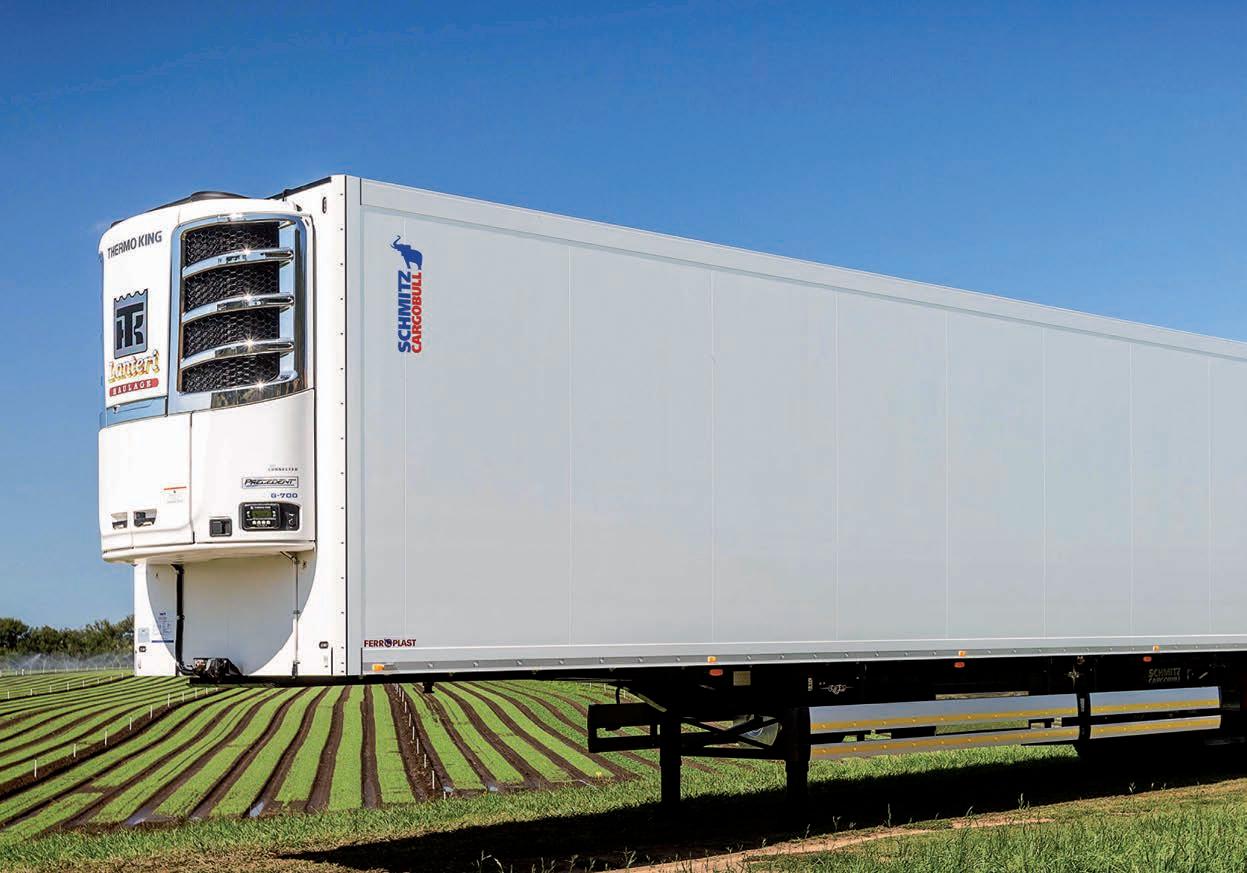
13 minute read
Refrigerated Transport Equipment
Market value
TO KEEP FRESH PRODUCE AT CONSTANT TEMPERATURES, WHILE MAINTAINING BUSINESS GROWTH BETWEEN MELBOURNE AND SYDNEY, LANTERI HAULAGE HAS INVESTED IN THE LATEST SCHMITZ CARGOBULL REEFERS.
