
28 minute read
METRO CLEAN UP
Metro Waste cleans up with Isuzu
TO CAPITALISE ON THE RAPIDLY GROWING WASTE SECTOR AND BOOST ITS MINI BIN CONCEPT, METRO WASTE IS UTILISING A HEARTY FLEET OF ISUZU WASTE TRUCKS.
According to the latest National Waste Report, Australians generate an estimated 67 million tonnes of waste over a 12-month period. This translates to a staggering 2.2 tonnes of waste per person every year.
Analysing these figures, it’s no surprise that there’s been renewed focus on established waste and recycling management and solutions.
The microscope continues to be applied to key industry stakeholders and their waste and recycling operations, and the rest of the nation is watching.
Operating in this space and contending with the rapidly changing waste and recycling conundrum is Metro Waste.
Arguably one of the more recognisable waste and recycling management businesses in Adelaide, Metro Waste, with its fleet of branded Isuzu Trucks, services Adelaide city and the greater Adelaide region.
They collect all manner of waste and recycling materials, before returning to their Thebarton-based transfer station for sorting, cleaning
Anthony Callipari, Carmelo Rositano and Justin Castelluzzo of Metro Waste developed the mini-bin concept to better cater for the diverse needs of their customers.
and categorisation.
Metro Waste has operated throughout Adelaide for more than three decades, headed by co-owners Anthony Callipari, Carmelo Rositano and Justin Castelluzzo.
Business partners and friends, the trio have a shared vision of growing and evolving with the waste and recycling landscape, and have added a mini bin service offering, so as to better cater to the diverse needs of their customers.
The mini bin service began as a straightforward concept, but Callipari describes it as the spark that kickstarted the beginning of their real success.
“The three of us went to school together and ended up purchasing the business. We then introduced the mini bin service to the mix and we’ve kept growing ever since,” Callipari says.
Having kicked things off with only one Isuzu truck on the road, Metro Waste now have a nine-strong Isuzu truck fleet covering the length and breadth of Adelaide and surrounds.
The latest additions are an Isuzu FVR 165-300 and the robust sixcylinder FSR 140-260, both fitted with skip bin loaders and adorned with livery – all facilitated by the team at North East Isuzu in Burton.
Metro Waste’s Isuzu fleet directly supports the mini bin segment of the business, with bins that range from two to 40 cubic metres in size available seven days a week.
Anthony Callipari Co-owner, Metro Waste
“Our trucks pick up and drop off bins throughout the suburbs, as well as waste from the bigger commercial construction jobs in and around the CBD,” Callipari says.
“They work in dusty and dirty environments, and are sometimes required to go off road. They’re definitely put through their paces. Each truck will cover a minimum of 600 kilometres each week, clocking anywhere between eight and 15 bin
Metro Waste operate a nine-strong Isuzu truck fleet.
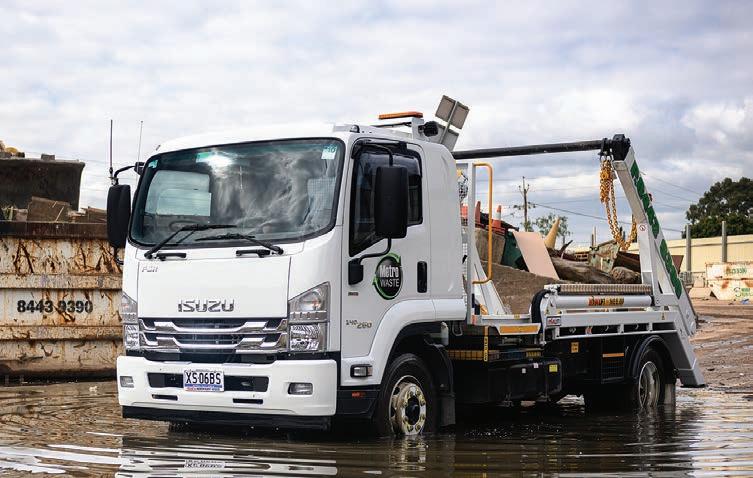
shifts.”
Callipari and his partners recently returned to North East Isuzu with the need to “fill the gaps”, so that Metro Waste could facilitate a full range of bin sizes and capacities. With an extensive range of Isuzu trucks on hand at North East Isuzu, they were well assisted in selecting the best solution for this unforgiving task.
“Without trucks, we haven’t got a business,” Callipari says, explaining the innate reliance of the waste management industry on the capital equipment charged with transporting materials from point A to point B.
“We’re obviously dependent on trucks, without them we’ll have stockpiles of waste and we wouldn’t be able to service our customers.”
Contact – Isuzu
P 1800 035 640 W www.isuzu.com.au
Metro Waste’s fleet of branded Isuzu Trucks services Adelaide city and the greater Adelaide region.
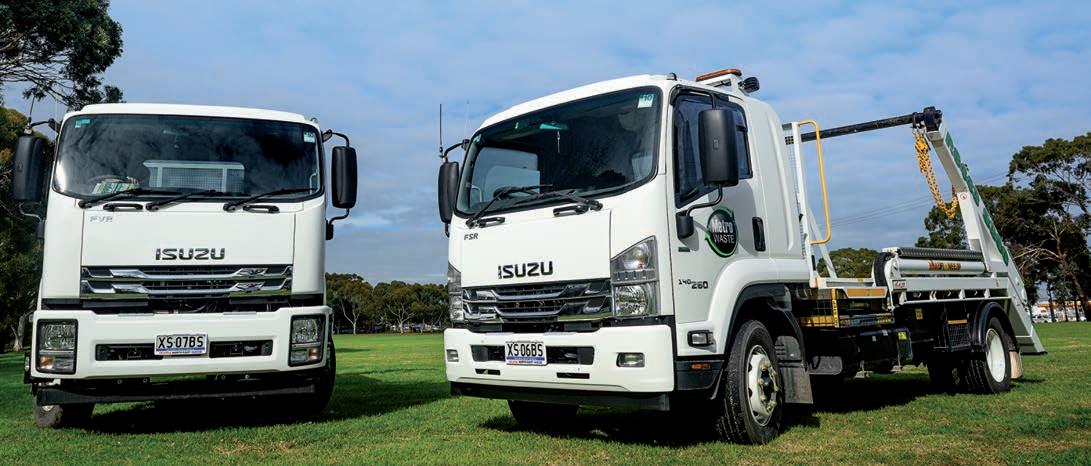
Wastech’s Flexus Balasystem’s can increase usable landfill volume by up to 40 per cent.
