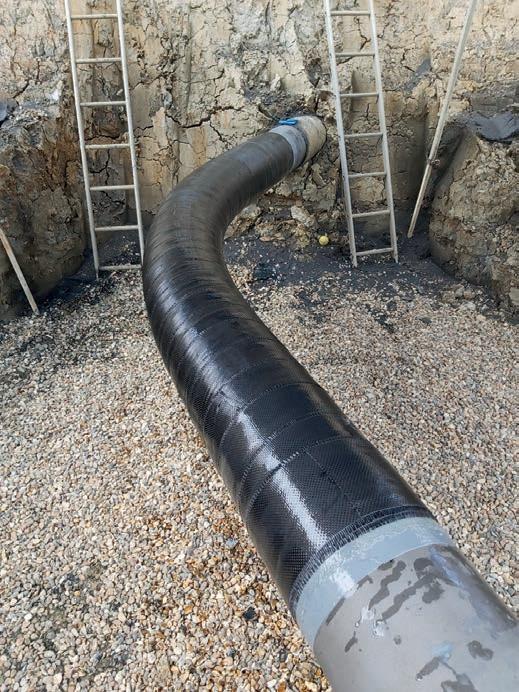
4 minute read
The ongoing journey of composite repairs for pipelines, process piping, tank and vessel repairs
from Pipeliner May 2022
by Prime Group
Composite repair systems are arguably the most versatile and robust solutions for pipeline rehabilitation and repair; however, their capabilities don’t stop there. PipeServ Director Geoff Gardiner summarises the history of the technology, their varied uses and previews how they could develop in the future.
For more than a century carbon steel has been the standard material for pipelines and piping systems. Over that time, countless new discoveries, techniques, and improvements have been made, and new pipelines laid today share almost nothing with their ancestors beyond their cylindrical shape.
With that in mind, let’s consider the recent advances in composite repair materials and technologies for these same pipelines. A composite repair is a combination of resins and fabrics applied over a damaged pipe area to restore any lost strength and help minimize or prevent future damage.
Often, these resins consist of epoxy, polyurethane, or vinyl esters but can contain more unique resins based on thermal or environmental needs. These combinations of fabric and resin are then applied over a damaged section of pipe.
Composite repairs can bring many damaged pipes to full service with the correct engineering, testing, and application. The specific benefits of using a composite repair include being lightweight, cost-effective, durable, safe, and expedient repair, to name a few.
The first composite repair system created and used in pipeline repair was the Clock Spring® system which is still available today. Using a precured composite with unidirectional fabric support oriented in the hoop direction, the Clock Spring system was thoroughly tested for wall loss features and dents.
Some more innovative uses have seen Clock Spring technology used as casing spacers and crack arrestors for the construction of new pipelines.
One of the more forward-thinking test programs demonstrated the longevity of a Clock Spring. The manufacturer of the technology, CSNRI, was able to obtain an in-service Clock Spring on a section of pipe that was installed in 1995 and recently removed from service intact.
With a 25-year-old sample on hand, end caps were welded on the 24 inch diameter spool and pressurised. With the worst defect identified on the pipe as a 12 inch long, 63 per cent deep defect, any significant weakening of the Clock Spring could result in a failure within the repair zone.
After several pressure increases and five minute holds, the pipe burst outside of the repair zone at 2,180 psi (150.3 bar) which was more than three times the maximum allowable operating pressure (MAOP) of this pipe. Using these test results alongside an engineering analysis on a per-defect basis, CSNRI demonstrated this repair method can last over 50 years in most conditions under continuous use.
It’s probably safe to say there are likely very few other repair systems with this type of real-world data to reference. The use of composite repairs, Clock Spring or otherwise, has become a commonly accepted repair technique for corrosion and dents, but this article isn’t about origins; it’s about advancements and changes.
Improvements in the engineering capability behind composite repairs are not the only thing pushing the composite repair industry forward. Sometimes, it takes thinking outside of the box, or in this case, from outside of the pipe.
The CSNRI ThermoWrap family of products highlights the diverse capability of composites. The ThermoWrap family contains four different products but uses the same fabric to serve the purpose of wall loss reinforcement and leak containment.
All four systems excel at leak containment under an array of temperature conditions and enable long-term solutions. ThermoWrap and ThermoWrap MT provide an ambient cure resin with exceedingly good chemical resistance for services to 156°C. ThermoWrap HT and ThermoWrap 500 can be used up to 220°C and 260°C, but these require heat to cure properly.
Atlas™ is a high-modulus, bi-directional carbon fiber and epoxy system applied to pipelines and piping systems found with corrosion or thirdparty damage. One of the most significant changes that have occurred in the use of composite material, has seen CSNRI’s Atlas™ repair system used on longitudinal crack or cracklike features, including seam-weld anomalies.
Starting in 2015, the Atlas repair system has been involved in three Joint Industry Programs and nearly a dozen client-specific test programs. Most of the testing performed to date has been on seam weld defects or linear indications in the body of the pipe; however, additional testing is taking place looking at stress corrosion cracking (SCC) as well as girth weld reinforcement.
With testing in burst and extensive cyclic fatigue testing – across hundreds of repair samples – the Atlas repair system is now successfully repairing defects previously thought unrepairable by composites only ten years ago.
By continuously exploring and testing with new fabrics, new resins, and new engineering methodologies, we are just scratching the surface for the capabilities of composite repair systems. Composites truly are a durable, economical, and highly customizable solution.
With just a few examples discussed here, the diversity of composite solutions used in solving today’s integrity issues has already been demonstrated. There are still significant advancements to be made before the limits of composite repair technologies are found. But we can already state, with confidence, that a composite repair is not ‘just’ a composite repair; it can be so much more in the right hands.
ATLAS applied to a pipeline bend.
For more information visit www.pipeserv.com