
17 minute read
Simex Planer
SIMPLE EFFICIENCY
WITH SIMEX
Simex Planers are well suited to small and medium works.
Time is always of the essence when it comes to road building. Regardless of whether you are shutting down a council road through the middle of town or a major motorway linking two cities, road restrictions from construction are expected to be as minimal as possible.
This expectation can lead asset owners to implement penalties if timing is not met and roads have to stay shut longer than anticipated.
Local Queensland contractor All Whitey Profiling is involved in asphalt profiling and earthmoving projects and Owner Darrel Whitey has witnessed the effects of project delays during his time in the industry.
“Ten minutes can be like an hour to asphalt experts, if there is any way for you to make your works quicker and in turn better prepare the job for its next stage, that is worth its weight in gold,” Whitey says.
When searching for a new asphalt planer, Whitey was given a few good recommendations for the Simex Planers and decided to view one in action, on site.
“I managed to see the planers working on various sites with a couple of other companies and the practicality of them was really second to none. I knew that if I was going to buy a planer it would be the Simex,” Whitey says.
The Simex Planers, distributed through supplier Queensland Rock Breakers, are a two in one machine which is able to perform both milling and stabilising applications for the complete rehabilitation of roads and streets.
With a maximum width of 1500 millimetres and a milling depth of 350 millimetres (depending on model), the Simex Planers are well suited to small and medium works and are especially suitable in tight areas and around potholes or kerbs.
“We do asphalt patches up to 200 millimetres and we can do asphalt key ins with the planer. We can cut up to and against kerbs and in and around traffic islands. A key feature of the machine is that you can adjust the side plates to go up against objects, which is a huge benefit for asphalt contractors,” Whitey says.
Craig Einam, Queensland Rock Breakers Sales Area Manager, says the ability to get closer to manholes and kerbs is one of the big advantages of the planers.
“With the Simex Planer you can get a lot closer to these objects and that removes some of the manpower and other equipment like jack-hammers that might be required. All the people that use these planers love the fact that the machine can do a lot of the work for them,” Einam says.
The Simex Planers are also self-levelling, which helps the operator to ensure consistent milling depth regardless of any surface discrepancies.
Another feature Whitey says is impressive for asphalt contractors, is the left and right SIMEX PLANERS WORK TO INCREASE EFFICIENCY ON ROAD PROFILING JOBS BY PERFORMING MILLING AND STABILISATION WITH DEPTH CONTROL FEATURES. ROADS & INFRASTRUCTURE FINDS OUT WHY IT’S THE UNIT OF CHOICE FOR ALL WHITEY PROFILING.
depth control capability.
Independent depth control on either side of the planer can create sloped surfaces. When paired with the self-levelling feature and the traverse tilt system this ensures there are no height differences in the final product even if a project begins with uneven ground.
“We’re are also able to get into tighter situations behind traffic islands. Being compact, means you are not restricted by a big unit. I was shocked at how smooth and efficient the machine is and the accuracy of the final cut we get,” Whitey says.
Simex Planers are also designed with a built-in water tank and pump which reduces any dust produced during milling operations.
“Profiling has seen large growth in the last 12 to 18 months, with our operating and safety benefits we see the Simex Planer as being really favourable in the industry,” Einam says.
“Time really does cost money and many of the features on the Simex Planer work to make applications more efficient on site, helping to keep projects on time and budget.”
Simex Planers are available across the country throughout the Simex dealership network which includes; Walkers Hammers in VIC and TAS, Groundtec in NSW, QLD Rock Breakers in QLD and NT, Total Rockbreaking Solutions in WA and Renex Equipment in SA.
MATTHEWS BROTHERS:
A JOURNEY OF ROADS AND FAMILY
An early spraying machine.
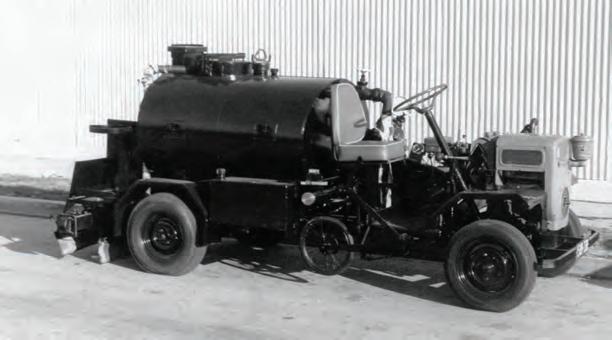

An early Latland 6x4 sprayer.
MATTHEWS BROTHERS ENGINEERING WILL REACH ITS CENTENARY YEAR IN 2021. ROADS & INFRASTRUCTURE SPEAKS TO THE THIRD-GENERATION FAMILY OWNER OF THE BUSINESS TO DISCUSS THE EVOLUTION OF THE AUSTRALIAN OWNED AND OPERATED ORGANISATION.