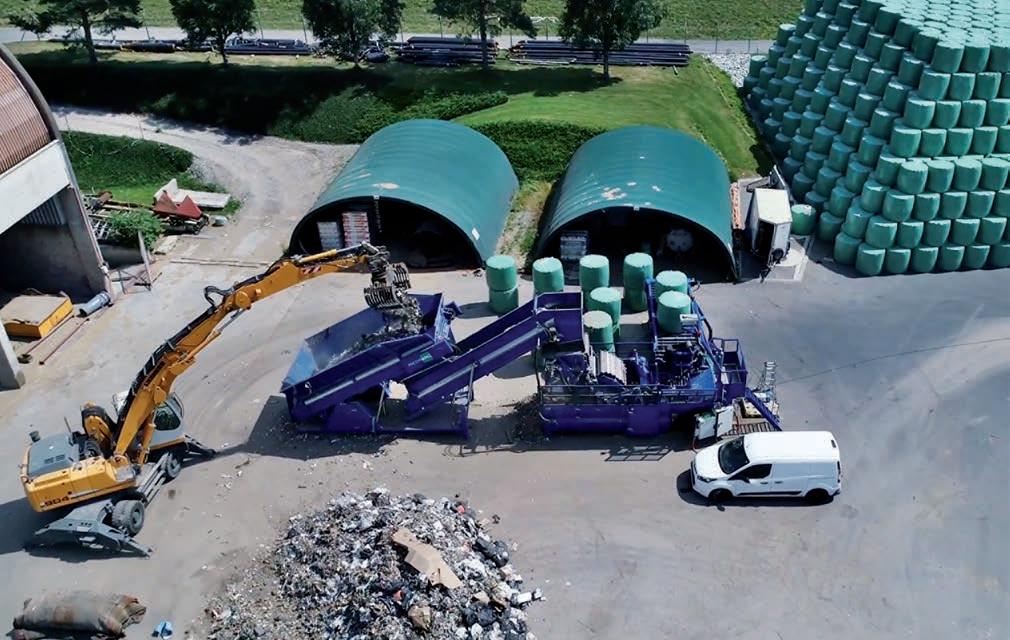
Maximising landfill life
AS THE EXCLUSIVE AUSTRALIAN DISTRIBUTOR OF FLEXUS BALASYSTEM’S, WASTECH ENGINEERING IS WORKING TO OPTIMISE SUSTAINABLE LANDFILL MANAGEMENT.
In the spring of 1997, Flexus booming tourism industry. The project world-wide. The system provides an Balasystem was asked to install was a success, with similar installations optimum solution for the handling its unique integrated bailing and now complete in over 53 countries. and disposal of municipal solid waste, wrapping machine in a small town on While Flexus Balasystem’s offering significant advantages over the Mediterranean coast of France. At technology has advanced significantly traditional bailing in terms of cost the time, Adge produced an average since 1997, the ethos of the company efficiency and environmental safety. of 25 tonnes of municipal solid waste remains the same: building waste To capitalise on these advantages each day, with daily peaks of over 150 handling technology that produces and fill an identified gap in the tonnes in the summer months. The positive environmental outcomes. Australian market, Wastech goal of the municipality was to manage The unique Flexus round-bale Engineering recently developed an waste in an environmentally safe technology was pioneered in Sweden, exclusive distribution partnership with way, while not disturbing the regions with several hundreds of installations Flexus Balasystem.
According to Chris Andel, Wastech National Product Manager – Projects, the partnership will provide Australia’s waste sector with access to sustainable landfill solutions. He explains that as the country begins to grapple with declining landfill space, the distribution deal could not have come at a better time.
“By utilising the Flexus system, landfill densities are radically improved and day-to-day landfill problems such as wind control and litter are eliminated. Odours are also controlled, and vermin issues resolved,” Andel says.
The Flexus system is a complete heavy-duty unit for bailing and wrapping, storing and transporting compressed waste in round bales, allowing the material to be buried or stored for incineration at waste-toenergy facilities.
“Material is rolled or milled and naturally compressed with no external pressure, with the natural filling effect allowing desired density to be achieved,” Andel says.
With a processing capacity of up to 30 tonnes per hour, the Flexus system has a helicopter-style wrapping component, with bale ejection at either side of the machine. Finished bales are then ejected onto a bale conveyor that holds up to three finished bales at once.
“As an all in one system, the Flexus is cost effective, with a single machine fulfilling all tasks along the chain,” Andel says.
“The result is significant waste volume reduction and no leachate during round baling. Because of the compressed nature of the bale chemistry, contents are rendered biologically inert, leaving no methanogenic activity inside the bale.”
This is a particularly salient fact, Andel explains, as state governments across Australia attempt to reduce the harmful effects of landfill methane gas via reduced organics to landfill targets.
“By preventing oxygen and waste from penetrating the waste, Flexus bailing and wrapping systems halt the biochemical process,” he says.
In a study conducted by the University of Lund in Sweden, no considerable temperature increase or methane production was observed from the bales after a year, with most biological and oxidation reactions virtually stopped. Andel adds that the system has a small footprint and low civil costs, with compacted and wrapped bales sealed in modular cells that can be stored on site. The Flexus is particularly suited to municipal solid waste landfill remediation, he says, while also offering the ability to optimise landfill space at functioning sites. Andel explains that the unit can increase usable landfill volume by up to an extra 40 per cent.
Standard bale weights range from 600-1600 kilograms, with rapid handling and full manoeuvrability.
The system can be designed for stationary installation and be fully integrated into waste treatment plants.
The installation is designed to meet the demands and conditions of each specific case, Andel says. He adds that the mobile baling system can be easily transported from site to site.
“This provides operators with the flexibility to handle both smaller and larger baling commissions,” he says.
The system is available in three different models, with each designed to provide clients with many years of reliable service.
Contact – Wastech Engineering
P 1800 465 465 E info@wastech.com.au W www.wastech.com.au
ONBOARD AXLE LOAD INDICATOR
DISPLAYS AXLE AND GROSS WEIGHTS
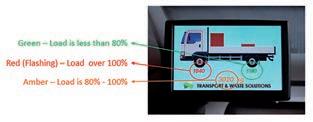
SIMPLE COLOURCODED DISPLAY
WHY FIT AXTEC ONBOARD?
