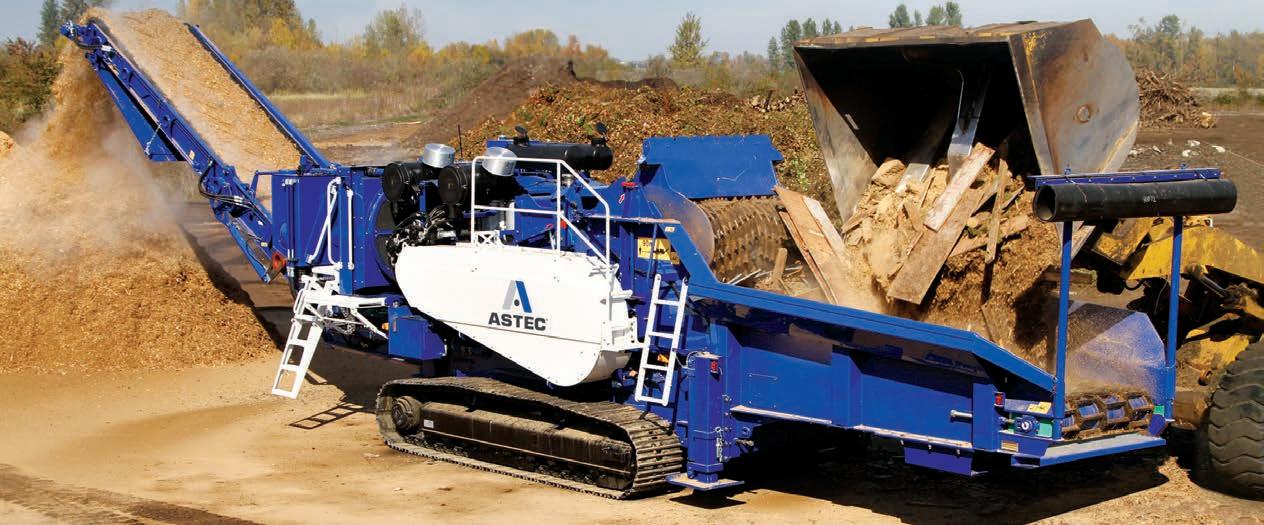
34 minute read
A RICH HISTORY
KF & Peterson: A Rich History
WMR LOOKS AT THE ORIGINS OF WHAT HAS DEVELOPED INTO A FRUITFUL RELATIONSHIP BETWEEN KOMATSU FOREST AND PETERSON, AND HOW ITS PRODUCT RANGE HAS EXPANDED.
Komatsu Forest (KF) has had a very keen interest in the Peterson chipper and grinder distribution for the Australian market since the late 1990s.
As Brett Jones, Komatsu Forest’s Managing Director recalls, Peterson’s close association of their products with the forest and timber industries was an exciting proposition.
“There was an existing dealer at that time, which prevented us from becoming involved with the Peterson products. We were persistent and Peterson were convinced to appoint us their dealer for both Australia and New Zealand,” he says.
The agreement marked a new era for KF, with the company now exposed to new technology. As such, steps were taken to ensure a beneficial changeover. A smooth transition of spare parts transfer, sales history, and technical support was established with the previous dealer.
Brett says it was important to maintain continuity with Peterson’s established customer base. As a result, Peterson retained the services of Mal Windrim, the factory Area Manager for Asia Pacific region.
“After many successful years with the KF team, Mal thought it was time to retire, this decision wasn’t taken lightly but Mal wanted to see if the fish were still biting,” Brett jokes. “KF have been fortunate enough to maintain Mal’s services on a consultant basis where his skills and long product history are invaluable.”
“The Peterson Pacific Corporation was purchased by Astec Industries Inc in 2007 and operated as an independent company within the Astec Group. Last year Astec changed its structure, rebranding and the look of its various companies which led to the new company name of ‘Astec’ for all products and companies,” says Brett.
“Interestingly, Astec has acquired nearly 20 subsidiary brands across the forestry, road building, aggregate and other industries,” he says.
Peterson’s 5710D Horizontal Grinder, processing waste wood.
The Peterson 500H Whole Tree Disc Chipper in action.
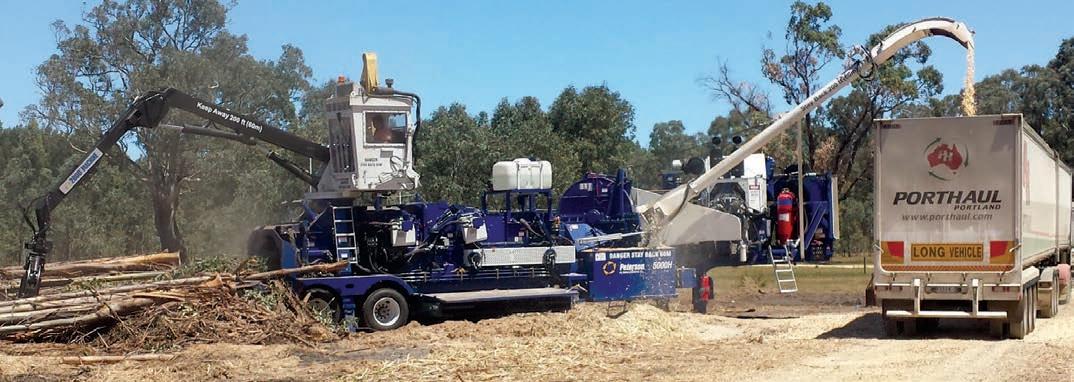
GRINDERS NATION-WIDE
The partnership was up and running by late 2010 and the first orders for machinery followed shortly after – these being the 2710C for Tripodi Transport and the 5710C for Davis Earthmoving, both delivered in early 2011.
These early sales lead to a good first year, with another two grinders and three chippers being delivered across Australia.
The grinder business has continued to increase over recent years with a strong emphasis on recycling products such as waste timber and green waste.
“Peterson has a broad model range from the 2710D (780HP) to the 6710D (1100HP), all with the same unique features,” says Brenton Yon Sales and Marketing Manager.
“An Impact Release System incorporates a Patented Air Bag protection for contaminated feed stock while the Impact Cushion System protects the mill from catastrophic damage from large items in the feed stock.”
Brenton says that all models sold in Australia are tracked grinders, with the most popular model being the 2710C/D, with 18 units sold across the country. Five of now belong to Snell Contracting in the Northern Territory. Behind the 2710C/D comes the 5710 C/D, the second most popular unit in the Peterson range.
“Most Peterson owners have multiple units, testifying to the quality of the product and back-up support which we have,” Brenton says.
A GROWING CHIPPER RANGE
Since 2011 KF has delivered 64 Peterson units, including 30 horizontal grinders and 34 units from the flail and chipper range.
Peterson’s range also includes drum and disc models, depending on customer requirements.
The disc chipper is primarily used to produce an export quality chip in bark content and chip size. It’s also capable of producing a product suitable for biomass and pellets.
The drum chipper is used to produce a product suitable for medium-density fibreboard manufacturing, panel board, biomass, garden products and with the change of drum can produce poultry and equine bedding.
The most popular chipper unit being the Peterson 5000H Whole Tree Disc Chipper, with KF delivering 22 units since 2011.
“There are several owners with multiple units including LV Dohnt, Tabeel Trading, Kevin Morgan Group, Les Walkden, Ashers, Bluewood Industries and Tiwi Islands’ Aboriginal Community,” Brenton says. “The Peterson 5000H’s popular demand is based on its combination as a flail, debarker, chipper, its suitability for softwood or hardwood operations and its ability to handle whole trees up to 56cm diameter.”
The machine is capable of producing export chip quality at up to 80 tonnes per hour, depending on tree size and characteristics. The 5000H also has a self-loading crane with a high position cab, providing improved vision for operators.
For larger requirements, a two-unit operation is required ie. a stand-alone flail and chipper. A prime example is the Peterson 6910 Disc Chipper which can accept a 69cm diameter tree, producing up to 160-180 tonnes per hour, depending on chip size and wood characteristics.
For smaller volumes and tree sizes Peterson manufacture a 5910 Disc Chipper which can be supported with the smaller 4810 Flail.
