
5 minute read
Boss of mine blasting
from STW Sep 2020
by Prime Group
BME is responsible for some of the world’s largest electronic detonator blasts on a mine site.
AXXIS TITANIUM delivers blasts with a bang
AS A PIONEER OF BLASTING TECHNOLOGY, BME HAS LIVED UP TO THIS REPUTATION WITH ITS LATEST RELEASE. THE AXXIS TITANIUM ELECTRONIC INITIATION SYSTEM MAKES BLASTING SAFER THAN IT HAS EVER BEEN BEFORE.
BME continues to capture the attention of the Australian mining sector.
When the company broke the world record for the largest electronic detonator blast in 2016, it proved that the AXXIS system was a frontrunner of electronic initiation systems.
Then, just two years later it surpassed its own record, when 7350 AXXIS detonators were fired in a single pattern, 1.7 kilometres long in a Central Queensland coal mine.
The accomplishment was unique as the technology was safely executed only by mine staff without direct AXXIS technical support. The blasts were also delivered with millisecond accuracy even with the very long delays that were needed for such large blasts.
Indeed, the AXXIS system is known for its safety focus, a highly desired attribute in the Australian market.
BME’s newly released AXXIS TITANIUM digital initiation system has added a double safety system featuring dual capacitors and dual voltage. This positions AXXIS TITANIUM as the only system in the world to include both safety features.
“Dual voltage effectively means that you can communicate directly with the detonator, write any desired firing times and log positions from your device to the detonator and do all that at a safe, lower voltage even with explosives loaded in the hole,” BME global product manager for AXXIS Tinus Brits says.
“So even if a detonator is damaged in some way, there is no risk of initiating its fuse head because the communication voltage is below the voltage needed to fire the fuse head. That’s the benefit of a dual voltage system.”
Dual capacitors, on the other hand, are comprised of a logic capacitor and separate firing capacitor.
The logic – or lower voltage – capacitor is used as an energy source to power the microprocessor, allowing communication with the detonator.
It has a small capacity that is insufficient to fire the fuse head. The firing – or higher voltage – capacitor in each detonator is only charged by a specific command during blasting time, when the pit is cleared and immediately before the countdown for the shot is started. The firing capacitor releases its energy to fire the detonator on command.
This creates two separate and independent methods of communication that makes it inherently safe to log, test and fire detonators while also providing increased flexibility in safe testing.
This is a huge leap from what is already a leading electronic detonator, the AXXIS GII. The AXXIS TITANIUM predecessor does not allow for detonator programming and testing to
BME global product manager for AXXIS Tinus Brits.
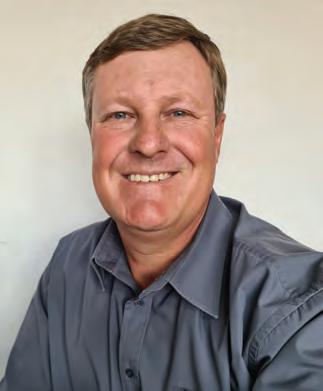
happen concurrently during logging.
“That’s why the stability of the AXXIS TITANIUM unit is a big win for us. It is a major improvement in reliability, performance, safety and quality for our clients,” Brits says.
Still, BME takes safety to another level. The company has put multiple safety barriers inside AXXIS TITANIUM to ensure that each detonator is immune to stray currents and most lightning strikes. This prevents high energy electrostatic discharges from reaching the sensitive fuse head.
Importantly, blast operators can count on reliable and safe firing every time. AXXIS TITANIUM’S applicationspecific integrated circuit (ASIC) design features a triple redundant firing switch that is extremely reliable for preventing misfires or uncommanded initiations.
Given the sometimes-complex environment of a blasting operation, AXXIS TITANIUM has been designed to withstand high dynamic pressure in holes with multiple charge decks.
“As a blast is fired, shock waves are generated from each exploding hole into the surrounding rock, creating very high pressure waves that can crush and damage the electronic components in unfired detonators, thus leading to misfires,” Brits says.
BME marketing manager Michelle Fedder.
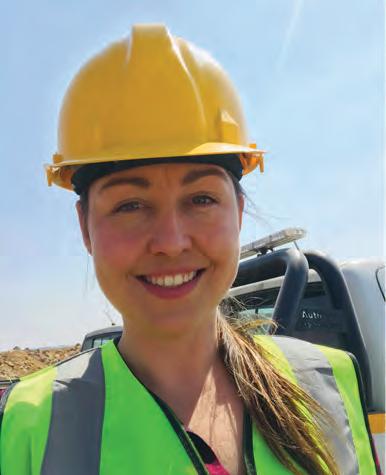
“With the higher strength shells and protection of the electronic components by encapsulation, AXXIS TITANIUM detonators are more resistant to dynamic pressure waves.
“Encapsulation also protects against the unlikely possibility of components heating up from external energy.”
Standing on the strength of BME’s significant research and development program, AXXIS TITANIUM has been tested in South African vanadium, coal and chrome mines.
A vanadium mine, for example, contains high iron content that can interfere with the communication between controller and blaster boxes, and between blasters and detonators.
But AXXIS TITANIUM has overcome this problem, the system is proven to retain its wireless communication range despite different commodities being mined.
When it comes to safety, there are no compromises. AXXIS TITANIUM fires the blasts with exceptional time accuracy, even at the extreme firing times of 35,000 milliseconds.
Mine workers can monitor every stage of the blasting process in real time. BME’s paper-free blast management system, XPLOLOG, captures and stores block activities
BME technical services manager Tom Dermody.
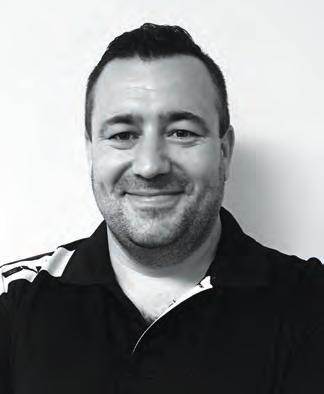
in the cloud, allowing operators to also evaluate blast records for future improvements.
“Mine employees can monitor their blasting operation and have a live feed of how it is progressing using Wi-Fi or GSM connectivity on site,” BME technical services manager Tom Dermody says.
“XPLOLOG has delivered efficiencies where the whole process of quality assurance and quality control are digitalised.”
BME has developed a complementary Blasting Guide application that is downloadable from the Google Play Store.
The app is useful for a rapid calculation and checking of blast designs, applicable to a greenfield site.
It includes advanced calculators, surface blast design rules of thumb, environmental guidelines and a BME contact director for every country.
“It replaces what used to be in a paper booklet and becomes a digital guide in the field,” BME marketing manager Michelle Fedder says.
These innovations demonstrate that BME has truly harnessed the power of digital technology in the blasting industry. By doing so, the company gives operators a world-class blasting experience.