Paul and Noel Matthews.

The early 20th century was pivotal for Australian road making and transportation. According to the Australian Bureau of Statistics most roads outside country towns were unsealed right up until the late 19th century.
It was only in 1913 that the first road department in Australia was established, the Country Roads Board in Victoria. This was closely followed by the Main Roads Commission in Queensland and the Main Roads Boards in New South Wales and Western Australia throughout the 1920s.
The early 20th century saw increased technological innovation for road building in Australia with the large-scale development of bituminous pavements and the binding of local gravels with tar and bitumen.
At this time, in 1921, Vic Bradley and Roy Matthews opened a site to mine and transport blue stone from a quarry that was located close to a site they opened on Mason Street just out of Melbourne.
From there, Matthews Brothers Engineering was born and over time the two owners turned to engineering works and secured a contract to supply torpedo heads and mortar bomb casings to the army.
The business then evolved to create affordable and innovative road construction equipment and was eventually passed on to Roy’s sons, Noel and Ray Matthews.
The businesses first introduction to creating road making equipment was for the Victorian Country Roads Board, where they supplied a number of small 130-gallon bitumen kettles. This pivoted the company towards bitumen spraying gear.
After the passing of Noel in 2018 and Ray in 2020, Matthews Brothers Engineering is led by Roy Matthew’s Grandson, Paul Matthews, and is a road construction equipment manufacturer heading into its centenary year of operation.
Working out of its purpose-built facility and manufacturing plant in Altona North, the Australian owned and operated business alongside its rental division, Flindane, continue to grow.
Owner Paul Matthews, started as an auto electrician when he was 18, he then became foreman of the Mason Street site and moved with the business to Altona North to oversee the new facility before becoming Managing Director of the business in 2019.
“When I started out there were two buttons on the sprayers and everything else was mechanical. To improve this technology, I did an electronics course and started to build control panels from there to make the
machines more efficient and easier to use for the operators,” Matthews says.
This legacy has lasted through generations of the family through to 2020 where Matthews Brothers is a well-established manufacturer of bespoke bitumen tankers and spray seal equipment.
“We have got the ability to take a raw truck chassis’ and transform them into state of the art, bitumen sprayers,” Matthews says.
“Around 90 per cent of the gear on our spray seal machines is made in house or from one of our local suppliers. We’ve got proprietary pumps, valves and equipment that can’t be bought off the shelf elsewhere, simply so these components can work in excess of 200 degrees, sometimes for days on end.”
One of the most recent innovations from the Matthews Brothers team is their Guaranteed Target Application Rate, or G-TAR. This system is an optional upgrade on Matthews Brothers Sprayers and is designed to assist the operator to achieve efficiency while upholding safety on site.
G-TAR is an automated system, which is operated through a touch screen control panel, to simplify operation of the sprayer systems while achieving consistency of application.
Amongst the team at Matthews Brothers there are two electrical engineers dedicated specifically to the assembly of intricate control panels and automation solutions such as G-TAR to advance spray seal operations.
The design department has hand drawn diagrams of early equipment showcased on the walls of the office, while the current team utilise state of the art parametric modelling software helping to keep Matthews Brothers at the forefront of design technology.
The same level of detail is upheld for Matthews Brothers mechanical components, with the company developing nearly 10 different types of spray bar valves over the years.
“We have always, and will continue to, strive towards the next innovation or improvement that is going to make a difference for contractors. Research and development play a huge part in the business, it’s important for us to understand what the industry is looking for and deliver,” Matthews says.
“With each truck we create we are eager to make changes and improvements for the client so that the next truck is always
Matthews Brothers Engineering’s 14,000 Litre sprayer.
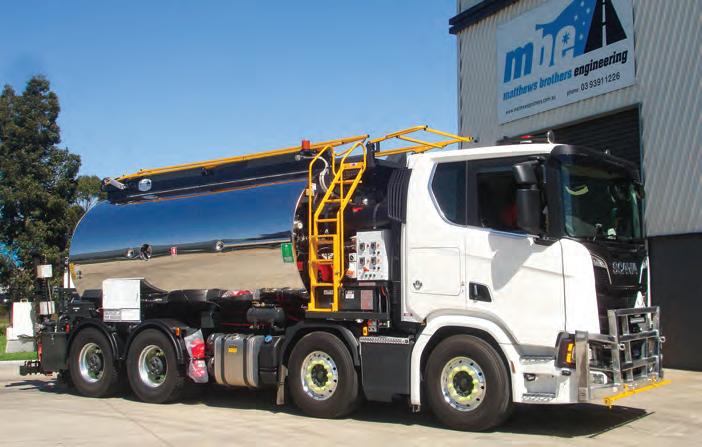
better than the last. If a client has ideas and provides feedback, that is taken on board so that we can continually improve.”