“The Peterson range complements our factory-owned forest products,” Brett says. “Peterson is now a significant contributor to our annual turnover in both unit sales and after-sales-support.”
For more information, visit: www.komatsuforest.com.au
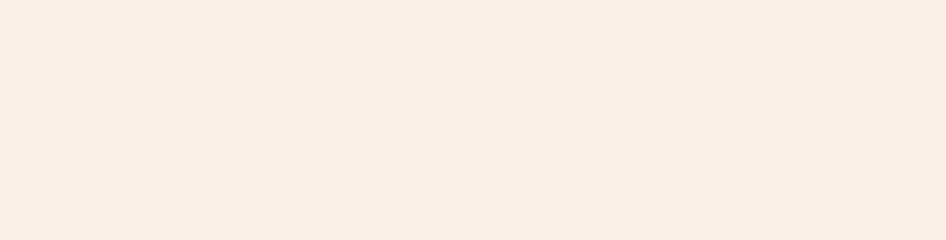
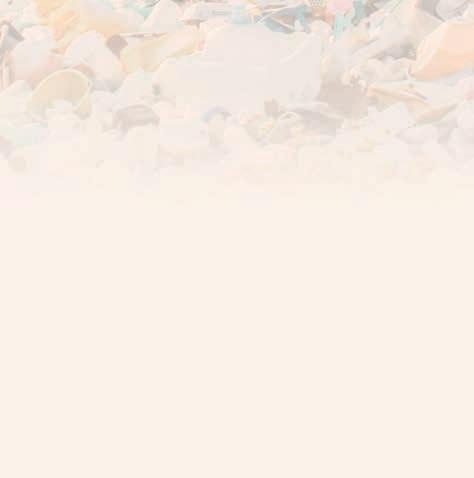
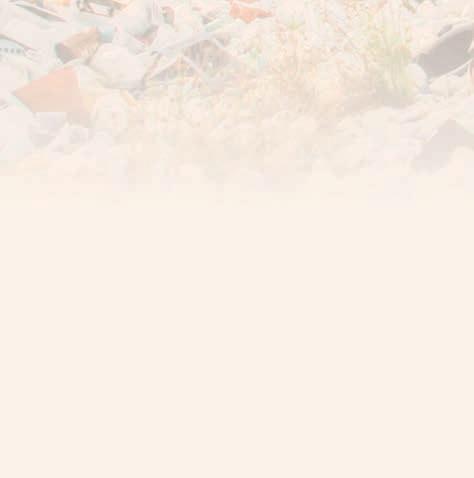
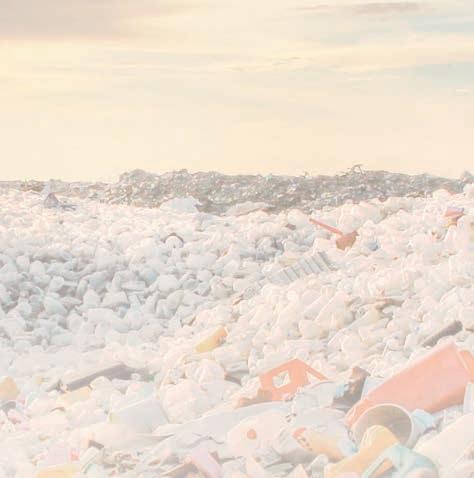
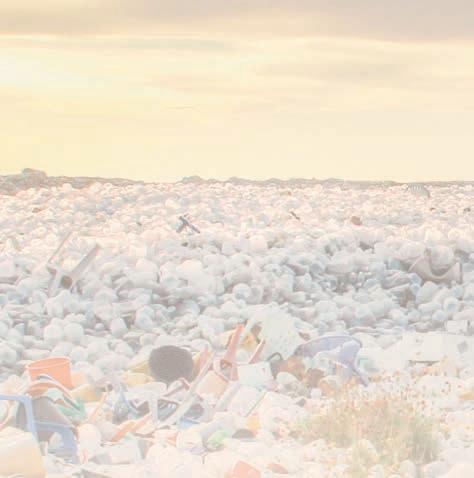
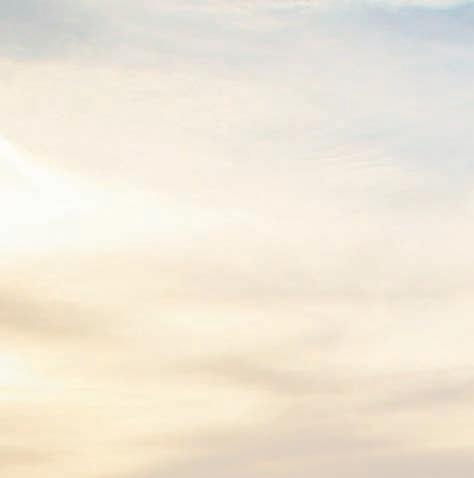
Plazrok
Turning Waste Plastic into a lightweight aggregate primarily for use in the concrete industry
Addressing two of our biggest environmental challenges with one product — Plazrok is a solution to the earth’s overwhelming plastic pollution problem while giving concrete manufacturers an eco-friendly alternative to standard aggregate.
An Advanced Product of the Future Plazrok™ is manufactured specifically to be a lightweight composite aggregate, made entirely from the waste stream, designed as an additive or a replacement for conventional aggregates for a variety of concrete applications. Plazrok™ not only provides a variety of advantages to concrete but uses all plastic waste without the necessity to sort or separate along side a variety of other waste derived from landfills.
Plazrok.com 0457 730 013

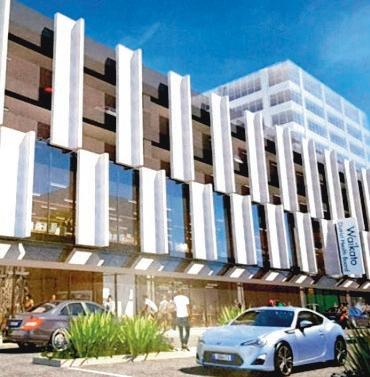
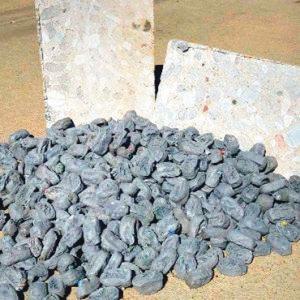
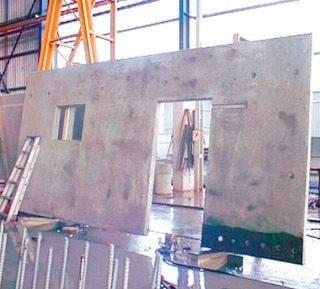
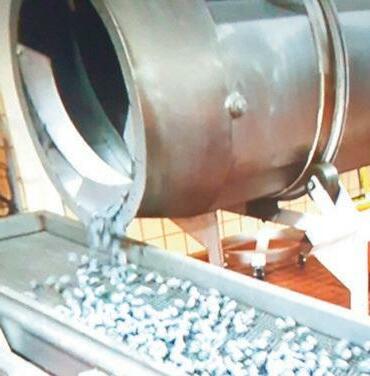
Onto a winner
THE WASTE INNOVATION AND RECYCLING AWARDS ARE A CHANCE TO CELEBRATE THE WORK CARRIED OUT ACROSS ALL LEVELS OF THE WASTE AND RESOURCE RECOVERY SECTOR.
Waste industry stalwart Harry Wilson scooped the pool at the 2021 Waste Innovation and Recycling Awards.
The founder of Handybin Waste Services took out awards for Leader of the year, Workplace of the Year and the Innovation Award.
REMONDIS Australia was the other big winner on the night, winning the Outstanding WARR Projects Metro for its Western Australia Container Deposit Scheme and the Operational Excellence Award. Susie McBurney, REMONDIS General Manager was the Woman of Waste winner.
More than 150 people from the waste and recycling sector attended the awards night at Showtime Events Centre.
