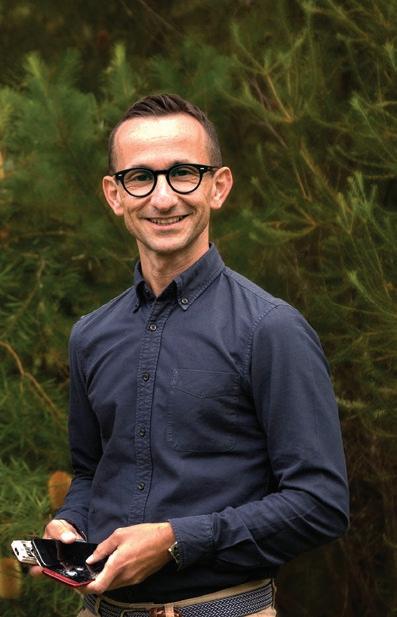
8 minute read
MOBILE EXTRACTION
MOBILEMUSTER MANAGER SPYRO KALOS TALKS TO WASTE MANAGEMENT REVIEW ABOUT THE RECYCLING PROCESS FOR SMARTPHONES AND THEIR REUSE POTENTIAL.
With recycling across the board gaining significant attention due to China’s National Sword and resulting policy changes, public trust in the process has been challenged.
“Plastic not so fantastic”, a recent 60 Minutes report, further complicated matters by suggesting the public’s recycling efforts were being wasted on dubious resource recovery.
While waste industry associations say the report didn’t paint a full picture of the Australian recycling industry or its processes, public
MobileMuster’s Spiro Kalos estimates 25 million unused mobile phones are currently sitting dormant in Australian homes.
discussion around China’s National Sword policy continues.
MobileMuster, the federally accredited product stewardship program of the mobile phone industry, is focused on educating the public about the mobile phone recycling process to further confidence in the e-waste resource recovery market and increase mobile phone recycling.
It’s a significant goal given 89 per cent of Australians own a smartphone, according to a 2018 Deloitte Mobile Survey, and many hoard their devices.
Since the product stewardship program began in 1998, MobileMuster has collected and recycled over 1400 tonnes of mobile phone components including handsets and their batteries, chargers and accessories.
To date the program has recycled over 13 million handsets.
MobileMuster works to provide free mobile phone recycling in Australia and is voluntarily funded by all major handset manufacturers and network carriers such as Apple, Google, Telstra and Samsung.
MobileMuster’s 2018 Annual Report estimates that e-waste is growing three times faster than any other waste stream in Australia. It is no surprise then that MobileMuster Manager Spyro Kalos estimates 25 million unused mobile phones are currently sitting dormant in Australian homes.
“While we know less than two per cent of mobile phones are being thrown into the general waste stream, we need to work to reduce the number of mobiles lying dormant in storage,” Spyro says.
“There is certainly value in recovering the materials inside those phones to reduce wasted resources.”
According to Spyro, what many people don’t know, or rather don’t think about, is their smart phone contains untapped precious metals and raw material, most of which has been mined.
Additionally, smartphones contain many of the materials the waste industry and public at large are accustomed to thinking about, plastic, glass and aluminum, making them full of untapped reuse and recycling potential.
“I am a strong believer in transparency. When someone recycles their mobile phone with MobileMuster, I want them to know exactly what happens and how the various components are being processed,” Spyro says.
“We need to increase the trust of consumers because without their participation, the circular economy breaks down. The industry has an obligation to all its stakeholders to ensure best practice is used when collecting and processing products.”
MobileMuster’s recycling partner is TES, a global electronic waste recycler and lifecycle management service. The two groups have been working together for six years.
According to Spyro, they work to maximise recovery rates and ensure
all mobile components are correctly processed.
“Through our recycling process, over 95 per cent of a mobile phone’s material re-enters the supply chain and is used for the fabrication of new products,” Spyro says.
“We transform the device’s waste components into valuable materials for reuse, which means fewer raw materials need to be extracted.”
Spyro says that when someone leaves their old device at one of MobileMuster’s 3500 public drop off points, it is collected and transported to a TES recycling facility in Melbourne, Sydney or Brisbane.
“The device is then disassembled into individual components including batteries, printed circuit boards, casing, screens, accessories and packaging,” Spyro says.
“None of the phones are resold, and any data left on the device is destroyed during the disassembling process.”
Spyro says components are then further processed though shredding and sorting techniques to maximise resource recovery.
“In 2017, TES started using Envirostream to process smartphone batteries, which is a difficult waste stream. At TES facilities in Melbourne, the batteries are granulated and sorted in materials for recycling,” Spyro says.
“The process recovers copper, aluminium, cobalt, nickel, lithium and plastics. The onshore solution also reduces the need to transport the batteries internationally for processing.”
In the age of smartphones and touch screens, glass is another core material in the recycling process.
“Glass from smartphones is crushed

and melted before being reused for new products or as a replacement material in construction elements like roadbase.
“Aluminium is another significant component of mobile phones, and one of the most easily recycled materials. The recycling process uses considerably less energy than producing new aluminium.”
Aluminium is melted in a furnace, with the resulting liquid aluminium placed in moulds to create new products like drink cans, bikes and car bodies.
MobileMuster recycled one million handsets last year, and according to Spyro, the organisation needs to keep that momentum going if they hope to continue effectively tackling e-waste.