Kim McDonald grew up in the transport industry with his family running milk tankers for a local dairy company. He started his truck driving career at the age of 18 and has been operating and maintaining heavy vehicles ever since. In 2014, an opportunity arose for Kim to purchase Lanteri Haulage in Bairnsdale, Victoria, from former owner Sab Lanteri. Kim has seen the business grow from two trucks in the fleet to nine – all coupled to 24- or 26-pallet refrigerated trailers. “I take great pride in running a wellmaintained fleet of trucks and trailers,” he says. “In addition to providing a consistent and reliable service, we have also been complimented by our valued customers for our immaculate fleet presentation.” Lanteri Haulage’s principal depot is based in Lindenow, East Gippsland, and the facility has all weather access along with warehouse and cool room storage for all refrigerated produce. The company also has warehouse and cool room facilities in the Melbourne fruit and vegetable market, enabling Kim’s team to maintain temperature control on the produce it stores. “We have a strong regional and metropolitan network,” Kim says. “We are positioned as a highly regarded distributor and a much-respected logistics partner to our customers. Fruit and vegetables are our main freight we transport along with dry freight when required to service our clients.” The Lanteri Haulage fleet comprises nine Volvo prime movers. “Four FH540 I-Shift dual clutch, three FH540 with I-Shift along with one FM540 with I-Shift all being Globetrotters with the final one in the fleet affectionately known as ‘The Old Girl’ doing most of her work locally after being retired off the long runs,” Kim says. “We have found that the Volvo trucks are most suited to our business and with having a local Volvo dealer and Volvo servicing on hand, our fleet is serviced regularly, well maintained and any issues that may arise our Volvo dealer and representatives are ready to provide the answers.” As for the reefers, Lanteri Haulage has three 26-pallet Schmitz Cargobull units and one
Schmitz Cargobull refrigerated trailers have excellent thermal properties that help keep storage temperatures constant.

This reefer has a 26-pallet capacity.
When the trailer refrigeration unit is at idle, fuel consumption is down, and a lower rev rate on the compressor means less wear and tear on the units.
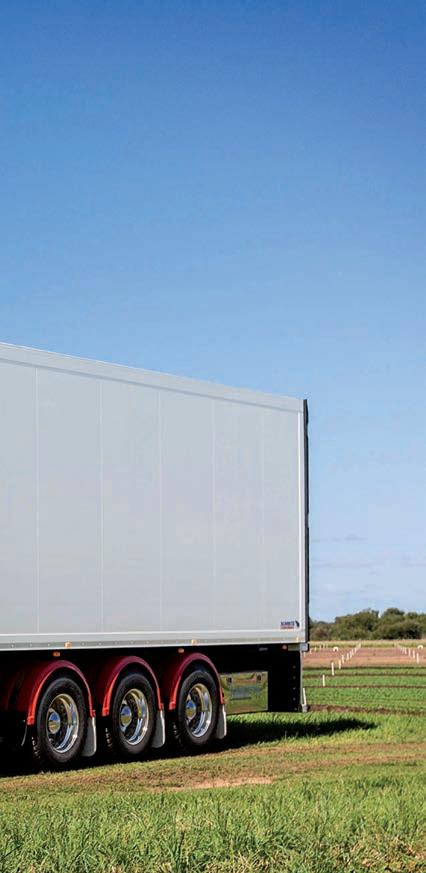
24-pallet Schmitz Cargobull trailer. “All of our trailers are kept cool by Thermo King trailer refrigeration units to ensure the produce is kept at consistent temperatures from loading to unloading at their destinations,” Kim says. The company fleet runs daily to Melbourne metro and into the Melbourne fruit and vegetable market at Epping. “Our fleet also runs Melbourne to Sydney five times a week transporting refrigerated produce into one harvest for processing to all the major supermarket chains throughout Australia,” Kim says. “We proudly support our local vegetable growers from far East Gippsland through to Central Gippsland providing on farm pickup for all produce heading into both local and metropolitan processors and markets. “Our growers appreciate the respect and constant communication given to ensure that all their transport requirements are met in a timely and professional manner. “This in turn allows our valued customers/ growers/clients and logistics partners to be reassured that their freight gets from A to B without any interruption.” Given the extreme heat conditions these trailers must withstand while in transit between Melbourne and Gippsland, Kim says the Schmitz Cargobull trailers hold up in the hot and ambient temperatures. “The Schmitz Cargobull trailers are very well insulated and therefore once down to the desired temperature maintain that temperature with ease even on the warmest of days during our growing season,” he says. “All our trailers are pre-cooled during the warmer months prior to produce being loaded as this helps greatly in keeping the pre-set temperature at a constant without the Thermo King units having to work overtime to bring the temperature down.” The latest addition to the Lanteri Haulage trailer fleet is a 26-pallet double loader. “The Schmitz Cargo Bull fridge van features BPW air suspension over a tri-axle configuration “ Kim says. “The other two 26-pallet trailers in the fleet are of similar configuration apart from one having a constant tyre inflation system on the BPW axle. “Our original and first Schmitz Cargobull 24-pallet trailer has proven its worth in the fleet and a pioneer in the company’s investment into the 26-pallet version.” Kim says the most important feature of these trailers is the flat flooring which makes it easier to guide a pallet jack to load and unload refrigerated produce. “The width of the van is generous without being oversized, enabling pallets and bins to be loaded with ease,” he says. “Having that extra ‘wriggle room’ to work with can cut down on loading and unloading times – rather than struggling with pallets. “The trailers are very well insulated and keep the temperature constant without the need for the Thermo King units to be working at full capacity trying to keep the produce at the desired temperature.” To date, the service and aftersales support from Schmitz Cargobull has been on-hand when required according to Kim. “The team are only a phone call away for all our enquiries and should we require spare parts – they are sent up express or if we have a truck in the area – we pick up direct.”