LEADER OF THE YEAR
SPONSORED BY
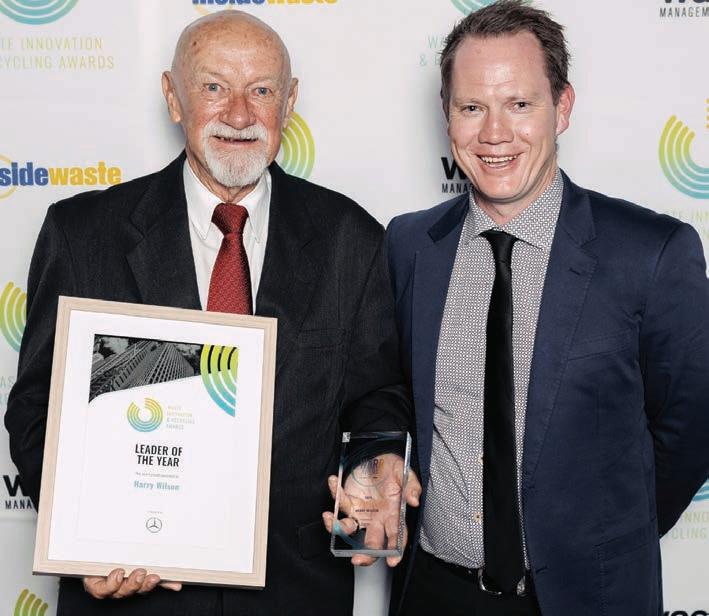
Winner: Harry Wilson - Handybin Waste Service
Waste Industry stalwart Harry Wilson is described as a quiet achiever, an unsung hero and a true gentleman.
He has lead innovation, conducted research and shared results leading to best practice in a career spanning 50 years in the waste and resource recovery sector. He has given back to the sector his time, experience, and expertise as an active executive member of Waste Contractors and Recyclers Association (WCRA), New South Wales for more than 20 years, 11 as president.
In 1987, Harry left his corporate position with Brambles to start a waste collection business for Sulo Australia MGB Pty Ltd, introducing the mobile garbage bin and single driver-side loading collection vehicles to councils across Australia and south-east Asia.
He acquired the business in 1992 and renamed it SMS Municipal Services. In partnership with councils and the communities it served, the company went on to identify best practice in the sector including optimising bin sizes and service frequency for both recyclables and residual waste.
Harry designed and built some of Australia’s most sophisticated MRFs of the 1990s and pioneered garden waste collections in Willoughby Council from 1993.
By 2000, more trials in organic waste collections led to FOGO (Food and Garden Organics) collections and extending the range of plastic polymers accepted in kerbside recyclables collections.
In 2005, Harry combined his logistics background with his deep understanding of resident behaviour to create a new company called Handybin Waste Services. He won the kerbside collection and MRF processing contracts for Coffs Coast – three mid NSW north coast councils of Coffs
Harry Wilson and Daimler’s Steve Ham.
Harbour, Bellingen and Nambucca. At the same time, Harry partnered with Paul Coffey a leading organics expert, to start Biomass Solutions. They won a 20-year processing contract of organics and mixed waste for Coffs Coast.
The investment brought overseas technology to regional Australia. The Coffs Coast MRF has since piloted plastic film and textile recovery, as well as a glass processing plant allowing both kerbside and commercial glass to be processed to local market specifications.
Harry said it had been a long journey, but one he had always enjoyed.
OUTSTANDING WARR PROJECT: REGIONAL
Winner: McMullin building demolition – Drumderg Services
The demolition of the McMullin Building proved to be a benchmark
Steven Fam from Drumderg.
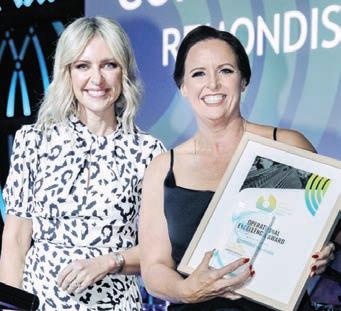
project for the University of Newcastle, Drumderg and TSA Management in establishing complementary protocols for planning, achieving and exceeding best practice environmental, recycling, HAZMAT removal and safety across all phases of the demolition project.
In total, the project diverted 99.83 per cent of materials from landfill, achieved an above six-star Green Star standard, retained 35 significant trees and processed and crushed more than 15,000 tonnes of concrete on site.
Detailed planning and significant investment into specialised equipment were all contributing factors to the project’s success.
The demolition works were monitored against the methodology with recycling initiatives and reported monthly. Through identification of the waste streams and recovery options the project exceeded the requirements of diverting building fabric from landfill.
Waste wood produced from the demolition was mulched and transformed into chipboard, all carpet was removed and stacked to supply to the pacific island nations and e-waste items were refurbished and donated to both rural school communities and the Rural Fire Service.
The project presented a unique opportunity for university researchers given the building’s age, structural composition, coastal location and endurance through the 1989 Newcastle earthquake. Researchers from the College of Engineering, Science and Environment captured data throughout the demolition to calculate the carbon footprint and for laboratory assessment.
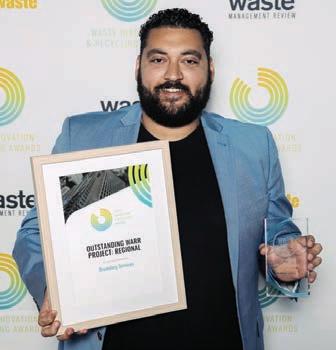
OPERATIONAL EXCELLENCE
Given to an individual or team that has achieved demonstrable improvements in efficiency, best practice OHS and impeccable records.
Winner: Operational excellence in ACT – REMONDIS Australia
REMONDIS Australia has operated Mugga Lane Landfill, Mugga Lane Transfer Station, Mitchell Transfer Station and ACT’s Recycling Drop Off Centres since it acquired Thiess Services in 2011.
It has also operated the Mugga 2 Quarry site, which receives contaminated soils from the region, since 2019.
The facilities are managed on behalf of ACT NoWaste and service all of Canberra and some adjacent New South Wales jurisdictions. Over time, the facilities have transitioned from disposal to resource recovery operations and are assisting the region to achieve its objectives under the ACT Waste Management Strategy 2011-2025.
Since the start of the current Mugga Lane Landfill (MLL) contract in 2016, REMONDIS and ACT NoWaste have made changes which have extended the landfill life expectancy, reduced labour and equipment costs by about $700/day and reduced greenhouse gas emissions by minimising plant and vehicle machine hours and fuel usage.
They have established the first KPI-based landfill disposal contract, delivering value for money to government and residents with a quantifiable bonus and penalty structure and enhanced the plant fleet, including an additional 836 compactors.
REMONDIS also has the benefit of retaining staff with more than 22 years of consecutive site management experience at Mugga Lane Landfill.
While the waste and resource recovery industry continues to evolve and pose new challenges, staff understanding of the site’s history and past challenges is invaluable.
Susie McBurney, REMONDIS General Manager, said the award is “for
Emcee Jacquie Felgate and Susie McBurney, REMONDIS.
the hard-working team” in the ACT at the Mugga Waste Landfill.
“They have certainly implemented a lot of strategic initiatives over the past few years, whether it’s our tarping initiative or what we’ve done with compaction, with a forward thinking client in ACT NoWaste.”
OUTSTANDING WARR PROJECT METRO
The Outstanding WARR project award is given to a project that has delivered cost-effective and high-impact success in its targeted field.
Winner: Creating change with containers in WA - REMONDIS Australia
REMONDIS Australia risked a nonconforming bid when it submitted a tender for Western Australia’s Container Deposit Scheme (CDS).
REMONDIS’ Chris Gusenzow and Susie McBurney.
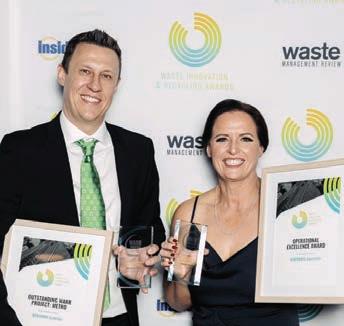
It was the first CDS in Australia REMONDIS had tendered for and the company wanted to improve industry practice to provide the cheapest model and the safest and most environmentally friendly collection service.