Customers can: • Load vehicle to capacity every time • Avoid fines and threats to Operating License • Avoid excessive wear and tear to associated with overloads • Reduce environmental impact • Receive real-time notifications via GPS / telematics system • Connect cameras to improve safety to pedestrians and cyclists
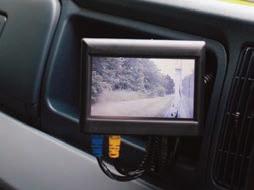
Safety and flexibility in the field
ZYGGY REINOGA, KEITH WALKING FLOOR AUSTRALIA MANAGER, OUTLINES THE SAFETY BENEFITS OF THE COMPANY’S PROVEN WALKING FLOOR TECHNOLOGY.
Australia generates over 67 million tonnes of waste each year, with more than a third created by the construction and demolition (C&D) industry. In 2017, the industry generated 20.4 million tonnes of waste, with much coming from road and rail maintenance projects and the booming infrastructure pipeline.
C&D waste is typically abrasive and heavy, comprised of bricks, concrete, metal, timbre, asphalt and rock. As such, transporting C&D to recycling facilities for processing can be a challenge.
To meet that challenge, Zyggy Reinoga, Keith Walking Floor Australia Manager, says operators require heavy
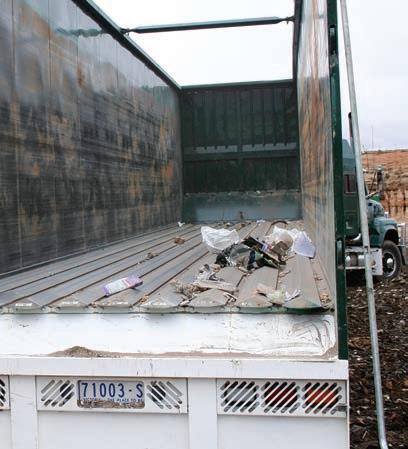
Walking Floor technology is a horizontal loading and unloading system. duty and versatile trailers.
Designed to handle a variety of bulk products, Reinoga says Keith Walking Floor systems offer many benefits over conventional tipper trailers.
Since launching the system over 45 years ago, Keith has adapted its proven Walking Floor technology to the waste, recycling and aggregate industries, resulting in a safer, more efficient and versatile trailer.
According to Reinoga, the horizontal unloading action of a moving floor system eliminates many of the hazards of using tipping trailers to unload products in the field.
“Several factors can cause tippers to become unstable when raised for tipping. A ground surface that is not level, material that shifts or does not evenly unload and wind gusts – all can contribute to overturned trailers,” he says.
Trailers with Walking Floor systems safety unload on uneven ground, provide a controlled material discharge and can unload in windy conditions. In addition, Reinoga says these trailers can unload adjacent to other equipment, which is not recommended for tipping trailers due to the increased risk of overturning the trailer.
“Another benefit of unloading trailers with a Walking Floor system is that there is no risk of hitting overhead power cables or trees during unloading,” he says.
“Trailers can also unload in tunnels, under bridges and inside buildings.”
A trailer outfitted with a Walking Floor unloader provides operators with flexible unloading options.
Unloading can be stopped or slowed as needed, allowing for the delivery of partial loads or loads at multiple locations. The systems also handle a variety of bulk materials, from abrasive products such as C&D waste to lighter materials such as organics and compost.
“This provides operators with nearly unlimited waste hauling opportunities,” Reinoga says.
Walking Floor technology is a horizontal loading and unloading system. While in motion, the floor slats remain horizontal, reciprocating sequentially and then in unison to convey the load. Advantages include an increase in the floor area that actually moves the load and a significant reduction in the weight of the slats.
Keith has more than 45 years of experience engineering trailer unloading solutions for its customers.
All systems are backed by a standard two-year warranty on hydraulic components.
Contact – Keith Walking Floor
P 0404 041 883 E zreinoga@keithwalkingfloor.com W https://www.keithwalkingfloor.com/
CAT’S DURABLE 966M WHEEL LOADERS
In the harsh and demanding environment of waste handling applications, operators require wheel loaders that can meet daily challenges.
With the high demands of inbound and outbound tonnages, feed line production rates and limited manoeuvring space, Cat’s 966M Wheel Loader provides safe, productive and reliable service.
The loader meets local emission standards and is designed to improve fuel economy while lowering long-term costs and facilitating un-interrupted performance.
The 966M is also equipped with new designed easy to load buckets and an integrated PAYLOAD system. Additionally, the loader features a next generation adjustable seat and a revolutionary suspension system. Controls are easy to use, intuitive and user-friendly with joystick steering.
The 966 Range offers a planetary transmission as standard, or an optional XE model where power is transmitted through a hydraulic variator unit alongside a parallel mechanical gear path to maximise transmission efficiency over a wide range of operating conditions at lower rpm, saving fuel by up to 25 per cent.
The Waste Handler configuration comes standard with specific industry guarding to protect critical areas of the
The 966M is equipped with easy to load buckets and an integrated PAYLOAD system.
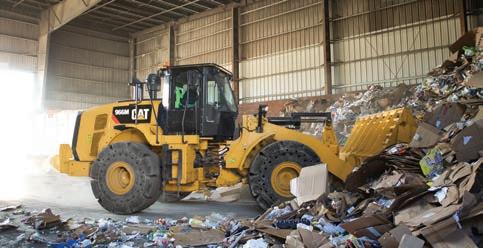
machine for working in waste. Hydraulic cylinder guarding, front frame, powertrain and crankcase guarding are all included together with durable axle seal guards for added protection.
All Cat M Series Wheel Loaders meet or exceed safety standards in waste handling applications and include features such as a rear-view camera, reverse lighting, standard anchorage points and back-up alarms.
With up to 15 per cent lower maintenance costs, operators benefit from extended service intervals, which in turn, saves businesses time, money and energy.
Contact - Cat W www.cat.com/en_AU.html
CJD’S HIGH-POWERED VOLVO L260H WHEEL LOADER
An asset to demanding waste operations, the Volvo L260H wheel loader is a reliable machine that has been upgraded with innovative technologies and increased payload capacity for greater productivity.
Available in Australia though CJD Equipment, the L260H boasts a range of features to enhance the operating experience.
For increased productivity, the Volvo cab can be customized to operator preference, with additional cameras and radar detect systems providing visual and audible alerts to operators to streamline safe waste handling.
Engineered for efficiency, the L260H is fitted with a powerful D13 engine, delivering six per cent more power and five per cent more torque than the previous L250H model.
Operators can achieve shorter cycle times with next generation load sensing hydraulics, designed to enhance the responsiveness of attachments and improve the lifting and lowering speed of the boom.
The L260H has also been upgraded with a new HTL310 transmission, which works in harmony with the powerful engine and axels. The new torque converter delivers increased torque output, resulting in enhanced performance.
For faster acceleration and smooth operation, the steps between gears have been reduced.