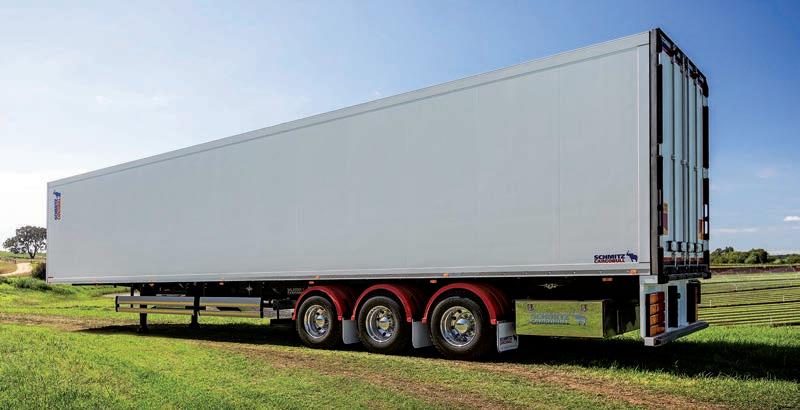
Contact
Schmitz Cargobull Australia Unit 2/221 Browns Rd Noble Park VIC 3174 Ph: 03 8794 6600 Web: www.cargobull.com.au
Primed for the long haul
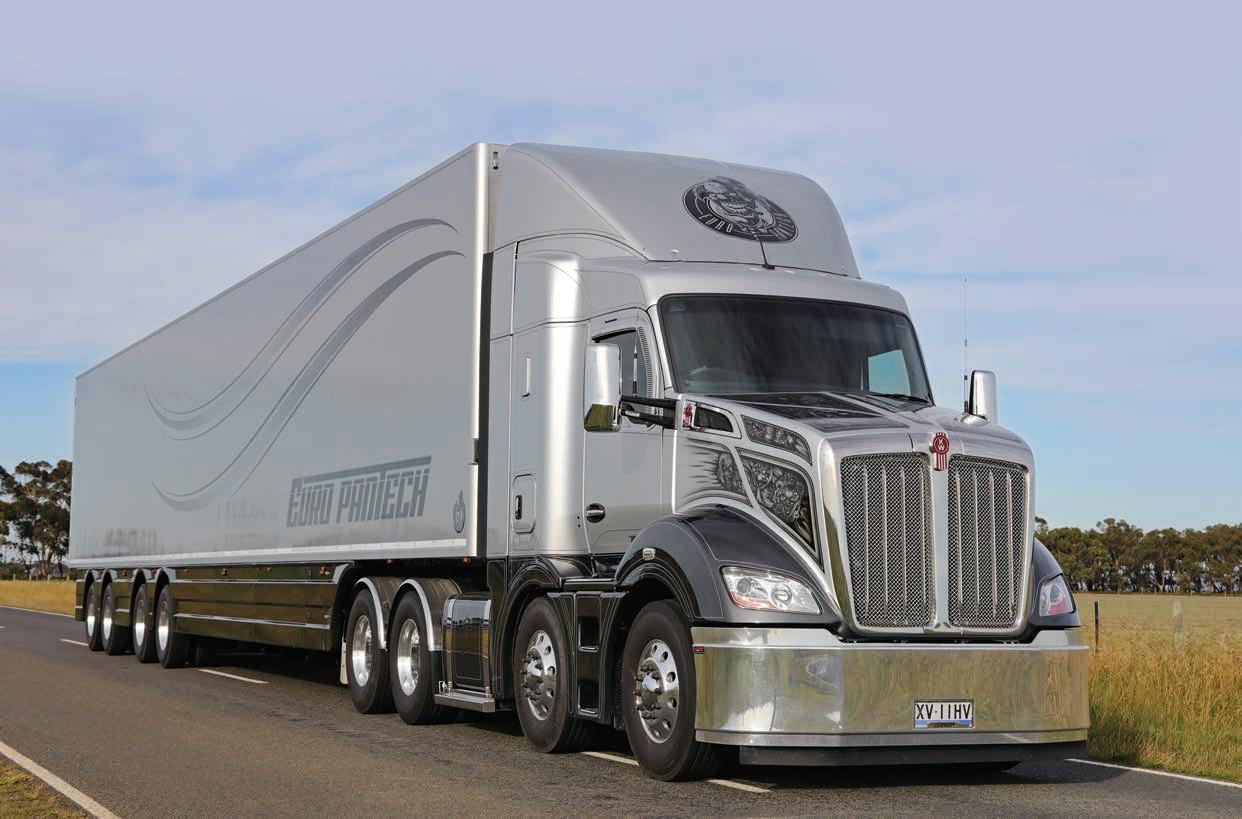
IN A BID TO DRAMATICALLY INCREASE OPERATIONAL EFFICIENCIES – NOTABLY FUEL AND TIME – IN LINEHAUL TRANSPORT OPERATIONS, EURO PANTECH OWNER DAVE MURPHY TOOK FULL ADVANTAGE OF PERFORMANCE-BASED STANDARDS TO DESIGN AND CONSTRUCT A 20.2-METRE REFRIGERATED TRAILER WITH A 33-PALLET PAYLOAD CAPACITY.
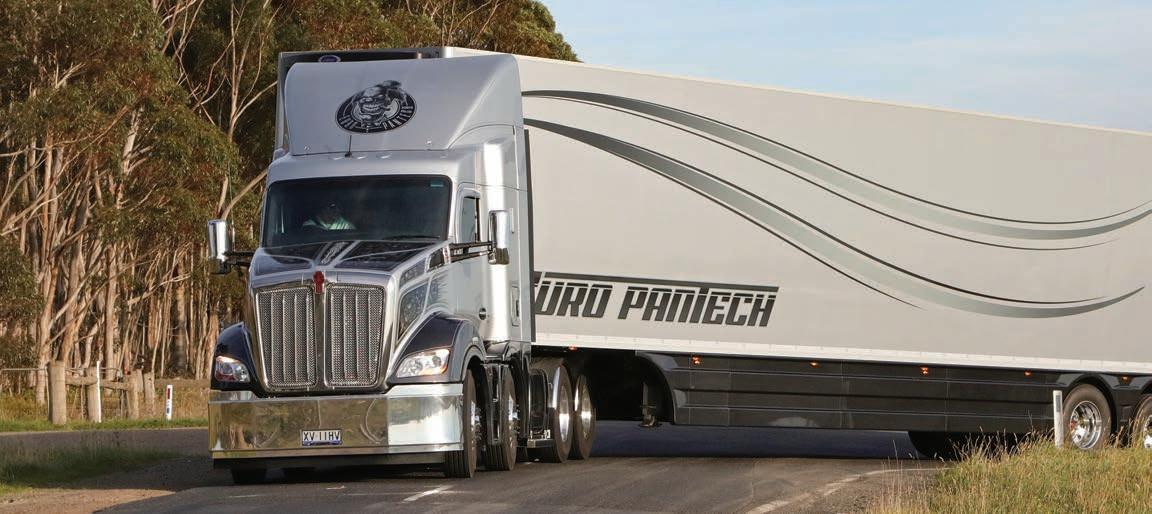
Efficiency is key in any transport operation, even more so with refrigerated transport where the cost of running the fridge plants adds to overall running costs. There’s also time efficiency. While refrigerated B-doubles provide a substantial increase in payload and cargo capacity over standard semi-trailers, the trade-off is the extra time it takes to split the combination for dock loading and unloading at either end of the trip. Additionally, the need to run a fridge plant on each trailer adds considerably to both the initial purchase and whole-of-life running costs. It was these factors and more that led Dave Murphy to develop super long refrigerated single trailers that he believes alleviate a common complaint with B-doubles doing linehaul work. “There’s too much work involved splitting and reconnecting B-double combinations at either end when running linehaul routes such as Melbourne to Sydney,” Dave says. “Due to this issue it’s necessary to have support crews involving local drivers who do the loading and unloading at either end, which adds considerably to the cost of doing business. “My initial reason for starting Euro Pantech was to supply imported refrigerated trailers from Europe to the Australian market,” Dave says. “In my opinion the press made panels of these vans are superior to the vacuum