“The public need to be sure that when they leave their phone with MobileMuster, almost the entire device is being reused.”
Genie in a bottle
SHRED-TECH SALES MANAGER SEAN RICHTER TALKS TO WASTE MANAGEMENT REVIEW ABOUT THE COMPANY’S 20-YEAR HISTORY IN E-WASTE RECYCLING AND DATA DESTRUCTION.
Governments and manufactures of electronic hardware are increasingly coming under pressure to implement policies and practices around safe e-waste disposal.
E-waste’s status as a problematic waste stream has a long history. In 1976, the United States Resource Conversation and Recovery Act made it illegal to dump e-waste. Likewise, in electronic products.
Shredding and recycling system manufacturer Shred-Tech has been in business for over 40 years. Sales Manager Sean Richter says in that time, the company has designed and manufactured some of the largest e-waste reduction systems in North America.
“These systems were originally
Electronics have become considerably smaller and lighter than Shred-Tech’s initial systems were designed for.
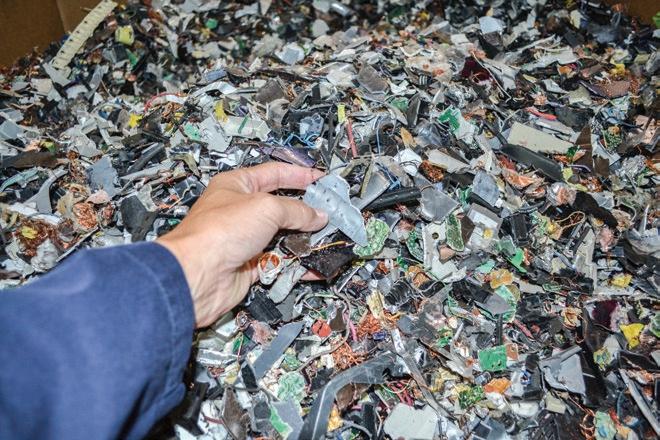
in 1989 the Basel Convention made it illegal to dump e-waste in developing countries.
As a Basel Convention signatory, Australia is bound to this agreement. E-waste is also banned from landfill in Victoria, South Australia and the ACT.
Legislative measures like these are incentivising recycling equipment manufactures to engineer technology and machinery capable of processing multiple material components present designed to use high horsepower and brute force to shred and granulate everything from large main frame computers, military electronics, telecommunications equipment and high-tech electrical switching gear,” Sean says.
As electronics have become considerably smaller and lighter than Shred-Tech’s initial systems were designed for, the equipment and processes have evolved.
“Today’s systems have advanced to encompass newer technologies in reduction, usually with lower power requirements, better material handling and separation of the materials prior to smelting or electrochemical processes for extraction,” Sean says.
An end-of-life laptop or phone could expose the financial records, health records, photographs and personal communications of its prior owner. Data and privacy is therefore a key consideration for e-waste recyclers.
According to Sean, the level of shredding provided by Shred-Tech plants makes it virtually impossible to extract data from the end material.
“Computers and telecommunications equipment are subject to massive reduction forces, shattered into hundreds of fractions and mixed with thousands of other materials before heading to final recyclers. Finding one with usable data would be like finding the genie in the bottle.”
Sean says one of the challenges with e-waste processing is how varied the waste stream is, encompassing a range of materials requiring different cleaning and processing methods.
“We have designed and built custom machines and systems ranging from portable hard drive shredders, systems that shred only circuit boards and standalone machines designed primarily for destruction purposes,” Sean says.
A key component of Shred-Tech’s business is the design of modular e-waste shredding plants.
“Our shredding systems can be custom configured using proven system
modules to meet specific capacity and separation requirements,” Sean says.
“The systems reduce and separate component material such as plastic, aluminium, copper, steel and precious metals.”
According to Sean, a typical ShredTech e-waste recycling plant starts with an incoming triage.
“The triage sorts material into type slots, such as hazardous material, material suitable for manual disassembling and resaleable components like integrated circuit chips and power supplies,” Sean says.
The next stage is primary reduction, typically completed by a large twin shaft shredder.
“The goal during primary reduction is to break the material into sortable fractions. The material is then sorted manually on pick lines or via magnets

and additional size screening devices,” Sean says.
“Ferrous-based and commingled material is then removed by an initial magnet before being sent for secondary reduction and liberation to minus 50 millimetres.”
According to Sean, there are several schools of thought on how to best achieve secondary reduction. The first is sending all ferrous based material to a high-speed reduction unit such as a ring mill.
“The ring mill liberates all ferrous material with the help of a secondary magnet and removes clean steel for resale. All remaining materials carry on to secondary reduction,” he says.
“Others like to send all material to a large four shaft shredder for liberation and final reduction. I find the high content of ferrous material in this stream results in accelerated wear, however, and leads to high maintenance costs for the four-shaft shredder.”
Following this, material fines are removed by screeners, which eliminates all particles minus two to five millimetres. Sean says removing fines enables increased tuning of the downstream separators.
“All material is then passed over by an eddy current for aluminium removal. Additionally, the stream is then sorted manually to ensure the highest purity of aluminium for resale.”
Remaining materials such as circuit boards, copper and plastic continue to further separation. “The plant then optically sorts using a wide variety of technologies that specifically targets plastic of colour, green circuit boards, wire, copper and other materials into various resalable streams,” Sean says.