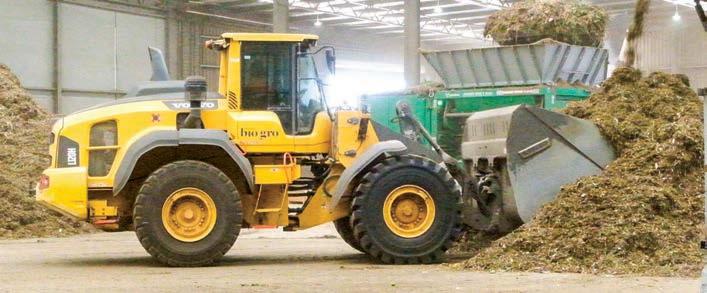
4 minute read
CULTIVATING CHANGE
AN AUSTRALIAN PIONEER IN COMPOST AND ORGANIC RECOVERY IS LEADING BY EXAMPLE WHEN IT COMES TO MANAGING WASTE AND CONSERVING RESOURCES.
When the team at Bio Gro sat down last year to develop a strategic plan for the next five years, one of the key focus points was how to describe the diverse activity of Bio Gro that encapsulates the company and its values.
Sage Hahn, Operations Manager Victoria, says when you strip it back, “Recover, Refine, Reapply” relates to every aspect of the business.
“Whether it’s organics, green waste or forest and timber residues, we Recover materials and Refine them so they can be Reapplied for the next growth cycle.
“Recover, Refine, Reapply works in the circular economy, and works with every part of our business.”
While the description of what Bio Gro does is new, the sentiment isn’t. Bio Gro has been working within a circular economy context for 45 years.
Hans Van Schaik and his wife Marjan began the business in Mount Gambier, South Australia in the 1970s in a bid to reduce the amount of bark and organic waste from the local forestry industry being burnt or sent to landfill.
Hans used the organic materials in his own backyard and worked with the Commonwealth Scientific and Industrial Research Organisation (CSIRO) to develop what became the basis of the first potting mix in Australia. The company expanded to develop and manufacture growing substrates, soil conditioners and mulching mediums.
Bio Gro is still family owned and is a leading innovator within horticulture and waste management industries.
Sage says Bio Gro began looking at treating organics from kerbside rubbish collection schemes in 2011 and worked with the City of Casey in Victoria, one of the first councils to introduce a universal green organics collection system.
In 2016 it secured the tender for food waste and organic recovery for a group of five councils in Melbourne.
The company could see the need for growth in this space and has invested in a fit-for-purpose processing system at its Victorian Dandenong South facility, which is a processing and transfer hub for organic material.
The processing line consists of a shredder to reduce the material size, but doesn’t break down the contamination too small, so that it can still be removed by hand. It then passes through a magnet to remove ferrous metals and a star screen to separate the clean fine fraction. Contaminated, coarser material is sent through a picking station where non-organic material is removed by hand. These products are then blended back together to be further processed at Bio Gro’s primary composting facility for reuse.
The line is fully integrated with a PLC system that allows the speeds of various sections to be adjusted, based on moisture levels, material size and contamination requirements.
Sage says the ability to adjust the system gives greater control of the separation process and the end product. She says being able to access and separate contamination of materials brought on site will be more important once mandatory Food Organics Green Organics (FOGO) collections are implemented across Victoria.
“We understand that once FOGO goes ahead statewide, contamination will likely increase,” Sage says. “With an opt-in service people want to do it and will typically do the right thing but once when FOGO becomes universal, we expect to see an increase in contamination because despite best intentions, not everyone will get it right all the time.
“Councils work with us to make sure there is community education about the importance of a clean product. However, it is important that we can
Bio Gro is a leading innovator within the horticulture and waste management industries.
give continuity to councils and process as much organic material as possible into a clean product.”
Sage says Bio Gro has processed three times as much organic material as it did last year, due in part to the new infrastructure but also a surge in popularity of gardening during COVID-19 lockdowns. As an example, the company processed 300 per cent more volume in October 2021 than it did compared with October 2020.
“It’s a credit to the infrastructure we have invested in, as well as our people, that we can cope with that sort of an increase,” she says.
Bio Gro has long had a strategy to invest and support much-needed growth in organics recycling. Alongside new automated technology the company has secured a Sustainability Victoria grant to extend its Dandenong South infrastructure and replace an existing water treatment system with an underground treatment plant, which will reduce the footprint of the plant and the amount of mains water used.
“We want to be as self-sufficient and environmentally friendly as we can,” Sage says. “Water is a big resource that we use and we need to apply the same mantra of Recover, Refine and Reapply to these resources, too.”
Bio Gro sees other opportunities for compost, such as application in soil health programs. It has R&D activities underway to see how value-added products can be returned to soils.
“One of the best ways we can fight Climate Change and soil degradation is by adding organic matter back into the soils that need our protection to continue to provide for us.”
A new processing line gives greater control of the separation process.
For more information, visit: www.biogro.com.au
BUILT TO CONNECT
ASTEC - Connecting People, Processes and Products
With unmatched strength from rock to road, connection is at the heart of everything we do. At Astec we design and manufacture products used to build the infrastructure that physically connects the world, but it’s the connections we make with people that drive us forward. Our company was founded on innovation and we’re committed to helping our customers succeed. Astec, we are Built to Connect.

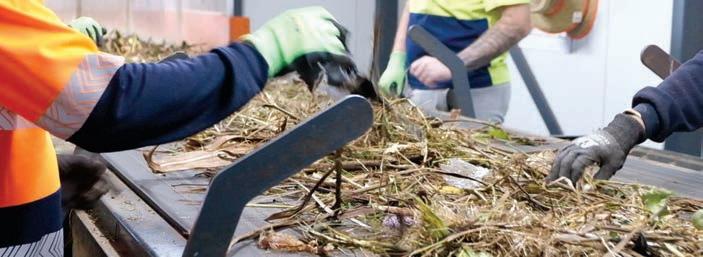