
7 minute read
Back to basics
AN INNOVATIVE APPROACH TO ROAD REHABILITATION
Pavement Recyclers were subcontracted to undertake pavement rehabilitation as part of the Northbourne Avenue upgrades in Canberra.
PAVEMENT RECYCLERS, A SUBSIDIARY DIVISION OF STABILISED PAVEMENTS OF AUSTRALIA, IS CENTRED ON PROMOTING THE ENVIRONMENTAL AND SUSTAINABILITY BENEFITS OF REUSING AND REJUVENATING EXISTING PAVEMENT MATERIALS FOR ROAD REHABILITATION. ROADS & INFRASTRUCTURE REPORTS.
Driven by a commitment to keep the Australian pavement recycling industry at the forefront of global innovation, one Australian company is setting examples by making the most of existing resources through a sustainable insitu road recycling process.
Stabilised Pavements of Australia (SPA) is an Australian-owned company that has become a leading specialist stabilisation contractor in Australasia. Commencing in Australia in 1984, the company has been providing road recycling services for local government and state road authorities, non-council and private customers and has expanded overseas to operate internationally.
In early 2020, SPA launched a new subsidiary division called Pavement Recyclers to specifically focus on delivering Paver Laid Insitu Recycling – a technique based on rehabilitating the existing road pavement materials onsite, using the Wirtgen 380 (W380) Cold Recycler from Germany.
A first of its kind in Australia, Pavement Recyclers’ operations occur in just one pass of the forward moving train, including milling, recycling, material management and placement. Alongside many improved
features on current conventions, the single pass, paver laid aspect is a key difference compared to other recycling methods used in Australia.
General Manager David Berg says by introducing the brand Pavement Recyclers, the company aimed to bring attention to the significance of this latest development in the road rehabilitation industry.
“Stabilisation is used worldwide to improve the engineering characteristics of pavement material and is frequently selected by road asset managers because of the sustainability benefits that are often relied upon when pavements are in urgent need for rehabilitation. Pavement Recyclers’ new plant and process delivering recycled pavements is a game-changer as it improves the efficiency of the process. The new brand was a way for us to emphasise that recycling of pavements is what stabilisation is. A fundamental benefit of the process, essential for many of Australia’s rural roads where shoulder failures are prominent, is that the Wirtgen 380 Cold Recycler allows Pavement Recyclers to simultaneously widen the roads while rehabilitating them,” Berg says.
“The recycler machine showcases a full working width of 3.8 metres. When paired with the paver screed capable of extending even further, this allows recycling to occur, depending on the project, in a single pass across full lane widths, multiple lanes or with simultaneous shoulder widening. The machine also doubles up as the world’s largest profiler,” he adds.
USING GEOTECHNICAL ENGINEERING PRINCIPLES For Pavements Engineer Davina Smith, rehabilitating existing road pavement materials is the ideal process to achieve sustainable pavement solutions, supported by basic and fundamental geotechnical engineering principles.
“Why import new materials when you can recycle the road that’s already there?” says Smith.
“So far, the most popular type of Paver Laid Insitu Recycling treatment used by Pavement Recyclers has been Foamed Asphalt, which uses foamed bitumen technology,” says Smith.
“The reason we have been predominantly using Foamed Asphalt treatment is because the foamed bitumen technology, used to recycle existing pavement materials, is most comparable to deep lift asphalt pavements in terms of thickness and performance. Deep lift asphalt pavements are well known in the mainstream, but by providing a more sustainable alternative that is focused on working with the available pavement materials, we are hoping to assist road authorities meet their sustainability targets, encompassing cost savings and environmental benefits,” she adds.
According to Smith, Pavement Recyclers can recycle a range of common pavement materials relevant to the Australian context, including granular materials such as gravels and sands, asphalt and even small portions of clay that make their way into the mix.
“It is a matter of being able to understand and apply geotechnical engineering principles to determine the suitable mix designs (blend of binders) and provide adequate quality assurance to verify results in the field.”