One thing the Matthews team has observed in the industry is the movement to minimise the use of kerosene to improve environmental outcomes.
“Our Forward Motion Chipsealer has features which help minimise the use of kerosene, meaning the operator doesn’t have to flush out the piping system” Matthews says
“This same technology is now being developed within a new prototype which we hope may even remove the need for cutting agents which are sometimes added to the bitumen”.
Because the business manufactures such a large proportion of the parts used on the spray sealing units, replacement parts and technical support for the machines is second nature.
“We really understand the equipment we are building and how it works in the field. We have a pool of people that know how to use each of these products and parts and how to repair them. Most repairs can be done over the phone or quickly resolved by sending the correct replacement part,” Matthews says.
“Quick resolution of technical issues is crucial when you have a team of workers standing by and waiting for a machine to be ready so that works can continue. We know these products inside out so can often fix them quickly.”
This year, Matthews Brothers are producing their first 14,000 litre, twin-bar, bitumen spraying unit featuring their G-TAR Maxi control system. Matthews Brothers have worked closely with Scania to optimise interface with the trucks systems, though things can be tailored to suit Mercedes Benz, M.A.N., Volvo and Isuzu chassis’.
Once complete the unit will take its place as the new flagship model of the entire sprayer range.
Looking ahead to the next 100 years Matthew’s excitedly finds it hard to picture the extent of just what the company could achieve.
“A lot of our staff members have been here over 20 years and the ‘family’ aspect of the business goes much further than the Matthews’ family. It encompasses all of the people here, working together to improve,” Matthews says.
“I’m sure if you had told Roy Matthews where we would be today, he would be amazed. The main thing we know is that the nature of the business is to strive for improvement and we just want to get better and better from here.”
Rear view of a Matthews Brothers Engineering spray unit.

PRODUCTIVITY
IN THE FAST LANE
GUIDESIGN VERSION EIGHT HAS BEEN RELEASED IN AUSTRALIA THIS MONTH, WITH A MULTITUDE OF UPGRADES AND NEW FEATURES TO FACILITATE SIMPLE, FAST DESIGN OF ROADWAY AND HIGHWAY SIGNS OR MARKINGS.
The latest version of Transoft Solutions’s specialist road signage software, GuideSIGN version eight is now available across Australia pushing sign creation into the fast lane.
Transoft has developed innovative and easy to use software for transportation professionals since 1991. Transoft’s engineers work closely with the world leading agencies including Austroads to develop its specialised applications. GuideSIGN uses Computer Aided Design (CAD) software to create road and highway signs that meet Australian specifications within minutes, saving time and money for engineers on many projects. Version eight is available as the basic GuideSIGN product for sign design and in addition Transoft Solutions released GuideSIGN Plus featuring a sign planning module and pavement marking module.
The original GuideSIGN module for sign design has seen upgrades to Australian specific content and general improvements to usage. For version eight, Transoft Solutions focused on GuideSIGN Plus which includes significant upgrades to the sign planning module and a brand-new module for pavement marking. This module was enabled through Transoft Solutions’s acquisition of the British company Keysoft Solutions.
Wesley Butler, Civil Technologist at Transoft Solutions, says the sign planning software has been revamped to be a threedimensional tool.
“Now you can take the signs you have created in sign design and view them in the sign planning module in a 3D format. You can also take standard signs from the library and view them in a 3D environment,” he says.
Sign planning also features a new system for the customisation of labelling, which can be designed to relevant standards. In future versions, this system will be the beginning of enabling the export of these designs to a Geographic Information System (GIS) format.

“We have also created sign plan templates which allow the user to place several signs at the click of a button in a common scenario. For example, if you are working on an intersection you can place all of the signs that are relevant to that area with one click,” Butler says.
For the new pavement marking module, Transoft Solutions has integrated this with the sign planning software. These can be used at the same time, in the same program, to implement all traffic lines, arrows or text needed on a roadway. GuideSIGN software is created to facilitate design efficiency using a panel style approach. When creating a sign, the user begins with a blank panel based on the standards required and this is populated with the text and symbols needed.
In the sign design module, Transoft Solutions has a library of panel styles that are based on the AS1743: 2018 Australian standard. For sign planning there is also a basic library of signs that adhere to the 2018 Australian standard, and for pavement marking the content is also created to Australian specification. Pavement marking also includes some of the unique New Zealand standard designs.