Operators can achieve shorter cycle times with next generation load sensing hydraulics.
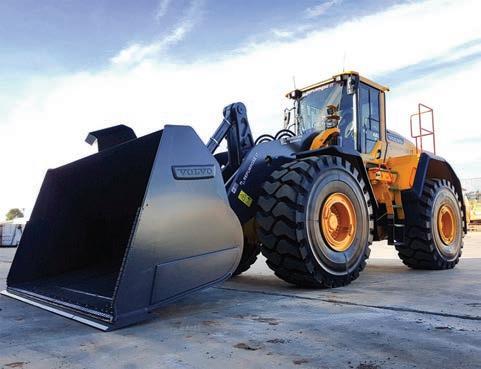
For strength in demanding applications, Volvo’s proven Z-bar linkage provides high breakout force.
Additionally, the robust lifting arm enables fully loaded buckets to be elevated to maximum height and fast hydraulic speeds offer quick cycle times.
Contact - CJD Equipment P 08 9478 0000 E enquiries@cjd.com.au W www.cjd.com.au/
SUEZ and Hitachi Construction Machinery Australia have enjoyed a healthy relationship since the delivery of an ZX200LC-3 hydraulic excavator seven years ago.
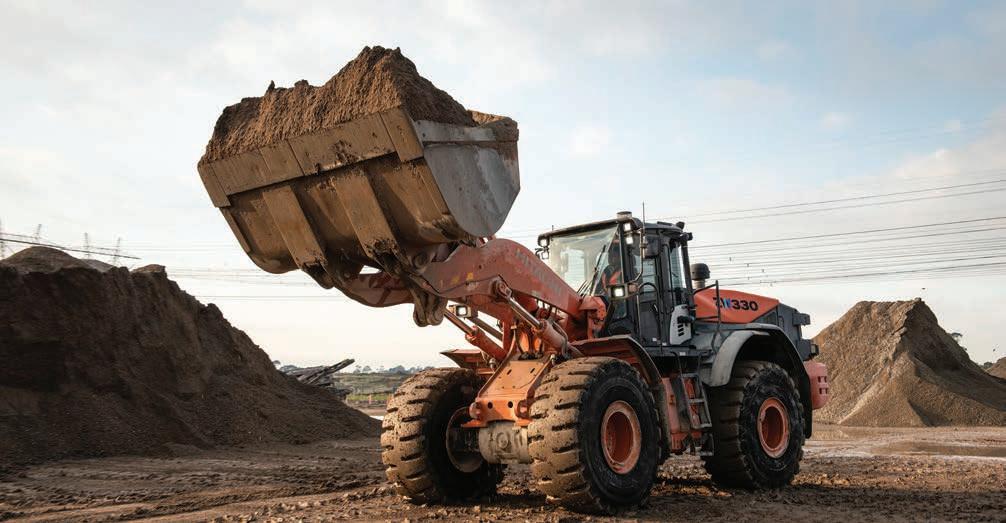
Machinery to close the loop
TO BOOST SYDNEY’S RECYCLING NETWORK, WASTE MANAGEMENT GIANT
SUEZ HAS WELCOMED 11 HITACHI CONSTRUCTION MACHINES TO ITS FLEET.
Spanning approximately 13.4 recyclable materials into different cutting edge technology. hectares, SUEZ’s NSW Chullora streams, which will then be transported As a company strongly committed Resource Recovery Park sees to manufactures for reprocessing into to innovation, SUEZ recently engaged over 157,000 cars and trucks each year. new products. Hitachi Construction Machinery
Opened in 1997, the recovery park, Operating globally for 160 years, Australia (HCA) as a like-minded which incorporates a transfer station SUEZ aims to help businesses, provider of construction machinery and organics processing site, is currently governments and communities shape to assist their waste management under redevelopment. a sustainable environment through the operations.
The $40 million project includes plans reuse and recycling of water and waste. SUEZ has purchased 11 machines to develop a state-of-the-art materials Employing over 2800 people in from HCA, including six ZW180-5- recycling facility (MRF), with the view Australia alone, SUEZ operate more wheel loaders and five ZX135US-5 of increasing the capacity and resilience than 100 waste management facilities excavators. Prior to this purchase, SUEZ of Sydney’s recycling network. across the country. acquired a ZW250-5-wheel loader for
Through the implementation of a As a result, this enables them to its Spring Farm, NSW facility, along pull-through model that conceives of provide solutions that supply seven with purchasing an ZX490LCH-5 the sorting, reprocessing and specified million Australians with safe drinking excavator and ZW330-5 and ZW370-5- end uses of processed materials as an water, while diverting 1.2 million wheel loaders for its Victorian business. integrated, closed loop solution, the tonnes of waste from landfill each year. HCA’s excavators will be used at new facility aims to deliver on the SUEZ prides itself on innovation the new Chullora MRF to recover principals of a circular economy. and always looking forward, globally resources from various waste streams,
The Chullora MRF will sort investing $175 million every year into unblock chutes and crush material to
increase payloads.
Additionally, the wheel loaders will stockpile various waste materials and load hoppers with material.
According to Ash Turner, SUEZ NSW Business Manager, SUEZ’s loyalty to the Hitachi brand comes down to the reliability, comfort and ease of operations of the machines, competitive pricing and high-level servicing support.
“The excavators have been well received, are extremely comfortable and perform the required tasks well,” Turner says.
Additionally, he praises HCA’s Barry Cahill, Matt McCarthy and Grant Warren on their structured commitment, professionalism and great detail when delivering the machines, particularly in light of current COVID-19 social restrictions.
McCarthy, HCA National Major Account Manager, says HCA and SUEZ have enjoyed a healthy relationship since the delivery of an ZX200LC-3 hydraulic excavator seven years ago.
“Since then, our relationship has really strengthened, as both companies enjoy a professional and collaborative approach from site level to senior level,” he says.
Furthermore, McCarthy says HCA’s close relationship with the waste industry allows the company to manufacture machines based on extensive specialised knowledge.
He adds that HCA takes its contribution to the waste and recycling industry very seriously.
“We are committed to doing our part to improve the earth’s environment, and working alongside with SUEZ makes it all worthwhile,” he says.
McCarthy explains that HCA and SUEZ share a similar commitment towards investing in charities and supporting local communities.
Both are key sponsors of the Clontarf Foundation – a program established in 2000 that aims to improve educational attainment and employment outcomes for indigenous boys and young men.
The Clontarf programs are established as a “home room” in selected high schools where students receive mentoring to improve discipline, life-skills, self-esteem and education.
