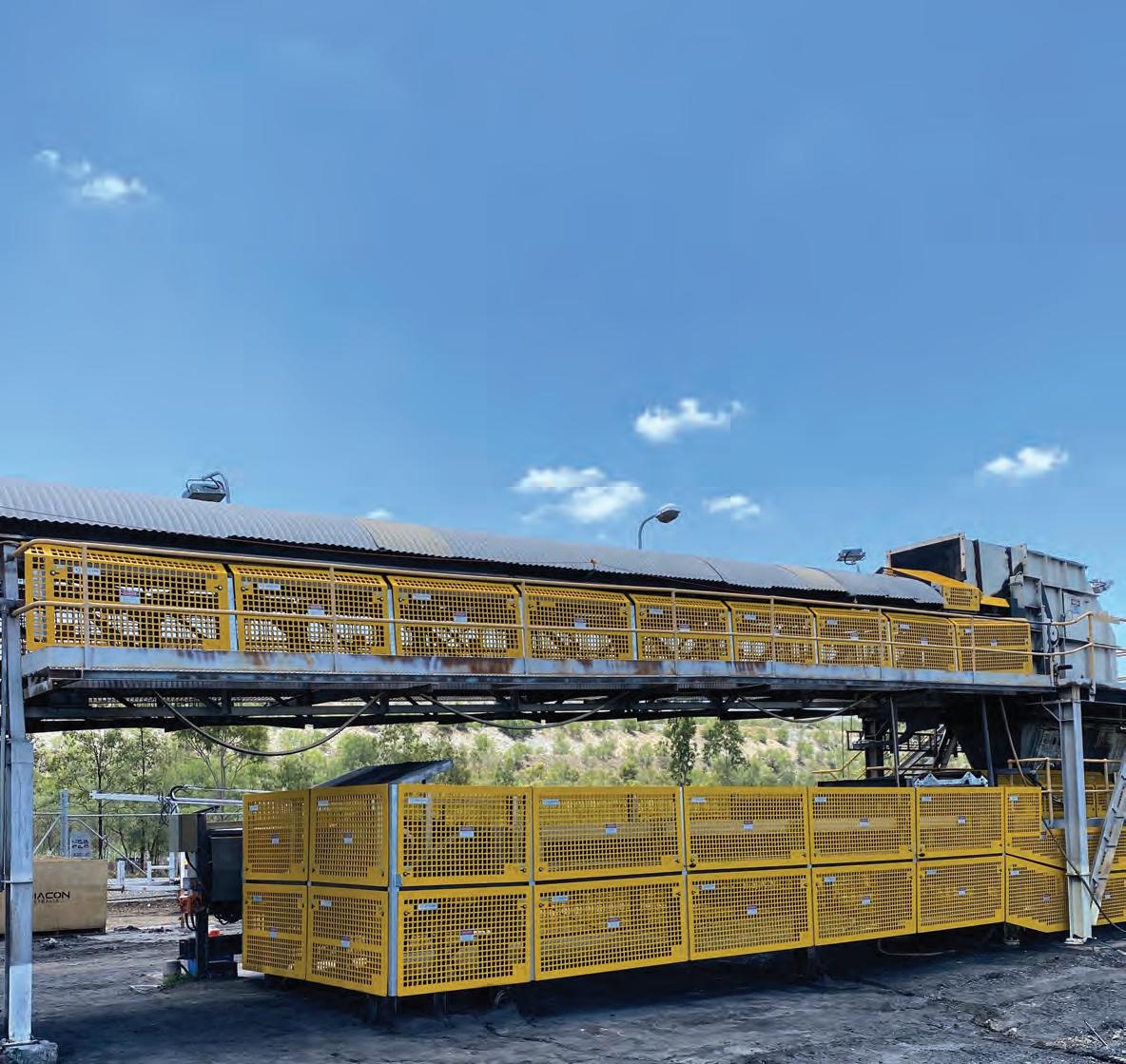
4 minute read
Conveyor safety vigilance a success story
Conveyor safety vigilance a mining success story
AS DIACON AUSTRALIA CONTINUES ITS WORK WITH AUSTRALIAN MINING COMPANIES, THERE’S A POSITIVE TREND PERMEATING THROUGH THE INDUSTRY: CONVEYOR SAFETY AWARENESS IS SKY HIGH.
When it comes to ensuring and progressing mine safety, Diacon Australia needs no introduction.
The conveyor guard specialist has been honing its craft for more than 20 years, continually improving its product and evolving with an everadvancing sector.
One of the main purposes of a conveyor guard is to protect workers, whether it be from rogue material flying off the fast-paced machinery or to prevent employees from entering the danger zone.
As Diacon Australia managing director Brendan Refalo explains, given their importance, it’s vital conveyor guards are practical to use.
“Diacon Australia guarding started on a coal mine in central Queensland. It was developed due to a demand needed on site for better quality, more easily removed and replaced guards that could stand the test of time because they don’t corrode and are lightweight,” he says.