In the near future, Smith says Pavement Recyclers aims at introducing to Australia technology for 100 per cent asphalt pavement recycling, all done on site using the Paver Laid Insitu Recycling process.
“This is already occurring overseas on major highways and freeways using the Wirtgen 380 Cold Recycler. Pavement Recyclers is undergoing the necessary research and development, and consultation with authorities to bring this exciting prospect to Australia,” she says.
Moreover, Smith says Pavement Recyclers’ passion for environmentally friendly road recycling is supported through the cold recycling process, which eliminates the need for heating the road pavement mix, with obvious safety and environmental benefits. She says this is an advantage over conventional hot mix and warm mix asphalts.
NORTHBOURNE AVENUE PAVEMENT REHABILITATION IN CANBERRA The full benefits of Pavement Recyclers’ unique paving technology were well demonstrated at a recently delivered project in Canberra, where Pavement Recyclers worked for head contractor Woden Contractors on rehabilitating two critical sections of Northbourne Avenue.
The first phase of the project included rehabilitating a 1.3-kilometre section of the northbound carriageway between Macarthur Avenue and Mouat Street. The original project plan of using standard methods of pavement rehabilitation would have taken approximately 26 weeks to complete. However, by using the alternative Foamed Asphalt process, the project took just six weeks.
An internal sustainability assessment concluded that approximately 6100 tonnes of existing pavement material – which would have otherwise been excavated
Pavement recycling and widening at Bundeena Drive, Sutherland Shire Council.
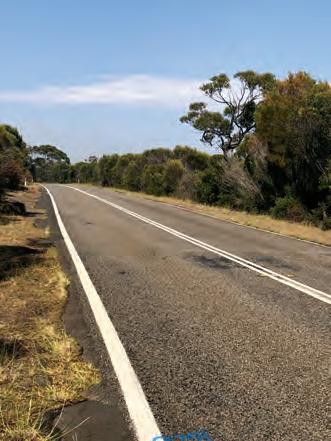
BEFORE AFTER
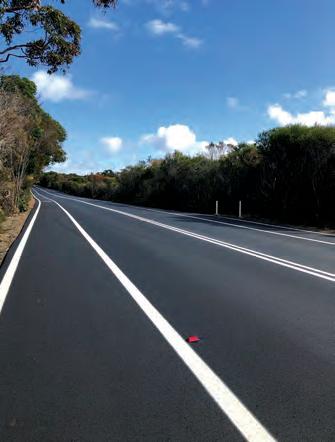
Pavement Recyclers recently installed a Trimble Universal Total Station on its W380 Cold Recycler.
and discarded before replacing with deep lift asphalt – was instead treated with Foamed Asphalt and recycled on site. This consequently reduced the need for new imported materials to site by approx. 70 per cent.
Along with a twenty-week reduction of the impact on traffic during construction, this resulted in up to 40 per cent cost savings and a reduction in greenhouse gas emissions (measured in Carbon Dioxide Equivalents) of approximately 61 per cent.
The second phase of the project between Antill Street and Wakefield Avenue commenced in June 2021 and was completed the following month. Here, Pavement Recyclers worked for head contractor Woden Contractors again to rehabilitate another section of the northbound carriageway, spanning a length of approximately one kilometre across three lanes and a cycle lane.
Similar to stage one, the structural layers of the pavement were simply the existing road materials that were recycled into an improved pavement. For stage two, approximately 4000 tonnes of existing pavement materials were treated with Foamed Asphalt recycled and renewed, rather than excavating and replacing with new asphalt.
The project completion date was reached in only five weeks, ahead of the project deadline. Notably the rehabilitation works on just under 9000 square metres of pavement took only four days to complete. This was achieved despite the cold and wet weather events during the construction period.
