bell says.
“As you are working beside a live rail line, rail upgrade requires closing the rail line every time you want to install the beams, which causes major disruption to rail traffic. With the L beams joined as U troughs off site, you take all the construction activity related to splicing off site and do it when the rail is still open. Then you can close the rail for significantly shorter periods just to install the complete U trough beams.”
Mr. Bell says the U-trough is a very
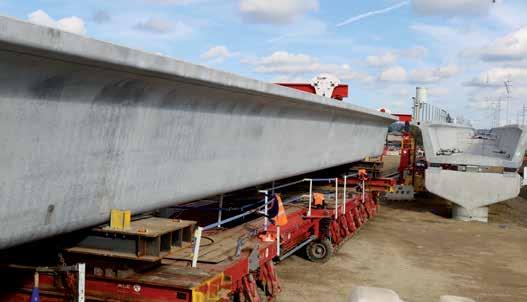
efficient design as the trains operate within the walls of the beams which provides a much lower profile and is more aesthetically pleasing elevated structure.
“The offsite fabrication of the U Trough beams for the Skye project was a great initiative by the main contractor and provided many benefits to the overall onsite construction process, through the benefits of both off site precast techniques allowing rapid installation, great quality control, a reduction in the overall construction footprint, and eliminated a lot of safety issues.”