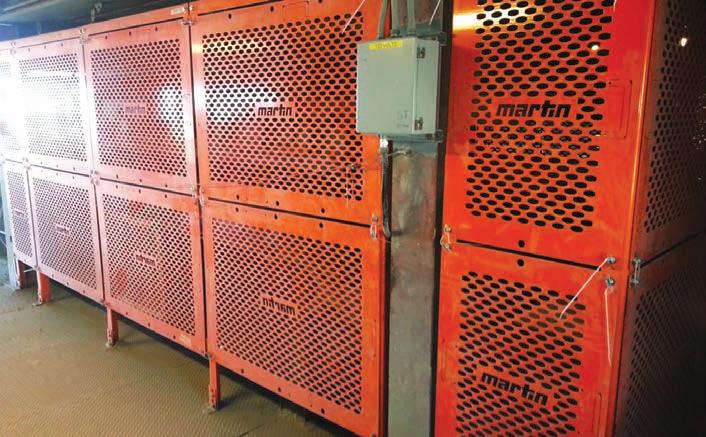
2 minute read
Improving efficiency through conveyor safety
MARTIN ENGINEERING PRESIDENT EMERITUS TODD SWINDERMAN EXAMINES HOW USING EQUIPMENT DESIGNED FOR SAFETY ALSO HELPS TO IMPROVE EFFICIENCY.
Conveyors are among the most dynamic and potentially dangerous pieces of equipment in a mine or quarry.
Even though safety and performance of conveyors are critical to the operation’s success, their contribution to overall efficiency can be unrecognised by management and workers alike. As such, the operational basics of belt conveyor systems –regarding the hardware installed and the performance required from the components – are often a mystery to many employees.
This knowledge gap also creates a safety gap.
Designing For Safety
Since people are the single most important resource of any industrial operation, Australian work health and safety (WHS) standards continue to tighten. To meet these standards, the consensus among safety professionals is to design a hazard out of the component or system, which historically yields more cost-effective and durable results.
Engineers often recommend operators retain an outside firm to examine requirements and design new equipment to address bulk handling safety and efficiency issues. Getting this kind of outside viewpoint can identify overlooked issues.
Before the drafting phase, designers should:
• establish the goals of reducing injuries and exposure to hazards (dust, spillage, etc)
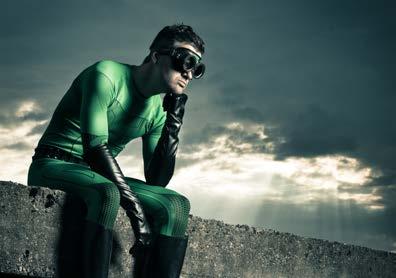
• increase conveyor uptime and productivity
• seek more effective approaches to ongoing operating and maintenance challenges. Designs should be forward-thinking, which means exceeding compliance standards and enhancing operators’ ability to cost-effectively incorporate upgrades by taking a modular approach. This method alleviates several workplace hazards, minimises clean-up and maintenance, reduces unscheduled downtime, and extends the life of the belt and the system.
Combining Safety And Productivity
To meet the demands for greater safety and improved production, some manufacturers have introduced equipment designs that are not only engineered for safer operation and servicing, but also reduced maintenance time.
Examples if such equipment include the Martin QC1 Cleaner HD/XHD STS (Safe-to-Service) primary cleaner and the Martin SQC2S STS secondary cleaner, both of which are designed so the blade cartridge can be pulled away from the belt for safe access and replacement by a single worker.
The same slide-out technology has been applied to impact cradle designs. Systems like the Martin slider cradle are engineered so operators can safely work on the equipment without breaking the plane of motion. External servicing reduces the need to enter confined spaces and eliminates reach-in maintenance while facilitating faster replacement.
The result is greater safety and efficiency with less downtime.
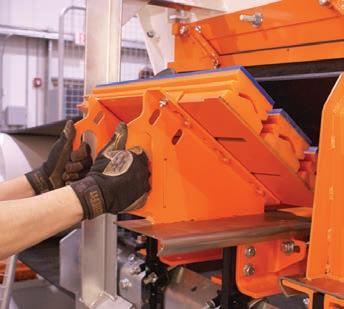
An example of a safer belt cleaner is the CleanScrape, which features a patented design that reduces the need for bulky urethane blades altogether. It delivers extended service life and low belt wear and significantly reduced maintenance, which improves safety and lowers the cost of ownership.
Unlike conventional belt cleaners that are mounted at an angle to the belt, the CleanScrape is installed diagonally across the discharge pulley, forming a three-dimensional curve beneath the discharge area that conforms to the pulley’s shape. The novel approach has been so effective that, in many operations, previously crucial secondary belt cleaners have been rendered unnecessary, saving further on belt cleaning costs and service time.

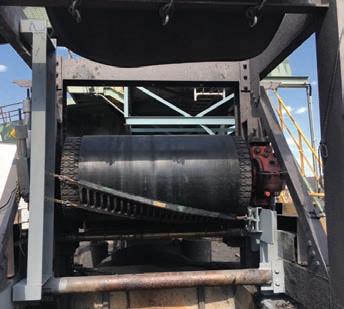
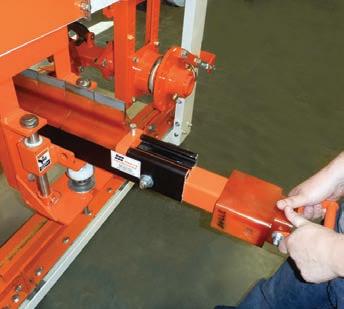
Lifecycle Cost
Maximising the volume of cargo and minimising the price of the system usually means choosing the narrowest feasible belt operating at the highest possible speed. This leaves little margin for error and, in many cases, can result in chute-plugging, excessive spillage, reduced equipment life and unsustainable amounts of unscheduled downtime.
When companies buy on price, the benefits are often short-lived and costs increase over time, ultimately resulting in losses. In contrast, when purchases are made based on the lowest long-term cost (ie lifecycle cost), benefits usually continue to accrue and costs are lower, resulting in a net savings over time.
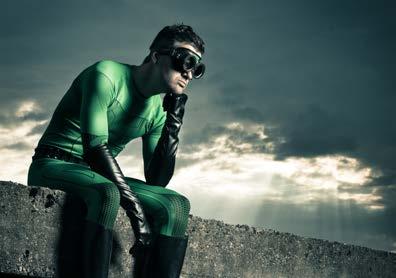
Design Hierarchy
To safely maximise production, designers and engineers are urged to approach a project with a specific set of priorities. Rather than meeting minimum compliance standards, the conveyor system should exceed all code, safety and regulatory requirements using global best practices.
By designing the system to minimise risk and the escape and accumulation of fugitive material, the workplace is made safer and the equipment is easier to maintain.