REMONDIS’ solution was onsite compaction and rear lift truck compaction to reduce the amount of air and increase the number of bottles able to be collected and transported, while using RFID and trade approved scale technology to ensure a high level of auditability and accountability. Since October 2020 the initiative has collected and processed more than 28 million containers per month, equivalent to 500 tonnes, from more than 60 locations.
Accepting the award, Chris Gusenzow REMONDIS General Manager – WA said the company worked closely with Containers for Change when making a submission for the WA scheme.
“We wanted to come up with something that was completely different,” he said. “We went out on a limb, they believed in us and it’s producing savings across the board, not just in environmental savings but cost savings.
“We’re really happy with what we’ve delivered.”
WARR WORKPLACE OF THE YEAR
Winner: Handybin Waste Services PTY Ltd
Handybin is committed to the philosophy of seeking maximum recovery of recyclables and of achieving the highest economic value for all of its products.
It is also a strong advocate for local employment. Handybin is a significant local employer of more than 65 locals drawn from the three nearby council areas. Where larger multi-national companies sometimes consolidate their services typically in metropolitan regions, Handybin’s key business activities are all Coffs Harbour based, including its workshop, administration and call centre and processing facility.
The company offers apprenticeships and traineeships to locals and has a long-standing relationship with not-for-profit social enterprise New Horizons, providing employment for its members in the Materials Recovery Facility or with projects such as collating for education mail-outs and compost bagging for resident giveaways.
Harry Wilson, Handybin Founder, said he entered the award because of his employees.
“I have been fortunate enough to work for a large private company, a large public company, an overseas German company and now my own company,” he said.
“The one thing I’ve appreciated over all those years is my employees.
“I hope I’ve developed a good relationship with all of my employees. I work very hard at it, and I can only recommend that to every other waste company in the operation. Look after your employees and they’ll look after you.”
YOUNG PROFESSIONAL OF THE YEAR
An individual aged 35 years or younger who has impressed their colleagues and counterparts with their contribution and impact to their organisation, and excellence in service.
Winner: Tara Osborne – BINGO Industries
At the age of 28, Tara Osborne is a general manager and has seen BINGO through its initial public offering and several large acquisitions.
Collecting the award for Young Professional of the Year, Tara said she was especially grateful for her “BINGO family” which has supported her career and afforded her development opportunities over the past few years.
“I couldn’t ask for better cheerleaders and mentors in senior management that I’ve been fortunate enough to have at BINGO. In my relatively short five years in the waste industry, I’ve witnessed so much change and I’m excited
Tara Osborne.
Winner: TerraCycle School Recycling Program – TerraCycle
TerraCycle is empowering teachers and parents to raise the next generation with sustainable practices and values, by incorporating hands-on learning about recycling in the classroom, while driving positive outcomes for the environment.
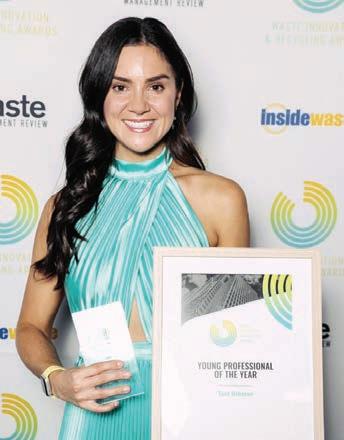
Since 2017, TerraCycle has helped more than 5500 Australian schools sign up to recycling programs, to divert 1.8 million units of waste from landfill.
TerraCycle partners with leading brands such as Colgate, BiC, PAW Patrol and Glad to offer schools free recycling solutions. Schools that return waste earn TerraCycle points that can be redeemed to raise funds for themselves, or non-profits such as Wide World Fund for Nature (WWF) and Keep Australia Beautiful.
The programs have generated longlasting benefits for schools and the wider community through the installation of playgrounds made from recycled waste, community garden beds and outdoor classrooms.
Challenges which encourage school communities to collect the most waste for recycling have not only demonstrated how recycled materials can be used as a sustainable alternative to virgin plastic but prizes that have been won through the competition promote gardening and healthy eating among students.
TerraCycle first launched recycling programs in Australia for schools to sign up to in 2014. In the first four years, school sign-ups grew steadily year on year. In 2017, sign-ups significantly increased by 111 per cent. 2018 became the first year that sign-ups exceeded more than 1000 new schools recycling.
TerraCycle schools recycling program has been replicated in the United States, United Kingdom, Canada and New Zealand.
Alice Cooke.
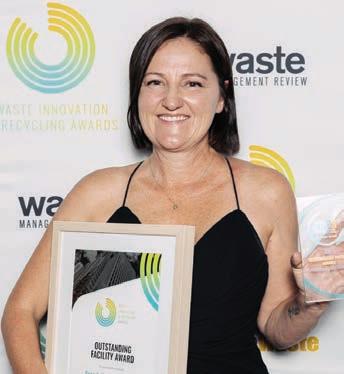
about the future prospects that we have as we push towards a circular economy.
“BINGO has been at the forefront of this push, leading the charge for greater recycling of building and demolition and commercial and industrial waste along the east coast of Australia.
“It’s the challenges and the opportunities that we have as an industry and as a business to shape better outcomes for our environment and our community that really motivate me and give me such a rich sense of purpose in my role of leading group strategy and innovation for BINGO.
“By working together collectively as an industry I have no doubt that we can continue to lead the investment in innovation and recycling to drive towards our common vision of a more sustainable future.”
COMMUNITY ENGAGEMENT SUCCESS OF THE YEAR
Private, not-for-profit or government organisation that has started programs that have had measurable success in engaging and communication with the community, resulting in positive outcomes for the industry.
OUTSTANDING FACILITY AWARD:
Given to a new infrastructure project that commenced operating in 2020 or 2021.
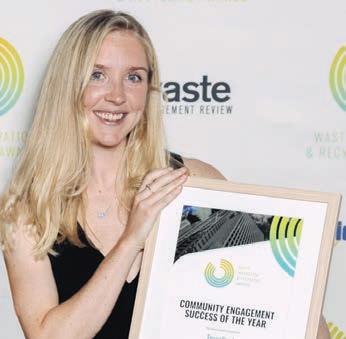
Winner: Central Waste Facility -– Bega Valley Shire Council
The Central Waste Facility emergency landfill was Bega Valley’s response to help the community clean up after the devastating 2020 bushfires.
In New South Wales, about 2400 homes were lost in the fires, with the Bega Valley Local Government Area sustaining some of the greatest losses across 540,000 hectares, or 58 per cent of the shire.
The amount of waste the fire generated in the Bega Valley was estimated at more than 200,000 cubic metres, of which half was asbestoscontaminated, all destined for landfill.
The Bega Valley landfill was
Joley Vidau, Waste Strategy Co-ordinator Bega Council.
already under pressure after the cleanup of the March 2018 Tathra and Reedy Swamp fi res. Council was proud of how it managed this clean-up but could never have expected the plans and processes it put in place during this disaster would need to be actioned again so soon, and on a much bigger scale.
“We managed to construct a 200,000 cubic metre landfi ll, seven dams, weighbridge, gatehouse, four roads, two kilometres of water and a fence in four week,” Joley Vidau, Bega Shire Waste Strategy Co-ordinator said at the awards ceremony.
“That was achieved because our contractors and everyone from Bega council and New South Wales planning stepped up and really supported us. This award is for all those people who helped get us across the line.”
INNOVATION AWARD
SPONSORED BY
Given to an individual or company that has implemented processes and practices or developed and/or rolled out technology and/or plant that have successfully closed the loop, creating a demonstrable circular economy.
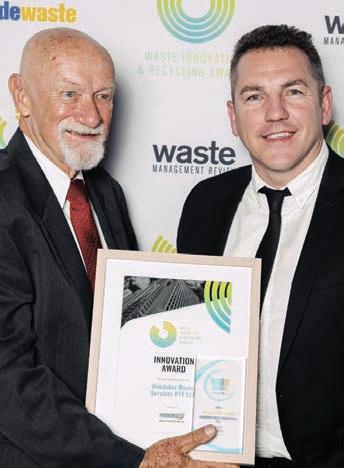
Winner: Handybin multi-stream recycling services – Handybin Waste Services Pty Ltd
In addition to traditional materials processed at its Materials Recovery Facility, Handybin has successfully introduced glass, polystyrene and textiles recycling to the communities its services.
