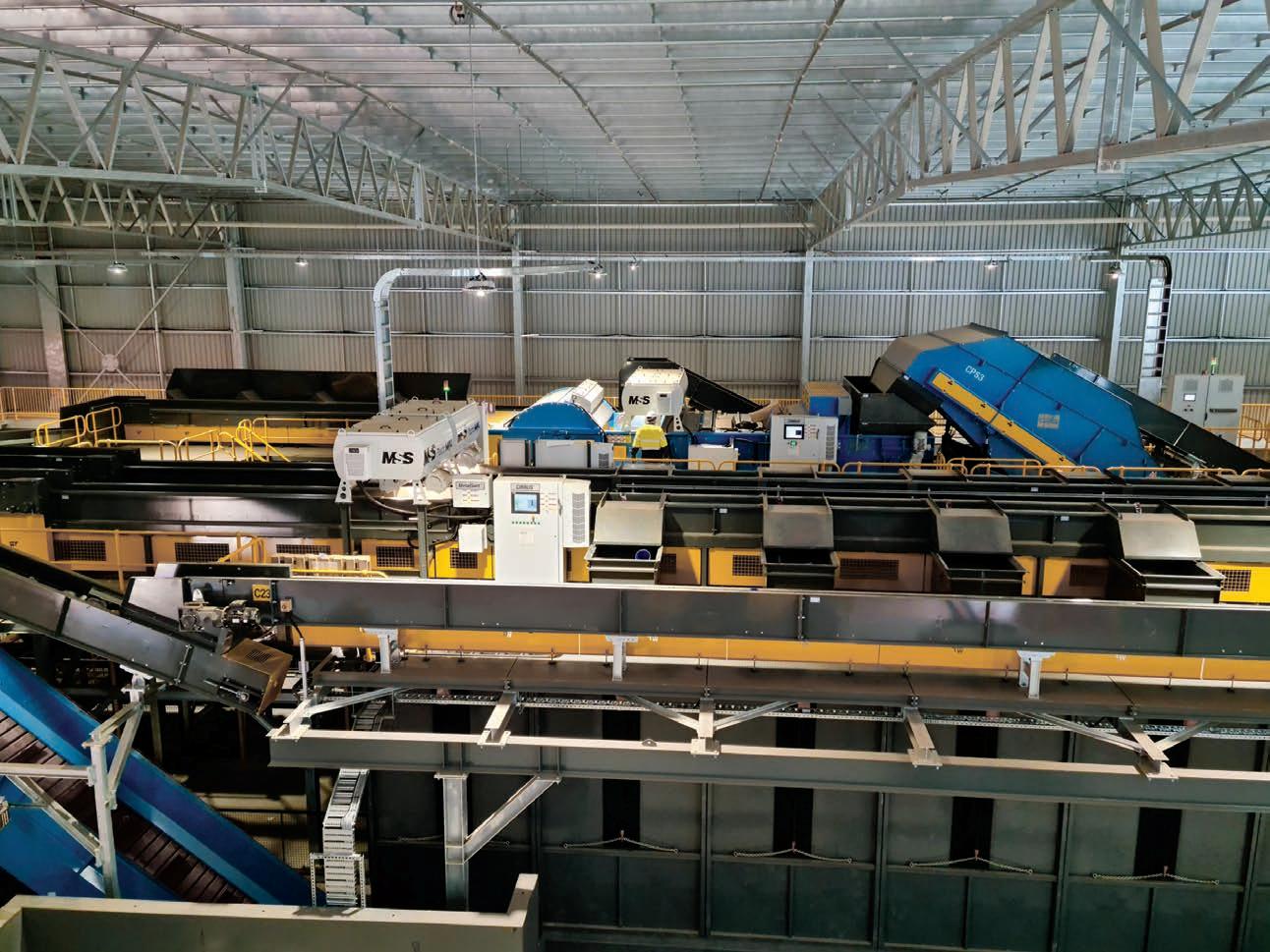
4 minute read
A FEAT OF ENGINEERING
The finished plant includes the latest technology and is designed to process 50,000 tonnes of co-mingled household recycling annually.
WASTECH ENGINEERING HAS OVERCOME EVERY OBSTACLE COVID-19 HAS THROWN ITS WAY TO DELIVER A MATERIALS RECOVERY FACILITY AT THE FOREFRONT OF THE RECYCLING INDUSTRY.
When you work with large-scale, complicated equipment you plan on a certain level of difficulty. However, no amount of planning could have predicted the challenges that confronted Wastech Engineering during its biggest project to date.
The Victorian-based company engineered and manufactured a stateof-the-art sorting plant for a Materials Recovery Facility (MRF) in South Australia in the midst of a global pandemic that forced Australia to shut its borders to the world and interstate.
Scott Foulds, Wastech General Manager – Projects, says COVID-19 “added complexity” to the project including supply chain shortages, transport issues, border closures and changing quarantine rules.
Despite the obstacles, the $23.2 million recycling facility in Kilburn was delivered on time without compromising on quality and standards. The plant started operating in testing mode in November 2021 and went to full operation in January 2022.