“Because the software is geared towards Australian standards, this means you don’t really have to know the standards inside out. A user can simply drag elements around
An example of Transoft’s sign and road marking software in action.
and follow the prompts given by the system which will alert them if something is not to standard,” Butler says.
“The standard prompts are automated, making it easy to design an accurate sign that meets specification. But this can also be avoided using manual overrides if the user is looking for a more advanced application.”
Sign design is customisable so any of the arrows or symbols created in the software can be adjusted for alternate applications.
“Recently we created signs for social distancing in GuideSIGN, these did not need to adhere to road standards as we were communicating to pedestrians not drivers. The software can be completely flexible for applications such as this,” Butler says.
There are three different modules as part of the GuideSIGN version eight release, Sign Design, Sign Planning and Pavement Design.
All three modules are included under GuideSIGN Plus. The basic sign design module is purchased under GuideSIGN and finally the sign planning and pavement design modules are available separately under a package called SIGMA. Transoft Solutions can work with each user to design a licencing or purchase package that suits the needs of each project, whether that be for smaller or larger organisations.
MOVING FORWARD INTO SPRAY SEALING SEASON
ROADS & INFRASTRUCTURE SPEAKS TO QUALITY FABRICATION AND ENGINEERING, THE COMPANY BEHIND THE DUAL CONTROLLED FORWARD MOVING AGGREGATE SPREADER, THE Q-FE ROAD ANT, AHEAD OF THE 2020/21 SPRAY SEALING SEASON.
The Victorian spray sealing industry is inching closer to the VicRoads deadline which will mandate the compulsory use of forward moving aggregate spreading trucks for all VicRoads sprayed sealing works from 1 July 2022.
With Glenn Hardiman at the helm, the Quality Fabrication and Engineering (Q-FE) team have developed the Q-FE Road Ant, an innovative dual controlled forward moving aggregate spreader that meets the VicRoads mandate.
With just over two years to go and the 2020 spray sealing season getting into full swing, contractors are trialling and acquiring new equipment that will meet this mandate.
Q-FE debuted its first Q-FE Road Ant in early 2020 and the vehicle has been of keen interest to the market with a number of orders already been taken and completed units carrying out demonstrations to many in the industry.
“We’ve made the Q-FE Road Ant operator-friendly and with exceptional vision of the work site and spreading area, we’ve had safety and practicality at the forefront of our design,” Hardiman says.
“We wanted the machine to be easy to adopt so the process for operation is similar to what has been seen in traditional spray sealing units.”
As the spray sealing season lasts for about six to eight months of the year, the Q-FE team designed the Q-FE Road Ant to be able to carry out other work. The unit has been designed to accept standard Trout River attachments which gives it the versatility to be used year-round.
David Lockwood, Q-FE’s Head of Sales, says he’s seen interest from national and state-based spray sealing companies right through to smaller contractors.
“We were involved in an Australian Asphalt Pavement Association meeting recently and they were really excited that we have been able to come so far with the machine and that we can supply a truck that meets the mandate,” Lockwood says.
Since the debut of the Q-FE Road Ant the team has continued to fine tune the vehicle hydraulics and sub conveyor system.
“We’ve learnt that industry does have challenges with spreading the 20 millimetre aggregate, so we have made changes to handle the larger rock. Overall the machine has evolved into something that is easy to operate,” Lockwood says.
To date, the Q-FE Road Ant has been built on 6x4 and 8x4 cab chassis. A compact short wheelbase unit is currently being built to suit the difficult to access ‘small areas’.
Q-FE are proud to build a forward moving aggregate spreader that can be customised, for specific cab chassis, and to date they have built them for Isuzu, Iveco and DAF chassis.
Hardiman acknowledges that local manufacturers and parts suppliers have always been an important consideration for the Q-FE team.
“At the beginning we had a good idea of what we wanted to do but we leant on the experience and knowledge of these local suppliers, to turn the Q-FE Road Ant into what it is today.”
“For example, Power Transmissions in Bayswater have created unique electric motors for our auger drives which are terrific, and Reverse Smart who helped develop our dual emergency braking system,” Hardiman says.
During the COVID-19 pandemic, Q-FE were confronted with a number of challenges from overseas sources, and Hardiman is proud that the local manufacturers were
The Q-FE team has seen keen interest in the Road Ant ahead of the 2020/21 spray sealing season.

able to come to the party.
Using local parts and components also has an advantage in the repair or maintenance stages with machinery, as Q-FE will often be able to source parts from within Australia or Melbourne without the need to wait for overseas shipments.
The new Q-FE website is now live to help spread the word about the Q-FE Road Ant and other solutions that Q-FE offer, including their robust road brooms and aggregate loaders, where they have two ground up loader builds under way. For more information visit: www.qualityfab.com.au or email sales@qualityfab.com.au