“They’re important for mines, along with many other industries as well, because they are easy to use. When the conveyor is isolated, maintenance personnel can remove and replace the guards where they are supposed to be, and then lock them in place.”
“Just the fact that they get used and they get put back properly means that they potentially save lives.”
Diacon’s product has been developed this way simply to meet the requirements of the industry. Regular customer input and feedback has been vital to how the company’s product has evolved over the years.
Conveyor injuries are an all too common cause of injury on mine sites and become a major concern for employers.
“If you have a look at the stats of injuries and the fatalities that have occurred relating to conveyors, it is significant,” Refalo says.
The industry has never been more vigilant in addressing conveyor safety.
“There has been a huge number of people injured in conveyors and unfortunately a few deaths; the industry is dedicated to ensuring zero harm more so now than ever.
“So guarding is a vital part of striving for zero harm, and guarding to Australian Standards is even more important.
“Diacon Australia guards fit the bill and meet the practical requirements of on-site personnel. Our guards are lightweight and strong, and are designed to make removal and replacement easy.”
While conveyors have resulted in a significant number of injuries at mine sites, Refalo believes the industry has never been more vigilant in addressing the issue.
“The mining community is very conscious of making sure their conveyors are safe,” Refalo says.
“We are seeing that mining companies are regularly engaging consultants to do audits on their conveyors and the audit process obviously highlights concerns or potential risks in relation to the guarding. Once the potential risk is identified and recorded, they are vigilant about making changes to improve the guarding.”
Conveyor inspections and auditing can involve the creation of detailed reports on specific components of a conveyor or the entire conveyor system. Problem areas are identified within the report with the required actions to follow.
Refalo cites one of Diacon’s current mining partners as an example of the industry’s advanced awareness of conveyor safety.
“We’re doing a project right now in the Bowen Basin with a company who had a comprehensive audit done on all their conveyors and their response to making sure their guarding meets Australian Standards,” Refalo continues.
“They have an extensive document with many hundreds of pages which gives them the guidelines as to where they need to focus their efforts. Those requirements are minor in most cases, but in some cases those requirements may mean replacing the guards on an entire conveyor which would be a substantial investment.”
The mining industry can be fickle financially with stock prices rising and falling day by day. One thing that doesn’t change however, is the sector’s commitment to preventing injury on mine sites.
“Even in times where commodity prices might be falling and when budgets get tight on sites, something Australian mining companies don’t cut back on is the continuous improvement of safety systems,” Refalo says.
An example of how the Diacon product continues to evolve to meet the needs of its clients is the current implementation of stainless steel mesh inserts into its HDPE guards to improve visibility for cleaning and inspection aspects required around troublesome areas, like tail ends and gravity takeup units. Diacon Australia’s current work extends from Tasmania through to the coal-rich regions of Queensland and across to the iron ore expanses of Western Australia.
Diacon also provides conveyor guarding for the ports, an essential cog in the mining supply chain and something which Refalo says is a critical part of the business.
“We’ve always had a strong association with the ports because they are always looking for improved products that don’t corrode and that don’t require painting, aspects that limit the life of equipment at the ports. If you have a product that doesn’t corrode nor requires painting then that reduces the burden on the maintenance personnel,” he says.
Earlier this year, Diacon Australia also commissioned a new, purpose-built facility in Queensland in partnership with Consolidated Engineering Plastics Products – another feather in the cap of an unwavering patron of the mining industry.
Conveyor inspections and auditing can involve the creation of detailed reports.
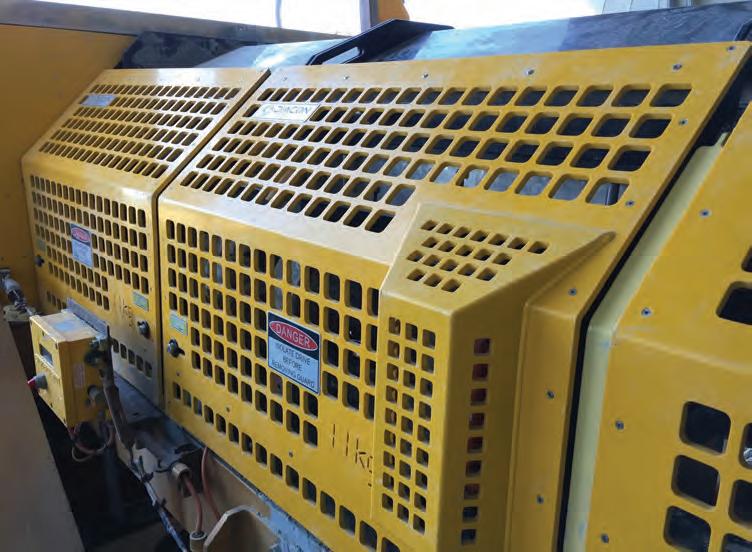