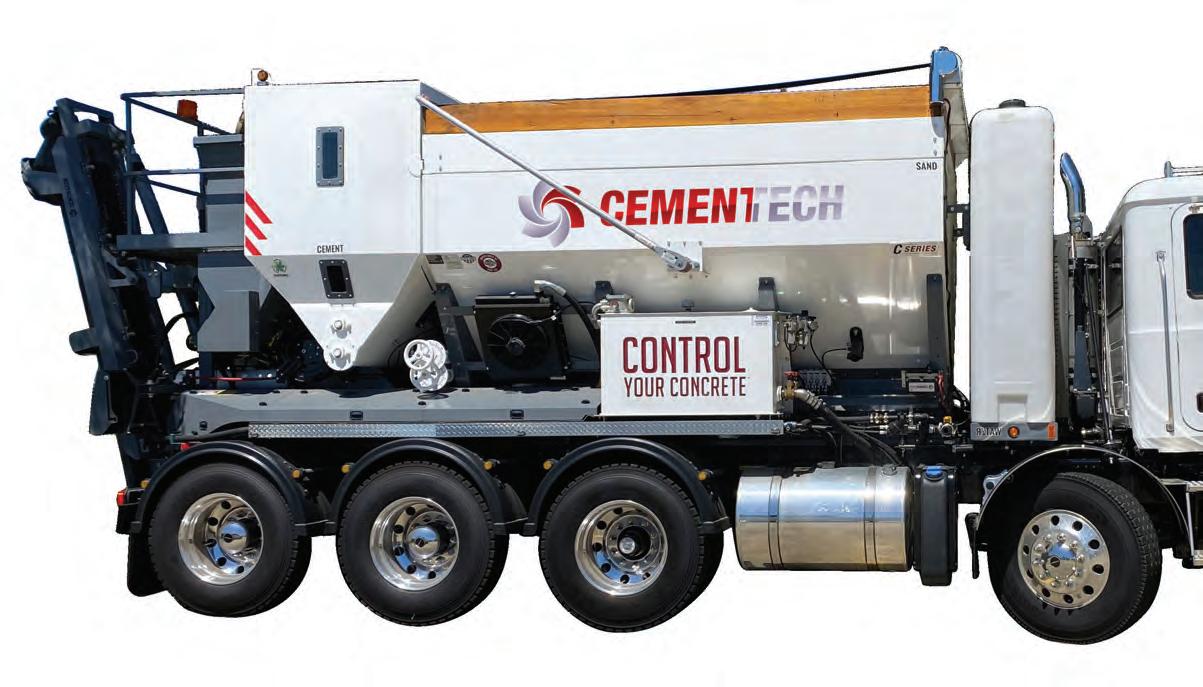
4 minute read
Taking control of the concrete mix
ANTEC’S VOLUMETRIC CONCRETE MIX TECHNOLOGY ENSURES QUALITY CONCRETE, WITH ACCURATE BATCHING, IS PRODUCED RIGHT ON THE CONSTRUCTION SITE. JON COLES, ANTEC’S GENERAL MANAGER – CONCRETE EQUIPMENT DIVISION, EXPLAINS FURTHER.
Pre-mixed concrete has long enjoyed a spotlight as the preferred method of transporting concrete to construction sites. And with advantages too. The economics of being able to produce concrete in large volumes at a batching plant and shipping it to the pour site in barrel trucks has often convinced project managers it was the better option compared to site-mixed concrete.
But with batched concrete, comes certain challenges – most notably a lack of control on the consistency of the mix, particularly with transit times and potential site delays having an impact on concrete quality. Now, an innovative concept, the Volumetric Concrete Mixer, is offering the best of both worlds to construction projects.
By storing all of the concrete’s
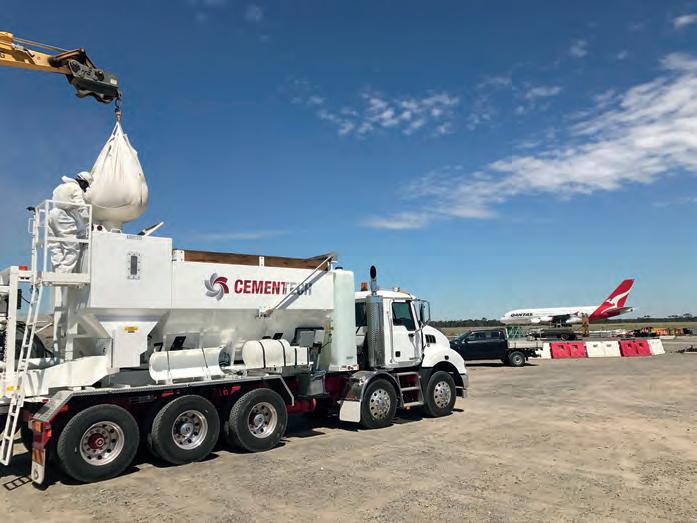
The Volumetric Concrete Mixer is ideal for road repairs using quicksetting concrete.
