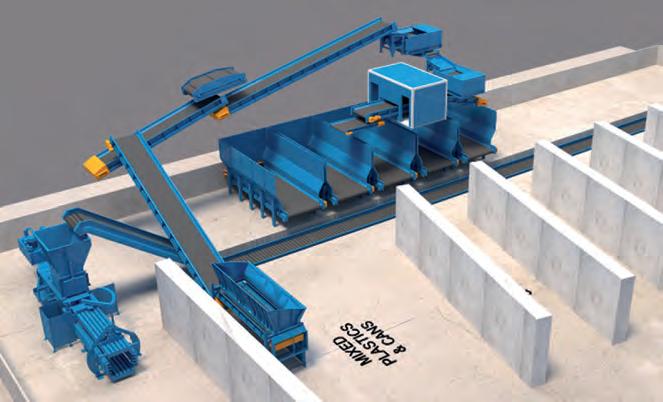
9 minute read
MINUTE MATERIAL RECOVERY
WASTE MANAGEMENT REVIEW SPEAKS WITH TREVOR SMART, TURMEC UK MANAGING DIRECTOR, ABOUT THE RECOVERY POTENTIAL OF MINIATURE MATERIAL RECOVERY FACILITIES.
When the Federal Government launched an inquiry into Australia’s waste management and recycling industries in October, Committee Chair Barnaby Joyce said the committee would examine international best practice.
The inquiry will consider opportunities to better manage domestic waste, as well as current impediments to innovation.
It’s a welcome move for Trevor Smart, Turmec UK Managing Director, who says the Australian waste industry could learn a lot from the UK’s approach to resource recovery – notably the uptake of mini material recovery facilities (MRF). He says that a series of events on his recent trip to Australia has him thinking about potential solutions to the country’s current recycling challenges.
Flying from the UK to attend Waste Expo Australia in 2019, Trevor arrived in Melbourne at a time of industry flux. The Council of Australian Government’s waste export ban had just been announced, Victorian councils were dealing with the collapse of SKM Recycling and container deposit scheme discussions were challenging the efficacy of kerbside collection.
Of most interest to Trevor, however, was how the amalgamation of these issues highlighted an opportunity to reshape Australia’s resource recovery and logistics network.
“In Melbourne I met a councillor from a small rural community in Victoria. He explained that the
Turmec sees potential for widescale implementation of mini MRFs across Australia.
demise of SKM had placed a lot of local authorities under financial and operational pressure,” Trevor says.
“In addition to the loss of this facility, the fact that the council’s recyclates had to travel over 400 kilometres to an MRF meant there were few alternatives.”
This lack of infrastructure capacity, parried with low recyclate tonnages, creates a challenging situation for smaller councils, Trevor says.
Following SKM’s collapse, many rural councils were forced to transport materials further afield, or in some cases, simply revert to landfill.
Trevor adds that the collapse of SKM is a story that’s played out globally numerous times, meaning international approaches can serve as a case study.
Over the course of Waste Expo Australia, Trevor says he had multiple conversations about the applicability of greater kerbside separation in Australia. He adds that the idea was routinely challenged, with many suggesting the economic cost would outweigh recovery benefits.
“We saw the same reaction in the UK when kerbside sorting was introduced. But from our experience, kerbside sorting was a successful move that greatly improved recycling rates and recyclate quality,” he says.
While Trevor admits kerbside separation can be challenging in high
density urban areas, he says suburban and rural implementation is simple.
Referencing urban planner David Gordon’s 2016 analysis of Australian cities, Trevor says 86 per cent of the population live in suburban or exurban neighbourhoods.
“Only 14 per cent of Australians are living in high-density housing, suggesting greater kerbside separation would be well suited to this country. For it to work, however, the system needs to be supported by parallel investment in mini MRF’s.”
Under Trevor’s plan, households separate containers, paper, cardboard and glass. From there, the material is collected by multi-compartment vehicles – eliminating many of the issues associated with kerbside contamination.
“Materials are then delivered to a mini MRF for further sorting, for instance, separating ferrous and aluminium containers from plastic, before baling and onward sale or further processing.”
Trevor adds that paper and cardboard would be baled and stored, ready as a saleable product.
“Glass would also be stored in the yard area for bulk transportation to a reprocessor,” he says.
“This system would not only suit low tonnage, but also give value to the recyclates, whereby semi-sorted clean materials can go directly to a reprocessor or exported for further sorting.”
Trevor says the concept of a mini MRF is simple, with widescale implementation potential across Australia.
He adds that Turmec’s comprehensive engineered recycling solutions cater for a wide range of tonnages and material applications.
“We integrate equipment from market leading suppliers in waste separation technology to produce a high-quality separation process with 99 per cent recovery rates,” he adds.
Trevor says the cost effectiveness of mini MRFs, paired with increased recyclate quality and saleability, has been proved in many UK local authorities.
A 2016 study commissioned by the Welsh Government, for instance, shows switching to source-separated recycling collections could save Welsh councils over one million euros a year.
“Other benefits such as employment, increased householder participation and a reduction of residual waste are also evident in UK studies,” he says.
