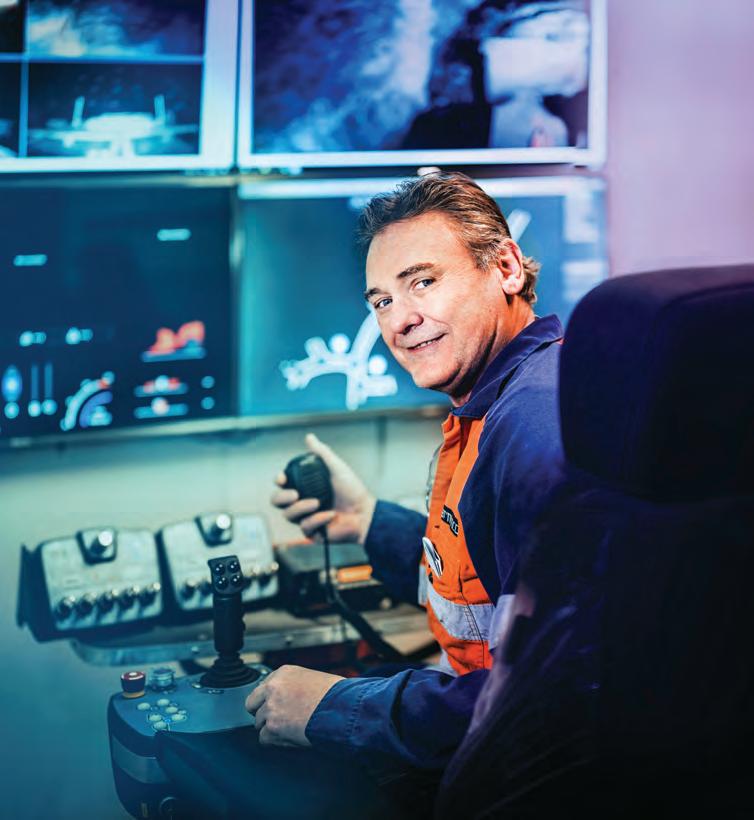
7 minute read
Remote operations of today
What protects the technology keeping mines safe?
The Sandvik-Barminco trial has demonstrated that the Nova operation, 160 kilometres from Norseman in Western Australia, can be operated from Barminco’s office in Perth more than 750 kilometres away.
Barminco employee, Guy Gilbert has operated a Sandvik LH517 underground loader at the nickelcopper-cobalt mine, remotely bogging 400 tonnes in a little over two hours from a stope to a stockpile, from the company’s control rooms at Hazelmere in Perth.
Not only was the trial of the Barminco Remote Operating Centre (BROC) successful, but it also occurred via the internet rather than through a fibre-optic cable, the common method at these kinds of operations.
Gilbert’s feedback about the experience is resoundingly positive. He says when the telehut door is shut he forgets he is at Hazelmere and goes about his job like he is on-site at Nova.
The potential of remotely-operated SANDVIK AND BARMINCO HAVE PROVED AT IGO’S NOVA MINE THAT REMOTE OPERATIONS ARE A REALITY IN THE NOT TOO DISTANT FUTURE, BUT HOW CAN CYBER SECURITY BE ENSURED?
Barminco operated a Sandvik LH517 underground loader at the Nova mine from 750 kilometres away in Perth.
mines offers an exciting opportunity to improve safety for workers, removing them from potentially dangerous situations, according to Gilbert.
Operating from a distance allows workers to make better use of less productive time in a more flexible workplace closer to cities like Perth
rather than in remote areas.
It also allows workers to return home after shifts rather than working a fly-in, fly-out (FIFO) roster where they are away from families and friends.
While keeping workers safe is the number one priority, remote operations also need to be protected
from a new wave of threats that come with the advanced technology being implemented, including cyber security.
Barminco general manager, technology and innovation Darren Kwok plays a major role in keeping the BROC safe from cyber threats.
“The integrity of our networks in general outside of BROC is certainly something that we put a lot of thought into,” Kwok tells Safe to Work at the Sandvik: Digitalisation in Mining conference.
“BROC operates in the confines of those networks already, so that’s the first level of security that we have. Like many global businesses, Barminco transacts over the internet now.
“Level two is the machine to machine security, and we’ve built some great things with Sandvik to allow us to have a high level of confidence when Barminco employees working the Nova mine near Norseman from Barminco’s Perth office.
it comes to the security of the physical act of manoeuvring the machine.”
