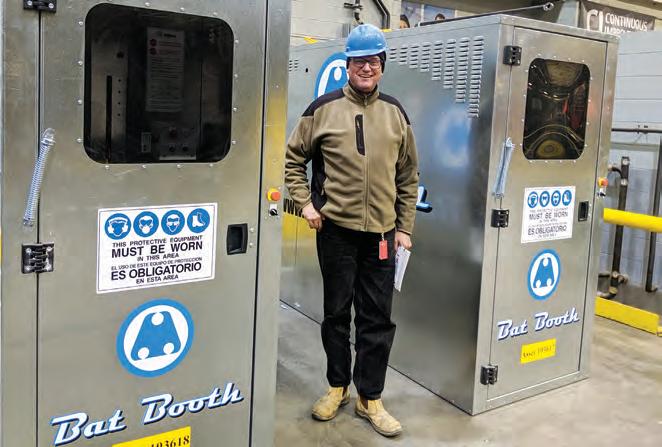
4 minute read
Cleanest place on a mine site
from STW Sep 2020
by Prime Group
Mideco fends off secondary dust exposure, COVID-19
DUST CONTROL ENGINEERING SPECIALIST MIDECO COMBATS TWO CENTRAL PROBLEMS FOR MINE OPERATORS – DUST EXPOSURE AND BODY TEMPERATURE SPIKES – WITH A SINGLE SOLUTION: BAT BOOTH 2.0.
After speaking at the Smart Mining conference in Denver, Colorado, in 2019, Mideco director Melton White heard an intriguing presentation on incidents in American mines arising from heat stress affecting workers.
White, who developed the Bat Booth personnel de-dusting system recognised by BHP as the Best Innovative Safety Product of 2016, sought out the presenter. Their conversation opened his eyes to the potential of an extra safety function – a temperature check that could detect possible viral infections as well as heat stress.
“I’ve not spoken to this woman again since, but everything she said made sense and planted a seed in my head,” White says.
The Melbourne-based dust-control expert was already familiar with the dangers of very high temperatures at Australian mine sites.
“When our body temperature elevates, we lose many cognitive abilities even though we may not be sick,“ he tells Safe to Work. “That means when a driver is operating a loader or forklift under extreme temperatures, he or she is no longer driving that machine safely.”
The enhanced Bat Booth 2.0 has a speedy intelligent function, so a mine’s first responders can act before a heat-affected employee’s condition became critical. Within 15 seconds of an individual entering the de-dusting booth, the system automatically measures their body temperature and reports the result in real-time to managers at any location.

The Bat Station facial recognition function captures body temperature.
Ironically, although White was aware of the potential of temperature checks to guard against the spread of viral infections at work sites, the development of Bat Booth 2.0 was in train long before the arrival of the coronavirus pandemic.
“We were well and truly under way through the design phase for Bat Booth 2.0 months before the pandemic hit,” White says. “In fact, if it weren’t for COVID-19, Bat Booth 2.0 would have been launched sooner.”
Among the hurdles was the search for an appropriately sensitive infrared sensor. Commonly used heat measuring guns are designed to measure temperatures ranging from 0 to 400 degrees Celsius and are not calibrated for the human body.
“You will most likely miss the temperature spike you’re looking for,” White says.
“They’re usually two to three degrees out. So we had a problem finding an infrared sensor that can accurately measure body temperature.”
The plug-and-play Bat Booth 2.0 is designed to drastically reduce secondary exposure to dust coming off workers’ apparel. According to White, over 80 per cent of the dust that clings to clothing can become airborne, affecting the individual and people around them and increasing health risks such as silicosis, black lung and lung cancer.
“You can’t see any of that happening, but that really strikes a chord with us.”
“When a person takes a break or finishes his shift, the first thing they do is to take off their personal protective equipment, go to the lunchroom and expose their mates to dangerous respirable dust,” White says.
According to an analysis by Queensland’s Safety in Mines Testing and Research Station (SIMTARS), the Bat Booth can reduce an employee’s respirable dust exposure by up to 88 per cent.
The dust collector fan inside the Bat Booth 2.0 draws in clean air through louvers mounted on the side panels. At the same time, low-pressure air jets blow dust off clothing as the individual turns around. The liberated dust is fanned off the floor as soon as the system is activated.
The low-pressure air and dust are carried to the dust collector, with the negative-pressure environment ensuring that the dust is contained and captured by HEPA grade filters.
“The air we blow back into the atmosphere is as clean as the air they blow into a birthing suite,” White says. “So, really, the place with the cleanest air on a mine site would be the outlet of the Bat Booth.”
To date, around 60 units of the original Bat Booth are in operation in almost every state in Australia. They are also used in the United States, Canada and Chile.
Mideco has also developed the Bat Station, a companion device with a facial recognition function that automatically captures an employee’s body temperature in half a second.
“When a truck driver looks at the Bat Station, it will recognise his face and measure his temperature. If he’s fine, the Bat Station will give him a green light, allowing him to get on with his work,” White says.
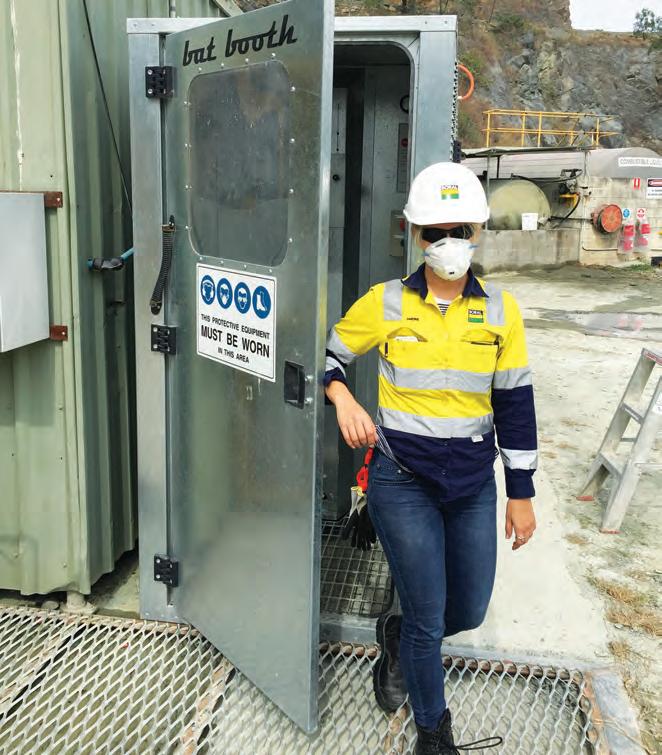
The Bat Booth 2.0 captures up to 88 per cent of respirable dust.
If the temperature reading is too high, the Bat Station sends a text message to the first responders.
“Someone may just be asked to go into an air-conditioned room and have a glass of water,” White explains.
“However, the reading could be a warning sign that the employee should be checked for a viral infection, such as influenza or the COVID-19 virus.”
Mideco emphasises that both Bat Booth 2.0 and Bat Station can be used flexibly for dust control, temperature monitoring and health and safety management of any scale.
The company is happy to arrange demonstrations of Bat Booth and Bat Station on sites around Australia.