The glass is used in the manufacture of new glass and production of aggregate material. Since 2012, Handybin has successfully used all its glass and disposed of none to landfi ll.
The textiles are offered to local charities for resale and the polystyrene is used to produce outdoor furniture and fencing with substantial environmental and social benefi ts. Handybin has processed just over 15 tonnes of polystyrene – about 6000m3 – enough to fi ll 100 shipping containers or to cover a full-sized football fi eld to a depth of more than 1m3.
Harry Wilson, Handybin Founder, said the award comes from years of experience.
“My history goes back to recycling beer bottles off the back of a garbage truck, followed by crates, followed by a divided wheelie bin, which is the worst recycling service I’ve ever handled in my life, to Handybin, which is a threebin system for recycling materials.
“By the time we got to a real recycling bin we’d really thought about how we could successfully maximise our bin and we’ve been successful in our endeavour over a 13 to 15-year period,” he said.
“We’ve loved the journey and still are looking for more innovation.”
Harry Wilson and Steve Harrison from ResourceCo.
WOMAN OF WASTE
SPONSORED BY
Recognises a woman in the industry who has driven change and continues to do so, leading to progress in breaking down barriers and creating new career prospects for the next generation.
Winner: Susie McBurney – REMONDIS Australia
Susie has more than 20 years’ professional experience in the waste industry, including senior management positions at both REMONDIS and Cleanaway.
Her exposure to the waste and resource recovery industry started much earlier, growing up involved in a waste and recycling business that was started, operated and managed by her family.
As REMONDIS’ General Manager for New South Wales and ACT, Susie oversees more than 15 sites, including landfi ll operations, composting and material recovery facilities and domestic and commercial collection depots.
Accepting the award, Susie thanked her parents who, 20 years ago “recognised the benefi ts of women in leadership long before it was popular and have always been my greatest supporters”.
She said she had the benefi t of working for and with some amazing male colleagues, including those who employed the fi rst female general manager of REMONDIS in 2014.
“As a 24-year-old female, let’s be honest ladies, joining the waste industry in the year 2000, it wasn’t without its challenges. Today I am a strong advocate for women leading the way in the waste management sector.
“My advice to women in a still male dominated industry is work hard, have balance and if you’re told no, fi nd someone who will say yes.”
Susie paid tribute to the other nominees and said she could continue a personal commitment to “shining that light on a path for other women to follow”.
Tipping point
WITH ITS REGIONAL LANDFILL DUE TO REACH CAPACITY IN 2023, THE CITY OF GREATER BENDIGO IN CENTRAL VICTORIA IS LOOKING FOR A CIRCULAR ECONOMY SOLUTION TO MANAGE WASTE AND RESOURCES.
Greater Bendigo City’s FOGO collection facility.
With a lifespan of less than 12 months at its Eaglehawk landfill, Greater Bendigo City Council is taking a bold step and saying ‘no’ to more landfill.
Instead, it aims to create a local circular economy to create jobs and keep resources and resource recovery spending in the region.
Greater Bendigo City councillors placed a moratorium on the development of new landfills in the region in 2014 and in 2019 acknowledged the urgency for action on both the climate and biodiversity crisis, which kick-started the Circular Greater Bendigo project.
In 2020, as phase one of the project, the City called for Expressions of Interest for solutions to manage its waste when the landfill’s last active cell is full.
More than 40 submissions were received, with 22 proceeding to codesign discussions. Of 11 submissions received during a closed tender process, three have been shortlisted for further investigation.
Brooke Pearce, Resource, Recovery and Education Manager City of Greater Bendigo, says the City’s waste system struggles to do much with end-of-life materials. However, the creation of circular economy solutions will change how material resources are handled and valued.
“It’s really about shifting from a ‘take, make, waste’ society to a ‘take, make, reuse’ society, where we recover and eventually reuse all of the material resources from products that are no longer needed,” Brooke says.
“With details and thorough design to meet the community’s disposal needs, and effective recovery of materials, we will be aiming to avoid landfilling waste completely and creating new opportunities for local industries in Greater Bendigo.”
Brooke says the creation of a local circular economy will also reduce greenhouse gas emissions as landfilling waste materials, and the process of moving waste materials to landfills, accounts for more than half of Greater Bendigo’s emissions.
The City manages about 95,000 tonnes of waste materials each year and says more than 85 per cent of the current waste stream could be used in an alternative circular economy process in the future.
The three projects to be further investigated include establishment of a local composting site within 25 kilometres of Bendigo to process more than 15,000 tonnes of food and garden organics each year. The site would reduce emissions by 16.3 per cent, in comparison to current kerbside organics disposal arrangements.
Establishment of a small-scale, modular Energy-from-Waste plant, using pyrolysis and gasification, could convert 30,000 tonnes of general waste per year to 5660 tonnes annually of biochar. The gas would then be converted to electricity and exported to the grid, resulting in a 78 per cent reduction in emissions in comparison to sending the waste to landfill.
Another proposal would process soft plastics into a road-based additive to be used in roads in Greater Bendigo. The plastics would be processed by a Melbourne-based manufacturer,
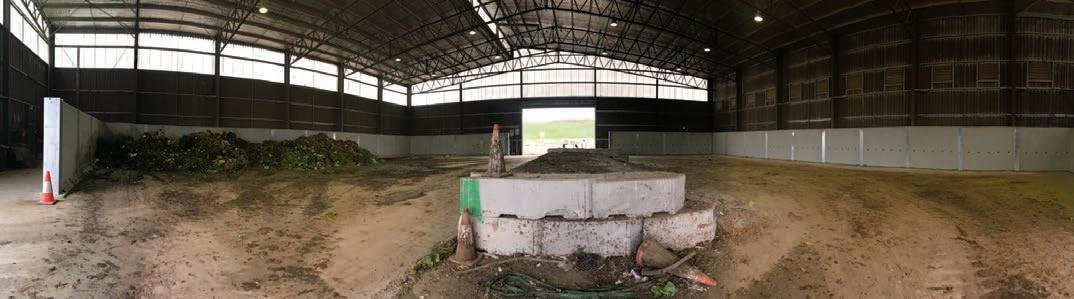
Greater Bendigo City Council’s Eaglehawk Landfill will reach its capacity next year.
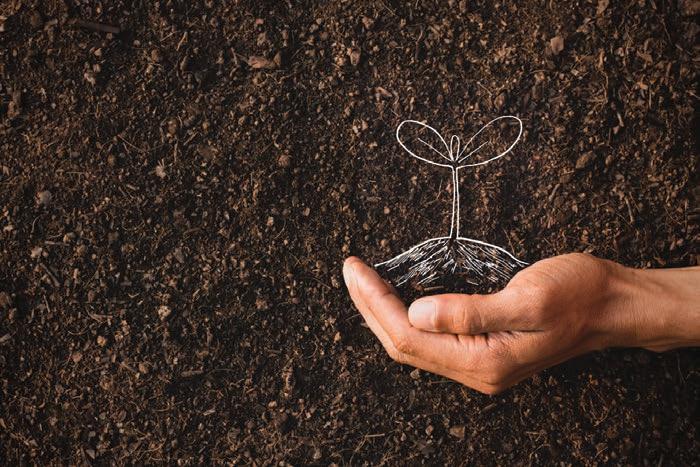
resulting in a 392 per cent reduction in emissions when compared with current landfilling of soft plastics.
Kylie Douglas, Senior Landfill Engineer City of Greater Bendigo, says the City’s intent was to target local industry that could provide circular economy solutions as well as creating employment in the region.
“Circular economy means thinking about alternative solutions for these resources and no longer referring to them as ‘waste’. The current practice of landfilling is simply dealing with the end product and limits options and innovation,” she says. “We don’t want to transfer responsibility and shift one gate fee to another, this is about finding long-term circular solutions.
“The reality is we have no more room to move at the Eaglehawk Landfill. We had to make a change.”
The Eaglehawk Landfill site will remain open to the public as a full-time transfer station when it reaches capacity next year.
The City is calling for solutions for other material streams including commercial and industrial waste, textiles, plastics and other items traditionally sent to landfill.