Barminco’s team in Perth also continuously connects with the site via more conventional methods such as telephone, video and extended
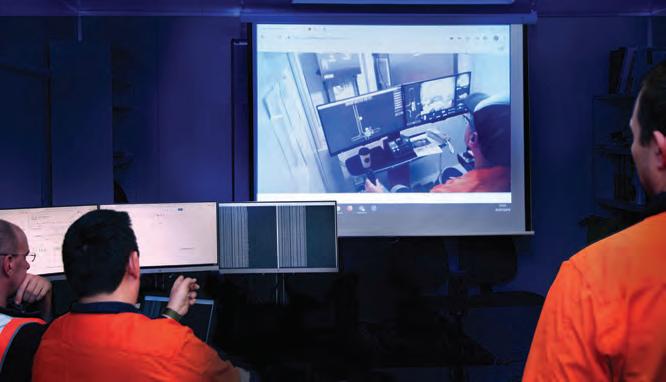
two-way radio, allowing further communication between them and with the operator.
Barminco chief executive officer Paul Muller says the remote operations were tested over a greater broadband
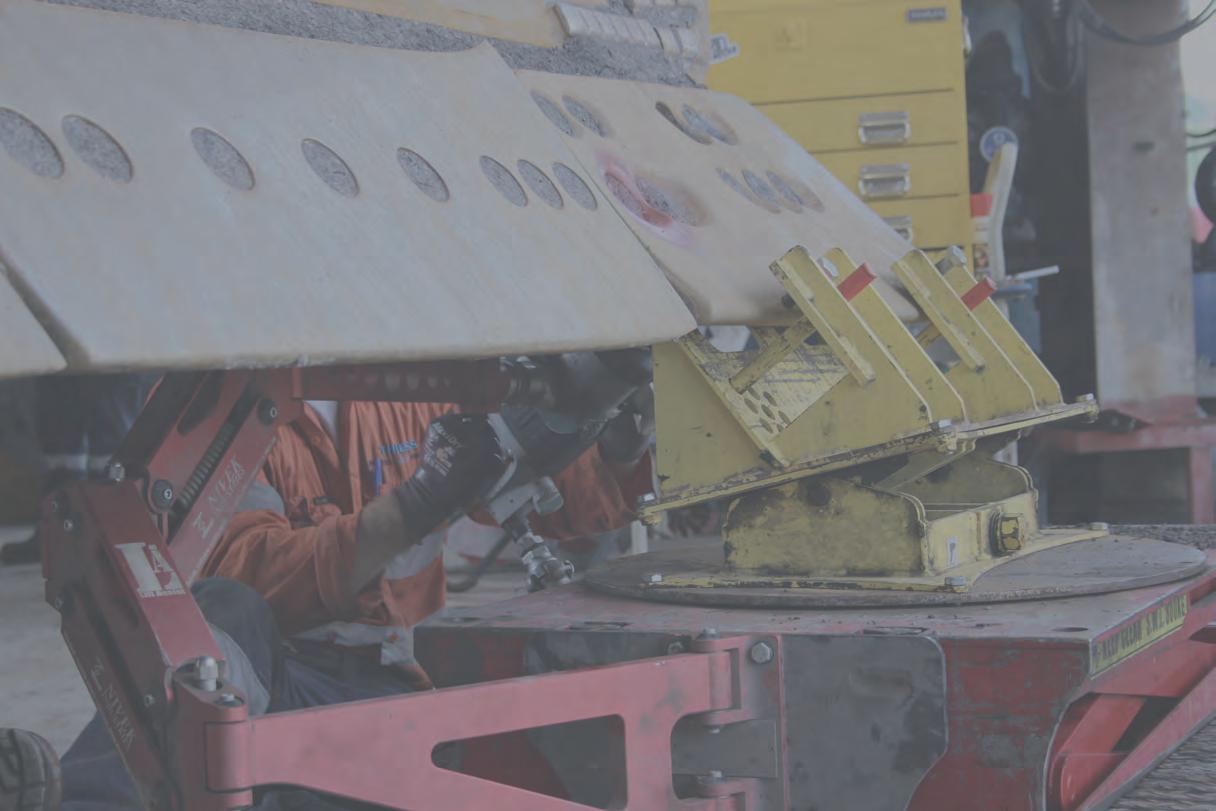
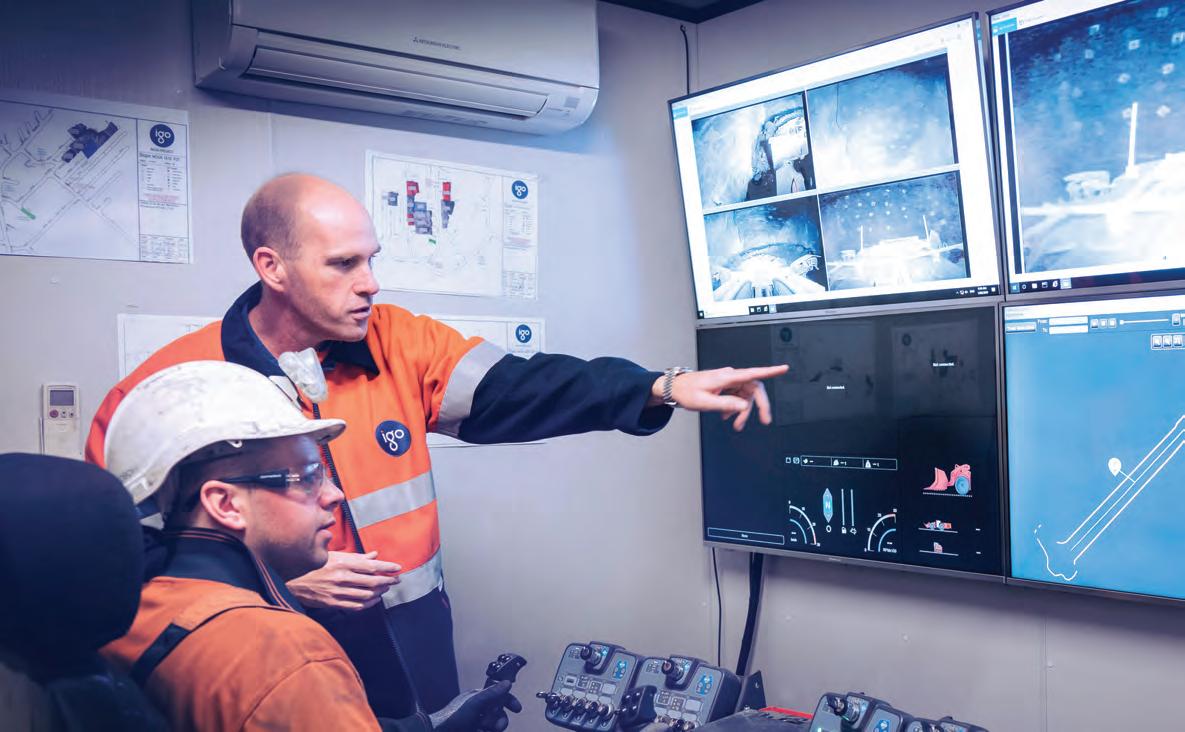
network and the National Broadband Network (NBN) during the trial.
“The primary objective of the BROC proof of concept was to understand how the control of underground mining equipment would be affected by real world internet conditions,” Muller explains.
“All data was encrypted from end to end and standard safety systems were in place. If there was a network interruption for more than 250 milliseconds, the loader would stop and require a manual reset.”
Barminco has designed systems to resolve the challenges encountered in the first attempt, such as network disturbances, using information gathered during the trial.
“The Automine system is reliant on there not being any data losses through the network,” Muller says.