Wastech worked in partnership with Pascale Constructions, which built the facility on a greenfield site for the Central Adelaide Waste and Recycling Authority (CAWRA), a joint initiative of the cities of Charles Sturt and Port Adelaide Enfield. The project received $4.36 million funding from the Federal and State governments’ Recycling Modernisation Fund.
Scott says the project involved 7000 hours of design and engineering work. More than 11,000 hours of manufacturing was carried out at Wastech’s Hallam factory before components were freighted to South Australia for a three-month installation.
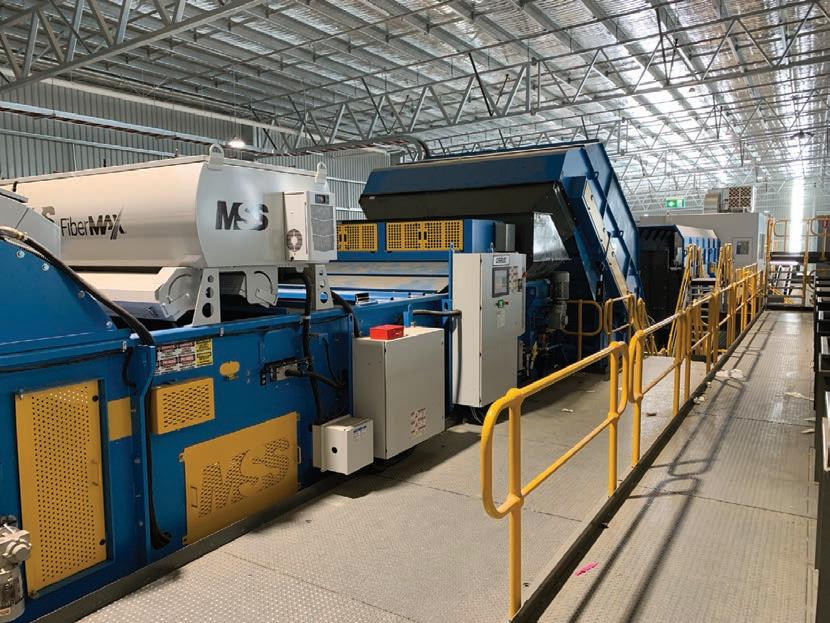
“Every facility has its uniqueness and challenges, and somewhat custom engineering and solutions are required,” he says. “We always try and advance and improve on what has been done in the past. Continuous improvement and development are part of our company’s strategic vision for growth and to find solutions for our customer’s needs.”
The finished plant includes the latest in optical sorting technology and is designed to process 50,000 tonnes of co-mingled household recycling annually.
It processes 15 tonnes per hour of incoming co-mingled material and separates it back into single commodity types including paper, cardboard, glass, aluminium, steel, HDPE (High Density Poly Ethylene) and PET (polyethylene terephthalate), as well as the full range of container deposit and other materials.
The plant uses a combination of mechanical screens and optical sorting to separate and produce the various commodity types. Once the commodities are separated, they are stored in bunkers and then baled in readiness to be freighted out for further processing.
Ben Quill, Projects Manager, says the Wastech team is “incredibly proud” of the plant, the largest project he’s been involved with and the largest in-house Material Recovery Facility the company has built.
“It is our design and our product,” he says. “All the steel work, all the conveyors; it is our plant. We not only designed it but made it ourselves in our workshop.
“When you look at what’s going on in the world right now, this tells us what we can do. It’s deeply satisfying to watch it all work.”
Ben says Wastech introduced split shifts at its Hallam manufacturing facility to continue working within COVID-19 restrictions. The company changed its design and review process to allow engineers to work from home.
For the installation build, a Victorian supervisor was on site in South Australia for the entirety of the job and a local labour force was hired.
Ben says co-operation between CAWRA and Pascale ensured the build remained effective even in some challenging circumstances with the COVID-19-related issues.
“We would like to recognise CAWRA and the hard work they did behind the scenes to keep the project on track, especially when it came to cross border restrictions in the height of COVID-19,” he says.
“We worked in lockstep with Pascale to make sure the whole of the site was completed.”
Scott Russell, Wastech Chief Executive Officer, says the team did an “extraordinary job to see it through” and deliver an impressive facility.
“The team led by Scott Foulds, which included project managers, engineers and the manufacturing team, went above and beyond to get this project to completion,” Scott says.
“We’re all extremely proud of what was achieved through teamwork to produce the completed facility. At the end of the day, the facility speaks for itself.
“We’re proud of integrating local design and manufacturing with the latest, world-class technology that’s available and what this facility can produce, not only for councils and waste management companies, but the local community as it aims to reduce waste to landfill.”
He echoed Ben’s sentiments that a strong partnership between CAWRA and Pascale was essential in producing a quality facility.
Rebekah Schubert, CAWRA Executive Officer, says CAWRA’s goal was to build the local circular economy by prioritising local markets.
“We want to see South Australia’s recyclables processed right here in South Australia,” she says.
“This facility means we will always have somewhere for our recycling to go and we will keep this local, in South Australia, at every opportunity to help grow our local circular economy.”
The Materials Recovery Facility was designed and manufactured by Wastech Engineering in Victoria and freighted to South Australia for installation.
For more information, visit: www.wastech.com.au