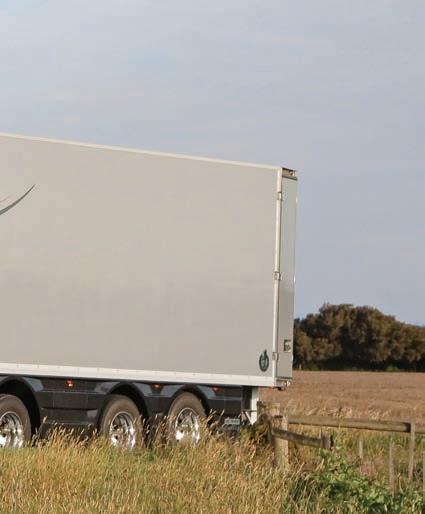
made panels we use here, and it was during discussions about obtaining licences to do this that I discovered the possibilities enabled by Performance-Based Standards (PBS).” Dave engaged with Marcus Coleman, Managing Director of PBS certification company Tiger Spider and, after initial discussions, discovered that combinations could be 20 metres (16.75-metre 28-pallet van) under Level 1 PBS. “Then, after some more research of the regulations, we worked out that a 20.2-metre single trailer was permissible under Level 2A PBS,” Dave explains. “I calculated that this would enable us to carry 33 pallets in a single van, but we then needed to validate thermal efficiency of the van within that longer space to ensure adequate cooling capacity.” When it came to the axle configuration of the trailer, Dave decided to incorporate a bi-tandem axle setup similar to that used in super-dog tippers. “This allowed for a seven-tonne increase over a traditional quad under Tier 3 Bridge assessment,” he says. “It makes the van almost impossible to
Fast Fact
High thermal efficiency panels and a slippery shaped combination make for superior fuel efficiency of both the truck and fridge plant.
Fast Fact
Front and rear self-tracking axles provide the 20.2 metre 33-pallet Euro Pantech trailer with a similar swept path to a standard B-double. overload with normal industry sized pallets provided a twin-steer prime mover is used.” To ensure swept path dimensions were met, the front and rear axles on the trailer self-steer and can also be