“This caused a number of interruptions throughout the trial, requiring the machine to be manually reset. We expect the new system
designs will mitigate this issue in the future without compromising safety.”
With technology in mining now a necessity for both large and small mining operations, rather than just an optional add on as it has been in the past, designing the best possible defence systems is essential to safe operations.
As Kwok explains, this means finding more than just the best security solution for the present, but continuously developing securities to keep up with evolving technology.
“There’s no end-game in security, it’s constantly evolving,” Kwok says. “What we believe to be best practice today may be different tomorrow, so the whole concept of what we’re trying to build is one that progresses ahead of technologies evolution.”
“As part of the design of
Barminco employee Guy Gilbert remotely operating IGO’s Nova mine from Barminco’s Perth control room.
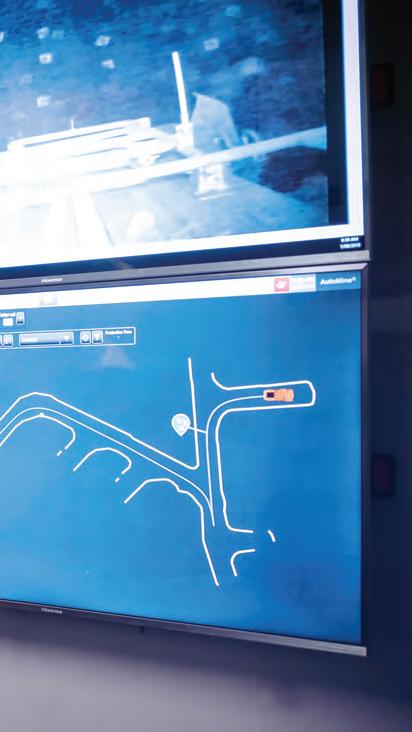
BROC, we are able to adopt new security practices as they are being developed.”