Through their partnership with the Clontarf Foundation, HCA and SUEZ have provided Clontarf members with workplace experience and job opportunities.
Contact – Hitachi
P 1300 HITACHI E marketing@hcma.com.au W www.hitachicm.com.au/
Did you know that VENTING Refrigerant to the Atmosphere or simply burying/scrapping your whitegoods & aircon units with the refrigerant left in, is ILLEGAL
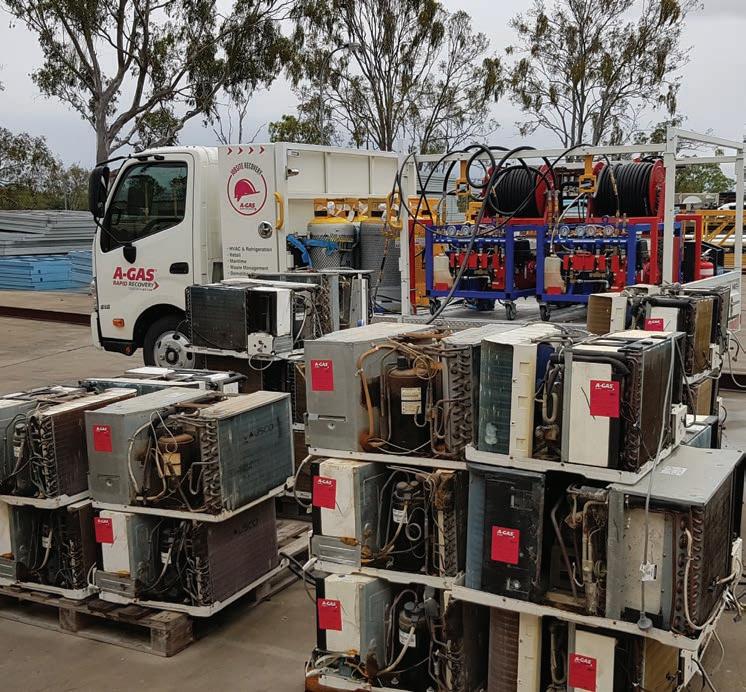
in Australia?
Don’t risk a fine, get the Arctick ✓
Call A-Gas Rapid Recovery 1800 002 427, Your Refrigerant Recovery Experts.
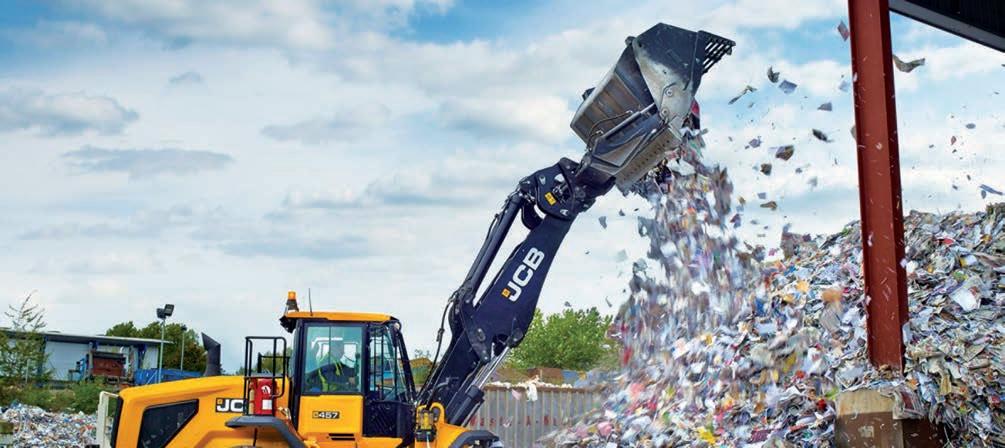
JCB wheel loaders are designed with customer input at every stage of the process.
Waste never stops
COREY JEFFS OF KTS RECYCLING EXPLAINS HOW RELIABLE JCB WHEEL LOADERS AND EXCAVATORS HELP KNOX TRANSFER STATION KEEP UP WITH 24/7 WASTE INPUTS.
Earlier this year, KTS Recycling pledged to TAKE2. Delivered through Sustainability Victoria, TAKE2 is a collective climate change program supporting individuals, government and businesses to help the state achieve net zero emissions by 2050. The pledge is one in a long line of sustainability initiatives from the KTS team, who’s transfer station provides a valuable, local recycling and trading centre for Melbourne’s Eastern Suburbs.
Working in connection with the Knox City Council, KTS is committed to reducing Victorian landfill and maintaining the natural beauty of the surrounding Dandenong Ranges.
The transfer station differs from Melbourne’s traditional waste tips by offering a recycled goods store and employing the philosophy that ‘one man’s trash is another man’s treasure.’
To ensure it fulfills on these commitments while serving residents from five different councils, KTS’ Corey Jeffs says his team rely on heavy duty equipment from JCB.
He adds that KTS run four transfer stations in Melbourne, all of which operate JCB machines.
Operating a range of JCB wheel loaders and excavators, Jeffs explains that the key benefit of JCB machinery is its reliability.
“JCB machines are very durable and don’t break down as easily as other machines,” he says.
“In our industry reliability is vital because you’ve got waste coming at you 24/7. The waste never stops and it’s never going to stop, so we need machines that never stop,” he says.
JCB wheel loaders are designed with customer input at every stage of the process, with particular consideration given to safety, efficiency, performance, ease of use and maintenance, reliability and comfort. Performance wise, JCB wheel loaders deliver big power and torque, high power-to-weight ratios, powerful breakout forces and excellent traction.
Throughout JCB’s history, the company has always invested heavily in research and development, keeping them at the cutting edge of innovation.
As such, the latest generation loader’s driveline comes standard, with additional features such as auto
lock axles. This automatically locks the front axle when required, allowing the loader to operate on any surface.
Operators can choose their ideal loading arm with a Z-bar linkage for high breakout applications or high torque for parallel lift and multiattachment use.
Similarly, JCB designs its hydraulic excavators around the principal that success relies on putting the operator at the heart of the design. As such, JCB excavators provide class-leading ease of maintenance, tough components and exceptional operator comfort.
Despite the rugged durability of JCB’s machinery, for Jeffs, it’s the JCB CEA team’s commitment to customer service that is the standout of the company’s ongoing partnership.
