
13 minute read
Workers come rst for drilling and blasting techniques
by Prime Group
Workers come first for drilling and blasting techniques
AS TECHNOLOGY IN DRILLING AND BLASTING METHODS ADVANCE, ONE ASPECT OF THE PROCESS WILL CONTINUE TO BE THE MOST IMPORTANT TO MINE OPERATORS AROUND THE WORLD – SAFETY.
Drill and blast techniques have been an integral part of the mining and resources industry for centuries.
Considered one of the most economic and efficient ways of extracting ore and precious metals from the ground, the techniques have seen considerable development over the years.
One of the major reasons for this development has been to improve the safety of workers on-site, particularly considering the complexities of the machinery and technology involved.
Original equipment manufacturers (OEMs) like Sandvik are focused on removing the guesswork and human error out of drilling applications by developing autonomous solutions.
As automation technology advances, user-friendly machines that reduce manual labour are in high demand for the industry, delivering more efficient, safer and reliable operations for mining companies.
Sandvik prioritises operator acceptance in this way when designing and selling new products.
Simple controls and aftersales support are at the crux of what makes the OEM’s products so appealing, not only to mining companies but to the operators themselves.
“Operator acceptance in Australia is a really big thing for drill owners and us,” Sandvik business line manager underground drills Patrick Mckenna said.
“It encompasses ease of operation, familiarity – anything to make the operator’s life a bit easier.”
The ethos behind Sandvik’s consideration for the operator stems across its entire product line of underground drills, including development, tunnelling jumbo, top hammer longhole, rock support, in-thehole longhole, low profile, narrow vein and secondary breaking drill rigs.
For Mckenna, automation brings several advantages to underground drilling. Aside from safety, he says the big advantage is that it allows the operator to own the shift change.
“It gives the operator the ability to drill from the surface during a shift change, which basically gives you more time drilling and that equals more metres,” he said. “The automation function gives you a better-quality hole and straighter hole with less overbreak or underbreak in the tunnel.”
Sandvik has been an integral player in the market for autonomous equipment as interest in the technology has increased.
Mckenna says several customers in Australia are now using DD422i drills, which incorporate autonomous functions and are getting a better tunnel profile with less underbreak or overbreak.
When it comes to blasting technology, Austin Powder has been in the business of helping customers break rock safely and efficiently for more than 185 years.
Today, Austin serves operations in mining, quarrying, construction, pipeline, and oil and gas across the globe.
Each blaster is trained to know the details about the products, safety, and regulations related to every shot.
Austin Powder Australia managing director Fil Lassak said the industry had come a long way in terms of developing blasting technology.
“Obviously, the whole industry and regulators are working every day to enhance various aspects of safety,” he said.
“I’d highlight modern blast design modelling with a combination of precise electronic blasting.
“Such practice eliminates risk during blasts and brings predictability, which is valuable when managing operations.
“For underground mining, we should mention central blasting systems that allow multiple electronic blasts to be triggered remotely in the safety of an office above the mine.”
Lassak said improvements in traceability have had a significant impact on the industry, allowing companies to trace where their detonators originate.
“Our detonators used in Australia and New Zealand are produced in the EU, which has strong regulations on the traceability of explosives,” he said.
“Each detonator has a unique
Austin Powder is a leader in blasting technology.
identifier, and information about the seller and buyer are stored for 10 years. This creates comprehensive practice, preventing the misuse of explosives.”
According to Lassak, the electronic detonator is the latest generation of initiating systems and is superior to electric and non-electric detonators.
“Electronic detonators are precise, which leads to significant benefits like desired fragmentation,” he said.
“The name electronic suggests another advantage, which is the digitalisation of the blast process. The deep insight we receive now with electronics is not possible with legacy detonators.”
Drilling technology has also seen advances in technology that allow operators greater economy and productivity, while still highlighting safety.
Used by some of the world’s largest mining companies, the remotecontrolled Epiroc Pit Viper can operate continuously.