The Cemen Tech Volumetric Concrete Mixer from Antec is a batch plant and mixer in one.
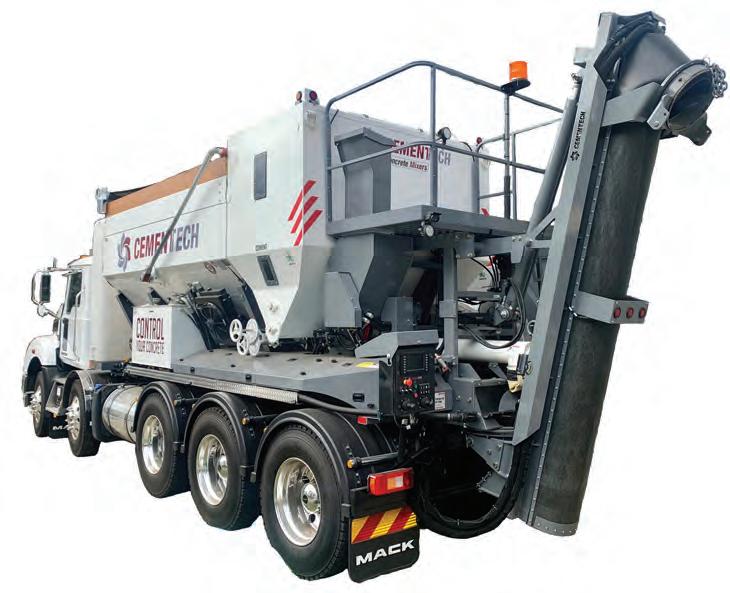
constituents in separate compartments on a truck and mixing them with preprogrammed volumetric ratios on site as per the batch requirement, the technology helps produce fresh concrete with every pour, and with precise mix design.
Antec is a pioneer in introducing Cemen Tech’s Volumetric Concrete Mixer technology to the Australian market. Antec’s General Manager for the Concrete Equipment Division Jon Coles says there are multiple advantages to using Volumetric Concrete Mixers.
“Self-reliance is a big factor that our customers seem to enjoy,” he tells Roads & Infrastructure. “By having a mobile mixer, you have full control on the quality of your concrete and when it’s delivered. You can produce different concrete grades with the one mobile unit. By simply adjusting the parameters on a menu, you can change the mix ratios and pour a different concrete mix for different sections in your project.”
This also comes with environmental benefits, as Coles explains further.
“In large roads and infrastructure projects, you often need to set up a batch concrete plant on the site. But instead of setting up a large mixing plant, you can use two or more Volumetric Concrete Mixers and feed the project with fresh concrete, without all of the environmental controls and expenses in setting up a batching plant,” he says.
“Another key advantage is that there “BY HAVING A MOBILE MIXER, YOU HAVE FULL CONTROL ON THE QUALITY OF YOUR CONCRETE AND WHEN IT’S DELIVERED. YOU CAN PRODUCE DIFFERENT CONCRETE GRADES WITH THE ONE MOBILE UNIT. BY SIMPLY ADJUSTING THE PARAMETERS ON A MENU, YOU CAN CHANGE THE MIX RATIOS AND POUR A DIFFERENT CONCRETE MIX FOR DIFFERENT SECTIONS IN YOUR PROJECT.”

is no wastage. You don’t have to carry a full load of mixed concrete in a barrel and then have to dump the excess on the ground somewhere. Because you are mixing the water on site, there is less water used in the concrete mix and less water required for washing out the mixer.”
Quick-set concretes in particular are a notable application for the Volumetric Concrete Mixer. Coles recalls an example where one Antec customer used the Volumetric Concrete Mixer with advantages.
“Our customers were doing a road repair where they used a fast-setting cement, which goes off very fast; so, having it delivered by a barrel truck wasn’t feasible. Volumetric Concrete Mixers are a really good option for such a situation because they can just mix the concrete on site as it’s required, then wash the truck very quickly and the road is back up and running in a matter of hours. They just do the concreting overnight and by the morning it is ready to drive on.”
Antec’s Volumetric Concrete Mixers are available in different sizes, and with different degrees of computerisation.
Antec’s Volumetric Concrete Mixers are available in different sizes, and with different degrees of computerisation. Coles says the larger models, namely the M30, M60 and C60 are the most popular in the roads and infrastructure sector.
Where Antec’s service offering makes a difference to customers is also through spare parts and technical support.
Antec’s team receives the units from the US manufacturer and assembles them onto trucks at Antec’s Blacktown facility in Sydney. This allows the team to incorporate some level of customisation as per customers’ requirements and to ensure compliance with the Australian heavy vehicle standards.
“Our spare parts holding adds to the reliability factor of our Volumetric Concrete Mixer units. We have all of the critical and consumable spare parts for the Cemen Tech machines in stock and our technical support is available 24/7 to respond to any customer queries. Antec has 13 branch locations nationally with parts holding capability,” says Coles.