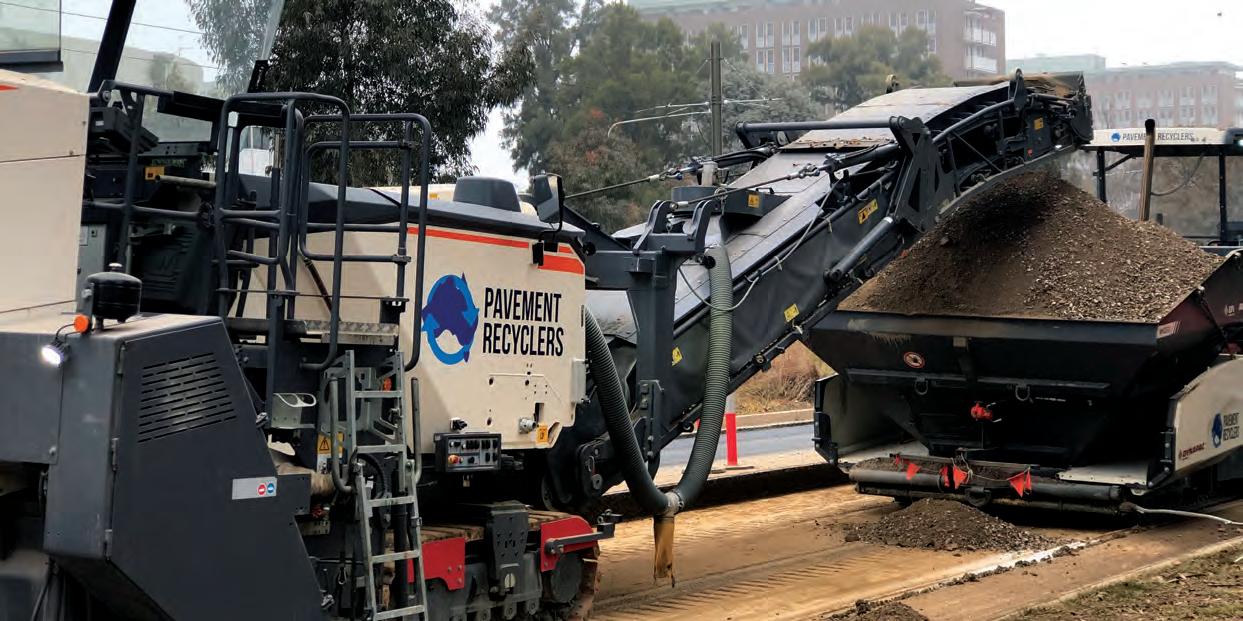
AN OVERLOOKED RESOURCE With the undeniable benefits of insitu pavement recycling, Berg says Pavement Recyclers is proud of their ongoing contribution to sustainable pavement initiatives, based on advancement in plant and machinery, geotechnical engineering and project management expertise.” “Whilst there have been creative concepts to increase the use of recycled materials in roads, Pavement Recyclers is centred on maximising the recycling potential of the most obvious, yet often overlooked, resource – the existing road,” he says
As one example of Pavement Recyclers’ continued advancements, a Trimble Universal Total Station (UTS) has now been installed on the W380 Cold Recycler, allowing millimetre precision in the operations.
“The UTS technology is typically associated with graders, and it allows the machine to work automatically to design levels created from the survey. With the Trimble system up and running on the W380 Cold Recycler, another string has been added to the bow. It is exciting to be able to show our clients another layer of sophistication to the already new innovative single pass, paver laid process,” Berg says.
“Beyond direct road rehabilitation services, Pavement Recyclers is also committed to going the extra mile with helping clients achieve their sustainability outcomes, including sustainability reports compiled on projects that quantitatively measure metrics such as greenhouse gas emissions and resource utilisation.”
For Berg and his team, being able to use their technology and their knowledge to assist asset owners recycle up to 100 per cent of their existing pavement material is very rewarding.
“If introducing a process and machinery never-before-seen in the country wasn’t enough, the initiative has sparked a golden opportunity to take the company’s vision for recycling roads a step further,” he says.
“With a single-pass process that recycles up to 100 per cent of the existing pavement material, with a clean, paverfinish, asset owners have the opportunity to revolutionise the way pavements are rehabilitated. Through this process, Pavement Recyclers can deliver pavements with structural integrity, environmental sustainability and economic savings.”