“We have a great relationship and they communicate very effectively
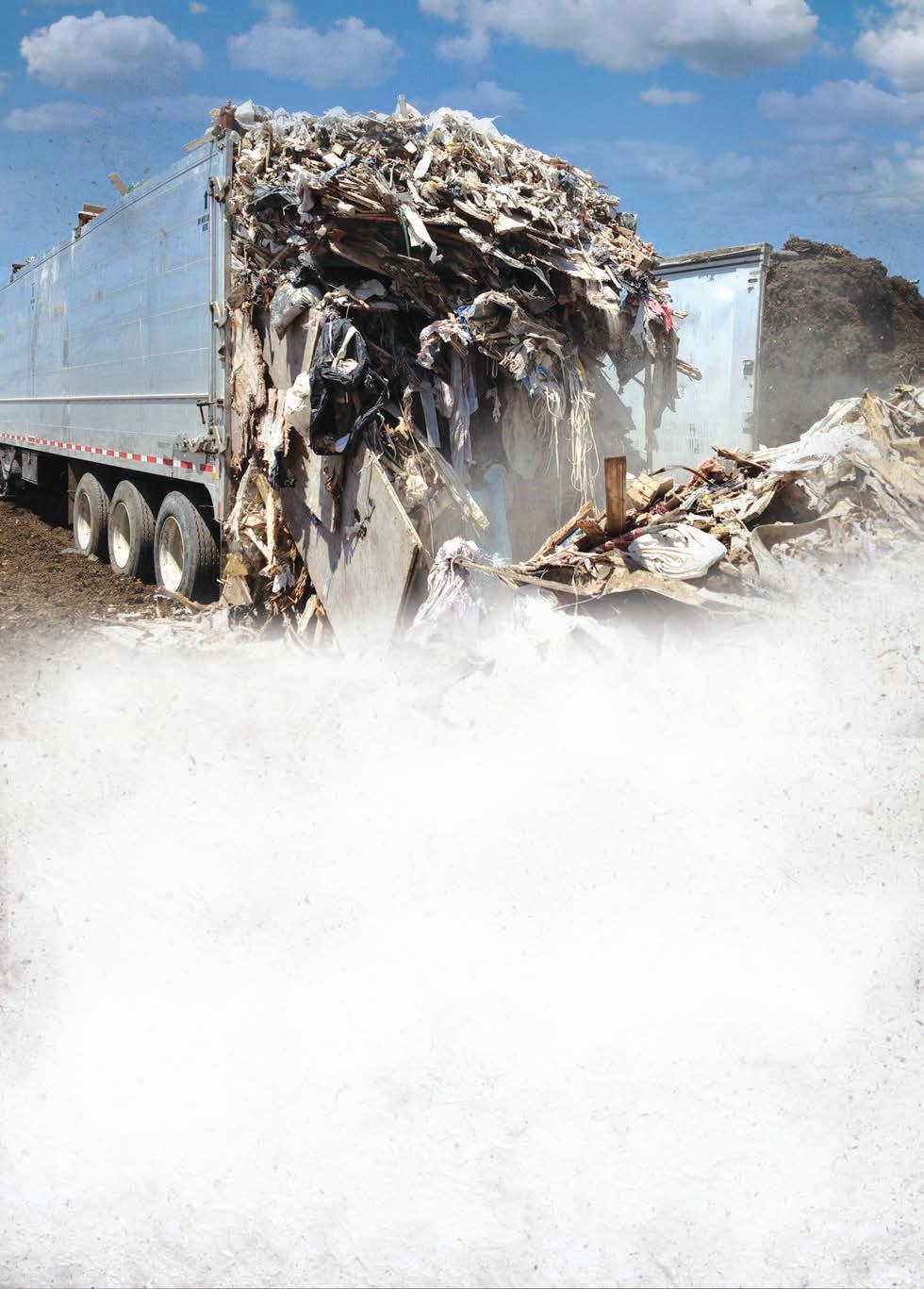
with us. I talk to our JCB CEA sales manager at least once every two weeks and he touches base with all the machines and how they’re going,” he says.
Additionally, Jeffs says the JCB CEA team make at least two trips to the KTS site each year to understand how the wheel loaders and excavators are running.
“They jump into the machines and see if anything needs improvement, such as new settings or attachments, and make those changes based on our specific needs,” he says.
“It’s great to have that service because they might see something wrong that we didn’t notice ourselves.
“From my perspective, JCB CEA have all of the bases covered. You get the whole package when you invest in JCB equipment.”
KTS operate a range of JCB wheel loaders and excavators.
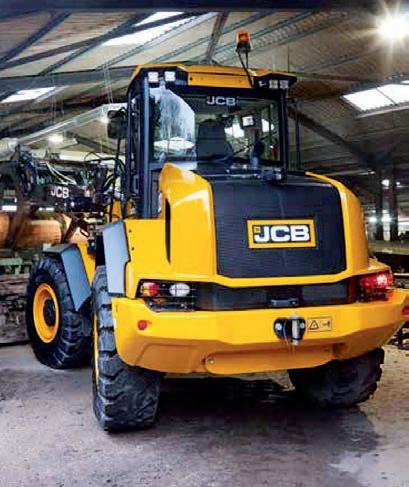
Contact – JCB CEA
P 1300 522 232 W https://www.jcbcea.com.au/
FLIR’S A400/A700 SMART SENSOR
FLIR’s thermal imaging technology has been used in waste facilities across the globe for fire prevention for over 40 years.
With advanced analytics and world-class thermal imaging, FLIR’s A400/A700 Thermal Smart Sensor Camera builds on that technology to provide an efficient screening solution for a range of complex monitoring applications.
Applications include early fire detection at landfills and waste facilities, critical infrastructure and product quality.
The Smart Sensor configuration includes multiple measurement tools and alarms, while also providing computing-on-the-edge. Analytics are performed at the camera level for immediate results.
With a range of lens choices, motorised focus control, and unrivalled connectivity, A400/A700 cameras offer unmatched power and flexibility.
Easy configuration allows users to tailor the monitoring system to specific quality, productivity, maintenance and safety needs.
The camera provides high-level image quality, with up to 307,200 pixels and a measurement accuracy of +/- 2 °C.
FLIR’s smart sensor provides high-level image quality, with up to 307,200 pixels.
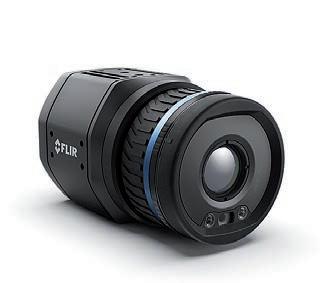
Edge analytics with features such as a polygon function help operators make immediate and informed decisions.
Additionally, with flexible measurement features, the A400/A700 advanced includes options to adjust measurements and alarms based on a reference temperature source.