“While the initial capital expenditure for the vehicles, containers and mini MRFs is going to be higher than refuse collection and transfer vehicles, when compared to MRF gate fees, transportation cost and material quality, the advantages are clear.”
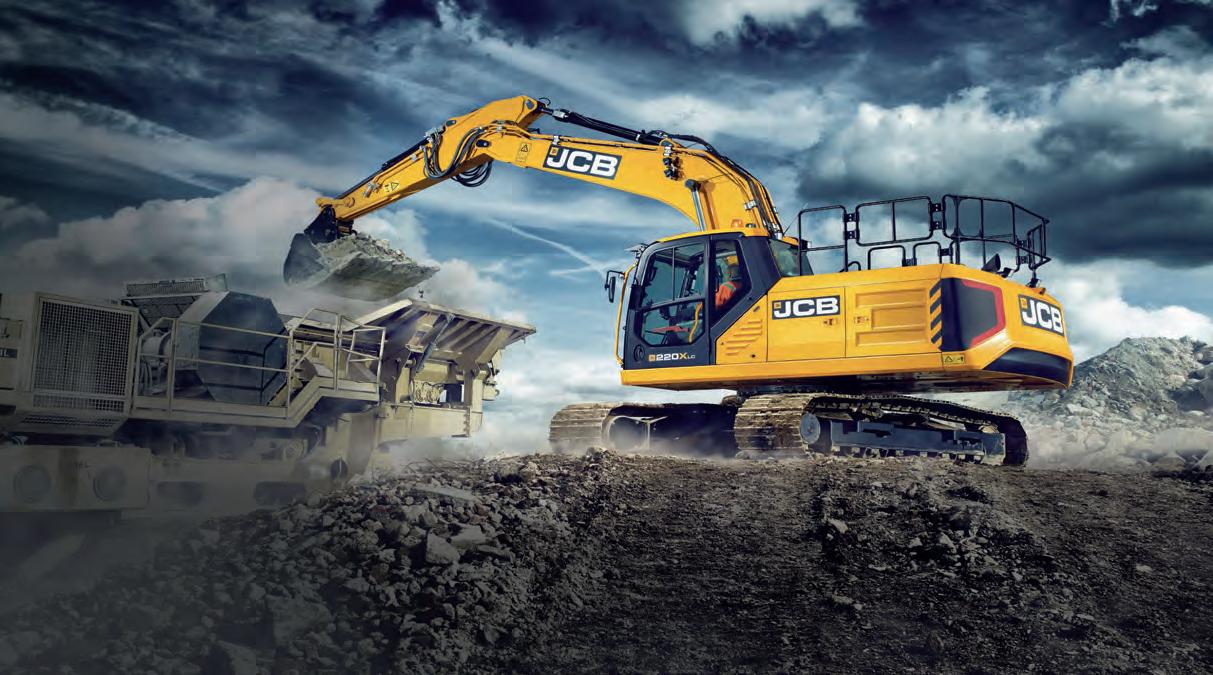
EXPERIENCE THE NEXT LEVEL
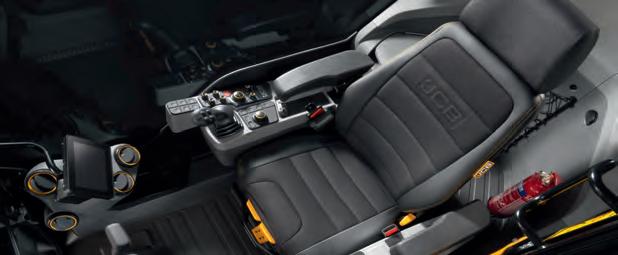
NEXT LEVEL PERFORMANCE PRODUCTIVITY + COMFORT
Sustainable mining gains traction
ADAM HOLLAND, CDE META, SPEAKS WITH WASTE MANAGEMENT REVIEW ABOUT HOW WET PROCESSING CAN TRANSFORM MINING WASTE INTO A SUSTAINABLE VALUE-ADDED RESOURCE.
While sustainable mining might appear like a contradiction to those in the stereotypically green resource recovery industry, it’s a movement that’s gaining global traction.
With rising demand for quality metals, in addition to increasingly stringent environmental legislation, protecting finite natural resources and extracting value from “waste” is not just environmentally sound, but good business.
For CDE Meta, the mining arm of international wet processing design and manufacturing company CDE, delivering sustainable mine operations via iron ore beneficiation is central to its “New World of Resource” purpose.
According to Adam Holland, CDE Meta Head of Business Development, with billions of tonnes of low-grade and overburden iron ore stockpiles around Australia, there is a growing appetite to invest in sustainable practices.
“CDE strives to make it as easy as possible for companies to use their waste products for the greater good, while also delivering return on investment,” Adam says.
“We’re committed to maximising product value while reducing environmental impact. Sustainability is at the heart of all CDE projects.”
CDE was recognised for its commitment earlier this year, winning two awards, one in Ireland and one in South Australia, for its Iron Baron and Iron Knob projects with SIMEC. The two awards, gained on the same day at opposite sides of world, are a testament to the global reach of the company and the strength of its sustainability driven purpose.