The short-listed projects in the first round were to be presented to the Council in April for consideration.
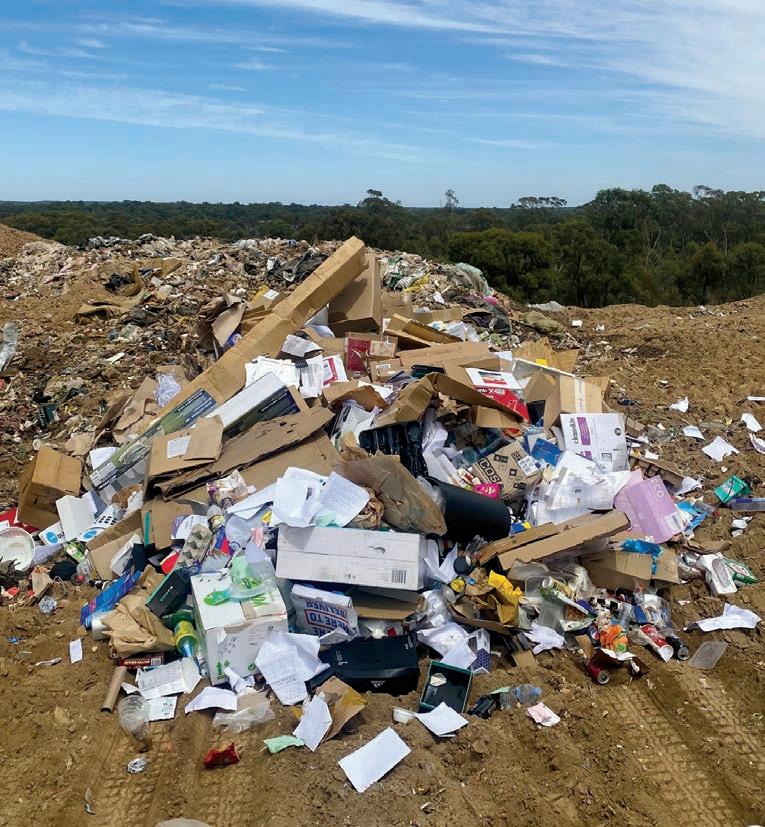
TRIMBLE® LOADRITE® E2750
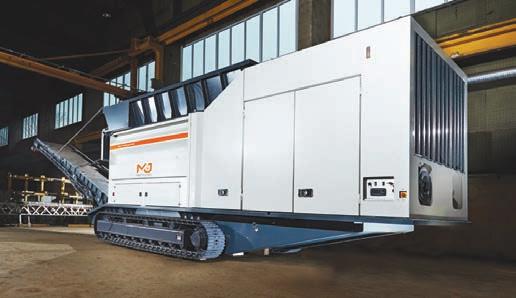
Improve your waste haul operations tracking, safety and profitability with accurate payload measurement.
The Trimble® LOADRITE® E2750 weighing system gives you the information to increase efficiency and maximise profits. Knowing the weight of each customer’s bin helps to charge correctly; unprofitable customers are no longer subsidised by more profitable ones. Accurate weighing ensures trucks are loaded to the correct value avoiding expensive overload fines.
By tracking the weight of each bin, you can provide accurate weights to your customers for environmental reporting and help reduce their environmental impact by increasing their recycling rate.
The E2750 is easy to use and integrates into your onboard computers. The system automatically measures the net weight of the bin as it is emptied, providing accurate bin weight information to improve business operations and maximise profits.
M&J Recycling shredding technology is based on an extremely aggressive knife design and open cutting table, which provides outstanding performance when dealing with mixed and challenging materials.
These key features make M&J pre-shredder units extremely resistant to wear caused by materials and waste normally considered as un-shredable; including solid steel, reinforced concrete and rocks.
The machine is designed for easy maintenance and seamless uninterrupted operations. Loading and discharge height parameters can be varied to allow optimum performance even in challenging environments.
Visit Tutt Bryant at Booth 46 of the 2022 Waste Conference in Coffs Harbour.
TUTT BRYANT, M&J4000M PRESHREDDER
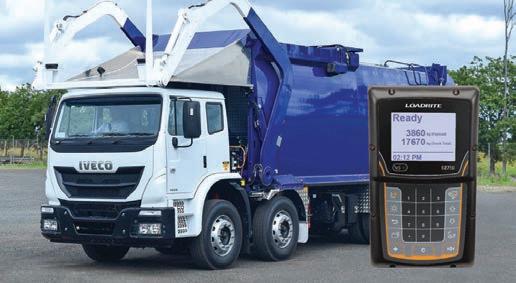
KOMPTECH CEA, TERMINATOR 6000S
The Terminator is a slow-running, single-shaft shredder for all types of waste. Robust teeth on the shredding drum and the opposing counter comb give coarse pre-crushing to a defined shredding size.
The continuous cutting gap adjustment allows precise setting of the particle size for subsequent process steps.
The hydraulic drive with load-dependent speed control ensures maximum use of the engine output. The hook lift platform, 3-axle chassis and steel tracks with hydraulic drive options provide excellent mobility.
Hydraulic drive is also a good choice where frequent changes of materials require constant throughput rate adjustments to accommodate downstream machines, thanks to integrated throughput regulation by the drum speed.
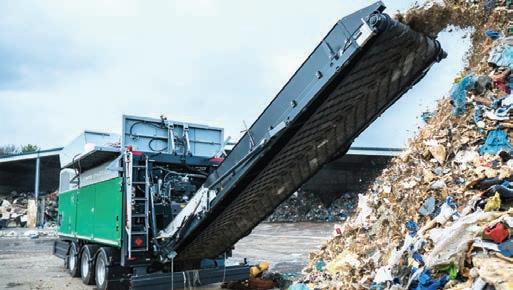
The E2750 integrates into onboard computers.
Contact - SmartTech Australia
P 1800 655 860 W www.smarttechaustralia.com.au
Contact - Loadrite New Zealand
P 0800 493 444 W www.loadritescales.co.nz E info@loadritescales.co.nz
M&J pre-shredders are extremely resistant to wear.
Contact – Tutt Bryant
P 1300 658 888 E www.tuttbryant.com.au
The Komptech CEA, Terminator 6000S.
Contact - CEA
P Deon Cope E d.cope@jcbcea.com.au W www.jcbcea.com.au
TELFORD SMITH, SESOTEC FLAKE PURIFIER+ MULTI-SENSOR SORTING SYSTEM
ELDAN RECYCLING, MULTI PURPOSE RASPER
The FLAKE PURIFIER+ provides effective contamination detection and separation as well as sorting by material type, shape and colour. It is used especially for the sorting of plastic flakes such as PET, HDPE or mixed plastics flakes.
These systems use a modular concept to allow the combination of all available sensors for contaminant detection: sensors for metal separation, sensors for colour separation / sorting, and sensors for the separation and sorting by plastic types.
The information provided by the individual sensors is processed by the evaluation unit based on octa-core technology. Separation of material is by air-blast unit.
SESOTEC is one of the world’s leading manufacturers of inspection, separation and sorting systems that are used in process, packaging, and production lines throughout industry and in the specialised preparation of materials for recycling. SESOTEC systems are used for detecting and separating bulk material precisely and consistently at high speed, such as separation of plastic bottles, crushed electrical appliances and mixed plastic scrap, PET flakes, and all by material type, colour, shape and metals.

SESOTEC systems are used for detecting and separating bulk material.
The Multi-Purpose Rasper is available as an extra heavy-duty version.
Contact - Telford Smith
P 03 8792 9777 W www.TelfordSmith.com.au
The Eldan Multi Purpose Rasper is a tough, versatile shredder with built-in screening for both primary and secondary size reduction, depending on the material.
Suitable for a variety of applications, it can be used for steel wire cleaning, aluminium, cable, electronics and fridge recycling, municipal solid waste, various scrap and tyre recycling.
For tyre recycling, the Multi Purpose Rasper can be used for size reduction of shreds from any type of tyre from passenger vehicle tyres through to mining truck tyres.
