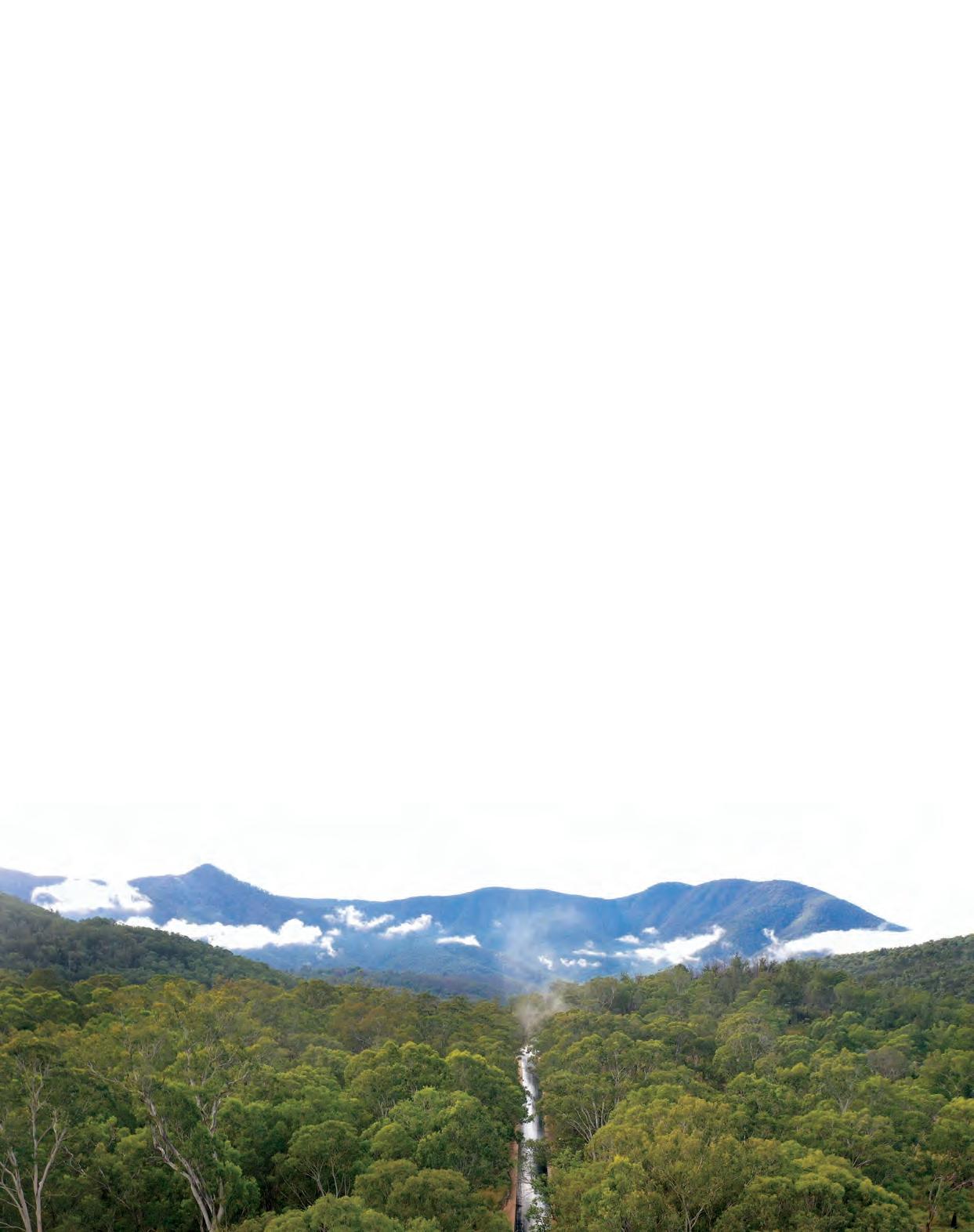
6 minute read
Embracing the benefits of high float emulsions
EMBRACING THE BENEFITS OF
H2 HIGH FLOAT EMULSIONS SAMI BITUMEN TECHNOLOGIES HAS RECENTLY DEVELOPED SAMIFLOAT, A CATIONIC INTRO HIGH-FLOAT THIXOTROPIC SPRAYED SEALING EMULSION. SAMI’S NATIONAL R&D AND LABORATORY MANAGER KANJANA YINDEE TALKS ABOUT THE PRODUCT’S BENEFITS AND POTENTIAL APPLICATIONS FOR AUSTRALIAN PAVEMENTS.