lifted when travelling empty. In addition, the rear of the trailer is tapered and incorporates bi-fold doors – which contributes to aerodynamic efficiency and enables one pallet space at the very back of the trailer. Dave concedes, however that the bi-fold system is a step too far for most operators who only foresee damage from drivers. Maximised fuel efficiency is key to success in transport, Dave says, adding that having one trailer to cool rather than two leads to significant savings in fridge fuel usage. He also contends that the relative lightness of the Unitrans panels contributes to the Euro Pantech’s tare weight of 13 tonnes. He mentions that his Italian based panel supplier Unitrans is one of Europe’s elite panel makers and has been at the cutting edge of van building for many years. According to Dave, while not mass produced, the panels have proven to be durable and easily maintained over a long life – 12 years at maximum grade on the European grading or downgrading system. It’s a standard Dave believes Australia should adopt to ensure consistent thermal qualities of refrigerated equipment. Euro Pantech’s fuel-saving features – including the aerodynamically enhanced prime mover close coupled to the Euro Pantech trailer with its unique boat-tail rear end – should pique the collective interest of refrigerated linehaul operators across Australia. “Fuel efficiency is affected by aerodynamics and rolling resistance (weight), so we have aimed to maximise both wherever possible,” Dave says. “Across 110,000 kilometres, we have averaged 37l/100km or 2.7km/l – and this is improving as the Cummins X15 engine beds in. “What would a 25 per cent saving in fuel do for your business’s bottom line?” Dave asks.