With Barminco and Sandvik running a more advanced trial integrating the new system designs in early 2020, the companies are hopeful to take the next step in cyber security and make BROC a permanent fixture at the Nova mine.
Sandvik conference prioritises people in digital mines of tomorrow
Sandvik’s conference may have been called “Digitalisation in Mining” but one of its key focusses was how to ensure people are a part of the digital journey. Nearly 300 mining, quarrying and construction leaders from Australia, Japan and Indonesia gathered in Brisbane for the two-day summit, which showcased some of the industry’s best examples of digitalisation.
While technology and digitalisation were the hot topics, industry leaders emphasised the importance of using human intelligence to truly understand the technology being implemented at Australian mine sites. One of these was Byrnecut Australia managing director Pat Boniwell, who urges the industry to not take people for granted as more operations take on technology such as automation and artificial intelligence (AI). “We are doomed to failure unless we take our people with us and are prepared to question and be challenged,” Boniwell says. “Technology is a key part of the equation on how we best optimise systems and processes in mining and if we don’t use it, we can’t make the most of them.” Boniwell also emphasises the importance of the ability to gather data while working autonomous machinery then using the data to find information for future operations. “Data is essential, but if it is not being looked at then we are just gathering data for the sake of it,” he says.
“The background analysis of data, particularly for machines, maintenance, costs and so on, how does that then translate into information and operations and how quickly does it happen? “So yes, the analysis is happening at the moment, but it doesn’t flow instantaneously through the operations.”
Sandvik provided delegates with the opportunity to virtually visit its clients sites, including the Barminco Remote Operating Centre (BROC) and Northparkes and Tritton mines in New South Wales, and showcased other clients including Resolute Mining and RedBull Powder Company. Attendees had the opportunity to not only view, but have a go at crushing, drilling and controlling mock operations digitally, giving them practical insight into the mine of tomorrow.
“An amazing two days at the Sandvik Digitalisation in Mining conference,” Cement and Aggregate Consulting chief executive and attendee Steve Franklin says.
“There was an incredible range of world class speakers who basically all had the same message; innovate or lose to someone else who will.”
Bespoke electronic vehicle safety solutions
Dual Axis Inclinometers
We offer a range of digital inclinometers that provide machinery operators with highly visible pitch and roll measurements. 24 .6 38 .4
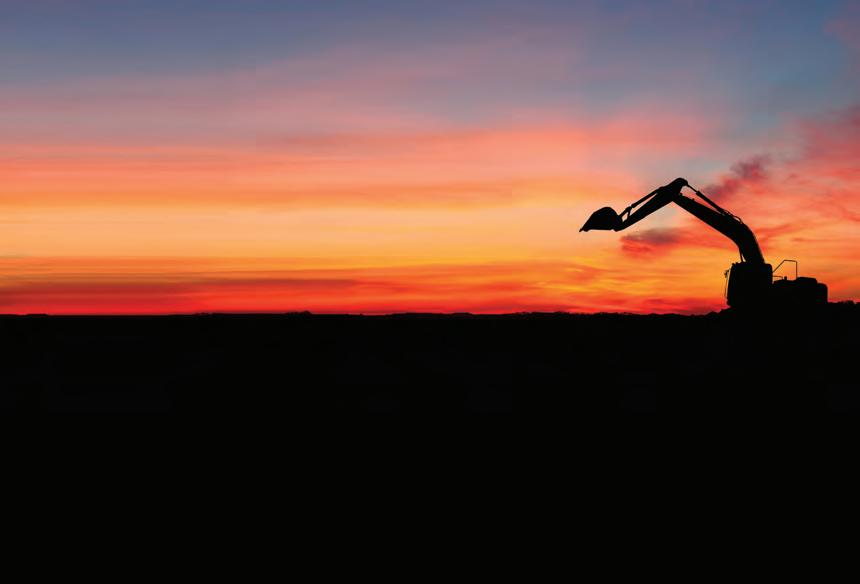
Audio Alert System Our Audio Alert System provides clear, voice readouts for a range of customisable inputs, to serve as warnings and safety reminders.
Silent Horn
Our Silent Horn is for machinery operating in noise-sensitive environments. Horn blasts are replaced with a wireless link, allowing for communication with no external noise. DIGGER MODE
Hummingbird Electronics are specialists in electronic vehicle and machinery safety solutions. We offer a suite of safety focused products designed to protect operators and equipment in the mining, civil, industrial, machinery hire and agriculture industries. Designed and manufactured in Australia to the highest standards, Hummingbird is a brand you can trust to improve safety on your worksite.
1300 155 541 hmbe.com.au