High inertia from the flywheel ensures an even load on the machine, yielding a higher cutting power. The machine is belt driven for simple transmission, and the rotor is manufactured and designed for minimum wear.
The knives can be reground multiple times on a “flat-bed“ grinder, ensuring long life and low operation costs. The machine is designed for quick and easy change of knives and screens, which are available in different hole sizes for flexible production. Wear parts are exchangeable.
The Multi Purpose Rasper is available in different sizes and as extra heavy-duty versions depending on the capacity and cutting force required.
A frequency converter, available at an additional cost, allows adjustable rotor speed, reduced power consumption by up to 40 per cent and for the machine to be started when full loaded.
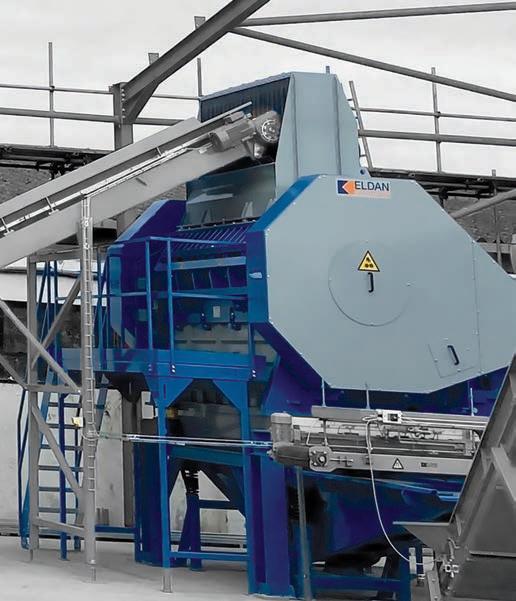
Contact - Eldan Recycling – Carsten Nielsen
P +45 2149 1967 E cn@eldan-recycling.com W eldan-recycling.com
Building a national approach to SUPs
PLASTIC RECYCLING REMAINS ONE OF THE MOST CHALLENGING AREAS IN AUSTRALIA’S JOURNEY TO ACHIEVING THE 2025 NATIONAL PACKAGING TARGETS. BROOKE DONNELLY, CEO OF AUSTRALIAN PACKAGING COVENENANT ORGANISATION (APCO) LOOKS AT THE STATE OF PLAY.
With just 16 per cent of plastic packaging successfully recovered in 2019-20, Australian government and industry will need to make signifi cant changes to successfully reach our plastic recovery target of 70 per cent. Building a clear and nationally consistent approach to the phase-out of problematic and unnecessary single-use plastic packaging (SUPs) is one of these allimportant areas of change.
In 2019, about 50,700 tonnes of single-use plastic packaging was produced, making up 5 per cent of the total 1 million tonnes of plastic packaging placed on the Australian market. Phasing out SUPs is fundamentally a packaging design issue and an essential part of closing the 14 per cent gap that exists between packaging that is recyclable by design (84 per cent) and Australia’s 100 per cent recyclable National Packaging Target.
The good news is that both industry and government have made signifi cant progress on the phase-out of SUPs already. Since the 2025 National Packaging Targets were agreed in 2018,
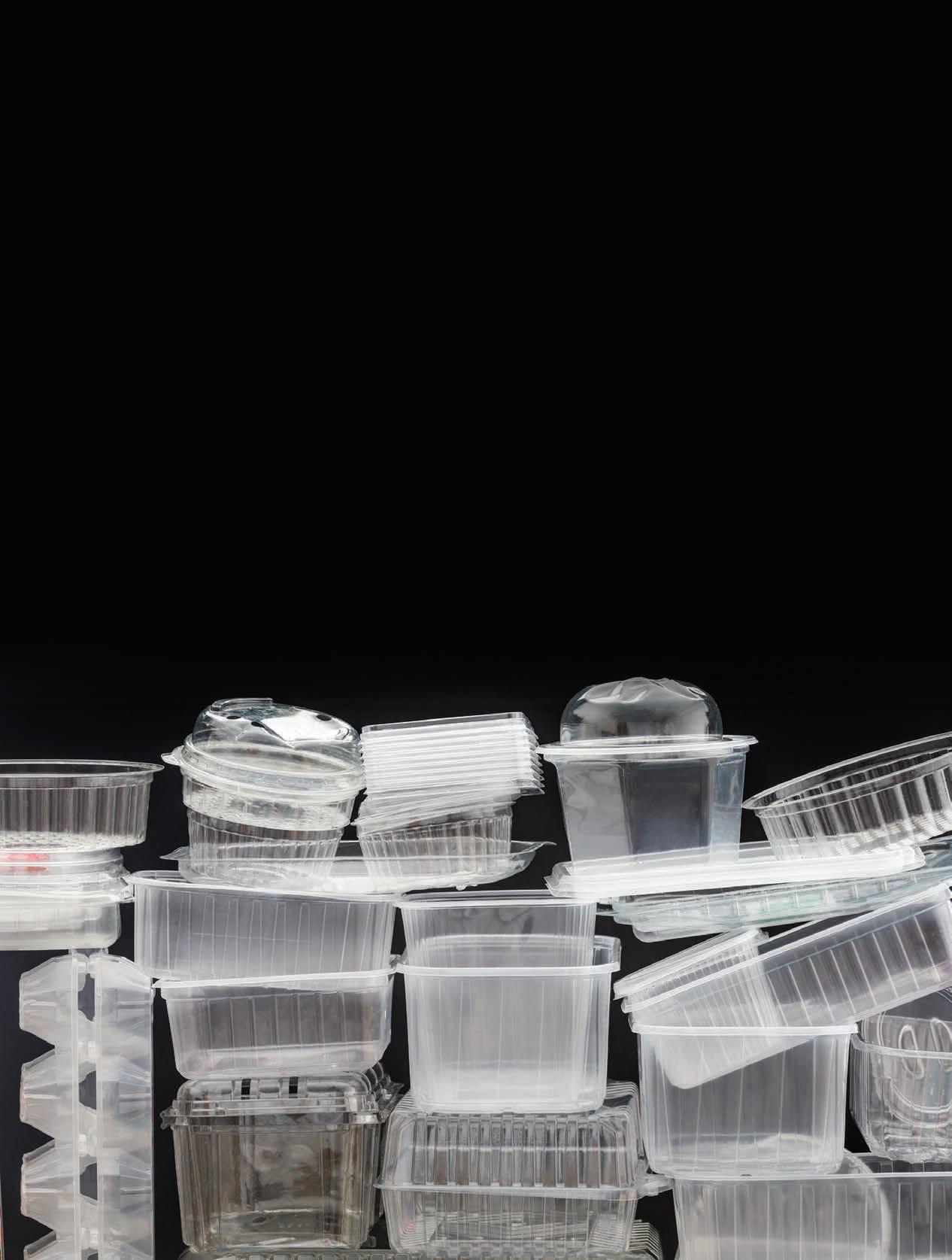
APCO is seeking coherent, national approaches to plastic packaging regulations.
Brooke Donnelly, CEO Australian Packaging Covenenant Organisation.

APCO has worked with the whole plastic supply chain to produce an agreed list of materials for phaseout and agreed timelines to meet that phase-out.
The items that businesses and government are working to phase out include lightweight plastic shopping bags, fragmentable plastics, expanded polystyrene (EPS) packaging for food/ beverage service and fresh produce, EPS loose fill packaging, moulded EPS packaging for white/brown goods and electronics, rigid polyvinyl chloride (PVC) packaging, rigid polystyrene (PS) packaging, opaque polyethylene terephthalate (PET) bottles and rigid plastic packaging with carbon black.
At the federal government level, the National Plastics Plan released in 2021 set out a new standard for how Australia will tackle the plastics issue. The Plan provides a comprehensive approach designed to keep plastic in the economy for as long as possible, and out of landfill and the environment. It also sets out clear deadlines that industry needs to make in the phase-out of single-use plastic packaging.
State and territory governments are continuing to develop and implement policy and legislation on SUPs, including some packaging items. In November 2021, the NSW Government passed the Plastic and Circular Economy Act 2021. This legislation provides for the government to ban problematic and single-use plastics items, establish mandatory design standards, mandate product stewardship approaches and targets, and require the development of action plans.