Contact
Euro Pantech PTY LTD 340 Forest Road South, Corio, VIC 3214 E: Dave@europantech.net Web: Europantech.com.au
Driven to the edge
CARRIER TRANSICOLD IS LAUNCHING ITS FIRST AUTONOMOUS ELECTRIC REFRIGERATION SYSTEM, THE VECTOR ECOOL. SEVERAL COLD CHAIN CARRIERS ACROSS AUSTRALIA ARE PLANNING TO INSTALL THESE STATEOF-THE-ART UNITS TO BOOST PRODUCTIVITY AND ENERGY EFFICIENCY.
Fast Fact
For more than 50 years, Carrier Transicold has been an industry leader, providing fleets around the world with advanced, energyefficient and environmentally sustainable refrigeration systems. Carrier Transicold helps improve the transportation and shipping of temperature-controlled cargo with a complete line of equipment and services for refrigerated transport and cold chain visibility. Specialised business unit, Carrier Transicold, has reaffirmed its commitment to reducing emissions, improving sustainability and increasing efficiency across the refrigerated transport sector with the launch of the Vector eCool – the first fully autonomous, all-electric engineless refrigerated trailer system. Carrier Transicold is a part of Carrier Global Corporation, a leading global provider of innovative heating, ventilating and air conditioning, refrigeration, fire, security and building automation technologies. “We believe the Vector eCool represents the future of refrigerated trailer technology,” says Carrier Transicold International Truck & Trailer President, Victor Calvo. “It’s one of the most exciting new products we have ever
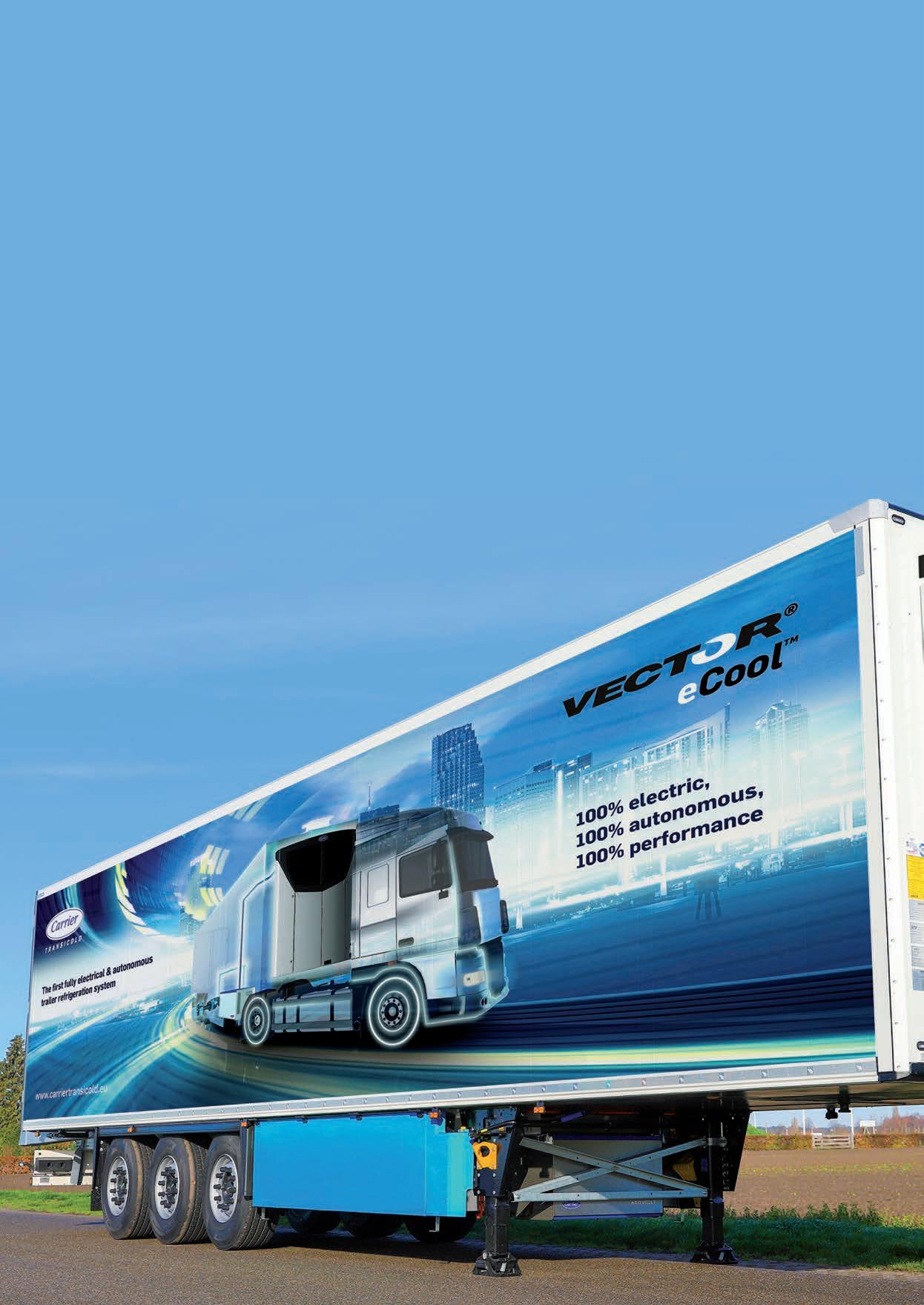
brought to market. The launch follows years of research and development, including extensive real-world testing with prototypes operating in customer fleets.” Suitable for operation with the engineless versions of Carrier Transicold’s Vector HE 19 and Vector 1550 E, the Vector eCool combines the company’s E-Drive all-electric technology with a new cutting-edge energy recovery and storage system. This converts kinetic energy generated by the trailer into electricity, which is then stored in a battery pack to power the refrigeration unit. This loop creates a fully autonomous system that produces no direct carbon dioxide or particulate emissions. When the refrigeration unit is operating on battery power, Carrier Transicold’s energy management system will automatically switch on when the charge reaches a certain level and conditions, initiating the generator to recharge the battery to ensure full refrigeration capacity.