Xxx XxxDespite their many environmental and safety benefits, bitumen emulsions have traditionally not been the preferred method of sprayed sealing for Australian contractors, with hot modified binders currently dominating the field. But SAMI Bitumen Technology’s National R&D and Laboratory Manager Kanjana Yindee believes that could be changing soon.
One of the reasons bitumen emulsions have not achieved a significant penetration rate in Australia so far, she observes, is due to lack of confidence among contractors that they can provide the performance requirements.
“Unlike other countries, limited amount of emulsion has historically been used in sprayed seals in Australia. As the local industry migrates towards using more emulsion binders, the manufacturers should aim to provide high performing, user-friendly products, and we will need to retrain the crews in the construction practices to deliver high performing sprayed seals. Details such as whether we need to precoat the aggregates or whether we can just wash them with water are some of the issues to be addressed,” says Yindee.
“Using emulsion for sprayed sealing is more environmentally-friendly than using hot unmodified or hot polymer modified binders. The latter options require using a high percentage of cutters, sometimes up to six per cent or more, which is associated with emission of volatile fumes. So, using emulsion fits very well with the industry’s overall direction towards more sustainable sealing,” she adds.
To address these and other challenges associated with using conventional emulsions for sprayed sealing, the team at SAMI Bitumen Technologies have come up with an innovative product: a cationic high float rapid-setting emulsion modified with latex, known as SAMIfloat.
What makes the high float SAMIfloat binder different, Yindee explains, is its gellike structure of the binder, which offers better aggregate adhesion and prevents emulsion run-off, or bleeding.
“Unlike conventional sprayed seal emulsions, after the water evaporates, SAMIfloat leaves more than just the sprayed seal binder behind,” she says. “The gel structure allows a thicker binder coating on the aggregate particles. This thicker film prevents aggregate stripping and is more resistant to oxidation from exposure to the atmosphere.”
The result, Yindee explains, is more durable, better-performing sprayed seals.
“The SAMIfloat residue is resistant to flow at high road surface temperatures allowing for a softer bitumen to be used that will resist bleeding at high temperatures. The softer binder also does not become as brittle at low temperatures and resists stone loss. The thixotropic gel structure doesn’t flow at pavement surface temperatures, that’s why they tend to bleed less than other unmodified emulsions or cutbacks,” she says. SAMIFLOAT AND GRADED SEALS The concept of developing a cationic high float emulsion product, Yindee says, initially emerged when Trevor Distin, Colas Australia’s Technical and Marketing Manager, contacted Yindee looking for a cutback-free
The SAMIfloat emulsion is ideal for sprayed sealing applications, as it resists bleeding at high temperatures.
“QUOTE”
The test showing flow properties of SAMIfloat highfloat emulsion at ambient temperature (left) and after four days (right) sitting in the same conditions.
binder to use for constructing graded seals.
“Normally, sprayed sealing applications in Australia use single-graded aggregate, but Trevor had this idea to use a high float emulsion for graded seals to help him minimise the use of cutters. We knew this was done elsewhere in the world, but we also knew that our formulation had to be unique to Australia. While most countries use anionic high float emulsions, products used in Australia have always been cationic, so it was not practical to introduce an anionic emulsion here,” explains Yindee.
Working with her colleagues and counterparts across the global Colas Group, Yindee developed the cationic formulation, which has proven to offer the same benefits and properties as the anionic formula.
While Colas Australia is now planning to evaluate the performance of SAMI’s high float emulsion on one of their projects in New South Wales, Distin says he is very optimistic about the potential benefits.
“Graded seals require the binder to be sprayed at an application rate above 1.8 litres per square metre. The problem with standard sprayed sealing emulsions is that they have a tendency to run off the road when spraying them at these higher application rates. By using higher viscosity emulsions like SAMIfloat, higher net binder application rates can be sprayed especially in areas with steeper gradients without the risk of run off,” explains Distin.