In January 2022, regulations came into force in Western Australia to ban certain single-use plastic items. Enforcement of bans on stage 1 items will start from 1 July, except plastic cups (including some plasticlined paper cups) which are banned from 1 October 2022. Plastic and plastic-lined takeaway coffee cups are included in stage 2 of the bans, which start on 1 January 2023. A full list of single-use plastic phaseouts for the relevant states and territories can be found in the February government update on the APCO website: https://apco.org.au/ news/20Y9e00000000fUEAQ.
There are plenty of Australian businesses that are making these changes in their packaging already. In 2019, Woolworths and Coles phased out single-use plastic bags while Officeworks is a leader in the space, having successfully phased out all polystyrene packaging from its home brand furniture and shredders and now helping the wider supply chain to follow suit.
APCO also has a range of tools, programs and resources to help businesses make these changes. In December 2020, APCO published Strategies for Problematic and Unnecessary Single-Use Plastic Packaging, a practical resource to help Australia’s packaging supply chain phase out this packaging through innovative, sustainable solutions.
APCO has a range of new resources currently in production to help industry make the change from single use to recyclable packaging. This includes the roadmap to implement a national phase-out of business-to-consumer EPS packaging, which sets out a voluntary, industry-led approach to address the environmental impacts associated with EPS packaging in Australia.
Looking ahead, APCO will continue to engage with state and territory governments, members and stakeholders regarding SUPs policies.
We are seeking coherent, national approaches based on sound evidence and environmental outcomes. By continuing to collaborate with the complete packaging supply chain, we can shift our approach away from single-use, disposable plastic to more durable reusable and recyclable options.
Brooke Donnelly, CEO Australian Packaging Covenenant Organisation
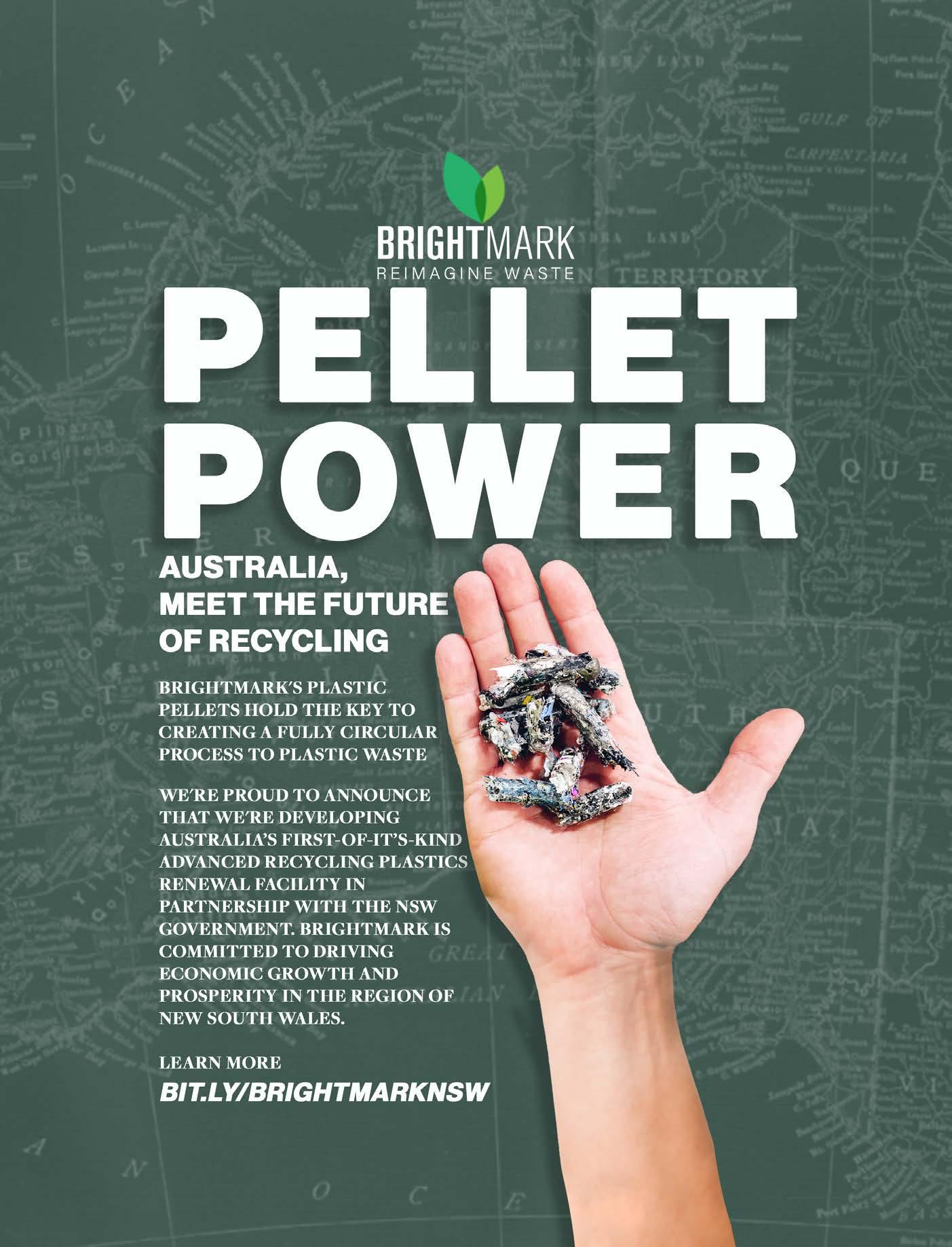
Komptech CEA is a leading supplier of machinery and systems for the treatment of solid waste through mechanical and mechanical biological treatments, as well as the treatment of biomass as a renewable energy source. Komptech CEA is proud to provide innovative solutions for handling waste and biomass.
Komptech CEA’s extensive range of products cover all key processing steps in modern waste handling. At Komptech CEA the focus is always on innovative technology and solutions ensuring maximum benefit to the customer. Like to know more? why not speak to one of our team today?
SHREDDERS TROMMEL SCREENS STAR SCREENS WINDROW TURNERS
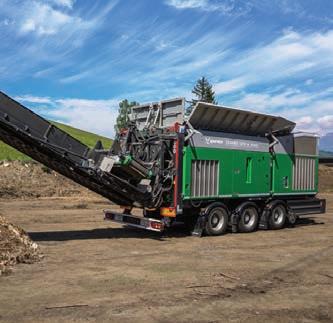
TERMINATOR
Where Function Meets Technology
A slow-running, single-shaft shredder suited to all types of waste.
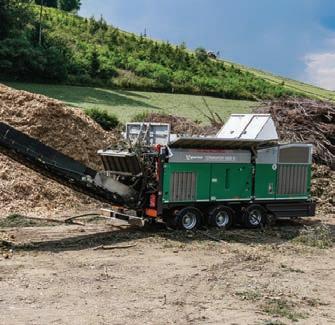
CRAMBO
Less Fuel, More Power
Ideal for shredding all types of wood and green cuttings.
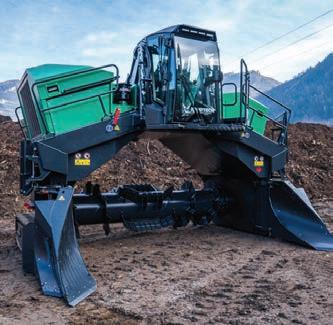
TOPTURN X
The Ideal Combination of Performance and Design
With a sturdy frame, powerful hydraulics and large drum, the Topturn X is ready to handle any work situation.

MULTI STAR
Screening with a Star
Makes waste wood and biomass processing highly efficient.

NEMUS
Robust and Reliable
Combining the practice-proven virtues of its predecessors with new solutions for even greater performance.
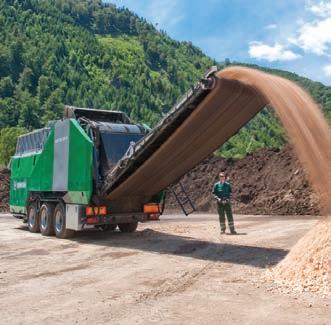
AXTOR
Shredding and Chipping Made Easy
One of the most versatile machines around for processing wood and green cuttings.