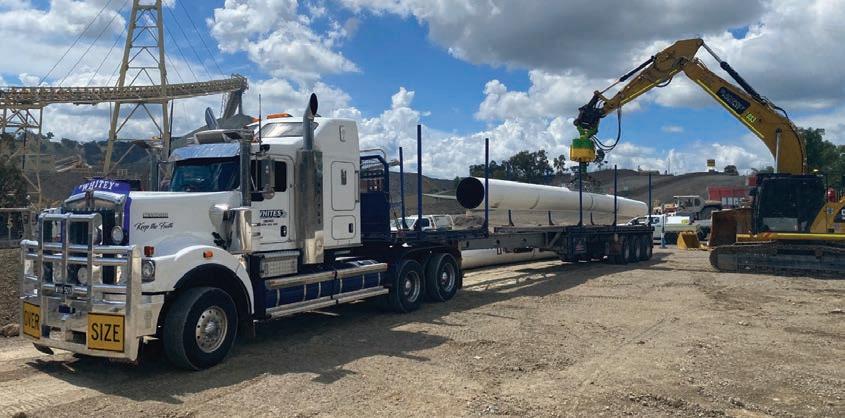
5 minute read
Five reasons to choose Pipeline Plant Hire for your VacLift solutions
There are plenty of grounds for choosing Pipeline Plant Hire (PPH) for VacLift solutions. PPH director Gerard O’Brien discusses with The Australian Pipeliner, five good reasons to turn to the experts for specialist equipment needs.
PPH has the largest fleet and most extensive range of VacLifts in the country. Not only that, but the machines are Australian designed and manufactured, meaning the company can avoid supply issues that have impacted the import economy.
PPH has just received a global patent to export its machines to the Americas. The company is recognised for its world-class safety standards and diesel-free design, meaning greater reliability, less noise pollution, and more environmental benefits.
Largest fleet, most extensive range
PPH currently has more than 50 VacLifts in its fleet – the largest fleet of VacLifts in the country, catering for a range of different pipe sizes and composition.
“The range is in what they call the pipe shoes. You need a different shape to suit the diameter of the pipe you’re lifting,” director Gerard O’Brien says. “We have the most extensive range of pipe shoes by far in the country. Whether it's poly pipe or steel, we have the range to support it.”
PPH can supply a suitably configured machine for any project. “We now have a range of VacLift equipment that spans from our smallest unit used to feed poly pipe into fusion welding machines, lifting a few hundred kilograms, through to our largest units capable of lifting large diameter high pressure pipe weighing upwards of 10 tonnes,” says Mr O’Brien.
“The thing that constrains you in VacLifts is the machine - not the capacity of the vacuum to lift the load. The design of the shoe in conjunction with the vacuum equipment may lift 30-odd tonnes. But the excavators you’ll see on a pipeline job may only lift 10 tonnes, for example. It’s generally the host machine that’s the constraint – not the capacity of vacuum.”
Operator interface, incorporating visuals, sound indicators and warnings, increase the level of safety on VacLifts.
Australian designed and manufactured

Much of the equipment required to handle long lengths of HDPE didn’t exist not so long ago. PPH soon recognised the need for long vacuum spreader bars and short vacuum shoes, suitable for highly flexible loads. The rest of the world has been playing catch-up in this area. Pipe lifting on pipelines is not a trial and error process, and PPH has rungs on the board when it comes to safely handling complex loads.
Because of the local design and manufacture, PPH has been able to circumvent many of the supply chain issues that have afflicted importers in the industry throughout the pandemic. “Being Australian designed, built and owned, we have a point of difference,” says Mr O’Brien. “We’ve got more demand than we’ve had since the three largest gas pipelines built down at Gladstone.”
PPH currently has machines in the field constructing the Fortescue slurry and water pipeline as well as a gas pipeline in Western Australia. “Because they are Australian designed and manufactured, we can also adapt and make specific enhancements for a challenge that a project may pose,” he says.
“Enhancements tend to come in the form of the ancillary products rather than the base machine, and PPH can offer custom solutions for any VacLift job.
“We once had a job where a client wanted to join two pipes with rubber rings where it was too difficult to push the two together. We came up with a solution to put a vacuum shoe on each side, and a hydraulic ram that pushed the pipes together.”
Mr O’Brien explains that this project was what they call a “do-and-charge” deal – a pricing model that accommodates time and materials at a set price per hour.
“The design was so successful that, on that particular project, it cut down the joining time so dramatically, that they’d done themselves out of money.”
This case study is a testament to PPH’s efficient and effective design solutions.
VacLift loads truck with long lengths of HDPE.
Worldwide patent
Last year, the company received licence on a worldwide patent and is now exporting its
technology to the Americas. O’Brien says this is a result of PPH’s industry-leading technology, meeting all technical, safety and environmental criteria in Australia and abroad.
Machines are supplied with all specified safety equipment, risk assessments and certification- respected nationally and beyond.