“The use of high float emulsions will eliminate the need to spray hot bitumen cutback with kerosene to construct graded seals. This will reduce the amount of heating required to transport, store and spray the binder. High float emulsions are handled at much lower temperatures, so it reduces the risk of a person being burnt from the binder during handling and/or from an explosion,” he adds. A GLOBAL PERSPECTIVE Being part of the larger Colas family, SAMI Bitumen Technologies has also had access to shared knowledge and expertise across the Colas family when developing its latest innovation.
One expert whose technical input has helped SAMI’s team during the development of SAMIfloat is Tony Kucharek, Technical Director of Canada’s McAsphalt – another subsidiary of the Colas Group.
Kucharek says unlike in Australia, in Canada and in major parts of northern United States, sprayed sealing – or chip sealing as it’s called there – is predominantly done using emulsions.
“In Canada, there is no hot applied sprayed sealing. The concept of loading hot bitumen into a distributor and spraying it on the road is very foreign here,” he says. “This, to a great extent, is due to strict limitations around generation of VOCs, which also limits cutback usage for precoating chips.”
Drawing on the similarities between Canadian and Australian roads, Kucharek says SAMI’s high float emulsion binder could very well be a game-changer for the way roads in Australia will be sprayed sealed in the future.
“There’s similarity between Australia and Canada in that we both have large countries with areas that are sparsely populated. So, we must cover a lot of roads, majority of which are remotely located. They are not in areas where aggregate resources or paving materials are readily available. Emulsion-based graded seals, or sprayed seals, have proven to be very good solution for remote areas and areas with low traffic loading. For that matter, I don’t see any reason why SAMI’s solution wouldn’t work well for Australia,” he says.
Kucharek says across the global Colas Group, there have already been many successful examples of uptake for high float emulsions. In one recent project in the French Guyana region, the local road authorities successfully trialled high float emulsions for sprayed sealing for the first time.
“The project was a collaboration between Colas Canada, Colas France and Colas Guyana. The road was put down a year ago and there are indications that the local road authority would want to do more such projects,” he says.
So, when should Australia expect to have increased its adoption of high float emulsion binders and moved away from hot mix binders?
“The proof is always in the pudding,” says Kucharek. “SAMI has developed something that’s very new for Australia. What they are doing is very innovative. Once people see more projects that have used the technique, the contractors will start wanting to trial it too.”
That day might not be far away. Colas Australia has already planned to construct a trial section on an existing project alongside hot cutback binder to evaluate the performance of the high float emulsion graded seal under the same traffic and environmental conditions in Northern New South Wales. Distin and Yindee are confident the trial will confirm what they have already seen in laboratory test results.
“The goal for SAMI is to help reduce use of hot cutback binders in sprayed sealing and to contribute to more sustainable, more durable roads in Australia. We look forward to sharing the outcomes of Colas’ trial with the industry in the coming months,” Yindee concludes.
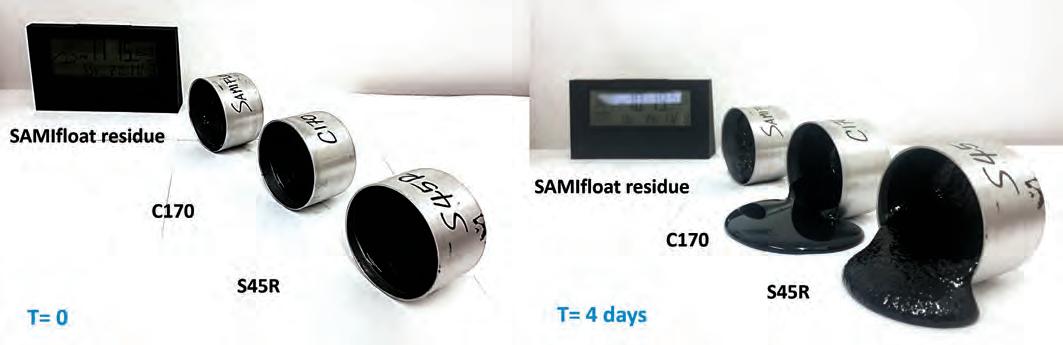