The autonomous Pit Viper is safer and more productive than traditional blasthole drills, with up to 41 per cent higher productivity than traditional drills.
“Automation and interoperability are the future of mining,” Epiroc Australia’s regional application centre manager Rohan Anderson said.
“Mining companies will increasingly use autonomous machines that talk to each other through a common technology platform, and require less human intervention.” Six years in the making, this next-generation drill technology was co-designed at Epiroc’s Swedish, US and Australian operations.
Anderson led a local team of 20 who worked with Epiroc’s global innovation experts and Australian mining companies as part of the Pit Viper’s development.
Lassak said mining and quarrying were increasingly data-driven operations, and electronic blasting was an important step on this digital journey.
“We also see that some regulators aim for fully electronic blasting due to its highly safe nature,” he said.
“I believe that the whole industry realises that there must be a sustainable path for our operations in the near future. Among many sustainable processes, we support this path with so-called eco-detonators that don’t have nasty chemicals.”
Austin Powder’s E*Star CUBE is the company’s central blasting system and represents a major safety development.
Lassak said the mining industry response to the E*Star system had been extremely positive and put a strong focus on worker safety.
“We have been enhancing our E*Star ecosystem for over a decade, and customers’ feedback has been in the centre,” he said.
“So when customers have an idea or experience which can be enhanced, our in-house R&D (research and development) team simply do it.
“Our customers have much appreciated this practice and they are happy with the product ticking all their boxes.
“Our team, for instance, completely redesigned the connectors based on customer feedback.
“Our connectors are very innovative; for instance, the ‘double connect’ capability allows for eight points of contact on both the detonator leg wires and the bus lines.
“They are also effortless to use, close and reopen, which is handy for the blasting crews.”
Safety will remain at the forefront of drilling and blasting techniques as companies focus on providing protection to their workforce.
While there will definitely be more technology advancements to come, companies like Austin Powder recognise the importance of having workers return home to their families.
“Our company has been in the industry since 1833, and with almost 200 years of experience we know there is nothing more important than safety,” Lassak said.
“Safety actually formed our mission to improve the world we live in through the safe and responsible use of explosives.
“We all want to return home from our work safely, and I’m glad to say we successfully managed decades without incidents.”
Minimise downtime and labour with the Bolt On Saver Sub
J&S ENGINEERING HAS DEVELOPED A SIMPLE AND COST-EFFECTIVE WAY TO KEEP THE TOP SUB THREAD ON DRILLING MACHINES IN A MORE SERVICEABLE CONDITION, INCREASING THREAD LIFE IN DRILL RODS BY MORE THAN A THIRD.
Minimising downtime is critical to a mining operation, especially when the cost of the labour involved increases due to the complexity of the job at hand.
J&S Engineering has developed and patented a way of keeping the top sub thread on drilling machines in serviceable condition. The Bolt On Saver Sub reduces downtime during changeout from around three hours to 20 minutes.
Operating out of Maitland in the
Hunter Valley of New South Wales, the company specialises in a full range of consumables for blasthole drills.
J&S Engineering business development manager Luke O’Neill said since the business implemented the patent around 15 years ago, it had meant significant savings for drilling companies.
“The old way you used to attach these saver subs is you had to weld them on, which used to require a lot of hot-work gear. Previously, the change out of a saver sub has been a slow and costly process requiring craneage, boilermakers, welding machines, heating and gouging equipment,” O’Neill said.
“This has taken all of that out of it now, so you don’t need the workforce and the time to take these subs out.
“Now there is no welding required at all and it has taken all of that hot-work risk out of the installation.”
One of the important aspects of the saver sub is increased longevity. The internal thread takes the majority of wear, as this thread is continually tightened and untightened to allow drill rods to be put on and off to increase and decrease drill rod length for different hole depths.
This is effectively giving the top sub a life span of years rather than months.
