
7 minute read
CLEANING UP A LEGACY STOCKPILE
TYRECYCLE’S JIM FAIRWEATHER EXPLAINS THE STRATEGIC PLANNING REQUIRED TO CLEAN UP ONE OF AUSTRALIA’S LARGEST TYRE STOCKPILES IN REGIONAL VICTORIA.
Tyrecycle was appointed last year to clean up a legacy stockpile at Numurkah. Photo credit: EPA Victoria
One of Australia’s largest tyre stockpiles, located within metres of homes and businesses in Victoria, was this year cleaned up by the Victorian Government.
The government at the end of last year appointed Tyrecycle, one of the country’s most experienced tyre recyclers, for the clean-up operation, with the site now deemed safe.
Over 44 operational days, Tyrecycle removed a 5200 tonne stockpile, equivalent to 500,000 tyres, at Numurkah near Shepparton, which posed an extreme fire, health and safety risk to local residents. The total transformation of the site saw 334 truckloads of tyre waste removed over this period.
The company worked closely with Moira Shire Council along with the Environment Protection Authority (EPA), which used its powers to enter the site late last year under the Environment Protection Act 1970.
The EPA introduced tighter controls for waste tyre storage in 2015, prompting a significant reduction in the number of known stockpiles across Victoria, with Numurkah being one of the legacy sites.
The Environment Protection Act 1970 requires scheduled premises to be licensed, with requirements for onsite firefighting resources, limits on the size of the piles and minimum distances between and around them. Stockpiles of more than 40 tonnes or 5000 equivalent passenger car units of waste tyres are scheduled premises under the regulations.
EPA CEO Dr Cathy Wilkinson said the site was an unacceptable fire, environmental and human health risk.
Tyrecycle began work on cleaning up the site in December 2018 under the control and guidance of the EPA and Moira Shire Council.
Jim Fairweather, Tyrecycle CEO, says that the company was transporting 125 tonnes of end-oflife tyres per day from Numurkah to Tyrecycle’s EPA-licensed processing facility in Melbourne at Somerton, where they were cleaned, sorted and shredded for recycling.
“Tyrecycle ramped up its Melbourne facility to a 24/7 operation for the project and doubled its processing capability to remove the huge amount of waste tyres in the most efficient and time effective way,” Jim says.
“We increased our staffing levels to handle the waste, with most of each delivery being processed within 24 hours.”
According to the CFA and EPA, the consequences of a fire at the Numurkah site would have been catastrophic to the local community with air quality impacted and the contamination of soil, groundwater and surface waters.
“It was a great outcome for the local residents, to help them feel safe again
after a decade of uncertainty. It was made possible due to the collaborative efforts between the Victorian Government, authorities and industry – working together,” Jim says.
The EPA conducted site inspections at Tyrecycle’s Somerton facility during the transportation and processing phase of the waste tyres from Numurkah.
Jim says that Tyrecycle is proudly the only EPA-licensed collector and recycler of tyres in Victoria and all environmental regulations were met during the project.
“Our planning procedures are thorough, including specific transportation schedules for the collection and arrival of waste.”
He says that the conditions were extremely challenging and strategic planning is required to begin a clean-up operation especially of this magnitude.
“Firefighting equipment is always onsite. However, when temperatures went to 40 degrees or if there was a total fire ban, all work ceased as the searing weather conditions resulted in an unsafe working environment.
“Fire safety preparation is paramount during a clean-up, as well as heightened security and effective management of any wildlife and vermin on site. With careful planning and protocols, we were pleased to deliver an incident-free project.”
The majority of the shredded and recycled waste tyres were converted into tyre-derived fuel (TDF), helping companies reduce their environmental footprint across South-East Asia.
“TDF is an attractive alternative fuel on an international scale. The


extremely high calorific value of the product has significantly lower volumes of greenhouse gases when compared with coal,” Jim says.
The recycled tyre waste from the Numurkah site is also being used for a variety of products across the construction, manufacturing and automotive industries, including crumbed rubber for road surfacing, athletics tracks and brake pads.
Tyrecycle also worked with the EPA in Victoria in 2017 to remove another dangerous and large tyre stockpile on the outskirts of Stawell.
During a clean-up operation lasting just over two months, 9500 tonnes of tyres which had been stockpiled for many years were removed, with more than two-thirds of the tyres transported to Tyrecycle’s Melbourne facility for processing and recycling.