The eCool system can also be plugged into the electrical grid when the trailer is parked and will fully charge in under four hours. On the road, the battery pack is recharged using power generated by the axles and the kinetic energy created under braking. When used with Carrier Transicold’s flagship Vector HE 19 unit, the Vector eCool can provide even further reductions in energy consumption. Even with the system’s axle generator and battery pack fitted, it is still significantly lighter than a standard diesel unit with a full tank of fuel. The Vector eCool is also PIEK-compliant, meaning when used with the City versions of the Vector HE 19 and Vector 1550 E, operating noise is below 60 dB(A).
Combined with its emissions performance, the Vector eCool provides the ultimate solution to ever-tightening inner-city and urban regulations. Carrier Transicold Australia Product & Aftermarket Solutions Director, Kelly Geddes, says the Vector eCool was developed to provide cold chain carriers with a flexible solution where the trailer is completely autonomous as it is today with a standard diesel solution. “The type of power source on the prime mover is irrelevant and no modifications to it are required,” he says. “Our goal is simple: don’t change customer behaviours and company structure to be able to provide a sustainable solution.” The system, according to Kelly, runs the Carrier Vector refrigeration unit in standby mode when plugged in at the distribution centre. “When the Vector unit is off, the system will switch to charging the battery if required,” he says. “The system also runs the Carrier Vector refrigeration unit on-road using energy from the trailer axle. When the refrigeration unit is off, the axle will recharge the battery pack or switch off if not required. The system also runs the Carrier Vector electric refrigeration unit in full autonomous mode using only stored battery power when the trailer is not moving or when grid power is not available.”
We believe the Vector eCool represents the future of refrigerated trailer technology. It’s one of the most exciting new products we have ever brought to market. The launch follows years of research and development, including extensive real-world testing with prototypes operating in customer fleets.
Fast Fact
Carrier Transicold’s latest innovation – the Vector eCool – is an engineless system based on an alternative power source to operate Carrier trailer refrigeration units for all applications from long haul to urban distribution. The alternative power source, in this instance, is a combination of a modular battery pack unit (energy storage) and an axle generator (energy recovery) as well as standby power to run the E-Drive architecture. This solution is also compatible with the Iceland series Carrier truck engineless product.
Contact
Carrier Transicold Australia Ph: 1800 448 166 Web: www.carrier.com.au