Contact - FLIR P 1300 729 987 E info@flir.com.au W www.flir.com.au/
KOMPTECH TERMINATOR SINGLE-SHAFT SHREDDER
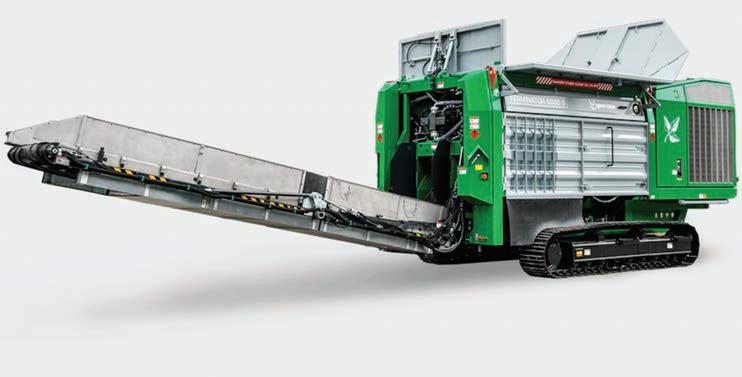
Komptech’s Terminator 6000S is a low-speed, high-torque single-shaft industrial shredder designed to process nearly all types of difficult waste including heavy C&D debris, white goods, mattresses, tyres and municipal solid waste.
The heavy-duty, mobile shredder is powered by a choice of modern CAT engines Tier 3 – Tier 5, which Continuous cutting gap adjustment allows for the precise setting of desired particle size. deliver 600 horsepower to the drum.
The direct drive drum, with load dependent speed Operators benefit from adjustable cutting gaps, control, creates maximum shredding force that can counter combs and swap shredding units, which can reverse at any time to prevent blockages, redistribute be configured from coarse pre-shredding to defined material or clean the drum. shredding.
The intelligent drum design features robust teeth in Available in Australia through Komptech CEA, the a spiral arrangement for maximum cutting and tearing, shredder features a remote-controlled hopper with a 3.4 while keeping shredded material consistent. Overload metre feed opening into one of the larges shredding units protection prevents unshreddable contraries from ruining on the market, facilitating fast and efficient operations. the tool elements.
Continuous cutting gap adjustment also allows for the Contact - Komptech CEA P 1300 788 757 precise setting of desired particle size. W www.komptechcea.com.au
STEINERT’S STEELMASTER OPTIMISED FOR TOUGH CONDITIONS
Hand-pickers are generally responsible for separating copper meatballs and ferrous scrap metal. With hundreds of objects passing over the sorting belt every second, it isn’t easy for hand-pickers to find and sort these problematic items. The purity of the ferrous product, e.g. the basic requirement for use in steel mills, may therefore vary greatly, making the product harder to sell. By deploying a combination of ballistic and magnetic effects, the new STEINERT SteelMaster is a good and efficient addition for reducing manual work. Following the tried and tested electric magnetic drums – STEINERT MTE – for recovery and initial cleaning of the ferrous fraction, the use of downstream magnets results in greatly improved quality and much less manual sorting. The STEINERT SteelMaster is specifically designed based on customer feedback and adapted to the tough conditions experienced in shredder plants. For example, the mechanics of the belt section have been adapted to improve material flow and separation properties, simplify maintenance and reduce the copper content in the iron to < 0.2 per cent. The robust design, typical of STEINERT, stands for a long service life and good availability of the technology. RecoveryAd_WMR_10_20.qxp_Layout 1 9/7/20 8:55 PM Page 1 The mechanics of the belt section have been adapted to improve material flow and separation properties.
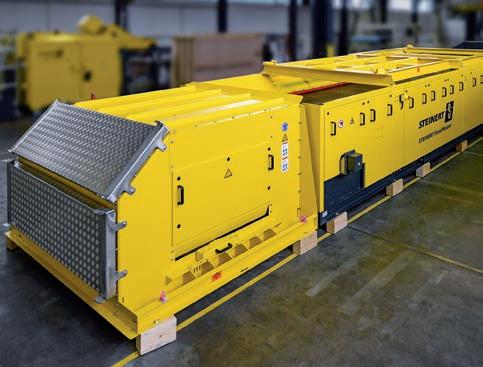
Common grain sizes are 20 – 400 milimetres with high sorting efficiency. Depending on the material composition the throughput is at 75t/h per meter machine width.
Contact: STEINERT
P +61 3 8720 0800 E sales@steinert.com.au W https://steinertglobal.com/au/
Turn Waste into Profit
Maximize Metal Recovery
Ultra-High Frequency
Eddy Current Separator
• Process sub 3mm particle size • Large number of frequency changes • Rotor spins at far higher RPM than standard eddy current
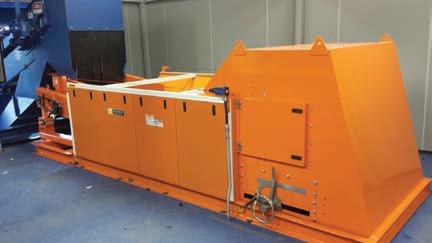
P-Rex Scrap Drum Magnet
• Exceptionally STRONG magnetic field • Greater pick distance • Wide pick up and carry arc in over flow or under flow applications
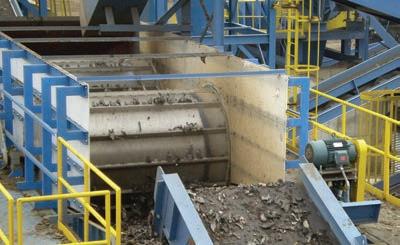
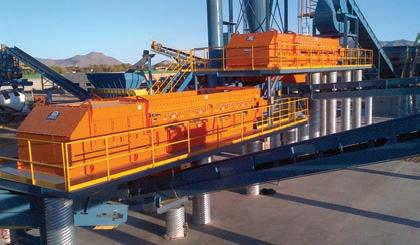
Shred1 Ballistic Separator
• Produces a premium #1 low copper shred • #1 shred contains less than 0.2% copper • No x-ray scanning neede d
Achieve better recovery and a higher grade product while delivering it at a lower cost per ton
Best practice delivers performance and innovation for CDS
A CONTAINER DEPOSIT SCHEME THAT FOLLOWS BEST PRACTICE LEADS TO BETTER PERFORMANCE AND INNOVATION AND SHOULD BE TOP OF MIND FOR VICTORIAN AND TASMANIAN GOVERNMENTS AS THEY DEVELOP THEIR STATEBASED SCHEMES, WRITES NWRIC CEO, ROSE READ.
