
3 minute read
Green cement
CEMENTING A CARBONNEUTRAL FUTURE
A CARBON-NEUTRAL CEMENT HAS BEEN DEVELOPED TO DRASTICALLY REDUCE EMISSIONS, BUT ITS POOR WATER RESISTANCE AND STEEL CORROSION PROPERTIES HAVE RESTRICTED ITS USE – UNTIL NOW.
In 2018, the BBC reported that the creation of cement is the source of about eight per cent of the world’s carbon dioxide emissions.
If the cement industry was a country, it would be the third largest emitter in the world, behind only China and the US, the article states.
In an attempt to reduce emissions from the sector, an alternative cement has been created known as MOC (magnesium oxychloride cement). This cement is made from mixing magnesium oxide (MgO) powder and a concentrated solution of magnesium chloride (MgCl₂).
A Chemical Review paper from ASC Publications by Sam A. Walling and John L. Provis at the University of Sheffield, UK found that the ingredient MgO offers a unique potential to develop carbon neutral, carbon-negative concrete or concrete products by absorbing carbon dioxide.
Significant challenges have been discovered when using MOC, such as its poor water resistance and its ability to corrode steel.
These hurdles have restricted the cement from being widely used in the building of structures, as steel is commonly used for reinforcement and outdoor structures will be attacked by water when raining.


For the past three years, researchers from the University of Western Sydney and UNSW have been developing MOC. The cement uses MgO as an ingredient and researchers hope the product will one day gain widespread use in the construction industry.
In the researchers’ latest breakthrough
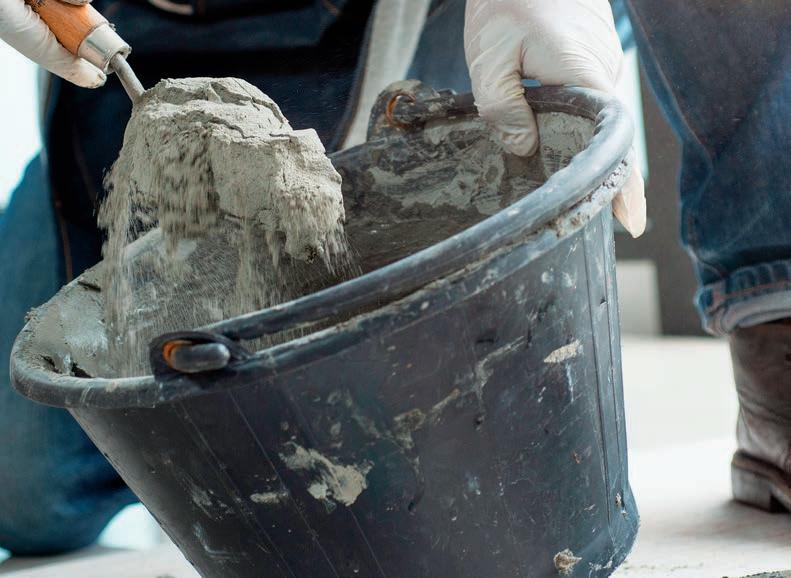
for MOC, full compressive strength was achieved by the material in water for 28 days. This proved the material’s water resistance.
Yixia (Sarah) Zhang, Engineering Associate Professor at Western Sydney University and team leader, says they first tried using fly ash, which significantly improved the water resistance of the cement.
The team then added silica fume and when all materials were combined, full compressive strength was achieved in room temperature water for 28 days.
The fly ash and silica fume are byproducts of the coal and silicon metal industries respectively. When combined, they produced a high strength and durable MOC in room-temperature water.
In warm water, however, the cement weakened faster. To prevent this, the team used both organic and inorganic chemical additives, which improved warm water resistance.
“We have been working on this for the past three years and we made a breakthrough, so this material can now be used in external applications,” Dr. Zhang says.
The cement now has an expanded portfolio for use. From its original capabilities of indoor decoration such as floor panels or tiles, the research will allow for its external use on structures to create the cladding of a building or an external board.
The second challenge is one that Dr. Zhang identifies as a significant hurdle. The cement as a raw material contains chloride, which is corrosive to steel over long periods.
Creating large concrete structures, such as railway stations or airport terminals, requires steel reinforcement.
As a result, the MOC is unable to be used in concrete for large infrastructural applications.
“We believe we must be able to solve this problem.
“We are trying to do a pilot project, though that will take a long time because the corrosion happens slowly over a long time,” Dr. Zhang says.
She says there are a few ideas for further testing, but research funding and collaboration will be needed to support the project.
Dr. Zhang is optimistic a solution can be found. She says with the UN aiming for environmental and sustainable construction practices, social responsibility is prompting companies to change.
“In the long run, people will be thinking about the environment and sustainability and then this kind of green material will have a strong market,” she says.
“If the new MOC can be used to replace the original Portland cement or even partially replace it, for example by 50 per cent, that could make a big difference for emissions in the construction industry.”