The Bolt On Saver Sub is also fitted with a seal unit that prevents water and air pressure escaping through the abutment face between the saver sub and the top sub.
O’Neill said the Bolt On Saver Sub was widely used in the mining industry and had become a very important component of the drill string.
“I would say around 90 per cent of the drilling operators here in the Hunter Valley operate using the saver sub,” he said. “We supply our products to Queensland as well, and we have supplied our drilling gear over to Papua New Guinea.
“Essentially, this is all about safety to the fitters and the people who are changing the sub out. It used to take a team of people with all kinds of gear – at times it could be a three-hour process – just to change one of the subs out.”
The job is often delayed due to costly downtime and the logistics of organising staff and equipment.
“We fit a modified top sub once as per the usual procedure, which has been machined to fit the Bolt On Saver Sub. It can be lifted and screwed into place by hand,” O’Neill said. “Two locking plates are then fitted with four retaining screws each. Once this has been completed you are ready to drill.”
O’Neill said safety is one of the key benefits of the Bolt On Saver Sub.
“If you can eliminate hot works when it comes to your hierarchy of controls it makes everyone happy,” he said.
“The solution is extremely valuable to the mine site, saving time, money and most importantly it’s a much safer option.
“We spent a lot of work on improving the safety aspect and trying to make it more efficient, and now we have it down pat.”

The Bolt On Saver Sub is widely used throughout the mining industry.
One tech platform can make each blast smarter than the last
AUSTMINE MEMBER HEXAGON SHARES ITS INSIGHTS AND EXPERIENCE OF SMARTER DRILL AND BLAST PROCESSES.
There are few certainties in mining, but reduced ore yield is all but guaranteed if errors are made at any stage of the complex, multi-layered drill and blast (D&B) process. The wasted energy, time and opportunities cost today’s business more in an age of declining grades, when miners are digging more earth for less ore.
In the mining cycle, D&B is arguably the first – and most important – step to get right.
D&B operations impact the entire mining process, from equipment efficiency through to crushing and grinding circuit performance, to recoveries and final product quality. Costs and energy usage increase throughout the comminution process. Efforts targeted at optimising the blasting process can pay huge dividends downstream, reducing costs and energy consumption.
A correct blast not only optimises the cost of that blast but also improves the total cost profile of the entire mine. Correct fragmentation means easier digging, reduced shovel cycle times, reduced rework, less oversize causing downtime at the crusher, lower-cost crushing, and improved tonnes per hour (TPH) through the processing plant.
A continuous D&B feedback loop underpinned by technology not only increases the profit from every blast, but also a mine’s purchasing power over one of the most expensive parts of the process – explosives.
Hexagon’s MineMeasure is a tailored portfolio for D&B, improving yield, fragmentation and dilution by combining blast design software, high-precision drills, blast movement monitoring, fragmentation analysis, and enterprise analytics.
From one platform, MineMeasure ensures data does its best work, empowering customers with a feedback loop calibrated to increase profit from every blast. It is a good example of Hexagon’s Power of One approach, a holistic, life-of-mine platform connecting sensors and software, infield apps and cloudware.
MineMeasure represents a scalable, platform-agnostic answer to challenges previously addressed by point solutions and multiple vendors. Here’s a closer look.
BLAST DESIGN AND HIGHPRECISION DRILLING
A well-designed blast pattern and the effective execution of the blast plan using high-precision drills are an important part of an effective D&B operation.