Tasmania has signalled its intention to have a container deposit scheme (CDS) up and running by 2022, with Victoria to follow suit by 2022/23. There is now plenty of active discussion on best practice. The National Waste and Recycling Industry Council (NWRIC) has written to both the Victorian and Tasmanian Environment Ministers highlighting the need for each scheme to be fair, equitable and transparent. Strongly recommending that targets for community access, container redemptions, resource recovery and litter reduction are regulated, that operating and revenue sharing protocols are consistent with existing schemes and that scheme performance is publicly reported each quarter.
NWRIC’s preference has always been for a nationally regulated CDS rather than separate state and territory-based schemes.
With Victoria and Tasmania developing their schemes concurrently, the opportunity to ensure greater regulatory and operational consistency between all schemes should be a priority.
Consistency between state and territory CDS’ removes administrative duplication, creates cost efficiencies and drives innovation in collection, investment in local recycling capacity and greater reuse of materials into beverage containers.
As a minimum, the Victorian and Tasmanian governments should look to and learn from existing schemes for best practice.
NSW’s Return and Earn CDS has clearly set the benchmark in best practice in community access, container redemption and recycling rates, social and environmental outcomes and transparent governance.
The NSW Return and Earn governance model separates the roles of scheme regulator, network operator(s) and scheme coordinator.
Whereas in Queensland and Western Australia, the government has outsourced the network operations role to the scheme coordinator.
By doing this, the Queensland and Western Australian governments have lost control of ensuring community access is delivered.
By being one step removed, the
NWRIC CEO Rose Read says transparency, fairness and equity must be applied to new schemes.
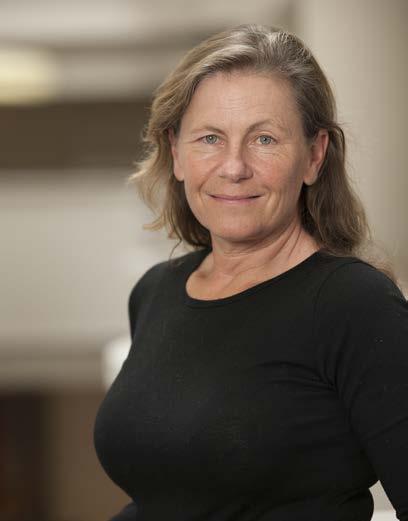
government’s ability to correct and fine tune network operations no longer exists. Likewise, the incentive to innovate and optimise collections and material recovery through an open and competitive process has been removed.
The reason the NSW CDS works well is because of how it is structured.
By separating the roles of network
operators and scheme coordinator, it ensures consumer convenience is being delivered and provides a commercial incentive to collect and recycle containers back into the economy.
In Queensland, even with a community access target set by government, customer convenience is still poor, with many collection points only open for limited hours or located in light industrial areas.
This is what you get with too much devolution of responsibility and a least cost compliance approach.
Similarly, when it comes to recycling containers, the Queensland scheme coordinator’s current online auction system, where accredited recyclers bid for material through a secure online portal, is flawed in two ways.
Firstly, the portal is not publicly accessible, thereby raising concerns about how recycled materials are traded and revenue shared between network operators and the scheme coordinator.
Secondly, it’s a closed shop, restricting access to legitimate organisations to purchase feedstock necessary to encourage investment in onshore processing facilities.
It is clear that CDS’ drive better outcomes including investment in onshore processing facilities, such as the recently announced two joint ventures by Cleanaway, Pact and Asahi, and Veolia and Coca-Cola Amatil, to establish recycled plastic processing plants.
This not only creates jobs and adds value to the Australian economy, but also ensures greater transparency of downstream recycling, as processing stays locally in Australia.
It also increases the amount of traceable local recycled content for the manufacture of beverage containers, creating a true circular economy.
Irrespective as to which governance model the Victorian and Tasmanian Governments finally choose, the regulatory instrument must, as a minimum, ensure the scope of containers included and the deposit amount for the proposed scheme is consistent with existing state and territory schemes.
The regulatory instrument should include annual targets for community access, container redemption, resource recovery and litter reduction, as well as fair and equitable operating rules and cost/revenue sharing arrangements that are consistent with existing schemes.
Finally, to instil community engagement and business confidence, the scheme coordinator and network operators should be required to report publicly every quarter on key targets.
The NSW scheme has done this particularly well. NWRIC has continually advocated for regulated product stewardship schemes such as CDS because of their ability to reduce environmental harm and protect human health by preventing waste and keeping resources circulating in the economy and out of the environment.
Given the community reach, environmental benefits and involvement of the hundreds of local councils, charities, collection and recycling businesses and beverage companies, it is critical that the Victorian and Tasmanian Governments get the CDS governance right.
The principles of transparency, fairness and equity must be applied and the NSW Government approach of separating the roles of network operator (s) and scheme coordinator clearly delivers this.
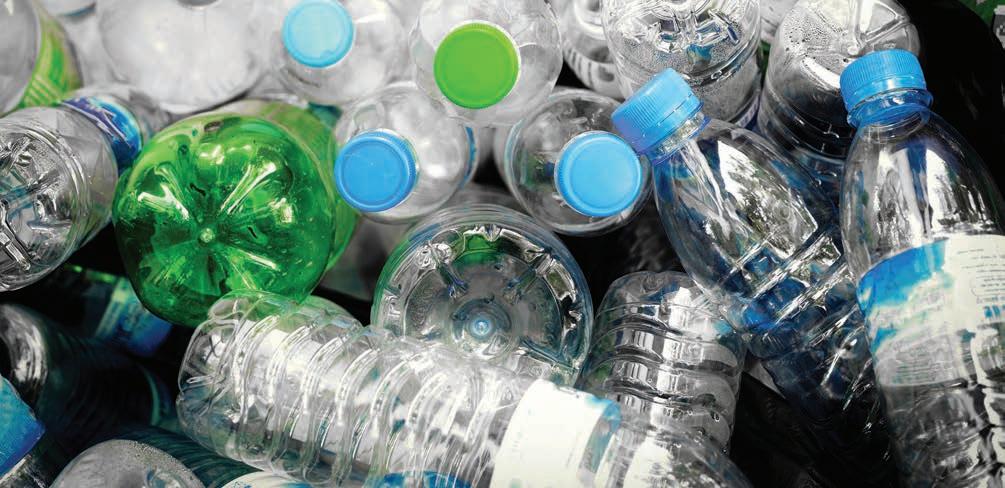
NWRIC’s preference is for a nationally regulated CDS rather than separate state and territory-based schemes.