Safety
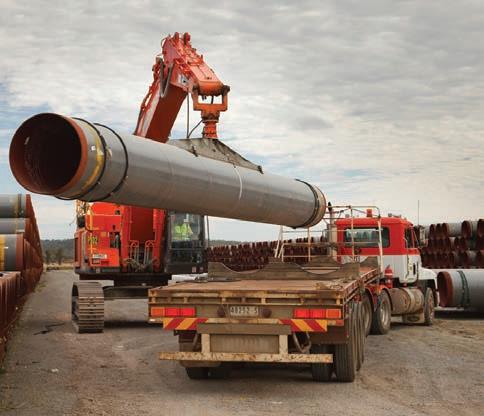
PPH’s machines feature special considerations to guarantee the health and safety of the operator. In 2013, the company was nominated for the APIA Safety Awards for its intelligent operator interface and custom safety developments. Safety features include a booster vacuum reservoir, fully integrated operator controls, ground-only release system, and a patented multi-fit hitch for use on multiple machine makes.
PPH developed a unique swivel joint allowing 360-degree horizontal rotation to the lifting beam and shoes. A sophisticated operator interface also incorporates visual, sound indicators and warnings to increase the safety level of our VacLifts over existing designs.
“It senses when the load is grounded: it won’t pick up unless it knows that it is sitting on firm surface. Similarly, it will not release the pipe if it is not fully lowered,” says Mr O’Brien.
These Australian designed and manufactured improvements the company has made to pipe handling, safety and productivity are precisely the reason PPH was nominated for the 2013 APIA Safety Award.
No diesel engine
One of the innovations PPH made to VacLift design was removing the auxiliary diesel engine.
“Typically with vacuum-lift hire, you’ll have to hire an excavator that has the VacLift attached. But the PL1500 is an attachment that goes on the client’s machine,” says Mr O’Brien.
“One of the reasons we went this way is because auxiliary engines are one of the most unreliable components of conventional vacuum lift attachments. The host machine tends to be more reliable and more capable of managing the Australian conditions.”
By removing the diesel engine, PPH has eliminated the necessity for additional fuelling.
“We removed the noisy dedicated diesel motor, and replaced it with a hydraulic motor driven from the excavator, which in turn reduces noise, heat, and burn hazards, as well as improving reliability,” he says. And less noise means improved communication between ground crew.
The hydraulic system has a more positive impact on the environment by reducing exhaust fumes and noise pollution.
PPH has the most extensive range of VacLift shoes in the country.
For more information visit www.pipelineplanthire.com.au
www.peternorman.com.au 1300 THE KEY (1300 843 539) pipework@peternorman.com.au
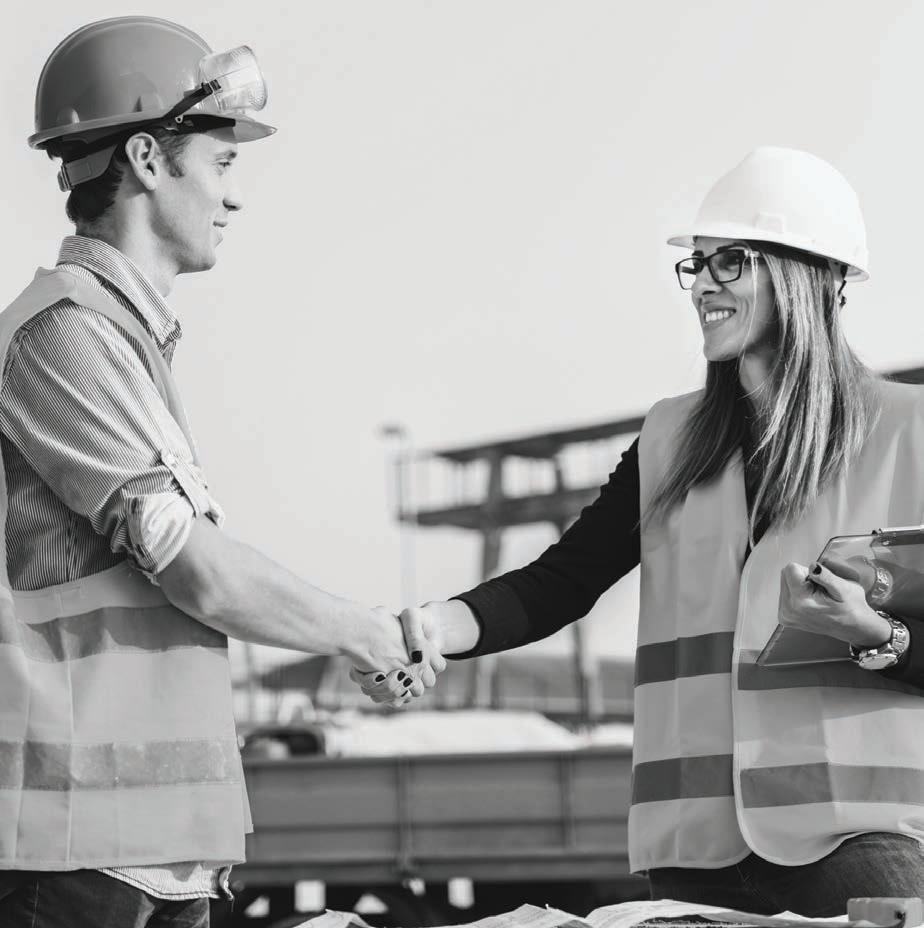