
6 minute read
IN IT TOGETHER
Together to zero waste
REDUCING FOOD WASTE IS A KEY FOCUS OF COLES’ “TOGETHER TO ZERO WASTE” AMBITION.
Every year in Australia millions of tonnes of food is disposed of in landfill but leading waste management company, Cleanaway, is working with one of its major customers, Coles, to find a sustainable solution for this waste stream.
Although Coles’ preference is to donate unsold, edible food to food rescue organisations such as SecondBite and Foodbank, it has other waste solutions to manage food that cannot be donated.
Cleanaway collects packaged food waste from more than 900 Coles supermarkets, Coles Express sites and Coles distribution centres across Australia and removes the packaging, leaving organic material which is processed into compost for farmers rather than sent to landfill.
In addition to the organics service, which has expanded since its inception four years ago, Cleanaway also provides information to Coles team members about recycling, conducts waste audits, and worked with Coles to produce a waste and recycling guide.
Wade Mosse, Coles’ Head of Resource Recovery, says the partnership with Cleanaway has helped Coles reduce its tonnage of general waste sent to landfill by 10.5 per cent in the 2021 financial year and increased diversion of solid waste from landfill to 80.6 per cent in the same time.
“We’re passionate about reducing our environmental impact and, by working with customers, suppliers and industry partners like Cleanaway, we aim to increase food security, reduce waste and conserve valuable resources,” Wade says.
Andrew Crosling, Cleanaway’s Strategic National Account Manager, says Cleanaway is proud to partner with Coles to help it realise its ambition to become Australia’s most sustainable supermarket and work together towards its ‘Together to zero waste’ aspiration by reducing waste.
“At Cleanaway we see all waste as a resource and, by working with our customers like Coles to divert waste from landfill, we are contributing to the creation of a circular economy, which is consistent with our mission
From left, Cleanaway Resource Recovery Specialist, Sarah, with Coles Customer Service Manager, Isabelle, and Coles team member, Tanya at the Willawong depackaging plant.
Andrew Crosling, Cleanaway Strategic National Account Manager
of making a sustainable future possible,” Andrew says.
He says diverting waste from landfill also reduces the impact of government levies and assists with addressing climate change, as food breaking down in landfill produces greenhouse gas emissions including methane, which is 28 times more potent than carbon dioxide.
Since its contract with Coles began in 2017, Cleanaway has been expanding its organics service to more sites and, by the end of the 2021 financial year, was collecting food waste from 558 Coles supermarkets, 14 distribution centres and 347 Coles Express sites.
Coles Express has introduced a recycling service for packaged food products that are unsold, unusable and beyond their use-by dates. The packaged organics collection service captures food waste that cannot be donated to community groups, farmers and animal sanctuaries or used as animal feed.
EDUCATION AND AUDITS
Recycling is a key focus when Cleanaway’s in-house experts provide customised education sessions to Coles’ team members to help them manage waste in-store and implement initiatives for food that cannot be sold, including donations.
More than 750 education sessions were delivered in store and via phone in the 2021 financial year.
Team members are encouraged to follow the Coles food waste management hierarchy, which ranks the principles from most preferable to least preferable: reducing, reusing, recycling and reprocessing, and disposal.
Cleanaway has also assisted Coles to develop customised posters and bin stickers, which are displayed in stores, including bin rooms.
“The effectiveness of education is demonstrated by the increase in diversion of waste in the period after these sessions, noting an uplift of more than two per cent following an education visit,” Andrew says.
Cleanaway also conducted more than 100 audits of waste bins in Coles supermarkets and Coles Express sites in the financial year to determine if waste was being put into the correct bins and whether processes needed to improve.
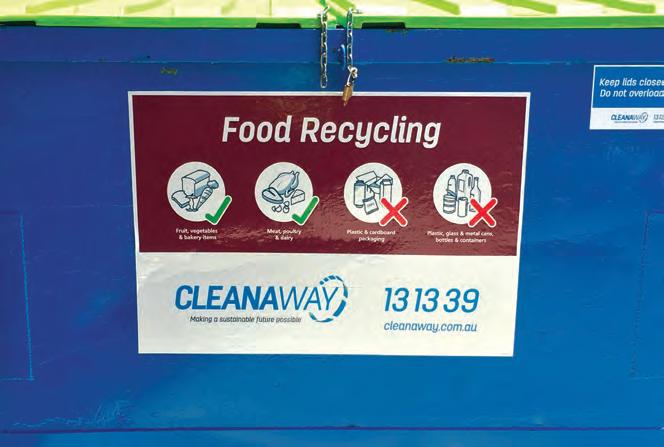
WASTE & RECYCLING GUIDE
The education toolkits available to team members were strengthened with the development of a waste and recycling reference and training videos, which supplemented Cleanaway’s portfolio of education tools, including the Greenius interactive online training modules.
The Coles Waste & Recycling Guide is a one-stop reference document covering all waste services available to Coles supermarkets, information about Coles’ waste diversion strategy and establishing efficient waste processes.
Each section of the guide is dedicated to a waste stream across food, plastic, and cardboard and paper, with images and graphics for ease of reference as well as highlighting the layout of
Cleanaway has developed customised posters and bin stickers.
bins, stickers, posters and processes to ensure every stream is optimised and without contamination.
The guide highlights Coles’ food waste hierarchy. It also covers aspects independent of Cleanaway such as Coles’ partnership with SecondBite, Coles’ relationship with Goodman Fielder which turns bread waste into animal feed, Coles’ soft plastics collection program in partnership with REDcycle, as well as Coles’ donations to farmers, animal shelters and zoos.
DEPACKAGING UNITS
In 2019 Cleanaway installed an industry-leading food organics depackaging facility at its South East Organics Facility (SEOF) in Melbourne to remove food from packaging such as fruit, vegetables, bread and grocery items collected from Coles and other commercial and industrial customers. The unit, consisting of a turbo separator and industrial green shredder, removes packaging, including plastic, bottles and cardboard, leaving a slurry-like organic waste which is mixed with garden organics at SEOF to produce high-grade compost for sale.
Cleanaway installed a similar facility at its Willawong recycling and transfer station in Queensland in 2020, and has been using similar third-party facilities in other states since 2017.
“The depackaging unit is a key recycling capability for large retail customers like Coles because it allows us to separate inedible but recyclable food from packaging. Without the ‘depack’, food including meat, bakery, delicatessen and other grocery items would go to waste because the nutritious organic material can’t be separated from the packaging,” Andrew says.
Cleanaway provides organics services to more than 1750 customers and, in FY21, provided 146,732 tonnes of material for composting, up from 135,521 tonnes the previous year. At other facilities the food waste is converted into renewable energy using anaerobic digestion technology.
“We all know that the benefits of keeping food waste out of landfill are huge but in practice it’s a big shift. Working with Coles we can see what’s possible when you combine leadership, technology and education to change the way people think and make a sustainable future possible,” Andrew says.
For more information visit: www.cleanaway.com.au
RELIABILITY YOU CAN COUNT ON


MEET THE TEAM:
LG918
6,200 kg | 77 hp
LG936LA
11,350 kg | 123 hp
LG938L
10,900 kg | 130 hp
Reliable performance isn’t expensive to build, SDLG has been proving that for decades.
The SDLG range of wheel loaders deliver simple operation and easy upkeep at some of the most competitive prices in the industry. With the performance of a premium machine, and a 2 year / 2,000 hour warranty, you can’t beat the value for money SDLG can offer.
LG946L
13,130 kg | 173 hp
Images are for illustration purposes only.
L958F
17,560 kg | 217 hp