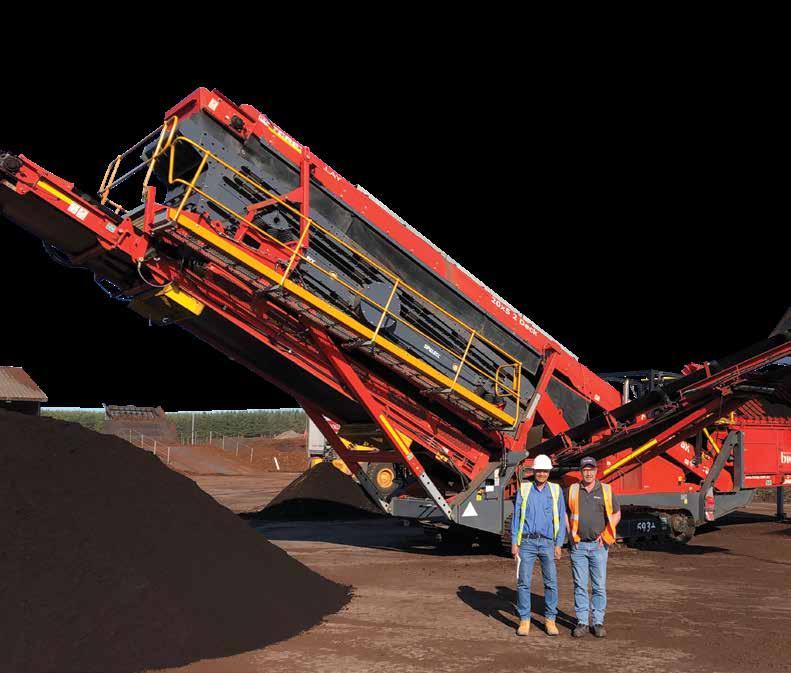
3 minute read
MOBILE MULTIVITAMIN
CRAIG TURNER, BIO GRO PROJECT MANAGER, TALKS TO WASTE MANAGEMENT REVIEW ABOUT IMPROVING SOIL HEALTH THROUGH HIGH-ENERGY SCREENING. T he viability of Australia’s productive land is being challenged by extreme weather conditions, as droughts and floods alter soil compositions and reduce nutrient levels.
Sustainability Victoria modelling suggests that as a result, the country’s agricultural and horticultural sectors will feel higher rates of climate change than other sectors.
Van Schaik’s Bio Gro, a family-owned company based in Mount Gambier, South Australia that supplies growing media, mulches and composts, are working to limit these impacts by stimulating soil health and reducing organic methane emissions.
Craig Turner, Bio Gro Project Manager, says the company works in partnership with various councils and private organisations to achieve optimum organic resource recovery.
He says that currently, it processes in excess of 750,000 cubic metres of organic material per annum.
“The organic material is processed into a range of specialist growing and mulching mediums, soil amendments and biological growth stimulants, perfectly tailored for the urban amenity, intensive and extensive agriculture and viticulture markets,” Craig says.
“To effectively process the organic material, which is inconsistent and varied by nature, we require highintensity screening equipment, which is why we work with Finlay Screening, Crushing and Recycling Systems.”
Bio Gro and Finlay’s relationship began in the early 2000s, when Finlay supplied the company with a Terex 693 Double Deck screener for mulch processing.
“Finlay offers a quality product with
great service and advice, is always fast to respond to any issues we have and supplies a good spare parts service with 24-hour support,” Craig says.
“When we required a new screen to address high moisture level and increase productions times, Finlay was the obvious choice.”
After considerable consultation and on-site testing, Bio Gro purchased a Spaleck Flip Flow from Finlay in 2017.
“We needed a screen that could produce at the required volume without operators having to regularly clean screen decks, which causes downtime and poses a significant safety risk to our staff,” Craig explains.
“Additionally, we wanted a mobile screen that was versatile enough to process the wide range of organic material we receive.”
Craig says Bio Gro uses the Flip Flow to screen and separate compost bark, organic compost and recycled timber, at up to 100 cubic metres an hour.
Spaleck Flip Flow screens are designed to screen damp and wet
The Flip Flow has helped Bio Grow reduce safety risks and improve output performance.
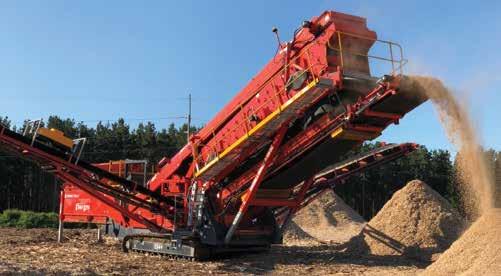
Craig Turner Bio Gro Project Manager
materials of inhomogeneous origin, with separation cuts of 1.2 to approximately 50 millimetres.
According to Craig, the machine’s base frame is agitated by a shaft and unbalanced motor drive, with vibrations passed to the frame through thrust rubbers to produce reliable and high-energy screening.
A key component of the mobile system is the Spaleck 3D Combi FlipFlow screen, which Craig says screens and loosens material on a top deck with optimal turning.
“The screen deck is mounted above the Flip-Flow deck to form a cascade, with 3D screen segments to reduce loads for the flip-flow screen mat,” he says.
“This increases the mat service life and guarantees optimum screening results. Plus, the screen mats are secured without screws, meaning there are no sharp edges or safety hazards.”
Craig adds that the 3D screening segments guarantee correct particle size, with no long pieces or extraneous material passed to the tension shaft screen on the lower deck.
“The Flip Flow has far exceeded our expectations and helped Bio Gro reduce safety risks, improve output performance and meet all our product quality requirements,” Craig says.
“The screen hasn’t suffered any blockages or downtime to date, which means we can consistently produce nutrient rich mulch and soil amendments to feed our land and protect the environment.”