MineMeasure includes a comprehensive software utility for D&B and reconciliation. Rather than risking high-wall stability problems, uneven blasting, poor fragmentation,
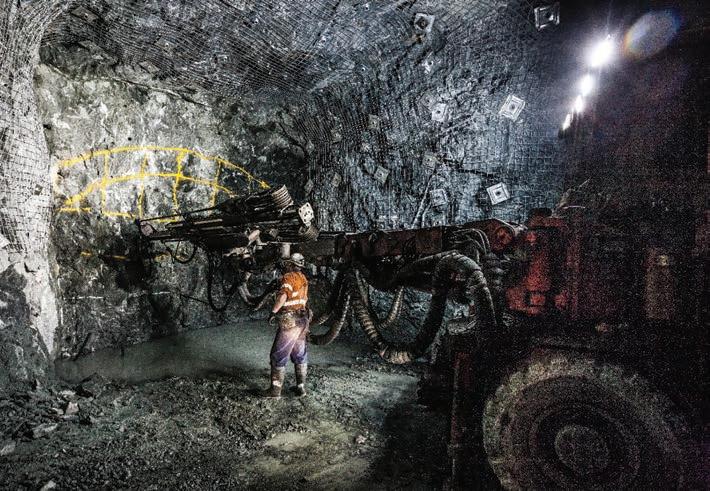
The acquisition of Minnovare will accelerate and enhance MineMeasure.
unnecessarily high energy costs, and dangerous working conditions, MineMeasure incorporates charge and blast design templates that are based on sound engineering principles and methods proven in mines worldwide.
The portfolio features machine guidance for drills (as well as dozers and loading equipment). This ensures drilling is performed to the right position and elevation. It provides accuracy and instantaneous feedback, meaning improved loading times across the fleet, less mis-routed material, fewer hours of rework on ramps, roads and benches, and fewer over- and underdrilled holes. It is proven to improve both the quality of material produced and fragmentation with precise drillhole placement and depth.
Integration with Hexagon’s operational management hub means a single source of reporting and support.
BLAST MOVEMENT MONITORING, FRAGMENTATION ANALYSIS AND BLAST OPTIMISATION
Preparing for the D&B stage, mine operations have already spent significant amounts of money (running into the millions) to accurately locate the ore body and maximise the information known about the surrounding geology. Proven fragmentation analysis and blast monitoring solutions minimise loss and dilution, and deliver the data necessary for the next blast pattern design.
Acquired by Hexagon in 2020, Blast Movement Technologies (BMT) is an integral part of MineMeasure, providing accurate ore location information for open-pit mines. Via sensors and software, BMT provides accurate blast information that is used to recover all of a mine’s resources. It ensures that, post-blast, the mine retains a full vision of where its ore body moved to.
Hexagon’s Split Engineering systems are flexible and can monitor in different areas and process along with the operation automatically, such as in shovels, excavators, loaders, haul trucks, crushers, conveyor belts, mill feed and screen decks. The entire process can be connected from pit to plant for a unified approach to fragmentation management.
Monitoring trends in size at each point in the comminution circuit enables operational adjustments in real-time. Alarms can be created for oversize events, reducing the downtime from inefficiencies caused by blockages and broken screen decks.

PRECISION DRILLING UNDERGROUND
In January 2022, Hexagon acquired Minnovare, a leading provider of drilling technology that improves the speed, cost and accuracy of underground drilling.
Minnovare specialises in eliminating the manual, labour-intensive and unproductive processes in underground mining that lead to blast-hole deviation, dilution and downtime. Advanced hardware and data-capture software combine to deliver drill data faster and more accurately than ever – improving the efficiency, productivity and overall profitability of underground drilling. Its solutions combine sensors, software and data analytics to address deficiencies in drilling processes across the resource definition, development and production phases.
The acquisition will enhance MineMeasure and accelerate Hexagon’s underground development roadmap.
A UNIQUELY HOLISTIC APPROACH
The ability to tailor fragmentation outcomes and minimise ore loss and dilutions through blast movement monitoring are proving to be highly sought after. This uniquely holistic view of an operation combines key knowledge banks, such as geology behaviour, effects on powder factor, blast design, planning and fleet management.
MineMeasure’s comprehensive D&B approach delivers the power to improve the most vital part of the mine, where everything starts with the D&B, without losing purchasing power over the bulk commodity blasting material.
All from a single technology vendor. That’s the Power of One.
MineMeasure provides accurate blast information that’s used to recover all of a mine’s resources.