Geological journey
TELLUS HOLDINGS’ STEPHEN HOSKING HIGHLIGHTS CONSTRUCTION WORKS ON AUSTRALIA’S FIRST KAOLIN MINE AND GEOLOGICAL WASTE REPOSITORY.
According to the Department of Innovation, Industry and Science, as of January 2019 the amount of hazardous waste in Australia was growing at a faster rate than the population.
If not managed correctly, hazardous waste can have disastrous effects on communities and the environment. In order to regulate the industry and mitigate the risk of rogue operators, the approvals process needs to be thorough.
These risks highlight the significance of infrastructure development company Tellus’ Sandy Ridge facility. Sandy Ridge will accept up to 100,000 tonnes of hazardous waste per annum, using a best practice multi barrier system that comprises man-made barriers (active control) and natural barriers (passive control) that can permanently isolate the waste for millions of years.
The Federal Government shares a similar contention, awarding the facility Major Project Facilitation status in 2017.
Tellus has recently received local government approval from the Western Australia Mid-West Wheatbelt Joint Development Assessment Panel (JDAP), the latest step in a long run of studies and approvals over six years for the project.
The company received approval from a number of government bodies including the Commonwealth Department of Environment and Energy, the Western Australian EPA, the Western Australian Department of Mines Industry Regulation and Safety and the Western Australian Department of Water and Environmental and Regulation.
The JDAP approval is a further show of support for Tellus’ plans for long term storage, recycling and recovery of valuable materials and the permanent isolation of hazardous waste, including naturally occurring radioactive material and disused radioactive sources.
With approvals in hand and financing secured earlier this year, Tellus’ General Manager Stephen Hosking, who is responsible for constructing Tellus’ infrastructure, says the company has now commenced construction of enabling works at Sandy Ridge.
“GR Engineering Services (GRES)
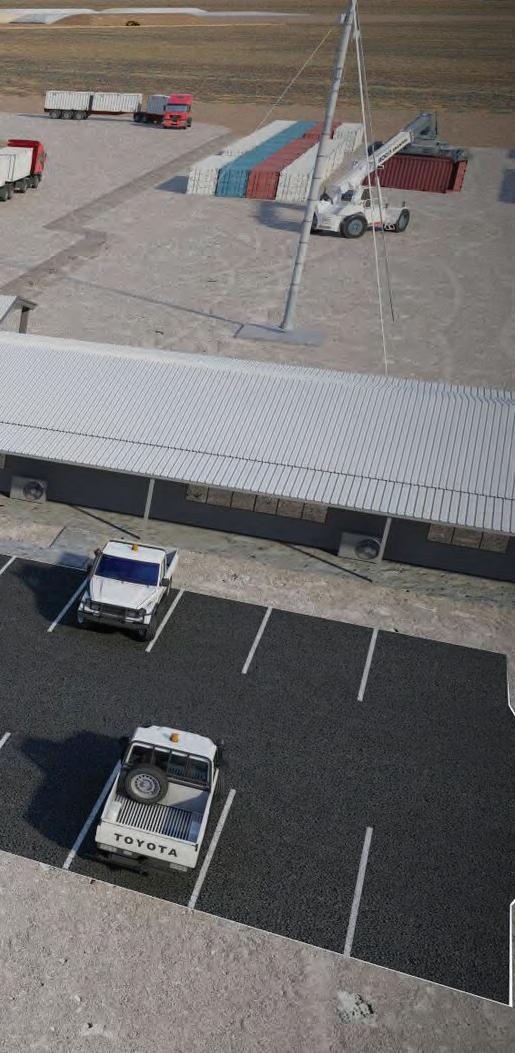
were awarded the lead engineering, procurement and construction (EPC) contract in February and have commenced detailed design and procurement ahead of mobilising to site in June this year.”
As well as the lead EPC contract, the enabling stage of construction also
Sandy Ridge operations will commence from March next year.
involves maintenance and upgrade contracts focused on local roads and intersections around the facility, allowing for safer access. It also involves upgrading a neighbouring airstrip to enable the site’s workforce to travel to and from the site.
Stephen says work on the airstrip is particularly important to the company as the site will soon see the arrival of more than 100 construction workers and up to 80 operational staff at its peak.
“We have spent a considerable amount of time focusing on how we can make our site a great place to work and so being able to fly to a nearby airstrip cuts down travel time considerably. Providing our staff and contractors with best-in-class accommodation and food with good
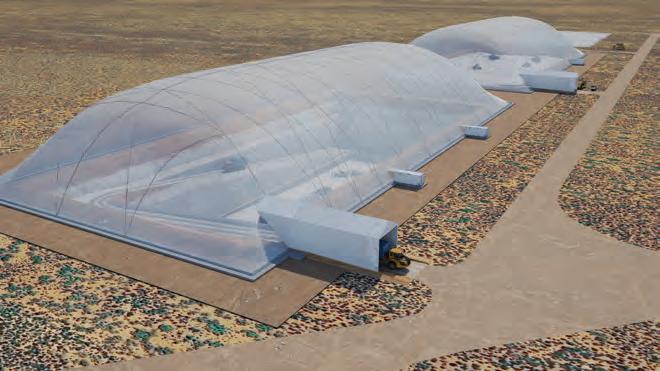

communications connectivity have been non-negotiables for us.”
In parallel to the GRES award, Tellus has also mobilised project management consultant Turner and Townsend to its Perth office, and placed long lead procurement orders with Fleetwood Australia for site buildings and an innovative air dome structure from US-based supplier Arizon Building Systems.
“Air domes are very popular in North America and Europe and we are very excited to be bringing this innovative and low-cost building system to Australia. The air dome will be installed by GRES before mining of our first waste cell. It will allow year-round waste operations for our clients, while providing a safe working environmental for our personnel,” Stephen says.
Commencement of construction on the main facility site is planned for June when GRES will mobilise to Sandy Ridge.
The site works will include installation of the air dome, development of the first kaolin open pit or waste cell, container yards, an onsite laboratory, office and accommodation village.
The facility will start to accept waste for surface storage in September this year with full operations commencing from March next year.