The awards, Adam says, highlight that while sustainable mining might not be taking over the sector just yet, solutions are available, and a return on investment is possible for resource companies interested in taking a greener approach.
The SIMEC projects, commissioned in 2017, involves two separate wet processing plants with a combined capacity to convert 17 million tonnes of historic lowgrade iron ore overburden waste into a high-value product. Without processing, iron ore waste often sits in unused stockpiles.
“With a processing capacity of 950
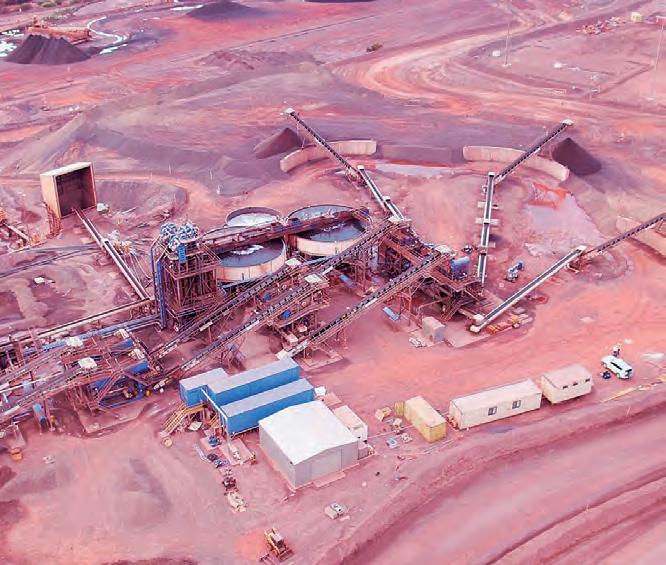
tonnes per hour, the two plants are successfully recovering high-quality iron ore from 100-year-old-plus-low grade mining waste feed material,” Adam says.
“Our plants beneficiate iron ore waste at 42 to 53 per cent Fe content through washing and gravity separation up to 63 per cent, at an almost 50 per cent yield.”
CDE was approached by Arrium (shortly after it was acquired by SIMEC) in 2013, before signing a design and construction contract in 2016.
“Because they were dealing with a historic stockpile, and therefore variable feed, SIMEC recognised CDE’s modular approach as a differentiating factor with inbuild flexibility,” Adam says.
“SIMEC understood the inherent value of its iron ore waste but needed our assistance to develop a costeffective beneficiation solution.”
While the plants, Iron Baron and Iron Knob, engage similar processes, Adam says the Iron Baron facility is more complex – beginning with a 42-millimetre down feed.
Each process module is spaced out and separated by conveyors and pipe runs. This, Adam says, provides operators with superior access and flexibility when maintaining the plant and allows additional processes to be added for optimisation with minimal downtime to cope with feed material that changes periodically. The Iron Baron process begins with two L55 hoppers, each feeding 350 tonnes of material per hour. Conveyors then transfer material into CDE’s patented P2-108 double deck infinity screens which wash and split the ore between fine and course beneficiation circuits.
Following initial screening, the course fraction travels to CDE’s AggMax – a combination of a Rotomax logwasher and dewatering screen.
“This is where the ore is scrubbed to liberate any smaller particles and break off impurities,” Adam says.
“It has performed exceptionally well – running for well over a year before we had to change out the paddles.”
Once the material is cleaned
“What sets these plants apart is CDE’s ability to design a modular solution, tailored to SIMEC’s unique requirements, delivered on a turnkey basis for cost-effective operations in a mining and iron ore context. This provides a superior return on investment for SIMEC,” he says.
In addition to effective return on investment, Adam says CDE is
Adam Holland, CDE Meta, Head of Business Development.
and scrubbed, it travels up more conveyors for dry screening, and then enters a fine or coarse jig for gravity separation.
“The plant then separates material into three stockpiles: a course product, fine product and rejected material,” Adam says.
“Given the nature of our process, however, even the rejected material can be reclaimed, with SIMEC using it for road construction around the mine.”
Adam says attention to maximum reuse was also behind the decision to install AquaCycle thickeners at the site. The thickeners, he says, produce a sludge from the reject slimes and enable recycling of 90 per cent of process water back through the plant.”
Additional benefits of the unique CDE modular solution, Adam says, include minimal civils, a faster, safer and reduced risk installation due to factory testing and per commissioning process, as well as reduced capital and operational expenditure. committed to providing ongoing customer care, adding that it works with a “customer-for-life model”.
“As part of this project, CDE has also invested in a significant vendor-held spares consignment that SIMEC can draw down as and when required,” he explains.
“We also have two full-time employees who work at the site and support SIMEC through maintenance and manage the VHS consignment, ensuring that bin levels are replenished for optimal plant performance.”
Adam says he hopes CDE’s SIMEC plants serve as a case study for larger resource companies seeking to increase operational sustainability. He adds that for every tonne of ore waste processed, mining companies can significantly extend the life of their mine and maximise reserves.
If you would like to find out more about transforming mining waste into a value-added resource, visit CDE at the RIU Explorer’s Conference, Booth 2 on the 18th-20th February in Perth.